A STUDY OF PAITHANI SAREE

CopyrightDISCLAIMER©2022 TANA BANA NIFT All rights reserved. No piece of this archive covered by the copyright hereon might be reproduced or utilized in any manner without the prior written permission of the copyright proprietor. To request permission, email priya.singh.20@nift.ac.in Layout and Edit by Priya Singh Illustrations by Shruti Gandhi Photographs by Nandini Vyas, Priya Singh, Vrinda Pasrija and Yash Pathak
RadhikaSinghTrivediShrutiGandhiVrindaPasrijaYashPathakSubmittedto:
NATIONAL INSTITUTE OF FASHION TECHNOLOGY, MUMBAI Nandini Vyas Neha Bapat Priya
Vinesh Tapre ( Associate Professor) Sushmita Das ( Course Coordinator - FC)
This is to certify that the below-mentioned students of semester-IV, Fashion Communication of National Institute of Fashion Technology, Mumbai have successfully documented the craft of Yeola Paithani Saree, as part of Craft Research Documentation. Under the project, a document has been prepared. The study has been conducted under the guidance and mentorship of Mr. Vinesh Tapre.

Acknowledgement
We would like to express our gratitude to the Ministry of Textiles, Govt, of India for providing us with this opportunity and helping be a part of this initiative. and for giving us the chance to learn more about the craft of Paithani, its weaving techniques, and getting to know the artisans on a closer scale. Furthermore, we would like to thank Dr. Pavan Godiadwala, the Director of NIFT Mumbai for allowing us to explore Yeola and work on an unmediated document about the craft. We also want to express our deep gratitude to Mr. Vinesh Tapre for his guidance and encouragement throughout the documentation.
Finally, we extend our gratitude to all the Artisans we contacted during the course of research and their families for sharing with us their experiences and stories about the oppulence of the craft. This project could’ve never been completed without their support.
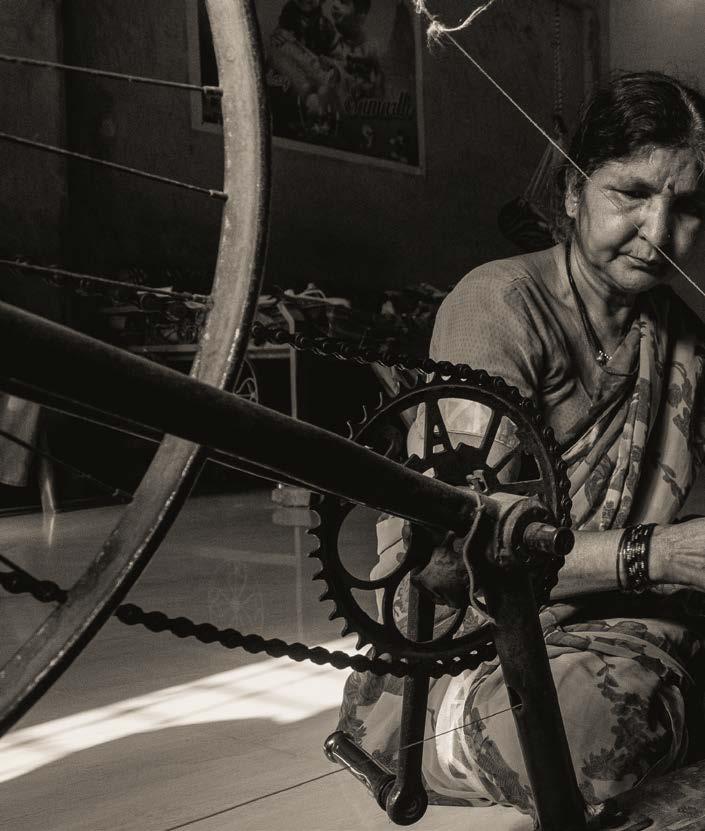
Abstract
The visit to Yeola kindled a sense of appreciation for not just beautiful crafts but also those without whom our country’s rich culture would merely be another chapter in history. The most riveting part of travelling to Yeola is the journey through Nashik and its outskirt areas in Maharashtra. Watching craftsmen work sitting in their mud-walled houses with bright coloured walls, working on the beautiful craft of Paithani was a fascinating sight. The students were very amazed by how welcoming the artisans were.
Documentation of the Craft Cluster study done by Neha Bapat, Nandini Vyas, Priya Singh, Radhika Trivedi, Shruti Gandhi, Vrinda Pasrija and Yash Pathak, students of the National Institute of Fashion Technology (NIFT), Mumbai on Crafts of Paithani(Yeola) in the academic year 2021-22.
Through an in-depth study of the processes, techniques, current scenario of the crafts and the socio-economic conditions of the craftsmen and interaction with the crafts people, this cluster intervention sensitized the student towards the craft and the artisans. It was also aimed to give student an insight into regional sensibilities, diversities, resources & environment. Further, the intervention provided a window to the student on methods to work in the crafts sector with artisans and aid them to promote themselves through various means of design & technology that they have learnt.

10 Background and Provenance 16 About the Craft Product Artisan Profile GovernmentMarketing Schemes ProblemsSWOT and Focus BibliographyAreas 28 30 42 44 46 50 55
CONTENT
Background and Provenance
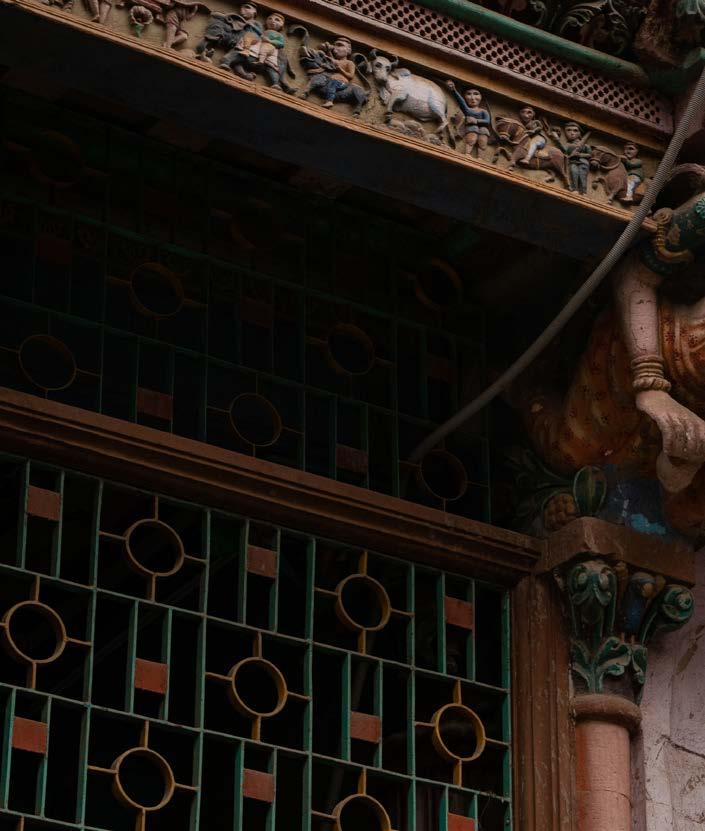
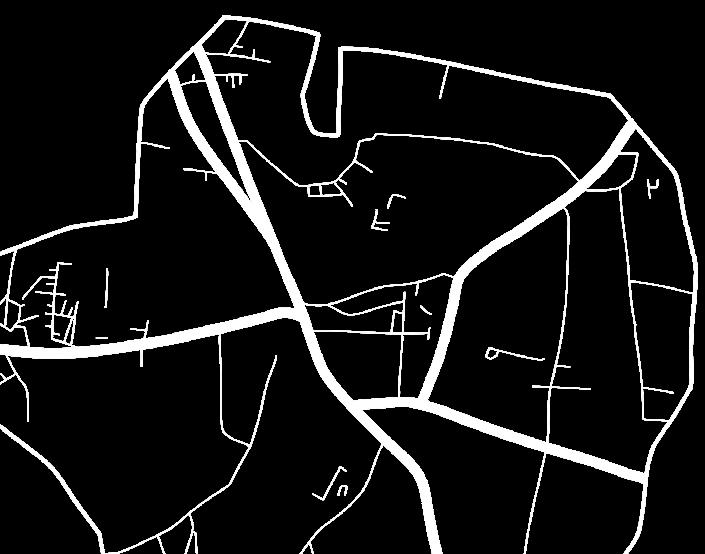
LOCATION
Yeola, is located close to major locations in Maharashtra, Nashik and Shirdi, but still remains scarcely known. But, the first thing you get to know when talking to any of the locals, is a proud nod towards the National Handloom Award winners, Bhandge, Kapse and Soni Paithani, that have set up shop in the village. We hire an auto to go to the Paithani Paryatan Kendra, and as we drive past the open land, and the local eateries, the driver starts proudly telling us about the town. He said it was founded by Raghujibaba Patil in the late 17th century, when he moved there with families of weavers. He also proudly tells us that Tatya Tope, a prominent member of the 1857 revolt, was born there.


The craft of Paithani originated from Paithan. Popular motifs in Paithani include peacock and lotus motifs, and the zari work and extravagant pallus on saris with the colour changing, or dhoop chhaon body is also a salient feature of paithani.
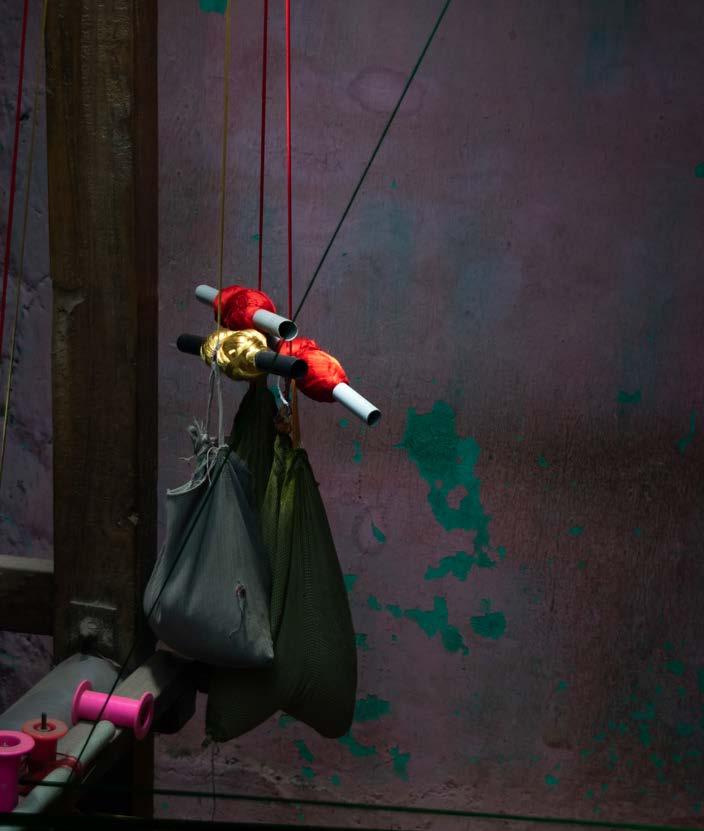
SATVAHANA EMPIRE c. 120 - 300 CE SATVAH A N A
Paithani first grew under the patronage of the Satavahana Dynasty, and later made its way through the Deccan region of India. The colour changing nature of this silk sari, comes from different colours of threads being used for the warp and weft.
Paithanis are made with rich ornamental zari work, and have a characteristic border of an oblique square design. Paithani, with its rich material and intricate weaving techniques, stands amongst the highest and most celebrated textiles of India. Much like Patola sarees of Patan in Gujarat, these are ceremonial sarees, traditionally worn by maratha women only on special occasions. Older generations of these women used to prefer their paithanis with coin motifs, or buttis all over the fabric, in colours like bright green and red, with elaborate pallus. These sarees started out as a sign of wealth and prosperity, worn by brides, in traditional Maharashtrian weddings. To this day, a paithani saree remains a prideful cultural possession in the Maharashtrian wardrobe.
13
The Romans imported this woven fabric and gave equal weight in gold in return. It even survived change in rulers in India and flourished under the rule of Mughal ruler Aurangzeb, who helped bring back its glory. He patronised the craft, and under his rule, prohibited weavers outside his court to produce this luxurious textile. This era contributed to many changes and novelties in the look of the sari, such as floral motifs and Amar Vel or aurangzebi motif. After the Mughal influence declined, Paithani reached its peak in the Maratha Period. The Peshwas of Pune harboured a special love for paithani sarees. They became the patrons of this craft, and helped settle weavers in a small town near Shirdi- Yeola.
14
Later, in the 19th and 20th century, the Nizam of Hyderabad became the major patron of paithani sarees. He ordered such large quantities of paithani silks, that the craft is thought to have survived because of his support. Attribution to the creation of the parinda or pheasant motif is given to Begum Niloufers contribution, from the same patron family.
EVOLUTION
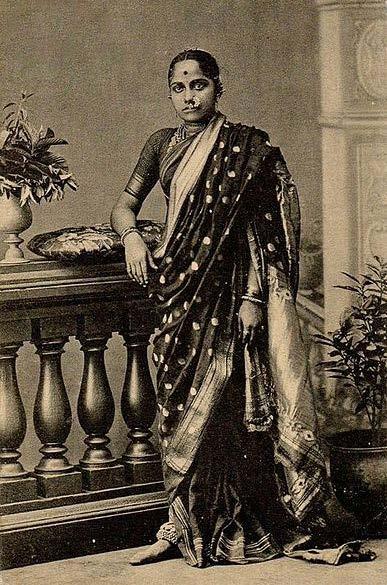
PAITHANI IN YEOLA
15
In Yeola, Paithani acquired a new dimension. In design, popularity and accessibility. This period is credited with the creation of the Asvali, a motif of a flowering vine. Now,Yeola has become the largest producer of handloom paithani sarees even after experiencing a brief decline in the absence of royal patronage. The Government of India along with the Government of Maharashtra took interest in the revival of paithani sarees.
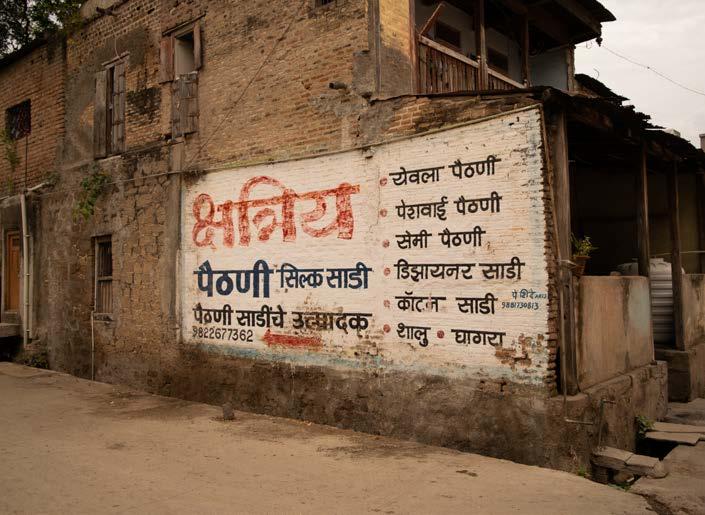
Nowadays, due to the advancement of technology, silk is usually pre-dyed with chemical dyes and comes in two varieties. The tana, or warp, is pre-stretched and imported with pre-counted threads in two saree lengths. The bana, or waft, on the other hand, is imported as single silk filaments and blended 4 to 5 times depending on the thickness of the silk cloth. The weavers buy silk by kilogram based on the market prices. Every saree requires approximately 700 to 800 grams of silk thread for the tana and bana. Only the highest quality of silk is bought.
In the olden days, Mulberry silk was sourced mainly from Bangalore and Mysore. It was the most preferred for weaving. It was raw, unsorted, and undyed when brought to Paithan and later colored with organic dyes of various hues in a separate dying unit.
Zari comes in two different varieties; silver zari and copper zari. The silver zari is made of silver wire woven with cotton thread coated in gold foil. Copper zari, on the other hand, is a copper wire weaved in gold foilcoated cotton thread and is significantly less expensive than silver zari. In the olden days, Zari was made from pure gold but now it's made from cheaper metals to make it more affordable and reach a wider market. The Saree’s value depends on the amount of gold and silver zari present in it. As a result, the fluctuations in the gold-tosilver ratio also determine the name of the saree. Since gold is measured in masa, this saree is also known as Baramasi, Athara, Choudamasi and Tinsheri, Pavsheri, and other terms that refer to the amount of gold utilized. The gold and silver can be extracted from the saree tears later by burning. However, copper can not be extracted from the saree because burning them can cause chemical reactions.
MULBERRY SILK ZARI
About the Craft Raw Materials
16
17 ZARI SHUTTLE JACQUARDMACHINE RESHIM THREAD HOLDER
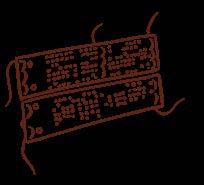
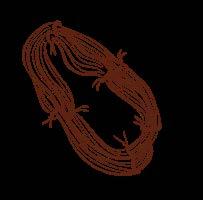

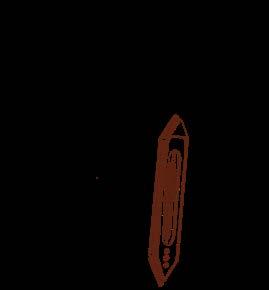

Traditional Technique
18
This technique of making the paithani saree is similar to other handloom products. Throughout this process, the non-continuous horizontal weft thread interlocks according to colors and design. Because this technique is timeconsuming, labor-intensive, and tedious, the product is quite expensive compared to power-loom products. People of the town called 'Pratisthan' have mastered the art of weaving paithani saree with silk yarn and gold zari. They have created intricate techniques of bleaching and dyeing the silk. Around 250 grams of silver tana was used with 18 metres of gold wire to make borders, pallu, and design patterns. During that period, the sarees weighed around 2 to 3 kg. The movement of the pedal and shuttle controls the motion of the weft across the thread of the warp. It takes a long time to weave. Even if the weaver sits for nine hours a day, only five to six centimeters is woven per day. The weft is interlocked and knotted on the upside and weaving eventually becomes the wrong side of the saree while the downside becomes smooth and finished.

19
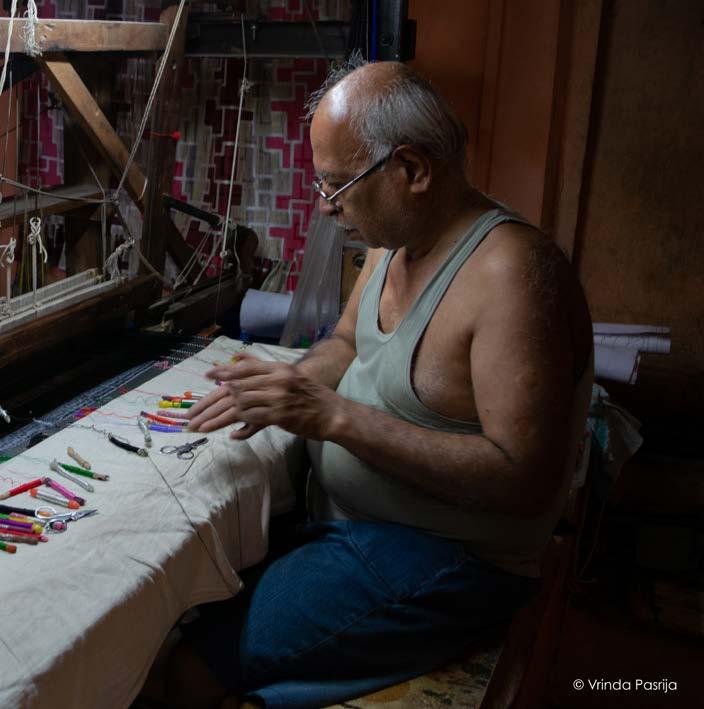
The Weaving Process
DYEING PROCESS Historically, natural or organic dyes were used in dyeing silk threads. However, in current times weavers have found comparatively cheaper and easily available options with more favorable properties in dyeing, known as chemical dyes. The silk threads are dyed with two types of chemical dyes; vat dye and acid dye. The entire process takes place in Yeola itself. Even the loom setup and tools like dhota, kandi, needle, and yarn winding equipment are available in the local market of Yeola.
20
The silk threads bought from Bangalore are separated into thok bundles. Then for around 15 minutes, the silk is kept in hot water saturated with Khar (unprocessed salt). Next, the excess impurities are extracted bvy inserting a rod between the bundle of threads and frequently dipping it in cold water. 1. 2. 3.
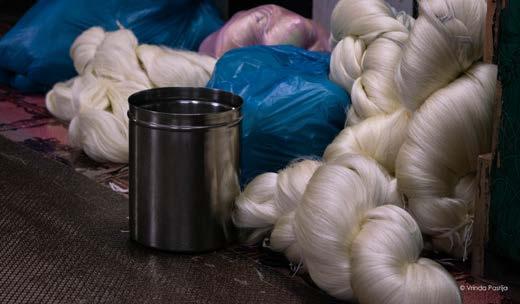
The process of bleaching and dyeing happens in a copper vessel that contains the solution.
20 to 30 grams of dye powder is used per kg of yarn. The dye powder is mixed in water and acid is used as a fixer, while coconut oil gives the resham a soft finish.
5. 4.6.
The dye baths are then prepared that vary according to hues and shapes. The dye is chosen later through a government-approved shade card of 400 plus samples.
21
The yarn is dipped in the dye bath for 30 to 40 mins hung on a copper rod. It is eventually removed after a few washes and then squeezed and left to dry in the shade.
After the dyeing process, the threads are wound upon the Asari and a machine made up of a cycle wheel. This process is usually performed by the women of the family as it requires a soft touch. And afterward, the silk threads are transferred on a kandi and finally set on the loom.
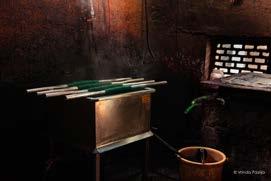
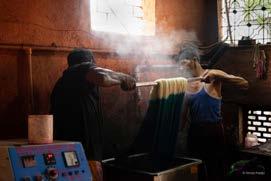
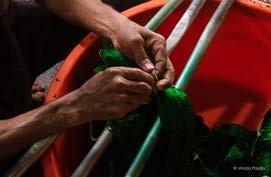
PRE-WEAVING PROCESS
Preparation of the tana and bana on the loom itself requires four to five days.
22
The tana (warp) is prepared by stretching and separating the individual threads multiple times and wrapping them around a spindle to smoothen out any kins and detangle the threads in general. It is wrapped around the drum of the loom, that is also called the dhol. It is wound tightly to maintain tension as the loosening of the tana may cause unequal weaving and warping of the saree. Next, a beam called ata is connected to the rear end of the loom and the tana is sorted into bundles of 90 threads each. The threads are then individually joined by twisting through the heddles. This process is called jodni. Jodni is a time-consuming and tedious process that takes 12-18 hours to finish and involves the individual threads joining alternatively over and under the bar of the hand-loom.
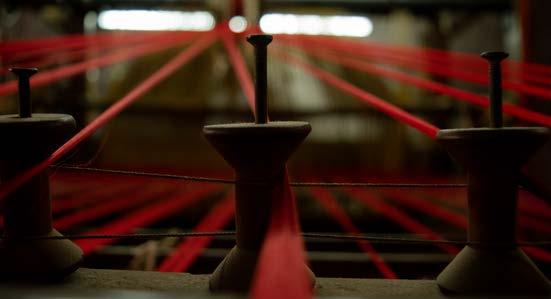
The bana (weft) is prepared on the thape, a set of three stone pedestals. Three wooden rods are attached to the stone base, one of which has grooves to hold the phalka. The prepared banais then moved to the tansal and is generally made into 3 or 5 plies by winding on thape multiple times.
The looms were usually made of teak wood as they are durable and less prone to warping or decay. However, in recent times, due to lack of availability, only main elements like the warp beam, cloth roller, and beater are made from teak wood as they need to be the most durable so that they don't cause defects in the saree. After the tana and bana is set on the loom, the weaving process is ready to be started.
After the 3-ply bana is made on the weft, it is stretched on the yantra (spinning wheel) and then wound around the kandya (bobbin) made of pine wood and tapered at both the ends.
23
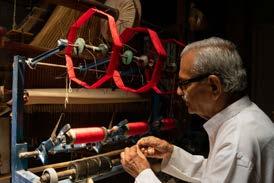
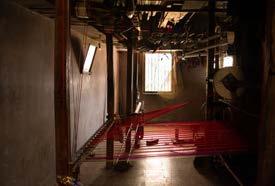
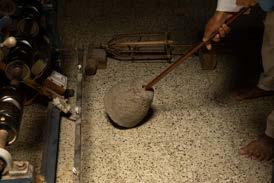
STEP 3: HANDLING THE ATA AND TANA
STEP 1: WEAVING THE PALLU
For the weavers to weave the padar or pallu, they use either silk warp or zari work. Weaving the pallu is a time-consuming and complex task that takes two weeks to a month depending on the length, level of detail, and design motifs. The motifs are formed in bana on a foundation of gold zari. During the weaving process, the weavers count the number of threads that are used in order to maintain consistency throughout their weave.
STEP 2: WEAVING THE BODY
The next step involves weaving the body of the saree. A paithani saree is bordered on both the edges. A throw shuttle is used if the body is kept plain. But if there are any buttis in the body, each butti is handwoven in gold or silver zari. A single paithani saree typically has 200-300 buttis. Since every butti in a handloom saree is handwoven, it takes a long time to complete the body. The buttis, just like the pallu, is woven with different motifs like flowers, peacocks, parinda, petals, and paisa. Each paithani saree has a set pattern. Each weaver adds his unique elements to it as they weave. The weavers have the freedom to create unique designs or follow the traditional one. But while weaving, the thread counts have to remain the same. In a single day, a weaver may weave 2 inches of the pallu and 5-6 inches of the body. Even though the weaver regularly monitors the tana for consistent tension between the threads, the tana is tightened and wetted with water to enhance the tension if there is any discrepancy. That is because unequal tana can cause snarls in the saree's fabric.
24
WEAVING PROCESS
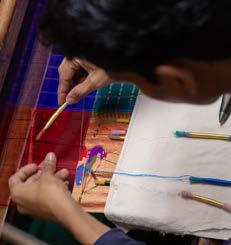
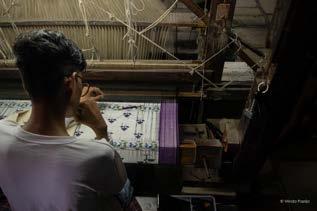
STEP 4: POLISHING THE ZARI WORK
If the foundation of the zari is silver then there will be a reddish tinge, but if it's copper or bronze, then there will be a touch of bright golden or yellow. Once the saree is woven it is unwrapped from the roller or tulai, washed, and folded.
A saree with two distinct coloured warps and wefts are called Dhoop chaon, and sarees with mulitple colours weft and warps are called par-i-taus, whereas the ones with square shades are called charkhani.
STEP 5: OBTAINING THE COLOURS
25
fter 3 to 4 inches, the zari is polished with a mixture of gum and water to keep it firm and preserved. This polish seals loose threads as well as stiffens the border. Other than gum, some sticky substance like methi or jaggery is used. It is worth noting that these elements don't leave any stains, marks, or deposits in the zari work. The tana is made of silk, while the bana is made of zari. That, as a result, gives a distinct color to the border.
By combining different colours of bana and tana, a variety of colours can be obtained for the saree. As a result, one can find an enhanced spectrum of colours of paithani saree. For example, by combining blue bana and red tana, purple shade is obtained, where as by combinging green bana and black tana a shade of dark green can be obtained. Sometimes these shadesare blended in such way that they can create a dual tone or dhupchaon effect. Despite the limited colours of tana and bana, the variety of combinations mae it possible to create a wide range of colours. A single coloured paithani saree with the same warp and weft is called a Daryai.
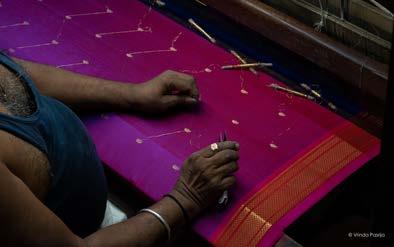
Popular Motifs The Kamal The Panja The Muniya
The paithani motifs amalgamate human culture and its close relationship with nature. Each motif has a story to unveil.
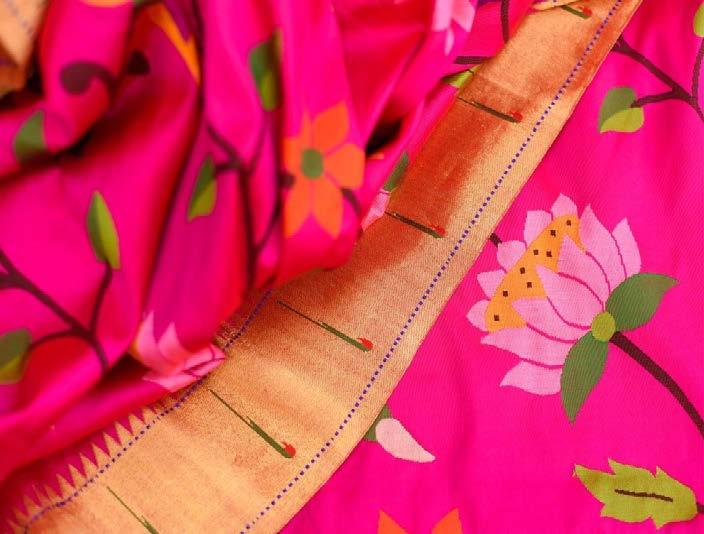
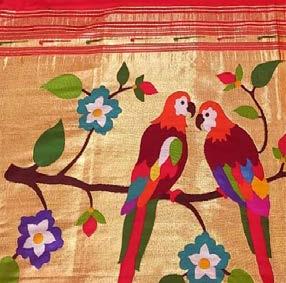
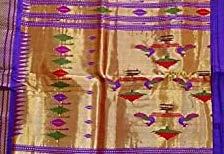
The Muthada The Asawalli

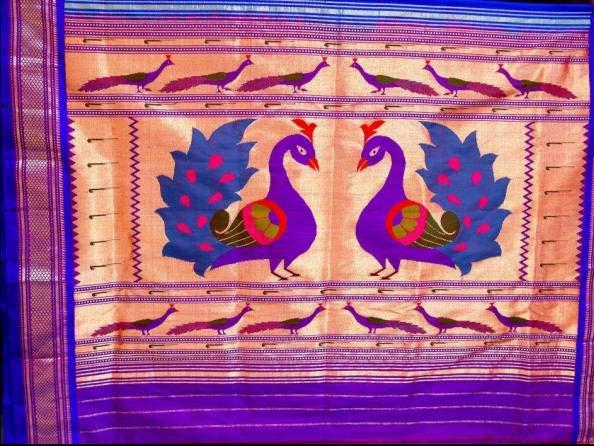
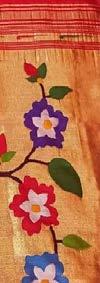
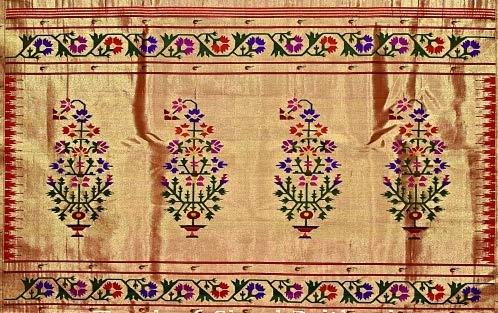
28 Cream WhiteTusserGolden BrocadeGolden YellowLemon Yellow Dark PinkCarrot PinkLight PinkVhiskitViolet PeachReddish OrangeRustPomogrenateBlood Red Parrot GreenDark Parrot GreenDark GreenOlive GreenTeal Blue TurquoisePeacock BlueRoyal BlueNavy BlueLavender BlackDark GreyOlive Green BrocadeSilver BrocadeWhite
29 Colour Psychology
Traditional Paithani usually carry bright colours that are quite intense and in your face. Since this traditional garment has a rich history of being adorned by royalty and is now by the rich or by individuals on very special occasions, the bright colours invokea sense of happiness that comes with the festivities. The colour combinations also attract a lot of attention to the person wearing the saree. Furthermore, When dyed on silk the colours give a rich feel which suited the royalty.
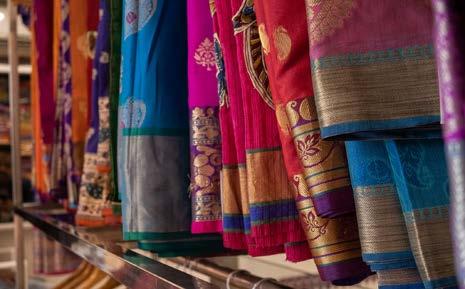
30
Product
The artisans have started bringing variations to their products by making purses, lehengas, cushion covers, bags etc.
Most paithani sarees are packed in a box with a plastic wrap to prevent them from getting spoiled because of water. This is a very standardised packing system and artisans or traders do not look at improved packaging as an area to strengthen for growth of sale. Artisans either sell through social media platforms, or are dependent on traders to sell their sarees. These artisans who sell through traders are not connected to the person buying their saree.
Paithani sarees date back to the Satavahana Dynasty(2nd century BC- 2nd century AD) this makes paithani an ancient weave and this alone makes a paithani saree a very treasured possession. Women in artisan families also own paithanis that were handed down to them by previous generations.
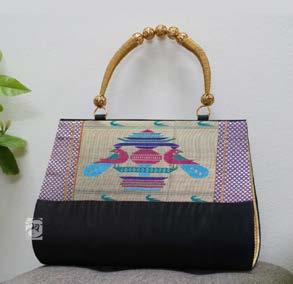
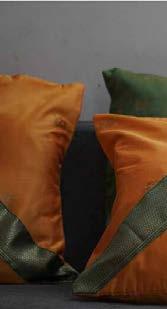
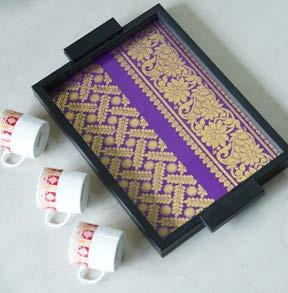

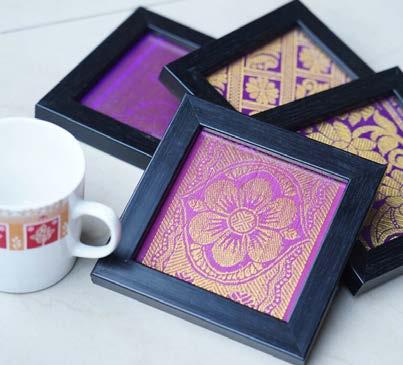

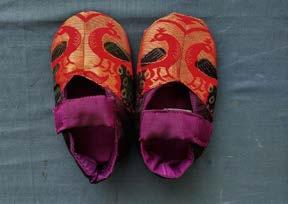
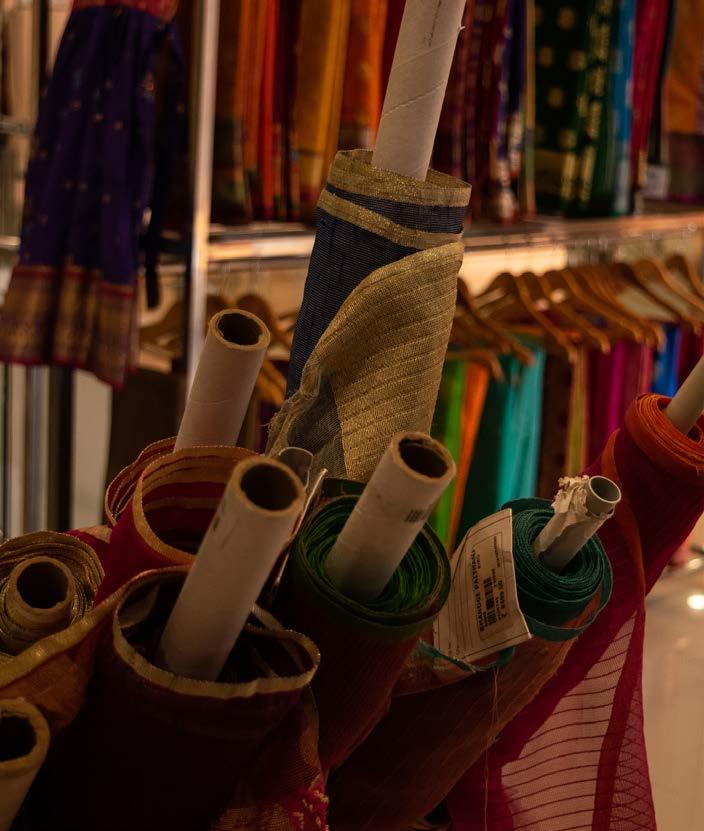
Sometimes rats or other creatures can disturb threads on the loom. The threads can then be reattached or completely go to waste if the damage is irreversible. Climatic conditions also affect the quality of product. Most looms are made of wood, which tends to get swollen up and absorbs moisture in monsoons. This causes the silk to stain from the wood. To avoid this, the weaver usually weaves dark coloured sarees in monsoon.
33
An artisan would describe a product with no defects, good market demand and one that does not take too much time and sell for a lower cost as a good product. A defect may be related to colour, breakage of threads or a wrong design. Some jacquards leave stains on the paithani. Poor quality of raw material can lead to breakage of threads. This leads to holes in the saree.These minor defects are covered up with embroidery and are sold as defective products at lower prices
Quality Control

Artisan Profile The weaving families of Yeola
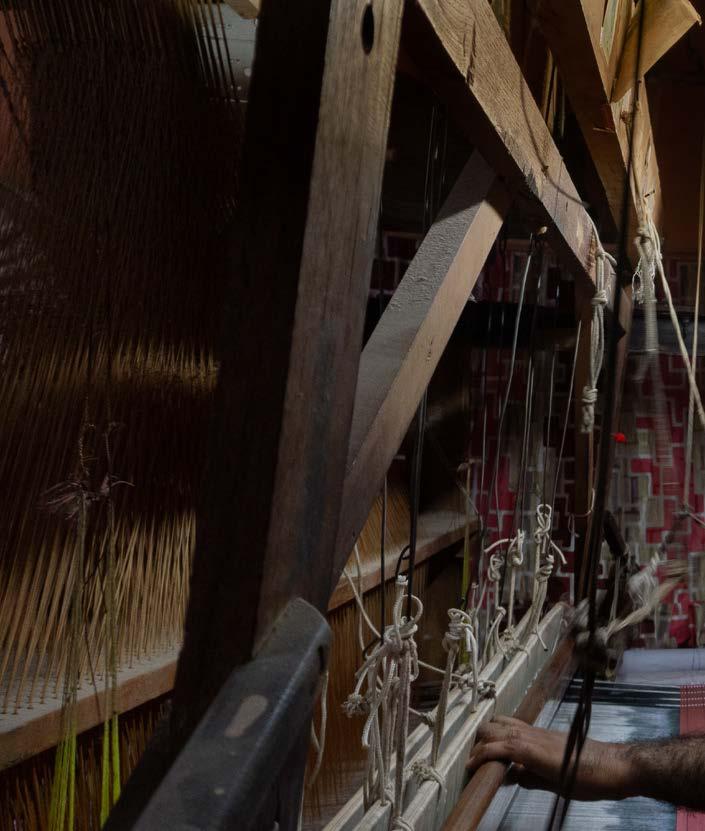
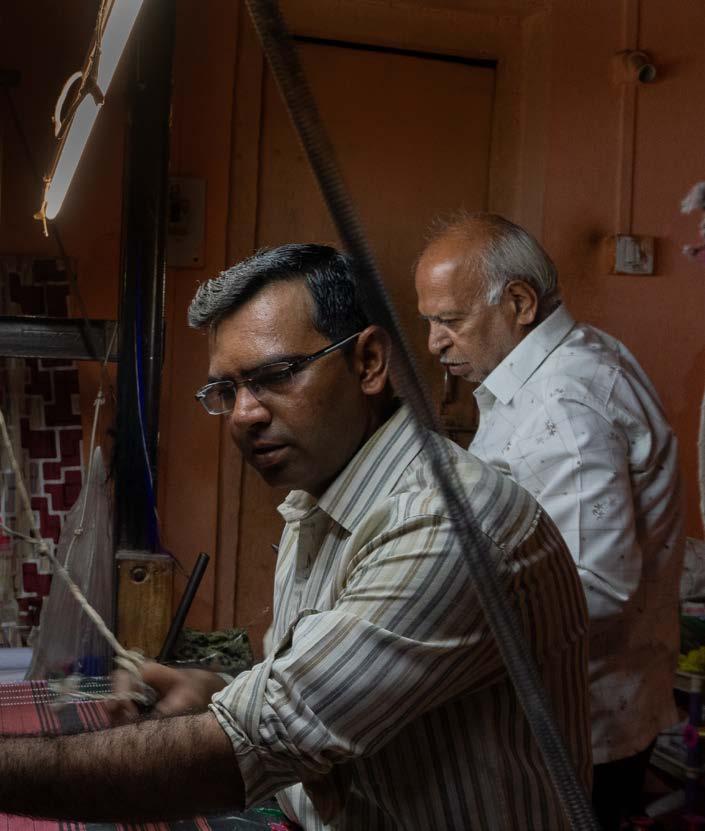
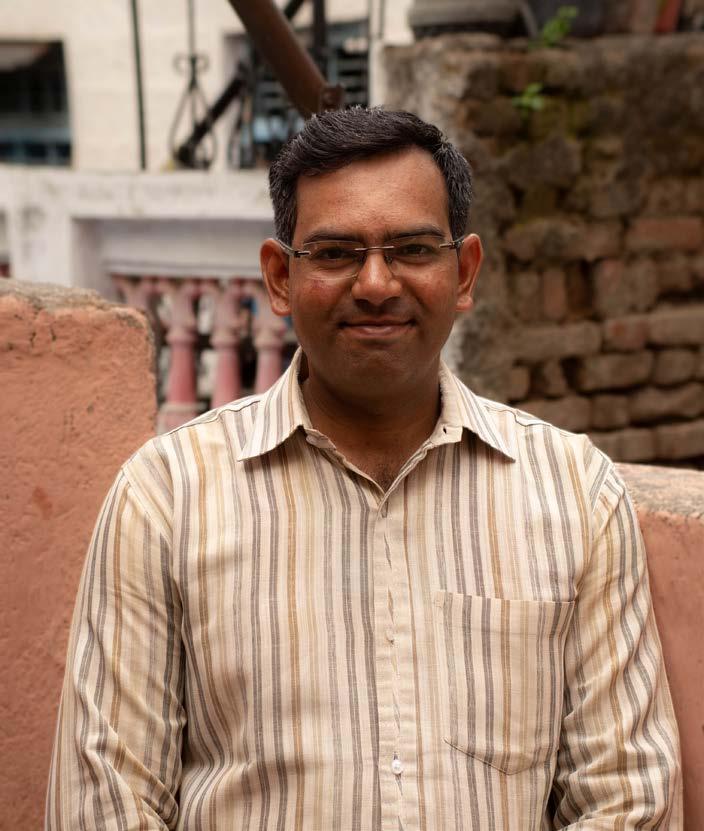
Sagarji is the businessman in the family. He started his weaving career like many others, making buttis on the saris with his father’s help when he was a child. The pandemic hit the Kherud family hard, but Sagarji realised that he could capitalise on the fact that everyone’s lives had shifted online during the pandemic. Sagariji is not afraid of taking chances and learning new things, so with his brother in law’s help, he set up an instagram account, and soon after, his business was booming. Sagar Kherud’s brother, Sanjay also runs a paithani business. He has two sons, one of whom is not interested in the craft, and is more academically inclined towards subjects like english and maths. Sanjayji’s wife also has taken an affinity to the weaving practice at the loom. She is busy with housework, but still spends three hours a day weaving, to help out the family business and because she finds the various designs and colours of paithani very fascinating. She would like to work a bit more on the loom once she has more time, and admires women who do so. The yellow rectangle represents a member of the artisan’s family who is also an active weaver and the rectangle’s position showcases the generation.
The Kherud Family is composed of second and third generation craftsmen.The family consists of the grandparents, their two sons and their wives, and the older son’s two children. Everyone in the family pitches in and takes part in the weaving process.
Kherud Family
37
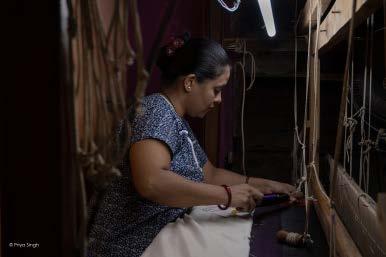
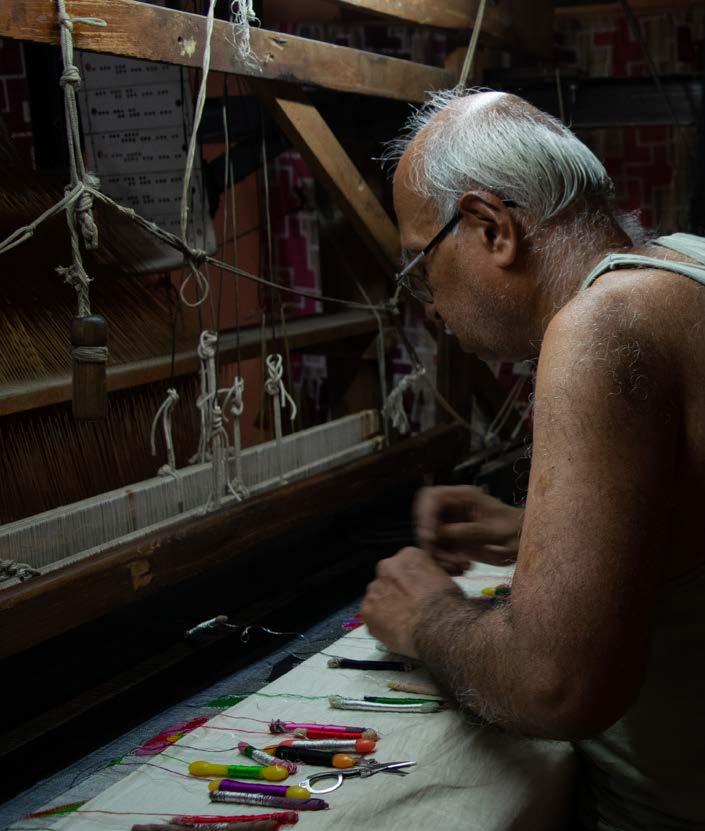
Their father, Mr. Vijay Sadashiv Kherud has been in the practice for over 50 years. He too learned the craft from his father, and passed it onto his sons.

Nagpure Family
The Nagpure family, like many others in Yeola, is a third generation weaving family. The two brothers have learnt the craft from their father, but in a rarely seen path of events, went to pursue their academic careers at Nashik. The younger brother subsequently got involved in an alternate occupation, while the older brother, Chetan Nagpure came back to the family weaving business and is currently working at the loom with his father, who has been weaving for over 50 years. Chetan Nagpure is somewhat hesitant to expand beyond the current structure of selling orders to bigger merchants. He says that selling his craft online could either be a hit or a miss, and does not want to forego the reliability that the bigger merchants offer. The men of this family have been previously involved with Societies and Cooperatives in the area, but saw their failure. Thus they remain sceptical of any organised operations for their help and upliftment.
Chetan’s mother is a success story of her own, She had an interest in weaving ever since she was a child, but in her time, girls were not allowed to sit at the loom. She was the one who sent her children to college, because despite her faith in the craft, she believed children should receive an education before making any choices about their future. Once the kids went off to college, and only her husband at the loom wasn’t enough to provide sustenance to the whole family, she started her own general shop in the middle of their town. Now, she is the one that handles the shop. She is very happy that women have started getting more involved in the weaving process, and would love for her daughter in law to eventually do the same.
40
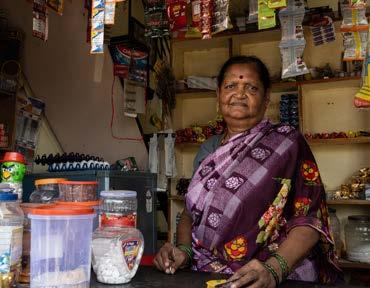
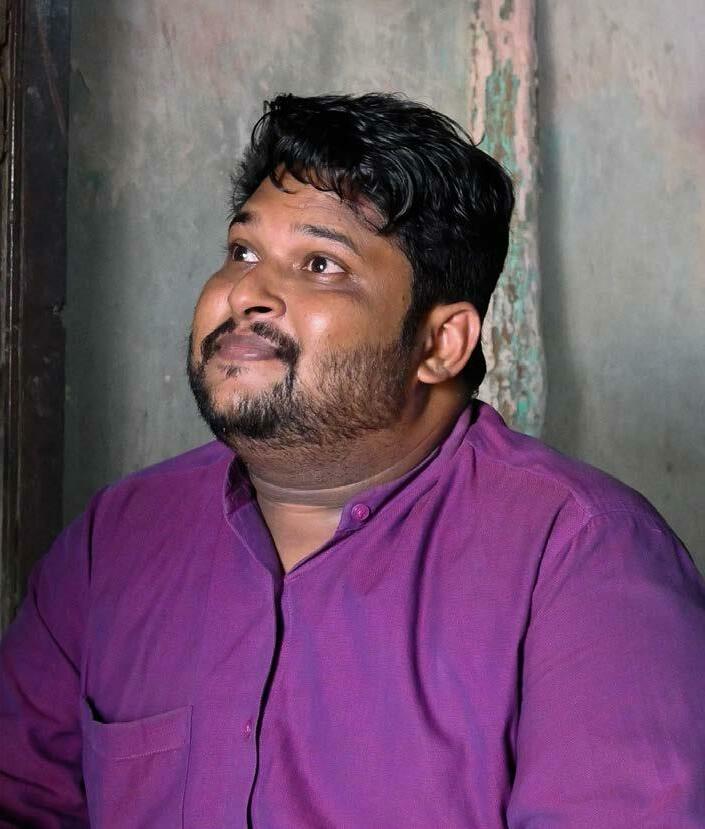
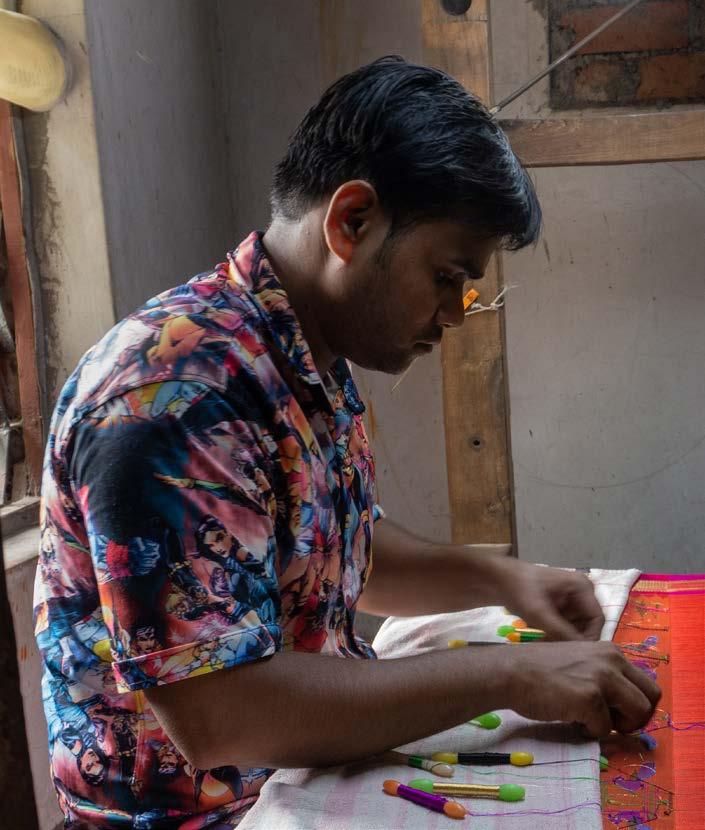
43
The Awankar family, owns a whole lane of homes, each of which houses looms. Despite this, they prefer to keep to themselves and their work. They are not keen on expanding their business via online resources, despite the success of their neighbour, Sagar Kherud.
Awankar Family
However, Aunty Awaknkar was eager to talk to us about herself and how she wanted to learn the craft soon, so she would be able to help out the family. She has a Bachelor of Arts and her Masters in Library sciences. She has also done her craft teacher diploma, art teacher diploma, and even her Montessori teacher diploma. She taught as an art teacher for eleven years, but after moving to Yeola and having a child, her career seems to have reached a standstill. She has not learnt weaving yet, but would like to, as she is a firm believer that all members of a family should know the craft, so it can stay in the family for generations to come. Once she got to know about the various workshops that are conducted she was eager to join those as well, in hope that those in combination with her current knowledge could be of help to the business.
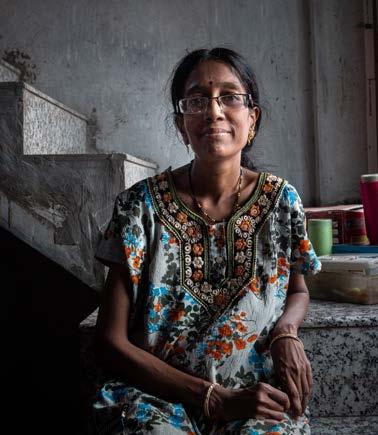
Nagpure Family
This family has third generation weavers. The three brothers run a weaving business together. They are expanding their business online, despite being sceptical of its success. Currently they have a whatsapp group where they take orders. They are also sceptical of welfare schemes that come to them. They would like to take the benefits, and have tried to do so, but feel like it is often more work to go through tedious processes and long waiting periods, than to just continue as they were.
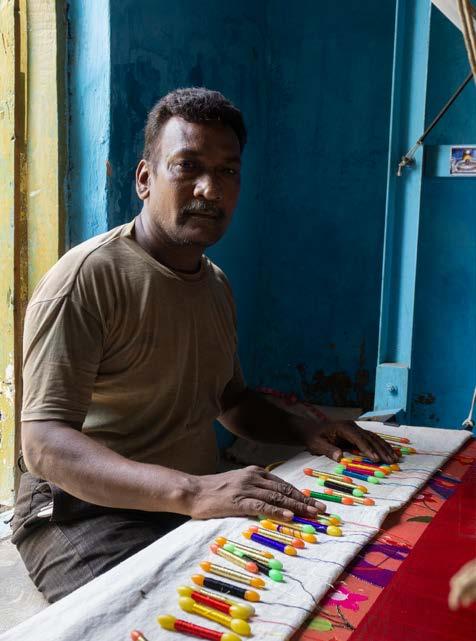
Nagpure Family
The Nagpure family is a first generation weaving family. They are not that well off, but the three brothers are thankful to the government for providing them the loom at a low price. They like to keep to themselves and did not feel comfortable giving video or audio recorded interviews. Their sister, Induvishnu Nagpure, is divorced and has a daughter who has just finished her 12th standard. Induvishnu Nagpure does the san
45

The main market for sale of Paithani sarees in Yeola are the stores present in and around the town. These stores buy sarees from small artisans, these sarees go through branding and pricing and are ready to be sold. Families from Aurangabad, Pune, Mumbai and other cities travel here to buy sarees. This gives them an assurance that they are buying an authentic product at the right price. Some store owners are also weavers as they have been a part of the cluster for years. While Maharashtrians mostly buy the traditional Yeola Paithani, a major chunk of the sarees made go to the south indian market where paithani sarees with intricate and time-consuming designs sell for higher prices.
46 Marketing
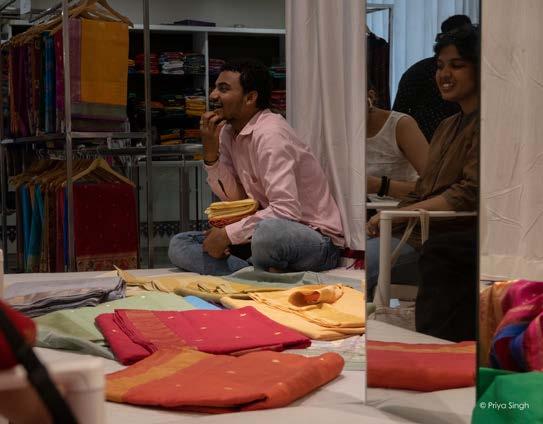
47
Social media and the internet is a new and emerging mode of trade that has helped many artisans prosper. The onset of the Corona Virus in India, initially had a great negative impact on the sale and production of sarees. Artisans were deeply hit as the traders stopped buying sarees from them. They had no other way to sell their sarees, when they learned about social media and started selling their sarees through platforms Whatsapp and Instagram. They had thus found a way to sell their products directly to the consumer by avoiding traders and store owners completely. Many artists in Yeola are now covering National and International markets through online sales.
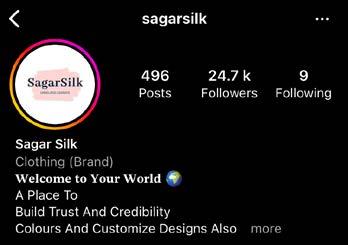
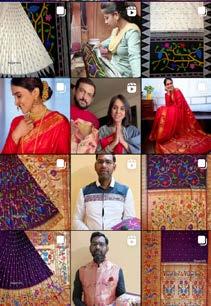
The Yarn Supply Scheme has two parts. These include; the supply of yarn at Mill Gate price and a ten percent subsidy on domestic yarn such as silk. Under this scheme, weavers or weaver groups that are enrolled under CHCDS will get a ten percent value appropriation for a total of 4 kgs of silk each month.
48
Mahatma Gandhi Bunkar Bima Yojana (MGBBY) and Health Insurance Scheme SchemesGovernment(HIS)
This scheme is for the development of Mega Handloom Clusters, to help with their growth and development. There are more than 15000 handlooms in each group, and a budget of upto 40 crores per group. This budget goes towards things such as improving foundation offices, creating better storage spaces, improving technology, etc.
Yarn Supply Scheme
Handloom Cluster Development Scheme (CHCDS) MGBBY has the goal of giving upgraded insurance cover to the handloom weavers, incase of normal or unintentional demise and in instances of aggregate or halfway inability. The Health Insurance Scheme focuses on the financial empowerment of the weaver community, and ensuring that they receive the best medical care. The plan covers the weaver, their significant other and two children's prior and new illnesses, and saving generous arrangements for OPD.
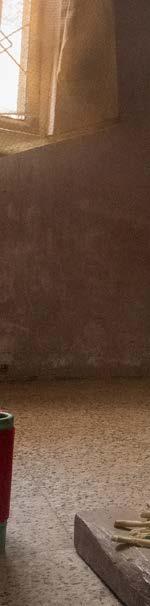
49

FLEXIBLE DESIGN
Yeola Paithani is different from the Paithani Saris made in Paithan. They use chatai design for the border and focus on making jacquard designs. Craftsmen in yeola have recognised the need for a broader scope of design to appeal to a wider customer base. Thus, in yeola we are not only seeing changes in motifs and colours of the saris they make, but also in the products made in the same technique.
SUPPLY CHAIN MANAGEMENT
SOUTH INDIAN MARKET
Strength
Even in a small village, the smooth running of the supply chain is impeccable. Damaged, or faulty goods are never delivered and pricing is always fair and equal for all under each given climatic circumstance every year.
50
During covid all the artisans were hit hard and sales fell. Although, some people dug themselves out of this hole by identifying and complying with the online market that everyone was flocking to. Now even after the pandemic, with the market being back to normal, many artisans are choosing to continue this system of selling goods online, and cutting out the middleman, benefitting both them and the customer.
SOCIAL MEDIA USAGE AND LARGER MARKET APPEAL
Even though variations of paithani are not too popular in its home state, maharashtra, other parts of india, especially the south, loves to place orders for all different innovations taking place in paithani. This is a big market for yeola paithani which has been made available through the online markets that they have started.
GOVERNMENT SCHEMES AND PROGRAMMES ARE OFTEN INACCESSIBLE The Indian Government, no doubtedly has come up with various schemes, relating to insurance, education and subsidies for these weavers. But sadly these schemes often remain inaccessible, and echoing around in the same circuits, missing the people who oftentimes need them the most.
SOME PEOPLE HAVE INHIBITIONS TOWARDS SOCIAL MEDIA Although some people found an almost natural affinity for the online markets during the pandemic, some people were still hesitant to expand. Even after trying their hand at it, they have wanted to go back to previous models of supplying to traders, in this post pandemic scenario. Not everyone is confident that they will get an influx of regular customers, which is something the middlemen can assure them.
Weakness
51
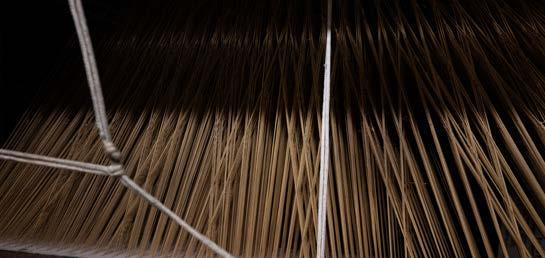
Online market structures have definitely helped artisans to appeal to a pan India audience, but the international market is a huge market that many are still missing the mark on.
52
Opportunity
The scope for innovation in crafts is large. One such area that is already being explored and may prove to be a major opportunity for the craftsmen is combining two crafts, by collaborating with other craftsmen.
INTERNATIONAL MARKET
FUSION OF CRAFTS (CHIKANKARI AND PAITHANI)
Many women in yeola are educated and willing to learn and take on what is given to them. Although, due to house duties and peripheral work in the home, they are able to dedicate little to no time at the loom. The issue of strength and capacity also arises, as women oftentimes cannot handle the physically demanding work of sitting at the loom. However, they have many valuable insights relating to colour, design and even marketing, that can be honed in on with just a little more training and direction.
UNUSED POTENTIAL IN WOMEN

Threat
Powerlooms sell sarees under the name and with traditional motifs and colours of paithani, at astoundingly low prices. These have harboured a huge market, from people who may not be aware of the history, significance and exclusivity that authentic paithanis have.
POWERLOOMS
FUTURE GENERATIONS DISTANCING
THEMSELVES FROM THE CRAFT Future generations want to actively distance themselves from the crafts and get more opportunities in urban areas. This could lead to the craft dying, or not staying within the families, creating the need for outsourcing.
53
MARKET MAY BE DYING IN MAHARASHTRA The paithani market in Maharashtra is not one that welcomes innovation. This is due to the usage of paithani for more traditional, and customary occasions
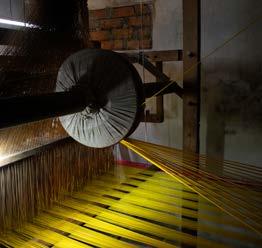
Problems and Focus Areas PROBLEMS IDENTIFIED / PROBABLE SOLUTIONS
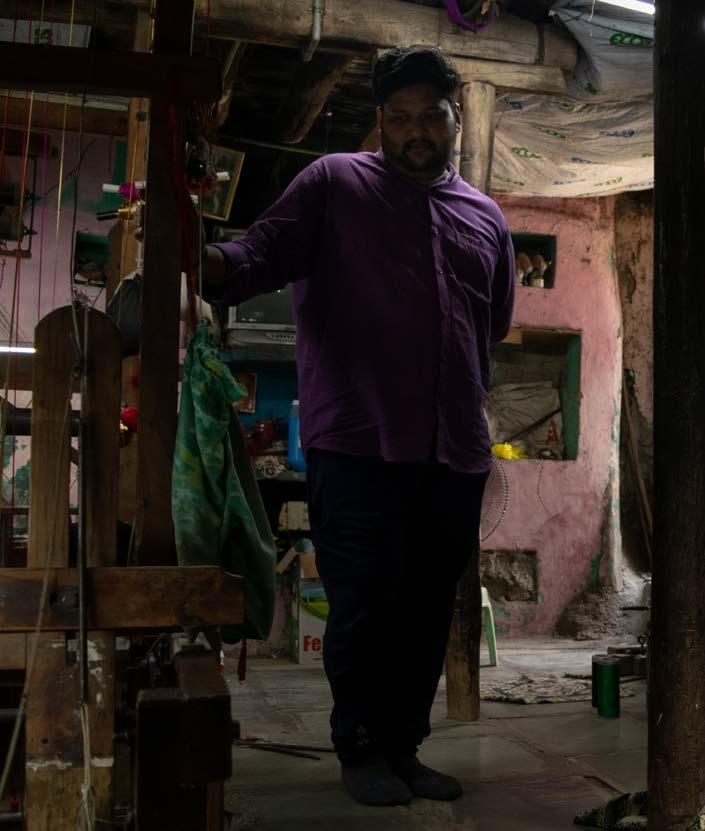
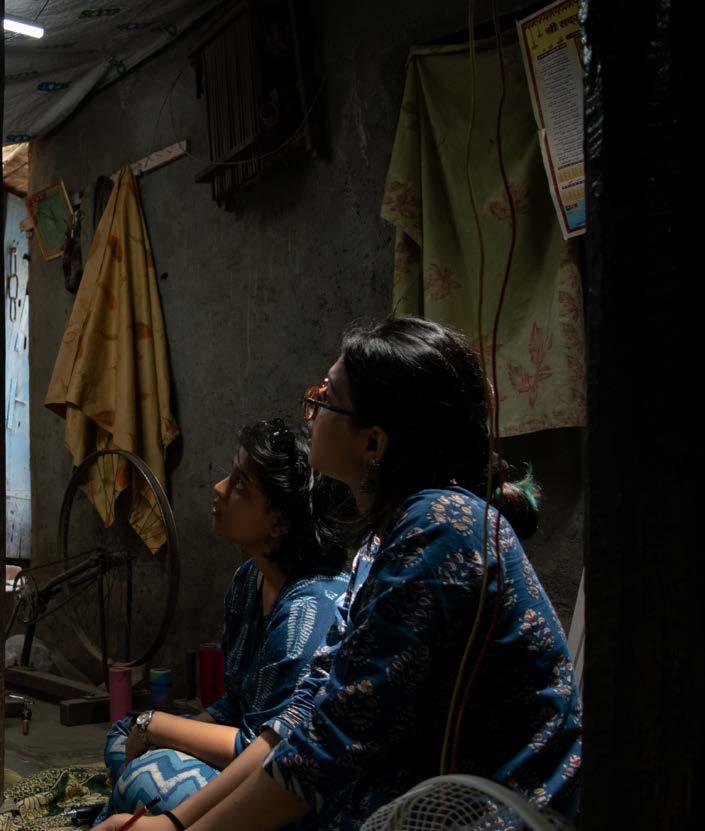
Many women in yeola are educated and willing to learn and take on what is given to them The Indian Government, no doubtedly has come up with various schemes, relating to insurance, education and subsidies for these weavers
The point of government schemes is to uplift those who are the underdogs. Currently, those who need the most help are the most skeptical of the thing that exists to help them A large part of this is the competition that exists between weavers, but also the fact that these people may not know how exactly to access these schemes in the correct way
What is stopping them? housework due to house duties and peripheral work in the home, they are able to dedicate little to no time at the loom. sadly these schemes often remain inaccessible, and echoing around in the same circuits, missing the people who oftentimes need them the most. Training centres In Paithan, there are training centres for women, which have enabled them to gain independence and take control of where their lives are going. It is also beneficial for the craft, and keeing it alive.
56
Women in Yeola are very educated and not from weaving backgrounds. Their education and knowlege from other sectors and backgrounds encourage them to be more Theyproactivearea very unrecognized resource, even when they are working on the looms, they are rarely selected for external workshops, etc
Weaving training centres for Mwomenakegovernment websites as NHDC more accessible to artisans
The NHDC website currently feels cluttered and difficult to comprehend Keeping in mind that its user base are artisans who often come from rural backgrounds with limited resources to understand technology, it is difficult to use. Expanding Scope One can take advantage of the fact that the women are educated in areas other than weaving, and help them apply this knowlege to other areas of paithani such as branding and social media.
most artisans complain that they dont get notifications of govt conducted exhibitions which ideally should be common knowledge to everyone. Restructuring websites like such could help artisans access these websites easily. strength issue of strength also arises, as women oftentimes cannot handle the physically demanding work of sitting at the loom. If they do reach the craftsmen, artisans often feel slighted, due to delay or incompetence in the working processes
potentialUnused in informationschemesGovernmentwomenandisunreachableProblemsProblems AnalysisAnalysis SolutionsSolutions
By coordinatingwith them, we can make sure the functioning of the support systm is running smoothly, and step in when necessary, Encourage the weavers to expand their scope of selling Why aren’t they functioning?
Alot of craftsmen have taken the route of expanding their business through online platforms, such as Instagran abd Whatsapp
For doing this and making sure the weavers have a support system in place, we can take the help of Non Government Organizations or Non Profit Organizations .
Covidcooperativeseffectonsellingandsourcing
Many artisans have already found the avenue of selling their goods online, through sites like Whatsapp and InstagramButmostof them are still afraid of the outcomes of expanding This is dueto unfamiliarity with digital media and also unpredictability Non functioning of SHGs, societies and
ProblemsProblems AnalysisAnalysis SolutionsSolutions
Because of the non functioning of these bodies, many people are not even aware of their existence. Covid has affected everyones business Self help groups and cooperatives are necessary in a craft cluster so the craftsmen are able to uplift each other and maximise their potential.
The lack of cooperatives is clear since many poor weavers are not able to get themselves out of their poverty cycle. Getting thesebodies up and running once again is not an easy task.
Take the help of NGOs and Non Profit Organizations
57
Many of the SHGs and cooperatives in the area havefailed to function properly because of internal disputes
The constant failure to provide a stable operation for the support of the weavers has wornthe community down. Even those who used to be a part of such initiatives are now sceptical of them.
For the weavers who are already comfortable with online media, introducing them to even more online platforms could be helpful, such as Etsy.
Providing education and information about how to navigate the world of online selling and social media might take away some of the fear and uncertainty. We may also help them make their branding stronger so they can establish a strong online presence as individuals but some are still hesitant to branch out due to fears of inconsistent orders or even a lack of orders
58
Encourage education adjacent to craft Encourage the feeling of exclusivity in each weavers craft Parents’ Views Even the parents wanted the kids to first complete their formal education and then decide for themselves. The big traders have made names for themselves, but the reality of the situation is that even they source many of their products by giving orders to these smaller weaving families. we can encourage the customer to buy exclusive sarees which won't be available with anyone else. This not only gives the customer a sense of pride but also makes the weaver confident in his craft and encourages sustainable fashion which runs on order basis.
ProblemsProblems AnalysisAnalysis SolutionsSolutions
Most families we interacted with made it clear that none of the young kids were interested in making a career in the weaving Tsectorhereis no way to know which sari has been made by which craftsperson This is a good sign for the academic growth of children. the weaving families will later have to depend on external help to work the Thisloomwilllead to an increase the production costs. Academic growth of the children should absolutely be encouraged But this does not mean they need to be estranged from the craft. They may use their new areas of expertise, to develop the craft in another avenue. They may even be involved and exposed to information and workshops which make them aware of how other fields of academia may be adjacent to the craft and thus helpful for them.
Even products sold at government emporiums do not have any identifying factor that would indicate who has made andit, increase the factor of pride, for the artisans making these saris. Kids want to leave the craft No recognition
59
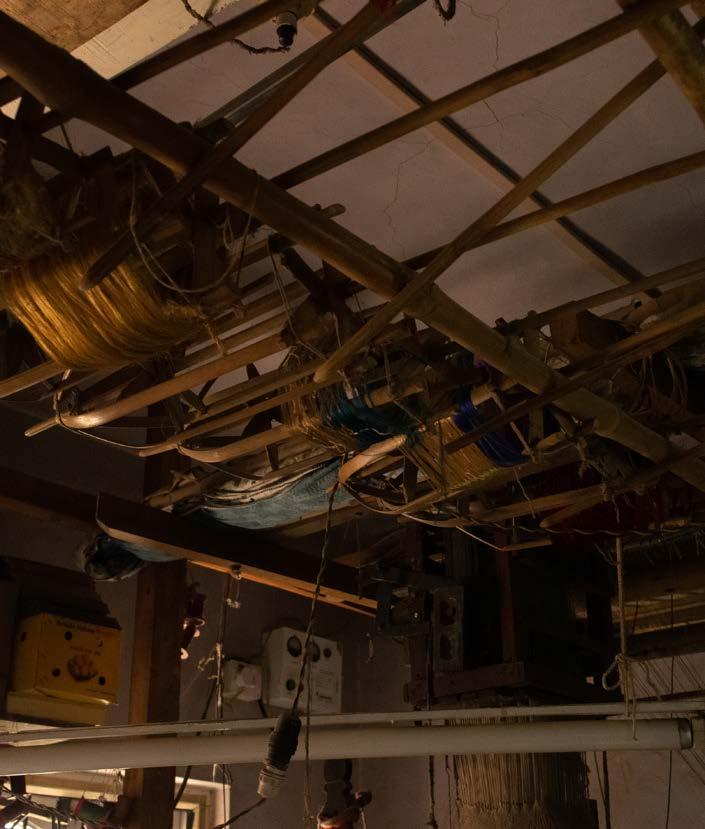
,
Patil Vaishali, Study of Informal Sector (Street Vendors) in Central Market Area of Yeola, Maharashtra (India) and their Integration in Market Architecture, International Journal of Applied Engineering Research, ISSN 0973-4562 Volume 14, Number 13 (2019) Bhatia Reena and Desai Deepti, SUSTAINING THE TRADITIONAL PAITHANI SAREE WEAVING OF MAHARASHTRA, INDIA, International Conference on Innovative Trends in Multidisciplinary Academic Research, October 20-21, 2014 N. N. Mahapatra, Sarees of India, Woodhead Pub, India, Year: 2016, p123-
2022yeolas-weavers-now-want-to-move-on/article24724650.ecehttps://www.thehindu.com/society/history-and-culture/they-made-saris-for-devdas-but-p137,accessedon14thJune
https://timesofindia.indiatimes.com/city/nashik/after-2-tough-pandemic-years-yeolaspaithani-saree-sales-flourishing-again/articleshow/92240227.cms accessed on 13th June https://www.craftsvilla.com/blog/paithani-saree-the-story-of-the-queen-of-heirlooms/2022 accessed on 13th June 2022
,
61 Bibliography