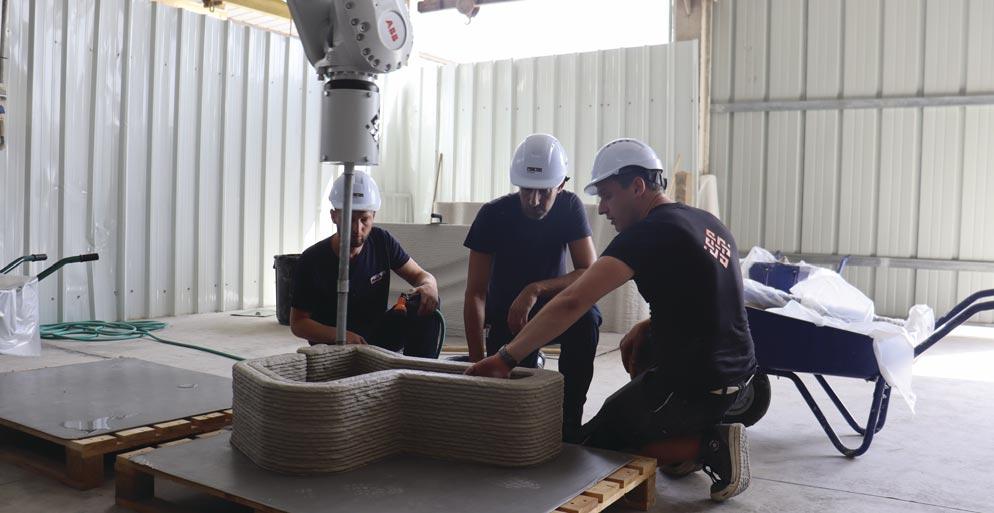
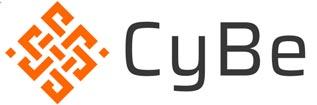

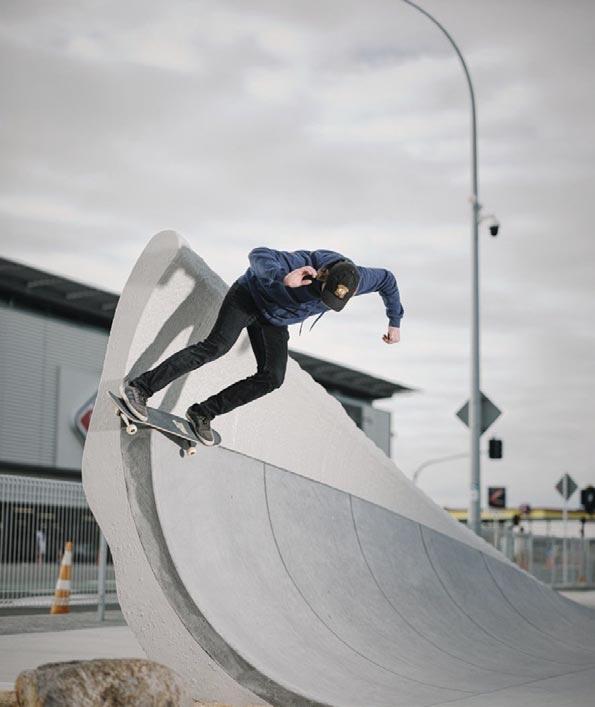
CYBE CONSTRUCTION
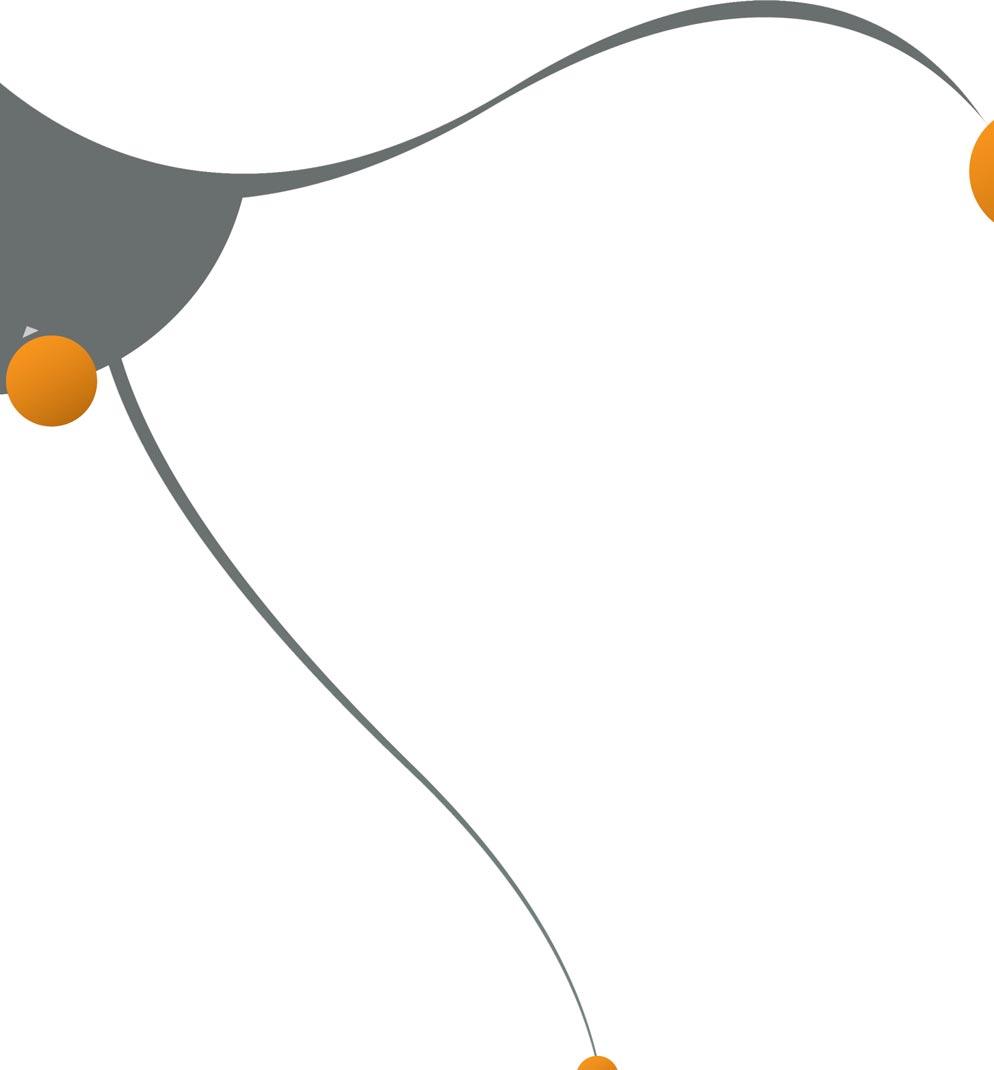
CyBe Construction, founded 11 years ago in 2013 as the world’s first commercial 3D concrete printing technology provider in building. Since then, the company has continued to develop and leverage its technology to create more affordable construction solutions. Founder & CEO Berry Hendriks explained how this was possible, during an in-depth interview with Inside Sustainability. Report by Imogen Ward.
Inspired to make a difference within the industry, Founder & CEO Berry Hendriks established CyBe Construction in the Netherlands.
“While working as a real estate developer within our family-owned construction company back in 2009 and 2010, I was inspired by the 3D BIM models we were working with,” said Mr Hendriks. “From there, I went looking for construction automation and discovered bricklaying robots and video simulations for small-scale robotics concrete laying.
“The concept itself seemed quite straightforward: material would be needed, alongside hardware and software capable of controlling the process. And with my previous experience in constructing buildings, I felt confident I could create such a machine. So, I quit my job, and the rest is history.”
Backed by Mr Hendriks’ determination and a century of construction background from the family-owned construction company, CyBe was founded in 2013. During that first year, the company creatives searched for the perfect building materials to work alongside its 3D printing process.
“The material determined how quickly we could print, so we needed to find a solution that was right for our needs, that could compete with limestone bricks,” explained Mr. Hendriks. “We had so many different
companies tell us it couldn’t be done, before we came across KORODUR and its extremely fast setting material.”
The product of KORODUR relies on a different type of binder, which is more compatible with the 3D printing process. It is also a non-shrinkage material, which provides a stronger defence against cracks. Additionally, the binding solution used in CyBe Mortar is more environmentally friendly, resulting in a 32% reduction in carbon emissions compared to alternatives on the market.
Once CyBe had secured its building material, the company set to work developing the software and hardware needed to turn Mr. Hendriks’ vision into a reality.
“Once we had the material, we knew we could build the system around it, and quickly developed a mix-pump system that could process CyBe Mortar,” commented Mr. Hendriks. “In 2013, we achieved our first successful print runs.”
Two years later, the company was already demonstrating its capabilities by printing benches and manholes. From there, printing advanced to produce CyBe’s first retaining wall, and then eventually, its first building, the R&Drone laboratory in Dubai. Each milestone became bigger and bolder as the company continued to develop its techniques to ensure high-quality, cost-efficient builds.
In late 2017, CyBe went on to sell its first printer, which was delivered in 2018 to a Japanese construction company, soaring into a whole new area of the market.
Today, CyBe has a portfolio of over four printers, including both large, stationary printers, found in the G-line, and smaller, often mobile units, found in the R-line. This variety enables projects of different sizes and requirements.
The CyBe R is the entry-level model perfect for precast production, which can produce concrete in lengths of up to 2.65m and a width of 3.2m.
The CyBe RT features a robotic arm on a stationary track. Starting at a length of 5m, the track can be extended with 1m plates to increase the robot’s capabilities. Another option within the portfolio, the CyBe RC, is the company’s mobile solution. With preinstalled rubber tracks and hydraulic feet for stabilisation and height adjustment,
the RC can adapt to its environment to provide the best quality construction on- or off-site.
Finally, the CyBe GR relies on an impressive gantry to print large structures and is the most cost-effective system for constructing modular, prefabricated multi-unit buildings.
“We partnered with ABB for all our robotics systems, and with the support of that company, we were able to develop a standardised user interface and software,” explained Mr Hendriks. “We wanted to make sure the user experience would remain the same, no matter what system our customers were using.
“Another huge benefit of ABB is its global presence. The company has multiple factories across the globe and mechanics in every country. So, if a client ever has a problem with one of our machines, no matter where it is based, ABB can have a someone there to help as soon as possible.”
With the cost of living on the rise and affordable housing hard to find, CyBe undertook the mission to create efficient products that could make a difference.
“In the Netherlands, like in many other countries, there is a housing shortage,” said Mr Hendriks. “And with the implementation of environmental legislation some years ago, the industry is somewhat stuck with using conventional on-site building methods. Despite that, we are very impact driven, and we are focused on developing different housing types for the various markets, built either on-site or off-site.”
“With local knowledge, experience and understanding we, together with partners, have worked hard to achieve a square foot building price for our methods that is better than average in comparison to conventional construction. This is just one
of the ways we are working and learning with partners to ensure affordable housing is more readily available.”
The company has also designed its printers with precision and speed in mind to ensure they are as efficient as possible. Waste mitigation is another important element of CyBe’s design calculations.
“A standard concrete wall is solid and often 30cm thick,” said Mr Hendriks. “Using CyBe Mortar, our printers can produce multiple layers measuring 4cm, ultimately saving on the amount of material used. We are also now trying to reduce the width even further – by 1-2cm – to minimise our material usage and related waste and emissions.”
Of course, the journey to now did not come without its trials. Over the years, CyBe has continued to adapt and enhance its printers to ensure they continue to meet the needs of its customers whilst retaining the high performance they are renowned for.
“With every completed project, we discovered new ways to improve our systems,” said Mr Hendriks. “Our first project in Dubai in 2016 and 2017 exposed us to the challenge of high and continually fluctuating temperatures. Having previously only manufactured in the Netherlands, we were used to a much different climate.”
“Dubai’s temperatures affected our setting times and the amount of water we needed to use during production. We soon realised that heating and cooling units were needed to maintain a consistent water temperature of around 25 degrees.”
As the company looks forward, it intends to continue improving its innovative solutions.
Having already developed and patented printing and building off-site via its Gantry Robot model, CyBe is now focused on constructing a multi-story building using this printer. In doing so, CyBe intends to further enhance the credibility of its systems.
Leveraging its 10 years in the industry, CyBe learned to shift with the market’s changing challenges. The company’s priority is now on creating the new generation of building - which will be the foundation of a new global industry.
“I have a vision for this company, and it's one that has remained strong as CyBe has continued to grow,” said Mr Hendriks, in conclusion. “Not only can we help improve the affordability of housing and give people a home, but, thanks to the true versatility of our systems, we can print anything we put our minds to. I am incredibly proud of the legacy we have built with our team and partners.” n
Even applications like skateparks can be printed