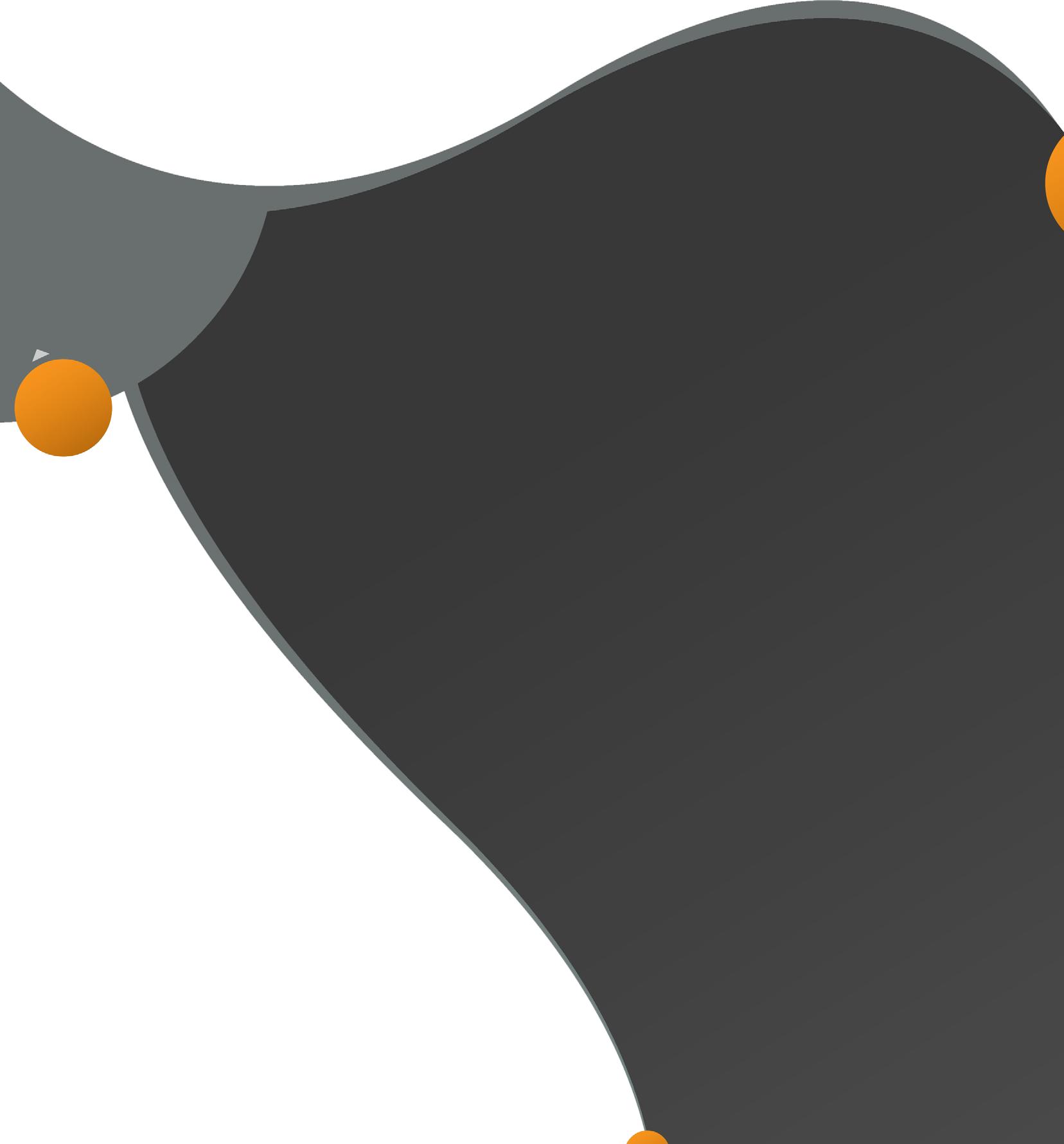
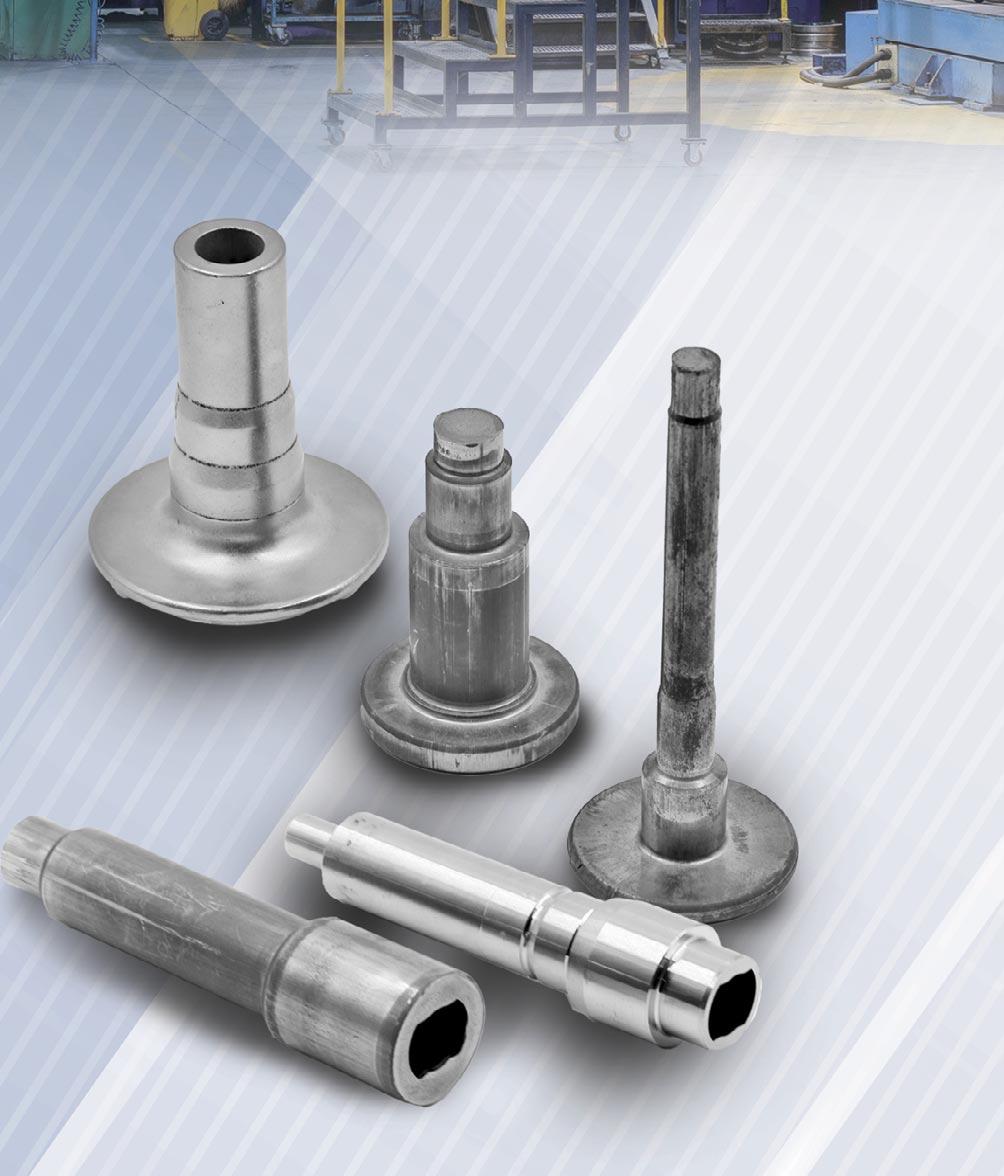
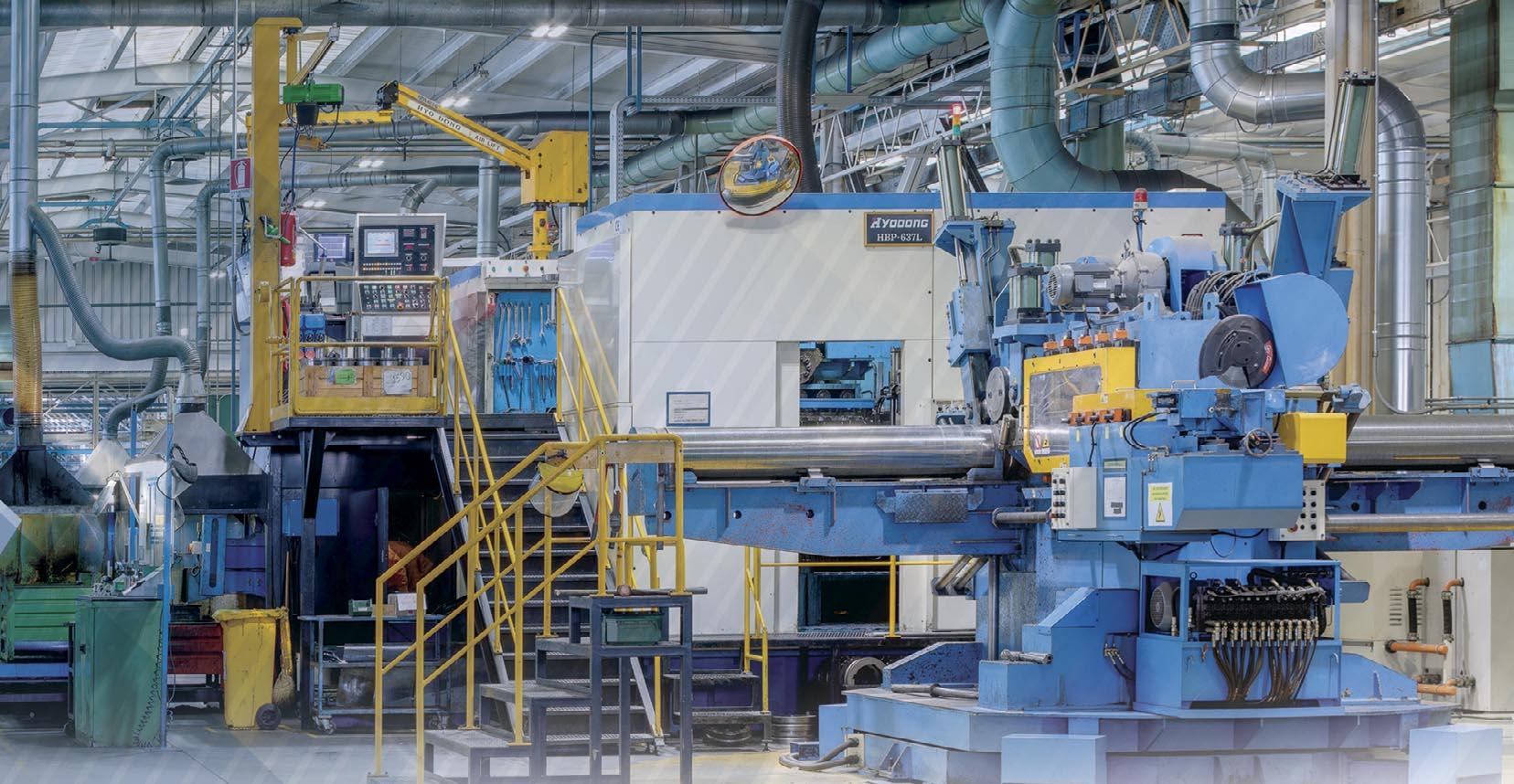

As the automotive industry continues to transition away from the combustion engine and focuses on everything electric, Fontanafredda Cold Forging (FCF) has been among the first companies to face the inevitable challenges of change.
Speaking to Andy Probert, Managing Director Zeno Rigato recounts the decisions and why the ambitious Italian manufacturer is firmly looking up.
For Italy’s Fontanafredda Cold Forging (FCF), it must have been a moment similar to when steam was replaced by electricity in the 1900s.
In 2016, the automotive sector was coming to grips with a new revolution – with the combustion engine transitioning to fully electric and hybrid. For FCF, it signalled a third significant and telling turning point in its 40-year history.
Founded in 1981, FCF specialised in the cold forging of metal components for spark plugs before this was delocalised at the end of the 1990s to cheaper economies in Asia and Africa.
Cold forging is a displacement metal shaping and manufacturing process in which a metal – typically steel, aluminium, copper or titanium – is shaped. Starting from wire coils of diameter between 15 and 38mm, material is forced between a matrix and a punch to produce parts with a defined geometric form. These technologies enable high production of finished parts with better mechanical properties and negligible swarf.
Given the company’s excellent know-how in cold forming, FCF shifted its emphasis on producing highly complex components, such as advanced form parts, and developed its own niche in the European automotive industry.
While this business flourished, the electric revolution was rapidly moving into the industry’s rear mirror. FCF again shifted its business dynamics in anticipation of the industry’s exit from combustion engines.
“Only five years ago, 80% of our products were related to com bustion engines,” reflected Managing Director Zeno Rigato. “Today, only 20% of our turnover is linked to this product family and will drop to below 10% in the next five years.”
FCF has completely changed its product mix, focusing now on components related to steering, the braking system and chassis without having to reduce its 90-strong personnel.
It has also invested €2.6 million in new tools and €4 million in new machinery at its headquarters in Fontanafredda, an hour from Venice, to expand its offering and create opportunities to access markets and customers.
Innovation in the automotive sector has also led to the increasing use of aluminium alloys for various car parts to help reduce its overall weight.
With its gained metallurgical knowledge and in responding to multiple manufacturers’ requests, FCF has further invested in R&D to test and verify the best choices of aluminium alloys. This will help in terms of effectiveness for lightening requirements, corrosion resistance, mechanical characteristics, and improve deformability, enabling greater use of cold forging.
“In addition to recyclability, these activities will help guarantee a lower consumption of natural resources and make its use eco nomically sustainable,” Mr Rigato emphasised.
In 2021, FCF began serial production of three highly complex components for the steering in aluminium, having accepted the challenge of achieving the levels posed by one of its key clients, a leading Japanese company.
Mr Rigato commented: “By 2024, 10% of our turnover will be for aluminium products, and we are continuing to study new impor tant projects to increase this share further.”
To achieve these objectives, FCF is implementing a corporate digitalisation program with the installation of a Manufacturing Execution System (MES), which will primarily manage and control the company’s production process from start to finish.
This will help extract valuable information to integrate into the production execution and improve performance in terms of qualit y and cost. The project will be completed by the end of 2022. FCF is also looking to expand its range of cold-forged products following the acquisition of a new, larger press to produce components up to 1.2kg in weight.
Mr Rigato said the company plans to match these investments, by increasing its workforce from 90 to 100 in the next three years to aid the mass production of products it has developed in the last two years;
“After falling from €17 million turnover in 2019 to €13.6 million in 2020 due to the pandemic, we have begun to rise again. We hope to achieve €17.5 million in 2022 and, with contracts already acquired, reach €23 million by 2025,” he reassured.
The entire process of study, design and development of FCF’s molds continues to be carried out internally thanks to an R&D unit of designers, mold specialists and operational technicians Mr Rigato described as “the flagship of our company”.
With years of experience in cold forging, its R&D unit can inter vene in co-design with a customer from the earliest stages of designing a new product, with immediate advantages.
“This methodology allows us to reduce study times, increase product quality, and reduce development and production times by exploiting the advantages of plastic deformation technology.”
The R&D team uses two simulation softwares – Simufact and Coldform – to develop the plastic deformation process to verify the product’s feasibility and optimise its configuration.
Mr Rigato confirmed that FCF has a business plan in place, starting from 2022, to invest an additional €3.5 million in creating a new fin ishing department for the production of steering shafts. This will be ready in 2023 and help FCF reach turnover potential of €23 million.
When considering the many challenges FCF faces, Mr Rigato offered a surprising answer. “Undoubtedly, people are central to a company’s success. At FCF, people can find passion, wellness, trust, growth, evolution and fun. Because it is people who make the difference and only with them, especially in critical moments, is it possible to achieve extraordinary results.”
He added: “We want to become ambassadors of our technology, cold forging, and the significant benefits it can bring in carbon footprint reduction compared to hot forging or machining.
“Just think – a finished part with a weight of 1kg obtained by cold forming instead of bar turning can reduce processing waste by up to 70%. To obtain these results, we offer customers our collabo ration, and in the product conception phase so that it is adaptable to our technology.”
Mr Rigato added: “At a time when market spaces are shrinking due to technological evolution towards electric, we aim to stay one step ahead of the competition. We set ourselves apart by creating what may seem impossible today.”
FCF is keenly adopting socially responsible behaviour, moni toring and responding to all stakeholders’ economic, environmental and social expectations, and operating in compliance with inter nationally accepted guidelines.
Underpinning this, the company launched a training program for all its managers to promote ESG issues. FCF plans to produce its first sustainability report within the next three years.
Expanding on its relations with suppliers and clients, he said: “We believe that creating a climate of trust is the most authentic engine of any long-term relationship. When we trust each other, it is easier to solve problems.
“To create this climate, transparency in relationships is important; opening up and allowing projects to be monitored and con stantly communicating what we are doing.”
Mr Rigato concluded: “FCF continues to be optimistic. The automotive world and beyond is profoundly changing, under mining all the certainties we were used to in past years. But we are equally convinced FCF has, among its women and men, the creativity and passion needed to ride the wave.” n