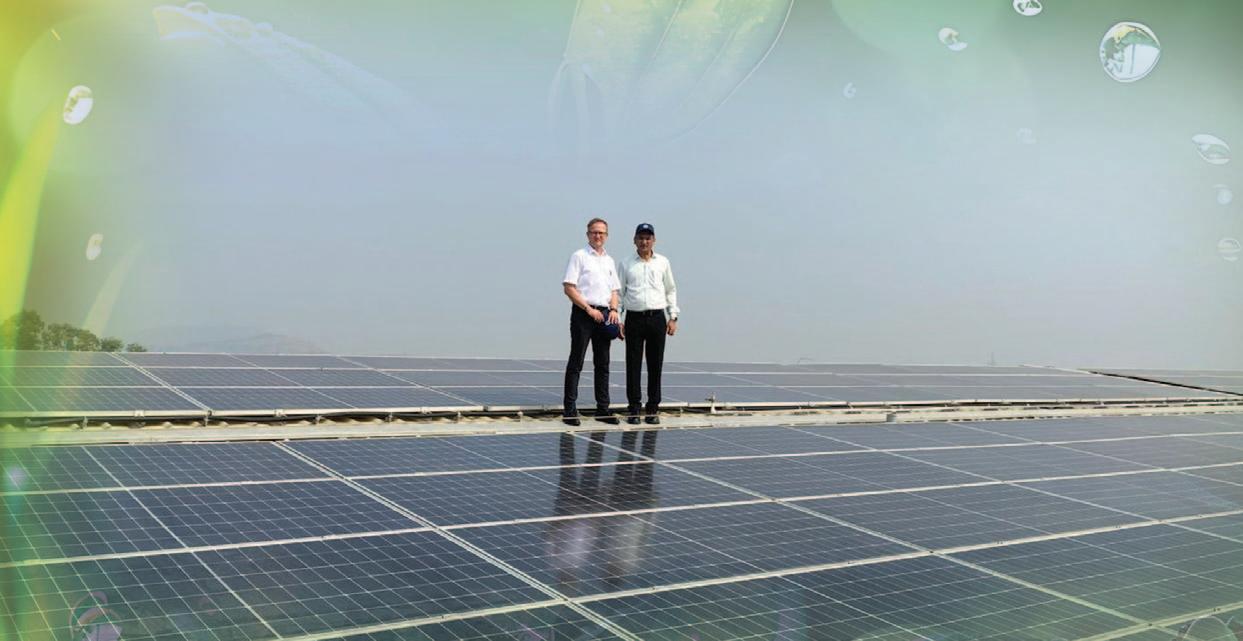

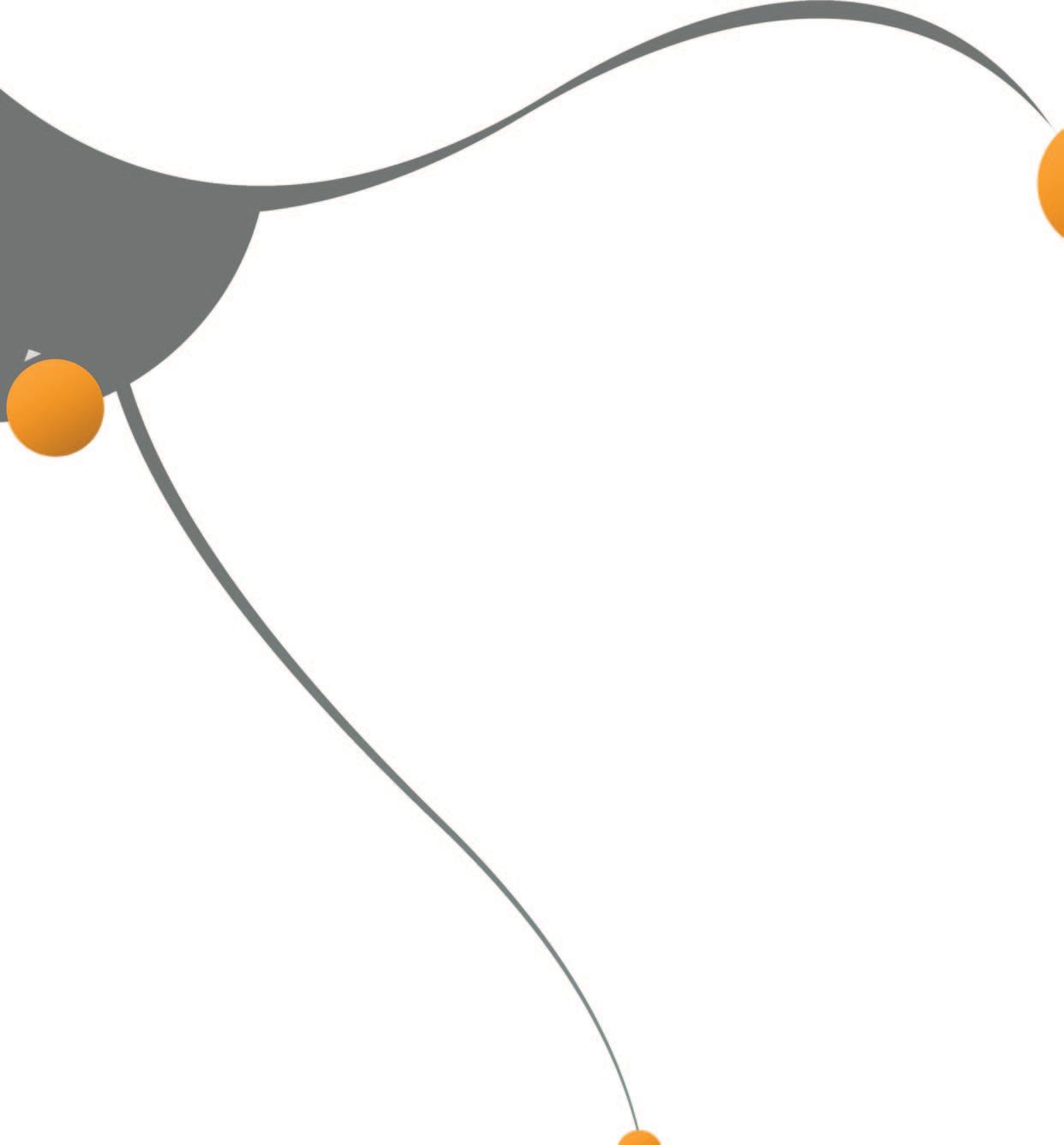
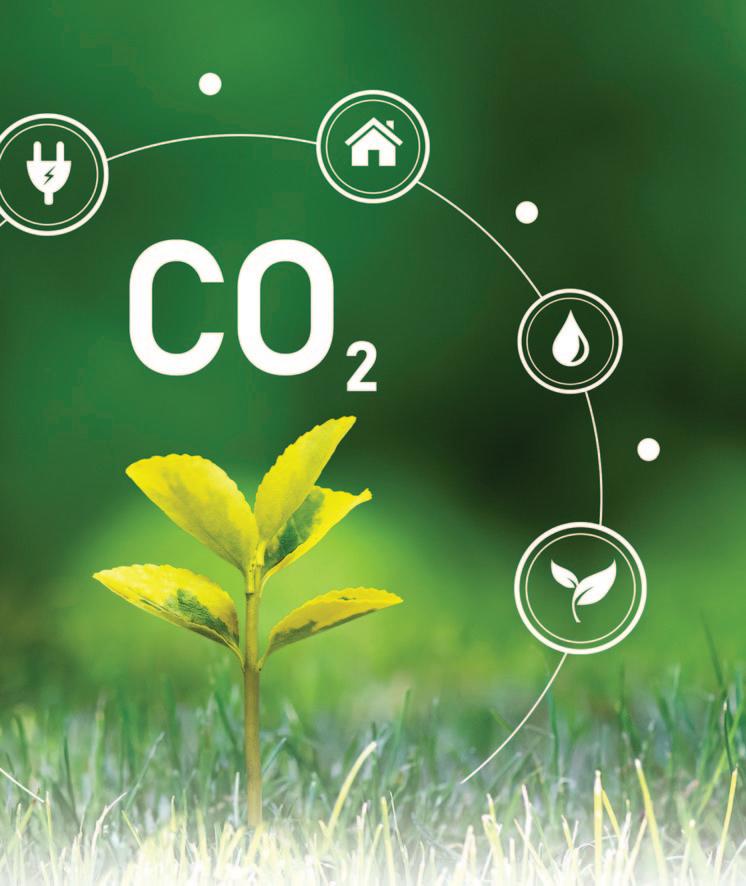
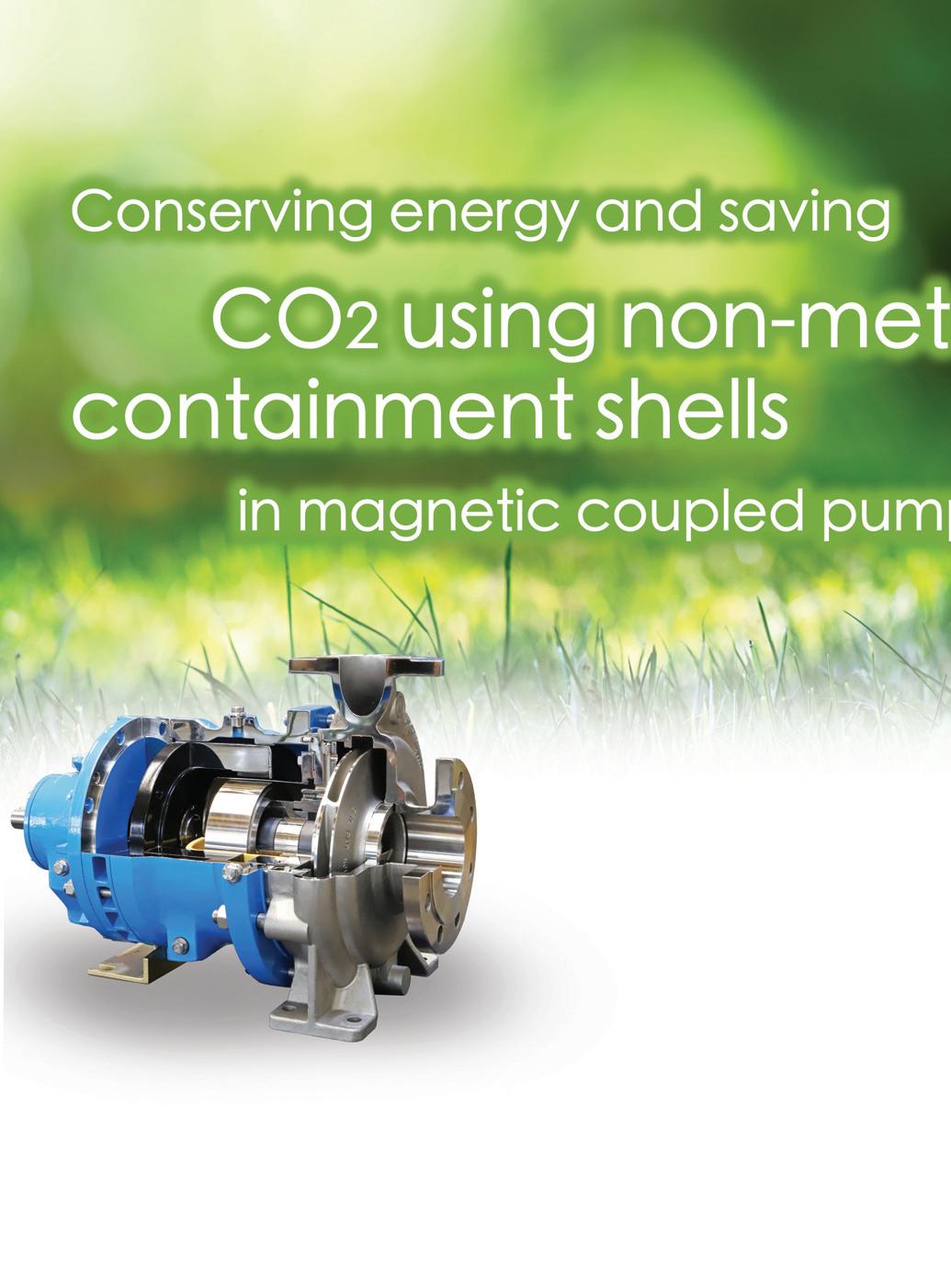
Rising energy costs and a growing awareness of limiting the CO 2 impact of production lead to increasing concern in many sectors on how to reduce energy consumption. Report by Klaus Union.
Pumps and their drives are one of the biggest energy consumers, both directly (drive power consumption) as well as indirectly (other utility consumptions and maintenance requirements).
Currently, the first steps to securing a more energy-efficient fluid handling mean putting increasing importance on the energy efficiency of the pump drivers. Higher and higher nominal efficiencies are required for electric motors to meet curren t and future regulations, not considering the resource requirements due to the need for more copper.
For example, a typical 45kW 2-pole motor has the minimum efficiency of 92.9% (IE2), 94.0% (IE3) or 95.0% (IE4). Assuming an optimally loaded pump and motor
combination, operating close to the rated power difference, and operating 24/7 all year, then the difference between an IE2 and an IE3 motor would be approximately. 4,965kWh. The difference between an IE3 and an IE4 motor would be about 4,414kWh.
The 2021 values for CO 2 equivalent data on the EAA website give an average for all 27 European Member states of 275g CO 2 e/kWh. Some heavily industrialised nations have considerably higher values (Germany 402g CO 2 e/kWh, Netherlands 418g CO 2 e/kWh), while others are considerably lower (France 67g CO 2 e/kWh or Sweden with only 9g CO 2 e/kWh).
The average electricity price for nonhousehold consumers in the EU in the second half of 2022 was specified at
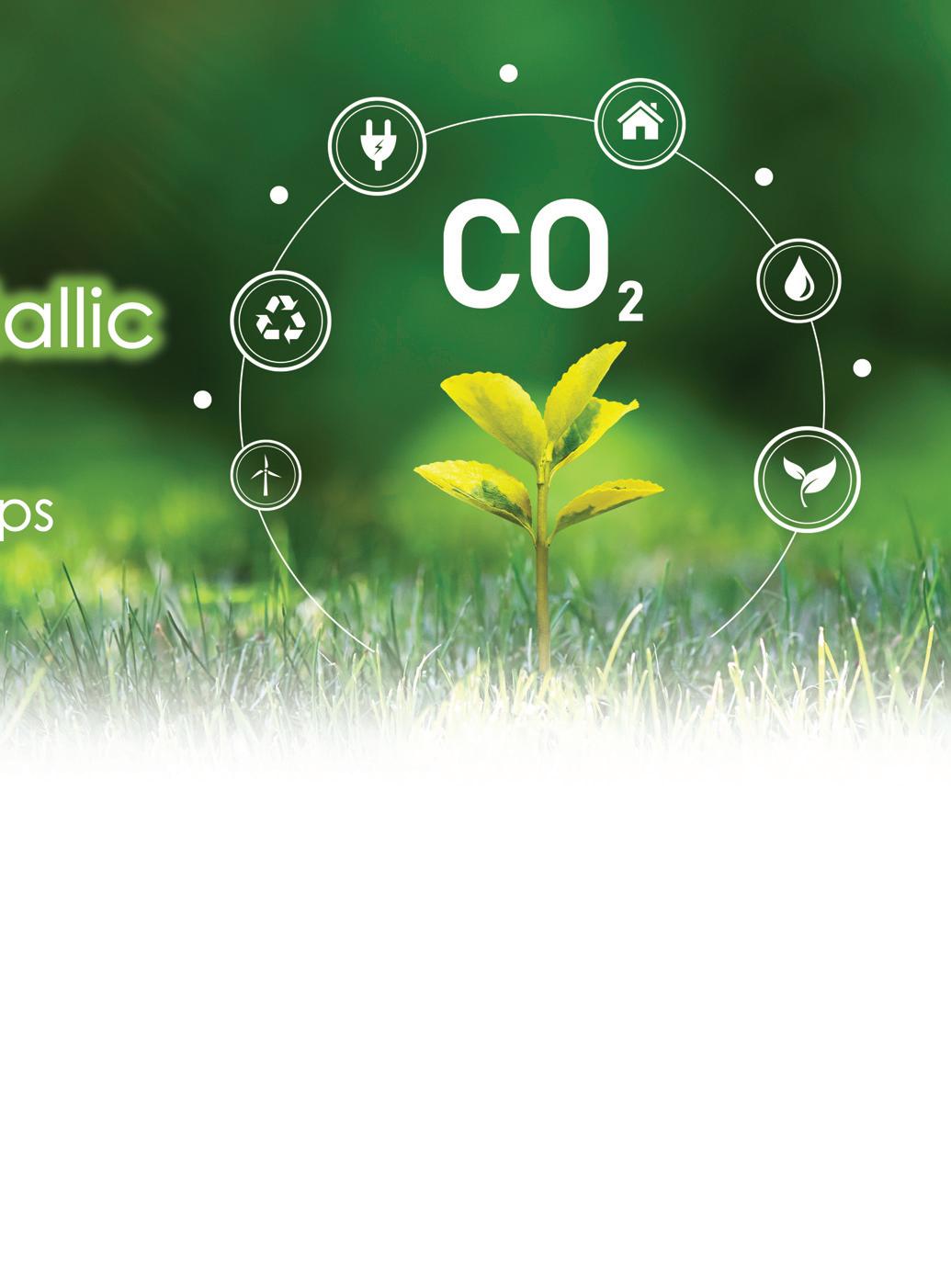
€0.21/kWh. These numbers mean, a 45kW motor operating all year around at peak power demand costs from €89,108.67 (IE2) to €87,138.87 (IE4).
Taking direct action
Companies have spent considerable time and money to upgrade the installed base of electrical motors. This ignores a more impactful way of upgrading the energy efficiency of their sealless pumps: containment technology.
By using non-metallic containment shells made from heavy-duty industrial ceramics, the efficiency of sealless pumps can be increased by 5% to 10% for small and by 10% to 20% for larger hydraulics. That technology has been field proven for
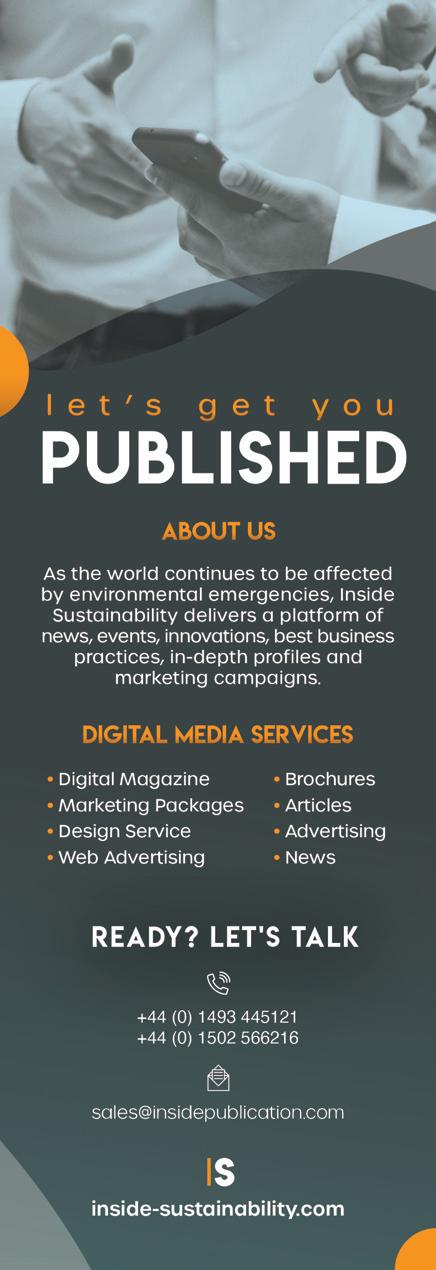
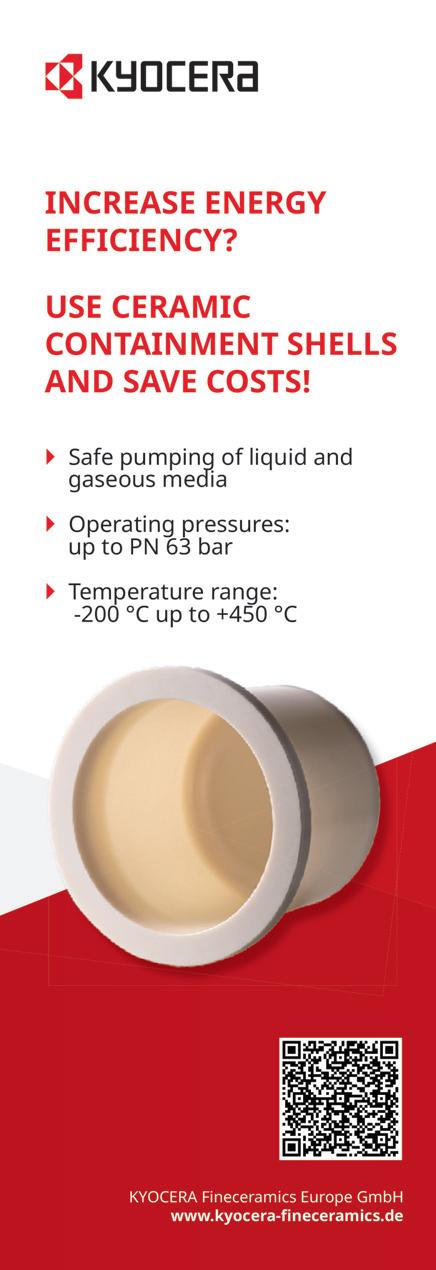

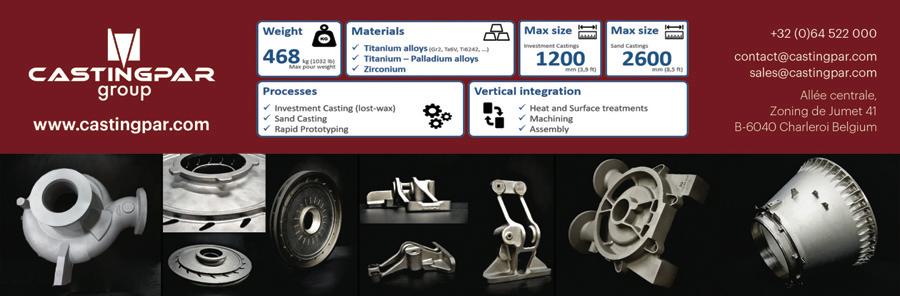
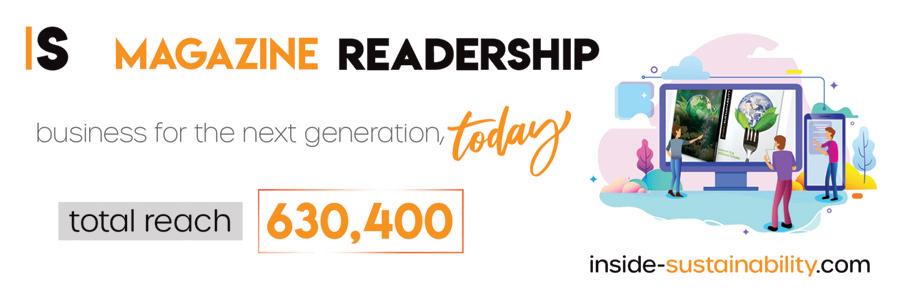
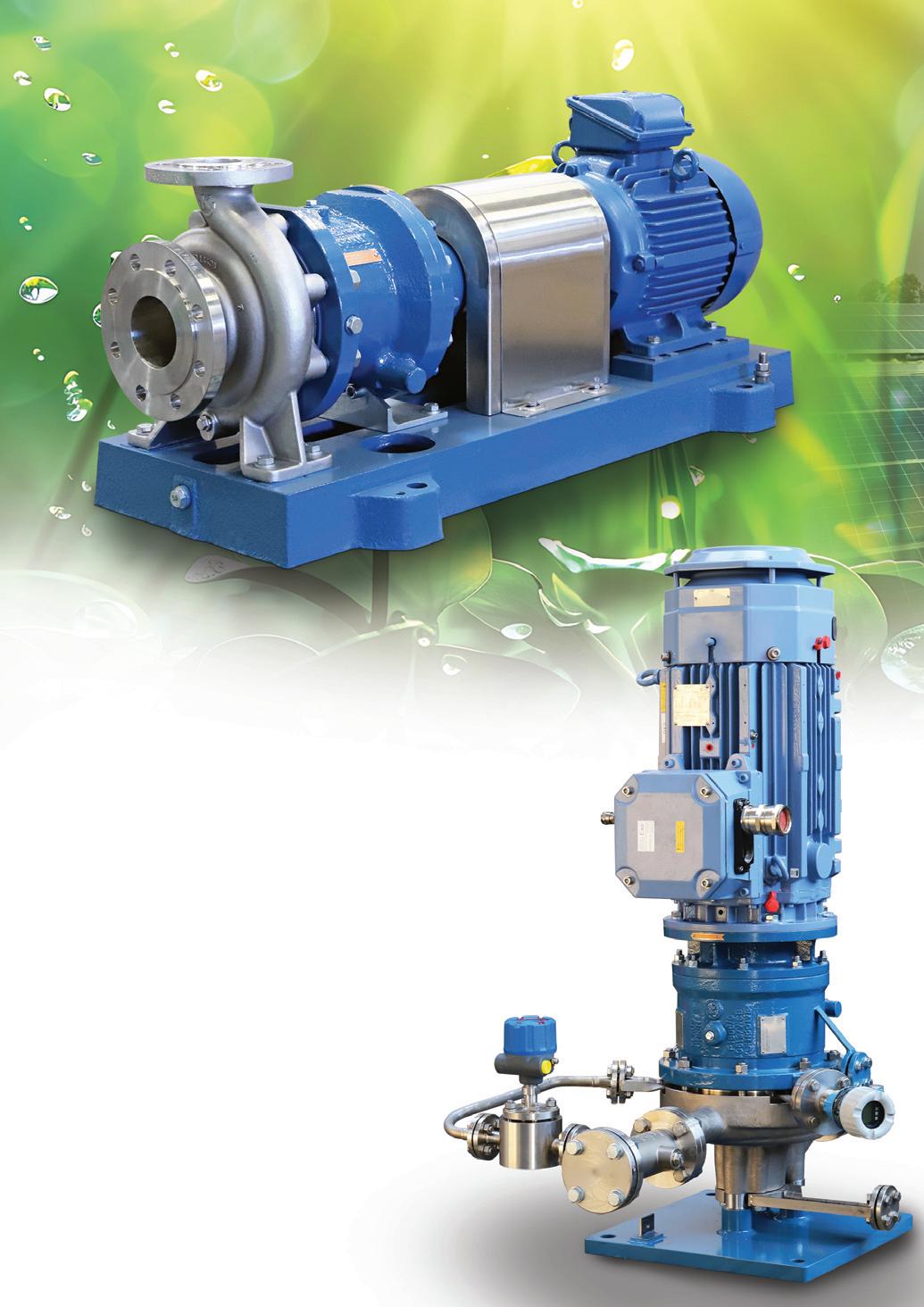
more than 25 years and is in use for the most demanding applications.
As the non-metallic containment shells are not electrically conductive, they transmit the power without generating any eddy current losses. These shells operate loss-free, giving a direct impact on power consumption, allowing the use of smaller, more efficient motors. These features have a direct impact on existing pump installations without requiring any new equipment to be installed.
Looking back at the earlier example, we would not be talking about such minuscule savings but the ability to save 17.7 tons of CO2e per year or €13,554.90 of electricity costs per year. When talking about these numbers, it does not matter that we are using the numbers for an IE4 motor as a base.
Going further
It would be a mistake to limit the applicability of the non-metallic containment shell technology only to those installations already sealless today. Sealless pumps are still a minority of installed pumps, even though they offer a lot more benefits when looking at the overall pump population in any plant or factory in comparison with mechanically sealed pumps.
Mechanical seals have finite operating life –requiring shut down for maintenance when the seals are worn out. There is unavoidable leakage through the seals, whether into the atmosphere (for single-acting seals) or the product (for double-acting seals). Leaks mean a loss of product or product quality and environmental contamination, either by the product or the barrier/quench liquid.
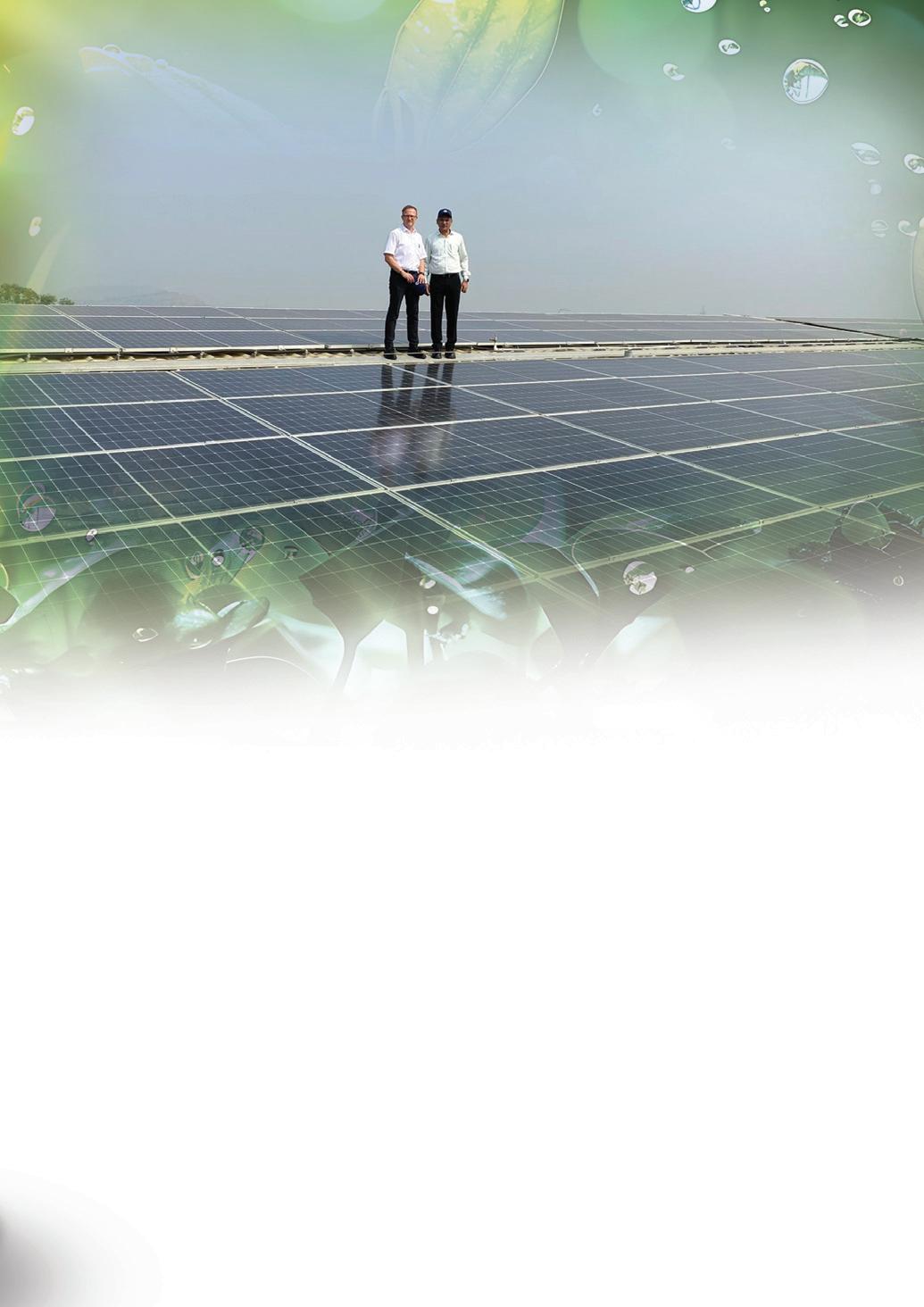
Double-acting and/or quenched seals require additional utilities, such as barrier liquids, steam, nitrogen. or oxygen, requiring energy and supplemental equipment to prepare and supply
One obvious solution to this would be to use sealless pumps (magnetic coupled or canned motor type). Yet these pumps are largely not considered as a solution to these questions because of a few prevalent myths. However, with the developments of technology during the last decades, there are field-proven solutions for the main points of criticism levelled at sealless pumps.
Busting the first myth
Myth one is that sealless pumps are less efficient than mechanically sealed pumps. This is one of the most complex criticisms
to address because pump efficiency has multiple aspects: pump hydraulic efficiency, drive efficiency and the impact of the power transmission.
The myth of hydraulic pump efficiency is the easiest one to dismiss. For most manufacturers, the same hydraulics are used for sealed and sealless designs with no appreciable energy impact.
The veracity of the myth that sealless pump drives are less efficient than mechanical ones depends on the type of sealless pump. A magnetic pump utilises the same standard motors as a mechanically sealed pump, so there is no difference. The electrical efficiency of canned motor pumps depends on the quality of the electrical motor, and thus the manufacturer, as they are not using standard motors.
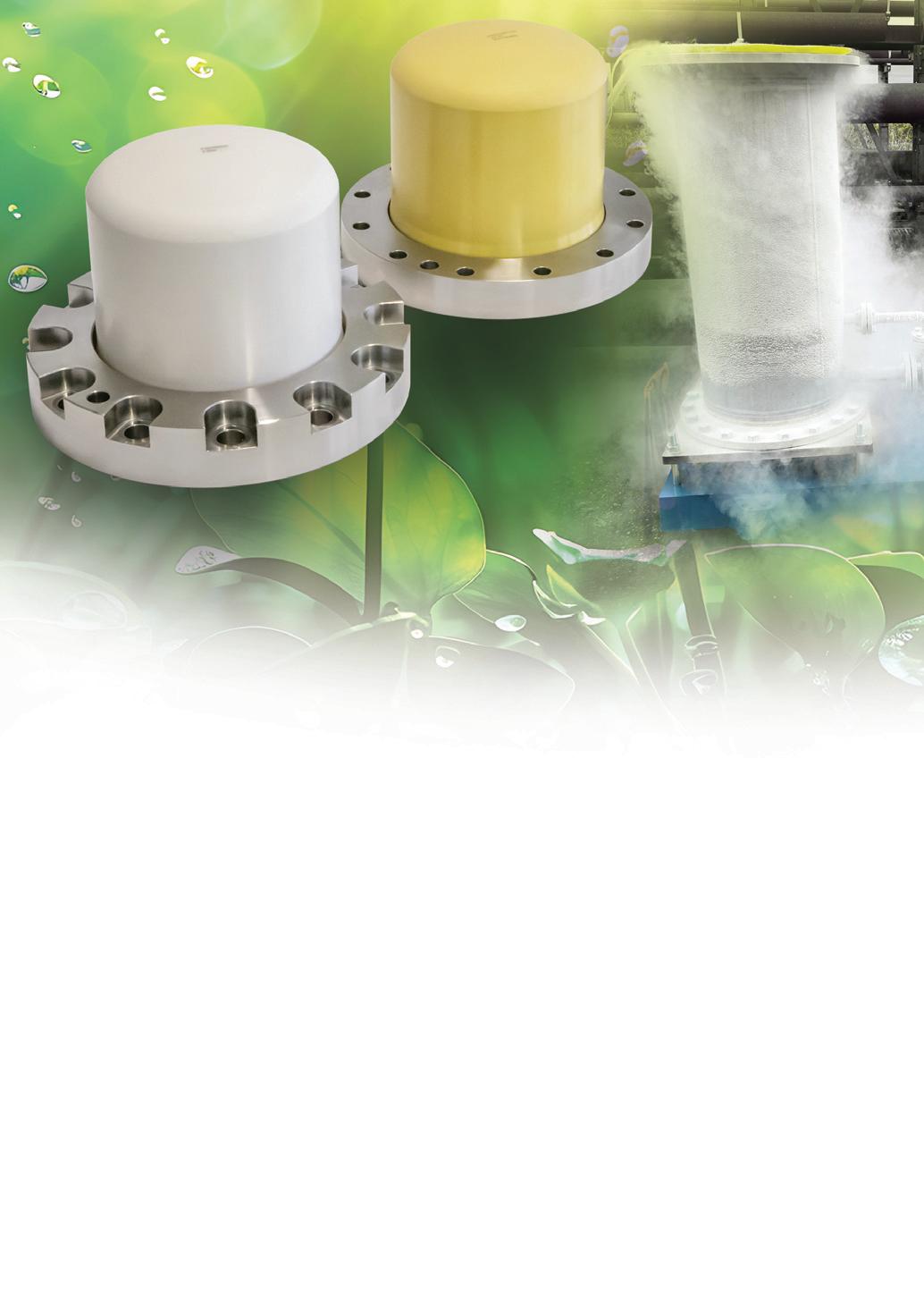
The final aspect of this initial myth refers to the transmission losses due to the metallic containment. Or, in the case of more desperate arguments, the liquid drag of the sealless pumps. Addressing the latter point first: with a carefully controlled liquid drag in the containment area, then the liquid drag can be eliminated for centrifugal pump purposes. Even in the high viscosities that are handled by positive displacement pumps, any liquid gap can be minimised by controlling and adjusting the liquid gap and the pump speed.
Meanwhile the former point has not been true in 25 years, especially for magnetic coupled pumps. Non-metallic containment shells, ideally made from heavy-duty industrial ceramics, allow for a loss-free power transmission. With up-to-date
magnetic drive technologies, powers up to 1MW can be transferred, depending on application and other situations. This no longer puts any practical limit on the use of magnetic couplings, both in terms of size of pumps or applications.
Further inaccurate myths
The myth that sealless pumps have more wear parts than mechanical sealed pumps depends on the design of the pump and customer specifications. A close-coupled magnetic coupled pump, which can be reliably used from very low to very high temperatures (-200°C to +400°C), actually has fewer wear parts than a mechanical sealed pump.
Close-coupled technology places the outer magnet carrier directly on the shaft of a standard electrical motor. In this design, there are fewer wear parts, because it operates without the need for a dynamic
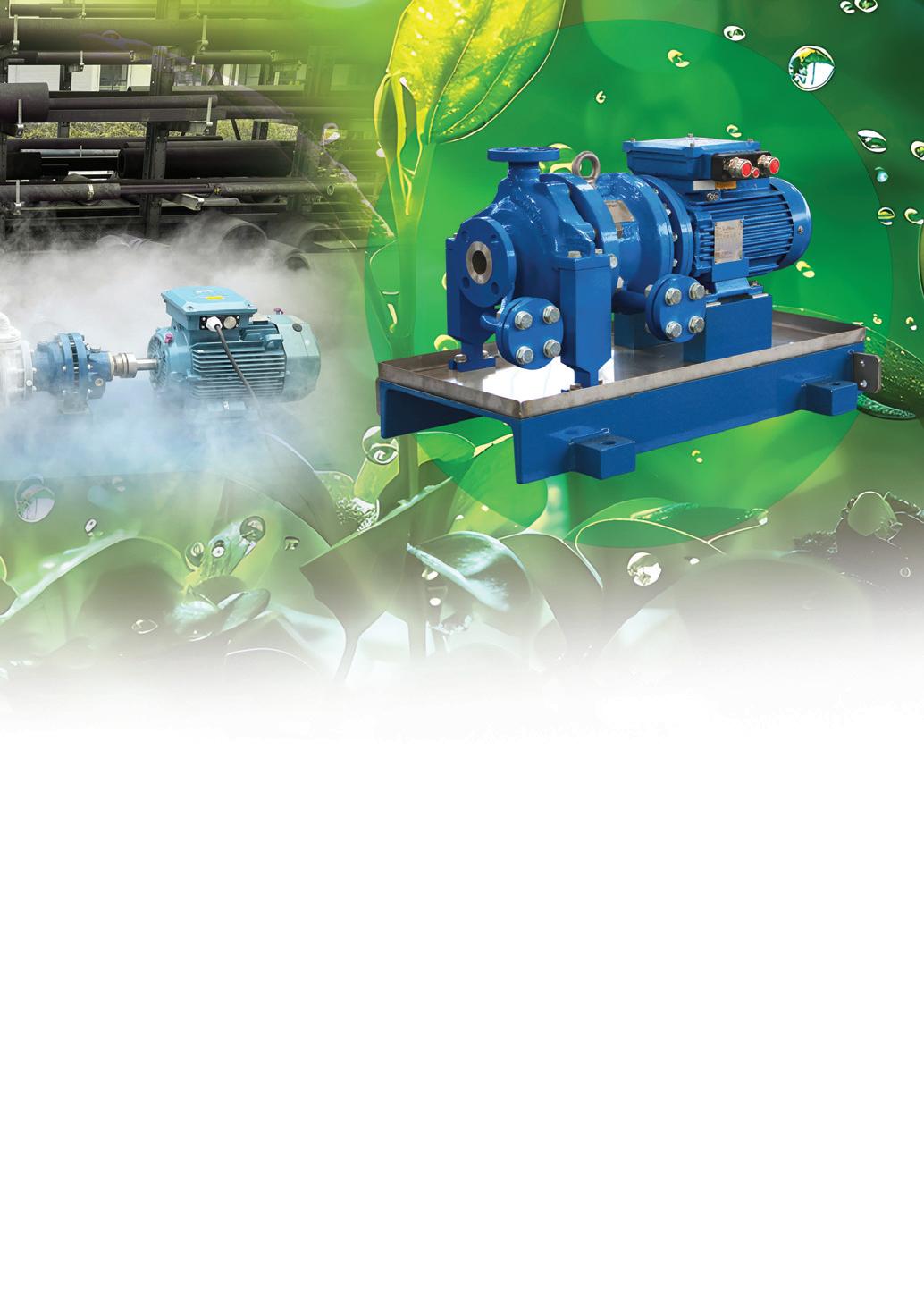
sealing element, a shaft coupling nor an additional bearing carrier. This considerably reduces maintenance requirements and costs. The journal bearings are typically maintenance-free if the pump is properly operated in clean liquids (or the bearings have been selected accordingly).
It used to be true that the journal bearin gs of sealless pumps cannot handle low viscosities. However, the reliable hightechnology materials available today make it possible to handle even liquified gasses with viscosities below 0.1cP without issues, even for the largest pumps. Solutions for high-viscous liquids have existed for decades. Low-viscosity operation is no longer a problem today, even without any utilities required for cooling and/ or flushing.
Open and honest communication with the pump supplier is key to the myth that journal bearings of sealless pumps cannot handle
solids very well. Modern materials allow for extremely solid loads without damage to the journal bearings. Today’s highly wearresistant industrial ceramic containment shells further improve wear resistance. These shells do not wear, even where the traditional dynamic shaft seals come to their endurance limits. Additionally, magnetic filters can allow the handling of liquids containing ferrous solids, such as iron oxides.
Another myth is that sealless pumps are more sensitive to the wrong operation than mechanical sealed pumps. The reality of this claim depends on the type of pump, along with open, honest communication between the customer and manufacturer. Today’s technology utilising non-metallic
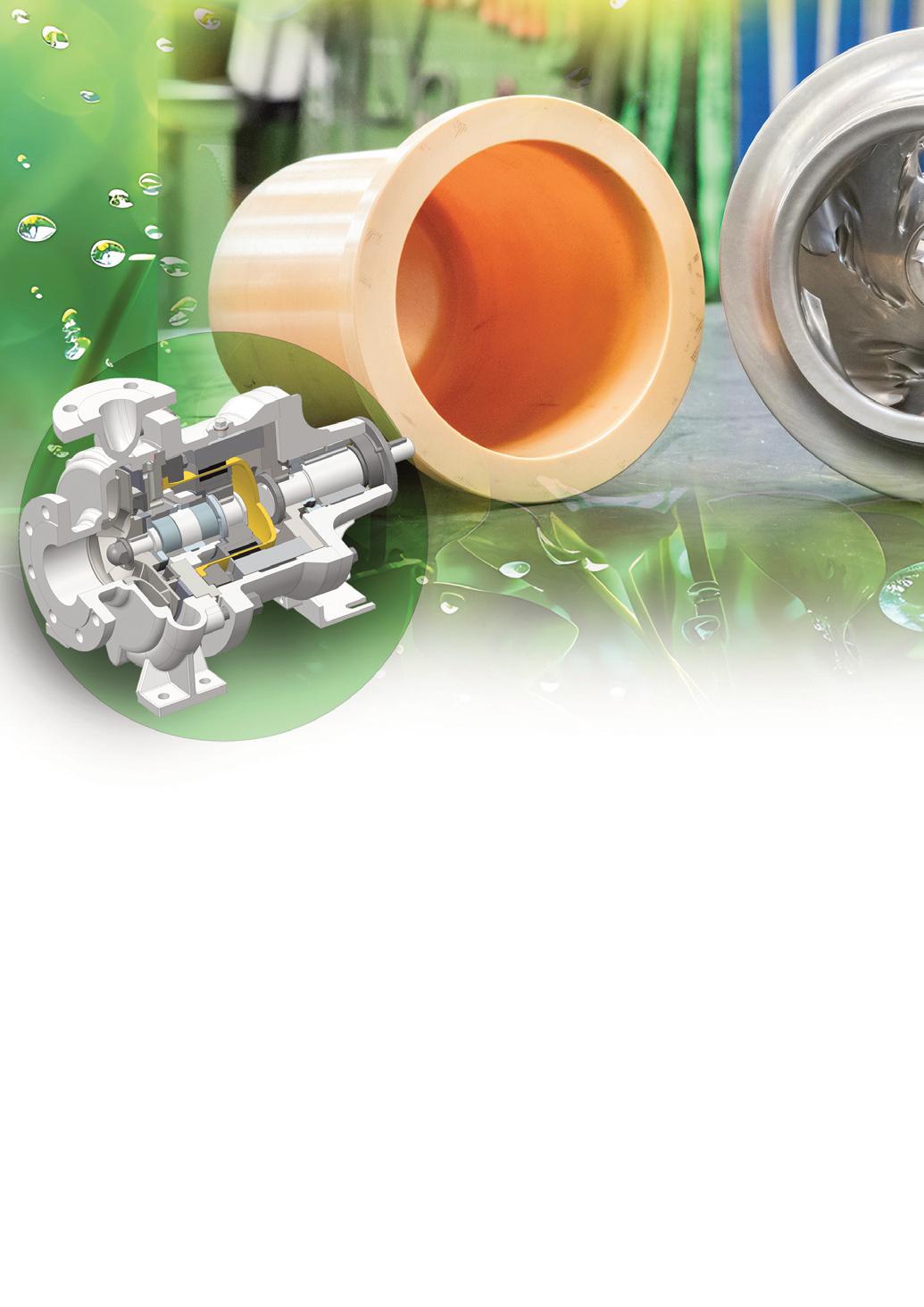
containment shells, allows for journal bearings that can handle operation outside the normal operating range very well.
The shells even allow dry running for a surprisingly long time. Klaus Union verified dry run capability over one hour without adverse effects on bearing performance. Such long-term dry running is not recommended, but customers have inadvertently verified these tests by doing the same in a production environment.
Finally, the myth that sealless pumps need more, and very expensive, instrumentation for use in hazardous areas has not been true since the advent of non-metallic containment shells. When using a non-metallic containment shell, a magnetic coupled pump can be
oper ated without any additional instrumentation in a hazardous area zone, providing the customer ensures the pump is operating within its intended parameters.
Conclusion
It is true that no technology is ideal for all applications. This is true for sealless magnetic coupled pumps – they are not the solution for everything. Yet there are many applications where their ability to improve efficiency and reduce maintenance is still overlooked today. Engineers became used to the situation as it had developed over the past decades – and were maybe even burned by improperly selected pumps in the past.
S ealless pumps, both centrifugal and positive displacement types, using nonmetallic containment shells of heavy-duty

industrial ceramics open the possibility of saving money and energy. There are direct savings by eliminating eddy current losses and the need for utilities. Indirect savings come from reducing maintenance and wear parts, plus increasing the reliability when compared to traditional pump seals.
These sealless pumps can be used for liquified natural gasses, over cryogenic CO 2, the most dangerous chemical and petrochemical products, and even other difficult-to-seal products such as vacuum residues, tar, bitumen and asphaltenes, as well as polymers. This is largely without the need for any utilities except a power supply for the main motor, simplifying plants, reducing both investment and operation and maintenance costs – all from carefully applying proven reliable and robust technologies. n
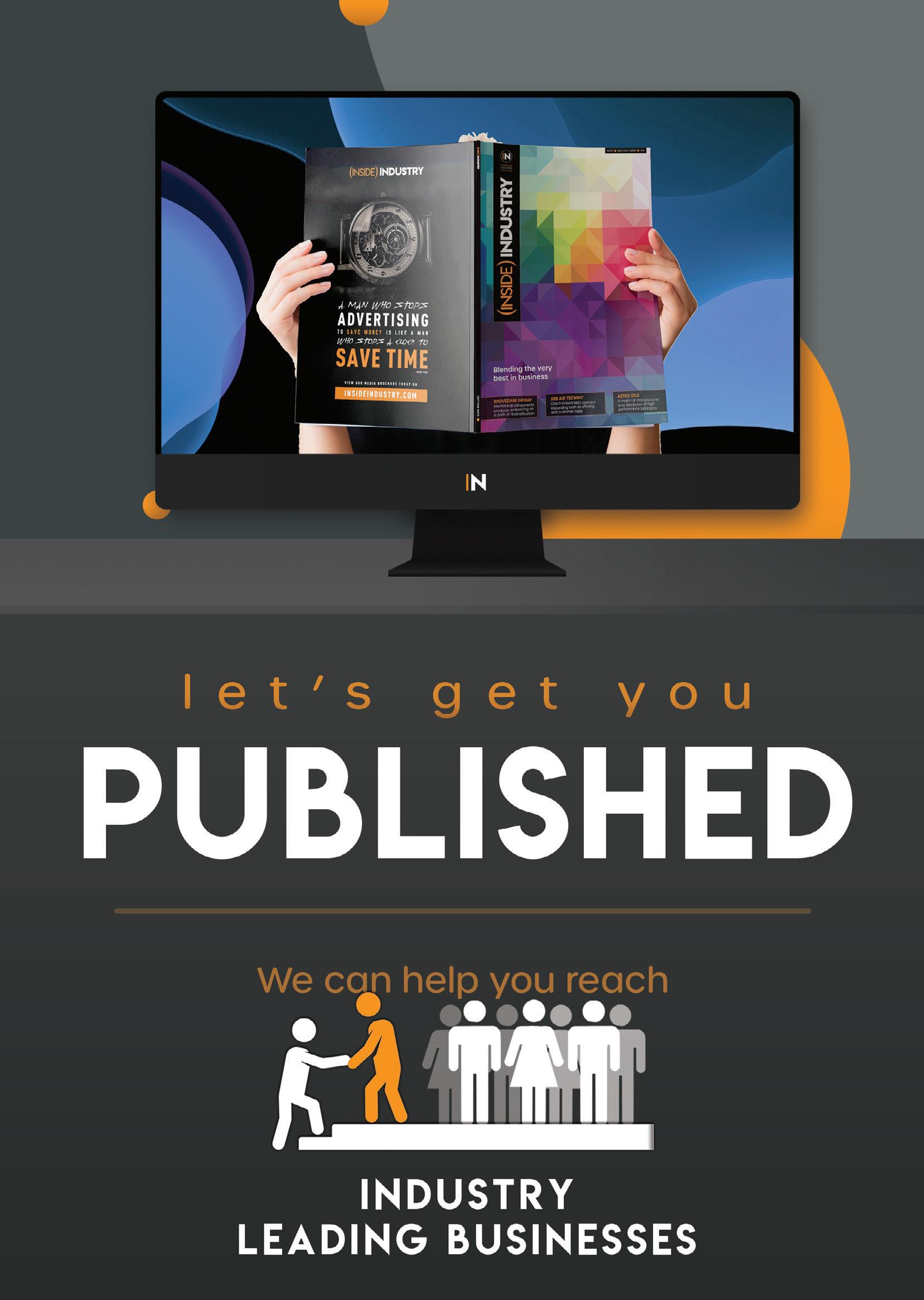
