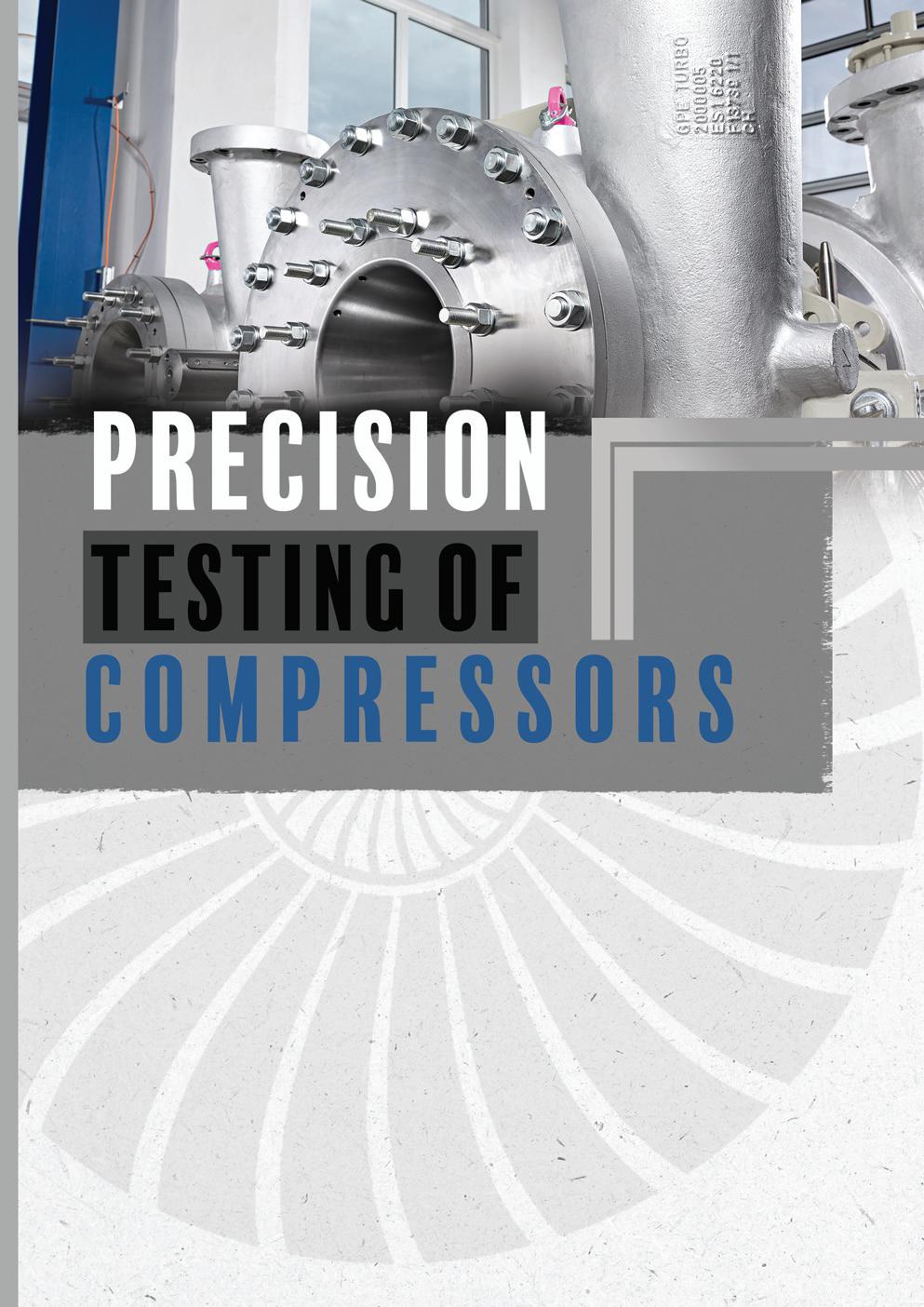
7 minute read
Precision testing of compressors
from OG33
GERMAN PNEUMATICS ENGINEERING I PROFILE
German Pneumatics Engineering GmbH has almost 10 years’ experience as a specialist for the development and manufacturing of compressor solutions, along with the maintenance, supply of spare parts and reconditioning of turbo compressor units. Managing Director Ralf Stephani and Sales Manager Michael Jürgen Scholz discussed investments and the benefits of being an agile company in conversation with Phil Nicholls.
Technology is always moving forward, and German Pneumatics Engineering GmbH (GPE Turbo) has kept pace by investing heavily in a suite of test beds for its compressors. These new arrivals enable GPE Turbo to maintain its reputation for engineering excellence.
“We now have quality assurance under our own control,” Managing Director Ralf Stephani explained. “These new test beds allow us to test all the rotating components in-house, then the certified parts move to the next department, where we assemble the complete skid.”
GPE Turbo was established in Leipzig in eastern Germany in 2013, originally as a service and maintenance provider for turbo compressors. By 2017, the company had expanded into manufacturing its own range of compressors from its single factory in Leipzig. Today, GPE Turbo employs 35 people and anticipates a 2022 turnover of almost €11 million, with orders in hand of €17.5 million. These impressive figures are part of the company’s steady growth over recent years, where turnover has been consistently doubling year-on-year.
The GPE Turbo range of compressors cover any application and work with all gas mixtures. These compressors operate with pressures up to 100 bar and flow rates up to 200,000 Nm³/h and can be driven by electrical motor, gas engine or steam turbine.
The GPE Turbo centrifugal integrally geared compressors are the company’s bread-and-butter product and designed with up to eight stages. Depending upon the client’s requirements, these compressors can be supplied API 672 and/or API 617 (part 3) compliant.
For some applications the company also manufactures non-integrally geared centrifugal compressors compliant to API 617 (part 2). GPE Turbo single-shaft compressors are offered up to eight stages only for process gas applications.
GPE compressors operate in a diverse range of industries including power generation, refineries, steel and petrochemicals. The company also offers a full range of service and spare parts for compressors, both for its own machines and those manufactured elsewhere.
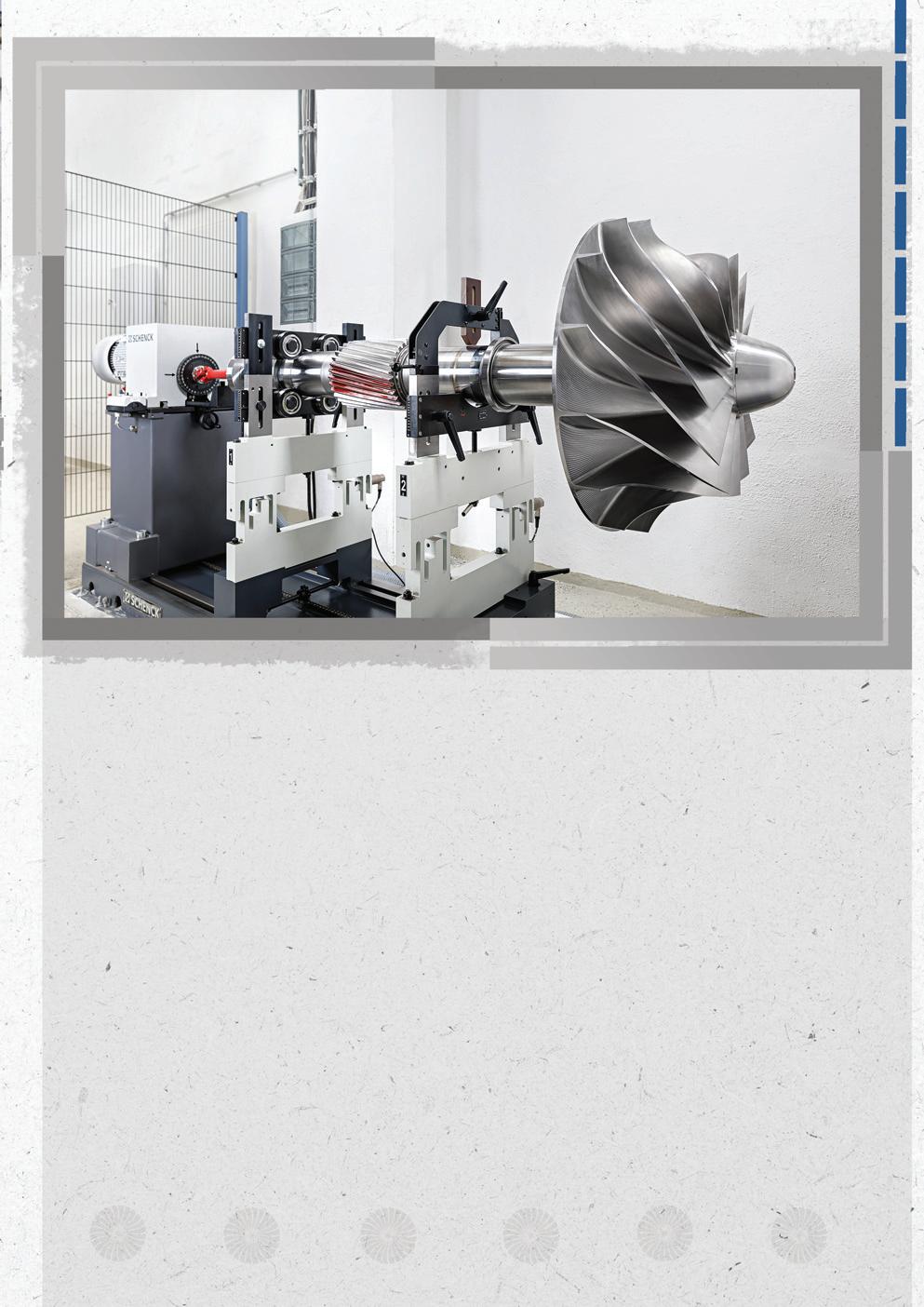
The innovation process
Throughout its range, GPE Turbo maintains an environment of continuous improvement through process innovation. The company has already realised project-specific compliance with industry standards like ANSI, API, CRN, CSA, CE/PED, DIN, ISO and VDI. As part of this ongoing process, GPE Turbo recently invested in a suite of new test beds to bring its stringent testing regime in-house.
Alongside a new compressor test bed, GPE Turbo has also invested in a new overspeed test facility.
“This new Centrio test bed is from Schenck,” said Mr Stephani. “We can now make overspeed tests for impellers up to one metre diameter. For the small impellers, we can go to a test speed of 65,000 rpm. The bed can test impellers from a diameter of 120 millimetres up to one metre. And directly next to the overspeed test centre, we have our dynamic balancing machines for completion of rotors.
“We have also installed a new compressor test bed which has a capacity of 4,000 kilowatts and by end of the year will be extended to 5,000 kilowatts. GPE Turbo has installed a harmonics frequency inverter from Siemens, which is the newest and the best technology worldwide. So, we can say that we have the most modern electrical test bed equipment in the world.”
An agile company
The new suite of in-house test beds gives GPE Turbo a complete portfolio of testing to support its quality engineering products. This is only one strand of the company’s USP. According to Mr Stephani, the small, agile nature of GPE Turbo is a real benefit.
“We are a very compact company, which is an advantage in terms of flexibility. If there’s a problem in our assembling department, then our technical department will be informed. Our engineers go downstairs, they find the solution and we make a decision quickly, displaying our flexibility.”
The size of GPE Turbo is a positive for many clients. “Companies come to us because they are looking for a flexible, slim company which has a very short reaction time and where documentation issues can be solved within a reasonable time frame,” said Mr Stephani.
Another aspect of GPE Turbo’s agility is the short supply chain the company maintains with local suppliers.
“All our purchasing is basically still from Germany,” Sales Manager Michael Jürgen Scholz explained. “We don’t outsource purchasing,
GERMAN PNEUMATICS ENGINEERING I PROFILE
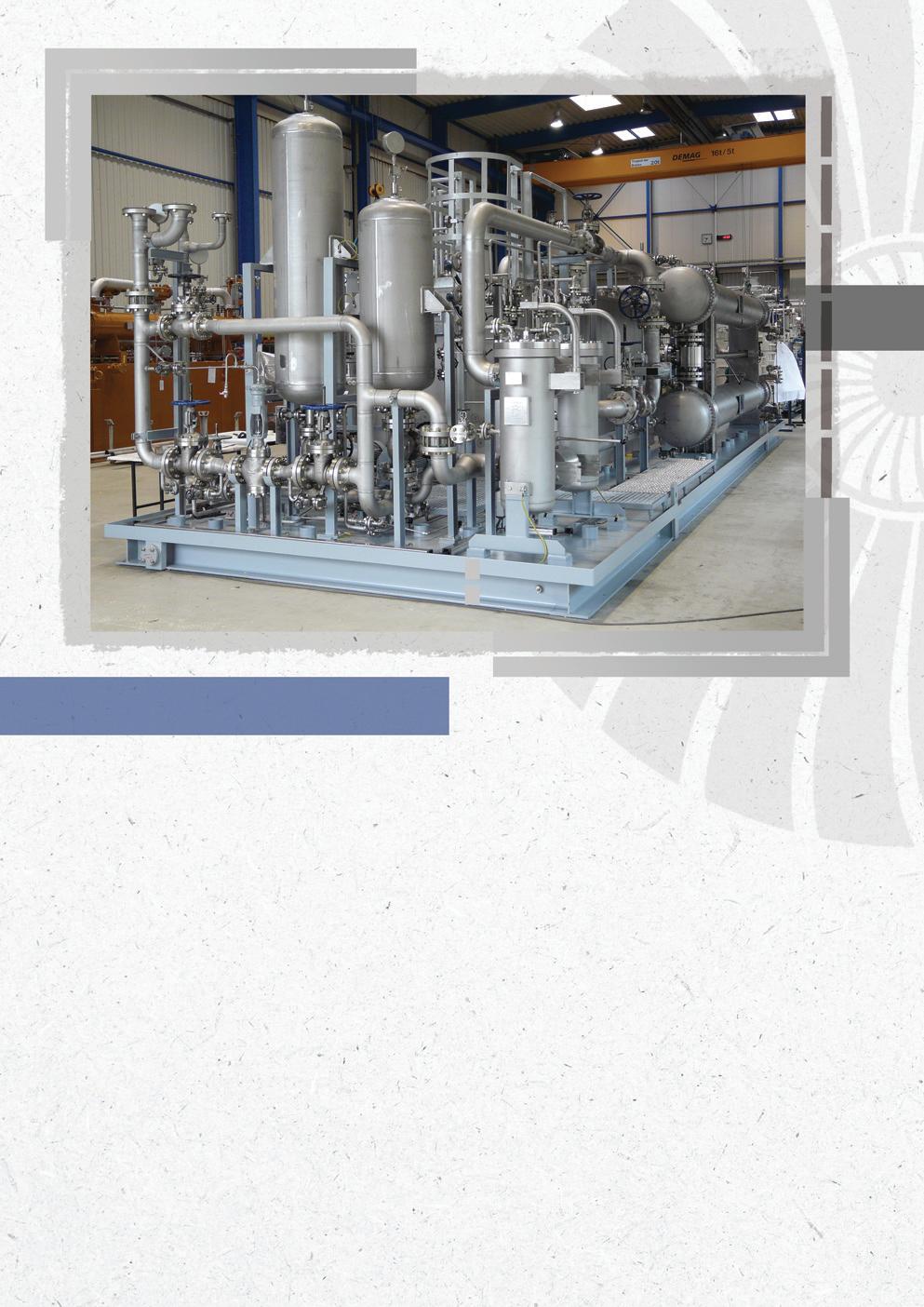
so the GPE Turbo purchasing department is here in Leipzig. There is a long tradition of engineering around Leipzig, as compressors have been built here for more than 100 years. GPE Turbo’s mission is to keep these suppliers alive in the area.”
By having so many suppliers nearby in Leipzig, GPE Turbo can build a strong and personal relationship with its partners in the supply chain. “We talk regularly to them, we visit each other to discuss issues,” explained Mr Stephani. “GPE Turbo has confidence and trust in our suppliers. This is more important than to source the best Asian supplier with the lowest price ever. We have reached the point where the purchase department is losing power in the system because the technicians are coming back on stage.”
Leipzig engineers
This supremacy of engineering specialists is at the heart of GPE Turbo and draws many experienced engineers into the company, according to Mr Scholz: “These people are leaving the big companies because they’re not really interesting places to work. Here at GPE Turbo, the engineers work closely with customers on the compressors and the applications.”
Specialist engineers in close contact with clients produces superb customer service and a company alive to the market trends. GPE Turbo is also responding to the demand for environmental sustainability in the market. The company is reviewing its CO2 consumption and developing compressors for use with natural gas, synthetic natural gas and hydrogen.
The short supply chain enjoyed by GPE Turbo allowed the company to avoid the worst of the recent global supply issues.
“If I have my supplier next door in Leipzig,” Mr Stephani said, “then I can be in their office in five minutes, and we can talk through any issue. All this is an advantage for GPE Turbo. People might say that we can do everything by video meeting, but at the end of the day it’s good to sit together at one table and solve problems face-to-face. This may not be the fashion, but it is a style which is very welcome to our customers.”
Despite these benefits from its Leipzig suppliers, Mr Scholz acknowledged there are still challenges facing GPE Turbo:
“Definitely the energy prices jumping up and players who hide behind it and increase their prices. Unfortunately, we must deal with that and try to keep our prices acceptable to our customers.”
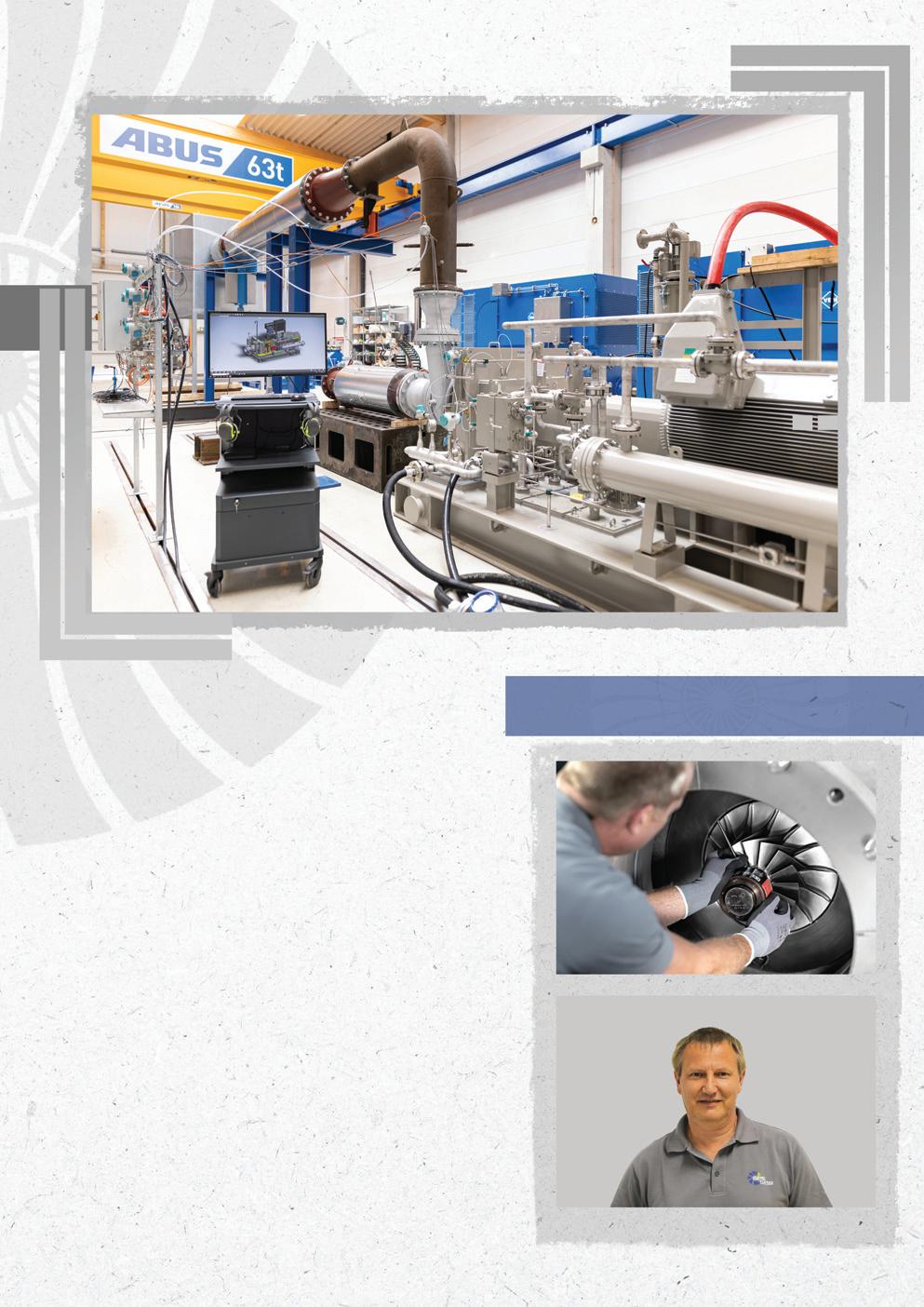
Steady growth
The purchase of new test beds has brought new capabilities to GPE Turbo, but the company is already considering the next round of expansion.
“The important thing is that we grow in a healthy way,” explained Mr Scholz, “meaning that the customer gets the quality of engineering they expect with a delivery time that is acceptable at the contractual rate. GPE Turbo wants to keep the customers happy, keep the employees happy, and keep the shareholders happy; they all must participate in our growth.”
Investment at GPE Turbo is an ongoing process, as the company works to stay current with the evolving technology. “Within the last three years we invested around €6 million in the company,” Mr Stephani added. “We have just purchased an additional new five axis milling machine – German quality from Bavaria – and a new turning and milling machine to make our vanes and other small components. These upgrades mean GPE Turbo will improve the quality of the crucial parts at the heart of the compressor, and manufacturing them here in our workshop will make us even more independent.”
“The most important thing about GPE Turbo,” concluded Mr Scholz, “is how it’s basically driven and guided by engineers, not by commercial people or bankers. This is what makes us a really different company.” n