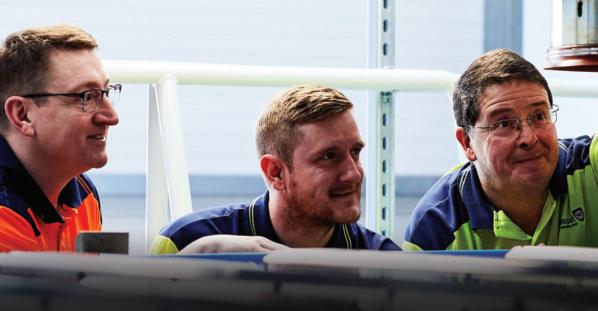
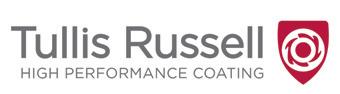

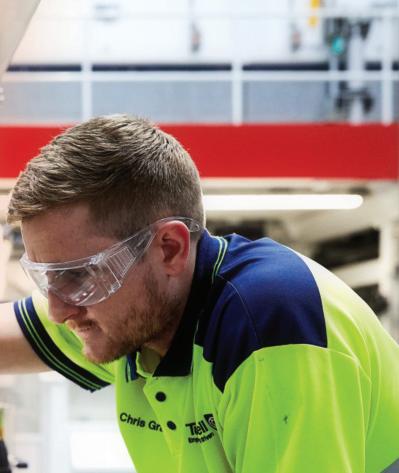

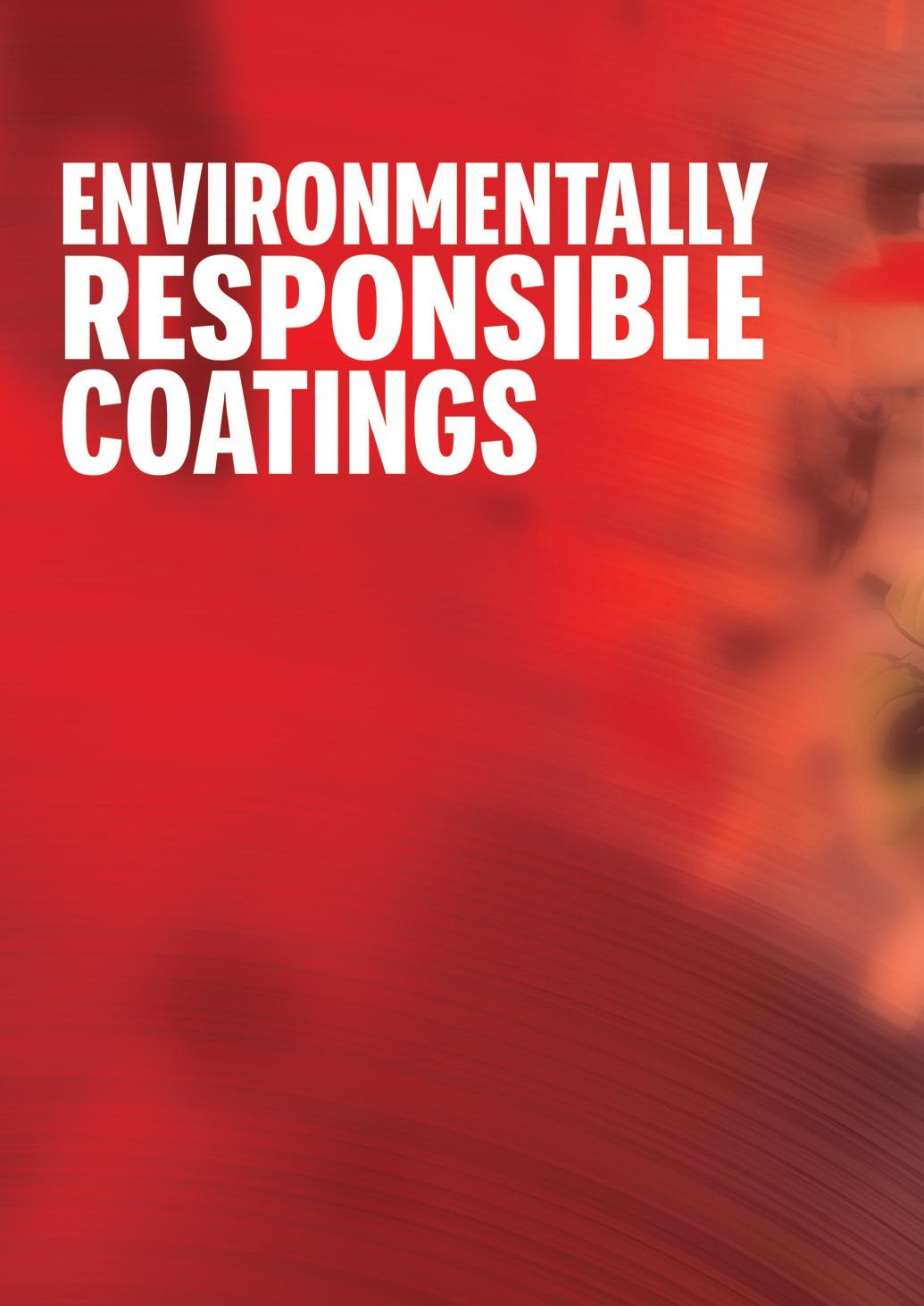
As coating sector leader in technology, expertise and capacity, Tullis Russell is at the global forefront of coated paper and film development. Key Account Manager Michaela Quinn, Sales & Marketing Director Mitch Lambert, Business Unit Manager Charlotte Healey and Product Manager Matt Littler explained more. Report by Hannah Barnett and Colin Chinery.
Tullis Russell is undergoing a metamorphosis, changing from the leading supplier of stamp and visa materials into helping to facilitate the revolution of removing non-recyclable plastic packaging from the world packaging market. Much work is being done on sourcing new and alternative raw materials, such as base papers and release liners.
“For our existing products, we want to see what’s out there, whether we can get 100, or even 50 per cent recycled materials, because we can’t compromise on performance, taking into account the production process,” said Key Account Manager Michaela Quinn. “So, it’s a balancing act of finding greener raw materials, while maintaining the excellent quality that we’re renowned for.”
World leader
Founded in Scotland in 1809 by Robert Tullis, Tullis Russell has been based at Bollington near Macclesfield for more than fifty years. The company has a depth of expertise in manufacturing high-performance surface, silicone and adhesive coatings and boasts extensive capabilities for contract coating and lamination, placing the 100-workforce business at the forefront of coated paper and film development.
The company formed the Russell Trust in 1986 and restructured as an employeeowned business, another metamorphosis in the company’s long history.
This move led to higher levels of employee engagement and customer satisfaction than could be achieved
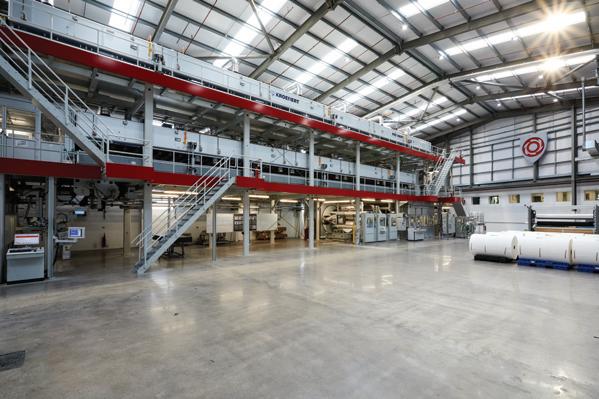
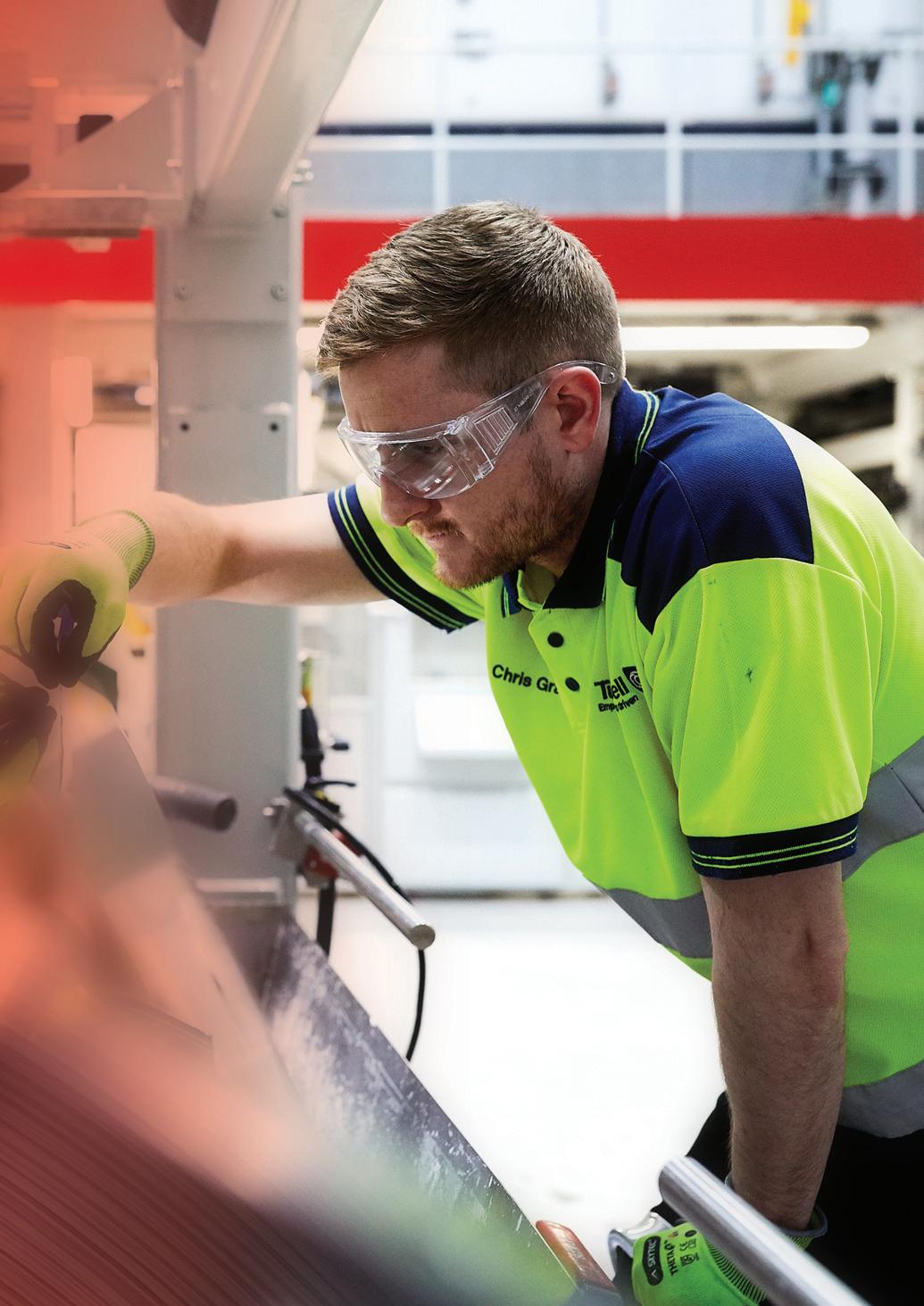
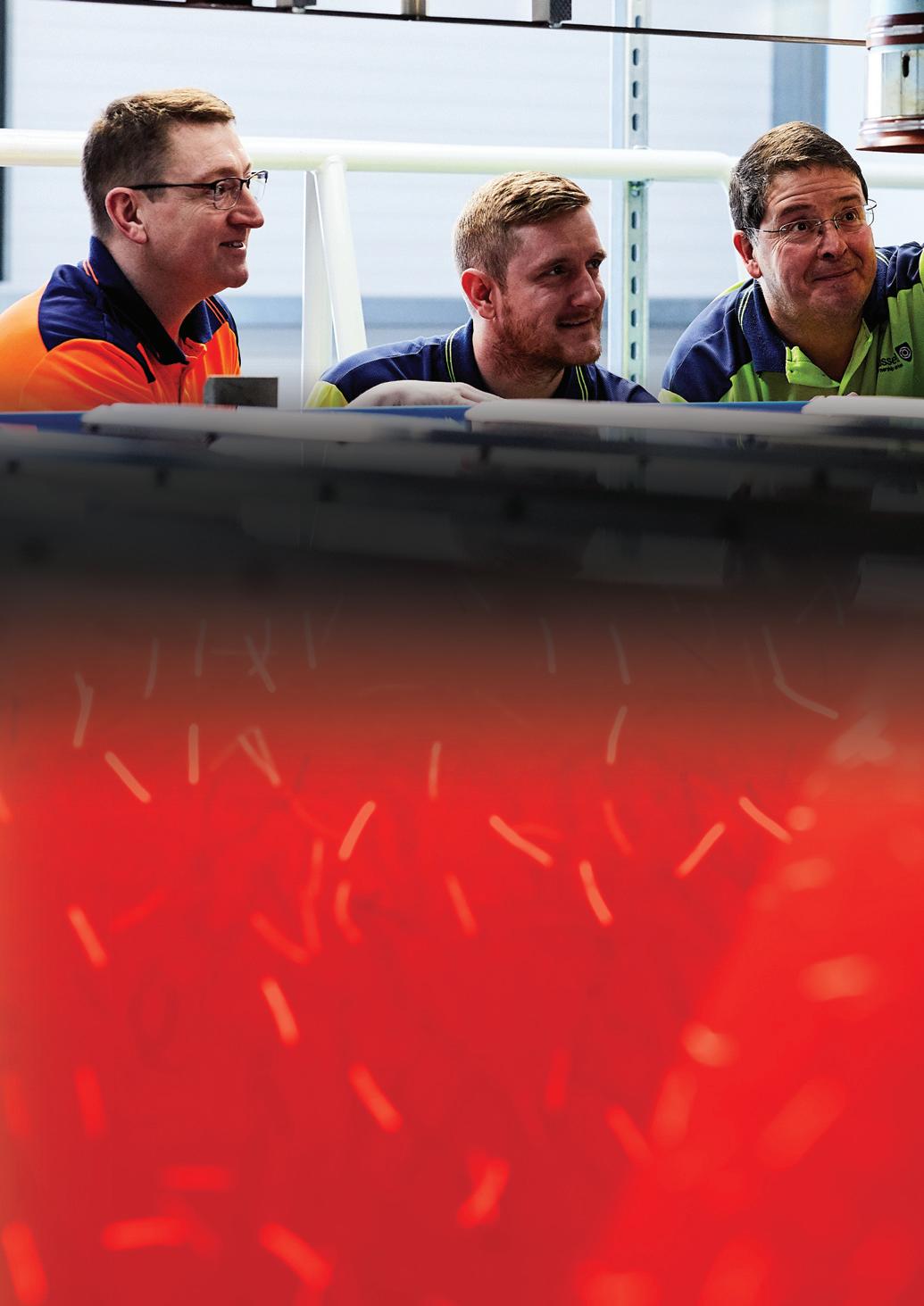

within a traditional shareholder or privately-owned structure, according to Sales and Marketing Director Mitch Lambert: “It is still managed in the same way as any other company with a Board of Directors, but the employees have a lot of say in whether they believe our strategy is right.”
Alongside this ethos of social sustainability, care of the environment is central to Tullis Russell’s operation and ethics. The company uses recyclable, water-based coating and laminating products, developed to create ecologically responsible alternatives to the materials being used today.
“Since 2018, one of our core pushes with the new coating equipment has been to replace single-use plastic materials in packaging,” said Mr Lambert. “As a result, we’ve worked heavily on creating various materials for quick service, food and restaurant packaging.”
Sustainable coatings
Today, Tullis Russell is the go-to supplier for many governments around the world, with 120 client countries. With a multitude of applications, the company produces laminate, self-adhesive and high-security products.
Tullis Russell’s market-leading ranges of trucal and trutextile papers are used by top ceramic and textile printers to create products for some of the world’s biggest brands. Deploying its cuttingedge, multilayer coating technologies the company can simultaneously apply different layers at high speed.
The wider Tullis Russell Group has further major manufacturing sites in South Korea and China, each of which has developed

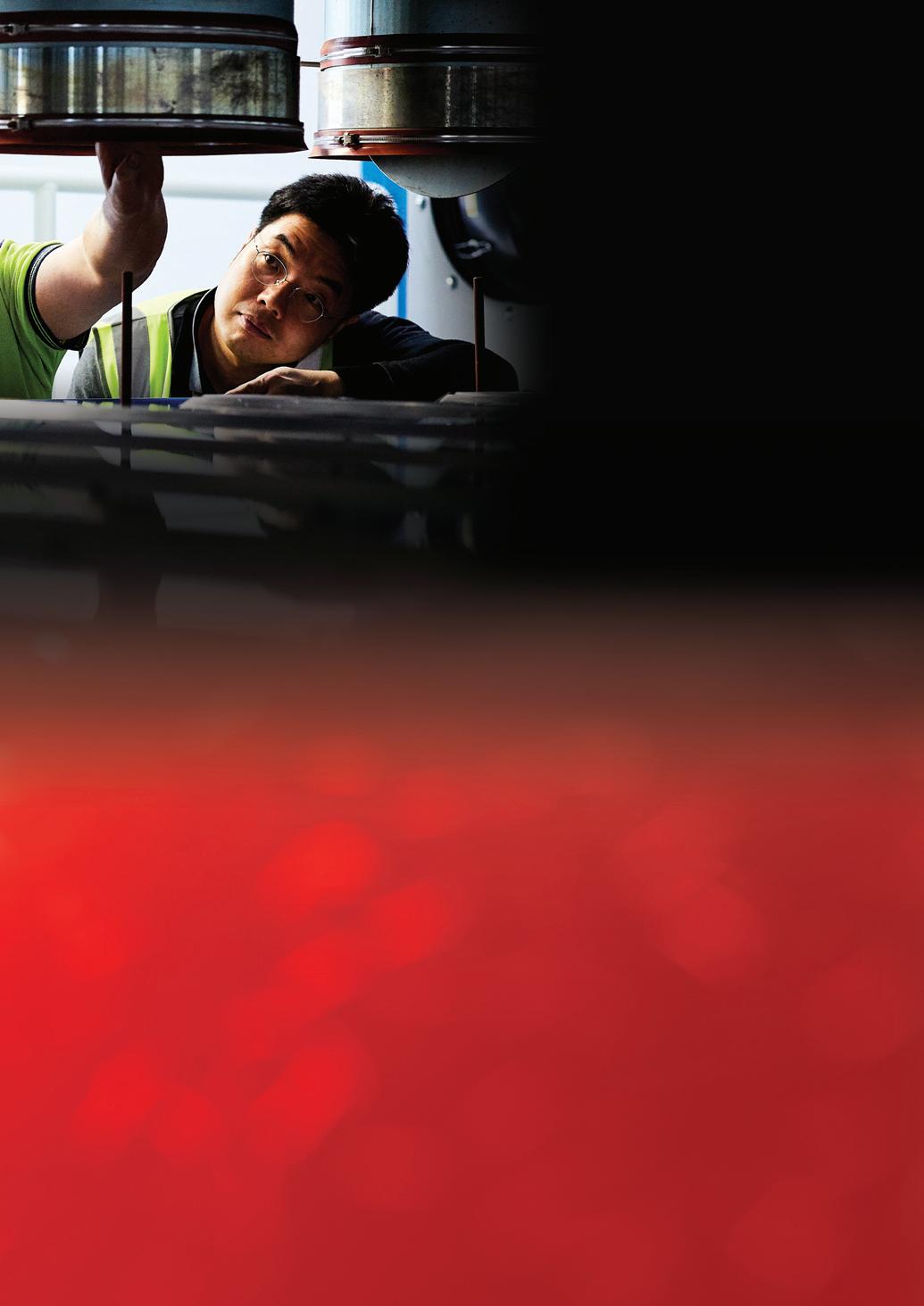
market-leading expertise in its field. Recently, the company invested in a £12M state-of-the-art coater at its UK site. This machine not only allows Tullis Russell to coat different products to the highest quality, but also delivers higher levels of productivity, reducing the carbon impact per square metre of activity.
“We’ve been using biopolymers in high-security paper manufacturing for over 50 years,” said Matt Littler, Product Manager. “So, we’ve got great experience with biopolymers, as well as physical coating technologies. It’s really interesting leveraging the existing knowledge and technologies of the company to give it more relevance for the 21st century.”
This core competence in handling biopolymers was deployed in a project as coating partner for a new sustainable packaging company, who won the international Earthshot prize with the coating applied by Tullis Russell. This coating is mechanically extracted from a sustainable source, meaning it is entirely plastic-free, compostable and recyclable.
In fact, according to the Dutch government, this is the only truly plastic-free solution to the takeaway and QSR food
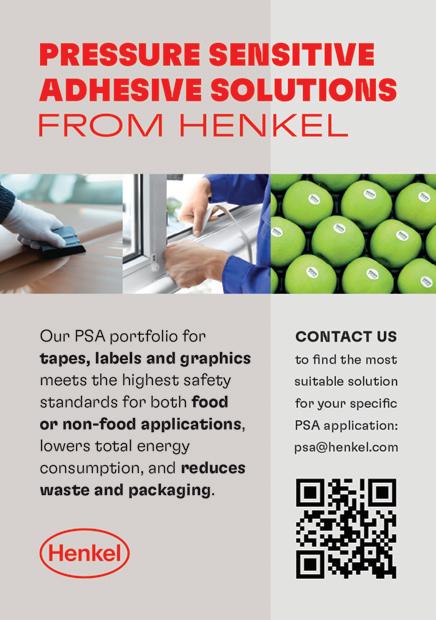
packaging problem in existence. Tullis Russell's client, Notpla, now supplies Just Eat Takeaway.com and many premier sporting venues through distributors like Levy. These partnerships are removing millions of items of single use plastic from the market every year.
Labelstock
Such a sustainable project is not a one off; the food and beverage industry now features heavily in Tullis Russell’s corporate strategy. Two of the company’s business units supply different products into the sector, and this accounts for approximately 40% of turnover.
“We started supplying into this sector around nine years ago, when we launched TRLabel, our Labelstock division,” said Business Unit Manager Charlotte Healey, “More recently, we expanded even further with the addition