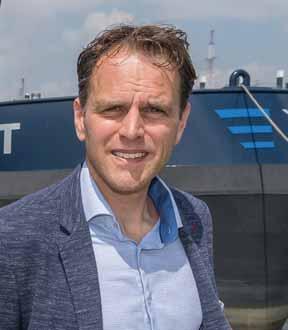
44 minute read
Column
06 14
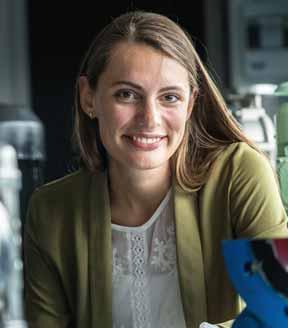
20
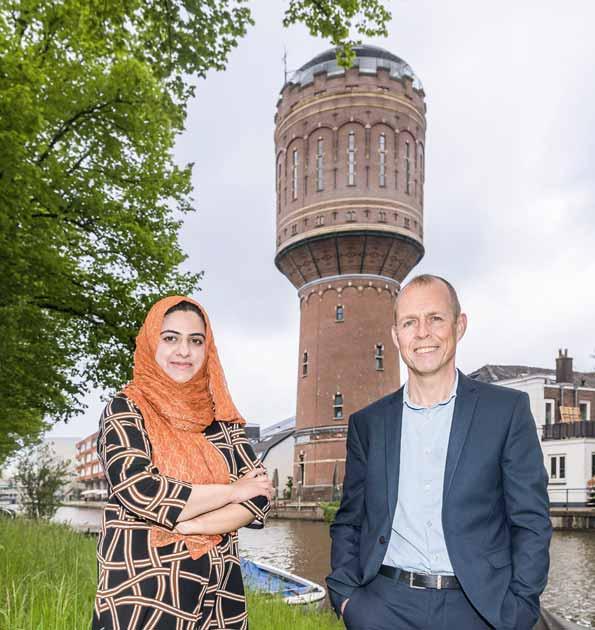
EN VERDER
03 Editorial
05 Column
28 Advertorial 30 Fluids Processing World
34 Marktnieuws
35 Agenda
COLUMN FILTERKAARSEN VERVANGEN? STEL DE JUISTE VRAGEN!
Vaak krijg ik de vraag; “Gerard, kun je een vervangend filterelement van fabricaat X leveren?” Ik kan dan natuurlijk naar een van de vele cross-referentielijsten, ofwel artikelnummervergelijkingslijsten, kijken. Op zich prima, en ook de snelste manier om een filter te verkopen, maar het laat wel ruimte voor fouten. Daarom zoek ik voor mijn klanten altijd eerst drie zaken uit: 1. Gebruikt de klant wel het juiste filter? Problemen in het filterproces worden niet altijd opgelost met hetzelfde filter als het filter niet is geconstrueerd met geschikte of compatibele materialen, géén geschikte efficiëntie biedt of niet voldoende gedimensioneerd is voor het proces. Issues met lage flow/ hoge druk, extraheerbare stoffen of slechte efficiency kunnen gewoon te wijten zijn aan het niet volledig aanpakken van de procescondities zoals temperatuur, flow, filtratiedoelstellingen, samenstelling van de processtroom of een duidelijk procedure voor hergebruik, reiniging of ontsmettingsprocessen. 2. Is er een equivalent beschikbaar? Soms is het antwoord op deze vraag ‘nee’. Hier schuilt wel het gevaar dat je de constructiematerialen van een concurrerend filter niet gelijk stelt aan de materiaalvereisten voor de toepassing. Nylon en PVDF zijn bijvoorbeeld concurrerende hydrofiele membranen die niet iedere producent aanbiedt. Maar in sommige gevallen zijn hydrofiele polyethersulfon (PES) materialen gelijkwaardig, of zelfs superieur, in termen van flow en capaciteit. Er bestaat dus niet alleen een equivalent, het kan ook een betere keuze zijn. 3. Is er een betere optie? Hoewel een vervangend filter mogelijk goed werkt in de toepassing, zijn er filters die betere prestaties kunnen leveren. Er zijn bijvoorbeeld filters met een hybride samenstelling. Deze bieden een mix van een geplooid filter met een dieptemedia die de flow en stroomsnelheden of verwerkingstijden kan verbeteren waar traditionele dieptefilters worden gebruikt voor zachte deeltjes of slurrytoepassingen. Kortom, weten welke vragen je moet stellen als je een vervangend filterelement nodig hebt, kan belangrijker zijn dan simpelweg het alternatief voor dit filter te kennen.
Gerard de Ruiter specialist procesfiltratie bij Hitma

Abonnementen abo@procesmedia.nl +31 (0)297 22 3462
Abonnementsprijs 2021 Voor de Benelux: € 120 (excl. 9% btw). Overig buitenland: op aanvraag. Losse nummers: op aanvraag. Er geldt een opzegtermijn van een maand voor het einde van de lopende abonnementsperiode. Bij niet tijdige opzegging wordt het abonnement automatisch met een jaar verlengd. Uitsluitend schriftelijke opzeggingen worden geaccepteerd. Uitgever: ProcesMedia bv, 1421 AC Uithoorn © 2021, ProcesMedia bv Niets uit deze uitgave mag worden verveelvoudigd, opgeslagen in een geautomatiseerd gegevensbestand of openbaar gemaakt worden in enige vorm of op enige wijze, hetzij elektronisch, mechanisch of door fotokopieën, opname of op enige andere manier, zonder voorafgaande schriftelijke toestemming van de auteur en/of de uitgever. ISSN: 1874-7914
MET DATAGEDREVEN ONDERHOUD DE
‘Data-driven’ is de nieuwe toverformule, ook in onderhoudsmanagement. Dat is geen hype, betoogt account manager Sophie Holsink van Inventflow in Almelo. Data maken het volgens haar mogelijk de klant verder te ontzorgen bij het beheer en onderhoud van pompen. Het mooie is: de data onderbouwen die mening.
“Wij zijn gespecialiseerd in levering, onderhoud, reparatie en revisie van pompen voor vooral de voedingsmiddelenindustrie en de farmaceutische sector. In die specialisatie is het niet zo moeilijk om te bepalen welke trend momenteel dominant is: het draait om data.”
ONLINE PLATFORM “Al een jaar of tien geleden begon Inventflow met een online platform. Wij registreren daarop de onderhoudsgeschiedenis van meer dan 30.000 pompen die wij beheren, met de onderdelen die daar bij horen. Bij reparaties voegen de monteurs foto’s van het schadebeeld toe. Klanten hebben een directe koppeling naar hun ERP-systeem,
Sophie Holsink, Inventflow
zodat ze goed zicht houden op de Total Cost of Ownership . Het werkt heel efficiënt. Het geeft ons een schat aan inzicht voor goed onderbouwde verbeteringsvoorstellen: over de onderhoudsinterval, preventief onderhoud, het overschakelen op een ander type pomp of het oplossen van knelpunten verderop in het proces. Het geeft ons de mogelijkheid om proactief te handelen en de klant op het gebied van pompen verdergaand te ontzorgen. De klant houdt tegelijk via zijn ERP-systeem altijd de vinger aan de pols.”
KUNSTMATIGE INTELLIGENTIE “Steeds meer fabrikanten rusten hun pompen en/ of motoren uit met ingebouwde sensoren. Maar bestaande pompen voorzien van losse, generieke sensoren op drie of vier punten maakt evengoed real-time monitoring mogelijk. Dan behoort ook retrofit tot de mogelijkheden. Die sensoren regelen zichzelf tegenwoordig in. Op basis van kunstmatige intelligentie bepaalt de sensor zelf de aanvaardbare minimum- en maximumwaarde tijdens de eerste twee weken na inbedrijfstelling. En als er een calamiteit is in die eerste twee weken? Geen nood, de achterliggende data weten dat op te vangen, door het herkennen van bepaalde vibratiepatronen. Hier blijkt weer: hoe meer data, hoe beter.”

TRILLINGSKARAKTERISTIEK “De trillingskarakteristiek van de pomp vertelt vervolgens alles over de conditie. Hoe groter de installed base die wordt gemonitord, des te
KLANT ONTZORGEN
Sophie Holsink, Inventflow
Sophie Holsink, accountmanager Inventflow.
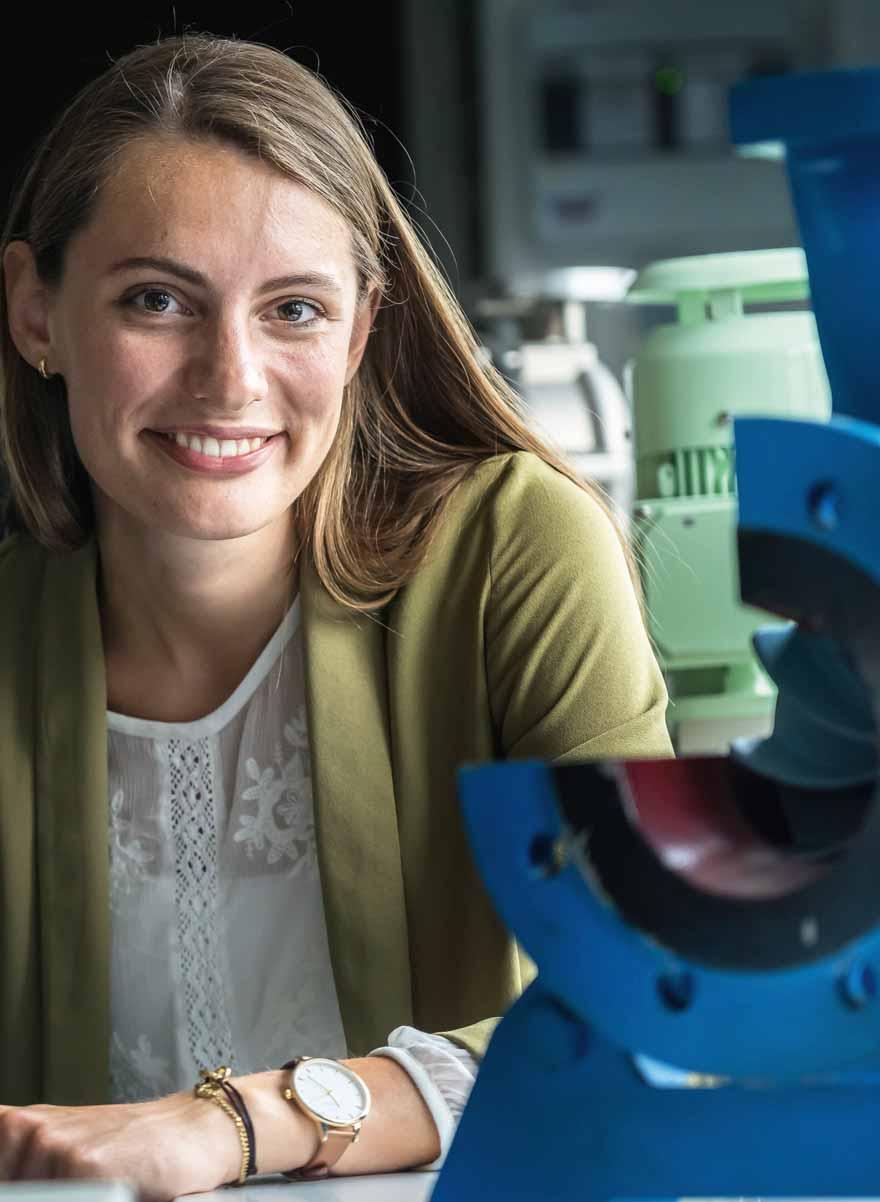
verfijnder de conclusies. De trillingen vertellen niet alleen hoe de pomplagers ervoor staan, maar maken het zelfs mogelijk veertien verschillende schadepatronen te onderscheiden. Dit maakt het mogelijk heel gericht het probleem aan te pakken, wat tijd en kosten bespaard. De sensoren zijn zelfs in staat om te checken of de reparatie effectief is gebleken. Het herkennen van beginnend falen is een stuk makkelijker dan dat. Onderpresterende assets verlagen de productieprestaties. Wie daarover data heeft, bezit de kennis om tijdig maatregelen te nemen en haalt daarmee waarde binnen.”
TERUGVERDIENEN “Het uitrusten van een pomp met sensoriek ligt op ongeveer twintig procent van de kosten van de pomp zelf. Het is voor ons op basis van de data niet moeilijk om aan te tonen dat klanten dat gemakkelijk terugverdienen door onderhoud op het juiste moment en het voorkomen van stilstand, zeker als de pomp op een zeer kritische plaats in het proces werkt. Neem Refresco in Sittard, dat een miljard blikjes per jaar afvult. Het is niet moeilijk uit te rekenen wat het minimaliseren van de stilstand oplevert.”
TWEE BENADERINGEN “In theorie zijn er twee benaderingen om stilstand te minimaliseren. Een bedrijf kan werken met redundantie, correctief onderhoud en het aanhouden van een voorraad aan kritische componenten. De tweede benadering, real-time monitoring gekoppeld aan voorspelling, kost minder ruimte, minder kapitaal en minder organisatie – en werkt beter. Steeds meer klanten staan daar voor open. Iedereen heeft inmiddels wel van ‘predictive maintenance’ gehoord. De voorlopers – en daaronder zijn eigenlijk alle grote voedings- en drankenconcerns – zijn er allang mee bezig. Maar zoals bij veel ontwikkelingen zijn er grote verschillen. Als je als bedrijf je onderhoudssysteem up-to-date hebt, is de stap om van de bewezen voordelen te profiteren ook niet zo groot. Maar dat geldt niet voor elk bedrijf. Er is altijd wat koudwatervrees. Niet elk bedrijf durft 100% op de ICT te vertrouwen.”
ONTZORGING “Tijdens de corona-crisis vond er tijdelijke weer veel insourcing plaats. Nu zien we dat rap veranderen naar outsourcing. Het tekort aan technisch personeel loopt weer snel op nu de economie aantrekt. Het voorspellen van onderhoud door middel van real-time monitoring stelt ons in staat klanten te bedienen met een gelijkblijvende personeelsbezetting, want het werkt heel efficiënt. De combinatie van onderhoudsgeschiedenis en de mogelijkheid preventief onderhoud te plegen is vrijwel onverslaanbaar. De totale ontzorging die dat klanten biedt, is de toekomst.” ●
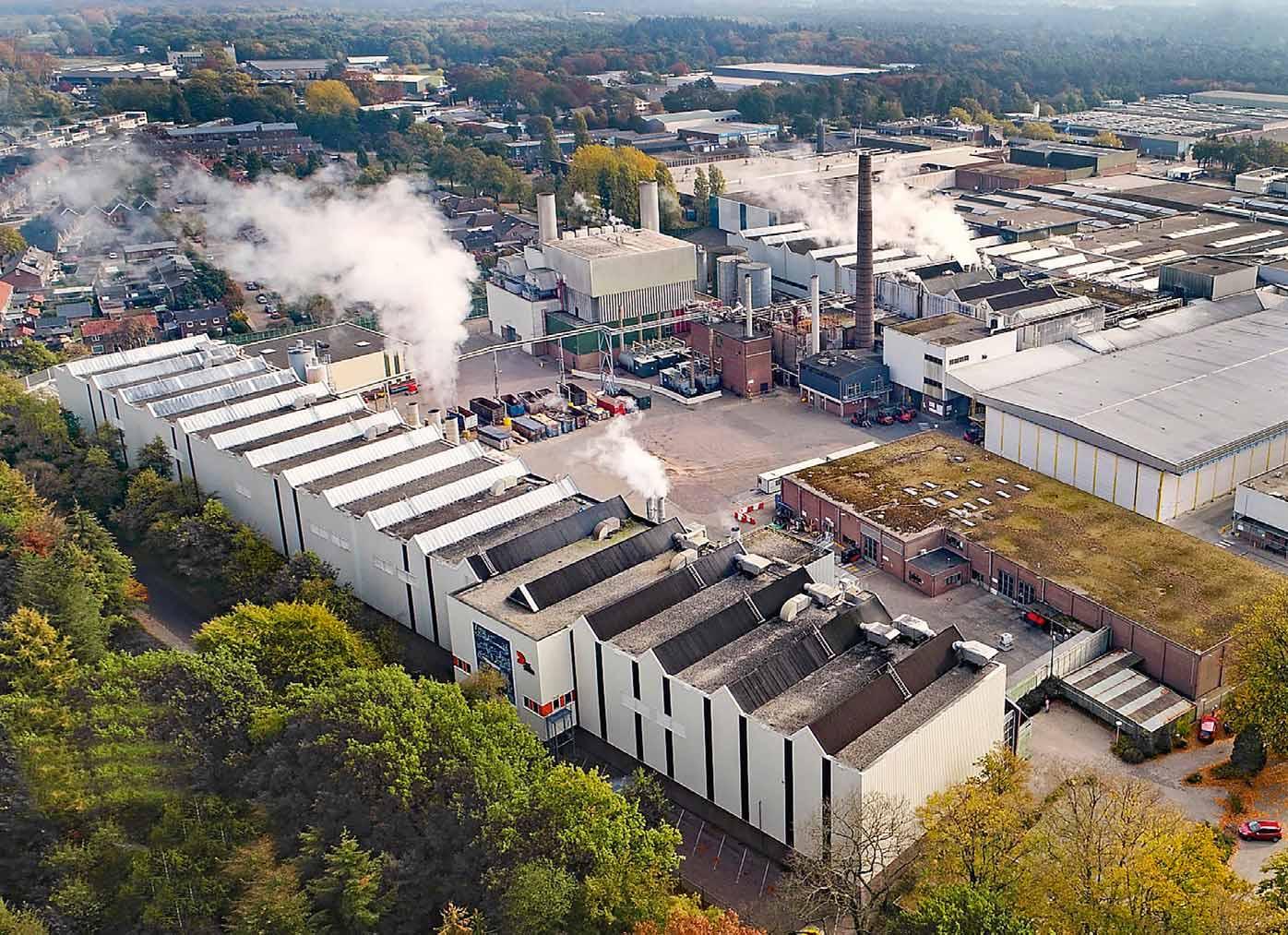
PAPIERFABRIEK PEILT IBC’S MET AUTONOME RADARSENSOR
Papierfabriek De Hoop gebruikt mini radarsensors om de voorraad hulpstoffen in mobiele IBC’s te monitoren. De sensors worden eenvoudig op de buitenkant geplakt of gespannen en leveren elke 6 uur draadloos informatie over het vloeistofniveau.
Papierfabriek DS SMith De Hoop produceert containerboardproducten (liner- en mediumsoorten) van 100% oud papier. “Wij recyclen ongeveer 400.000 ton papier en karton per jaar en produceren nieuw papier. Daar maken onze grootste klanten weer dozen, trays en displays van”, vertelt Marco Verkerk, coördinator technologie & product support bij Papierfabriek De Hoop.
PROCES Voor het papierrecyclingproces worden de balen oud papier met behulp van warm water in een van de vier pulpers afgebroken tot papierpulp. De pulp wordt ontdaan van alle onzuiverheden. De schone papiervezel gaat naar één van de twee papiermachines en wordt met een snelheid van bijna 50 kilometer per uur verwerkt tot nieuw papier, dat wordt gebruikt voor het maken van dozen en trays, en voor de buitenkant van gipsplaten of de binnenkant van deuren. De hulpgrondstoffen die in het proces worden toegevoegd, moeten heel precies gedoseerd worden. “We hebben daarvoor verschillende tussenliggende opslaglocaties van waaruit zowel vaste als vloeibare additieven worden toegevoerd, maar een aantal vloeistoffen wordt gedoseerd uit standaardIBC’s van duizend liter”, zegt Marco Verkerk uit.
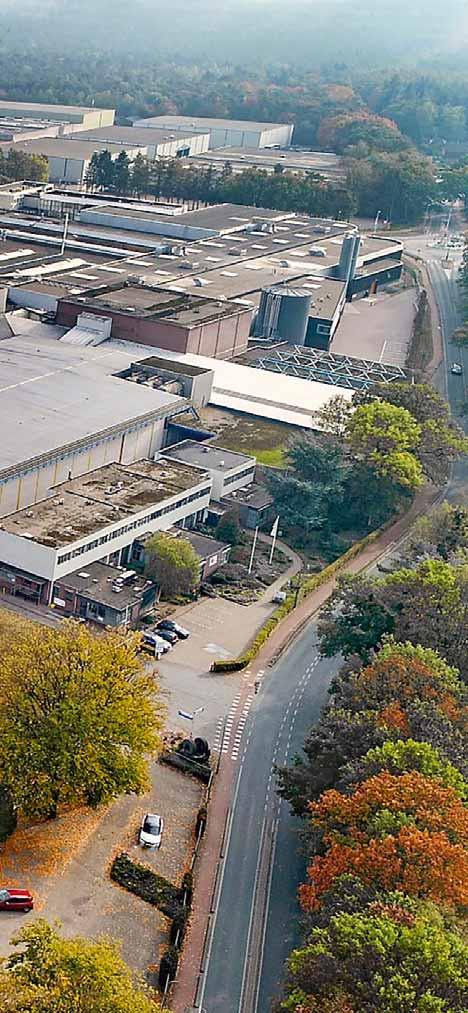
Papierfabriek DS Smith De Hoop in Eerbeek.

Op de IBC’s worden draadloze, autonome Vegapuls Air sensoren geplakt of gespannen (met een riem) die met 80Ghz radar het niveau meten.
Marco Verkerk, papierfabriek DS Smith
NIVEAUMETING Voor de niveaumeting in de silo’s gebruikt De Hoop al jaren Vegapuls en Vegabar niveaumeters, waarvan de waarden in een PLC worden verwerkt. Elders in de fabriek worden Vegawell, Vegason en Vegadif sensoren gebruikt, bijvoorbeeld op de papiermachines en bij de grond- en hulpstoffen. Sinds juli 2020 gebruikt de fabriek bij wijze van proef ook Vegapuls Air sensoren op de verwisselbare IBC’s. “We slaan meer dan 40 verschillende chemicaliën en hulpstoffen op in silo’s en IBC’s. De vaste opslagtanks en silo’s hebben allemaal een niveausensor die is aangesloten op de PLC. De waarden worden verwerkt in ons ERP systeem”, zegt Verkerk. “Bij de mobiele IBC’s, die niet voor elk eindproduct nodig zijn, was dit eerst niet mogelijk. Dus liep ik elke dag door de fabriek om de hoeveelheden in de IBC’s handmatig in te schatten”, zegt Verkerk. Tot de komst van de Vegapuls Air 23. DS Smith De Hoop was de eerste die de nieuwe sensoren ging gebruiken om het niveau in de IBC’s te bewaken.
DRAADLOOS EN AUTONOOM De draadloze, autonome sensoren zijn met klevende adapters of een rubberen riem heel eenvoudig op de IBC’s te bevestigen. Door de radartechnologie is meting van buitenaf mogelijk en hoeft de kunststof IBC-behuizing niet te worden geopend of aangepast. De plug-and-play sensor is snel te installeren. Het vast ingestelde meetbereik is 1,2 meter en het meet- en overdrachtsinterval is instelbaar tussen 15 minuten en 24 uur. Het vloeistofniveau wordt overgedragen ongeacht waar de IBC zich bevindt. Zelfs gestapeld meten de sensoren van elke afzonderlijke container het actuele niveau en de positie – en dragen deze gegevens draadloos over naar de cloud. Dit maakt ze bij uitstek geschikt voor IoT-toepassingen. De meetwaarde van de sensoren kan via een mobiel netwerk (NB-IoT/LTE-M of LoRa) ook naar het VEGA Inventory System worden gestuurd. De sensoren zijn zuinig met energie. Bij de ontwikkeling zijn de meetprestaties, de draadloze gegevensoverdracht en het energieverbruik geoptimaliseerd, zodat een sensor op batterijen een gegarandeerde looptijd van 10 jaar heeft. De gebruiksduur is afhankelijk van de meetfrequentie en dataverbinding. SNELLE OPLOSSING Aanvankelijk werden bij De Hoop drie IBC’s voorzien van een Vegapuls Air 23. De installatie was eenvoudig: beschermfolie verwijderen, aanbrengen en klaar. Met een antenne in vloeistofdichte kunststof behuizing meet de 80GHz-radarsensor door de IBC heen. “In eerdere instantie vroegen we ons af of we misschien verder konden komen met een bedraad radarmeetinstrument”, zegt Verkerk. “Maar de bekabeling was op die locaties lastig en de investering woog niet op tegen de tijdwinst.” Installeren kon zonder certificeringen en procesaansluitingen. Omdat door de containerwand heen wordt gemeten, worden geen bijzondere eisen gesteld aan de resistentie van de sensoren. Het maakt de sensor niet uit welk medium zich in de IBC bevindt. Bovendien kan de buitenkant van de IBC gewoon worden gereinigd, aangezien de sensoren IP68 en IP69K geclassificeerd zijn.
Marco Verkerk, papierfabriek DS Smith
GEMAK “Wij waren een van de eerste gebruikers en konden in die zin onze ervaringen noteren”, geeft Verkerk aan. Dubbelzijdige tape volstaat volgens hem om de sensor op de IBC te bevestigen. “We zijn bij het verwisselen van IBC’s al een keer vergeten de sensor mee om te wisselen. We vonden de sensor een paar dagen later terug in een van de heftrucks”, herinnert hij zich lachend. De sensor liet zich er niet door van de wijs brengen. Zodra hij op de juiste IBC was geplakt, leverde hij de correcte meetwaarden weer aan. De sensor optimaliseert het bedrijfsproces. “De oude situatie was gewoon niet praktisch. We konden de inhoud niet precies volgen en er ging elke dag tijd verloren met het checken van de voorraden. Nu hebben we een nauwkeurige meting die vier keer per dag automatisch wordt bijgewerkt.” De sensoren zijn ook ideaal als er tests worden gedaan met nieuwe chemicaliën, omdat ze zo eenvoudig en flexibel te installeren zijn. ●
DS Smith is een van de grootste aanbieders van duurzame verpakkingsoplossingen, papierproducten en recyclingdiensten. De onderneming is in de afgelopen 80 jaar sterk gegroeid en heeft bedrijven in Europa en Noord-Amerika overgenomen, waaronder de Nederlandse papierfabriek De Hoop, die al sinds 1657 bestaat. Het bedrijf is nu in meer dan 30 landen actief en heeft meer dan 29.000 medewerkers.
Overpompen van chemicaliën uit IBC-containers kan veilig en schoon met een zelfaanzuigende centrifugaalpomp met CDS- koppeling. De kunststof k oppeling met pakking is bestand tegen agressieve stoffen, en is voorzien van veerbelaste terugslagkleppen.
Overpompen van chemicaliën uit IBC-containers hoeft geen probleem meer te zijn, want sinds kort is hiervoor de zogeheten Safetec pompset. Deze set van Flux pompen bestaat uit een zelfaanzuigende centrifugaalpomp, die via een CDS-koppeling op de zuigbuis van een dubbelwandige IBC kan worden aangesloten. Het gaat om een koppeling en contrakoppeling van kunststofmateriaal, voorzien van een pakking. Beide zijn bestand tegen agressieve chemicaliën. Ook zijn de koppelstukken voorzien van veerbelaste terugslagkleppen, zodat er bij het ontkoppelen geen vloeistof kan wegstromen en er geen vuil in de container kan komen.
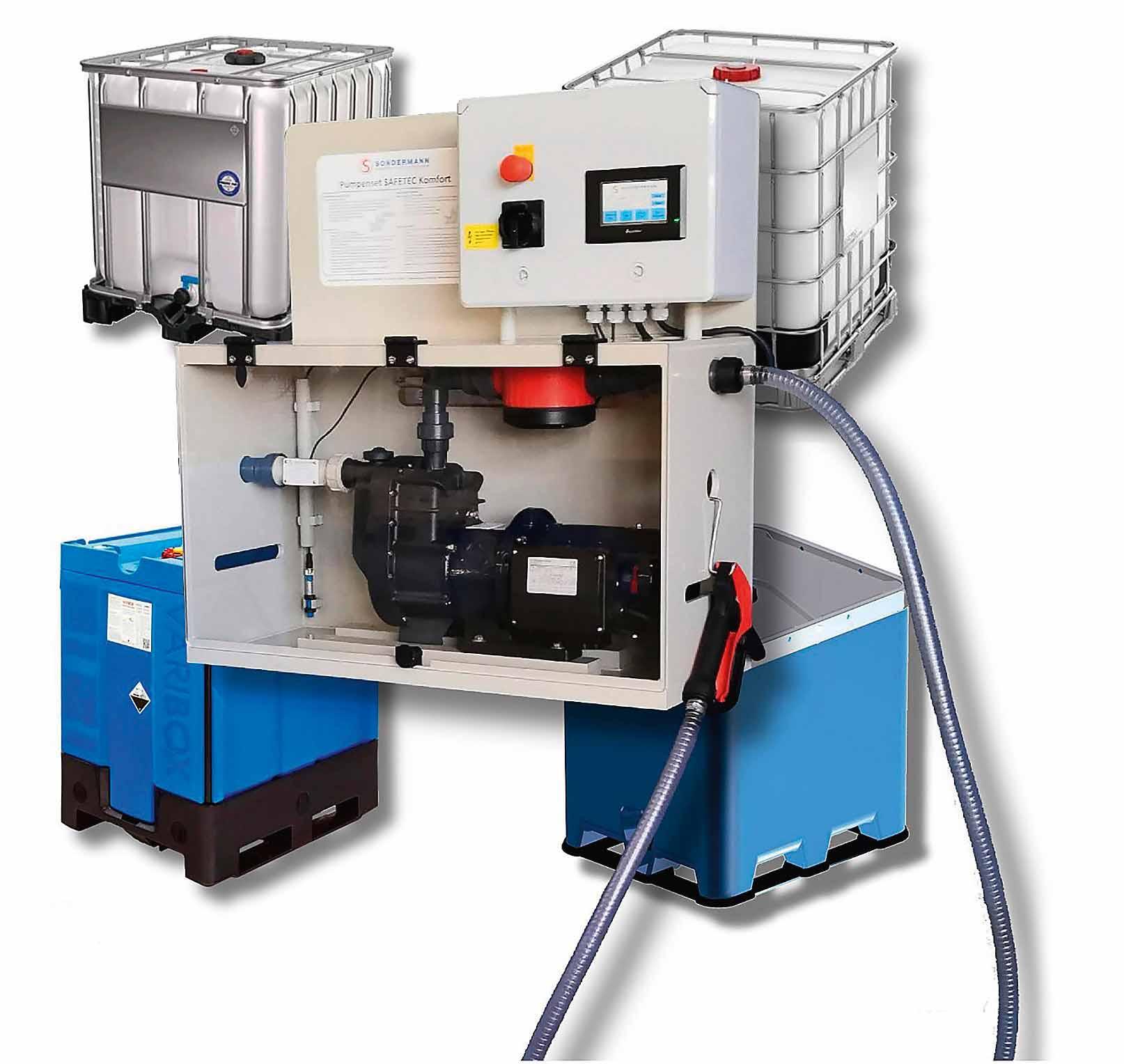
VERONTREINIGING “Bij een conventionele vatpomp schroef je het deksel van de IBC los en steek je een staaf door de opening in de vloeistof”, legt Mario Doornenbal, directeur van Flux Pompen Benelux in Zevenaar, uit. “Onderin zit de pompwaaier die via een as binnen de staaf verbonden is met de motor, die zich buiten de IBC bevindt. Een nadeel van deze werkwijze is, dat er verontreinigingen in de vloeistof terecht kunnen komen. Ook kan er vloeistof bij de motor komen als de asafdichting niet goed is.”
SAFETEC De nieuwe Safetec set kent dit nadeel niet. De pomp wordt via een slang met de CDS-koppeling op de zuigbuis van de IBC aangesloten. Het verzegelde schroefdeksel blijft dicht. Doordat het zegel intact blijft, kan de leverancier aan een geretourneerde IBC meteen zien, dat deze zonder spoelen of reinigen opnieuw gevuld kan worden. De klant betaalt dan geen schoonmaakkosten meer. Ook kan er bij dit systeem geen vloeistof bij de motor van pomp komen, omdat waaier en motor magnetisch gekoppeld zijn. De pomp bevindt zich in een kleine behuizing, die aan een wand gemonteerd kan worden. Mocht er vloeistof weglekken, dan valt die onderin de behuizing, waar een lekdetectie aanwezig is.
SENSOR Een sensor detecteert wanneer er geen vloeistof meer aangezogen wordt en de IBC dus leeg is. De pomp schakelt dan automatisch uit. “Met een vloeistofmeter erbij kun je ook een batch instellen van bijvoorbeeld 63,6 liter”, zegt Doornenbal. “Daarbij vindt er ook een correctie plaats voor de seconden die het duurt, voordat de aangezogen vloeistof de ingeschakelde pomp bereikt.”
TOUCHSCREEN De Comfort en de Comfort D versies van de pompset zijn voorzien van een touchscreen, waarop verschillende zaken zijn af te lezen en waarmee de pomp eventueel handmatig aan- en uitgezet kan worden. ●
Safetec pompset voor het veilig overpompen van chemicaliën uit IBC’s.
Vooruitblik beurzen EINDELIJK WEER LIVE: SOLIDS, PUMPS & VALVES, M+R
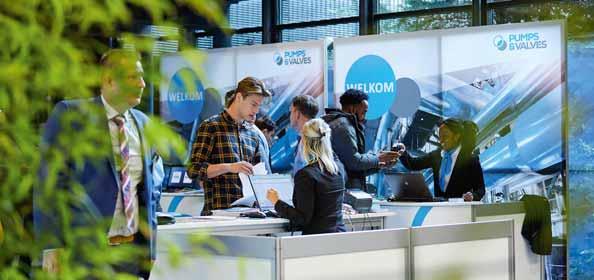
Op 6 en 7 oktober 2021 vinden de vakbeurzen Pumps & Valves, Solids en M+R plaats in Rotterdam Ahoy. Eindelijk weer face-to-face contact! Met een live conferentieprogramma waar kennispartners via best practices laten zien wat bedrijven en sectoren van elkaar kunnen leren.
CONFERENTIEPROGRAMMA Kennis delen staat op deze editie ook weer centraal. Van Gent: “We hebben tijdens de vorige editie gemerkt dat er veel animo was voor het conferentieprogramma.” Dit jaar delen de partners ISPT, KWR, TNO, Deltalinqs, iTanks & Aptean Foodware 365 kennis over optimalisatie van installaties, duurzaam produceren en veilig werken.
RONDE TAFEL ENERGIETRANSITIE Tijdens een rondetafelgesprek praten leveranciers over de energietransitie in de industrie. Welke rol spelen leveranciers hierin? Wat is er in het afgelopen jaar concreet aan duurzame techoplossingen ontwikkeld? Hoe gaan leveranciers invulling geven aan duurzamere machineparken en tech in de komende vijf jaar? Welke concrete stappen worden er gezet in energiereductie of is het een wassen neus? Betaalt duurzaamheid zich terug? Welke rol speelt circulariteit? ●
(advertentie)
De vakbeurzen Solids, Pumps & Valves en M+R vinden op 6 & 7 oktober 2021 gelijktijdig plaats in Rotterdam Ahoy. Bas van Gent, Business Unit Director Industrial: “Eindelijk mogen en kunnen we elkaar weer face-to-face ontmoeten en nieuwe innovaties ontdekken.”
Professionals uit de procesindustrie kunnen op deze combibeurs oplossingen vinden voor het gehele proces. Traditionele componenten en installaties voor droge (Solids) en natte processen (Pumps & Valves) staan centraal. Nieuw is de vakbeurs M+R. Een gericht event met focus op procesinstrumentatie en –automatisering. Van Gent: “Met de toevoeging van vakbeurs M+R spelen we in op trends als digitaliseren en meer autonoom werken.” De bezoekers treffen hier o.a. Vega, Endress + Hauser, Transtech, Lans Nivotherm, Sick, Elscolab en SMAR Nederland.
COG IS TOONAANGEVEND: Briljante ringen voor alle uitdagingen.
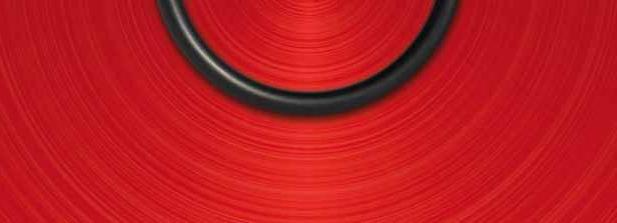
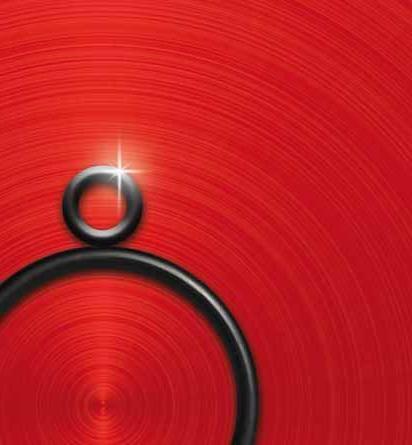
Praktische informatie
Solids, Pumps & Valves, M+R Woensdag 6 & donderdag 7 oktober 202 10:00-17:00 uur Ahoy Rotterdam Coronatoegangsbewijs vereist: volledige vaccinatie, herstelbewijs of negatieve test uitslag <24 uur; geen zelftest!
Voor meer informatie: www.pumpsvalves.nl/mr/en www.solidsrotterdam.nl en www.mr-processing.nl
Registreren kan via: https://bit.ly/3zGqcFt. Het toegangsticket geeft toegang tot alle drie de vakbeurzen. Precisie-O-ringen die voldoen aan de hoogste eisen voor de meest uiteenlopende industrieën.

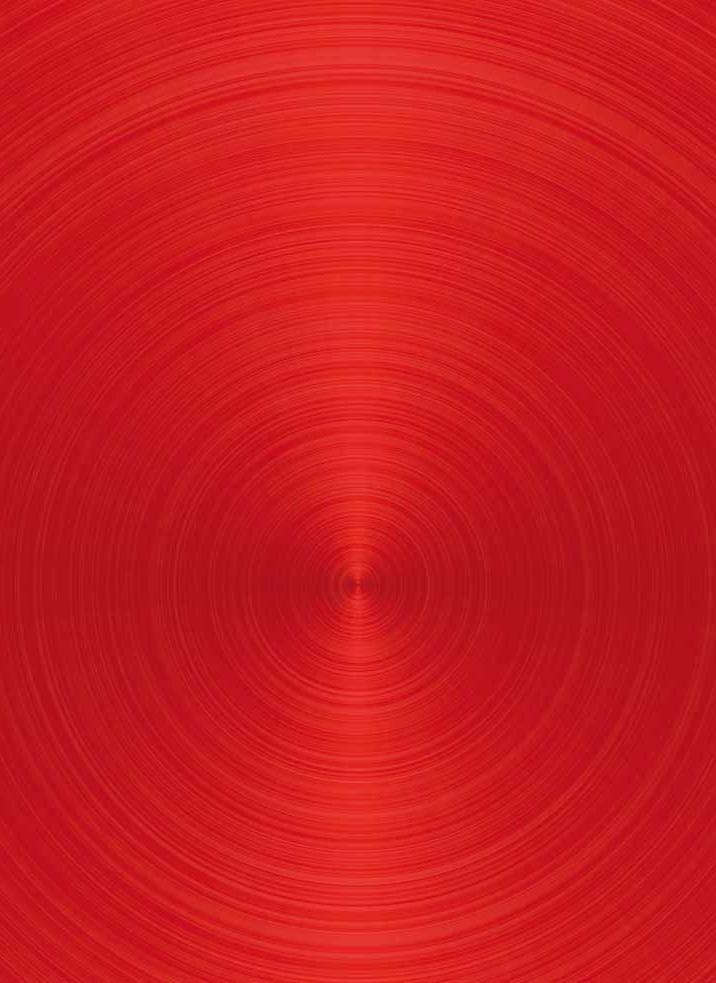
PELLETEERSYSTEEM VOOR FAR
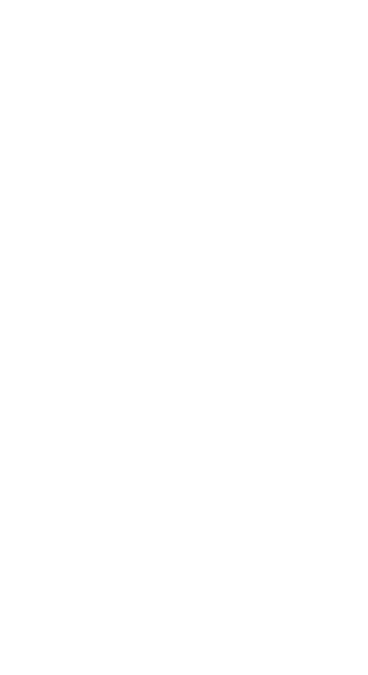
m Het Belt-Cooling Pelleteersysteem PFS is speciaal ontworpen voor in water oplosbare, broze producten. Het systeem kan worden aangepast aan het product, waardoor zelfs elastische en zeer flexibele polymeren kunnen worden verwerkt. De kwalitatief hoogwaardige pellets die het systeem produceert, maakt verwerking verderop in het proces een stuk makkelijker.
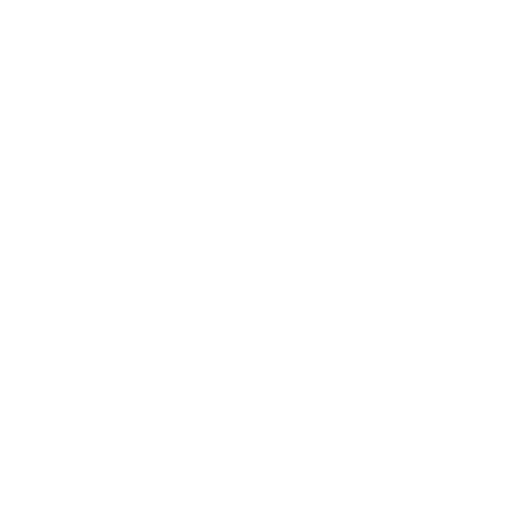

Extrex PFS tandwielpomp

Deze is speciaal ontworpen voor toepassingen in de farmaceutische industrie. Hij voldoet aan de specifieke voorwaarden voor het farmaceutisch productieproces: •hoge persdrukcapaciteit, •constante doorvoer, •zacht transport •een zeer klein temperatuurbereik.
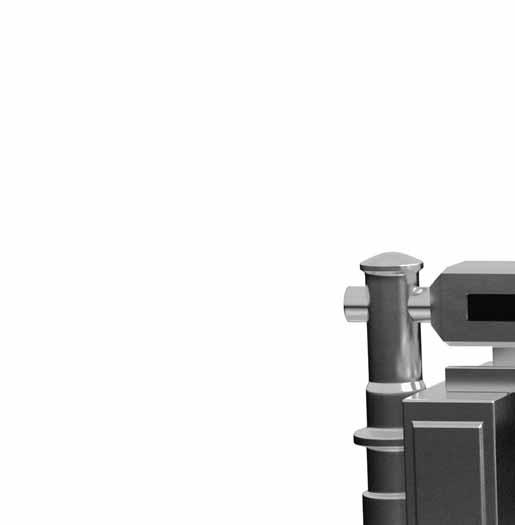
Hotmelt extrusie
Hotmelt extrusie (HME) is een opkomende technologie in de farmaceutische industrie voor de productie van medicijnen in een continuproces. Een belangrijk voordeel is het vermogen om een verscheidenheid aan formuleringen te produceren, zoals vaste doseervormen, die de biologische beschikbaarheid van medicijnen verbeteren. HME is een oplosmiddelvrij, continu proces. Het is in feite een vereenvoudiging van complexe, multifaseprocessen.
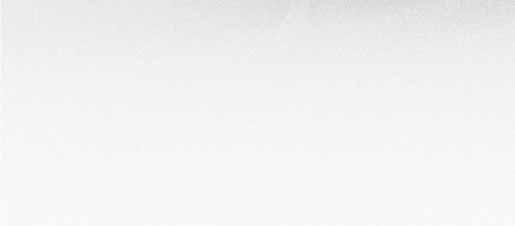
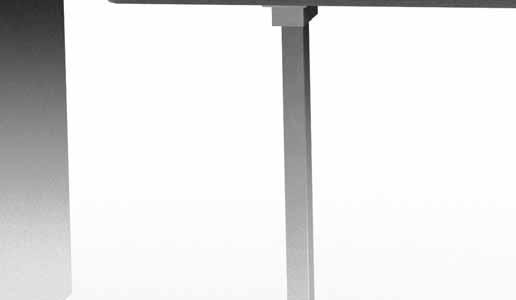
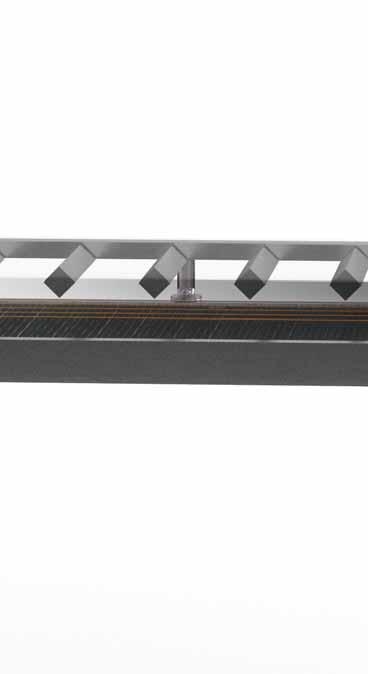
Die Head PFS
Deze snijkop zorgt voor homogene strengprofielen van het materiaal door middel van extrusie en is speciaal ontwikkeld voor toepassingen in farmaceutische processen. De plaatsing is na enkele of dubbele schroefextruders maar ook na reactorvaten.

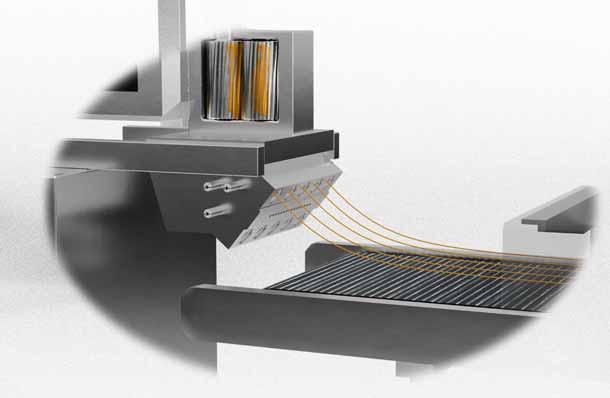
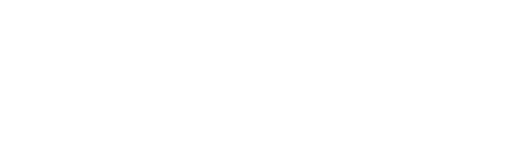
MACEUTISCHE TOEPASSINGEN
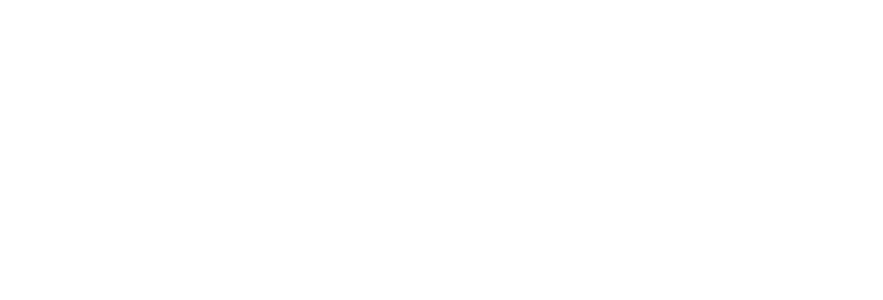


Lopende band
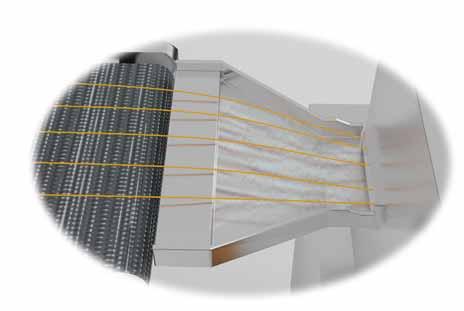
Op deze lopende band worden de strengen met luchtstromen gedroogd. Luchtgedragen gaan de strengen de snijmachine in
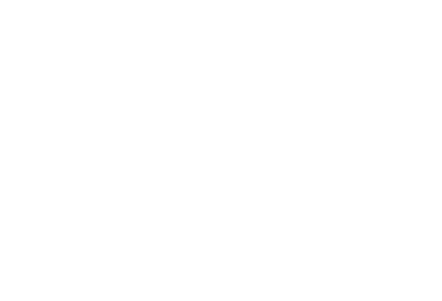
Snijmachine
De snijmachine pelletiseert de strengen op hoog tempo in exacte grootte.
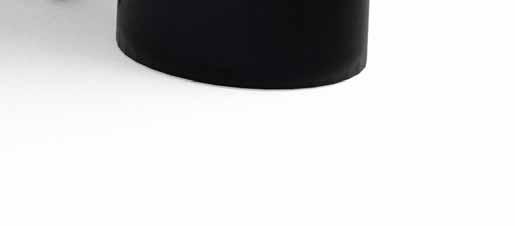

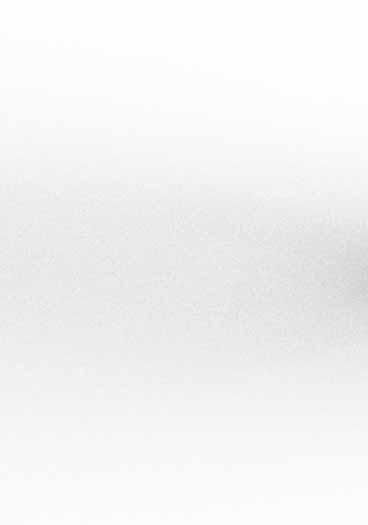
Micropellets
Tabletten en capsules zijn tegenwoordig de meest populaire orale vaste doseringsvorm in de farmaceutische industrie. Tabletten en capsules met fijne deeltjes actieve stof, zorgen voor een significant snellere oplossing. Deze deeltjes kunnen in de vorm van micropellets worden toegevoegd.
Pellets zijn geen poeder of korrels; zij worden gekenmerkt door een gedefinieerde vorm en een smalle deeltjesgrootte distributie. Dit maakt een zeer breed scala aan toepassingen mogelijk waarbij actieve stoffen worden geïntegreerd.

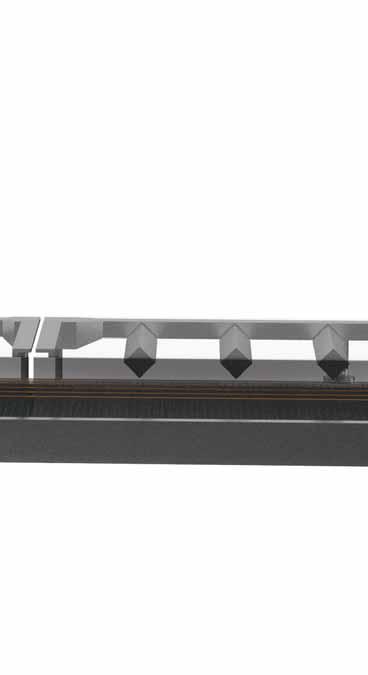
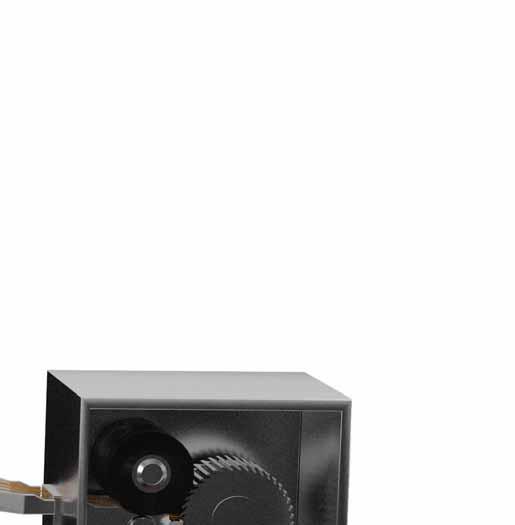

DECANTERS KANSRIJK IN BIOBASED
Decanteercentrifuges kunnen een grote rol gaan spelen bij het maken van biobased producten, voorziet Martin Huijsman van Pieralisi. Speciale features, zoals verstelbaarheid en in-place reinigbaarheid, maken decanters bij uitstek geschikt voor het zuiveren van productstromen met sterk fluctuerende vaste en vloeibare fracties, zoals biodiesel en proteïnen.
Opkomende markten met nieuwe producten vergen andere procestechnologische oplossingen. Neem biodiesel. De markt is booming sinds Brussel vorig jaar in de Renewable Energy Directive (RED-2) een bijmengpercentage van hernieuwbare brandstoffen heeft opgelegd. Het opwerken van oliehoudende organische reststromen – van frituurvet tot gewasresten – levert technische uitdagingen op. “Biobrandstofproducenten hebben hoogwaardige technieken nodig, om de kwaliteit biodiesel te krijgen die aan de hoogste standaarden voldoet”, vertelt sales manager Benelux Martin Huijsman van fabrikant Pieralisi van ontwaterings- en scheidingstechnologie.
FASESCHEIDING Een cruciale stap na het veresteringsproces is het zuiveren van de biodiesel door fasescheiding. Hierbij worden het zwaardere methanolrijke water en de aanwezige vaste stoffen van de lichtere fractie biodieselolie gescheiden. Het knellende vraagstuk bij de organische reststromen die de biobrandstofproducent gebruikt, is de steeds wisselende verhouding tussen vaste en vloeibare fracties. Van oudsher worden voor driefasenscheiding schotelcentrifuges ingezet, maar het nadeel van dit type apparaat is dat het niet goed kan omgaan met de continu wisselende verhouding tussen vloeibare en vaste stromen en daarmee niet de gewenste kwaliteit biodiesel kan realiseren. “Daarvoor moet je het centrifugeproces namelijk voortdurend bij kunnen stellen”, zegt Huijsman.
BIJZONDERE FUNCTIONALITEITEN Om de fluctuaties in vaste en vloeibare fracties te hanteren, zijn decanteercentrifuges met bijzondere functionaliteiten nodig. Als voorbeeld noemt Huijsman decanters met een ingebouwde verstelbare centripetaalpomp (Centri Petal Adjustable, kortweg CP-A, in vaktaal). “Dit type pompmodule kan rekening houden met een steeds wisselende verhouding tussen vaste en vloeibare fracties en levert zo een beter scheidingsresultaat en daarmee een schonere brandstofkwaliteit. Als er te veel water in de biodiesel zit, kun je het scheidingsproces op basis van een troebelheidsmeting sturen.” Het verstellen van het scheidingsproces in de decanter met behulp van de CP-A-module gaat standaard handmatig, maar deze handeling is ook te automatiseren met een elektromotor, aldus Huijsman.
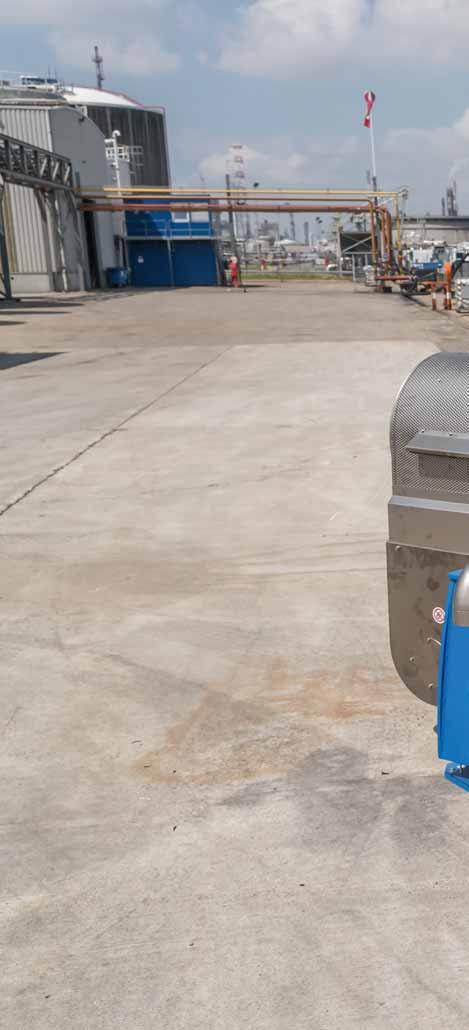
SCHOEPEN Recent heeft Pieralisi het CP-A-principe naar een nieuwe generatie decanters doorontwikkeld voor de productie van onder meer biodiesel. Het basisconcept, verduidelijkt technisch specialist en productmanager Michael Wünsch, wordt al decennialang gebruikt voor de productie van olijfolie. Op deze wijze wordt de olijfolie gescheiden van het water en de olijfpitten. Wünsch werkt op de vestiging van Pieralisi in Duitsland en heeft ruim veertig jaar ervaring met centrifugale scheidingstechnologie. In de centripetale pompunit, legt hij uit, draaien de schoepen niet rond – zoals in de centrifugaalpomp – maar zitten ze in een vaste stand, terwijl de behuizing van de pomp meedraait. De combinatie van centripetale krachten en druk zorgen ervoor dat de twee vloeibare componenten (water en biodieselolie) actief in de uitgangen van de decanter worden gedrukt. Daardoor is het mogelijk met de CP-A-module te sturen op het wisselende niveau van de zware en lichte fracties, terwijl de decanter aan het werk is. De decanter met CP-A-module heeft daarmee een grotere capaciteit dan een conventionele schotelcentrifuge en dankzij de pomp-unit is er continu druk (tot 3 bar) op een hoge outputkwaliteit.
CIP Daarnaast moet een schotelcentrifuge regelmatig worden geopend, aldus Wünsch, om het apparaat schoon te maken. Voor de decanter met CP-A-module heeft Pieralisi een Cleaning In Place (CIP)-voorziening ontwikkeld, die de decanter vanbinnen met nozzles kan reinigen. In de CP-Adecanteercentrifuge kunnen vaste stoffen continu verwijderd worden, terwijl de machine loopt.
SCHUIMVORMING De decanter met CP-A-module is inmiddels ook in gebruik voor het behandelen van afvalwater met vettige zeepresten. Bij een producent van shampoo en wasmiddelen in Berlijn is eerder een testopstelling met een decanteercentrifuge in bedrijf genomen als onderdeel van het zuiveringsproces. De decanter scheidt de vaste stoffen in het afvalwater af. Het aantrekkelijke van de CP-A is volgens Wünsch dat de unit schuimvorming in het afvalwater tegengaat. “Dat is een zeer ongewenst bijeffect, omdat het afvalwater onbehandelbaar wordt.” Bij deze decanteercentrifuge is de CIP ingericht op een continue reiniging van de machine.
EIWITSHAKES Nog zo’n trend is de productie van proteïnen (eiwitten) als voedingssupplement in de food-industrie, denk aan de populaire proteïne-shakes. Aan een proteïnefabrikant in China heeft Pieralisi een decanter met CP-A-module geleverd die het eiwitrijke poeder uit sojabonen kan isoleren. Ook deze decanter is uitgerust met een CIP-installatie die de machine continu reinigt (bij een temperatuur
Martin Huijsman, Pieralisi
PRODUCTIEPROCESSEN
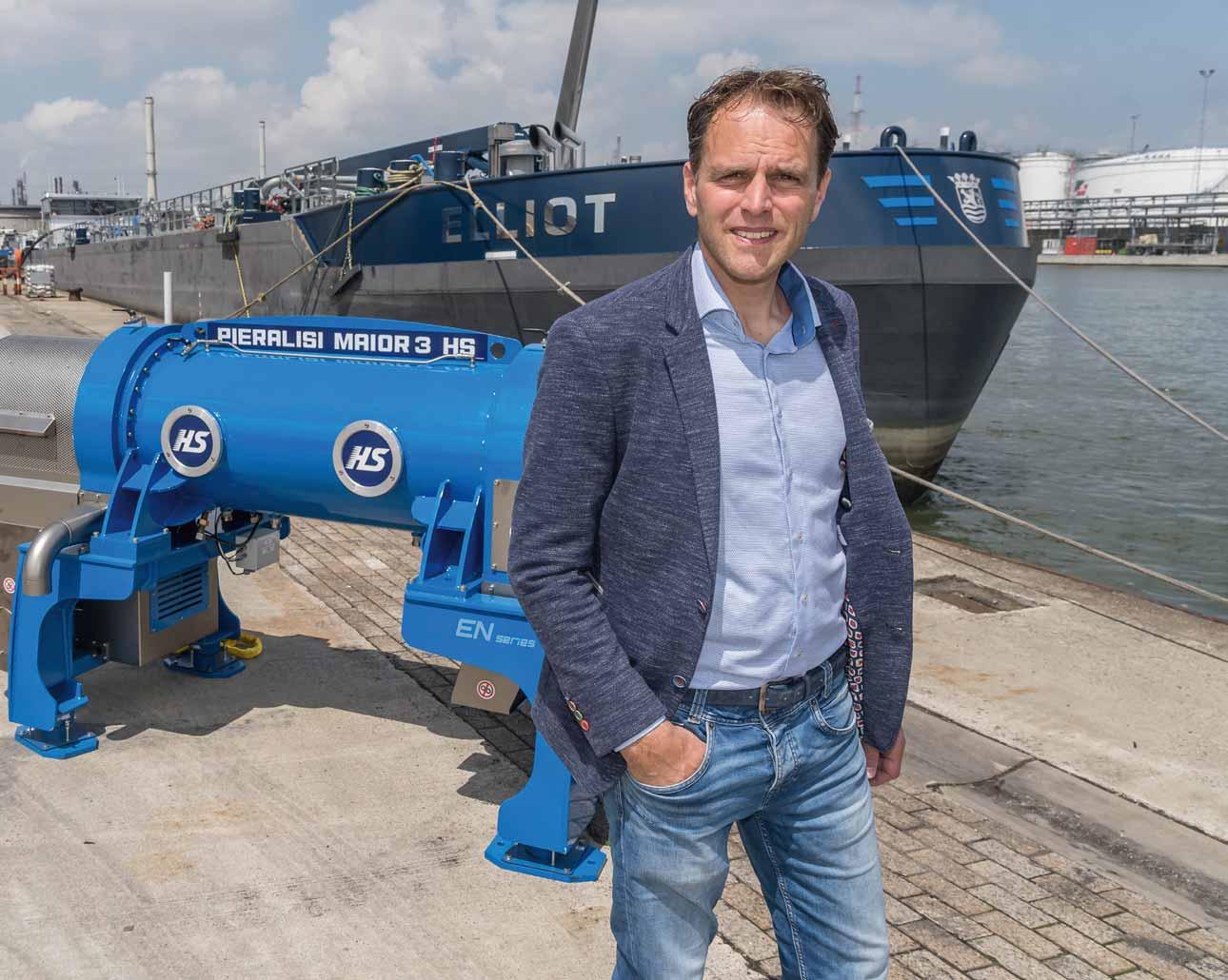
van 95 °C). “In de zetmeelindustrie is het eveneens zaak schuimvorming in het proces te voorkomen. De proteïnen in zetmeel kunnen hiertoe neigen. De CP-A-module kan dit tegengaan”, zegt Wünsch
RESTSTROMEN Huijsman voorziet dat de traditionele procesindustrie steeds meer om gaat zien naar zijn reststromen. “Bedrijven willen onderzoeken welke grondstoffen en zelfs producten ze daar nog uit kunnen halen. Reststromen kunnen zich zo tot een aantrekkelijk bijproduct ontwikkelen.” Cosun gebruikt bijvoorbeeld decanters van Pieralisi in een demofabriek voor de productie van het additief ‘Betafib’. De microvezels, die de suikerproducent uit zijn bietenpulp wint, worden in watergebaseerde producten gebruikt vanwege de uitstekende suspenderende eigenschappen, van wasmiddel tot verf. Het ingrediënt is daarmee een duurzaam alternatief voor fossielgebaseerde grondstoffen, zoals polyacrylaten en microplastics. Voor het scheiden van de cellulosehoudende vezels van de overige voor het productieproces benodigde vloeibare componenten koos Cosun voor decanters, omdat de vast-vloeistofscheiding goed is te sturen en controleren. Dat is nodig voor de kwaliteit van het vaste-stofingrediënt. man, “kijken naar ontwaterings- en scheidingstechnieken om de bijproducten uit hun processen op te waarderen. De inzet van decanters kan in dat opzicht tal van kansen bieden. Het voordeel van decanteercentrifuges is dat je ze exact kunt afstemmen op de eigenschappen van een product. Dat zien we onder meer bij de productie van proteïnen. Na de eerste testunits met klein formaat decanters voor het R&D-deel kunnen bedrijven dan op termijn de vertaalslag maken naar grotere machines. Het aantrekkelijke voor klanten die hierna komen, is dat ze bij een min of meer vergelijkbaar productieproces geen testinstallatie meer hoeven in te richten.” ●
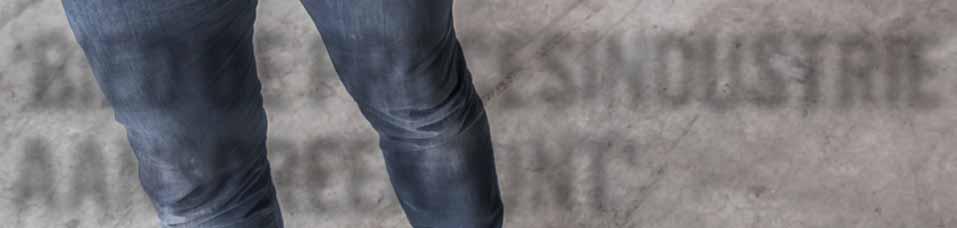
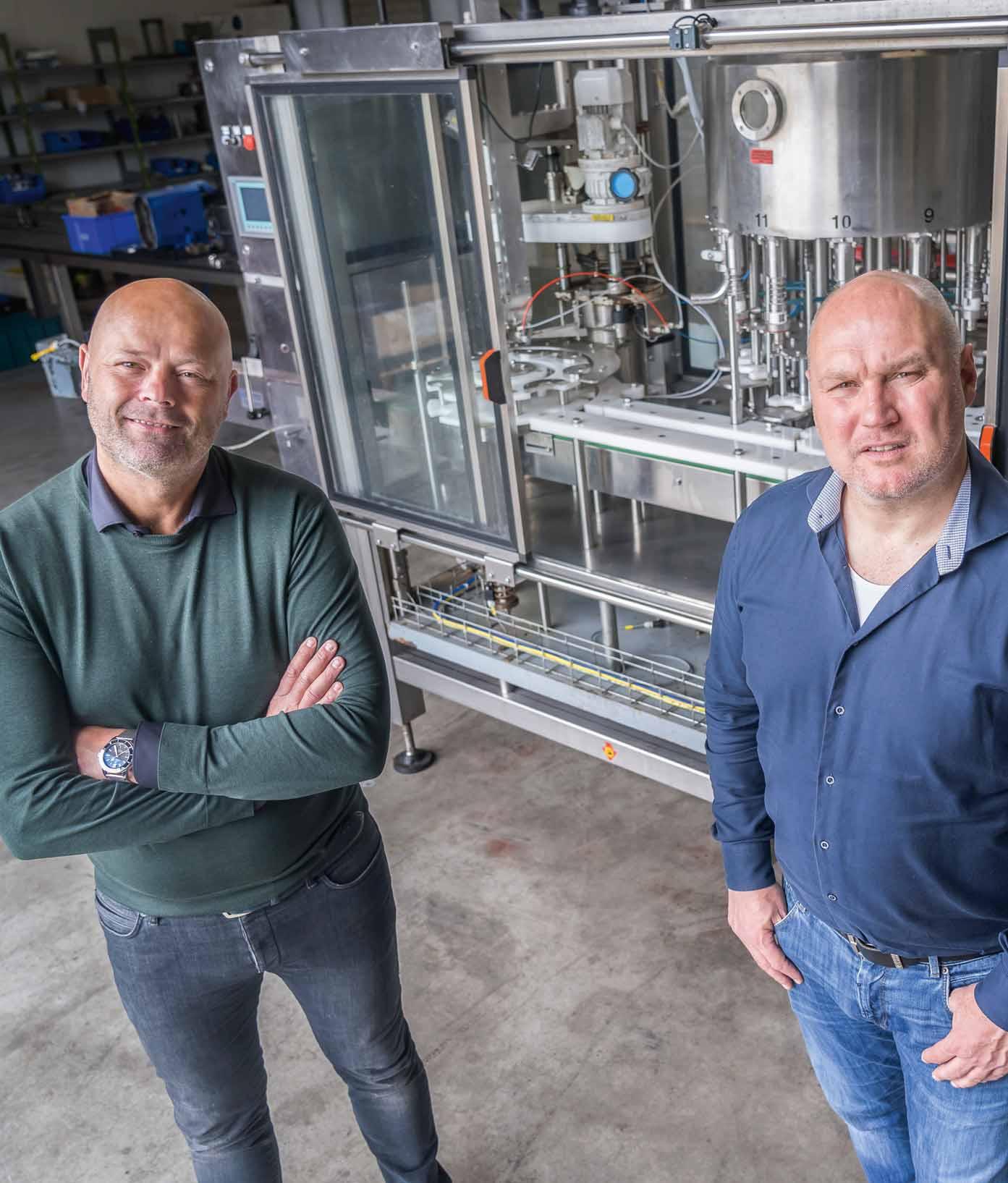
Eén aanspreekpunt, korte lijnen, grip op de kosten en alle disciplines onder één dak. Dat is wat de procesindustrie wil, stellen Michiel Werner van Flowfirm en Richard van den Boogaard van Strakker Doren Engineers. De engineeringspecialist en bouwer van proceslijnen de industriële ICT-specialist bundelen de krachten in Starcker. ‘Klanten zijn op zoek naar het totaalplaatje’
Flowfirm en Van Doren Engineers zijn al langer kind aan huis bij de grote namen in de food en farmaceutische industrie. Regelmatig werken de bedrijven intensief samen bij klanten. Flowfirm als specialist in ontwerp, engineering en bouw van procesinstallaties en Van Doren als expert in elektrotechniek, industriële automatisering en productie-ICT. “Vaak ging het dan om afzonderlijke opdrachten”, vertelt manager operations Richard van den Boogaard van Van Doren. “De klant gaf een stuk van een project aan ons en een deel aan Flowfirm. Als je dan niet oplette, kwam je ook wel eens tegenover elkaar te staan. We merkten dat de knowhow niet altijd aanwezig is bij klanten, om een goede match te maken.”
TOTAALPLAATJE “Klanten gaven zelf aan behoefte te hebben aan één aanspreekpunt en aan één partij die hen totaal ontzorgt, van het bedenken van een oplossing tot aan de uitvoering, de oplevering en service en onderhoud van een installatie. Ze zijn op zoek naar het totaalplaatje”, vervolgt Van den Boogaard. Om aan deze wens gehoor te geven, staken de beide bedrijven de koppen bij elkaar en kwamen tot de oprichting van een gezamenlijke onderneming: Starcker. “Een krachtige naam”, zegt managing director Michiel Werner van Flowfirm, “die benadrukt dat we elkaar aanvullen. Samen hebben we ruim 450 specialisten in huis. Alle benodigde kennis en disciplines zitten onder één dak. Klanten hebben één aanspreekpunt en iedereen kan sneller schakelen. We hoeven niet langer naar elkaar te wijzen, want we maken één planning. Dat betekent ook dat de perceptie bij onze medewerkers anders wordt. Bij elke aanvraag die we binnenkrijgen, stellen we de benodigde expertise uit de eigen gelederen samen. In de toekomst zullen onze mensen steeds nadrukkelijker in een Starcker-omgeving gaan werken. Naar buiten toe hebben ze al uniforme werkkleding. Het moet voor hen voelen alsof ze deel van het Nederlands elftal uitmaken. Intern hebben we onze medewerkers goed geïnformeerd wat het doel van Starcker is.”
KOSTENBEHEERSING Van den Boogaard en Werner zien dat procesbedrijven grote moeite hebben om bij uitbreidings- en vernieuwingsprojecten budgetten te bepalen en te beheersen. “De tendens is dat alles aan de voorkant niet goed is dichtgetimmerd en dat leidt dan tot kostenoverschrijdingen, omdat iedereen snel van start wil gaan”, legt Werner uit. “Wij beloven de klant dat als we eerder bij hem aan tafel zitten, hij meer grip krijgt op zijn investeringskosten”, vult Van den Boogaard aan. “We kunnen dan de juiste gegevens verzamelen en de juiste stappen voorstellen, zodat de klant een installatie krijgt die werkt en binnen budget klaar is. Bovendien brengen we niet alleen proceskennis in, maar ook expertise in het schrijven van software en het generen van rapportages.” Inzicht in hoe installaties lopen, weet Van den Boogaard, is een absolute trend. “Bedrijven willen de data terug kunnen halen over batches die mis zijn gelopen. Dat zie je zowel in de food als de farma. Productveiligheid staat voorop. Ook daarvoor moet je vroeg aan tafel zitten, wil je straks aan de juiste knoppen kunnen draaien.”
Richard van den Boogaard, Starcker
ONAFHANKELIJK Werner benadrukt dat Starcker onafhankelijk is in de keuze welke apparatuur ingezet gaat worden. “Als je als bedrijf met de grote technische dienstverleners aan tafel zit, ben je veroordeeld tot hun merk equipment. Wij kijken naar het onderscheidend vermogen dat de klant kan creëren. Al zullen we niet aarzelen een bewezen concept te introduceren. Onze technologen en engineers hebben voldoende bagage om verschillende concepten voor te leggen.” Het soort projecten waar beiden aan denken zijn niet alleen procesmodificaties, productoptimalisaties en veiligheidstrajecten, maar ook de inrichting van volledige proceslijnen. “Bij een aantal van onze klanten komen wij zeker in beeld, als ze een nieuwe lijn gaan bouwen”, zegt Werner. Een recent voorbeeldproject, waarbij de twee bedrijven van elkaars expertise hebben geprofiteerd, is de bouw van een doseerinstallatie voor sauzen bij een fabrikant van aardappelspecialiteiten. Ook zat daar een Cleaning-in-Place (CIP)-installatie bij, om de proceslijn na elke batch te reinigen. “Eerst hebben we een proefopstelling ontwikkeld, om exact de juiste viscositeit van de verschillende sauzen te kunnen bepalen. Dankzij onze krachtenbundeling konden al onze disciplines gestroomlijnd samenwerken”, zegt Van den Boogaard.
KNOWHOW Met Starcker verwachten Van den Boogaard en Werner beter in te kunnen spelen op het gemis aan procestechnologische kennis bij klanten. “Productiebedrijven zijn steeds meer gefocust op de productie”, legt Werner uit, “en niet zozeer op de technische omgeving. De tijd dat procestechnologen en technisch specialisten lange tijd in één fabriek van een bedrijf werkten, is allang voorbij. De expertise rond het functioneren van processen, is niet altijd meer volledig beschikbaar. Wij kunnen dat gat dan opvullen. We zijn goed ingewijd in de productieprocessen van de food en de pharma. Bij de klanten waar we al langer voor werken, kennen we bovendien de eigenschappen van producten en de grondstoffen die ze verwerken. Dat soort knowhow is onze toegevoegde waarde.”
DUURZAAMHEID De twee bespeuren nog een belangrijke wens in de markt: bedrijven willen steeds duurzamer opereren, om zo ook kosten te besparen. “Ze zoeken in hun processen naar technische oplossingen, om toch dezelfde kwaliteit producten te maken maar dan met minder energie of water, bijvoorbeeld door een aangepast productieproces of door warmteterugwinning of hergebruik van proceswater in het proces. Dat laatste hebben we al voor een klant in de aardappelverwerkende industrie kunnen regelen. Daarvoor moest hij zijn warme proceswater nog gewoon lozen”, zegt Van den Boogaard.
UTILITY-PLEIN Een tweede succesvol project uit deze categorie, dat de twee bedrijven samen al hebben gedaan, is het ontwerp en de engineering en het mechanisch
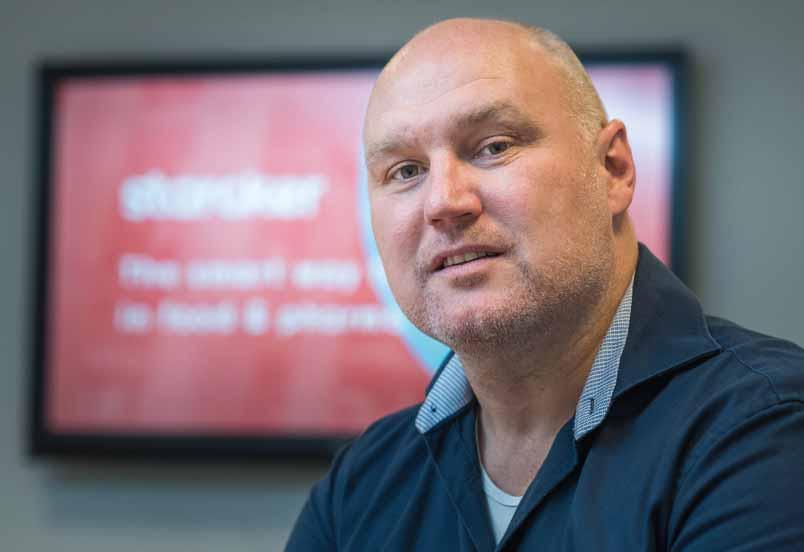
Richard van den Boogaard van Strakker Doren Engineers, expert in elektrotechniek, industriële automatisering en productie-ICT.
gereed maken van een ‘utility-plein’ bij een zuivelfabrikant voor het koelen van het productieproces. “We hebben dat zo efficiënt kunnen doen dat het bedrijf een van zijn koelunits helemaal niet meer hoeft te gebruiken en alleen maar voor het geval van een calamiteit stand-by hoeft te houden”, vertelt Werner. “Ook hier heeft het feit dat onze specialisten organisatorisch zo nauw samen kunnen werken beslist bijgedragen aan het welslagen van dit project. Alles kwam tegelijkertijd gereed en ook binnen budget.”
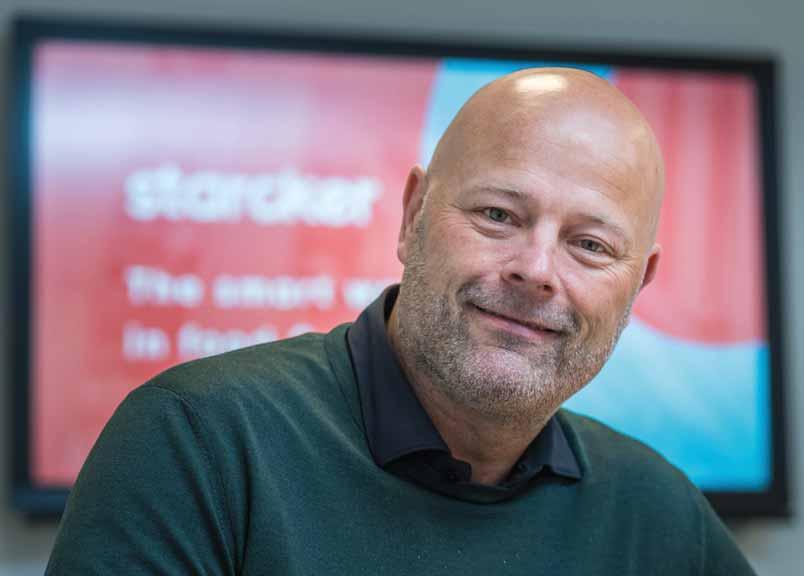
Michiel Werner, Starcker
LEERFABRIEK Dat betekent ook, beseffen beiden, dat Starcker de eigen technische bagage op peil moet houden. De schaarste aan gekwalificeerd technisch personeel is overal voelbaar. Maar daar is wat op gevonden. De twee gaan gezamenlijk een leeromgeving inrichten, en wel een limonadefabriek. “Het gaat niet zozeer om dit product”, vertelt Werner, “maar in deze fabriek kunnen studenten van de verschillende opleidingen in een echte productieomgeving de standaardprocessen in de vingers krijgen. Er komt ook een escape-room bij: doel is samen als team een procesinstallatie aan de gang krijgen.” De onderdelen van de fabriek zijn al gekocht. Begin volgend jaar moet de leerfabriek operationeel zijn. “We kunnen als land alleen onze positie als tweede voedselproducent van de wereld behouden, als we investeren in de technici van de toekomst. Daarom willen we hiermee onze nek uitsteken. We willen iedereen enthousiasmeren voor techniek, ook de jeugd en hun ouders.” ●
Watersector moet kennis op peil houden TOEKOMST DRINKWATERVOORZIEN
De ontwikkelingen op het gebied van de digitalisering van de drinkwatervoorziening gaan keihard. Daarom moet iedereen in de watersector zich bijscholen, benadrukken Martijn Bakker (Royal HaskoningDHV) en Jawairia Ahmad (PAO Techniek en Management). “Het accent verschuift van de waterprofessional-met-kennis-vanautomatisering naar de ICT’er-met-kennisvan-water.”
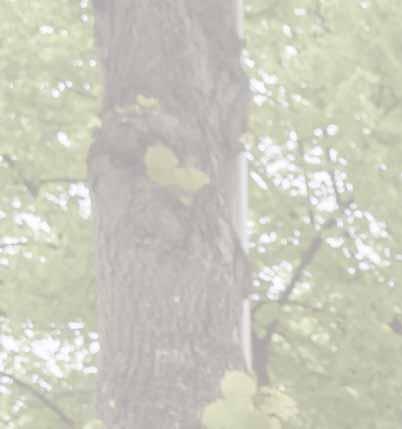
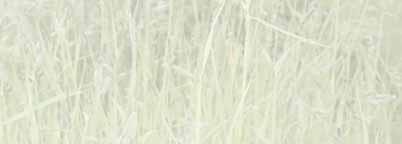
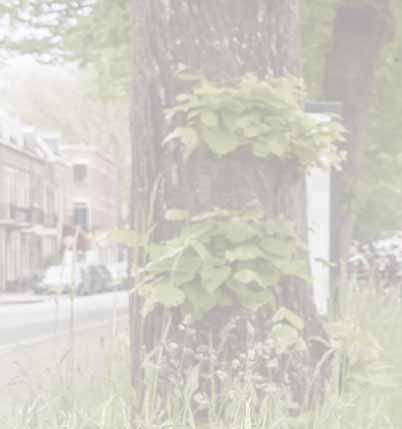
Geen thema zet Nederland internationaal zo op de kaart als de omgang met water. En zo dynamisch als water is, zo dynamisch is ook de kennisontwikkeling over water. Martijn Bakker weet daar alles van. Hij werkt al 25 jaar aan slimme oplossingen voor watersystemen en volgt de ontwikkelingen op de voet. In september organiseert hij een tweedaagse cursus voor PAOTM. Onderwerp is de digitalisering van de drinkwatervoorziening. “Samen met experts van bijvoorbeeld de TU Delft en Microsoft, behandelen we de toepassing van machine learning, digital twins en serious gaming in het drinkwaterbedrijf. En we staan stil bij de dataveiligheid en de cybersecurity: hoe veilig is de cloud en kunnen we daar straks nog wel omheen?”, vertelt hij.
DIGITALISERING ONONTKOOMBAAR Bakker stelt vast dat ICT steeds dominanter wordt in de drinkwatervoorziening. “Vroeger moest je vooral veel kennis van water hebben en een beetje van automatisering, nu moet je ICT’er zijn met kennis van water. Digitalisering is cruciaal voor het optimaliseren van het watermanagement.” Digitalisering is ook onontkoombaar geworden doordat de kennisdragers met pensioen gaan. “Het is zo goed als onmogelijk om nieuwe mensen te werven die over dezelfde hoeveelheid kennis beschikken. We hebben het namelijk over kennis die in tientallen jaren is opgebouwd en die vaak onvolledig in systemen is vastgelegd. Tel daarbij op dat mensen tegenwoordig minder lang in dienst blijven van een onderneming en je begrijpt dat slimme controle- en monitoringsystemen noodzakelijk zijn. Die maken het ook meteen mogelijk om met minder mensen méér pompstations aan te sturen.”
IN DE CLOUD De toekomst van de drinkwatervoorziening ligt in de cloud, zegt Bakker. Toch zijn drinkwaterbedrijven nog terughoudend om over te stappen op de cloud. “Ik begrijp dat wel: het is vitale infrastructuur en drinkwaterbedrijven willen die beschermen. Je moet er ook niet aan denken dat ze gehackt worden! Maar in de toekomst zullen bepaalde applicaties niet meer buiten de cloud beschikbaar zijn, wat de overstap onvermijdelijk maakt. Het gaat er dus om, dat ICT-infrastructuur van de drinkwatervoorziening aan de allerhoogste veiligheidsstandaarden voldoet.” Zelf is Bakker overtuigd dat de cloud een verantwoorde keuze is, maar hij begrijpt dat het eisen stelt aan de organisatie van drinkwaterbedrijven; de ICT-kennis moet omhoog.
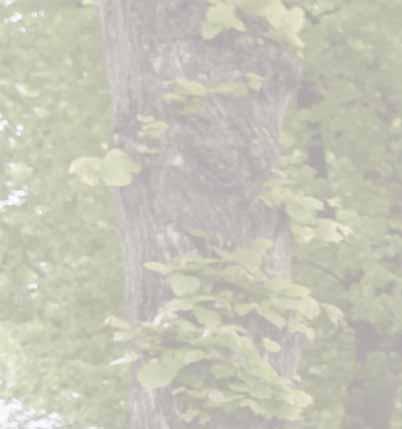
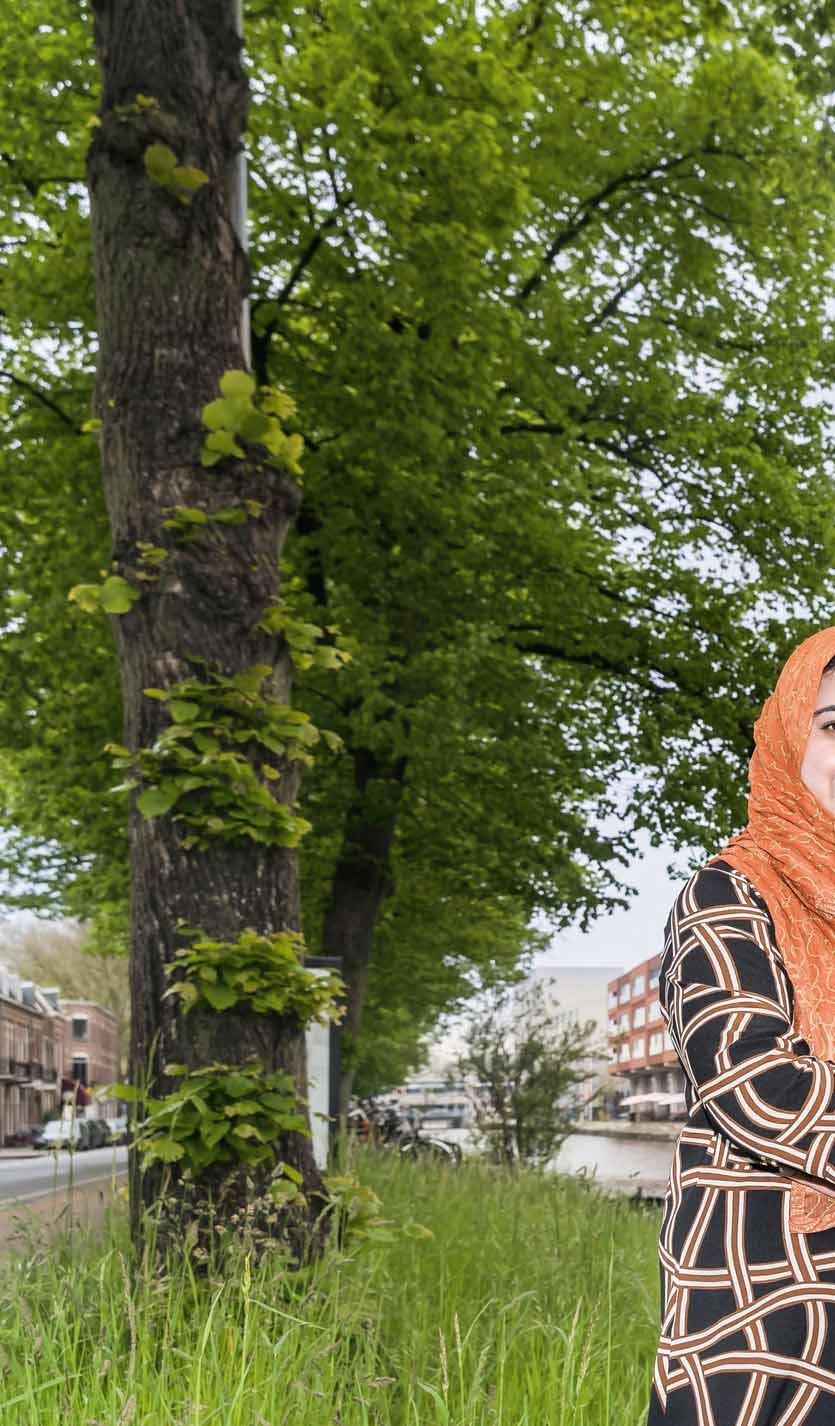
VERBRUIK Een derde ontwikkeling is het matchen van vraag en aanbod van water. “Het wordt steeds moeilijker om die op elkaar af te stemmen”, zegt Bakker. “Het drinkwaterverbruik zal omlaag moeten en de bedrijven hebben daar een rol in. Ook hier kan digitalisering helpen, bijvoorbeeld door het installeren van slimme meters.”
ACTUELE THEMA’S De digitaliseringscursus is onderdeel van het waterprogramma van PAOTM. “Ons waterprogramma biedt cursussen over alle aspecten van de watercyclus”, zegt Jawairia Ahmad. “We delen die in naar vier thema’s: oppervlaktewater, drinkwater, afvalwater en water in de circulaire economie. De cursus digitalisering gaat bijvoorbeeld over de drinkwatervoorziening, en heeft een lijn naar andere cursussen binnen dit thema.” Ieder jaar kijkt PAOTM wat binnen de verschillende thema’s actueel is. Ahmad: “We stellen de cursus samen op basis van de laatste ontwikkelingen en nieuw onderzoek en innovatie. Daardoor kunnen deelnemers steeds verder bouwen aan hun kennis en zo van meerwaarde zijn voor hun werkgever.” Aansluitend op de thema’s biedt PAOTM ook gratis webinars aan met de topexperts in hun vakgebied. “Die gaan in op actuele ontwikkelingen in de watersector, zoals de klimaatverandering of de komst van nieuwe typen verontreiniging in het oppervlaktewater.”
GIDSLAND De ruim 100 cursussen van PAOTM zijn gericht op Nederland en Vlaanderen. Doelgroepen voor de cursussen op het gebied van watertechnologie zijn waterschappen, drinkwaterbedrijven, industrie en Rijkswaterstaat. Jawairia Ahmad: “We hebben zo’n 1500 Nederlandstalige cursisten. Maar we krijgen steeds meer vragen uit het buitenland. Want wat hier speelt, speelt wereldwijd en Nederland is toch voor veel landen een gidsland op het gebied van watermanagement. Daarom gaan we ook Engelstalig aanbod ontwikkelen. Deze trainingen zullen wel een ander karakter krijgen, want de cursussen in Nederland zijn klassikaal, met veel aandacht voor interactie en met kleine groepen. Voor het buitenland ontwikkelen we andere formats. Maar we zullen daar ook weer kennis ophalen die we in Nederland kunnen gebruiken. We zien er naar uit!” Dat geldt ook voor Martijn Bakker, die in september aan de start staat. “Het is hartstikke leuk om samen met collega-experts deze cursus te ontwikkelen en zo bij te dragen aan optimalisatie van het waterbeheer.” ●
ING LIGT IN DE CLOUD
Jawairia Ahmad (PAO Techniek en Management) en Martijn Bakker (Royal HaskoningDHV)
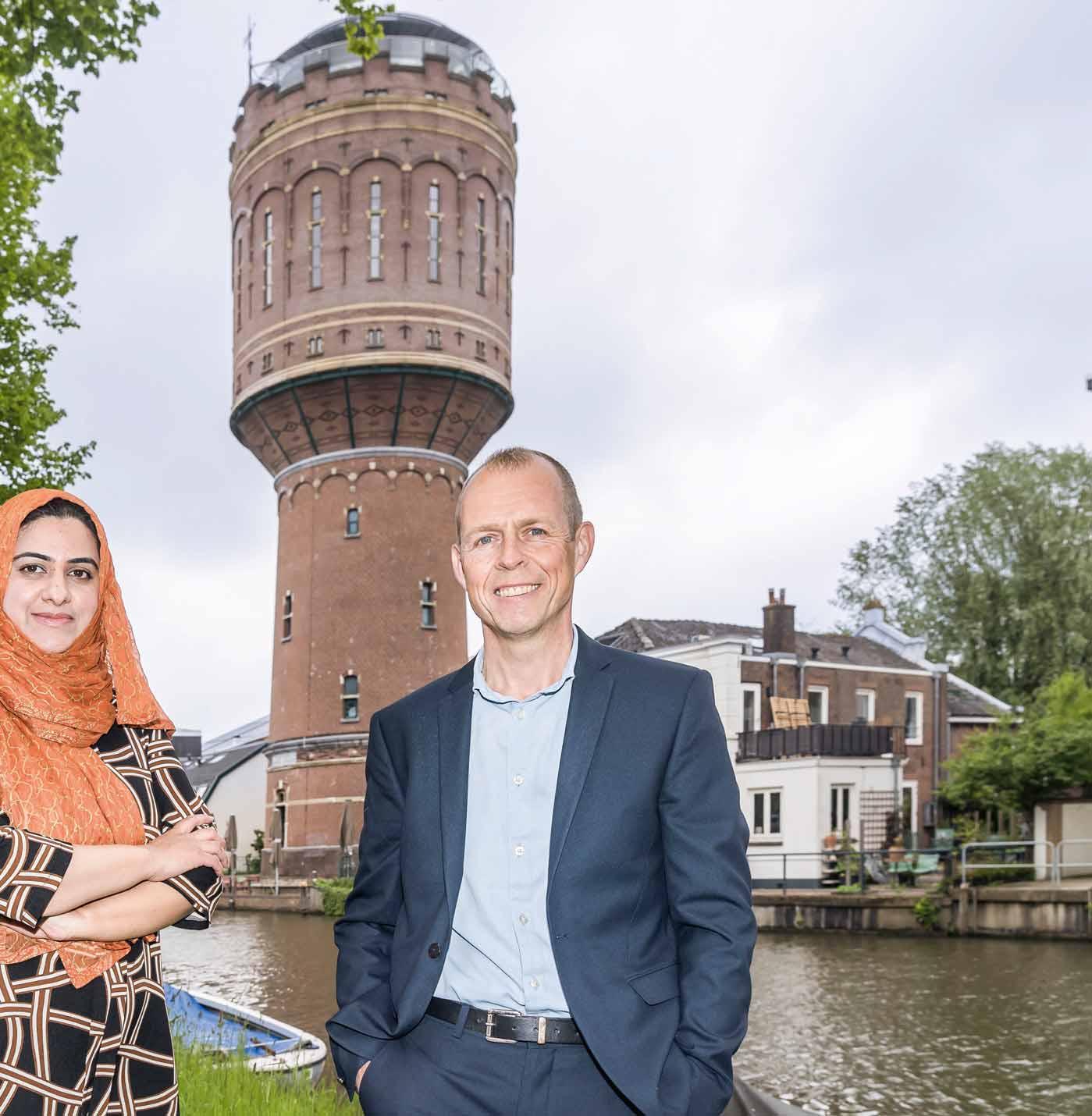
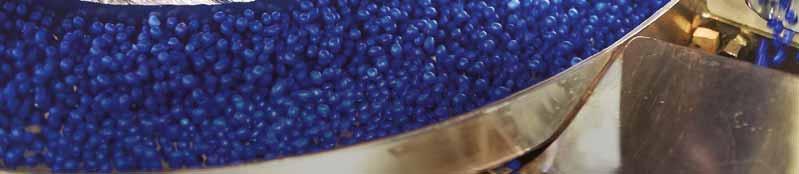
Newsline Newsline
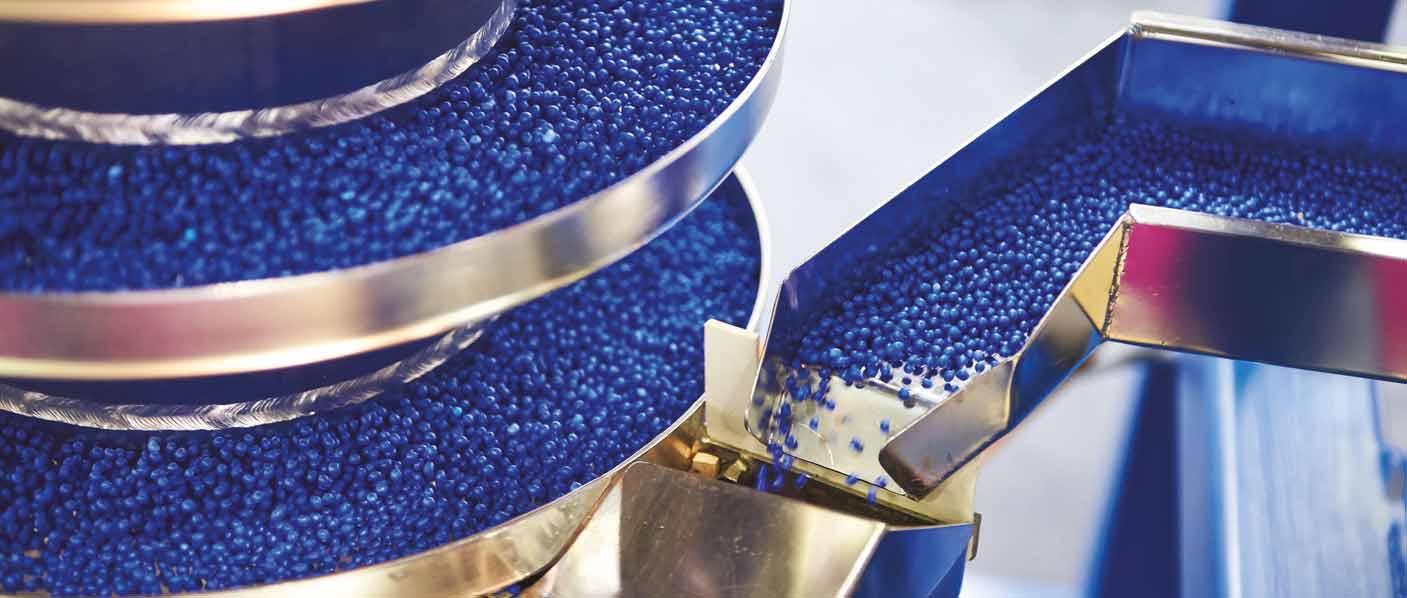
CHEMIE
Krachten bundelen voor terugdringing van CO2-uitstoot
De chemiesector ligt al jaren onder een vergrootglas. Begrijpelijk, want de veiligheid voor mens en omgeving spelen hierin een belangrijke factor. De processen worden gelukkig steeds effi ciënter en digitaal monitoren om de procesveiligheid te verhogen is dan ook niet meer weg te denken. Ook het reduceren van de CO2-uitstoot en de verduurzaming van de producten bieden nieuwe mogelijkheden. Verschillende initiatieven zijn hiervoor opgestart. Denk aan het inzetten van waterstof om de gasleiding “CO2” vrij te maken. Waterstof wordt hierbij rechtstreeks in het aardgasnet geïnjecteerd. Of door chemische recycling van plastic producten die mechanisch niet te recyclen zijn. Dit zijn voornamelijk huishoudelijke producten; uiteindelijk gaat dit weer zorgen voor duurzame grondstoffen. Zo bespaar je ook weer CO2. Bedrijven zullen meer gebruik gaan maken van elkaars kennis en kunde. KROHNE heeft op het gebied van procesveiligheid een compleet pakket aan meetinstrumentatie samengesteld. Zoals de drukmeetsensoren OPTIBAR met SIL-goedkeuringen, voor moeilijke omgevingen en digitale communicatie opties, eenvoudig via je mobiele telefoon te bedienen. Maar ook de MFC 400 een massafl owsignaalversterker voor alle KROHNE Coriolis massafl owmeters. De diagnostiek hiervan is conform de NAMUR-norm NE 107 voor status- en foutafhandeling. Dit maakt niet alleen uitgebreide (zelf)controle van de interne circuits en informatie over de gezondheid van de fl owsensor mogelijk, maar geeft ook belangrijke informatie over het proces en de omstandigheden. Met de inzet van de juiste meettechniek kunnen de processen effi ciënter en veiliger worden ingericht en deze tools helpen ook om uw medewerkers veiliger hun werk te kunnen laten uitvoeren. Uitgave 3 | 2021
Scherpe focus op veiligheid
OPTIWAVE radar niveaumeters, met hoge signaaldynamiek voor continue contactloze niveaumeting zijn SIL 2/3 compatible volgens IEC61508 en voldoen aan de hoogste veiligheidsnormen om uw personeel en installaties te beschermen.
Verstoringen van tankwanden, interne obstakels of lange sproeiers vormen geen uitdaging. De zeer kleine richtingshoek zorgt voor een scherpere focus op uw medium, of het nu vloeistof of vaste stof is. OPTIWAVE 7500 is ontwikkeld voor vloeistoffen in moeilijke omgevingen. • Toepassingen: Oplosmiddelen, zuren, schuimmiddelen, meststoffen (b.v. ureum), chloor, harsen, verf, inkt, corrosieremmers
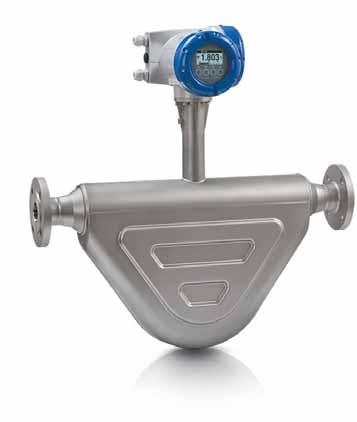
Highlights OPTIMASS 6400
• Coriolis-massafl owmeter voor geavanceerde procestoepassingen met hoge nauwkeurigheidseisen (meetfout: ±0,05% vlak) • Blijft meten over een brede range aan gasfracties en complexe fl owcondities (EGM™)
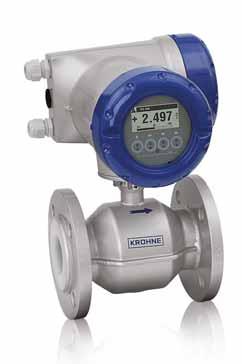
Highlights OPTIFLUX 4300
• Elektromagnetische fl owmeter voor geavanceerde doseertoepassingen met chemicaliën • Hoge nauwkeurigheid (±0,2% meetfout), gecertifi ceerd voor ijkwaardige meting
Modulaire oplossing voor dosering van speciale chemicaliën
• Real-time procesregeling van additieven in lijn met productiesnelheid van papiermachines • Consistente aanmaak van emulsies, dankzij nauwkeurige en herhaalbare fl owmeting • Coriolis massa- en elektromagnetische fl owmeters voor skid-gemonteerde unit Het in de VS gevestigde EGM produceert proces- en chemische doseer / aanmaaksystemen voor verschillende industrieën. Zoals het ontwerp en de bouw van ASA (alkenyl succinic anhydrides) emulgeerinstallaties voor de papierindustrie. EGM bouwde, voor een leverancier van chemicaliën, een emulgeer / meng-skid voor de aanmaak van speciale chemicaliën. Ontworpen voor de bereiding van ASA sizing-emulsie, een medium dat bij de productie van papier cruciaal is, voor het waterbestendig maken van papier. Het aanmaken van de ASA-emulsie bestaat uit ASA, samen met een kationische emulgator en verdunningswater. De mengverhoudingen zijn afhankelijk van de volgende factoren: de eigenschappen van de papiervezel, de
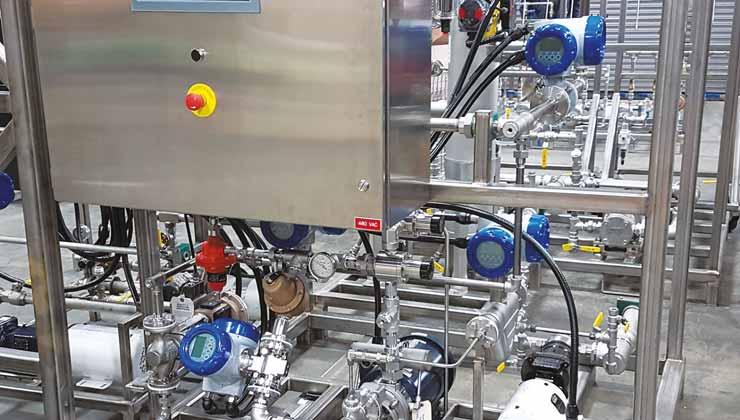
OPTIMASS 6400 C gebruikt om de ASA-fl ow te meten. De Coriolis-massafl owmeter levert superieure prestaties in doseertoepassingen. De meter is ontworpen voor zeer nauwkeurige metingen (met een meetfout van slechts 0,05 % in vloeistoftoepassingen) en een uitstekende herhaalbaarheid. Dankzij Entrained Gas Management (EGMTM) blijft de fl owmeter meten over een brede range aan gasfracties en complexe fl owcondities. De emulgator is watergedragen en wordt gemeten met de OPTIFLUX 4300 C. Bovendien wordt de elektromagnetische fl owmeter ook gebruikt voor meting van primair en secundair verdunningswater en voor de hercirculatiesnelheid van de mengpomp. De fl owmeter is geschikt voor kritische toepassingen, die hoge nauwkeurigheid en uitgebreide diagnostische functies vereisen. productiesnelheid van de papiermachine en het “soort” papier wat gemaakt wordt. De kationische lading van het mengsel zorgt ervoor dat het mengsel bij de vezel blijft tijdens het vormen van een vel papier. Vervolgens gaat het door de droger en “hardt” de chemische stof uit en is het papier waterbestendig. Om dit te kunnen volgen moeten er snelle, nauwkeurige en reproduceerbare fl owmeters toegepast worden, die zeer goed en accuraat met een regeling samenwerken, om de gevraagde emulsie te produceren. KROHNE meters werden getest en bleken perfect geschikt voor deze toepassing. Op het gebied van nauwkeurige en reproduceerbare fl owmeting voldeden ze volledig aan de eisen van de klant en bleken bovendien kostenconcurrerend.
De doseer-skids zijn uitgerust met de OPTIMASS 6400 C Coriolis-massafl owmeter en de OPTIFLUX 4300 C elektromagnetische fl owmeter. Aangezien ASA een chemische stof op oliebasis is, dus niet geleidend, wordt de
Met een breed scala aan liners en elektrodematerialen, geschikt voor veel producten, zelfs voor vele corrosieve of abrasieve chemicaliën.
Voor skids worden de compacte varianten (C) van de fl owmeters gebruikt. De meetwaarden worden doorgegeven aan de PLC van de gebruiker. Door de inzet van de OPTIMASS 6400 en OPTIFLUX 4200 fl owmeters, is de samenstelling van de sizing emulsie altijd correct en is een nauwkeurige regeling van alle fl ow mogelijk. De PLC is geprogrammeerd om de additieven in real-time te kunnen regelen en als de productiesnelheid van de papiermachine verandert. Naast een nauwkeurige dosering en reproduceerbare prestaties, maken de fl owmeters compacte inbouw in een relatief kleine ruimte mogelijk en is het systeem voor de eindgebruiker dan ook gemakkelijker te onderhouden.
Geen proces zonder druk
Druk en differentiële druk zijn fundamentele en veel gemeten procesvariabelen, voor de regeling en veiligheid van chemische- en petrochemische processen. Of het nu gaat om de procesdruk, niveaumeting in druksystemen, de verschildruk in distillatiekolommen, warmtewisselaars, strainers of fi lters of DP-fl owmetingstoepassingen, druk is overal in het hele proces terug te vinden. In de chemische industrie zijn er specifi eke eisen voor drukmeting, met name voor de procesveiligheid en toepasbaarheid, rekening houdend met de procesmedia en de omstandigheden. Naast goedkeuringen voor gevaarlijke omgevingen, zijn in kritische processen ook SIL2/3-gecertifi ceerde instrumenten vereist.
KROHNE heeft voor de chemische industrie een serie speciale OPTIBAR druk- en drukverschiltransmitters en accessoires, zoals membraanafdichtingen, manifolds en primaire fl ow-elementen. Een keuze aan materialen, coatings zoals tantaal, titanium, Hastelloy©, rhodium, goud, maar ook vulvloeistoffen voor hoge temperatuur, hoog vacuüm of reactieve processen, zijn beschikbaar. Het complete instrumentatieportfolio van druk, verschildruk en ook elektronische verschildruk ondersteunt ook alle digitale communicatie opties, zoals Foundation Fieldbus, Profi bus PA, 2-draads analoog met HART 7, allen optioneel confi gureerbaar via een handige Bluetooth interface en iOS of Android mobiele apparaten. 700 bar hogedruk uitvoering van de KROHNE OPTIBAR DP 7060 transmitter, voor veeleisende fl owmeting van waterstof.
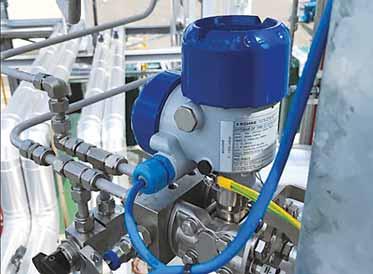
OPTIBAR PM/PC 5060 eDP
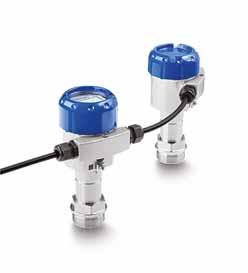
Master Slave
OPTIBAR DP 7060 C 316L
316L / 1,4404 Tantalum
Hastelloy C-276 PTFE
Diaphragm Seals & Accessoires
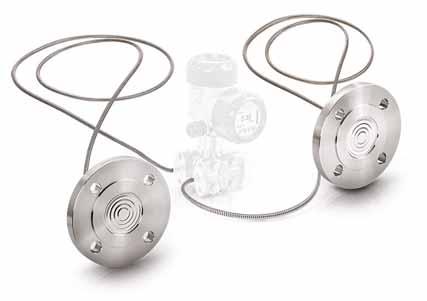
DP Accessoires
3D-Linearisatie
De kern van de OPTIBAR DP 7060 drukverschiltransmitter is KROHNE's unieke 3D linearisatie, die elke individuele DP-cel tijdens de productie op meer dan 400 punten kalibreert op de verschildruk range, omgevingstemperatuur en de geïntegreerde absolute druksensor. Dit garandeert de meest stabiele en nauwkeurige meetresultaten, zelfs onder veranderende of niet-ideale procesomstandigheden. Hierdoor is de DP-transmitter uiterst langdurig stabiel en vermindert deze de noodzaak van kostbare herkalibraties in het veld.
Voor relatieve en absolute drukmeting bieden de OPTIBAR PC 5060 met keramische meetcel en de OPTIBAR PM 5060 met metalen procesmembranen in combinatie, altijd de beste aanpak voor elke meettaak. De robuuste keramische meetcel is zonder extra maatregelen, waterstof- en hoog vacuümbestendig, terwijl de OPTIBAR PM 5060 met metalen sensor, meetbereiken tot 1000 bar biedt en kan worden gecombineerd met de OPTIBAR DS membraanafdichtings-serie. Voor het elektronisch meten van de verschildruk kunnen beiden series ook worden toegepast in een e-DP confi guratie.
Distillatiekolommen
Een typische toepassing in distillatiekolommen is de meting van de opvoerhoogte en de verschildruk over de verschillende secties en trays in de distillatiekolom. De drukken worden gemeten voor een effi ciënte procesregeling en om het vollopen van de kolom te voorkomen. Absolute drukken kunnen zeer laag zijn, afhankelijk van het specifi eke proces. Drukverschilmeting met een OPTIBAR DP 7060 transmitter is mogelijk, evenals DP-meting door twee afzonderlijke OPTIBAR PM 5060 druktransmitters in een elektronische DP-opstelling (eDP). In dit geval fungeert één transmitter als master en de andere als slave.
Totaal-leverancier voor toonaangevend chemieconcern
Onze kennis van drukmeting is niet onopgemerkt gebleven. Na een uitgebreide test werd KROHNE gekozen als totaal-leverancier voor het OPTIBAR drukportfolio door een wereldwijd chemieconcern met het hoofdkantoor in Duitsland. De geavanceerde instrumentprestaties, een compleet portfolio, inclusief hoge druk versies tot 700 bar, geschikte materialen inclusief tantaal membraanafdichtingen, SIL-goedkeuringen en de digitale communicatie opties, waren essentiële criteria voor deze beslissing. Inmiddels zijn een honderdtal OPTIBAR DP 7060, OPTIBAR PC 5060 en OPTIBAR PM 5060 met bijbehorende membraanafdichtingen en accessoires wereldwijd aan verschillende locaties geleverd en heeft het chemieconcern de druk onder controle.OPTIBAR DP 7060 in een chemische distillatiekolom
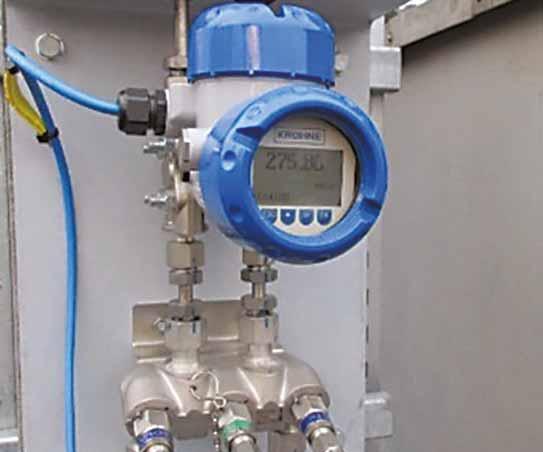
De rol van waterstof
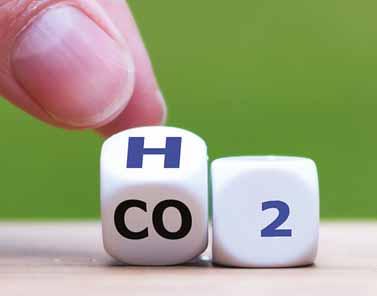
Om te voldoen aan de klimaatdoelstelling, de CO2-uitstoot verminderen met 49% in 2030, zal de industrie ook haar verantwoordelijkheid nemen. KROHNE biedt in haar toekomstvisie oplossingen voor lokale en internationale wetgeving, bijvoorbeeld door het effi ciënt inzetten van de juiste meettechniek in moeilijke applicaties. Zoals het Franse Jupiter 1000 “power-to-gas”demonstratieproject. Hier wordt via elektrolyse van water, hernieuwbare energie gebruikt om waterstof te produceren. Deze groene waterstof wordt op twee verschillende manieren gebruikt om het aardgasnet “CO2” vrij te maken: door waterstof rechtstreeks te injecteren in het aardgasnet, of door synthetische methaan, dat ontstaat uit een reactie van waterstof met afgevangen CO2, in het aardgasnet te injecteren. Verschillende soorten gassen en gasmengsels worden hierbij gemeten. Zoals H2, synthetisch CH4, afgevangen CO2 en aardgas. De klant wenste een lage drukval en weinig onderhoud, om de bedrijfskosten van de installatie te minimaliseren.
KROHNE leverde voor meting van de verschillende gasstromen de Coriolis, ultrasone en Vortex fl owmeters. Alle fl owmeters konden worden aangesloten op één enkele SUMMIT 8800 fl owcomputer en bovendien werden de kosten hierdoor ook teruggedrongen. Voor de productie van groene waterstof uit hernieuwbare energie, worden water elektrolyzers ingezet. Voor procescontrole worden in deze systemen drukmetingen uitgevoerd. Waterstofmoleculen veroorzaken materiaalstress op de rvs-membraan van de druksensor. Om deze waterstof-brosheid te voorkomen, is toepassing van druksensoren met vergulde membranen en vergulde afdichtingsvlakken of keramische membranen een goede oplossing. KROHNE leverde hiervoor de OPTIBAR DP 7060, OPTIBAR DSD 3220, OPTIBAR PC 5060 druksensoren.
Onze adviseurs denken graag mee om ook voor uw duurzame projecten de juiste meettechniek samen te stellen.
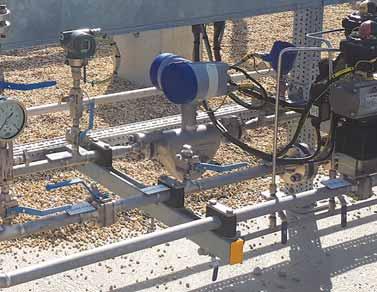

KROHNE Academy online
Met KROHNE Academy online trainingen bent u altijd op de hoogte van de laatste ontwikkelingen op het gebied van procesinstrumentatie. Het leerplatform, biedt digitale e-learning cursussen (niet commercieel) over verschillende onderwerpen, zoals: grondbeginselen en meetprincipes, entrained gas management, functionele veiligheid (SIL) en grondbeginselen van gasmeting. De Academy geeft u niet alleen directe toegang tot de kennis en uitgebreide ervaring van KROHNE. U krijgt ook de laatste informatie over normen en voorschriften van e-learning cursussen, zoals bijvoorbeeld ‘Functionele veiligheid (SIL)’, die we in samenwerking met onze partners ontwikkelen. Neem voor meer informatie contact op met:
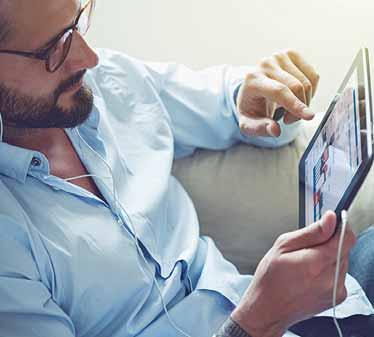
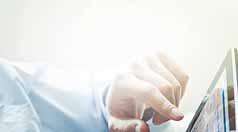
KROHNE Nederland B.V. Postbus 110 3300 AC DORDRECHT Kerkeplaat 14 3313 LC Dordrecht Nederland Tel.: +31 (0)78 - 6306 200 e-mail: infonl@krohne.com
www.krohne.com