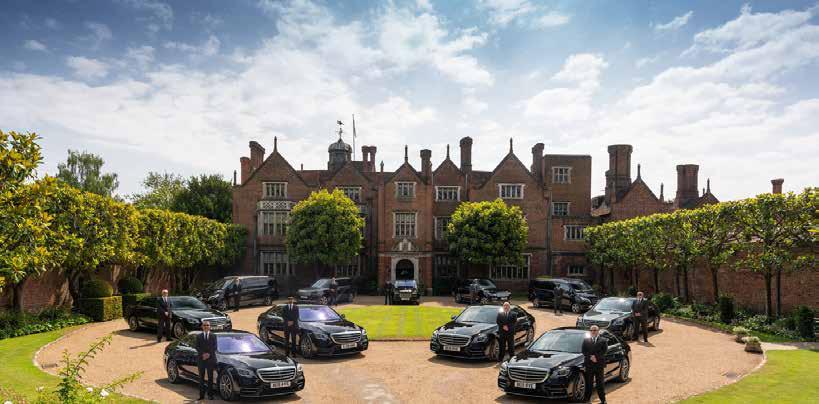
4 minute read
analysis: battery production
zones have been set up, offering tax relief for EV production.”
Speaking in 2021, Maros Sefcovic, European Commission VP for Interinstitutional Relations, said: “I am confident that by 2025, the EU will be able to produce enough battery cells to meet the needs of the European automotive industry, and even to build our export capacity.”
Whether that export capacity will be heading to the UK is another matter. It’s likely that demand from EU plants will soak up all the supply from the new gigafactories. It may prove easier for automakers to move their production closer to the batteries, given the significance of the battery as a proportion of the EV’s costs.
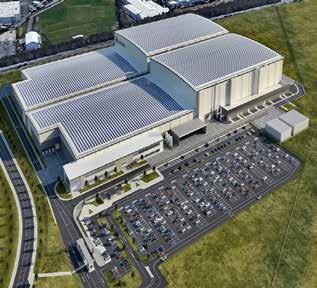
Prof Bailey believes this is likely: “The danger for the UK is that auto assembly will move to where the batteries are available cheaply. And that raises an existential question over the future of UK auto going forward unless battery production is built up quickly in the UK.”
The SMMT’s Full Throttle report calculates that by 2030, when the ban on new combustion-engined cars comes into force, the UK auto industry will require at least 60 gigawatt hours of locally sourced batteries. Even this would only maintain annual production of 1 million new cars. Less than current capacity of 1.3m.
Are we nearly there yet? Far from it. Only Nissan has any form of installed battery capacity, and that is just 1.7GWh to support Leaf production in Sunderland. But Nissan is at least doing what the other EU-based manufacturers are doing, which is colocating with a supplier-partner (Chinese firm Envision-AESC). An investment of around £1bn has been earmarked to increase capacity to 9GWh by 2025, which will support production of 100,000 nextgeneration Leafs a year, and a further £1.8bn could take the Gigafactory up to 25GWh by 2030.
But that would be less than half of the required total, and would only supply Nissan. BMW, Toyota, Stellantis and JLR, as well as Ford, which makes ICE engines in the UK, have yet to announce firm plans to build UK gigafactories – and the clock is ticking.
Jaguar Land Rover’s only EV, the Jaguar I-Pace, is built by MagnaSteyr in Austria, not in the UK. JLR is, however, close to announcing its own battery plant at Bridgewater, which would supply all its UK plants. But this is dependent on receiving Government grants of up to £1 billion.
While the tabloid press trumpets this a “Brexit success”, claiming the site was chosen over one in Spain, industry observers know that a Spanish plant would make no sense for a company with no assembly line in Spain. And funding a multinational’s enterprise via taxpayers’ money is hardly a success. Furthermore, the plant is still nowhere near built – unlike many of the European factories that are already supplying EU-based plants.
BMW stopped making electric versions of the Mini at its Oxford plant in October 2022, and announced that production of the Mini EV models would be shifted to China.
Toyota pinned its colours to hybrids and hydrogen – neither of which look like the winning horse in the clean car race. Its first EV, the BZ4X, has been poorly received. And as we know, Stellantis boss Carlos Tavares is waving his axe over Ellesmere Port, though again, a substantial Government sweetener to help Stellantis build its own battery plant might change his mind.
Without localised production, it could leave the UK industry trying to make EVs using imported batteries from the Far East, which would not meet the TCA RoO rules. The EU tariff for failing to meet them is 10%
– so EV prices – already at a premium over ICE models – would inevitably rise.
Part of the problem is that the UK industry is heavily geared to internal combustion engines. There is a lot of capacity for petrol and diesel engines – capacity that will be superfluous in just over a decade’s time. Toyota in Deeside, BMW in Hams Hall, Ford in Dagenham, JLR in Telford and Nissan itself all invested heavily in ICE production – most of which is intended to serve UK and EU plants.
These plants cannot simply be retooled for EVs. Batteries require very different production techniques. Electric motors are simple, relatively unsophisticated and commodified devices that equally don’t require anything as complex as an engine assembly line. By 2035, these plants will be as redundant as Sony’s Cathode Ray Tube TV plant in Wales was in 2005, when TV technology moved irreversibly to flat screen technologies such as LCD and LED.
What’s worse is the need to get EV battery production up and running even faster than the 2030 or 2035 deadlines. EV demand is growing on one hand – sales increased by 40% in 2022 to 267,203 registrations (16.6% of all new car sales), while plug-in hybrid electric vehicles (PHEVs) made up 6.3% or 101,414 cars. EVs outsold diesels for the first time.
Notably, much of that growth is coming from Chinese-built vehicles, such as MGs, which don’t meet RoO rules but can still undercut UK- or EU-made vehicles as a result of far lower manufacturing costs in China.
It is clear that none of this would be happening if it were not for the immense disruption caused by Brexit. As long as the UK remains outside the Single Market, there will be no incentive for automakers to supply UK plants from EU facilities. It’s just too much of a hassle.
The tide of public opinion is clearly turning away from the failed Brexit project, but there seems little political appetite to rejoin even the Single Market, let alone the EU. It’s no surprise that the Conservative government that created the Brexit mess wouldn’t countenance this, but Keir Starmer’s Labour, fearful of a tabloid backlash and a risk of losing votes in proBrexit constituencies, has also ruled out this sensible move.
It’s quite possible that, unless a seachange in policy happens pretty quickly, the price of the failed Brexit experiment will be the entire British car industry. Brexiters’ blue passports and “sovereignty” won’t recharge their batteries.
Is inter-city travel by EV as easy as with a petrol or diesel car? Not while the infrastructure struggles to deliver the advertised charge speeds. And then there’s the cost. Mark Bursa takes a Kia EV6 to Newcastle and back in order to test the networks