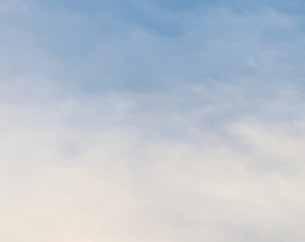
7 minute read
RECOMILL: Ready, Steady, Testplant
from Scope #16 (6/2022)
by Prohoc
READY, STEADY, TEST PLANT!
RECOMILL Oy has opened a new test plant-based on Hydrothermal Carbonization (HTC) in Stormossen Oy premises in Mustasaari near Vaasa, the Finnish energy cluster area. RECOMILL’s HTC technology has not been used similarly in Finland before. RECOMILL recognizes the significant potential of utilizing HTC as a nutrient in the recycling and energy industries. Customers and other stakeholders are welcome to visit and test their waste streams.
The RECOMILL Hydrothermal Carbonization test plant has been prepared and commissioned, and the first hydrochars have been produced. The facility is a modular 40-foot container that offers the possibility to test the customers' waste fractions' suitability for HTC technology before they implement a potential full-size HTC plant.
The plant is run with diverse parameters in the test phase by a joint test plan created with the customer. Analyzing and standardizing test masses for compatibility with the plant is part of the testing phase. In the process, diverse waste materials are exposed to varying temperatures, pressures, and treatment times. These enable the end products to be varied for miscellaneous applications.
TEST YOUR FEEDSTOCK SUITABILITY TO HTC
RECOMILL invites customers and other stakeholders to come to visit the plant site. A visit to the site is easy to arrange, and RECOMILL supports throughout the process, providing its expertise from start to finish. The journey to the test phase begins with an initial discussion with Jan Hägg, RECOMILL's Business Development Director. RECOMILL will send an offer to participate in the feasibility study based on the discussions and customers' needs.
The feasibility study, test run of the customers' waste fractions, and the definition of the end-products will set parameters for the full-scale plant. RECOMILL’s plants' biomass flexibility means the plant is the right solution for many waste challenges.
“The primary option is that the customer delivers the biomass to us, but, if necessary, we can also deliver the test plant to the customer’s premises. The test run takes one to two months, and we will process the gathered data into a project report. We will discuss the results with the customer and then provide a full-scale solution for the right need”, Jan informs.
CHANGING GLOBAL MARKETS
The challenging global situation has changed the waste management market this year. Global demand for circular economy and sustainability solutions has grown significantly, and efforts to reduce the use of virgin materials have increased. The change in the markets reflects in various areas, of which the agricultural sector is one of the most significant. "The availability of fertilizers has decreased, and prices have increased rapidly, posing major challenges for agriculture in terms of profitability," Jan says.
HTC technology enables efficient processing of sludge and other biomasses while also enabling commercial business. The method commonly used in biogas plants is to compost the post-digestate. The treatment process and its various stages to soil enrichment are a long and not cost-effective method. HTC creates the opportunity to produce biochar directly from the digestate, and the previous composting method can be bypassed.
“The HTC method brings significant land area savings and reduces unpleasant odors when you don’t need to store post-digestion in large open fields,” Jan describes HTC technology benefits.
Welcome to visit RECOMILL test plant
RECOMILL will arrange an open doors day to the Stormossen test plant where you can see the test plant in action. Follow RECOMILL's social media channels for more information about the event. To arrange your private visit at the test plant, please contact Jan Hägg.
Jan Hägg
DIRECTOR OF BUSINESS DEVELOPMENT
jan.hagg@recomill.com +358 45 3507 465
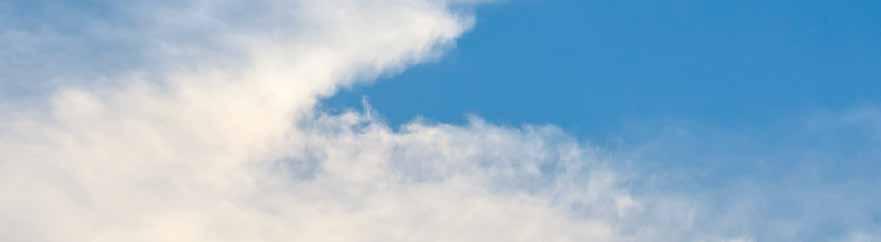
What is HTC?
HTC, Hydrothermal Carbonization is a thermochemical wet coal process. The process converts wet biomass into hydrochar at a 20–30 bar pressure and a 180–230 °C temperature. The process takes from half an hour to eight hours, depending on the feedstock and the requirements of the end product. After the process, the slurry is filtered or centrifuged, separating the solid and water phases. After the dewatering process, the solid material is suitable for producing pellets that can be used, for example, as a fertilizer and soil improvement product. This process also prevents the degrading of the material.
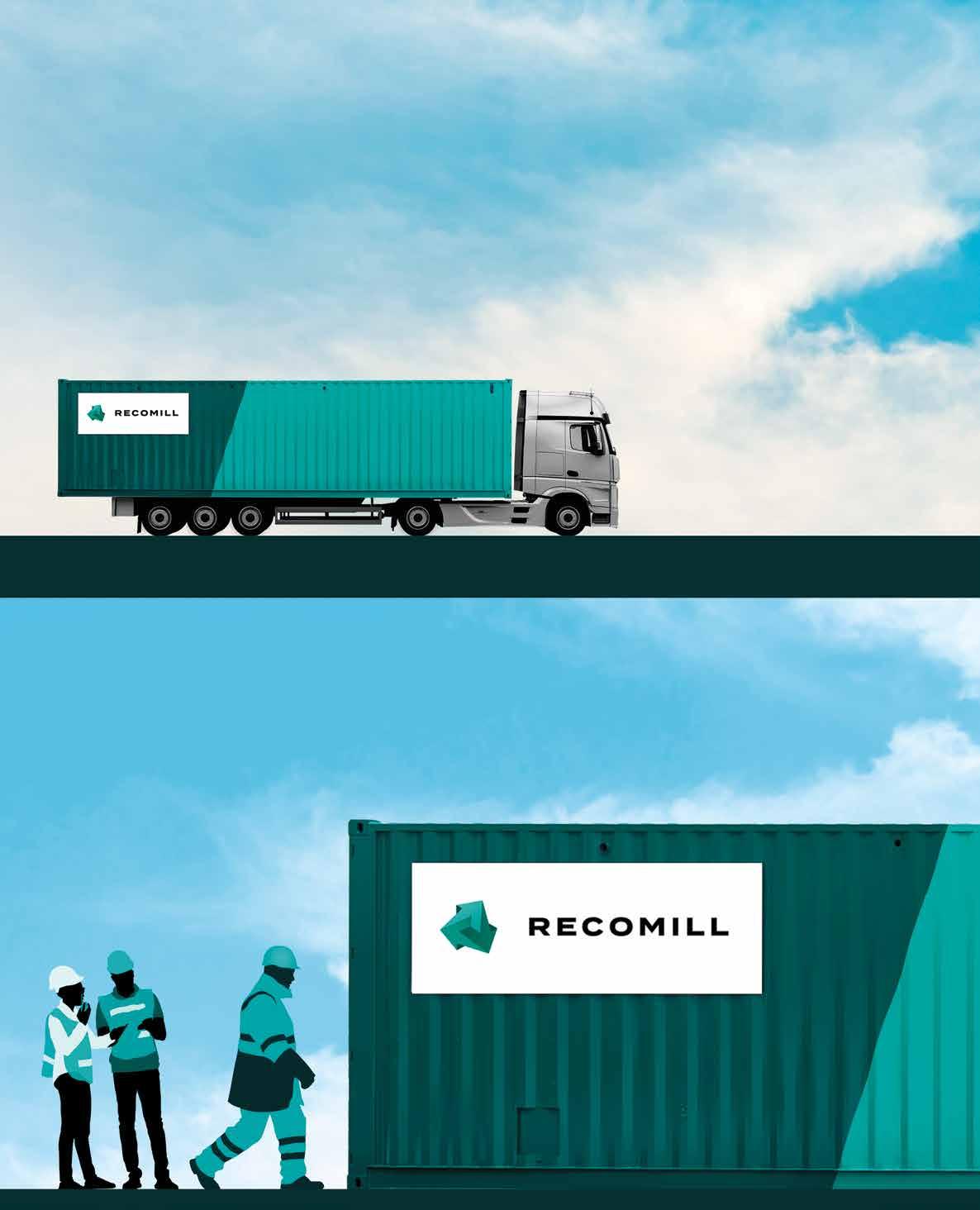
63.128895 21.765885
TEST PLANT
WOIMA
IN THE CORE of
GREEN ENERGY TRANSITION
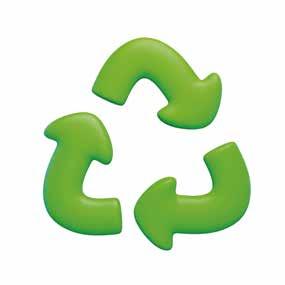
WESTENERGY
L S N
7300 t of clean transport fuels
G Cleantech export to global markets
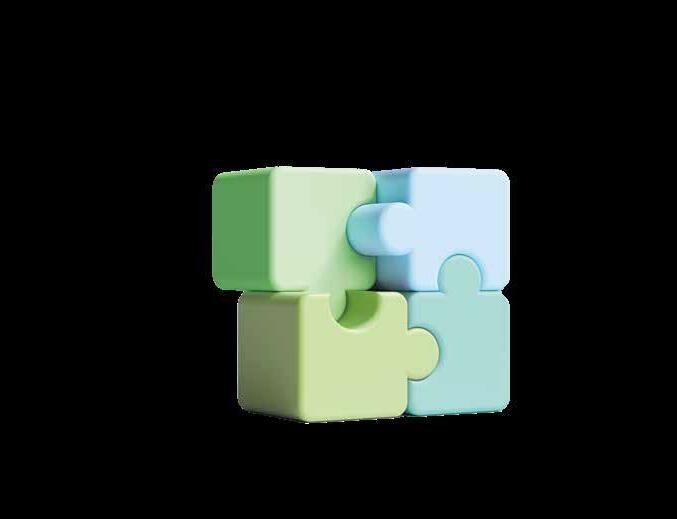
Global warming mitigation is driving the migration away from fossil fuels. This “need for change” is exacerbated by the recent disruptions in global oil and gas production and transmission. This has driven most countries to seek alternatives for imported energy and to increase self-reliance especially in the energy sector. Synthetic methane offers an excellent alternative for traditional transport fuels. Especially, since the infrastructure to store and transport it already exists in most countries.
EnergySampo CCU is the regional cooperation project in Ostrobothnia, Finland aiming at erecting Finland’s first next generation synthetic methane (LSNG) production facility at Westenergy's waste-to-energy site in Mustasaari next to Vaasa. The building consortium is currently finalizing funding for the project, and once confirmed, the plant is scheduled to be built in 2023–2025. The project supports Finland's journey towards carbon-neutral future in line with EU's “Fit for 55” goals, promotes decoupling from fossil fuels and plays a key role in the region's quest for carbon-negative district heating. Vaasa region’s position as the home of the energy cluster in Finland ensures that all technical know-how and expertise is available locally.
LOCAL ENERGY FOR LOCAL BUSINESSES
The plant will have a production capacity of 7,300 tons of LSNG per year (112 GWh). This equals the annual energy consumption of almost 500 trucks, a thousand lorries or two passenger ferries sailing between Vaasa (Finland) and Umeå (Sweden) in the Kvarken. In addition, the process generates excess heat, which is utilized in the local district heating network. The LSNG supply will utilize the existing natural gas and biogas distribution networks, thus enabling and ensuring the efficient utilization of the methane-bound green hydrogen. This will help decarbonize sectors that are hard to electrify, and thus help to limit climate change.
CCU in the project name refers to the capture and utilization of carbon dioxide, an essential part of the new plant concept.
CO2 CAPTURE PLANT
20 000 t/a less CO2 emissions from Westenergy
Renewable electricity & water
FOLLOW THE PROJECT
→ woimacorporation.com
CCU
The next generation power-to-gas value chain
LIQUEFACTION PLANT Added 51 GWh of clean district heating
METHANATION PLANT ELECTROLYSIS PLANT
The ccWOIMA carbon capture solution plays a key role in the process capturing 20,000 tons p.a. directly from the power plant’s flue gas stream. This reduces Westenergy's fossil CO2 emissions by 25%. The other components in the innovative modular plant complex producing the LSNG include the production of hydrogen through an electrolysis process, the combination of hydrogen and carbon dioxide into synthetic methane in the chemical methanation process, and the liquefaction of synthetic methane into transport fuel. The production process is powered by 100% renewable wind energy.
GOING GREEN – FASTER
The EU has set an already aggressive target of 40 GW of electrolysis capacity by 2030. And this target will only rise as investments in green hydrogen and LSNG increase due to the current energy uncertainty. The energy-dense synthetic methane is an excellent medium for the storage and utilization of hydrogen thanks to the already existing gas infrastructure. The replacement of fossil natural gas with synthetic gas fuels will play a significant role in the power generation and transport fuel mix in the coming decades.
WOIMA, with its modular, pre-engineered, and prefabricated carbon capture solution, is in a unique position to serve both the smallto-medium-scale carbon capture market and the LSNG production facility customers globally. The ccWOIMA solution scales flexibly between 20,000 and 200,000 tons p.a. thus offering the exact capacity required by each customer. The modules are easy to transport, fast to install and simple to maintain. The process utilizes widely available low-cost chemical called hot potassium carbonate (HPC) as the process medium ensuring safe and reliable operation throughout the plant lifetime. The energy-efficient solution also offers the lowest capture cost in the market.