
16 minute read
Solid Fertilizer Products
Dry bulk fertilizer products, whether they be within fertilizer factories or at shipping or receiving points, are mainly stored in stockpiles. Employing a pile instead of a high silo is an economical solution for large volumes. In most circumstances, the stockpiles are covered in order to protect both the environment, as the product is prevented from being blown around, and the product itself as it is shielded from being affected by adverse weather conditions.
In most instances where a fertilizer product boasts both a consistent composition and quality from an upstream chemical process, the piles also often function as buffer storage. The piles are thus employed to balance time and volume between production and shipping or to balance reception during interim storage and onward transport to users.
Advertisement
In other instances where there is very little or no consistency, specifically when mined ores of varying qualities and/or characteristics arrive at a chemical plant and require homogenization prior to a chemical process, piles can also be employed as a blending bed. This is often the case for large fertilizer storages, especially those with high throughputs for either stacking, reclaiming or both, and are usually equipped with fully automated stockyard machines. Stockyard machine expertise Tenova Takraf is a global OEM for mining and bulk handling equipment with a history dating back almost 300 years. The company boasts a successful 50 year plus track record of supplying stockyard machines to the global fertilizer industry, with its first scraper reclaimer (for a potash factory) being supplied in 1966. Since then, the company has designed, manufactured, supplied and successfully commissioned around 400 scraper reclaimers across various commodities with a large majority being employed in the effective handling of potash, urea, phosphates and sulphur. Tenova Takraf's approach to this vast array of global projects is “flexibility”. This means they treat the specific requirements of each project in a unique manner, ranging from the supply of a single machine to various machine packages and/or delivery of a complete bulk conveyor system including storage bin machines, conveyor belts and loading & unloading equipment. Such complete handling systems leverage an extended and well established material handling portfolio covering stockyard / disposal facilities, loading / un-loading equipment, conveying, port facilities and in-plant handling equipment.
Stacking and reclaiming In most instances, a storage facility is fed material through a network of conveyors that efficiently carry the product to be stored. In order to achieve an optimal pile width within the storage area, the stacking of material is carried out via overhead tripper cars. Having supplied machines with capacities of up to 4 000t/h, Tenova Takraf boasts significant experience in the supply of these underroof tripper cars. For the recovery of product from a pile, scraper reclaimers are the preferred (and dominant) equipment of choice for operators and planners alike. Some of the advantages of these machines include: • Proven robustness and reliability • High efficiency and low operating costs • Simple and steady working movements allowing for full automation • Gentle treatment of material and almost dustfree handling of fertilizer products Indoor areas As a result of general market developments and increasing fertilizer logistic requirements, the global demand for storage volumes and handling capacities is increasing. This growing demand has resulted in large pile widths, sometimes even exceeding 60m. For such indoor applications, the portal reclaimer, which boasts separate main and auxiliary reclaiming booms, is the preferred solution, as it requires a minimum amount of space due to its shape. This results in the maximum covered storage space for the product stack. Depending on bulk products’ densities, the company is able to supply portal reclaimers with handling capacities of up 6 000t/h and with rail-spans that can exceed 60m. Special features As previously mentioned, scraper reclaimers are, due to their method of operation, very gentle in their treatment of material and thus operate with minimal dust creation. This makes them ideally suited to fertilizer material that often comes in granulated form. This gentle treatment of a material, together with the minimization of dust, also applies in principle to all equipment within the fertilizer handling value chain including boom stackers and/or overhead tripper cars. These machines, which generally employ cone shell stacking for the minimisation of dust, can also be equipped with lowering booms or special chutes in order to further improve handling and dust minimisation. Nevertheless, depending on the characteristics of the fertilizer product and the customers’ unique requirements, Tenova Takraf is able to equip their scraper reclaimers and stockyard machines with special features such as: • Stainless steel design for blades and chutes • “De-lumpers” arranged within the discharge chutes for the breaking up (“de-lumping”) of caked bulk material • Hoses on hose reels for fresh air supply to operator cabins • Life-time lubricated outboard roller chains • ATEX-certified components in case of inflammable / explosive bulk material such as sulphur.


Bulk storage arrangement In addition to the globally popular solution of employing portal reclaimers in combination with overhead tripper cars for indoor fertilizer storage facilities, other alternative solutions can potentially be employed or even be better suited in certain specific instances. Spending the time to properly evaluate all options and making an informed decision based on all factors including the overall space situation, storage shed design and structure and/or on individual mass flows, may mean that the following machine solutions might be an even more suitable choice: • A stacker with tripper-car travelling on ground along the pile • A combined stacker / reclaimer • A circular storage arrangement.
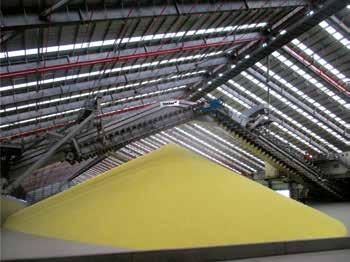
The images above provide a view of some typical portal reclaimers across various fertilizer types. A: Portal reclaimer for urea in USA, B: Portal reclaimer for sulphur in Kuwait, C: Portal reclaimer for potash in Russia

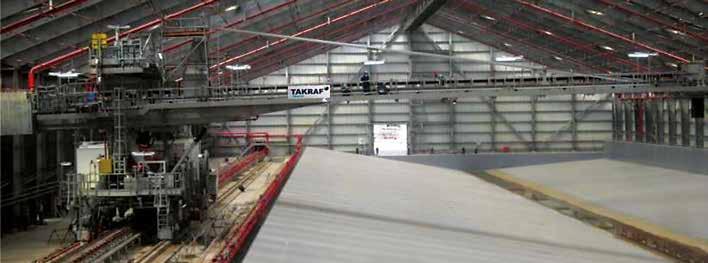
In addition, the requirement for homogenization may bear significant influence on equipment selection. Nowadays, very light building structures even for large shed dimensions are available and quite commonplace. Often, these light building structures do not allow for any under-roof installation of incoming conveyors with a travelling tripper car. In such cases, an alternative approach in combination with such a light building structure might employ an on-ground travelling stacker. In such instances where all equipment is installed at ground level, access to equipment for maintenance is significantly safer and more efficient as an additional benefit. If space at the site is limited, then a circular buffer storage facility may turn out to be the most effective space-saving solution. Bulk material is stored against a retention wall, with both stacker and reclaimer mounted on a central column. In circular buffer storage solutions, the feeding of the pile is conducted via a boom stacker employing the cone shell stacking method. Reclaiming is accomplished via a cantilever reclaimer, which conveys material into a central chute located below the central column. From this central column, material is then fed, via a feeder, to the outgoing conveyor. In operations where material logistics can be managed in such a manner so as to avoid simultaneous stacking and reclaiming operations, a combined
Circular buffer storage for 360° endless slewing operations with lowering stacker and cantilever reclaimer in India

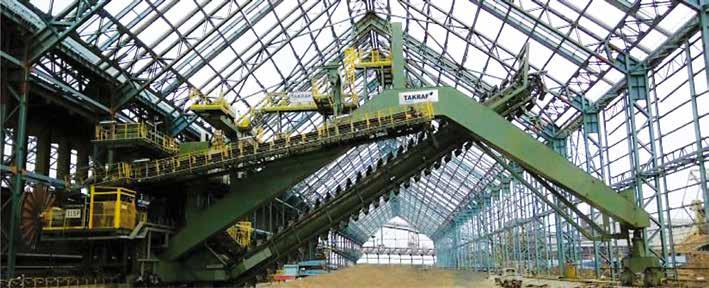

stacker / scraper reclaimer can also be an effective costsaving solution. In this instance, stacker and scraper booms are mounted on the same chassis resulting in substantial cost savings not only for the equipment itself but also in reduced rail lengths and fewer conveyors being required. Homogenization / blending In instances where fertilizer originates from mined ores and/or where variations exceeding the acceptable product range can be expected, material consistency can then be at risk. In order to protect against such consistency issues, the stockpile may, in addition to its buffer function, also be given the additional task of homogenization / blending. Blending beds generally operate in an adjusted combination of chevron-stacking and front-reclaiming. The stockpile is built up according to the so-called “chevron method” in a longitudinal stockpile, or the so-called “chevcone method” in a circular stockpile. In both methods however, stacking is required to achieve a sufficient number of material layers. Reclaiming is then conducted via a bridge-type reclaimer, which takes material from the front side of the stockpile. In this manner, reclaiming achieves a perfect mixture of material, depending on the number of layers and the incoming deviation and/or distribution. Tenova Takraf Ralf Katzke Tel.: +49 (0)341 24 23 5 00 Email: takraf.sales@tenova.com, www.takraf.com

Your boutique business destination


Surrounded by lush gardens in the hub of Johannesburg’s northern suburbs, The Peartree in Craighall Park caters for groups of fifteen through to 100 guests in three well-appointed and equipped business suites.
Breakfast meetings, working lunches, indoor or outdoor dining, half-day and full-day packages including all welcome refreshments, teas and lunches are offered in Standard, Gold and Platinum packages.
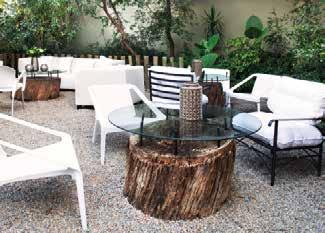
Secure parking, Wi-fi, lockable space, all underpinned by highly qualified and helpful staff dedicated to ensuring your event is a success, make The Peartree a destination of choice.
www.thepeartree.co.za e-mail: info@thepeartree.co.za Tel: 011 781 1401 41 St. Albans Ave, Craighall Park


Bottlenecks were preventing one of the world’s deepest gold mines from achieving its targeted throughput 2 850 metres below surface. Weba Chute Systems designed and manufactured the solution. A short slew conveyor was at the centre of the South African mine’s challenge, providing the only source of ore from that level. Frequent stoppages from belt cuts on this conveyor, often from large rocks stuck in the bottom of the existing chute, meant costly downtime and disrupted material flow to the plant. The solution, according to, Dewald Tintinger, technical manager at Weba Chute Systems, was to design a completely new chute solution that would remove the need for the slew conveyor arrangement. “The chute we designed has a bypass leg that drops waste material directly into the bypass, while allowing an inline channel of reef onto the conveyor belt,” Dewald says. The custom-designed chute was able to replace the mechanical moving component, which also improved the safety of the working area. The solution, which also involved 70 metres of conveyor belt extension, required the new chute to bifurcate the flow of material from the stopes into a reef stream and a waste stream. “We achieved that by installing a chute section mounted on a trolley frame, actuated to split the material flow as required,” Dewald explains. Another benefit was that the area no longer needed regular cleaning. Previously, four shifts of cleaners, comprising four workers each, were required to service the area around the slew conveyor and remove spillage. Weba Chute Systems & Solutions, Tel: (011) 827-9372 Email: weba@webachutes.com, www.webachutes.com
Cost and installation time analysis When diesel engine service and repair company, Diesel Power International Services subsidiary based in Namibia, needed advice on what cranes and hoists could be applied effectively to their newly designed work space, that would house their assembly lines and diesel engine stripping facilities, they called in Konecranes from Cape Town to assist. Installation and delivery times were tight, but the innovative solution that resulted from a Cost and Installation Time Analysis conducted by Konecranes sealed the turnkey deal. “The project was for a semi-free-standing gantry with 1 x 3.5 ton single Girder Crane and 2 x 500kg Column Mount Jib Cranes and hoists” says Markus Labuschagne, Konecranes’s Regional Branch Manager who is based in Cape Town. “The equipment specifications that the customer had originally requested - one 3.5ton jib crane and two 500kg jib cranes - would have worked out at a higher costing and not enhanced the layout of the proposed floor area. Additionally, our cranes have enabled the customer to place items on the new mezzanine level in the production plant” he says. The 3.5 ton crane will be used for the lifting, stripping and assembly of truck diesel engines while the 2 x 500kg column mount jibs will be used for serving two work stations where smaller components and parts are

The growing popularity of Products’ expanded offering has led the company to boost its service and repair facilities. Andrew Frank, operations manager at Mato Products, highlights the recent completion of the new spray-painting booth, which has doubled the firm’s capacity to finish refurbished items. Well known as a leader in conveyor belt lacing, the Multotec subsidiary also offers a range of belt cleaning solutions. “To keep up with market demand, we have expanded our spray booth significantly in terms of size and throughput capability,” says Andrew. “It can now accommodate components up to a length of 2,2 metres and provide a more productive environment for operators.” This now allows for all repair and finishing work, even on the longer diagonal belt cleaners, to be spray-painted in-house, he adds. Importantly, this improves turnaround time, quality control and cost to customer. Mato Products Tel: (011) 923-6000 Email: marketing@multotec.co.za www.multotec.com
The new spray booth is equipped with the latest filtration technology and complies with the highest standard of health and safety
repaired and serviced. Markus concludes, “As a result of our cost and installation time analysis it was our recommendation that the alternate cranes we had identified as suitable for their project, would cover a greater area than the equipment originally specified, and would offer greater benefits to the client, in addition to the fact that we were able to deliver the equipment to the customer in Namibia within their stated timeframe.” Konecranes Markus Labuschagne, Tel: (011) 898-3500 Email: markus.labuschagne@konecranes.com www.konecranes.co.za

Belt feeder FLSmidth has launched their new Hybrid Apron Belt (HAB) Feeder for run-of-mine and stockyard applications. A modular, hybrid, belt-overapron feeder, the feeder delivers the strength of an apron feeder with the spillage control of a conveyor system. It is a robust, power-efficient and high-tonnage hybrid belt-over-apron feeder that offers combined advantages of both apron and belt technologies. It provides a cost-effective solution for feeding abrasive materials, such as mineral sands, iron ore and bauxite, in mid-tier ROM applications and stockyard management operations. The low-profile loading deck easily accommodates different types of loading methods, including direct truck tipping, side tipping, front-end loading, dozing and ROM bypass tips, in order to prevent double handling. The feeder’s modular design allows for transportation within a standard-size container, simplifying freight solutions to remote locations around the world. Modularity also allows for specific discharge heights, depending on the required application. The HAB Feeder design incorporates a number of safety features, including a start-up alarm that is located behind the wing walls, an emergency stop on either side of the feeder, and an emergency bar at the feeder opening. According to FLSmidth’s Manager of Capital Equipment, PC
Greater versatility
The Potain Hup 40-30 self-erecting crane boasts a range of innovative design and technology features which, according to Louw Smit, sales director at Crane & Hoist Equipment SA, will enable greater versatility on construction and other project sites. “One of the major advantages of the Potain Hup 40-30 unit is that, with its 40 metre jib, it offers different configurations making it unique to this category of self-erecting cranes,” Louw explains. “The crane can easily be adapted for a range of job site applications increasing efficiency and versatility.” The crane has a maximum capacity of 4t, can lift 1t at its jib end of 40 metre and features a telescopic mast for a range of working heights. This design boosts the height under hook attainable by the crane to 25.6 metres in its “low position,”

Kruger, “This feeder is specifically designed to feed abrasive materials at an adjustable rate onto conveyor belts and sizers. Because it is entirely modular, it can be installed with minimal site preparation, anywhere near a stockpile. It is semi-mobile for simple onsite relocation or repositioning. Moving the feeder is as easy as dragging or pushing it with standard stockyard equipment.”
FLSmidth PC Kruger, Tel: 076-812-7610 Email: pc.kruger@flsmidth.com, www.flsmidth.com
and 30 metres when extended to its greatest height. The logistics are also improved, as no extra mast is required to install the crane. Further versatility is delivered with the crane’s luffing jib that offers three positions: horizontal, 10° and 20°. These options give the crane a height under hook range of 20 to 40 metres. Louw explains that shortening or extending the jib is a swift and straightforward operation, with the Hup 40-30 offering convenient configurations for both short and long jib lengths.
Crane & Hoist Equipment SA (Pty) Ltd Tel: 083-413-7524 Email: info@che-sa.co.za www.che-sa.co.za

What is High Security Weld Mesh HIGH Security Weld Mesh is wire fused and welded at a Horizontal distance of 76.2mm and a vertical distance of 12.7mm also known as 35B/3510 where 3 denotes 3”(distance between vertical wires), 5 denotes 0.5” (distance between horizontal wires), and B or 10 denotes gauge of wire High security welded mesh Pallisade Gates Gate Automation Razor wire and more ....

Salient Features • Difficult to Climb: The spaces between the Horizontal wires are too narrow for fingers to have grip • Impregnable: Extremely difficult to cut with a hand cutter as the beak of a wire cutter will not be able to penetrate the horizontal wires • Excellent Replacement option to Solid Wall as: 1. More economical than a solid wall 2. Faster to install than a solid wall 3. CCTV Camera has a clear view • Further upgrade possible with electric security system • Anti-corrosive & low maintenance



Standards • Manufactured according to BS EN 10016-2 • Wire Sizes in accordance with BS EN 10218-2 • Tolerance on Mesh Size in accordance wiht EN 10223-7 • Tolerance on Panel Size in accordance with EN 10223-4 • Welding Strength in accordance with BS EN 1461 • Zinc Coating in accordance with EN 10245-1 • Anti Corrosion in accordance with BS En 3900 E4/F4
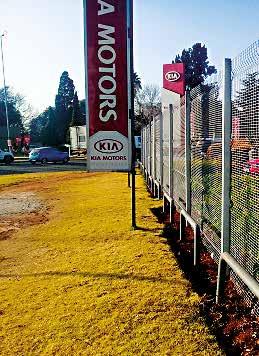
Tensile Strength • Wire has a tensile strenght of min 550 MPA
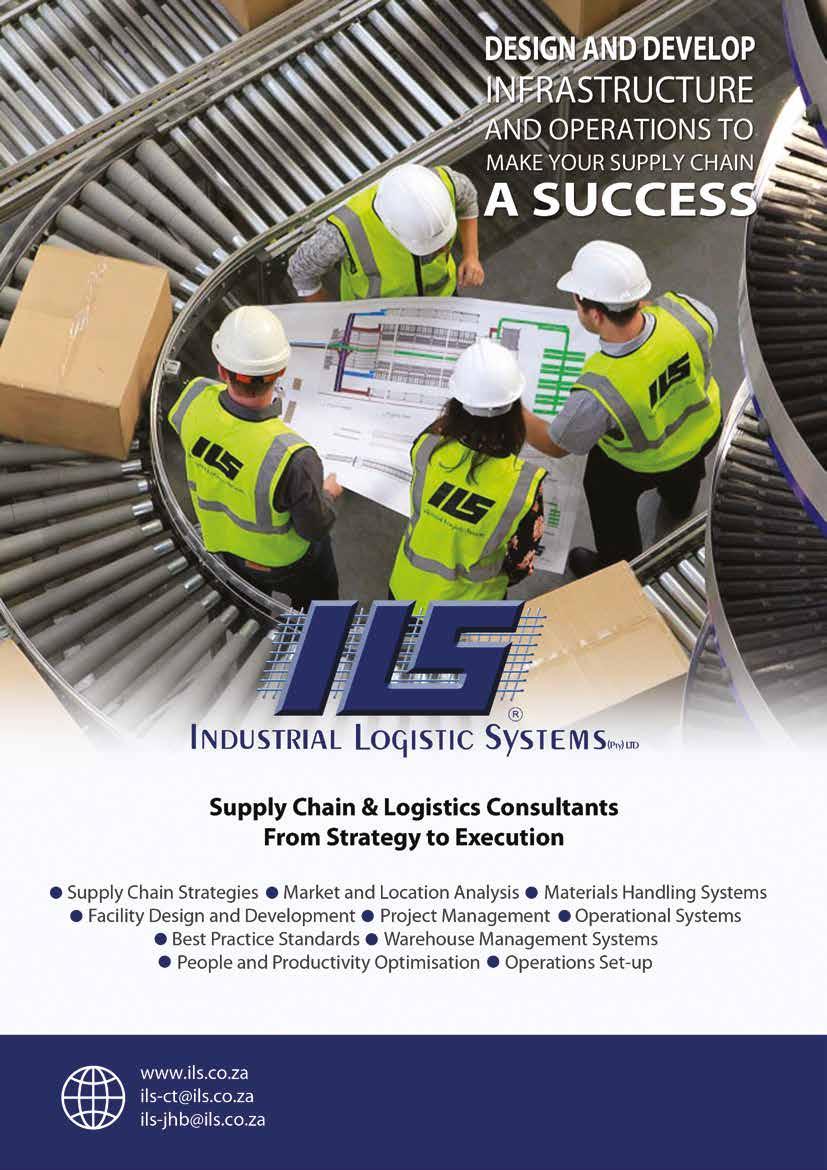