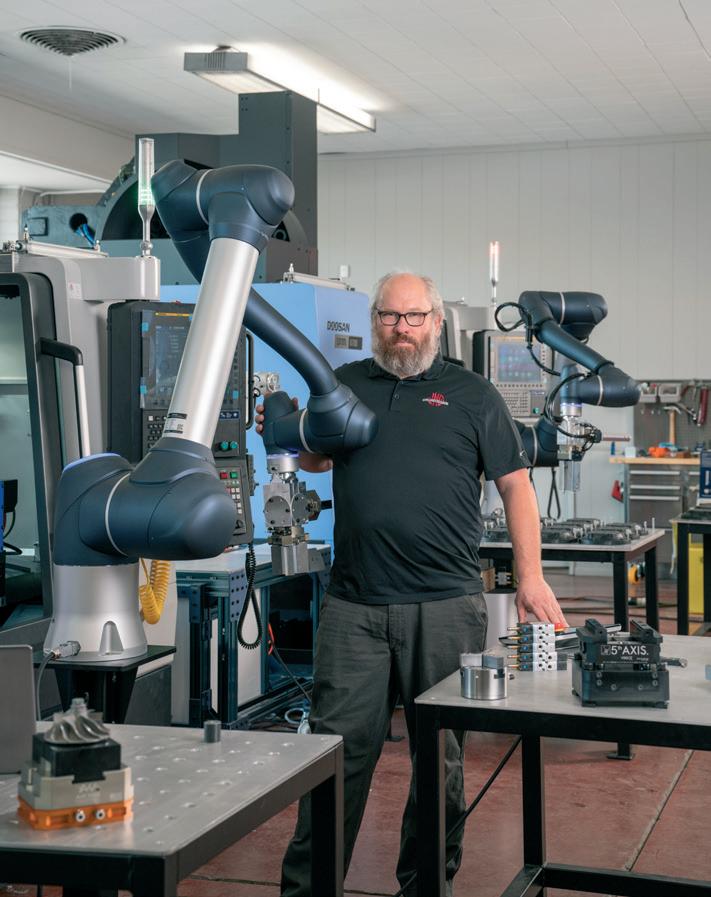
11 minute read
Cover Article
The manufacturing sector fared significantly better than most industries during the pandemic; U.S. manufacturing employment lost only 1 in 20 of the overall jobs that went away during the period. In fact, many shops were able to remain open, as they were deemed essential businesses. That momentum has continued into the post-pandemic economy; since the pandemic ended, the manufacturing sector has added around 1.3 million jobs, just about as many as it lost.
The resurgence of the domestic manufacturing sector stands out as one of the U.S. economy’s bright spots, and the nearterm outlook for the sector remains optimistic. Today, many manufacturers continue to report significant order backlogs that will drive their business activity into early 2023. There is a ‘But’, which is that virtually all research indicates that labor shortages remain the greatest long-term obstacle to growth.
Lars Grisley, president of 4th generation machine tool dealer J.M. Grisley, says, “Our customers are located in the Rocky Mountain region, including the states of Colorado, Utah, Idaho, Montana, and Wyoming. Outside of cities like Salt Lake City and Denver, many of the machine shops we support are based in rural areas, and it isn’t unusual for our customers to live in towns with less than 1000 people. There just isn’t an available labor force to draw from, and this hasn’t improved since the pandemic ended – in fact it has just gotten worse.”
Stuart Gill, Regional Sales Manager for J.M. Grisley says, “At J.M. Grisley we help our customers to grow their businesses by facilitating automation in their shops, which helps to alleviate their need for more employees. J. M. Grisley offers two categories of automation. The first, we term ‘hard automation’, and it includes systems that physically connect to one machine. These include pallet and gantry systems. The second is Robotics Automation. We have seen a huge increase in ‘Cobots’ as they are often referred, and they are designed to work alongside humans. Cobots can be used by a number of machines, as they are not tied to a specific machine.“
Dan Wall, Head of J.M. Grisley’s Automation Lab, pictured on the next column, adds, “The COVID-19 pandemic accentuated the need for resilient supply chains and human-machine collaboration at work. Despite labor shortages, supply chain disruptions, and other production challenges, manufacturers still have to meet their customers’ production needs. To bring the best of both worlds – human creativity and robotic precision – we are helping our customers adopt automation that can reduce human interaction and accelerate production cycles.” they improve human capabilities in performing tasks with greater strength, accuracy and data capabilities.”
The J.M. Grisley team is seeing unprecedented adoption of automation from their customers, both with pallet/gantry systems and with robots, both collaborative and Industrial. Asked about the adoption of automation solutions in the precision manufacturing industry outside of their customers, Stuart says, “There are robot companies out there that are promoting their specific robot or cobot solutions. What differentiates J.M. Grisley from many of these other companies is that we have a complete understanding of the machines the shops are using, the process of machining, and how to integrate robots into the part making environment.” He added, “When you go into a shop that has a cobot sitting unused because nobody knew how to install it, it was likely purchased by a standalone cobot company that just wasn’t equipped to integrate it with the machines. Our machine tending knowledge is invaluable to our customers implementing automation.” J.M. Grisley is also capable of providing flexibility and options when it comes to Robotics. As an Authorized Fanuc Robot Integrator and a stocking Doosan Cobot dealer, as well as having partnerships with companies like Schunk, 5th Axis and Air vice for work holding, they can offer the best platform for each project.
Gantry and Pallet Systems
Stuart describes the pallet systems that the team at J.M. Grisley installs for its customers. “Gantry systems are, in essence, workpiece changers. They are installed exclusively on lathes (~30% of DN Solutions’ lathes are spec’d with a gantry pallet as an option), and they load piece parts directly onto the lathe. Like gantry systems, pallet systems are ‘hardwired automation’ because you set them up on
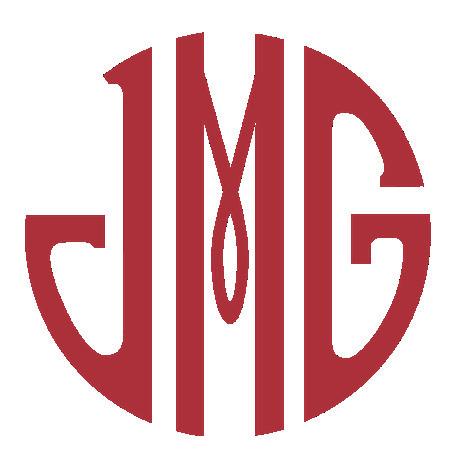

one machine and they will be used exclusively by this machine. With a pallet system, you are loading parts onto the pallets versus loading parts directly onto the machine. The benefit to gantry and pallet systems is that the machinists do not have to change the way they are making the part in any way. With a pallet system, the efficiency comes from setting up a new pallet while the machine is working on another product on another pallet or in the case of the gantry system, of loading parts automatically.” He adds, “Also, pallet systems can be installed on older machines, whether they are 3, 4 or 5 axes.”
He continued, “Pallet systems as a step in automation are popular because they are super easy to implement…they are the low hanging fruit. Pallet set up is identical to what the machinist is doing today, only they are setting up the parts on the pallet offline. There is no extra machining to do, no learning curve, and it is a really safe way to get into automation. Depending upon the number of pallets and cycle time, the machine can often run unattended.
Dan says, “We have a number of customers who are implementing automation solutions in conjunction with the Doosan (now DN Solutions) machines we have sold to them. In particular, we have customers who are doing automation with the DVF 5000, DN Solutions’ newest line of 5 axis machines. Since the DVF 5000 rotary axes are a cantilevered B and C configuration, pallets move in and out thru an automatic sliding door on the right side, allowing the operator full access to the front of the machine and CNC controller.”
Robotics
Dan says, “While gantry and pallet systems are easy to introduce into a shop since they require no major changes in the way the machinists operate with the part and with machining, cobots change the way in which parts are made. Cobots are so different from what machinists are used to and there comes the fear of not just how to run the cobot but also will this work me out of a job.“
He adds, “The more tech savvy the machinists are in a business, the more likely they will pick up and embrace the use of robotics. Like with gantry and pallet systems, cobots can reduce much of the mundane work that happens in a shop, including part loading.” Stuart adds, “Our Automation Lab is extremely valuable to our customers who are installing robotics, as all proof of concept happens with the help of our team.”
Dan says, “At one of our customers, they were deburring ~10,000 of a particular part each month. Naturally it was tedious for the machinist. When we put a cobot in place to do the deburring, we freed up the machinist to run parts on a machine. He is so much happier with his new role today.”
He continues, “With another customer, they had a part that required a caustic chemical. Those who were involved in the chemical process had to wear special clothes and breathing apparatuses. As you can imagine, nobody wanted to do this job. Once we installed the cobot, human contact is almost completely eliminated and the cobot solved the labor issue.”
Dan says, “If we are installing the automation with a new machine, we typically do the integration at our shop and then we bring it out to the customer’s facility. We will then come onsite to provide training to get our customer up and running as quickly as possible, typically within a week of training.”
Stuart adds, “We offer as much installation support as our customers want. We can offer as little as technical support for customers who have inhouse capabilities all the way to turnkey, where we even make the initial parts for our customer. Turnkey means providing everything, including the grippers and vices, the relays and solenoids, and we will do all the electrical installation. At J.M. Grisley, our Automation Lab team is expert at ensuring that our customers are up and running quickly and are maximizing the benefits available with their new automation equipment. With J.M. Grisley installs, you won’t see cobots off in a corner of the shop unused.”
Lars says, “Contrary to perceptions, automation can work well with older machines, whether they are 3, 4 or 5 axis. In fact, we do installations on older machines, even those from other builders. Additionally, many people believe that
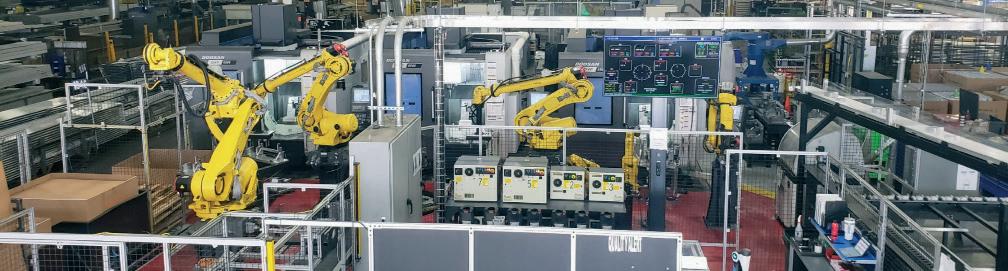
automation works well only in production (high volume, low mix) environments. While it works well in these environments, it can be extremely beneficial in low volume, high mix shops maximizing your skilled labor time and efficiency.”
Hear From J.M. Grisley Automation Customers
Visser Precision’s Adoption of Technology Makes It A Cool Place To Work
“Our founder loves manufacturing and embraces new technologies, and automation is a huge part of that. Our newest acquisitions, procured from J.M. Grisley, are the addition of 2 DN Solutions’ DVF 5000s, which are 5-axis machining centers. We purchased both machines equipped with the Automatic Work Changer (AWC). Each DVF 5000 has 12 pallets. For a specific Nascar job where we are machining suspension components, we are effectively doubling our spindle capacity. We are running the parts throughout the night so when the operator comes in the next morning, there aren’t inprocess parts; they are all finished.
Our DN Solutions (Doosan) DVF 5000 with the AWC means has so many benefits:
• less operator interaction • increased machine to operator capacity • increased predictability of each and every part; if we set it up right, every part will come out perfect • improved spindle utilization
There has never been such a dearth in the availability of human labor, and automation is literally the only way to increase productivity while minimizing the need to grow our team. Further, automation allows us to reduce mundane tasks like loading machines, allowing us to free up our team to do other things. If you don’t have automation, you have no choice but to have an operator doing the work.
We just finished installation of the AWCs, and the experience was absolutely outstanding. The J.M. Grisley person showed up on a Friday to train us. One of our programmers and I attended the training; our J.M. Grisley trainer showed us how to use the AWC and I jotted it down on my phone. The control on the AWC is so intuitive it took us 10 minutes to learn. I liken it to how you can add new apps to a smart phone, and you can learn and do it with almost no direction.
At Visser Precision we are technology driven and people powered. We don’t settle for old technology and we don’t ever feel that what we have is ‘good enough’. J.M. Grisley is a highly skilled partner in our automation process.” Patrick, Manufacturing Manager, Visser Precision Machine Shop In Montpelier, Idaho Uses Cobots To Take Over Tedious Mundane Tasks

“A few years ago we were doing some repetitive work on one of our machines when it crashed. A technician from J.M. Grisley happened to be at our shop when it happened, and he said, “You should get a Cobot.”
Shortly after, we did buy a Cobot from J.M. Grisley. When it arrived, I was thinking how am I going to get this thing running. J.M. Grisley has an automation specialist, I call him Robot Dan. Dan was at our place to help set up the Cobot. Dan is outstanding - he is so smart.
The next year we bought another Cobot, and this year we bought our 3rd. One is used on our lathe and it does the 2nd operation. The second is used on our ‘blow off station’ and the 3rd Dan retrofitted to do our hand filing. We’re ready to buy our 4th shortly.
Everybody thinks a robot/cobot moves faster than a human arm - it doesn’t. You watch it and you will think it is not super fast - but what you get with a Cobot is steady and consistent, so in the end it definitely saves time.
I bought my first machine from J.M. Grisley when I opened my business in 2006, and I have only been buying from them since. They are awesome and I am super happy with their customer service and their expertise.” Gordy, Shop Owner, Walker Machine
Interested In Automation?
Whether you have machines from J.M Grisley or not, and you recognize the need to automate, yet you want the help of automation experts, contact J.M. Grisley. Their Automation Team will help make your automation experience outstanding. Visit: jmgrisleymachine.com or call 801.486.7519