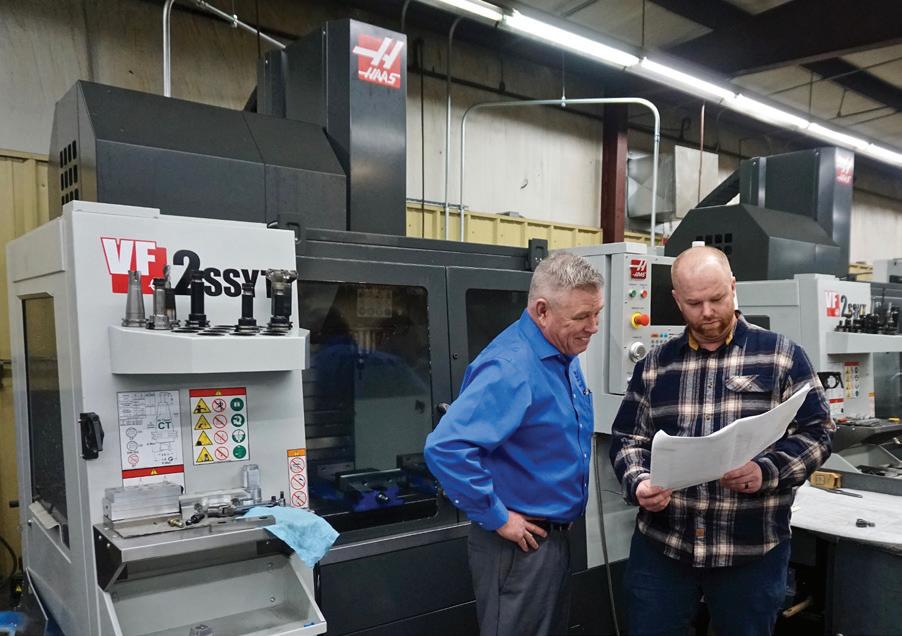
8 minute read
THE
NORTHERN UTAH CHAPTER OF THE NATIONAL TOOLING & MACHINING ASSOCIATION
Established in 2010, the NUNTMA is a gathering place for machine shops in Northern Utah.
January 18: Emerging Leaders Conference
$60.00 Connect. Learn. Lead.
Join us to grow your leadership skills! We will be discussing the future of the industry, how to bridge age-gaps and more!
Time: 9 am-2:30 pm
Location: SLCC Westpointe Campus/SSB Rooms
234/236 and a Tour of Hoyt Archery!
Presentations will include:
• Conflict Resolution/Crucial Conversations
• Staying Profitable in Turbulent Times

• How to Pay Your Dues & Grow in Your Career
Panel Discussion with Industry Leaders
REGISTRATION REQUIRED FOR ALL EVENTS. VISIT: NUNTMA.ORG/UPCOMING-EVENTS
NASA has extended that work in contracts totaling $9.3 billion covering the production of Orion capsules for NASA’s Artemis missions through 2030.
The Artemis 1 test flight is earning an A-plus grade so far, said Mike Serafin, NASA’s Artemis 1 mission director.
He described a few “funnies” — sensor readings or system behaviors that didn’t match expectations but weren’t necessarily problematic — that missions teams have studied, but generally, the launch and Orion’s mission have gone according to plan and are exceeding expectations, he said. “We’re like a kid in a candy store,” Hu said. “We’re that happy.”
Passing around the back side of the moon meant Orion lost contact with Earth for 34 minutes, during which mission control couldn’t know what the spacecraft was doing. The capsule emerged from the back side of the moon on course and gaining the right amount of speed, NASA said.
The few mysterious system readings during six days of flight that NASA has reported involved gas plumes from the service module thrusters catching sunlight and momentarily
“dazzling” the star-tracker instruments Orion uses for navigation, creating some odd readings; and some of the redundant electronic switches connected to the solar power system have behaved oddly, Serafin said. None of those issues are considered problems, though, he said.
NASA's Orion space capsule uses a camera on a solar array for a selfie image as it flies away from Earth on Nov. 16, 2022. The spacecraft, designed and built by Jefferson County-based Lockheed Martin Space, flew without crew on board to within 80 miles of the Moon's surface on Nov. 21, completing the first of two Thanksgiving week maneuvers designed to put Orion in lunar orbit for several days of testing.
The most unexpected aspect of Orion’s performance has been how much less fuel its thrusters have used than expected. The capsule has consumed less electrical energy than predicted too, while Orion’s solar panels are gathering more power than was modeled.
“How clean it has all been is a bit of a surprise, honestly,” Hawes said. “It’s been really gratifying to see so few things crop up.”
The extra power Orion has on this flight means mission planners will have more flexibility in planning the Artemis II mission carrying astronauts, Hawes said. That mission is slated to fly in 2024.
But the Artemis 1 mission still has some dangerous maneuvers ahead. A thruster burn Friday must go correctly to solidify Orion’s position in orbit more than 40,000 miles from the lunar surface. By Greg Avery – Denver Business Journal
CMC Adds Capacity with Hwacheon VESTA-2000
“Continental Machining Company (CMC) founder Butch Yaple probably trained half the machinists in Albuquerque”, owner Kelly Denison says. “Not only was he a legend and an extremely gifted machinist, but he was also highly committed to helping to train the next generation of machinists”, Kelly adds.
And what better training ground than a machine shop that manufactures parts for the Department of Defense (DOD) and the Department of Energy (DOE). CMC’s complex parts range from single parts to complete assemblies, and they specialize in machining (Turning and Milling on Horizontal, Vertical and Five Axis Machines), welding (AWS and ASME certified) and fabricating very large parts. You should not be surprised to learn that CMC is consistently an ‘A+’ shop for its Quality rating. It has to be, as you just can’t get a more stringent customer than our US government. CMC’s parts have gone to Mars with CMC’s contribution on the cameras, they have parts that are used for our nuclear weapon program, and they make parts for a weapon system that defends Israel. Kelly says that as a Christian, he is very proud to be a small part of programs that defend the USA and Israel. And while the majority of CMC’s parts are for DOD and DOE, they also make parts for the pharmaceutical, space, and directed energy industries.
A little about how the company started and has come to be. Kelly’s father, Dave Denison, was one of the lucky individuals trained by Butch. Though he had recently graduated from Central New Mexico Community College — CNM — (formerly Technical Vocational Institute), his real hands on training began when he came to work under Butch’s tutelage. Work at CMC was so rewarding that Dave spent his entire career at the company.
The business, after 35 years of ownership by Yaple, changed hands in 2000 when Dave purchased the business, allowing Yaple to enjoy retirement.
Dave’s son Kelly worked at the business from the time he was 14 years old, and officially joined full time working nights while attending classes at CNM in the day. Many years later, in 2020, he purchased the business from Dave. “Not only did I have the opportunity to learn hands on machining from the best, but I also was mentored by business minded team specialists with the other disciplines of running a business, from finance to logistics to marketing to real estate.” Kelly feels that in his early years, he was blessed to be trained in all of the facets of being an entrepreneur and running a company.
One can imagine how incredibly challenging it would be to have the US government as your primary customer. “We have to consistently excel at quality; you just can’t fail the government.” He adds, “We have always had a keen focus on quality, and Jason Romero, our Quality Manager, is just outstanding.” The company has been certified to ISO standards for more than 15 years now, and, Kelly says, “We don’t certify to be able to check it off for customers; rather we live and breathe it. We intuitively know that it is a tool that helps us to be a better company and enables the quality ratings we consistently achieve with our parts.”
Today, CMC has more than 30 machines, including 5 axis machining centers in their 26,500 square foot facility. “We specialize in very large parts, and we are skilled in machining, welding and fabricating. We are equally capable of manufacturing prototypes to production parts.” Kelly says, adding “We have a number of Haas machines, all purchased from MMT Productivity, the local dealer. We highly value the Haas machines, not just for their price points, but also for the service we get from MMT Productivity.” He continued, “Another huge benefit with the Haas machines is that since we hire many of our new employees from CNM, where they are trained on the Haas machines, when they come to work for us, they are immediately productive since they know the machines.”
Supplier loyalty is integral to the way CMC conducts its business. “I can’t say enough about the service and support we get from MMT Productivity. This includes company president Mark Smith, our local salesperson Danny White, and Dave Smith of Productivity’s tooling division. We value the company as a whole and respect their ethics.” He adds, “We have been working with them for a very long time, and we appreciate that Mark Smith and team have taken the company to the next level since the merger of MMT and Productivity.”
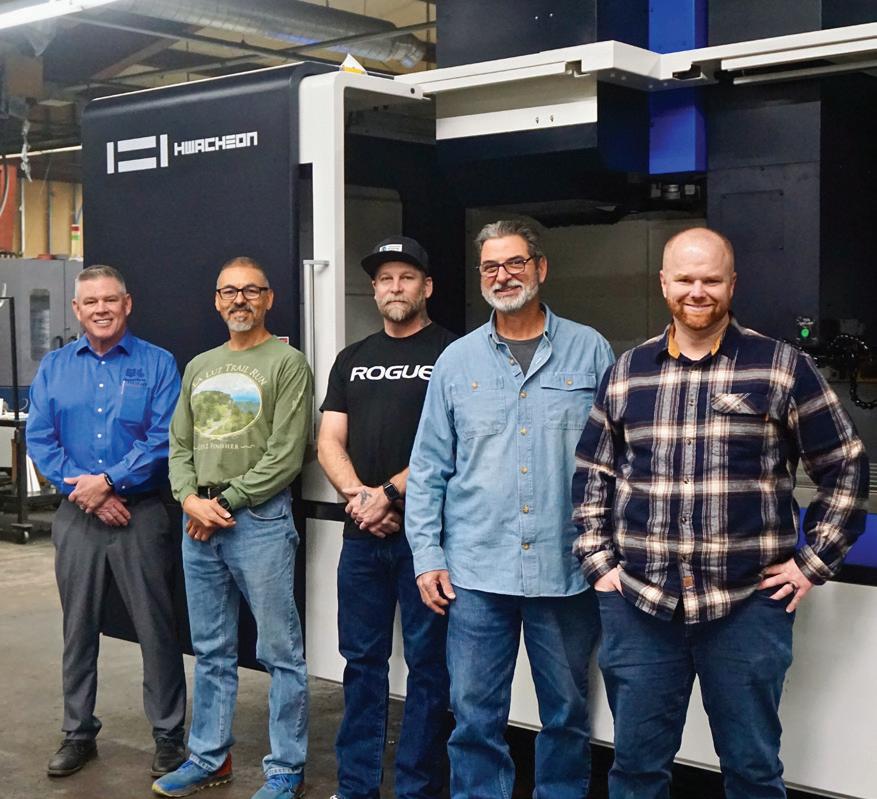
In 2019 Kelly attended MMT Productivity’s bi-annual Oktoberfest event, the largest dealer held machine tool show in the US with an average attendance between 3,000 to 4,000 visitors. It was during this event that he was introduced to the Hwacheon machine tool line. Kelly then contacted some Productivity customers who own Hwacheon machines and heard very positive feedback from all. “We recently received our first Hwacheon. We chose the VESTA-2000. We liked this machine for its value, capabilities, and quality. The finish and components are on par with other high-end machining centers. We added probing and a Nikken 4th axis rotary table to increase its capabilities”. He elaborated, “The 78” x 33” work envelope lends itself well for large part machining. In the end versatility, cost, and the service support we receive from MMT Productivity made the decision for us. Also, going from our previous machine with only 3000 rpm and now having the Hwacheon with 8000 rpm, all of our aluminum plate work will be done more efficiently and reliably.” Danny adds, “The best way I can describe the Hwacheon line is that you are getting a ‘Japanese caliber’ machine at a much lower price point. The VESTA-2000 is a solid solution for powerful cutting operations based on its rigid structure.” He adds. “To give you an idea of their reliability, I have a customer who bought 2 Hwacheon mills from me 3 and 4 years ago. He has had only 1 service call between both machines to date. Now that’s reliability!”
The company, at nearly 6 decades in business, continues the tradition of helping to ensure the next generation of machinists are available to manufacture precision parts. Kelly sits on the advisory board of CNM, he schedules quarterly visits to the school and he regularly invites students in for tours. Kelly says, “I believe in paying it forward, and frankly we have to be involved if we want our trade to survive.” Kelly also selects a machinist to accompany him to machine tool shows, saying that he wants to help CMC machinists learn about new products, and enable them to get out of the business’ 4 walls.
The CMC management team consists of Kelly, Jason Romero (Quality), Lance Palmer (Shop Foreman), and Vice President Vince Zarrella. Kelly says, “At CMC, we recognize how valuable not just our management team is, but also how integral to our success our machinists are. My dad always said this: “We should have a reason to be in business beyond making money –we must provide a career to support our employees and their families. We want a work environment that is conducive to our employees not dreading on Sunday night that they have to come to work tomorrow. As a team, we really do enjoy working together and hanging out together outside of work.”
Machining isn’t just a business for Kelly. It is his passion. Kelly started learning the trade when he was just 14 years old. He spent countless hours with his father building and driving their own championship winning mini-sprints, and later became a non-winged sprint car champion. He is continuing this tradition with his 8 year old son; they are currently building a Quarter Midget. Kelly says that Conner, pictured above, is learning to use tools such as a bandsaw and shear, and the work he is doing is indeed giving him a feel for what happens in manufacturing.
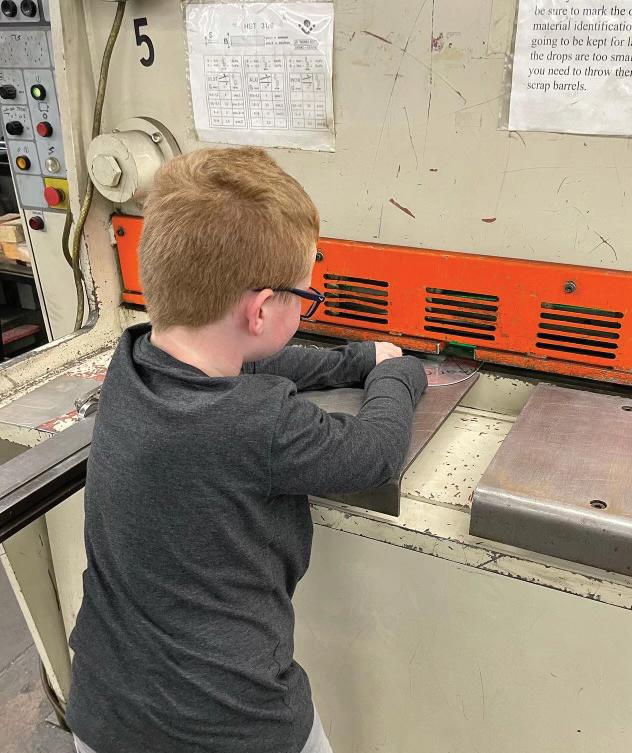
MMT Productivity is a complete machine tool supplier offering quality, long-lasting CNC machines, tooling & accessories, robotics & automation, machine repair and service, advanced engineering services, machine training and related manufacturing products and services. To learn more about how they can help you with your machining needs, contact them at: 303-571-4933 or visit productivity.com
CMC, in business since 1965, makes superior high precision parts, including large parts. To find out how the AS9100 certified company can help your business, call: 505-345-2483 or visit continentalmachiningco.com

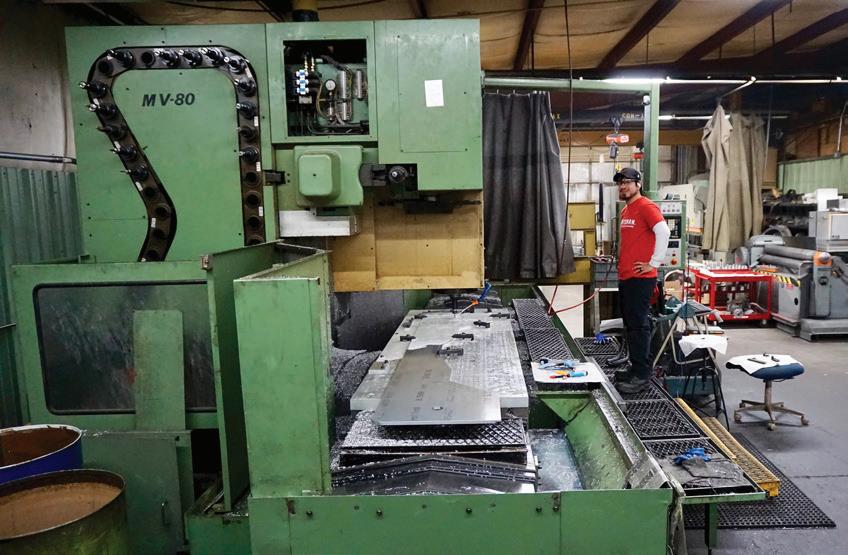