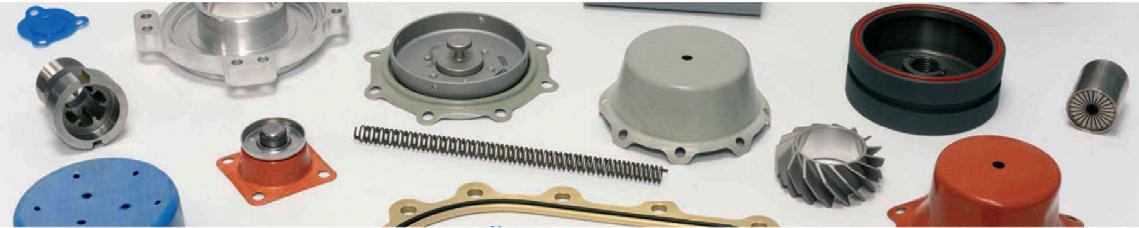
7 minute read
Feature Articles...........................1,10
3 Generations of Manufacturing Excellence
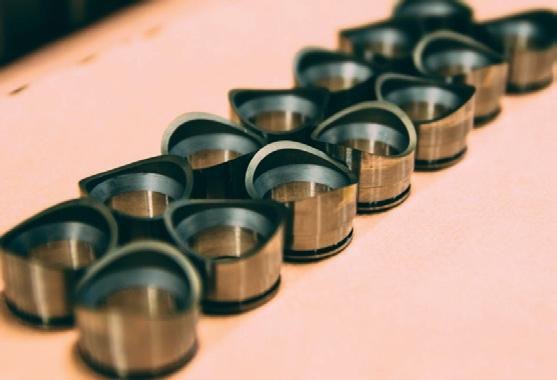
Micro-Tronics (MTI) is a contract manufacturer that is most certainly unlike any other company you are outsourcing to. Its sprawling campus headquarters in Tempe, Arizona includes 4 buildings and ~80,000 square feet of space, and it is here where its 100 plus experienced employees support customers. It differentiates itself in so many ways, but here is a snapshot.
• Woman-Owned – The company was founded by Angeline and John Marusiak, and today, John’s daughter in law Lucia Marusiak, together with her sons are the sole owners of the business. The business is in its 3rd generation of management, with Johnny and Charlie Marusiak leading the operations and business development for Micro-Tronics.
• Experience – The company is more than ½ century old, having been founded in 1968. The company brought in outside expertise to build the operation’s depth and take it to the next level of excellence. Jeff George is the current president of the company, having come on board nearly 2.5 years ago. Jeff is an aerospace and industrial manufacturing leader with over 30 years of experience, and was most recently Operations Director for SKF AB’s, multi-plant, Aerospace Business Unit. Lucia says, “Our customers directly benefit from the partnering of longevity, low turnover and experience of our team of devoted employees.”
• Credentials – The company is AS9100 Certified, NADCAP Accredited for Nonconventional Machining (EDM) and Elastomer Seals (Rubber Molding), ITAR Registered and soon to be compliant with NIST Cyber Security Requirements.
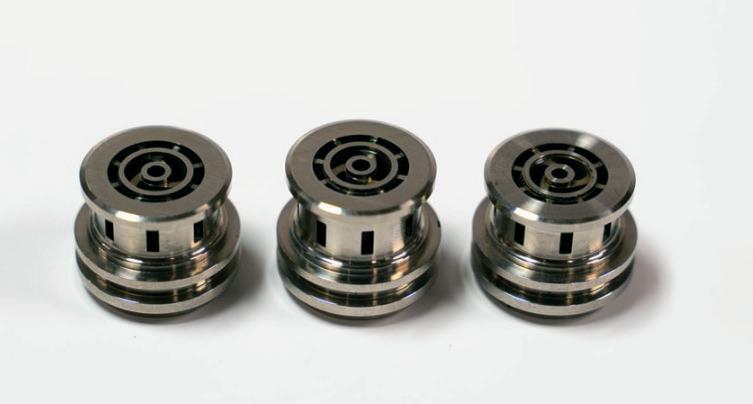
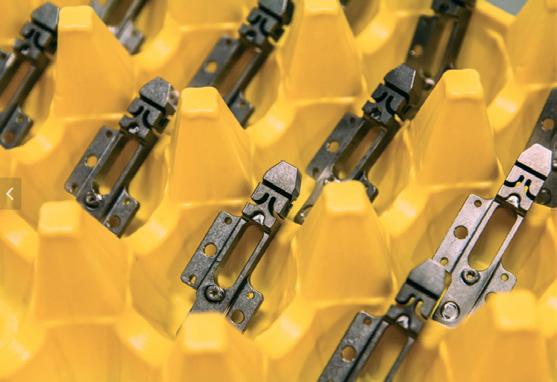
• Engineering – With a team of engineers (industrial, chemical and manufacturing), the company is able to support its customers with their prototype/R&D manufacturing to ensure that the products are being designed for manufacturability, and highly competitive compressed lead times with complete in-house solutions. timesthese include: EDM(Wire, Sinker, and fast hole), CNC machining, full Turn key products, custom elastomer/kapton molding, bonded plate seals, custom elastomer to metal bonding, fabric reinforced elastomer diaphragms, and final assembly/kitting and shipping of complete tested top level bills of material eliminating 20 or more sub levels of processing and assembly in one facility. Beyond these capabilities, the company also offers in-house tooling and mold manufacturing, Design For Manufacturability, and proprietary laser marking.
• Tier One Customers – a significant number of MTI’s ~ 50 customers are in the defense and aerospace business (original and aftermarket), and the parts they manufacture go into nearly every vehicle owned by the government, from land to air and to sea. They have retained customers today that they brought on when they first opened for business 54 years ago, though the companies have typically been through several name changes and acquisitions during this half century. Their more recently targeted customers hail from the oil and gas;,medical, semiconductor, transportation, and hydraulic and pneumatic industries.
• Culture – Jeff says, “When I joined MTI, I was delighted to experience our company culture, which is one of commitment and collaboration. Our entire team rallies around customer service. As an example, during Covid we had a new customer come to us. They were in crisis mode, as their current supplier had let them down. They needed production solid elastomer parts in 5 weeks, and this included building a mold. The material they required was somewhat specialized, though close enough to what we were very experienced with. Tooling took 4 weeks, as did the material ship time. The mold and rubber came in the day before Memorial Day weekend. Without hesitation, our team worked throughout the 3-day Holiday weekend to deliver parts to our new customer on time. Our commitment to on-time delivery and to supporting this new customer with a very difficult part has resulted in them awarding us an additional 15 parts.”
EDM/CNC EDM/ Wire EDM/ Fast Hole EDM – NADCAP Accredited Jeff says, “If you need EDM services, we’re probably the largest EDM shop west of the Mississippi. With 25 Sinker EDMs, 14 Wire EDMs and 6 Fast Hole Machines, we have the capacity to meet most all top level requirements. We can accommodate a wide variety of work pieces and configurations,
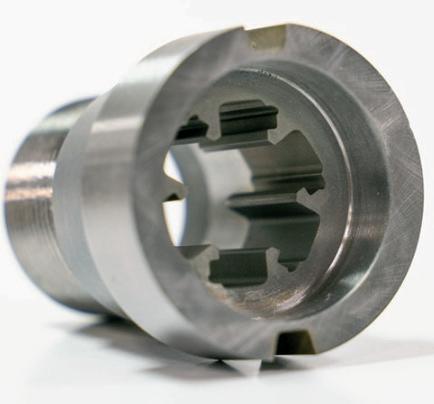
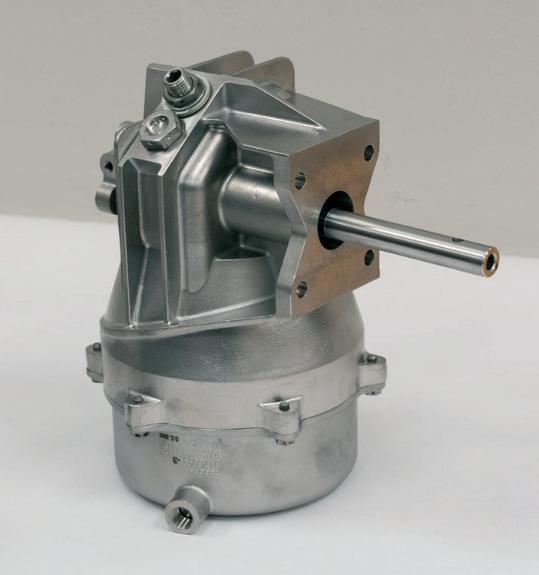
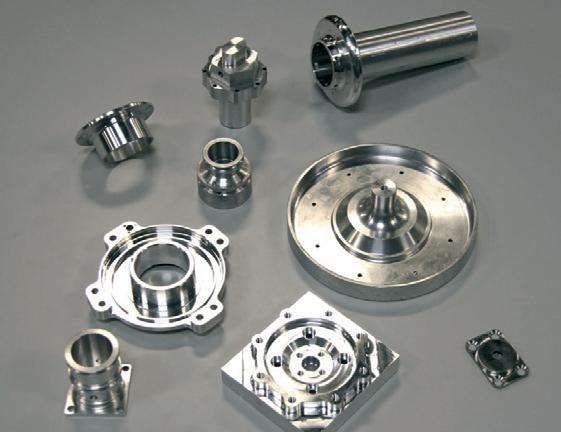
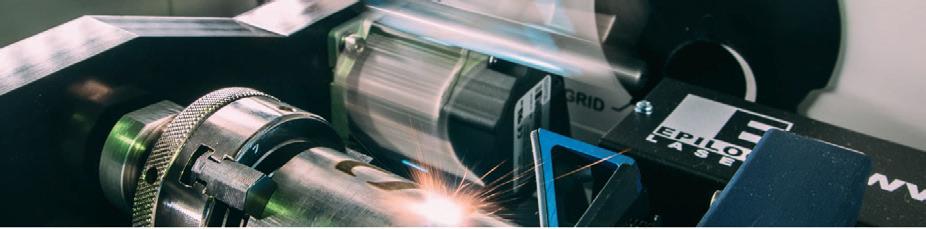
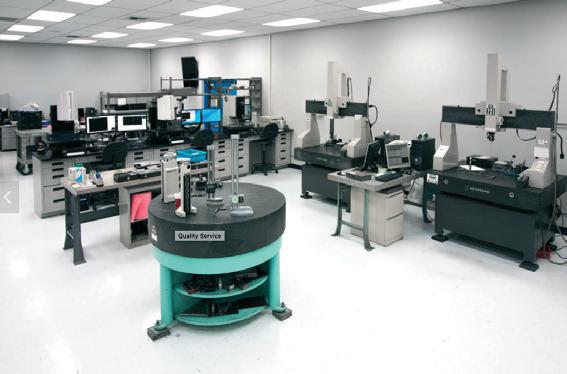
and we are confident you won’t find many shops that have been doing EDM for more than a half century. We are proud that our EDM department received the highest NADCAP status at our last audit – the ‘MERIT Status’.” The company was also awarded ‘Top Shop’ by EDM Today Magazine.
Charlie adds, “We have 3 Wire EDM machines with 4-axis indexing capability, which provides rotational cutting, which can, as is termed in our industry ‘turn and burn’. This allows for fewer setups on complex parts, allowance for more unattended burns and extends the capability of a standard machine. It has also unlocked an entirely new range of part geometries – geometries not possible to manufacture with any other machining method.
A Trusted Partner, MTI excels at Rubber and Rubber-toMetal Bonded Seals. MTI’s machine s h o p offers both CNC lathe and mill precision machining. In its milling department, it offers horizontal and vertical milling, with machine tools that include 3, 4, and 5 axis. MTI mills can machine parts up to 8” X 12” X 24”.
The MTI turning department is equipped with high productivity and rigid turning (including live tooling). They focus on turning parts in one operation where possible with dual spindle equipment. This eliminates costly operations like deburring and backside finishing operations. MicroTronics has also had remarkable success in unattended turning. Their record is 63 hours of uninterrupted, unattended run time.
The machine shop also offers in-house surface finishing capabilities, including grinding and honing. The latest capability brought in house, Jeff says, is laser marking. “Our customers were having difficulty with ink markings that could come off when they interacted with certain chemicals. Our proprietary technique has enabled us to mark on rubber and it doesn’t come off with chemicals. It has been so popular that we have aerospace customers who come to us strictly for our laser marking.” MTI offers laser part marking on steel, stainless, aluminum, brass, copper, magnesium, plastic, to name a few.
Charlie says that MTI opened its machining division to help reduce turnaround times for their EDM and rubber molding customers. And now its also being used to produce assembly details that are essential to the providing turn-key assemblies to their customers. “Everything we can do to help our customers through reduced turnaround times and increased consistency of quality parts, we bring in-house to control the complete process and eliminate supply chain constraints and delay issues.”
Like all areas of MTI’s manufacturing, the company focuses on increased automation. All departments are tasked with finding ways to automate tedious and repetitive tasks. This helps our machinists focus their talents on truly meaningful work.
Micro-Tronics is your complete source for all manufacturing solutions with a focal on top-level integration.
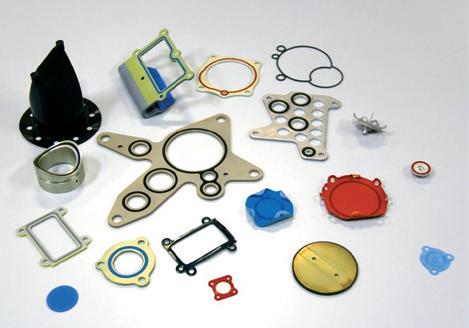

MTI offers a range of in-house services to their customers, including metal and rubber manufacturing, bonding, and product assembly, which allows them to cut weeks to months off startup lead times. • MTI’s application engineering team can ensure your designs are prepared and well suited for manufacturing. • Their machine shop enables them to machine the metal components (e.g., metal rings and plates) required for the rubber-to-metal bonding operations. • MTI’s tool room enables them to design and build all molds and finish dies. • The rubber formulation capabilities enable MTI to make standard or custom materials as needed. • Their assembly shop enables MTI to mate and assemble other components to molded rubber products to create larger subassemblies as well as kit the molded rubber products with other assembly line components. • MTI’s value-added services enable them to
accommodate laser marking, bag and tag, stock programs and other final packaging requirements.
Micro-Tronics has the experience, equipment, and expertise to deliver bonded seals for many different industries and applications. With over 30 presses with tonnage that ranges from 30-400 tons, MTI offers injection, transfer, and compression molding and over 25 AMS, MIL, and or ASTM standard materials with NADCAP certified molding.
MTI can manufacture products to meet your exact specifications and standards, including AMS, MIL, SAE, and ASTM. MTI’s AS9100D- and ISO 9001:2015-certified quality management system and NADCAP certification ensures all customers receive the highest quality solution. Machine Shop – AS9100 Revision D Certified
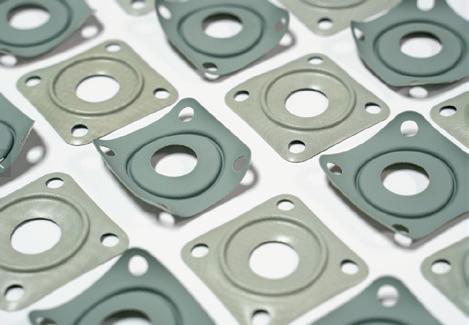