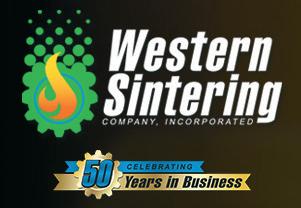
4 minute read
Feature Articles...........................1,10
For over 50 years Western Sintering has been an industry leader for powder Metallurgy.
Precision and Control
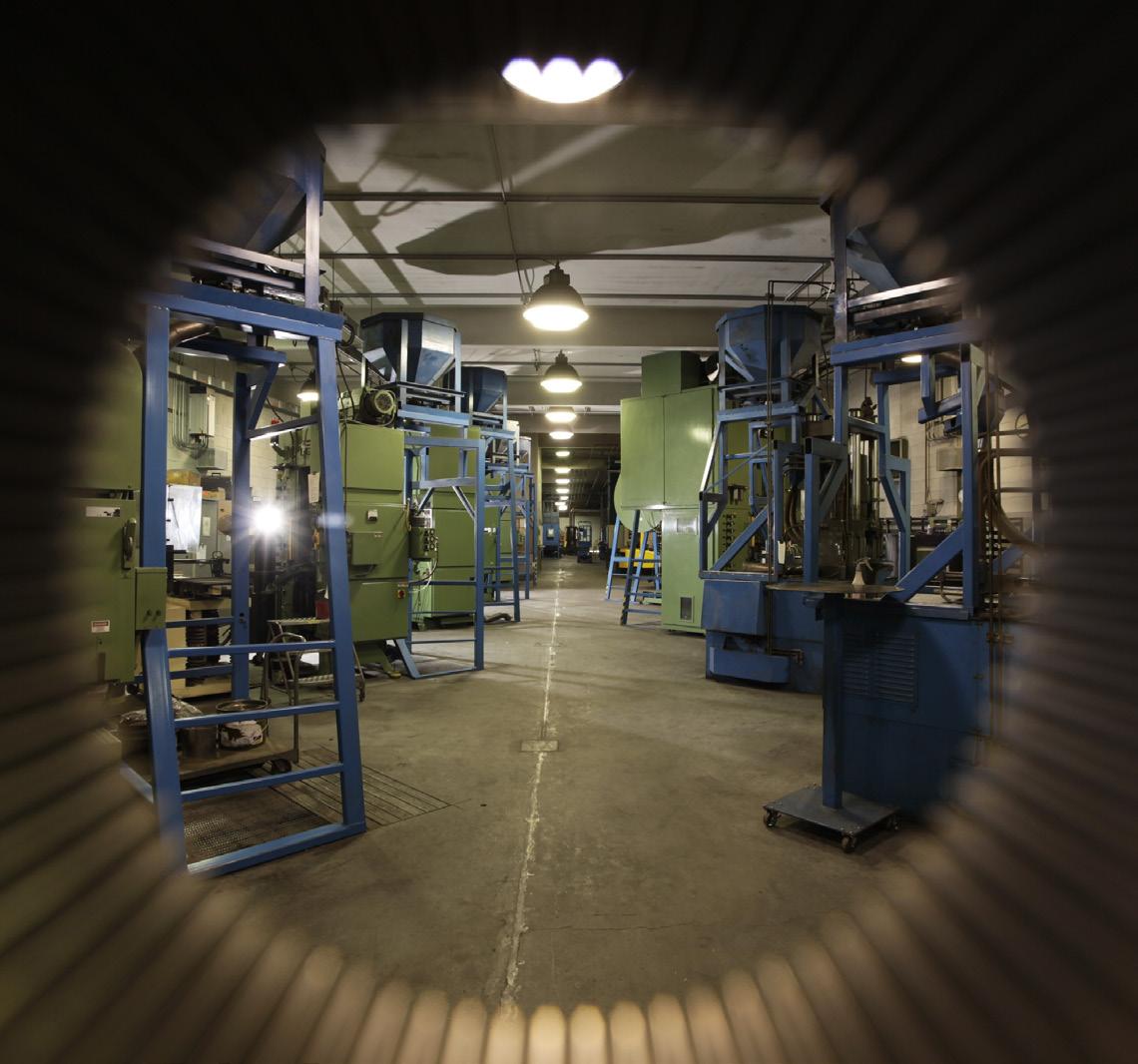
Controlled Atmosphere Sintering is the process of forming a solid mass of material by heat and/or pressure without melting it to the point of liquefaction. The study of sintering in metallurgy powder-related processes is known as powder metallurgy. An example of sintering can be observed when ice cubes in a glass of water adhere to each other.
Sintering happens naturally in mineral deposits or as a manufacturing process used with metals, ceramics, plastics, and other materials. The atoms in the materials diffuse across the boundaries of the particles, fusing the particles together and creating one solid piece. The sintering temperature does not have to reach the melting point of the material being sintered and thus the pressed component maintains its shape during sintering. .
In this process the parts are placed on ceramic trays and ran through a sintering furnace where the parts are heated in a controlled atmosphere up to a sintering temperature suited to the material and just below the metals melting point. The sintering temperature allows the powder metal particles to bond together and form a solid metal finished part. Yes, their expert engineers create a process that allows for high volume, consistent repeatable perfect parts every time. Their CNC machine shop can do what we call a ‘Kiss’ in the industry, to add any extra feature requirements they are not able to mold such as threads and undercuts. The powder is made from recycled metal and the press and sinter to net shape process, without the need for machining from a large piece of raw metal, is why Powder Metal is a “Recognized Green Technology”. WSC uses the same feed stock powder as Additive 3D Manufacturing process, but with hard tooling, high speed presses and robotic automation parts are pressed quickly, uniformly, consistently, and faster than most forms of manufacturing.
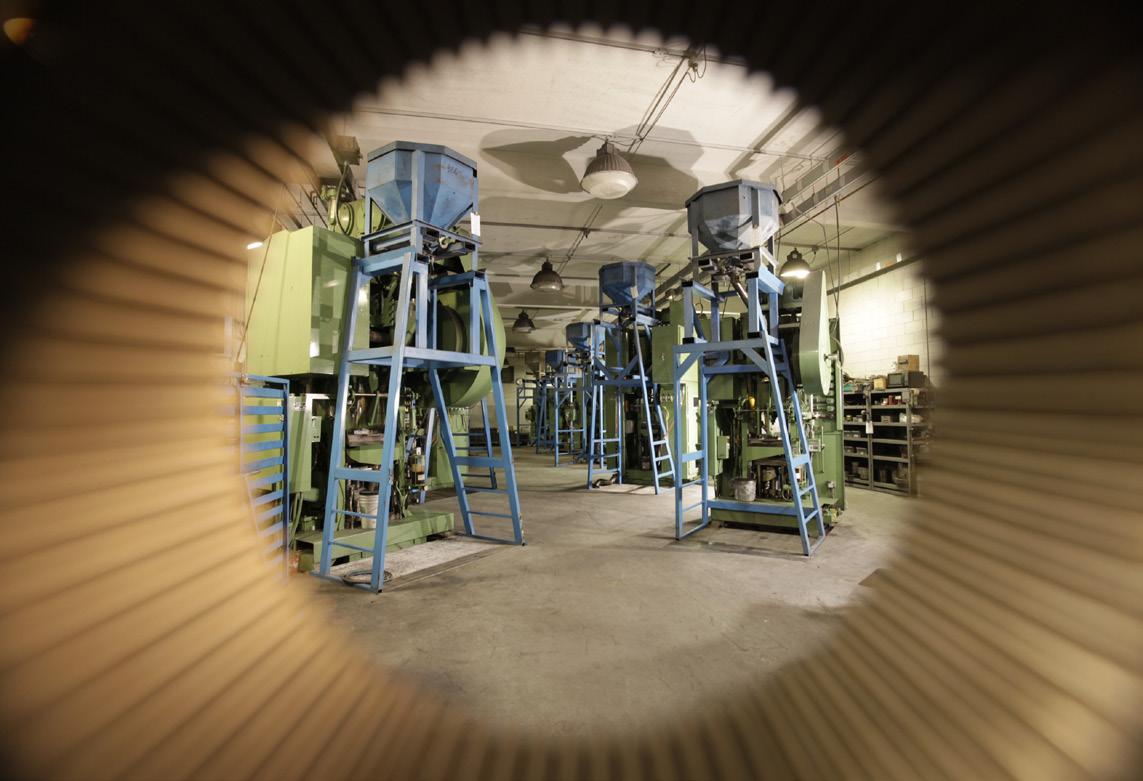
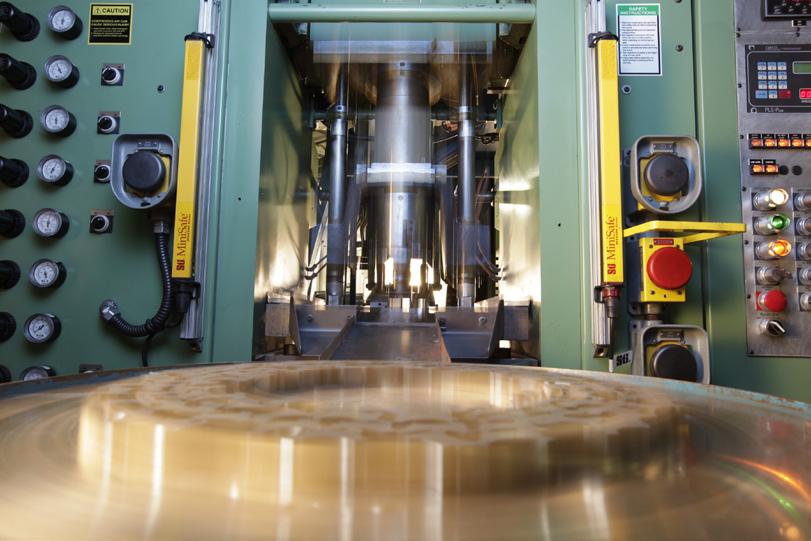
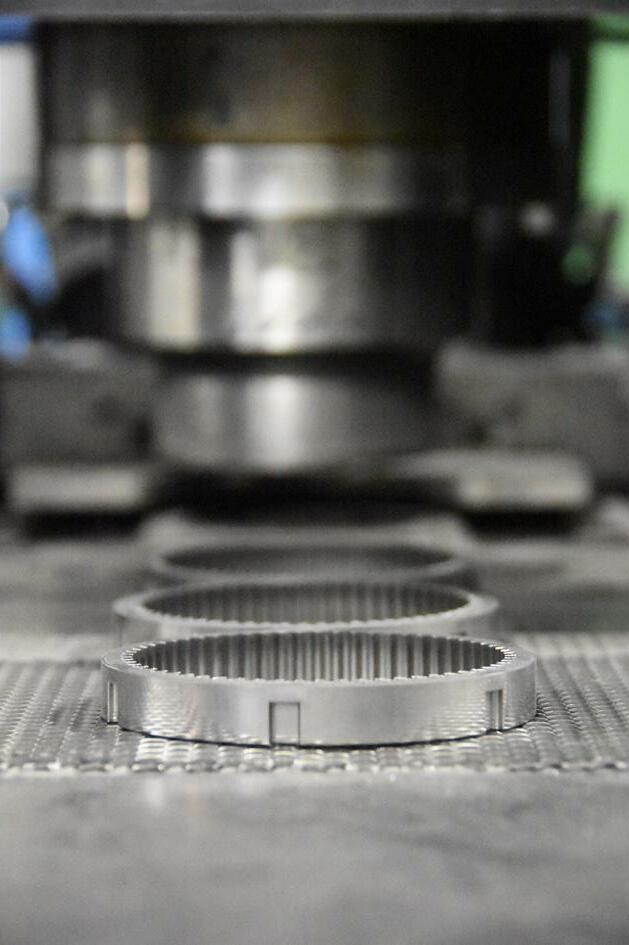
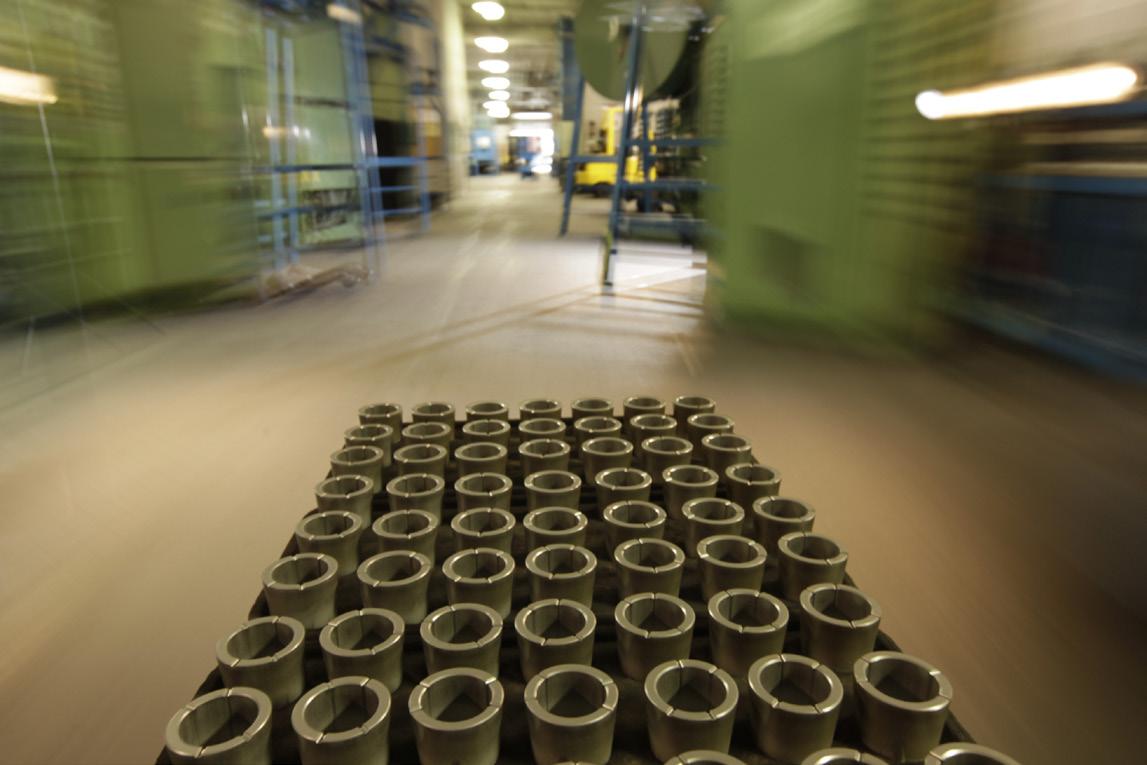
At Western Sintering we use controlled atmosphere sintering in our sintering furnaces. Our furnaces are electric heat with Hydrogen and Nitrogen used as a protective atmosphere in the sintering of our compacted powder metal parts. The Nitrogen acts as a cover gas and the Hydrogen acts as an oxide reducer for the parts being sintered.
One analogy for these two sintering atmosphere gases is to think of the Nitrogen as Water and the Hydrogen as Soap in helping to keep the pressed powder metal parts clean of oxides/oxidation while going through the sintering process. With our ability to fine tune the amount of each of these gases in our furnaces along with precise temperature control we can tailor our sintering to the needs of the different parts that we sinter.
Reduce Manufacturing Costs
Powder metallurgy is the process of blending fine powdered materials, pressing them into a desired shape or form (compacting), and then heating the compressed material in a controlled atmosphere to bond the material (sintering). The four basic steps of the powder metallurgy process are Powder Manufacture, Powder Blending, Compacting, and then sintering.
Compacting is generally performed at room temperature, and the elevatedtemperature process of sintering is usually conducted at atmospheric pressure. Optional secondary processing often follows to obtain special properties or enhanced precision. The use of powder metal technology bypasses the need to produce the resulting products by metal removal processes, thereby reducing manufacturing costs.
As an ISO9001 company, Western Sintering maintains an expertise in many varieties of metals from alloy steel, stainless steel, copper, brass, nickel silver (white brass), bronze, aluminum, and many others. WSC aligns approved outside processing partners to apply finish plating or powder coating to the powder metal parts. The end result is quality parts, that meet their customers’ expectations. Carefully packaged and shipped to arrive just in time to their customers’ production line.
Western Sintering has maintained their quality service by continuing to add state of the art processing, from 200-ton compacting press machines, 17 zone sintering controlled atmosphere furnaces, to now robotics that aid in handling the pressed parts off the presses. This all adds to the goal of WSC to move the production of their customers parts into a perfect state of
Why sintering is important in powder metallurgy?
The sintering process can determine the optimal structure and properties of the desired finished product. These include the material’s strength, electric and thermal conductivity, ductility, and toughness. Controlling the sintering process is, therefore, key to the entire powder metallurgy process.
Advantages of the Powder Metallurgy Process
• Minimizes machining by producing parts at, or close to, final dimensions • Minimizes scrap losses by typically using more than 97% of the starting raw material in the finished part • Permits a wide variety of alloy systems • Produces good surface finish • Provides materials which may be heat treated for increased strength or increased wear resistance • Provides controlled porosity for self-lubrication or filtration • Facilitates manufacture of complex or unique shapes which would be impractical or impossible with other metalworking processes • Is suited to moderate- to high-volume component production requirements • Offers long-term performance reliability in critical applications • Is cost effective
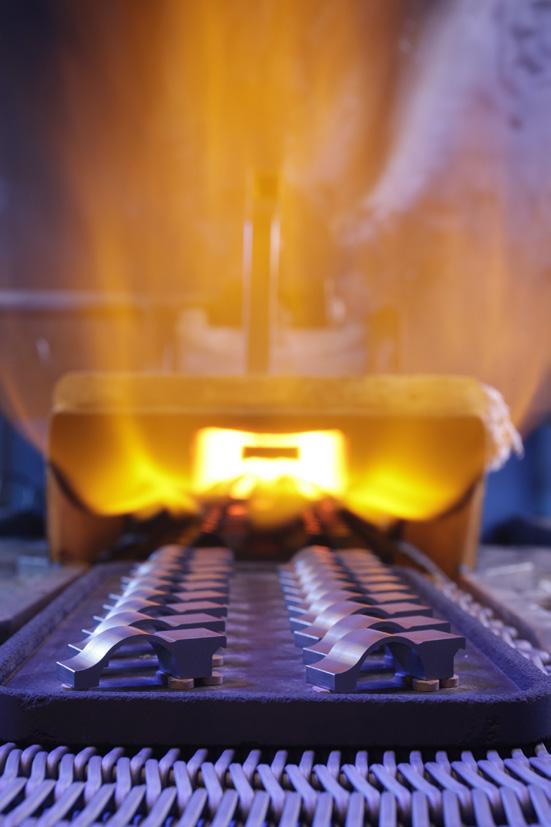
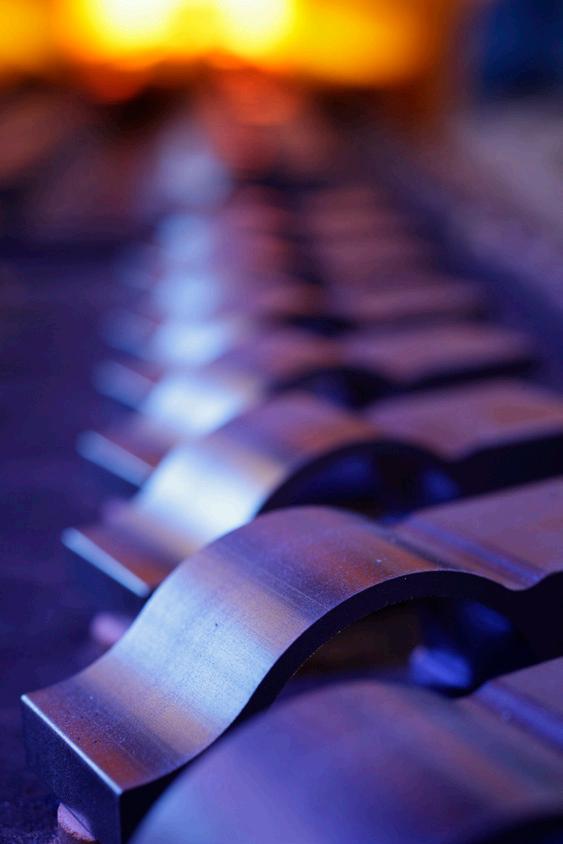