
28 minute read
Silviculture 20
Silviculture Paper highlights key role of forestry in SDGs
Anew paper has highlighted the key role that forests, forest managers and forest science can play in achieving the Sustainable Development Goals (SDGs).
The SDGs were agreed by nations globally in 2015 to tackle the world’s most pressing problems, such as hunger, poverty, inequality, climate change and biodiversity loss.
The Sustainable Development Goals, forests, and the role of Australian Forestry,’ published in Australian Forestry, the journal of The Institute of Foresters of Australia, commits to the rational and rigorous examination of all aspects of forests and the evidence-based improvement of forestry in Australia and the rest of the Indo-Pacific region.
Institute of Foresters of Australia and Australian Forest Growers (IFA/AFG) President Bob Gordon lauded the paper, saying that Australian forest scientists have an important role to play in informing and achieving the SDGs.
“Averting catastrophic environmental and hence developmental outcomes will require a concerted and efficient global effort, and high-quality science is essential to achieving this,” Mr Gordon said.
“Australia is a world leader in best-practice sustainable forest management and, as such, we can support not only our region, but the entire globe to meet the SDGs.
“Worldwide, 350 million people depend on forests for subsistence and income,” he said.
“Evidenced-based active and adaptive forest management can underpin a circular economy while also storing carbon, conserving biodiversity, protecting water supplies and meeting the cultural needs of societies. Well managed forests are a truly renewable resource.”
The paper is authored by Australian Forestry managing editor, Alastair Sarre, and Chairman of the journal’s editorial board, Stuart Davey. Drawing on several recent global publications, it includes a summary of the contributions of forests to the 17 SDGs and the potential impacts of the SDGs on forests and forest-related livelihoods and economies.
Dr Davey said that Australian Forestry is supporting the SDGs by communicating scientific, economic, social and policy research and analysis on forests in Australia and the Indo-Pacific region.
“The world continues to face economic, social, health and environmental crises. Robust, peerreviewed scientific inquiry and civil debate is vital if we are to avert and manage these crises,” he said.
“Our journal, Australian Forestry, is resolved to play its part, and we call on forest scientists and practitioners in Australia and the rest of the Indo-Pacific region to make full use of our platform to help achieve the SDGs.
“Most of the SDGs are to be achieved by 2030, which shows the urgency with which the world needs to act,” Mr Sarre said. “And we need to do so, backed by rigorous science. Forests are vital for our future; we need to know what’s happening to them, and we need to use them sustainably.”
‘The Sustainable Development Goals, forests, and the role of Australian Forestry,’ published in Australian Forestry is available to read at https://doi. org/10.1080/00049158.2021 .1920207
From modest beginnings, Ensign has grown to become one of the most trusted and respected names in the log handling business. Today, Ensign continues to build on that reputation as it continually refines and develops its product range in an effort to supply its clients with the very best tools for the job.
When there’s no standard option available we’ll build something that works exactly the way you need it. If you’ve broken it, we’ll fix it - and if you need it altered to work differently, we can do that too.
That’s why Ensign is the forest industry’s first choice.
LOG FORKS GRAPPLES
Servicing the BUCKETS PALLET FORKSforestry industry FOR PRODUCT & SALES ENQUIRIES CONTACT for 50 years GB FORESTRY
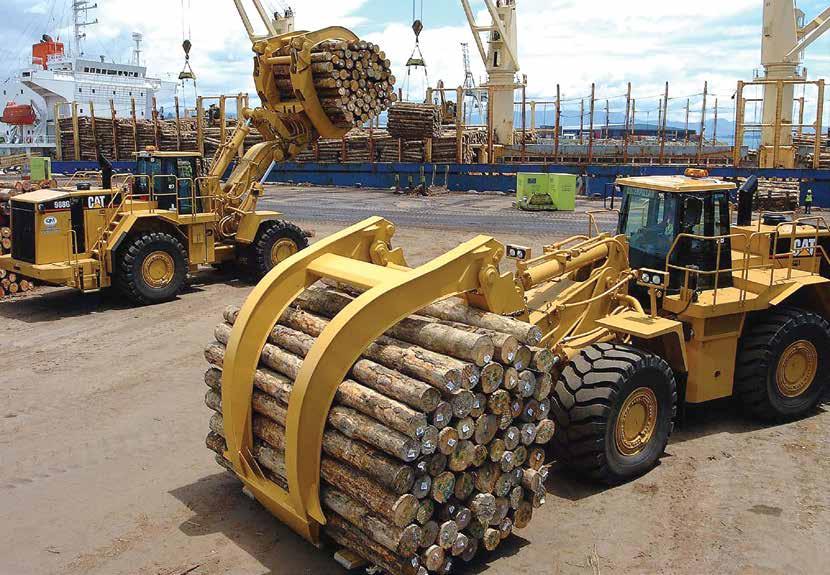
P. 03 8353 6655 E: office@gbforestry.com.au GBFORESTRY.COM.AU
GB Forestry are the exclusive distributor of Ensign forestry attachments & equipment.
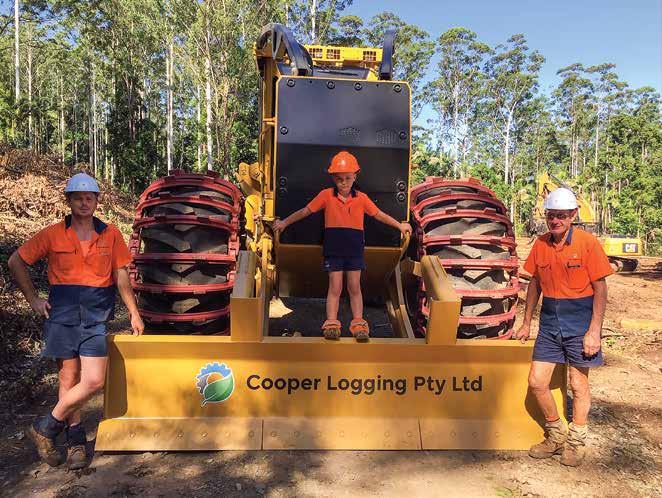
Weiler wheel skidder ticks boxes for die-hard logger
Chris Cooper admits he has a combination of “yellow and sawdust” in his veins. The sixth-generation timber worker and owner of Cooper Logging in northern New South Wales has been a big fan of Cat® equipment since starting his business in 2010.
Even as a primary school aged child he had a love and respect for Cat machinery, seeing his dad work with the equipment.
When Chris launched his business, he bought a number of used Cat machines, some dedicated for forestry work and others re-purposed construction equipment. Every machine served him well despite having considerable hours on their clocks.
Chris admits that before getting behind the controls of his latest purchases from WesTrac - two Weiler S450 Wheel Skidders – he was tentative about diverting from what he knew.
But from day one, he says he’s had no regrets.
“I was a bit nervous buying a brand I wasn’t used to, but the Weiler ticks every box,” Chris said.
“For hardwood logging, you need something that’s really tough and these machines are perfect for what we do.”
After buying his first Weiler Wheel Skidder in April 2020, Chris saw such an improvement in productivity that less than 12 months later, he bought a second machine.
In fact, the similarities between Weiler and Cat forestry equipment may be a lot closer than many people realise.
Weiler Forestry was created in 2019 to acquire the Caterpillar® forestry division and despite the badge change, the Cat quality and reliability remains as robust as ever. The range is marketed through Cat dealers around the world.
According to WesTrac Sales Representative Buddhi Edirisuriya, the machines utilise a Cat drive train, share a number of components and include many of the Cat features.
“The Weiler machines still have the Caterpillar underpinnings and come with the level of support customers expect from their Cat equipment,” Buddhi said.
“While there’s not a lot of awareness about the range in Australia just yet, cus•Chris Cooper, Josh Cooper and Pat Cooper with their Weiler S450 Wheel Skidder
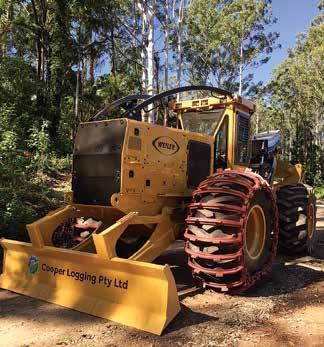
tomers that use the machines are really happy with the results.”
WesTrac Product Specialist – Paving and Forestry Products Michael Kelly says the Weiler range, which includes feller bunchers, harvesters, wheel skidders and loaders, is purpose built for the rigours of forestry operations.
“Safety is paramount with video cameras integrated into the machine, increased LED lighting, polycarbonate windscreens, as well as comfort for the operator such as air ride suspension seats and pressurised cabs to minimise dust ingress,” Michael said.
“The chassis is more heavily engineered than standard construction equipment with thicker grade steel – these machines are built tough to last longer.”
For Chris, the combination of Cat-based reliability and WesTrac service and support is what makes the Weiler machines a valuable addition to his fleet.
“You don’t steer away from something that you know and has treated you right,” he said
“I started with pre-loved Cat equipment and WesTrac support 11 years ago, and those machines just kept going.
“Downtime destroys a business and without that reliability when I started, I wouldn’t have a business today.
“So when WesTrac assured me the Weiler Wheel Skidders were Cat quality in slightly different clothes, I trusted their word and haven’t looked back.”
For more information on the Weiler Forestry Range, contact your local branch.
BRIEFS
KOMATSU UPGRADE
THE cutting unit on all Komatsu C-heads, Constant Cut, will benefit an upgraded design. The upgrade contains no less than 25 points and represents a number of improvements for customers, both in terms of increased productivity and better flow in the production. Constant Cut ensures that the head has a constant and efficient saw chain speed throughout the complete cutting cycle. This ensures efficient cutting and limits problems with cutting cracks. Now the cutting unit has undergone a major upgrade, which means that all Cunits get a new, fresh Constant Cut with productive benefits. Below are some of the biggest new features.
EXTENDED PROTECTION
PONSSE has introduced a new extended protection system for forest machines called Frame and Crane care for machines that have a Ponsse Active Care service agreement. The Frame and Crane care covers main frame structures for up to 10,000 engine hours. Source: Timberbiz
The Frame and Crane care covers main frame structures for up to 10,000 engine hours if the machine has a valid service agreement during that period. The Ponsse Active care service agreement needs to be valid for the whole period, but the agreement can be made in several parts.
NEW LOADERS
PONSSE has launched a new loader product family for the most popular forwarder models. The new K101 and K111 loaders are the latest additions to the product family, also represented by the previously launched K121 loader. The new loaders have been developed in cooperation with customers for efficient load handling, also in demanding conditions.
The new loaders have a structure designed and developed by Ponsse, with special focus placed on reliability and productivity. The Ponsse K101 and K111 loaders are available for Ponsse Buffalo, Buffalo King and Bison Active Frame forwarders.
Komatsu continues its Tassie forwarder success
Komatsu Forest’s success has been the development of over 30 years of local history in Tasmania, firstly with remote service operations during the 90’s followed by the establishment of the first forestry branch in 2000.
Then early 2009 the current larger branch opened at 6 Monroe St Bredalbane which is located near the Launceston Airport and is headed up by David Oliver with Shane McCarthy running spare parts. Between them they have a combined service history of 40 years at KF.
The Tasmanian forest machine business has many challenges and it takes a real team effort with David maintaining the same experienced field service guys for a number of years.
That being Brett Spilsbury and Mitchell Bennett in the north while Mick Gray in the southern region looks after the local contractor’s service needs.
All Tassie sales activities are handled by Nigel Howard with support coming from Brenton Yon. This team consistency is further enhanced by the product support team at Sydney head office and the technical support guys in Wodonga.
This combination of KF’s Tasmanian team and continued long history has provided strong forwarder sales with over 80 forwarders of various models delivered since 2000 including 35 of the current model Komatsu 895.
This has been reaffirmed with the 6 x 895’s delivered over last six months to a range of customers such as Tas Log, C3 Logging, Caulder Contracting and Orana P/L.
The latest Tassie 895 delivery was in late March to Rob Kerrison of Orana Pty Ltd which was his second in the past five months and the fifth since his first 895 purchase in 2015.
These two new units were replacements for the first two which had 9,000 hrs and 8,000 hrs respectively and were sold direct to their new owners with the help of Nigel and Brenton.
There are typically many family/ human interest stories associated with the forest industry in Tassie and a typical Komatsu Forest story is Meeghan Price who operates TP Bennett & Sons’ Komatsu 895. The sons Adrian and Neil operate in plantation hardwood around the Huon region of southern Tasmanian. They purchased a new 895 back in Nov 2018 when Meeghan had just finished her HSC exams and within the following week was operating the new 895.
Meeghan is a proud member of a fifth generation forestry family and the granddaughter of the late Tony Bennett. She was the youngest female in Tasmania to have her Forest Works licence and now holds a Certificate III in Harvest & Haulage. Meeghan started “officially” working around forest machines when just 14 and her passion continues having operated the 895 since new and clocking up a little over 4250hrs.
The Bennett name has been synonymous with forestry in Tasmania for over 50 years and with family members like Meeghan making sure this continues to be the case into the future.
Brett Jones, Managing Director of Komatsu Forest Pty Ltd, has very fond memories of Tasmania when he was first involved with the earlier Valmet forwarders. In the late 80’s, early 90’s he made multiple trips to Tasmania to help provide technical support for the original Valmet forwarder fleet of 886’s and 892’s.
“The forwarder technology of today has certainly come a long way from those two earlier Valmet model forwarders,” says Brett.
“Considering the early forwarder days and since KF’s involvement in Tasmania it would be fair to say the KF team must be considered the most experienced team in Australia.
“Actually, I am personally very proud of being with the Valmet and now Komatsu brand for almost 35 years, how has that time gone so quick,” he said.

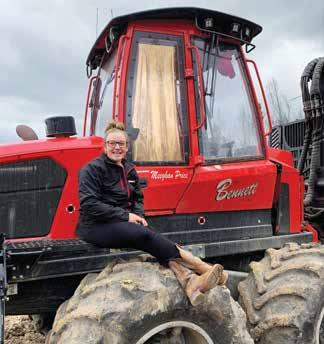
•Above: Orana’s Latest Komatsu 895. Left: Meeghan Price Komatsu 895 Operator.
Morbark grinder on its way Down Under
The first Morbark 6400XT Horizontal Grinder will be arriving soon in Australia.
“We expect the Morbark 6400XT to be well received in Australia,” National Sales Manager – Forest-ry and Recycling, Mark Malone said.
“Morbark’s proven reliability and quality has been the industry standard, and we believe this new model will minimise downtime, increase production and make maintenance easier. All backed by the service support and reputation of Lincom Group.” Morbark’s director of Industrial Sales Michael Stanton said Morbark had listened closely to cus-tomers when developing 6400XT Wood Hog.
“We took our previous proven design technology and added the features our customers want and the versatility they need when we created these high-production units.”
“The Model 6400XT is the newest model in Morbark’s next-generation platform of horizontal grinders,” said Stanton. “Industry demands for high-production mobile units that meet stringent logistic restrictions but remain economically viable were the leading drivers during the design phase.”
The 6400XT includes many feature improvements present in the smaller 3400XT, introduced last year. The infeed bed is 24 inches (60.96 cm) longer than previous Morbark grinders in the 1,000-plus horsepower range and has sloped sides. This configuration improves operator sight lines for more efficient loading of material. Standard on the 6400XT is a removable infeed chain return floor, which allows excess material to fall away to minimize the wear on the floor, bed chain and inserts, particularly useful in land-clearing or other applications with dirty material.
Also similar to the 3400XT is the focus on transportability. The 6400XT weighs in at less than 96,500 lb (43,772 kg) and measures 11’51/2” (3.49 m) wide with the standard Caterpillar 325L undercarriage with 600mm double grousers, allowing the unit to be transported to nearly all domestic and inter-national markets.
“When we introduced the 3400XT last year, our customers responded very favorably,” explained Stanton. “It had a major impact on the market, and we expect the 6400XT to be as well received.”
The 6400XT has several operator-friendly features focusing on accessibility for daily maintenance, including:
• The extended 31.5” wide (80 cm, 25% increase) platform between the hood and engine for ease of changing grates and access to diesel engine • A consolidated area for oil and hydraulic filters • An independent hammermill drive tensioning system for ease of adjustment • The larger feedwheel (40”/101.6 cm diameter, an increase of more than 15%), which raises 17” (43.2 cm) above the current 4600XL yoke and 11” (27.9 cm) above the 6600 yoke to allow better access to the hammermill during insert inspection.
Key Points
•A fixed work platform for better access and safety during common grate and hammermill maintenance •A hydraulic hinged door and hood locking system to provide quick access during grate changes — the hydraulics unlock with a simple turn of a knob. •An independent hammermill drive tensioning system for ease of adjustment
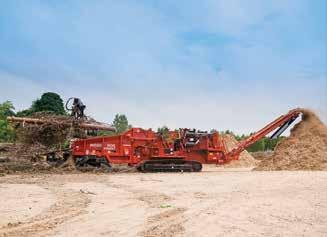
MORBARK
3400XT HORIZONTAL GRINDER
Fitted with a pin and plate hammermill, 34’’ top feed roll, chain type feeder, Caterpillar C18 (765HP) engine and Caterpillar 320L tracks.
Easy change grate system and remote control allowing for monitoring and adjustment of the engine and other machine parameters from the safety of your loader or excavator.
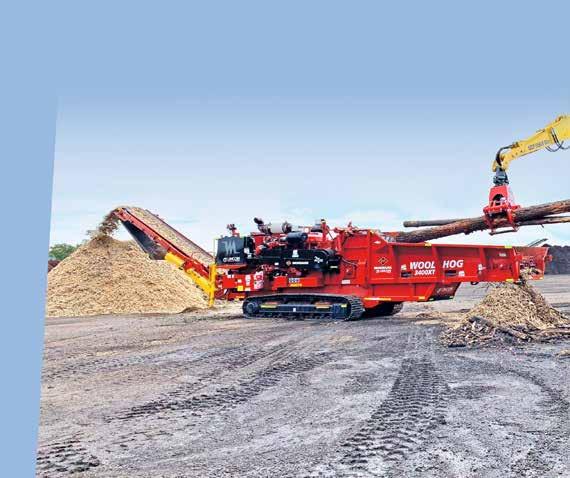
2400XT, 3000XT and 6400XT models also available.
SALES HIRE SERVICE PARTS
BRIEFS
SAFETY HUB
A NEW online safety hub has been unveiled by Australia’s leading transport and logistics specialist insurer, NTI, to support the growth and development of the industry.
The Better Business Hub helps protect Aussie fleet, transport operators and drivers by providing interactive, downloadable, applicable tools and resources to support them in their day-to-day.
The first educational content series on the Hub, Business of Safety, has been made possible through a $300,000 Federal Government grant, administered by the National Heavy Vehicle Regulator (NHVR), supplemented by NTI’s own in-kind contribution to match the grant.
For more information and to access NTI’s new purposebuilt online platform, go to The Better Business Hub.
WORK DIARIES
THE NHVR has approved Quallogi by Kynection as a fifth Electronic Work Diary (EWD) option for heavy vehicle drivers.
The introduction of EWDs means drivers can record their work and rest hours by pressing a button, rather than spending time ruling lines and counting multiple time periods on multiple pieces of paper. It includes features, such as alerts, to assist drivers to manage their compliance with work and rest rules.”
Drivers must continue to carry their written work diary for a transition period, to ensure that they comply with the requirement of carrying 28 days of records.
FIRE SAFETY
THE ARTSA Institute has launched a Truck Fires Safety Program to tackle heavy vehicle fires occurring each year in Australia.
The fire safety program consists of four manuals and six videos aimed at drivers, maintenance staff, fire investigators and transport managers.
The manuals and videos are downloadable at www. artsa.com.au/fires
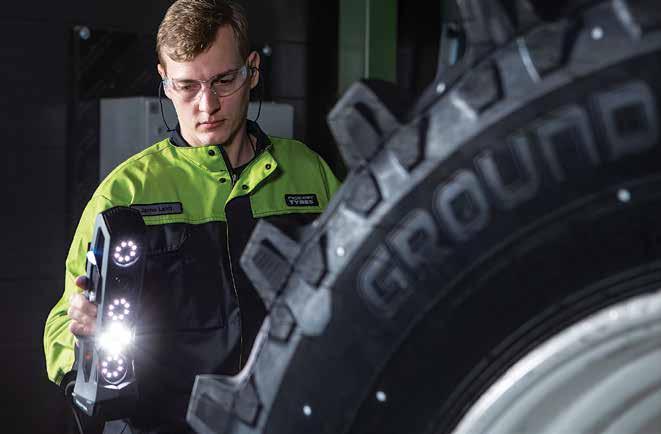
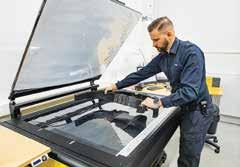
Testing time for safer tyres
Making professional tyre use safer and more efficient sets high demands on product development. To bring new ideas to the market faster, testing has an important role. Nokian Tyres has invested heavily on a new, state-of-the-art test centre for Nokian Heavy Tyres, upgrading the testing capabilities to a whole new level with added automation and capacity. Despite the challenges caused by the COVID-19 outbreak, the magic is already happening in the new building – enabling us to introduce more and better new heavy tires.
Due to Covid-19 restrictions, many phases of the construction process have been managed remotely.
“This kind of flexible problem-solving has been typical for the whole construction project, and it has kept us on schedule. Hats off for the whole team that made it possible,” says Development Manager Matti Kaunisto from Nokian Heavy Tyres. No substitute for testing
In the tyre product development process, testing is essential as it proves (or disproves) the design calculations and gives important data back to designers. That’s why the new, nearly 4000 m2 facility is a vast improvement both in terms of testing quantity and quality.
“For example, the drum testing capacity grew significantly,” says R&D Director Kalle Kaivonen from Nokian Heavy Tyres. “The product development and OEM collaboration are much more efficient. Thanks to the added capacity, the earlier bottlenecks in testing have been eliminated. And there is plenty of room for future investments still.”
Another important factor is testing quality. “The new machinery enables us to gather more data and analyse it better, as the integration with the product development is more solid than before,” Kaivonen says. Testing by order
The purpose of the facility is to provide answers. The whole testing process from installation to measurements and 3D scanning, from pressure testing to section-cutting is optimized to provide quality data efficiently for different information needs.
“Different kinds of tests and analysis can be ordered by a product development team, customer service or by a machine manufacturer, for example,” says Kaivonen. “We can provide them with extremely broad range of different analysis and in-depth information.” Ergonomics and pride
In work ergonomics, the transformation from old premises to purpose-built facility is massive. In the design of the new test centre, special attention was paid to the safe and ergonomic handling of the tyres and wheels. “Everything is more clearly laid out now and on a same level,” Matti Kaunisto says. “This makes the work safer and more comfortable – and has clearly boosted the spirits of the whole team.”
Speaking of work safety, the process where the tire segments are scanned with a high-resolution scanner and transferred digitally fits well together with today’s social distancing requirements. “The tyre cross section data moves between the testing and R&D teams digitally, without the need of any physical contact,” Matti Kaunisto says. Not just new tyres
Besides product development, the tyre testing facilities are needed for manufacturing quality control – but also for customer service.
“In a rare occasion, there can be a tyre failure, abnormal noise or some such problem in the field that needs to be thoroughly figured out,” says Mikko Pukkila from Nokian Heavy Tyres’ technical customer service.
“In these cases, tyres can be inspected and analysed in test centre. The feedback from the field gives us important understanding of the tyre life cycle.” A building full of Hakkapeliitta spirit
Sometimes, the Nokian Tyres way of doing things is referred to as “The Hakkapeliitta spirit”. It sums up the spirit of innovation and the resourcefulness a specialised manufacturer has, and the new building depicts it well – from its smart engineering down to the self-cleaning, energy-conserving windows. What’s more, the centre also lives up to company values of working safety, sustainability and peace of mind.
“There’s hardly any waste that isn’t recycled,” says R&D Director Kalle Kaivonen. “Also the heat generated by the test equipment is gathered for heating the facility, and more heat is generated by the local biofuel plant.”

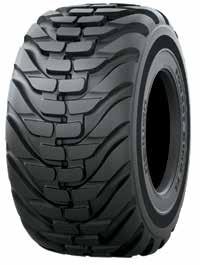
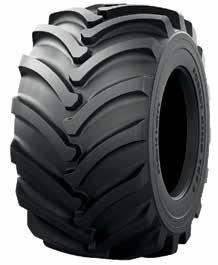
Harvester heads New technology updates boost harvesting head range
The Tigercat harvesting head product range continues to gain momentum globally as more contractors opt for the full Tigercat base machine and head set-up.
There are many advantages having the base machine and head from the same manufacturer. The head can be installed at the factory, which creates efficiencies, reduces lead times and freighting costs. Having one point of contact for all maintenance and service work is another key advantage that makes the day-to-day operations for Tigercat owners easier and more efficient. User-friendly D5 Control System
The D5 system combines field-proven hardware and bucking (cross-cutting) control with a simple and intuitive Tigercat-developed user interface. Available on three levels of control and reporting, the D5 system handles multiple jobs with multiple operators, and allows for customising menus and settings, right down to joystick button functions. Over 70 operator specific parameters are available to tailor controls to each operator’s preferences. The clean and easy to follow layout of the touch control screen allows the operator to make adjustments as easily as using a smartphone or tablet. RemoteLog for off-site access
RemoteLog provides machine monitoring and fleet management in real-time without need for a cellular signal. The RemoteLog data includes; • Geographic location • Satellite based text messaging • Activity timeline • Production metrics summary • Diagnostics • Fuel levels and consumption • Mechanical data • Analytics
Late last year Tigercat released new RemoteLog features including a new diagnostics dashboard where mobile users can easily review machine fault codes grouped in cards and colour coded by severity. Office personnel may view fault codes in an easy to sort and filter list. A single click brings up technical information for any fault code. The easily accessible engine troubleshoot guide gets you the answer you need quickly.
A new machine summary report was released with a new one-stop machine summary report being sent to the user weekly. It contains data such as operating time, production metrics, total fuel consumption, fuel rates, engine hours, machine utilisation, and summary of fault codes.
The offering provides enhanced machine management with easy access to the control software version running on the machine. Check telematics firmware version to see if it needs to be updated and quickly find your primary dealer contact.
Lastly the new production metrics can track how much you are producing with your machines. Mulch•Tigercat 575 (23”) Harvesting Head
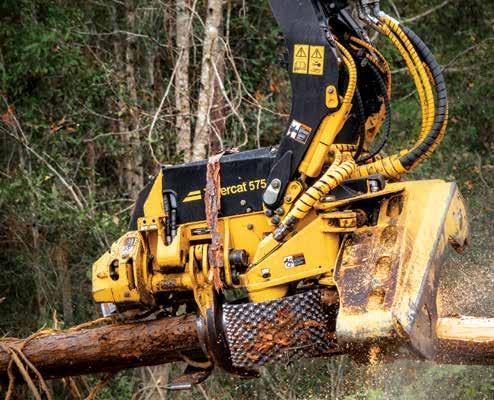
ers now reporting mulched land area, harvesters and processors report production volumes and stem counts while forwarders report number of loads.
More improvements were released in April this year with a RemoteLog web service. You can now access the ‘Data that Matters’ from RemoteLog directly through a new web service using your IT servers. Now it is possible to share geographic position and production data for your machines with whomever the machine owner wants, such as landowners and forestry operations companies. RemoteLog utilises the well documented ISO 15143-3 (AEMP 2.0) Web API that is widely used in mobile machinery applications. Direct on-site telematics via LogOn
LogOn is an on-board system that gives access to onsite telematics using a secure Wi-Fi hot spot. It gives the user quick access to the following data; • Detailed activity chart • Stem count and production volume • Detailed failure cause and repair information • Easy firmware updates with the Tigercat Mobile
App update manager • Access to operator and service manuals
Updates were also introduced for LogOn reports in April this year - You can now easily view production, activity timelines, and fuel consumption on your mobile device using LogOn at the worksite. Formatted reports in PDF or CSV formats are now downloadable to save to your mobile device. Reports can be viewed anytime or shared through email.
Tigercat harvesting heads are designed and built to match the high-performance capabilities of Tigercat tracked and wheeled carriers and are well suited to a variety of jobs including at-the-stump harvesting, roadside processing and debarking.
The range of Tigercat harvesting heads now includes a 575, 570 and 568 model.
“Several of the Tigercat heads are now working in Australia in various applications and species. We are very encouraged by the feedback from the contractors that are reporting improved production and ease of maintenance. We are confident the Tigercat harvesting heads will result in a lower cost per tonne than competitor heads well into the future”, says David Hazell, Managing Director at Onetrak – the national dealer for Tigercat in Australia.
Visit www.onetrak.com.au or call 1300 727 520 to learn more about the Tigercat range.
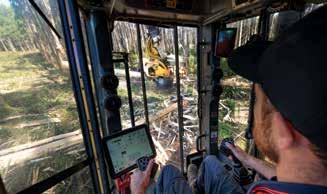
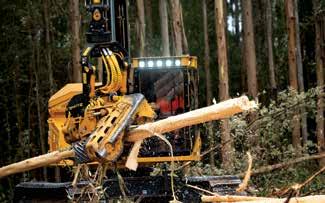
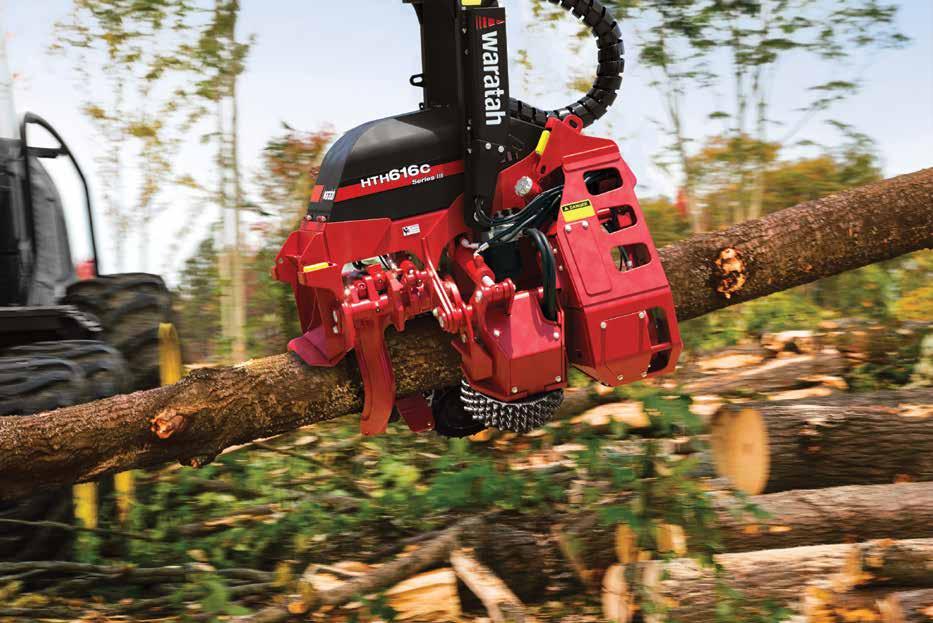
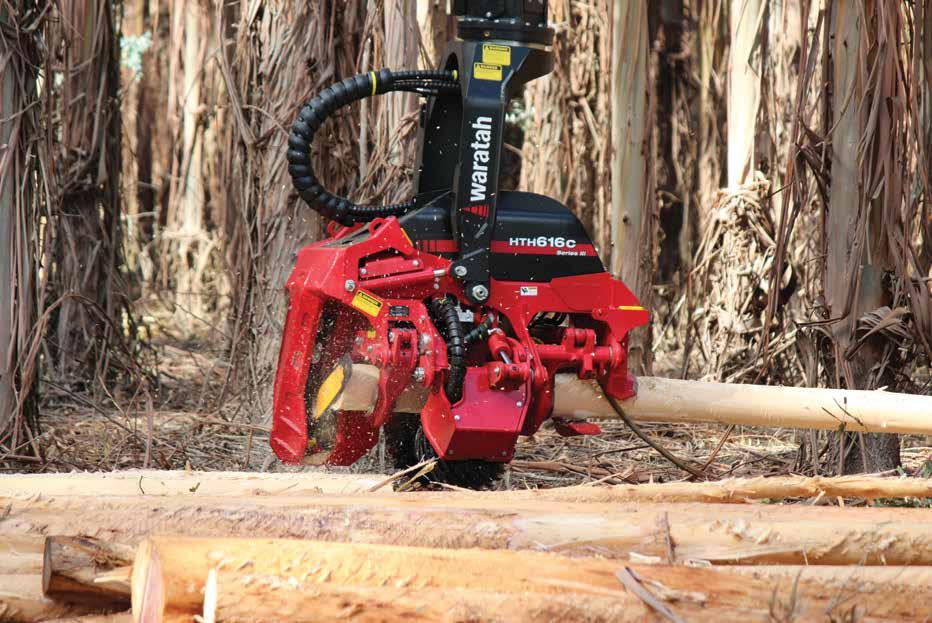

Looking Back
Mills across Australia are facing difficult times as the Covid-19-fed downturn in the building industry develops, but they are prepared.
Up to 43,000 new homes will not be built in the next 12 months as a result of Vovid-19 according to new economic modelling release3d this week by the Master Builders Association.
AKD Softwoods has temporarily stopped production at four mills due to the predicted decrease in demand for building products.
The Queensland timber industry has called on the Queensland Government to ensure forestry biomass is fully utilised and promoted in the State’s renewable energy future.
Timber Queensland Chief Executive Officer Mick Stephens said, “Bioenergy already represents over 65% of the State’s renewable energy output, mostly from the use of bagasse from the sugar industry. Biomass from timber processing such as sawdust and forestry waste can also offer significant potential to further contribute to the States renewable energy future.”
A NEW online tool for managing spotted gum forests is now available for private landholders to calculate their land’s carbon, timber and grazing productivity. The online resource works as a calculator using specific data related to spotted gum native forest sites in Queensland and northern New South Wales.
The spotted gum productivity tool and a comprehensive user guide are available as a free download from the forestry section under Plant industry tools at http://agbiz. business.qld.gov.au
Department of Employment, Economic Development and Innovation (DEEDI) research scientist Tom Lewis said the tool estimated timber productivity, grazing productivity and carbon levels to help land owners determine the economic and environmental benefit of their land.
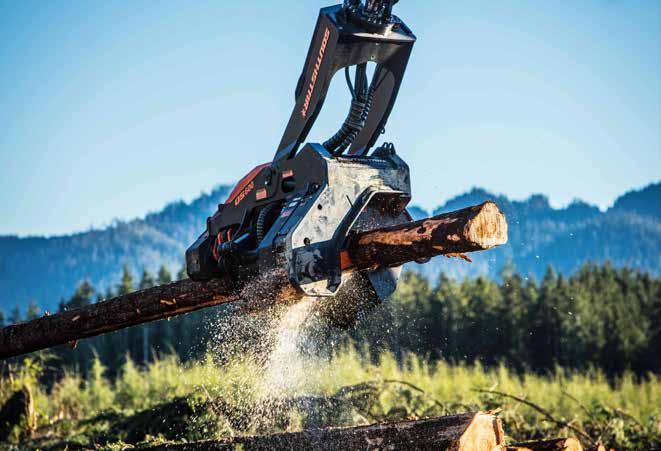
Southstar ticking all the boxes
The Southstar QS600 head ticks all the boxes as a productive 24” harvester/processing head for medium to larger timber.
Weighing in at 3600KG is it well suited to a 30-tonne excavator-based carriers or many of the larger purposebuilt levelling base units. Some of the standard features include: 360 degree rotation, laser find end, four driven rollers for maximum traction with auto tensioning on the ¾ “ main saw.
All Southstar frames are engineered from quality JFE high tensile steel and significant engineering effort has been made to achieve a durable “ built to last product “ that is a serious competitor in harvesting applications globally but especially in this part of the world where our larger wood tends to test attachments to their fullest capacity.
One of the unique features of the Southstar processor / harvester is the East – West valve configuration allowing for a super clean easy to maintain hose layout within the chassis. All Southstar products offer excellent serviceability to the main control valve area. The processing arms allow for easy pick up of logs in the cutover and the four driven rollers and frame design provide excellent traction and tracking in the roughest of timber.
Control system options include the Dasa 5 with a new second option soon to be released giving full compliance with Stanfor- D 2010 protocols and data reporting.
The success of the Southstar products in the industry has been significant by anyone’s standards with more than 900 attachments operating in the field. Southstar Equipment is part of the Quadco Group and can offer a full range of felling and processing heads including fixed disc sand and bar saws, direction bar saws, mulchers and of course the full range of Southstar harvester & processing heads from the QS450 up to the largest QS630.
Check out the product range at www.southstarequipment.com or contact Dean OConnor on +64 21 842413, email: doconnor@quadco.com
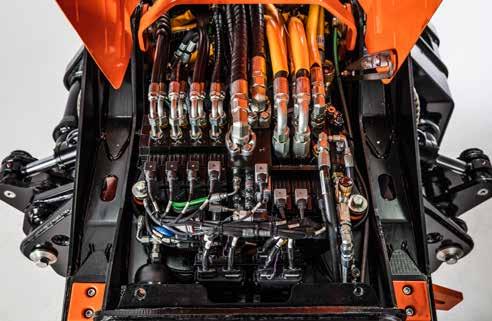
•The Southstar QS600 head in operation and, above, the internal working of the head.
New H423 a harvester head for all the right reasons
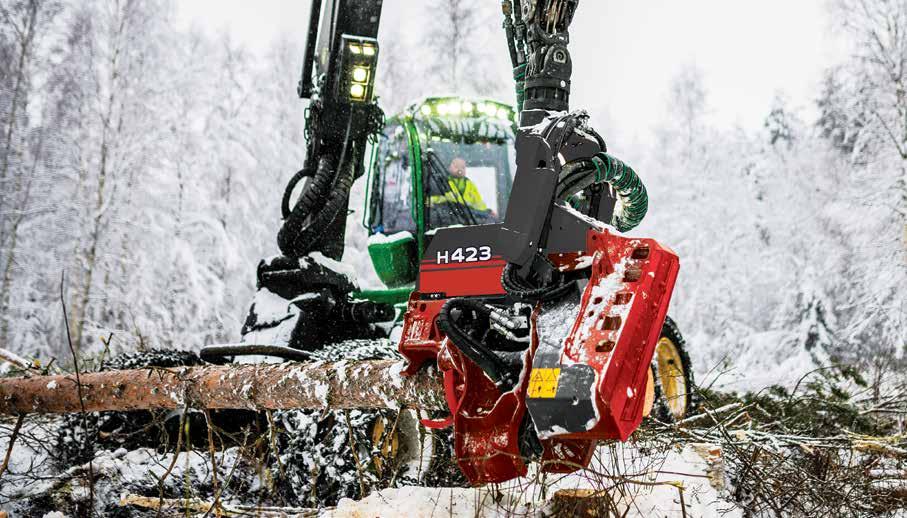
Key Points
•Waratah Forestry
Equipment, headquartered in
Rotorua, New Zealand, has served the global forestry industry for 45 years, manufacturing harvesting and processing heads as well as harvester and forwarder cranes in its state-of-theart facilities in New
Zealand and Finland. •The company’s extensive support and parts distribution network, rigorous global application testing, advanced manufacturing systems and sophisticated quality measures deliver customers with durable and reliable forestry equipment that is Built to Work.
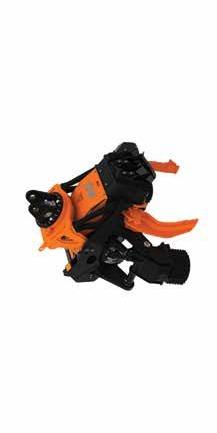
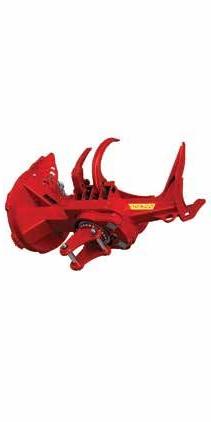
Waratah Forestry Equipment has released details of a new H423 harvester head designed to carry out a wide range of harvesting jobs from early to late thinnings, and even light regeneration harvesting.
Waratah says that with outstanding multi-tree-handling qualities, a compact frame design and excellent power-to-weight ratio, the H423 masters fast and precise felling and crosscutting.
“The Waratah H423 provides fantastic performance in thinnings,” Brent Fisher, product marketing manager for Waratah, said.
“Its short frame, fast feeding and optimal capacity position this model to make quick work of any thinning job that comes its way.”
The H423 is well-suited for delimbing stems of all diameters. Its outstanding multi-tree harvesting qualities and excellent power-toweight ratio take productivity to the next level.
Ideal for thinnings and other fellings where the tree diameter at breast height is 150-350 mm (6-13 in.), the 955 kg (2,105 lb.) H423 features strong, fast feeding in a nimble design.
Additionally, the H423 boasts a 420 mm (16.5 in) tip-to-tip delimbing diameter providing ample range for superior delimbing - and when combined with its 580 mm (22.8 in) cutting capacity and optional multitree-handling equipment, it is unmatched for productivity in varied diameter stands.
Beyond its productivity features, the H423 also hosts a variety of features that make it both reliable and easier to service – extending productive time.
This new model features next generation hose routing from the boom to harvester head and well protected hoses to the feed motors making interference from understory or limbs a thing of the past.
Likewise, serviceability to the main valve is easier and possible thanks to a new hinged valve cover and improved access to greasing points.
The Waratah H423 is currently available to customers in Europe, the United States, Canada, Australia, New Zealand, Russia, Asia Pacific, and Latin America.
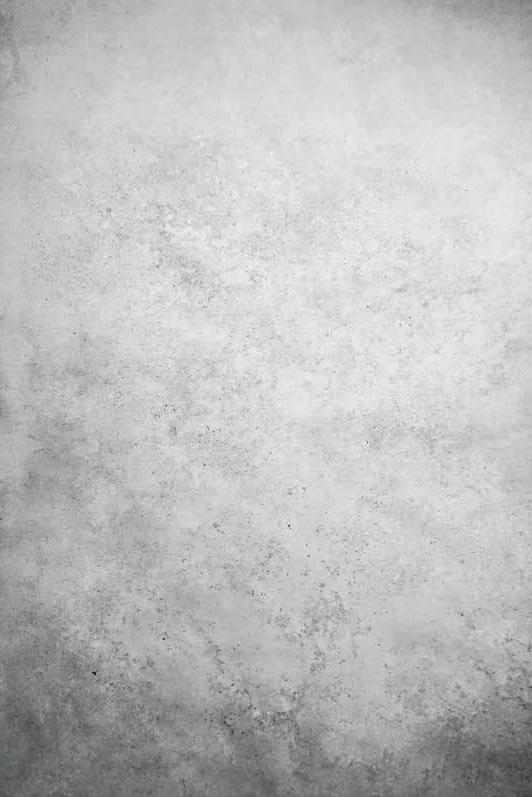
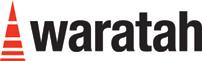