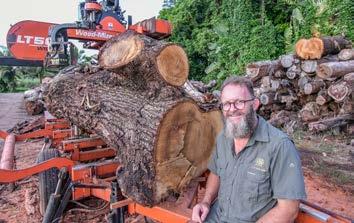
10 minute read
Mill profile
News Log salvage in the Whitsundays to serve new market
Amanda Buttram
IN the mainland hub of the world-famous Great Barrier Reef tourist destinations including the Whitsunday Islands and Whitehaven Beach, is Whitsunday Timber in Cannon Valley, Queensland, Australia.
Founded by Craig and Janelle Yeomans, the sawmill company seeks to help neighboring residents and businesses make use of the area’s valuable natural resources. With a Wood-Mizer portable sawmill, Whitsunday Timber mills salvaged logs into stunning wood slabs and dimensional timber that will serve new purposes in the community for generations.
Helping a friend cut down some trees initially led Craig’s wife, Janelle, to speculate that there must be an abundance of trees that needed to be removed. She recognized the potential value of processing this material, which led to the idea behind Whitsunday Timber. The business was started strictly as a side project, as Craig works another professional job during the week.
“I figured that if I could process three trees a week on my day off, we would make some money and I would enjoy getting outside,” said Craig.
According to Craig, starting the business was the easy part. He made partnerships with local tree services that supply free logs in exchange for removal from the site, which substantially reduces disposal costs for these businesses so everyone benefits. The purchase of a Mack rigid truck complete with a crane and the addition of a mounted rotating hydraulic grab and logging bolsters gave Craig the tools he needed to start picking up logs efficiently and bringing them to his facility for sawmilling. Currently, Whitsunday Timber operates out of a rented yard behind a local garden nursery, with 1,000 square meters of unpaved area and no sheds or cover on site.
While the Yeomans planned for Whitsunday Timber to be a small side business, work has quickly increased as their customer base has rapidly grown from word-of-mouth referrals along with a small social media presence. “I am processing several logs per week at present. Most of this is customer logs, which has been a profitable source of cash flow while I build my own inventory of timber,” said Craig. With about 70 tons of timber in the yard after a short time in the sawmill business, this side project has the potential to be a much bigger operation.
The work starts whenever a local tree service rings Craig to ask if he’d like the tree they’ve just cut. In most cases, the log must be removed from the prop-
erty on the same day, which means Craig is out picking up logs on his lunch break or after work at his day job. Upon returning to the yard, logs are stacked, sealed, and numbered. Whitsunday Timber operates a Wood-Mizer LT50WIDE hydraulic portable sawmill, chosen for its processing speed and computerized setworks to facilitate fast and efficient milling. “I have found the Accuset setworks invaluable. No other portable mill in Australia gives me convenient and simple calculation assistance. Once I get going, I don’t have to be constantly working things out. For a guy like me who tends to rush things or have multiple things on the go, it reduces the risk of mistakes,” said Craig. Before turning to a WoodMizer portable sawmill, Craig started with a chainsaw mill. He found it led to too much hard work, which wasn’t feasible in the hot and humid climate. “My experience with Wood-Mizer has been positive. The after sales service has been great and the equipment is fantastic. I have found the Australian distributor to be
warm and inclusive. There’s a family feel in the WoodMizer community,” shared Craig.
While his sawmilling equipment is portable, he rarely takes his sawmill to the customer as a log collection fee is less of an investment for the customer than a sawmill setup fee. When he’s ready to process, logs are moved to the sawmill using a wheeled loader. Details of each log are carefully recorded on a job card so that information is readily available when making marketing decisions and monitoring profitability. It’s not unusual for Craig to stop by the yard around 5:30 a.m. and mill a log or two prior to his workday and his days off from his full-time job are spent processing as much timber on the sawmill as possible. Once the timber is milled, material of all sizes is labeled, stacked, and strapped so the drying process can begin. Currently, Whitsunday Timber sells timber green, but there are plans to install a kiln in the future to provide more value for the customer.
Eucalyptus is the company’s main milling timber, which also includes blue
gum, Moreton Bay ash, and ironbark varieties. Mango trees are also milled quite frequently, as the trees grow large and become problematic in residential yards. Silky oak, Mackay cedar, white cedar, and pink cedar are also common woods milled by Whitsunday Timber, with kauri pine and hoop pine occasionally becoming available. “We will mill anything that has a good grain and an appeal for any purpose, from building to bespoke furniture,” said Craig. “[Mango trees] produce stunning furnituregrade timber.” "All of our timber is sustainably sourced from private customers who want us to mill their logs or from local tree services who have cut down a tree for one of their clients,” said Craig. Preorders make up the bulk of their sales, as milled stock is currently improving.
As the business has developed, Whitsunday Timber has carved out a desirable position in the community. Private customers and business clients are turning to Craig to process timber for personal and commercial use. “I have been surprised by the number of people who have a log lying around and are looking for someone to mill it,” said Craig. These one-off logs have become the business’s bread and butter. These private clients choose to salvage logs from their own property for environmental reasons, as well as to use the timber to create items that will be left to future generations.
Craig shares that half of the company’s clients are other businesses that use timber in their lines of work. “A local resort had to remove several trees for insurance reasons, and I am milling all of the trees and returning them as bearers and decking timber to replace the aging boardwalks around the property,” said Craig. In addition, some local builders hired Craig to mill logs to a certain size before they are sent off to another processor to be planed, creating vertical joints and other types of internal cladding timber.
Providing a needed community service has certainly paid off for Whitsunday Timber, as evidenced by the company’s rapid growth.
“It’s all happening faster than expected,” said Craig.
LOOKING BACK
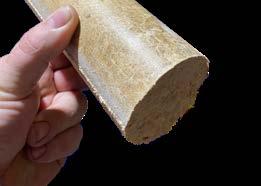
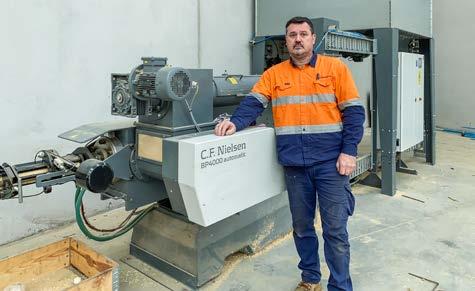
•Duncan Ratcliff beside his briquette maker.
Skilled and crafted in briquette manufacture
Keith Smiley
WHAT began as a love affair with furniture, morphed into a multi-level sawmilling and waste harvesting business, making Duncan Ratcliff’s cast-off timber and waste, his pride and joy.
The forty-nine-year-old Healesville owner of Amberwood brings to life, the new log, the old and discarded, the fire-laden, as he turns waste into usefulness. He began making furniture, and arts and crafts from recycled timber in 1995, showing his adeptness with the saw, and a lifelong passion with wood. Duncan then built a bandsaw, to cut urban recovery timber sourced from Melbourne’s suburbs. “We took whatever we could, some gum, and European oaks which had blown down or cut down to make way for housing extensions. We then bought a WoodMizer, did some custom sawing as well as our own sawing,” said Duncan.
Amberwood built a couple of crane trucks so they could send sawn timber to furniture makers. On the return journey, they’d pick up waste logs. Realising the need to dry their timber onsite, they built a dehumidifying kiln.
“The amount of log grew, so we bought an extra truck. Then we had Black Saturday, and a crew doing plantation pine salvage. We couldn’t saw everything we were harvesting. With mechanised harvesting you need to do hundreds of tonnes a day to make it work. The specialty stuff was still going through our own sawmill but the volume pine was going to export, or into other mills. We became the WoodMizer agent and the Knocker agent, bringing in forestry equipment from Finland.”
They were over committed and farmed out the WoodMizer equipment to a client, but when the GFC arrived, they had to fold up the entire harvesting business and liquidate it. In these ‘interesting times’ they found it cheaper to park all the equipment in the forest and go home, rather than cut down the trees. Duncan used his truck as a subcontractor to cart logs for other mills in the interim five years. “We supported small mills, servicing, repairing, and general maintenance with the WoodMizer agent. But a growing problem, is what do you do with your sawdust: the more you produce that isn’t square, the less margin you have. We began looking at pelletising and recycling options for wood fibre, and we ended up taking over two agencies, POR Micucci System of Italy and C. F. Nielsen of Denmark.
These systems can turn a variety of wood-based waste, into additional profits through briquetting solutions. The mechanical briquetting machines are in demand as green recycling ramps up to another level, providing another revenue stream for Duncan as he sells and services these systems.
“You can briquette anything organic from plastic to wood. No more splitting and no spiders. Since Covid has eased, you can go out and see people, as business slowly comes back to life. The timber industry is taking a deep breath, to see what to do with their waste. With fuel and waste increases, it’s a good time to turn your excess sawdust into a product that’s saleable. If you’re a fibre sawmill and you can make a fuel briquette, or a manufacturer of fibre board, we can help dispose the waste.”
“We will stick to our knitting; the market is only going to increase. You still have to pay for green. We’ve got a solution for everybody but not all can afford it. We’ll add more machines, as the end users want more of the briquettes, as they realise a recovery. You’re not burning wood to dry other bits of wood in your combustion stoves, that’s one of our plusses. “
Duncan lives and breathes timber waste while the timber industry asks for more, as costs skyrocket. He believes he should support timber producers, using his collective experience of over 15 years. While his workshop remains chockfull of furniture making equipment, Duncan’s positive self looks to the future in briquetting. “There are way too many holes to fill in, and if you took it to heart, you’d fold up. He is justified in being resilient, given the ups and downs of the industry. “Working for yourself, you’re responsible for everything.” 2019
THE timber industry bears the brunt of the pain in a massive expansion of parks and reserves in Victoria’s Central West under a Victorian Government report.
The final report of the Victorian Environment Assessment Council, released late on Friday, said the biggest impact on the regional economy was to the reduction in timber milling and commercial firewood production.
“There will be minimal regional impacts related to potentially displaced recreational uses,” the report said. The report emphasised the importance of nature conservation, recreation and tourism in the Central West investigation area of 403,815 hectares, of which 161, 215 ha, or 40 per cent, is public land. 2016
HVP PLANTATIONS (HVP) has adopted FOLS as its required standard for the recording of training and skills verification for high risk forestry activities.
FOLS is a national industry-led program, managed by ForestWorks, and supports the professionalism and safety of industry through an online system of recording and verifying the currency of operator skills. 2011
A NEW 1800 LOGHAUL number designed to drive improvements in log truck driver safety and behavior has been launched in NSW. The 1800 LOGHAUL number - 1800 5644285 – was developed jointly by Forests NSW and the Forest Industry Council.
Each log truck operated by contractors to Forests NSW will have a sign bearing the 1800 telephone number as well as an individual truck identification number.