
5 minute read
Offsite progression and the shift towards modular technology
from Health Business 20.3
by PSI Media
The government and the wider public sector are the biggest clients DfMA facilitates early design detail and threeof the construction industry. Here, the Modular Portable Building Association discuss the growth and benefits of off-site construction
The government and the wider public sector are the biggest clients of the construction industry, they have an important role in encouraging and facilitating the uptake of offsite technology. Historically, manufacturing operations have been considered extensions to construction processes instead of an integral and important part. This perception is changing as offsite has become an increasingly dominant force that utilises high levels of technology, the lines between manufacturing, engineering and construction have become blurred, creating a need for new skills and redefining existing ones. The more the offsite industry digitalises, the more the industry uses technology in end-to-end processes, attracting a new cohort of skilled operatives and technicians.
Offsite technology offers benefits that have had a huge positive impact on the construction industry, bringing longstanding traditional practices up to date. The first key shift away from traditional methods is that build processes take place in controlled factory conditions – requiring a change of mind-set and approach.

Advanced offsite systems and digital technology: DfMA and BIM
At the core of offsite manufacture, design for manufacture and assembly (DfMA) protocols and building information modelling (BIM) enable optimal configuration of offsite solutions onsite by engaging with multi-discipline and multi-tier suppliers from the beginning of the design development process.
DfMA facilitates early design detail and three-dimensional design information, while BIM minimises the risk of errors by eliminating the time-consuming process of translating engineers’ information into cutting lists and assembly drawings. BIM also facilitates the optimising and testing of designs in virtual and pre-production environments.
Technology is ever-evolving, and the offsite industry is now exploring integrating BIM and digital design specifications with Enterprise Resource Planning (ERP) and Material Requirement Planning (MRP) using ‘intelligent graphics’. This technology will permit manufacturing simulation and visualisation, clash detection and virtual onsite assembly modelling/programming, which can be enhanced using augmented and virtual reality digital developments. Digital technology is as
Offsite technology offers benefits that have configuration of offsite solutions and virtual onsite assembly modelling/ had a huge positive impact on the construction onsite by engaging with multi-discipline programming, which can be enhanced industry, bringing longstanding traditional and multi-tier suppliers from the beginning using augmented and virtual reality digital practices up to date. The first key shift away of the design development process. developments. Digital technology is as relevant to offsite manufacturing processes as it is to offsite design and architecture.
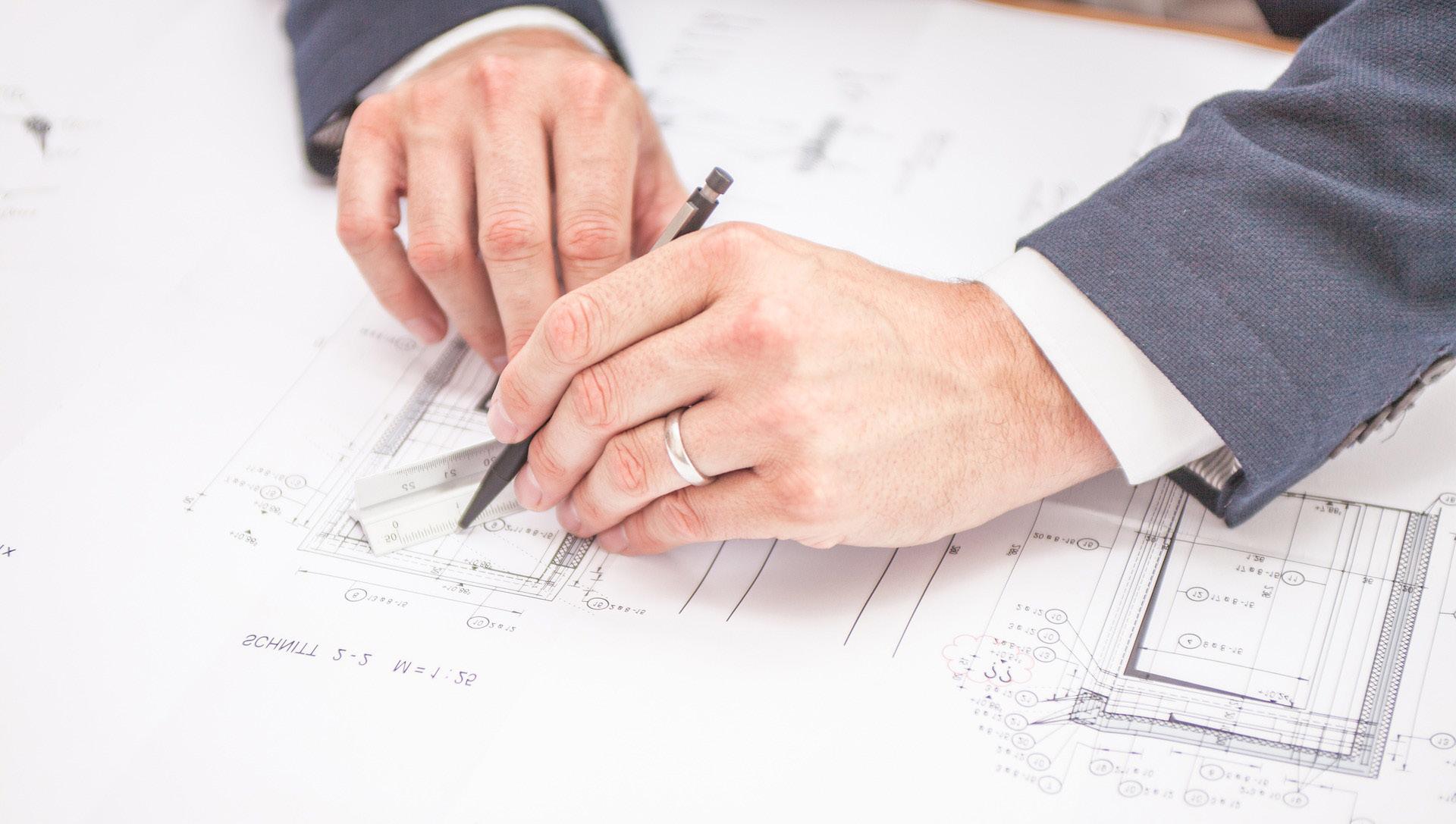
The optimum technology: modular construction
Offsite manufacture encompasses a variety of panelised and volumetric modular methods of construction. At the forefront of offsite techniques, modular building has had a remarkable impact on reducing costs while increasing quality and safety measures. Having gained considerable momentum over the past few years, modular construction makes up 60-70 per cent of offsite manufacture and reduces build times by an impressive 50-60 per cent.
Module selection is influenced by transportation dimensions and shipping distances. A number of other factors are also holistically considered to achieve optimal design efficiency: module connection details and quantities, installation and crane costing rates, specific site logistics, foundation/ transfer deck, volumes of required materials and other service core requirements.
The demand for customisation has led the manufacturing industry to develop methods for adaptation during mass production while meeting individual customer needs. These methods identify design parameters that can be integrated into architectural CAD applications using Revit structures.
Design parameters include: customer view that controls the modular design according to requirements; engineering view that constrains the module design according to deflection, strength, wind loads, fire, acoustic and building regulations; production view that identifies product dimensions and transportation constraints according to factory regulations and capacity; and site view for assembly constraints on site according to site layout/plans.

Benefits of modular and volumetric technology
Modular and volumetric practices augment the construction industry with a multitude of benefits that span from greener, healthier environments to maximised sustainability, heavily reduced costs and quick build times.
Volumetric technology allows providers to customise any modular building to meet exacting needs and blend in with surroundings. Each individual material can be selected specifically for its performance characteristics, tailoring every inch of a modular build. Eco-friendly materials are often specified, and waste is recycled for future projects wherever possible. Not only this, but components are also available in a range of sizes for expansions whenever necessary.
As units are factory manufactured, stringent quality control processes can be undertaken within these well-managed environments. These in-house conditions also prevent weather from inhibiting the manufacturing process, guaranteeing efficiency. On top of this, modular construction enables site work and building processes to be completed simultaneously, reducing labour costs and build times. Transportation rarely poses issues, as preconstructed, self-contained units can be transported to virtually any location, ideal when new premises need to be constructed within limited timeframes. As modules are designed to withstand long-distance transportation and craning onto foundations, they are structurally stronger than most traditionally constructed building materials.
About MPBA
As the single recognised voice for promoting and marketing members’ products and services, the MPBA plays a key role in the connecting of sectors in the modular and portable building industry. The association collaborates with specialist technical advisors to enhance innovation in the design and manufacture of modular buildings. These can be designed and manufactured from timber, steel or concrete, in any size and shape to meet individual client needs while ensuring full compliance with building regulations.
With the MPBA’s assistance, offsite construction companies remain ever competitive in the modular and portable building multi-billion-pound industry. The association is represented on committees for BSI, LPCB-Expert Group D and works with BRE, LABC, CLG, NHS, Cskills-CITB, NHS, LHC, CCS and Carbon Trust to represent the industry. L
FURTHER INFORMATION:
mpba.biz