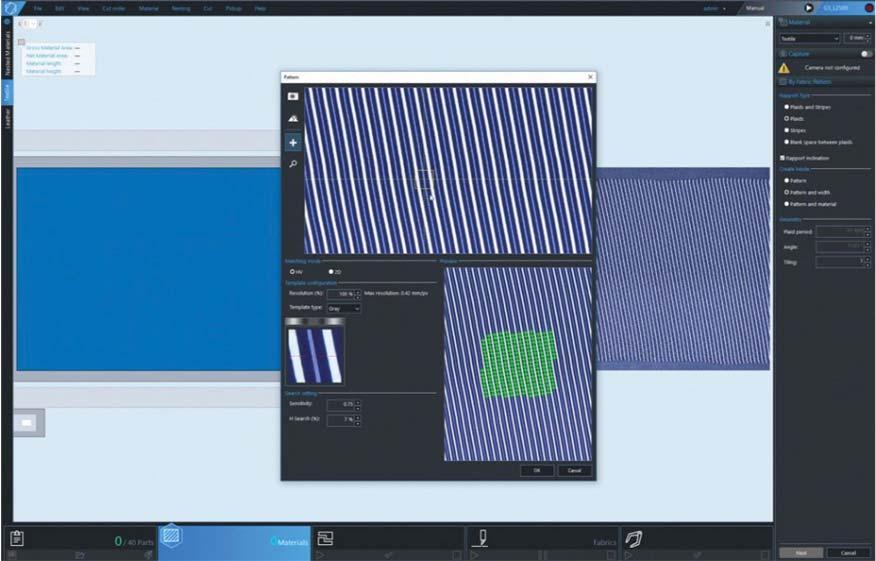
2 minute read
Zünd: – Mind software: New Features
Zünd Systemtechnik has added new features to the Mind software suite that are making Zünd digital cutting workflows for leather and textile applications easier, more efficient, and more profitable than ever.
This is the most significant and comprehensive software update since Zünd first introduced the Mind workflow suite five years ago, and the developers have added a host of new features. First and foremost is the improved UI, which is now even more intuitive, enables deeper integration with MIS data and production workflows and with additional tools specific to textile processing. It also opens up new possibilities in the exchange of data with third-party suppliers.
Advertisement
With Version 5.3, MindGest now supports scan-to-stock and scan-to-order workflows. The latter is an offline process that allows for digitizing hides and nesting parts away from the cutter through a capturing system like MindCut. In the Scan-to-Stock workflow, hides are digitized and then temporarily “stocked” until production can proceed. These workflows are in contrast to the inline process, in which hides are captured/digitized and parts are nested directly on the Zünd cutting system.
For print & cut textile applications, the system now also supports register marks created in Zünd Cut Center – ZCC. Furthermore, MindCut is now also compatible with PrimeCenter and RIP software from other manufacturers through multi-layer PDFs. Improvements were made to the way the system controls the Zünd ICC camera used to capture the exact position of printed parts on the cutter, allowing for perfectly matching cut to print. In Version 5.3, MindCut now also fully supports the cradle feeder 100 with integrated cut-off function, Leibinger Jet3, the laser module LM 100W, and the V-Cut Tool - VCT2.
With adjustments made to the stepby-step guidance through the nesting process, the nesting portion of the UI in MindGest has been improved as well. Users now have the option to graphically display relevant production data and are able to see anticipated nesting times at a glance. Pattern matching has also been improved with better guidance throughout the process. The system now displays the pattern in a separate window allowing the user to verify the settings before proceeding.
Furthermore, the labels for marking digitized hides can now be individually designed and the interface for nested jobs has been optimized as well. The Model Importer, too, has been enhanced with additional functionalities, e.g. with the option to automatically create seam allowances.
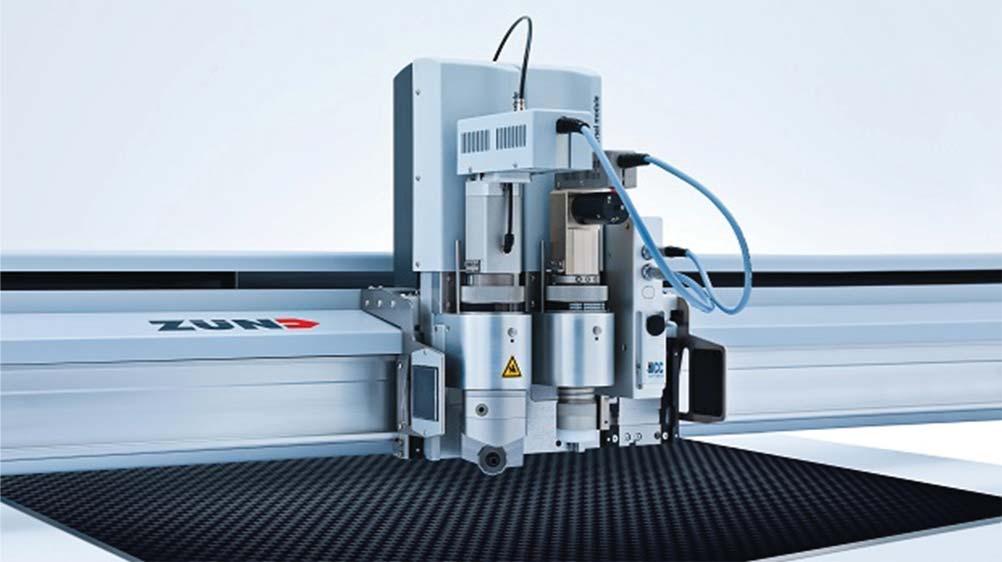