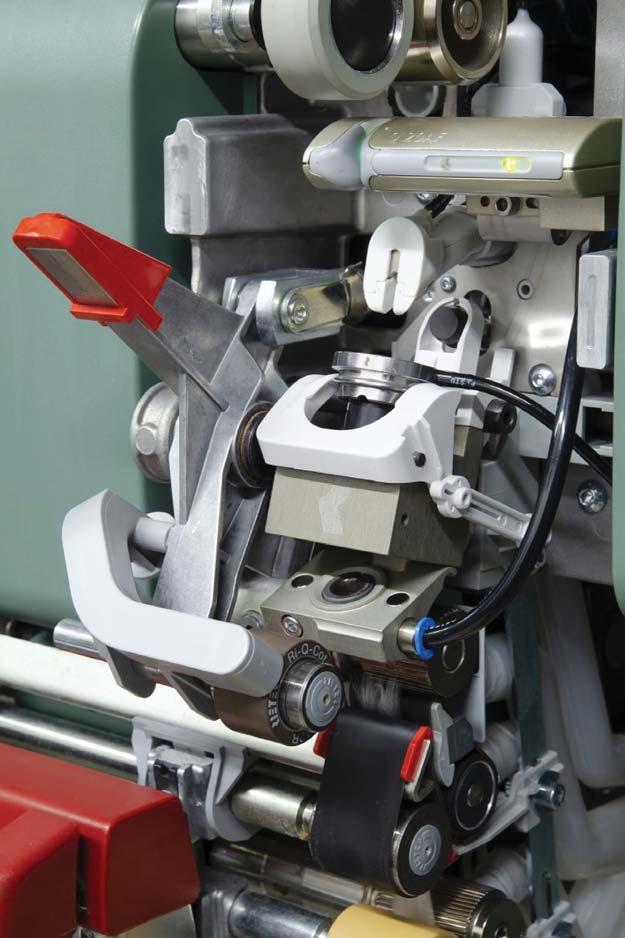
5 minute read
Unique Solutions for Processing Viscose with Air-Jet Spinning
Fiber consumption is on the rise, and man-made fibers play an important role in this. The consumption of cellulose fibers is growing the fastest and, due to their attractive properties, they are appreciated by spinning mills, downstream processing, and end users. The air-jet spinning machine J 26 offers new solutions for processing viscose with high productivity and quality.
Advertisement
As population growth and prosperity increases, so does the consumption of fibers across the globe. While this holds true for all staple fibers, the use of man-made fibers such as cellulosic staple fibers and synthetic staple fibers is growing particularly quickly. The consumption of cellulosic staple fibers is expected to double to 10 million tons by 2030 while the consumption of synthetic staple fibers is expected to grow by 48% to 28 million tons compared to 2015 (Fig. 1). Rieter addresses these market needs and continuously develops special technology components and solutions for man-made fibers and blends for all end spinning processes.
Air-jet spinning strong in viscose
Air-jet spinning is the dominant choice for processing cellulosic fibers – mainly viscose – and their blends with cotton. The high productivity and the low yarn conversion costs of viscose make it an attractive raw material for spinning mills.
Easy cleaning thanks to the option of opening the spinning nozzle housing.
Along with its special properties, like less fluff and fly in knitting and weaving, it is also popular in downstream industries. End users particularly appreciate the excellent pilling resistance and wash resistance of the finished products.
J 26 with new features
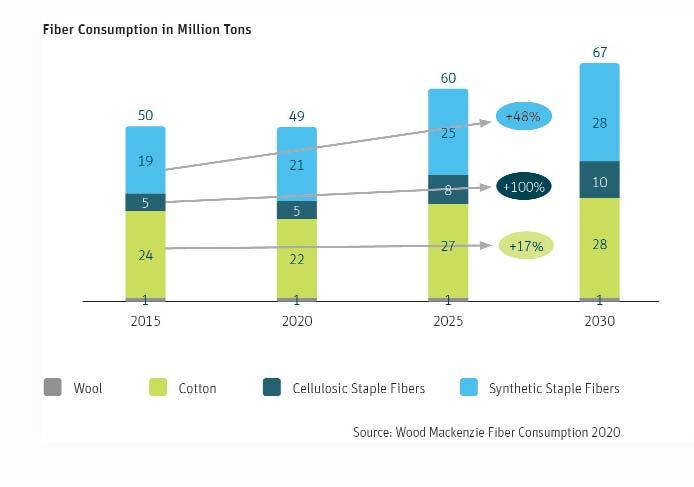
The air-jet spinning machine J 26 offers several unique features for processing viscose. The new spinning nozzle housing “Z+1 High Speed” with a reshaped fiber feeding element ensures high yarn tenacity and production speed at the same time. The delivery speed can be increased to 480m/min for 100% viscose Ne 30 without a loss in yarn quality. With 19 cN/tex, the yarn strength is the same as with the existing “Z-1” housing with a
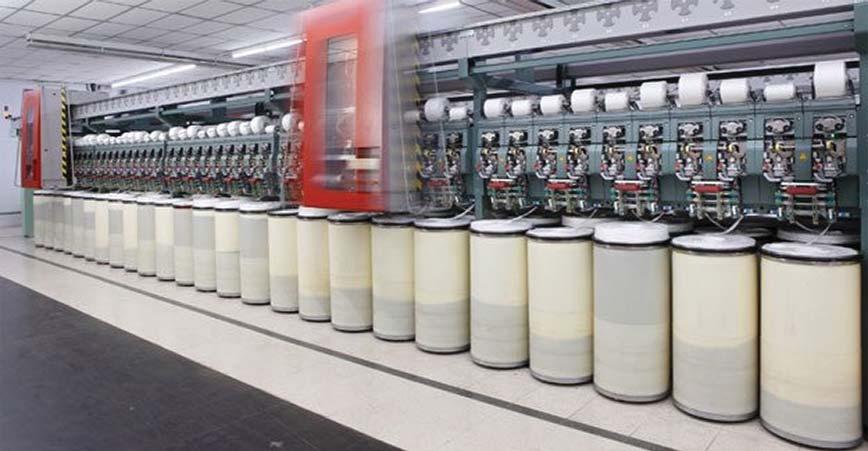
17% lower delivery speed of 400 m/min (Fig. 2). This reduces the yarn conversion costs because the air pressure for twisting remains the same at a higher production speed. The J 26 is also well suited for processing blends with polyester: cotton with a proportion of up to 50% polyester and viscose with a proportion of up to 80% polyester.
Simplified handling and easy operation
In addition to increased productivity, the operation has been simplified thanks to the option of opening the housing of the spinning nozzle. This means the nozzle and the housing can be cleaned easily and effectively without having to remove the ceramic spinning tip (Fig. 3). This results in fewer red lights and a reduced workload for operators. Spinning mills report a 50% reduction in operating time per event and red lights that are active for only 5 to 11 seconds compared to 25 to 45 seconds with a closed spinning nozzle housing.
Rieter Trade Press Article: Processing Viscose with Air-Jet Spinning, December 2021
Best package quality for downstream processes
The J 26 offers pneumatic package damping for uniform package quality and efficient unwinding for downstream processes. Packages containing manmade fibers, especially viscose, tend to be very hard with even harder edges. This results in an unwinding that is unstable and brings about yarn breaks. To prevent the yarn from breaking, the density is kept consistent over the complete package build-up. The unique stroke respiration softens the edges ‒ which is the secret for best unwinding performance. The optimized winding enables a 20% higher package weight with man-made fibers at the same diameter. This results in higher machine efficiency thanks to 20% fewer doffings. Weaving and knitting machines also benefit from less handling and less stops.
High yarn tenacity and production speed in air-jet spinning thanks to the new spinning nozzle housing “Z+1 HS”.
About Rieter
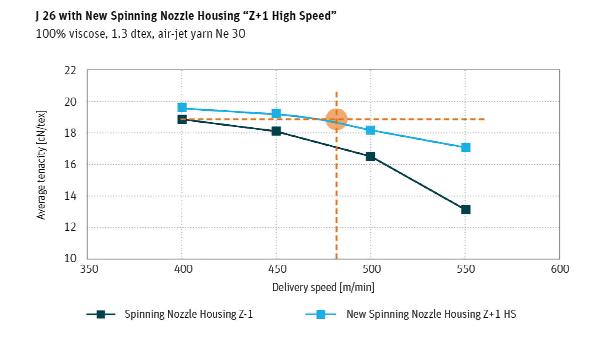
Rieter is the world’s leading supplier of systems for short-staple fiber spinning. Based in Winterthur (Switzerland), the company develops and manufactures machinery, systems and components used to convert natural and man-made fibers and their blends into yarns. Rieter is the only supplier worldwide to cover both spinning preparation processes and all four end-spinning processes currently established on the market. Furthermore, Rieter is a leader in the field of precision winding machines. With 15 manufacturing locations in 10 countries, the company employs a global workforce of some 4 400, about 20% of whom are based in Switzerland. Rieter is listed on the SIX Swiss Exchange under ticker symbol RIEN.
Health Safety & Environment newsletter automatic fire suppression system
Introduction:
Enormous changes took place across the industries globally due to COVID-19. HSE procedures focused on health and at workplace also revised. Fire safety is one of the major addressable jobs for industries, commercial and residential areas. Fires are avoidable if we improve the standard of prevention through right practices.
Types of Fire:
There are 6 types of fire, classified and identified by the kind of materials found in the location where the fire exists.
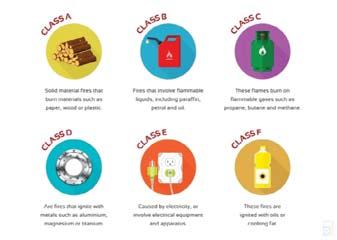
Types of Fire Extinguisher:
Fire extinguisher is a crucial element of comprehensive fire safety in industries and working areas. It is also required by local and international legal health and safety regulations.
Electrical Fire:
When electrical load increases, short circuit arises or electrical component malfunctions that leads to electrical fire. Fire causes loss of human and asset. This Fire needs extraordinary and immediate extinguishing action without any delay.
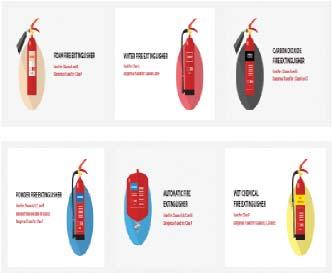
Introducing Automatic Fire Suppression System:
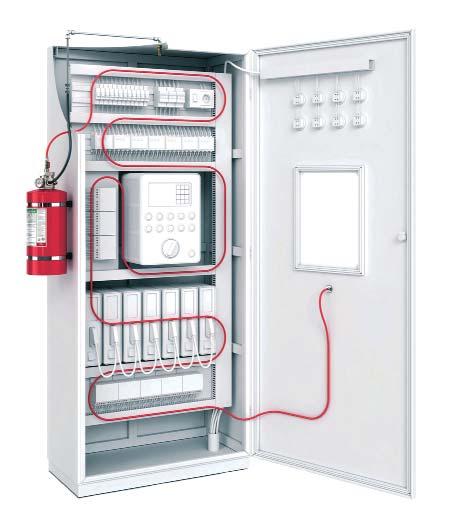
Electrical equipment fire suppression systems have been specifically designed to protect the equipment and put off electrical fires caused by electricity leakage (class E fire) quickly and efficiently without any personal interaction automatically.
Upon flame or heat exposure, the pressure detecting tube bursts and activates the cylinder valve to open and sprinkles the extinguishing agent within 15-30 seconds (FM 200, UL listed clean agent) to protect spreading of fire even inside of Electrical Distribution Panel which is most commonly a hidden area. These self-bearing pneumatic systems require no external energy or power supply.
This System is specifically designed for fire suppression in Electrical Panels, Battery Bay, Control Panels, Data Centers, Electric Equipment, HT & LT Panels, and Transformer Rooms etc. The System prevents damage of equipment, records, people and other assets that are vital for a business.
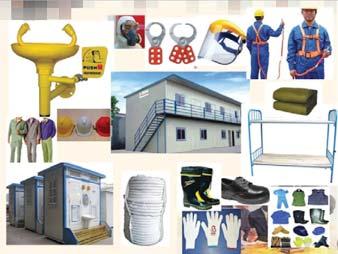
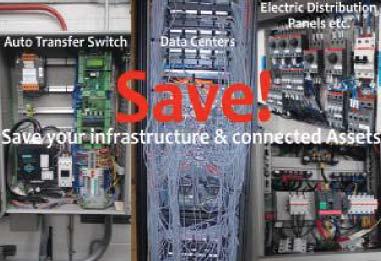
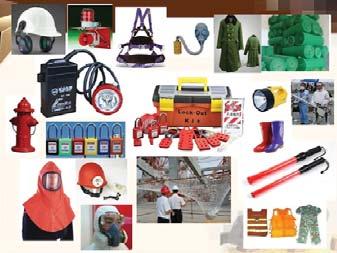
