
103 minute read
AROUND THE WORLD
AUSTRALIA
Cotton spices expected to rise in short-term
Advertisement
The gross value of cotton production is forecast to increase by 157 per cent to $4.3 billion by the end of the 2022 fiscal year. This rise is on the back of a sharp increase in production volumes and strong international prices.
And cotton export values are predicted to increase by a staggering 404pc to $3.4 billion in 2021-22 and a further $4.1 billion in 2022-23 with favourable production conditions to continue and large crops. This is according to the latest Outlook report from Australian Bureau of Agriculture and Resource Economics and Sciences (ABARES).
The national forecaster also predicted total cotton production around the world to increase by 8.1pc tp 27 million tonnes of 600,000 bales.
Favourable conditions across most of Australia's cotton growing regions mean production estimates sit at 5.2 million bales, almost 10 times larger than the drought impacted 2019-20 crop of 590,000 bales. International prices are expected to surge with the Cotlook 'A' index forecast to average US116 cents per pound in 2021-2022, up by 35pc compared to the previous year.
The surge is expected to stem from a combination of strong demand for cotton coupled with global supply chain disruptions causing cotton mills to seek additional buffer stocks, driving international prices.
According to the national forecaster, disruptions to international freight have proven to be a significant barrier to trade with the world's largest exporter, the US, struggling to get its recent 2021-22 cotton crops to major import markets.
But although demand for cotton is expected to grow, an easing of supply chain bottlenecks will result in lower international cotton prices in 2022-23 averaging US98c/pound.
BANGLADESH
Bangladesh garment workers' rights 'violated'
Garment workers in Bangladesh are suffering from violations of workers’ rights because of a lack of government action, according to a new report from the International Trade Union Confederation (ITUC).
They suffer discrimination and harassment, non-payment of wages and benefits, being forced to work unpaid overtime, and being denied freedom of association, according to ITUC, the world's largest trade union federation. The report, released ahead of the Bangladeshi government’s latest progress report to the International Labour Organization (ILO) recently, also focuses on the country's leather and shipbreaking sectors.
BGMEA stresses Bangladesh-India cooperation in apparel, textile industries
Bangladesh Garment Manufacturers and Exporters Association (BGMEA) President Faruque Hassan has said Bangladesh and India have enormous scope to complement each other for the development of apparel and textile industries of both neighboring countries.
He stressed the need for more collaboration and cooperation between the two neighboring countries involving business communities and trade associations to explore avenues towards deriving two-way trade benefits.
The BGMEA president made the observation at a meeting with Sri Narain Aggarwal, former Chairman of the Synthetic and Rayon Textiles Export Promotion Council (SRTEPC), at BGMEA's PR office in Dhaka. BGMEA Vice Presidents Shahidullah Azim and Miran Ali were also present at the meeting.
They discussed possible areas of collaboration between BGMEA and SRTEPC to identify mutual business opportunities and work to make the best use of them. They also talked about how
both associations could work together to create a bridge between apparel and textile businessmen of Bangladesh and India to facilitate meaningful business interactions.
CHINA
Chinese textile industry recorded double-digit growth in 2021
The textile industry of China witnessed a strong expansion in 2021 as its revenue and profits recorded a doubledigit growth, according to the Ministry of Industry and Information Technology (MIIT).
Textile firms with annual operating revenue of 20 million yuan (US$ 3.16 million) and above recorded profits of 267.7 billion yuan in 2021, up 25.4 per cent year on year (YoY).
The total operating revenue of the firms increased by 12.3 per cent YoY to reach 5.17 trillion yuan in 2021, as per official data.
Additionally, China’s garment exports grew 8.4 per cent YoY to reach a record high of US$ 315.5 billion in 2021.
CAMBODIA
New deal to promote Cambodian garment sector
The Garment Manufacturers Association in Cambodia (GMAC) has signed a memorandum of understanding (MoU) with the European Chamber of Commerce in Cambodia (EuroCham Cambodia) which aims to increase sustainability in the country's garment industry.
One of the first moves under the agreement will be for EuroCham to set up a public training programme on sustainable textile sourcing, worker health and safety, and compliance through the Cambodian Garment Training Institute (CGTI). This programme will be supported by the German development agency GIZ under its FABRIC project to promote sustainability and social responsibility in the Asian textile and garment industry.
INDIA
India achieves highest-ever export target of US$ 400 billion ahead of schedule
India has successfully achieved the export target of US$ 400 billion for fiscal 2022 (FY22) nine days ahead of schedule, up 37 per cent year-over-year from US$ 292 billion in fiscal 202021.India’s merchandise exports between April 2021 and Feb 2022 were worth US$ 374.05 billion, an increase of 45.80 per cent over US$ 256.55 billion in April 2020-Feb 2021 and a rise of 28.16 per cent over US$ 291.87 billion in April 2019-Feb 2020.
Additionally, India exported cotton textile products such as made-ups, yarns and fabrics worth US$13.95 billion between April 2021 and February 2022, surpassing the target of US$12.50 billion, as per official data.
“India set an ambitious target of US$400 billion of goods exports and achieves this target for the first time ever. I congratulate our farmers, weavers, MSMEs, manufacturers, exporters for this
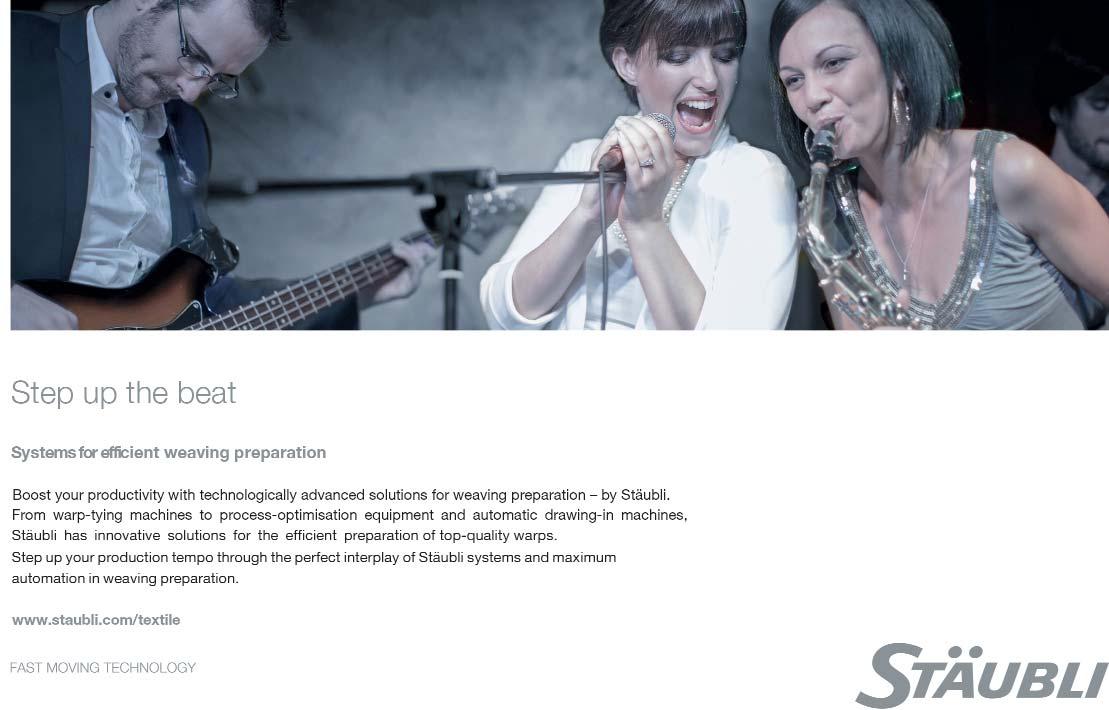
success. This is a key milestone in our Aatmanirbhar Bharat journey. #LocalGoesGlobal,” said Prime Minister Narendra Modi in a tweet today.
“We have scaled the US$400 billion goods exports mountain. Every hour, day & month leading to this monumental achievement has been exhilarating. Now, there are higher peaks to scale. #LocalGoesGlobal,” tweeted Piyush Goyal, minister of commerce and industry, consumer affairs and food and public distribution and textiles.
India’s merchandise exports in February 2022 were worth US$33.81 billion, an increase of 22.36 per cent over US$27.63 billion in February last year and a rise of 21.88 per cent over US$27.74 billion in February 2020. Merchandise imports in February 2022 were worth US$55.01 billion, rising by 34.99 per cent and 45.12 per cent over US$40.75 billion in February 2021 and US$37.90 billion in February 2020 respectively.
As per data shared by PM Modi in his tweet, India exported goods worth $33 billion every month and close to $1 billion every day
SRI LANKA
Sri Lanka’s apparel exports set 5-year record
Sri Lanka’s apparel exports in January 2022 were at their highest level for that month in the last five years. The performance demonstrates the industry’s underlying strength as it bounced back from the sustained shocks from the impact of the pandemic over the last two years, says The Joint Apparel Association Forum (JAAF).
Sri Lanka’s apparel export earnings rose to US$ 487.6 million in January 2022, overtaking the US$ 452 million recorded in January 2019, prior to the pandemic, by 8%. Growth over January 2021 export earnings was 23%.
“Amidst significant turbulence, this strong performance is testimony to the resilience of Sri Lanka’s apparel industry and augurs well for the industry’s progress towards realising its goals for 2025,” said Yohan Lawrence, Secretary General, JAAF, the apex body of the Sri Lankan apparel industry.
The industry’s 2030 vision is to transform Sri Lanka to a global apparel hub by that year and an intermediate goal is to increase annual export earnings from apparel to US$8 billion by 2025.
“Through close cooperation between all key stakeholders, the apparel industry can further increase its already-strong contribution to the national economy, as a major generator of vital foreign exchange and high-quality employment,” Lawrence added.
The industry’s January 2022 performance also reflects the success of rigorously applied safety measures adopted by the sector, in close cooperation with health authorities, to minimise the spread of the pandemic among employees to zero.
Additionally, apace with the national vaccination drive, 65% of employees in Sri Lanka’s apparel sector have now received both doses and the booster, while 95% of employees have received at least both doses. Apparel exporters also proactively adopted additional safety measures, even before the Omicron variant came to Sri Lanka.
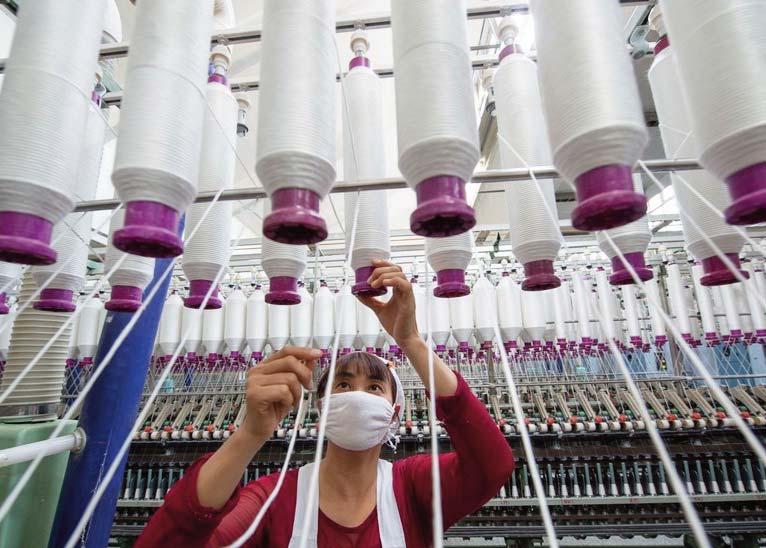
UNITED KINGDOM
UK plans to share EPR textiles scheme options in 2022
The UK government is conducting ongoing research to develop options for a textiles policy framework that includes EPR and it is said to be committed to engaging stakeholders on these options by the end of this year.
The UK Government’s Resources & Waste Strategy for England report identified textiles as being one of five priority sectors for a potential EPR scheme alongside chemicals, construction, food and metals. The report defines the textiles sector as including at least all clothing, as well as other household and commercial textiles such as bed linens.
A UK EPR scheme specifically for textiles would mean producers of apparel and textiles would contribute to the costs of recycling and this would be supported by measures to encourage better design and labelling. The scheme would also aim to boost the reuse and recycling of apparel and textiles and reduce the environmental footprint of the sector.
The Government’s draft Waste Prevention Programme for England that was published for consultation in March 2021 is also said to affirm its commitment to an EPR scheme and sets out its consultation approach.
The Government is already showing its commitment towards reducing waste within the fashion sector by starting engagement with stakeholders on the Textiles 2030 initiative.
USA
US drought pushes cotton prices to tenyear high
Cotton prices rose to their highest level in more than a decade due to a prolonged drought in parts of the central United States. The plant fiber reached US$1.3171 per pound (about 453 grams) on the key US futures contract, the highest since July 2011.
Rainfall has been exceptionally low since early January in the northwest part of Texas -- which produces about 40 percent of all US cotton production.
Depending on the region in the United States, cotton is planted from March to June, so there is uncertainty in the market about size of this year's crop, according to John Robinson, a professor at Texas A&M University and cotton specialist.
VIETNAM
Middle East market remains promising for Vietnamese exporters
With a population of 400 million, the Middle East is emerging as a promising market for Vietnamese exporters, a news agency quoted experts as saying.
According to VNA, the Middle East - thanks to the rising oil prices - is enjoying high growth. Among 16 regional countries, Vietnam has mostly traded with six member nations of the Gulf Cooperation Council (GCC), namely the UAE, Saudi, Kuwait, Bahrain, Qatar and Oman.
Trade between Vietnam and the GCC countries has surged from US$2.7 billion in 2012 to US$12.5 billion in 2021.
So far, Vietnam has signed economic, trade and scientific-technological cooperation agreements with five GCC countries, trade deals with two nations, double-tax avoidance agreements with five countries and investment protection deals with four countries. Vietnamese products are suitable to the demands of the GCC countries.
Nguyen Tuan, Deputy Director of the Investment and Trade Promotion Centre of Ho Chi Minh City (ITPC), said that Middle East countries have high demand for wooden furniture, plastics, grains, garments, footwear, rubber products, meat, milk and vegetables, which are strong products of Vietnam.
Ground-breaking ceremony for the Sparda-Bank Tower and Messeplatz entrance
Today's ground-breaking ceremony marks the beginning of work on a new architectural highlight for Frankfurt’s Europaviertel district. A new office and hotel high-rise with 35 storeys above ground and a building height of 124 metres is being built in conjunction with the new Messeplatz entrance to the exhibition grounds. The future users of the building have already been largely determined. Sparda-Bank Hessen, which will also own the high-rise, will locate its headquarters here. Messe Frankfurt will remain the owner and operator of the new Messeplatz entrance, which will be accessed through a shared forecourt. In future, the ATLANTIC Hotel Group will offer its guests outstanding service and a high quality of stay at a superior four-star facility with a sky bar, restaurant and sports facilities occupying 19 storeys of the high-rise building.
City Councillor Stephanie Wüst, Head of the Department for Economics, Law and Reforms of the City of Frankfurt am Main: “The architecture on the Messe Frankfurt grounds and in the immediate vicinity of the Europaviertel is characterised by iconographic buildings that are notable for their individual design. The new high-rise building at Messeplatz will fit in perfectly with its striking contribution to Frankfurt’s skyline, which is unique in Europe.”
Markus Müller, Chairman of the Board of Sparda-Bank Hessen eG: “We are very pleased that work has now begun on the construction of the new headquarters of Sparda-Bank Hessen. The Sparda-Bank Tower will not only set an architectural example but will also be a symbol of a strong cooperative that is already entering its 120th year this year. At the same time, we are creating modern office workplaces for our employees and investing in the promising Frankfurt real estate market.”
Uwe Behm, Member of the Executive Board of Messe Frankfurt GmbH, explained the significance of this project: For Messe Frankfurt, the design of the new Messeplatz entrance – which will remain our property – further strengthens our globally unique city-centre location by ensuring that our customers and guests can access the exhibition grounds from every direction quickly and easily. With the construction of a new underground line in the Europaviertel, our public transport connections will include two underground lines and four S-Bahn light rail lines in future, as well as trams and buses.”
The office and hotel high-rise project is being developed by the Gustav Zech Foundation. Wolfrat Voigt, President of the Gustav Zech Foundation, highlighted some of the benefits: “We are delighted that work on this magnificent building ensemble is now getting underway. I firmly believe that its outstanding architecture will make a valuable contribution to urban development and offer its users an excellent environment in which to work, live and relax.”
The building will be erected on site 42a on Europa-Allee, directly west of the Emser Bridge. The Sparda-Bank Tower and the Messeplatz entrance will be built according to an updated version of the competitionwinning design submitted by cyrus I moser I architekten (cma) and are scheduled for completion by 2025.
Both buildings will frame the new Messeplatz square being created on the site, which will serve as an entrance for various uses and comprise an open urban space on Europa-Allee.
As part of a general contractor agreement, Gustav Zech Stiftung Management GmbH is responsible for building the Messeplatz entrance.
Sparda-Bank Tower hotel and office high-rise
The project development for the high-rise building provides for the development of a hotel for the ATLANTIC Hotel Group with 373 hotel rooms over 19 storeys and approx. 13,400 square metres of office space on 14 storeys on the western part of the site. Approximately 200 car parking spaces will be created on four basement levels.

Markus Müller, Chairman of the Board of SpardaBank Hessen eG:
Messeplatz entrance
The new Messeplatz entrance is being built on the eastern part of the project site. This will create a new four-storey entrance to the exhibition grounds from the south that is located right at the future underground station for the U5 extension to the Europaviertel, which is currently under construction. Via Mobile the covered and glazed transport system with moving walkways and escalators on the Frankfurt exhibition grounds – will connect the new South entrance with Hall 12, which opened in 2018, and therefore also with all the other halls at Messe Frankfurt. The planned building of just under 5,000 square metres includes a spacious reception hall with access control systems, event and conference rooms, and catering facilities.
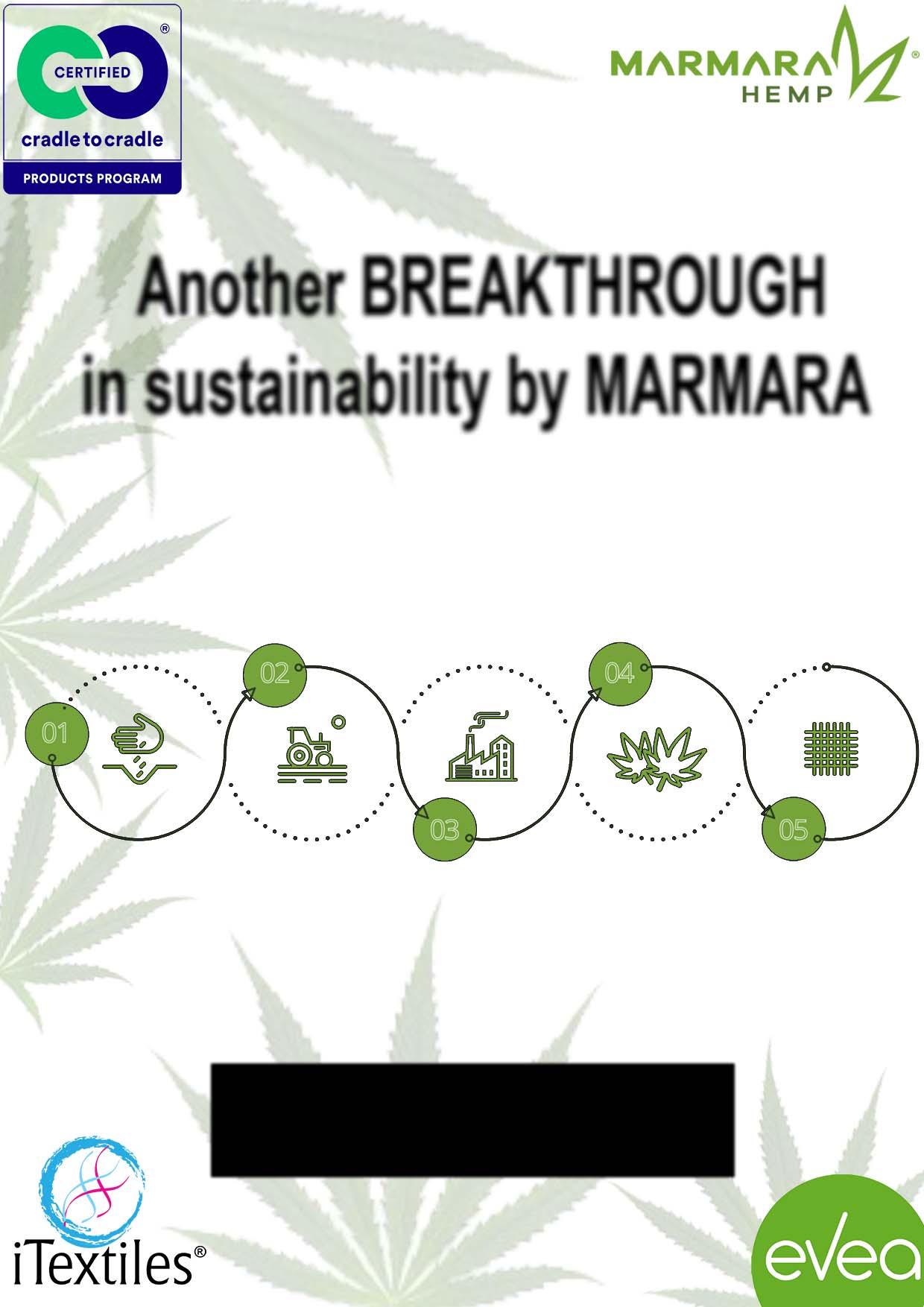
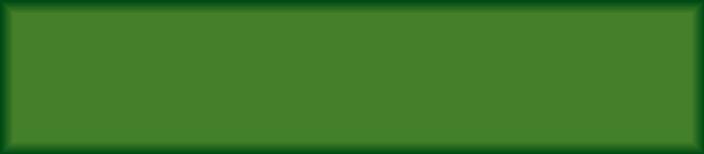
Sicomin supports advanced fiberglass industries in large scale adaptable mould composite project for the Museum of the Future interior
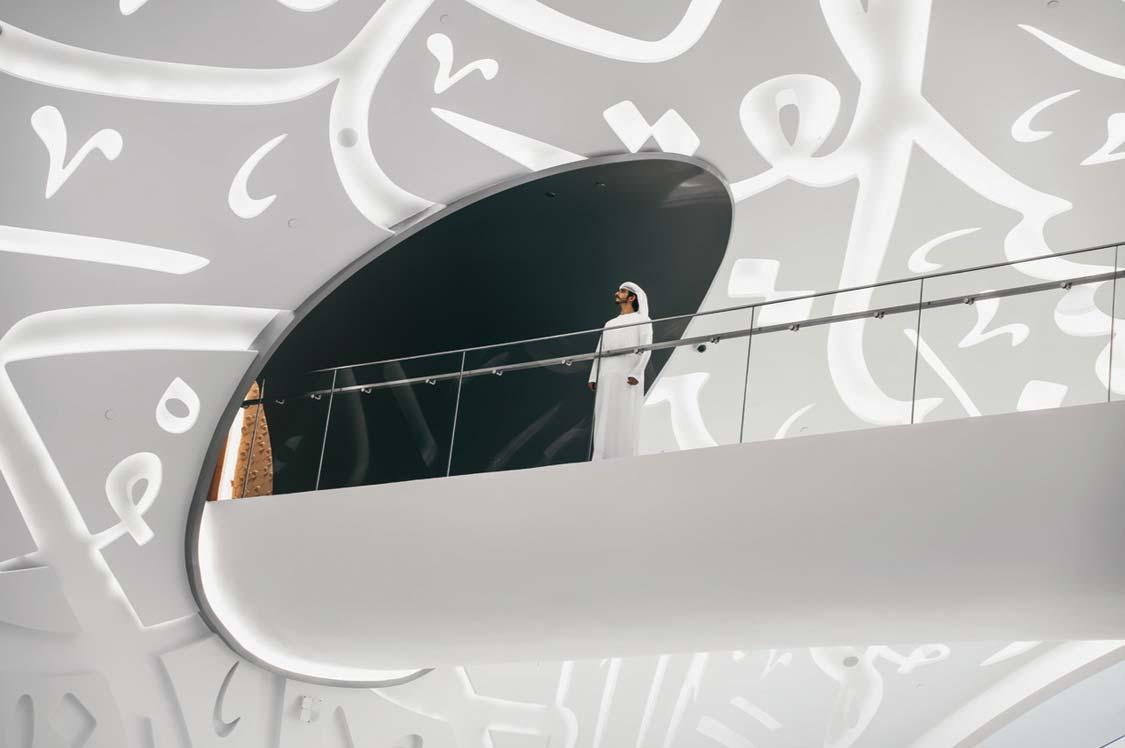
Sicomin is proud to have supported the build of Dubai’s Museum of the Future. Sicomin supplied its innovative bio-based intumescent gelcoat and fireretardant laminating resins for the production of over 200 double curved panels making up the interior of the Museum’s entrance lobby.
The Museum of the Future, a stunning new addition to Dubai’s skyline by architects Killa Design, engineers Buro Happold and contractor BAM International, opened last week on 22nd February 2022 and features a large percentage of composite materials in the interior construction.
Advanced Fiberglass Industries (AFI) manufactured 230 double curved interior panels, a unique doublehelix DNA structure staircase that scales the full seven levels of the museum and 228 GRP oval shaped light structures for the museums car parking area.
Lightweight, quick to install, durable and highly formable fireretardant composites provided the optimum material solution for the torus shaped Museum’s double curved interior panels that were

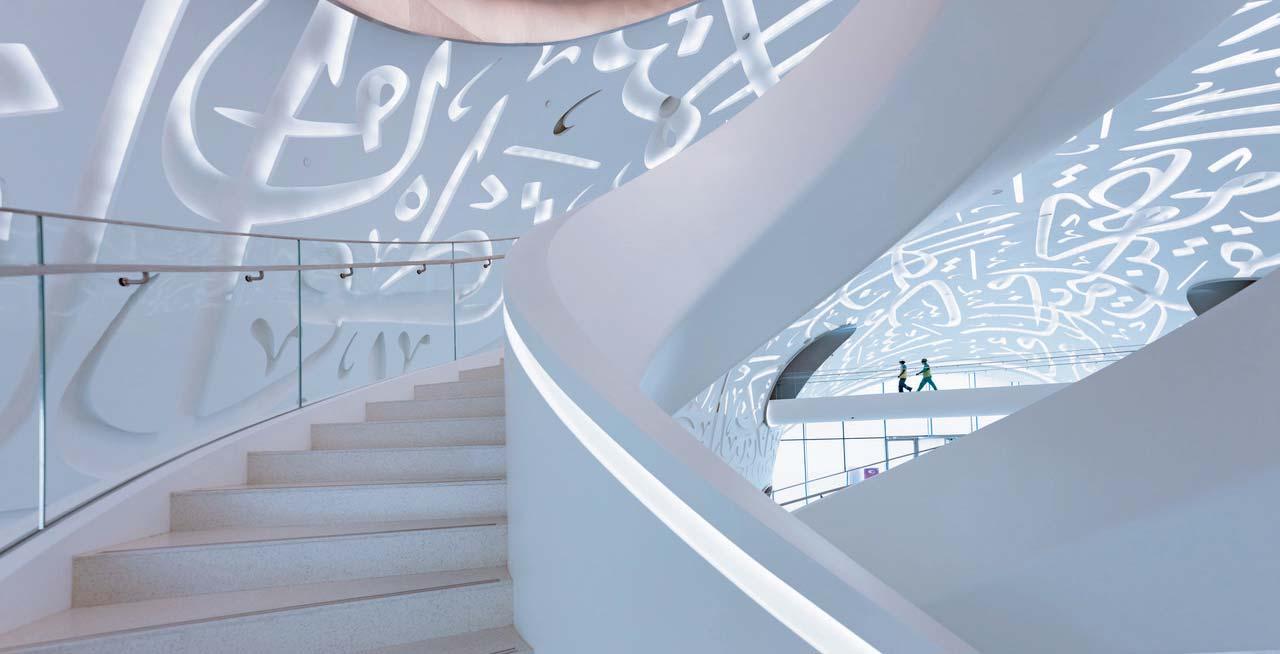
decorated with a unique raised calligraphy design featuring quotes from His Highness Sheikh Mohammed bin Rashid Al Maktoum, Vice-President and Prime Minister of the UAE and Ruler of Dubai.
In a first of its kind for a large scale composite project, adaptable mould technology from Danish company Adapa, was introduced by Advanced Fiberglass Industries, Dubai (AFI) to ensure that the interior panels could be delivered in line with the project schedule. As well as allowing each unique panel shape to be rapidly configured without the machining of traditional moulds, the adaptive mould technology massively reduced waste generated in the moulding process, contributing to the building’s low carbon LEED platinum credentials.
With a challenging structural and fire safety specification defined, Sicomin’s bio-based SGi128 intumescent gelcoat and SR1122 fire retardant laminating epoxy were chosen for the panels, an additional advantage being that in addition to high fire properties, SGi 128 is also formulated with over 30% carbon from renewable sources, reducing the final carbon footprint significantly.
Sicomin worked alongside the panel manufacturer, providing technical support for the fire test panels and the initial Adapa moulding trials. As a result the high-performance fire-retardant material solution was approved by Dubai Civil Defence, as well as achieving Class A (ASTM E84) and B-s1,d0 (EN13510-1) classifications in the testing carried out by Thomas Bell-Wright.
“Sicomin’s FR epoxy solutions gave us just the right balance of structural performance, processability and fire performance that we needed for the Museum’s interior panels,” commented Majid Akram Chaudhry, General Manager, AFI. “We were able to quickly dial in the new techniques required to use the materials on the Adapa moulds and the industrial scale up we needed to deliver the project on time was no problem for Sicomin to manage. As a result, we were able to increase the scope significantly and for the staircase and car park light fittings too.”
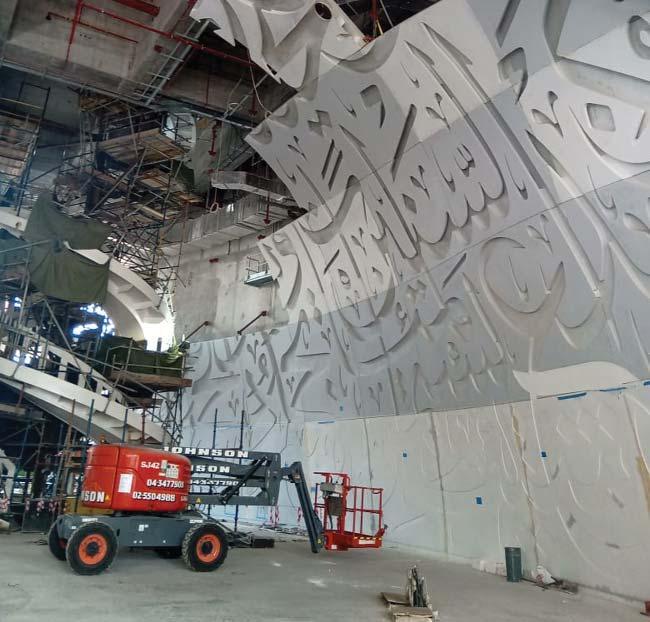
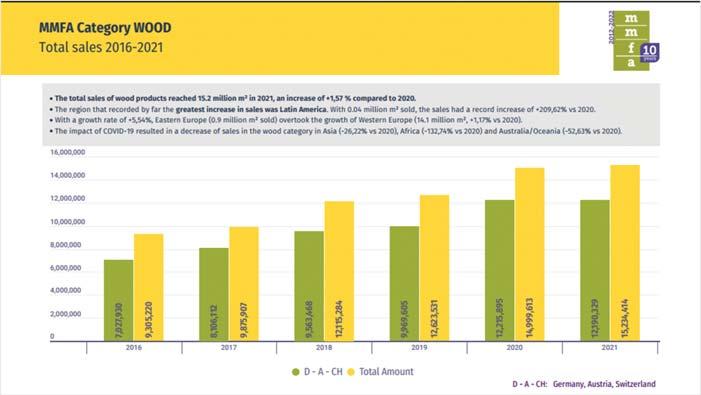
MMFA members record growth of +32% across all polymer categories in 2021
The global sales figures of MMFA members show a total growth of +27% across all categories in 2021 compared to 2020. Contrary to previous years, our members’ sales of wood products flattened (+1,6%), while members’ sales figures for all polymer products recorded a total growth of +32%, with Rigid EPC and SPC products showing an impressive increase of +79% and +30% respectively compared to 2020.
This significant growth follows from Rigid EPC and SPC’s sustained performance, anchoring them as strong contenders on the market. Amongst our MMFA members, Western Europe and North America consistently rank as leading markets in terms of volume of sales, while Africa, Latin America, Asia and Australia and Oceania are the most dynamic markets, with sales growth having doubled and even tripled since 2020. Finally, despite the current situation, our Eastern Europe members’ market share of 6% for SPC products shows significant market growth potential in the region.
Volume per category
Overall, in 2021 sales of wood flattened for MMFA members compared to last year, with a total of 15 million m² sold worldwide (+1,6%). Meanwhile, members’ sales of polymer products have continued to grow across all regions and reached 105 million m² total sales. LVT sales particularly increased this year (+27%), while SPC sales recorded +30%. Both categories respectively sold 46+ million and 49 million m² throughout 2021. Finally, EPC sales also recorded a significant increase amongst our members, with +80% and 9.3 million m² sold this year.
Total volume per areas
Members in Western Europe and North America account for 90% of sales for all categories of polymer products, except for wood, with the USA, Germany and France ranking as the top three markets. France is nevertheless significantly bigger than Germany when it comes to LVT clic sales.
Looking at MMFA sales of all polymer accrued products per total volume of sales per region, Western Europe ranks first with 54 million m² sold, followed by North America (41 million m²), Eastern Europe (6.1 million m²), Asia (2 million m²), Australia/Oceania (811.617 m²), Africa (654.124 m²) and Latin America (634.731 m²).
In 2021, wood sales were the highest with our Western Europe members in terms of volume (14 million m²), and in Eastern Europe (891.482 m²). This year, North America recorded 151.163 m² of wood sales, while Asia and Latin America sold 47.674 m² and 44.523 m² respectively. In Africa, 1.741 m² of wood products were sold in 2021, while Australia and Oceania sold 1.479 m².
MMFA’s largest single markets
The USA is our biggest market in North America this year for all polymer accrued products by far, selling 39 million m². In Western Europe, our biggest markets for all polymer accrued products in 2021 were Germany (17 million m²), France (14 million m²), Great Britain (5 million m²) and the Netherlands (4.5 million m²).
Germany was also the biggest market for rigid accrued polymer this year, with 10 million m² sold in total, followed by
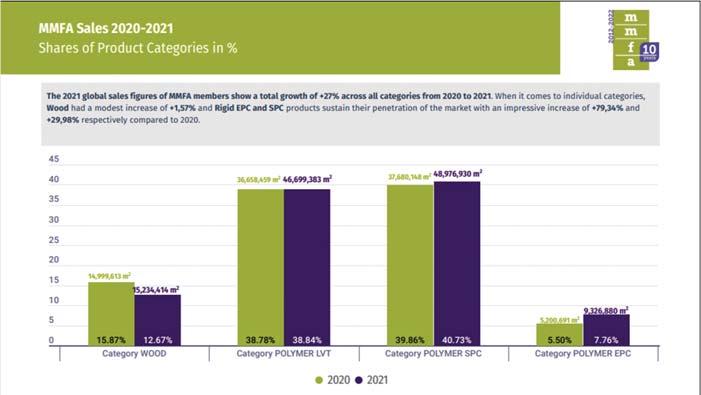
France (6 million m²) and the Netherlands (2.6 million m²). The USA remains our biggest market for rigid accrued sales in North America as well, with 21.5 million m² sold in 2021. Looking at our Eastern Europe market, Poland ranks first (1.4 million m²), followed by the Russian Federation (369.667 m²). Meanwhile, Australia recorded 655.413 m² of accrued polymer products sold, after the country became a rigid market due to historically bad experience caused by extreme exposure to sunlight.
When it comes to sales of LVT clic, France positions itself as our biggest market in Western Europe, with 8.2 million m² sold. It is followed by Germany with 6.9 million m², Great Britain (3.3 million m²), the Netherlands (1.9 million m²) and Switzerland, with 295.083 m² sold in 2021. In Eastern Europe, the Russian Federation was the biggest market for LVT clic this year (912.887 m²). In North America, the USA still stands as the biggest market, having sold 17.4 million m² of LVT clic products in 2021.
For wood products, MMFA’s biggest markets in 2021 were Germany (10.1 million m²), Austria (1.5 million m²) and Switzerland (493.693 m²). In Eastern Europe, the Czech Republic was the biggest market, with 432.194 m² sold. Finally, in North America, Canada was the most significant market for wood products, with 82.084 m² sold this year.
MMFA’s dynamic markets & growth potential
Overall, while we see that Western Europe (+43,7%) and North America (+16%) members are leaders when it comes to the total volume of sales of all accrued polymer products, MMFA’s African market, although starting with lower bases, is growing at triple rates with an increase of +247% in sales of EPC products (77.931 m²) in 2021 compared to 2010. Our Asian market also show a nice and even spread across a number of countries for all polymer products, with sales of SPC products being the most significant this year, with a +188% increase compared to 2010 (649.806 m² sold). Latin America and Australia and Oceania members have also doubled their volumes of sales compared to 2020, both recording an increase of +88% and +102% respectively across all polymer accrued products. Finally, despite the current situation, our Eastern Europe members represent a significant market size, already accounting for 6% of MMFA’s market shares for all polymer accrued products. Meanwhile, MMFA members in Western Europe accounts for most market share of wood products sales, with 92%.
About MMFA: The Multilayer Modular Flooring Association is an organisation representing the leading producers of flooring in Europe and their suppliers. The association was established in October 2012 in Munich, Germany, by seven European flooring producers. The management of MMFA has moved to Brussels since November 2019.
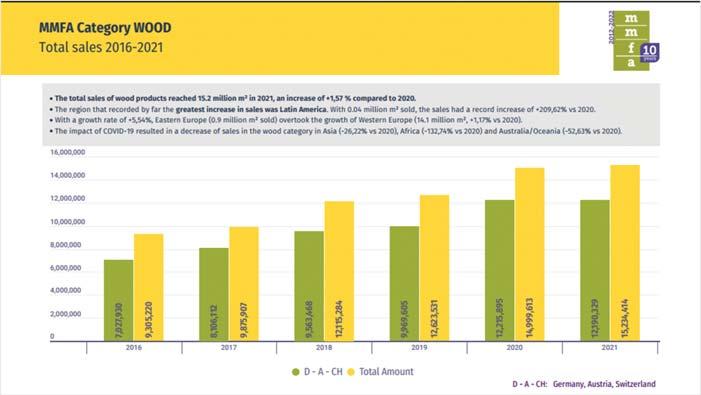
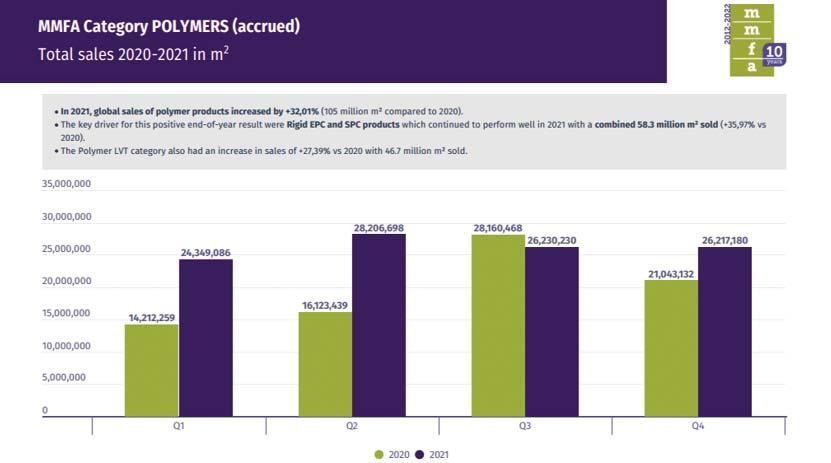
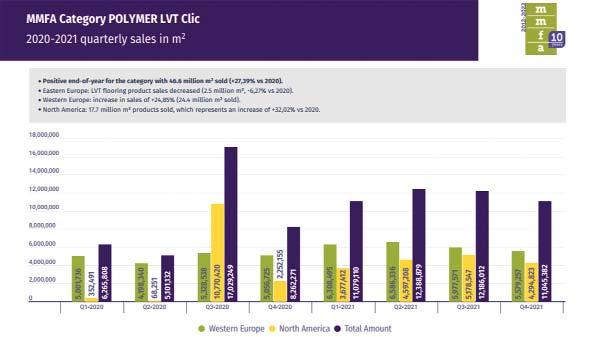
Archroma launches EARTH SOFT system based on Siligen® EH1, a new vegan textile softener with one-third plant-based active content
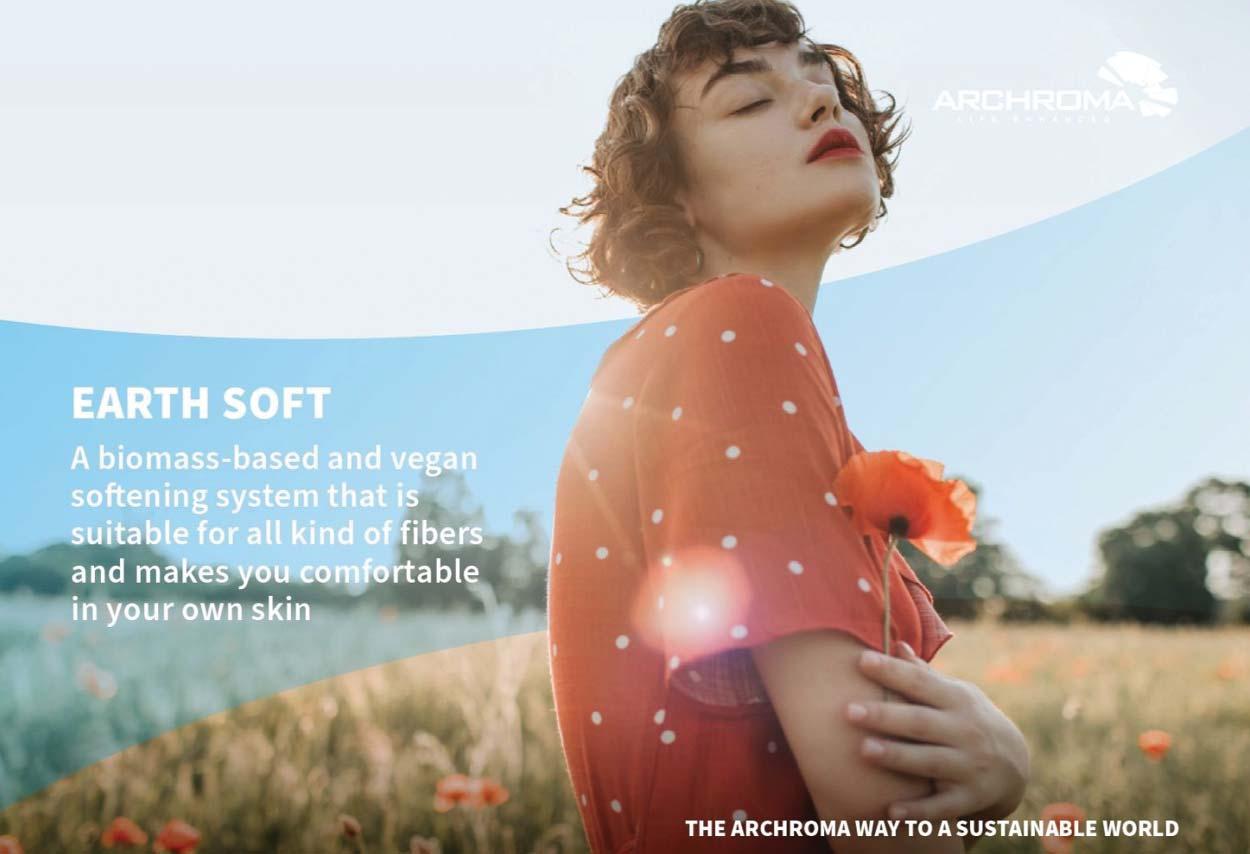
Archroma, a global leader in specialty chemicals towards sustainable solutions, today announced the launch of EARTH SOFT, a new softening system for textile and fashion applications, based on Archroma's latest innovation, a vegan silicone softener, Siligen® EH1, with 35% plant-based active content.
Siligen® EH1 is the latest addition in the plant-based innovations developed by Archroma in recent years, such as EarthColors® dyes and Appretan® NTR binders, as alternatives offered to manufacturers and brands looking to reduce the use of fossil fuel based ingredients without compromising performance.
The range has been developed in line with the principles of “The Archroma Way to a sustainable world: safe, efficient, enhanced, it’s our nature”. More than 35% of the Siligen® EH1 softener's active content is based on plant-based, renewable raw materials. In addition, the product features ultralow cyclic siloxanes (D4, D5, D6) which are classified by the European Chemicals Agency as “Substances of Very High Concern” due to their very persistent and bioaccumulative properties.
Siligen® EH1 is ideally suited for shirts, underwear, sportswear, towels, bed sheets, etc. as it provides an excellent wearing comfort by supporting a good moisture transportation and delivering a smooth and soft touch.
The new softener, and the EARTH SOFT system which also includes a Hydroperm® wicking agent to boost hydrophilic properties on synthetic and blended fibers, can be applied on all natural and synthetic textile fibers.
Siligen® EH1 is suitable for both woven and knitted articles. It can be applied by padding process, as well as by exhaust process as it shows a very good shear stability and a low foaming profile. It can be used on white articles and those treated with optical brighteners, as it doesn’t cause thermomigration nor phenolic yellowing.
Paul Cowell, Head of Competence Centers for Brand & Performance Textile Specialties at Archroma, comments: “The new EARTH SOFT system based on Siligen® EH1 softener adds to our growing portfolio of innovations based on natural and renewable plant-based resources. This new breakthrough innovation by Archroma helps us and our partners in the textile and fashion industry to minimize our dependence on petroleum fossil fuel products.”
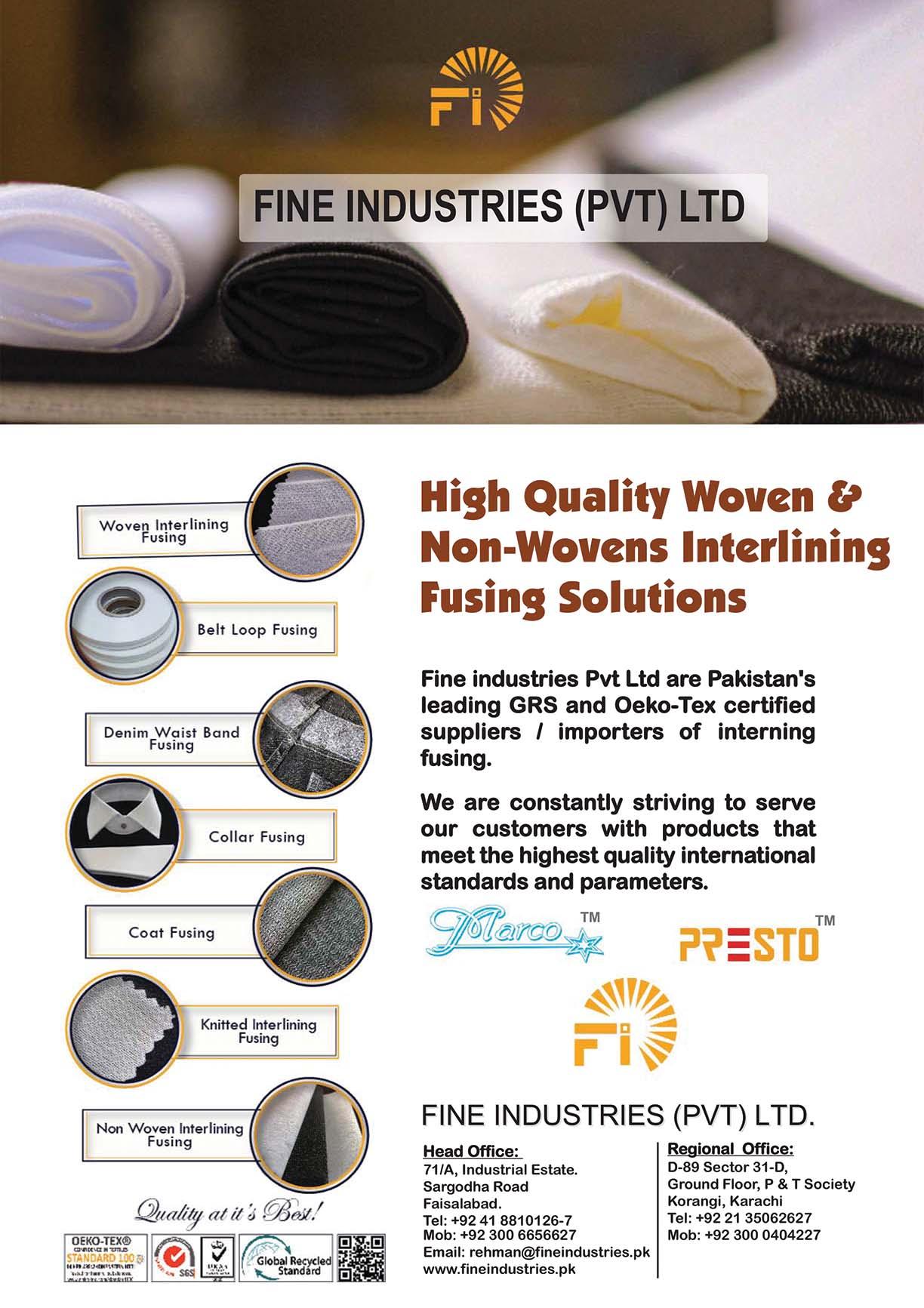
Huntsman Textile Effects launches water conservation project in India

76 KL/Day water saving by optimizing pH analysis process in dye vessels A step closer to achieving the
‘Huntsman Horizon 2025’ goal Potential savings of over Rs 10 crore or USD146,000 annually from the project
Singapore -Huntsman Textile Effects, the global leader in innovative and environmentally sustainable dyes, chemicals, and digital inks, has successfully implemented a water conservation process to improve water efficiency and reduce net water usage at its Baroda facility, which is located in the western region of India. The initiative undertaken at the plant aims to save around 76 kilo liters of Reverse Osmosis water per day by modifying the phase sequence in the pH measurement program.
Water is used extensively throughout textile processing operations. The amount of water used varies widely in the industry, depending on specific processes operated at the plant, equipment used, and policies concerning water use. This conservation project at the Baroda Plant will have a potential savings of Rs 10 crore or USD146,000 a year for the organization.
Speaking on the development, Mark Devaney, Vice President Manufacturing and Operations Excellence, Huntsman Textile Effects said, “At Huntsman, we recognize the important role we play in creating a more sustainable future and are committed to the well-being of the communities where we operate, and the protection of the environment. We are continually looking for ways to improve the environmental footprint of our manufacturing sites and have been implementing numerous projects in recent years to reduce our water usage.”
“The team has done a detailed assessment of the pH analysis process in dye vessels, mapping the existing water usage and potential conservation method. After a brief study and several brainstorming sessions, we were able to adjust the phase sequence, resulting in conservation of Reverse Osmosis water by almost 76 kilo liters of water per day.” said Kavishwar Kalambe, Site Director, Huntsman Textile Effects. “This project directly contributes to Huntsman’s Horizon 2025 goals to reduce net water usage at facilities in water-stressed regions,” he added.
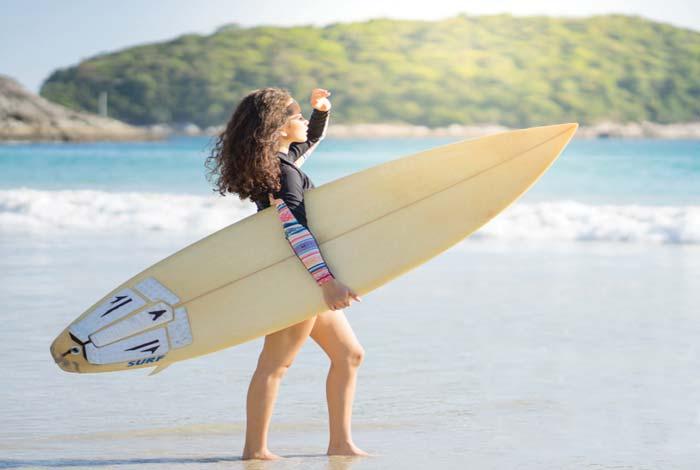

Full line-up of major exhibitors confirmed for FESPA Global Print Expo 2022

Berlin events will offer most comprehensive innovation showcase for print and signage since 2019
FESPA Global Print Expo and European Sign Expo 2022 (31 May – 3 June 2022, Messe Berlin, Germany) are set to bring together the strongest line-up of exhibitors since 2019, with more than 250 suppliers already contracted to exhibit and many more active discussions in progress. The list of confirmed participants includes many who were unable to be at the 2021 Amsterdam event and who are now eager to regain their momentum by being part of the Spring 2022 events.
Visitors will be able to see hardware solutions from major exhibitors including event sponsors Durst, Mimaki, Brother and HP, as well as Agfa, aleph, Canon, Epson, Fujifilm, Kornit Digital, Mutoh, M&R, Roland DG and swissQprint. The array of media and consumables suppliers includes 3A, Ahlstrom Munksjö, Avery Dennison, Hexis, InkTec, Neenah Coldenhove, Neschen, ORAFOL, PoliTape and Sun Chemical. Barbieri Electronic, Caldera, OneVision and ONYX Graphics are among the companies presenting automation, workflow and colour management solutions.
Head of FESPA Global Print Expo, Michael Ryan comments: “It’s so motivating to have such a strong vote of confidence from the supplier community for FESPA and our power to reinvigorate the speciality print industry after the challenges of the last two years. Suppliers who joined us in Amsterdam in October 2021 were reminded of the unique value of live events and the commercial advantage of connecting with customers and prospects face-to-face, so we’re delighted that many more exhibitors will reap these benefits in 2022.
Now that businesses are back up and running and senior decision-makers are looking to secure their future investments, the importance of live shows to accelerate recovery has never been more significant.”
European Sign Expo 2022, the leading European exhibition for signage and visual communications, will be co-located with FESPA Global Print Expo. The event will reunite key signage professionals with companies specialising in channel lettering, digital signage, dimensional signage, engraving and etching, illuminated displays, out of home media, LED, outdoor systems, laser cutters and sign tools.
Platinum Sponsor EFKA will return to European Sign Expo alongside confirmed
exhibiting companies including: Art Neon Lighting, Cosign, dap, Domino Sign, Harmuth, NEX LINE SRL, SolaAir, and vhf camfacture.
Christoph Gamper, CEO & Co-owner, Durst Group AG comments: “All signs point to FESPA 2022 meeting a weakened COVID scenario, and we can finally talk business again. But it's no longer about unchecked "wild growth" but solutions for a more sustainable world. Print can be an essential part of this, and FESPA is a fixed point in the universe of print. In this respect, experiencing print in motion means new, sustainable business models for our customers and us. We are looking forward to FESPA, to Berlin, and above all, to finally seeing customers "live" again and demonstrating new ways and possibilities.“
Kevin Jenner, European Marketing Manager, Fujifilm Wide Format Inkjet Systems comments: "Having not attended any major exhibitions since before the pandemic, FESPA 2022 is happening at the perfect time for Fujifilm. In 2021 we unveiled our 'new blueprint for wide format' with two new Acuity presses (the Acuity Prime flatbed and the Acuity Ultra R2) built with a completely new look, a new level of functionality and enhanced ROI. FESPA 2022 provides us with the perfect platform to reveal the exciting next phase of machines in this expanding range.”
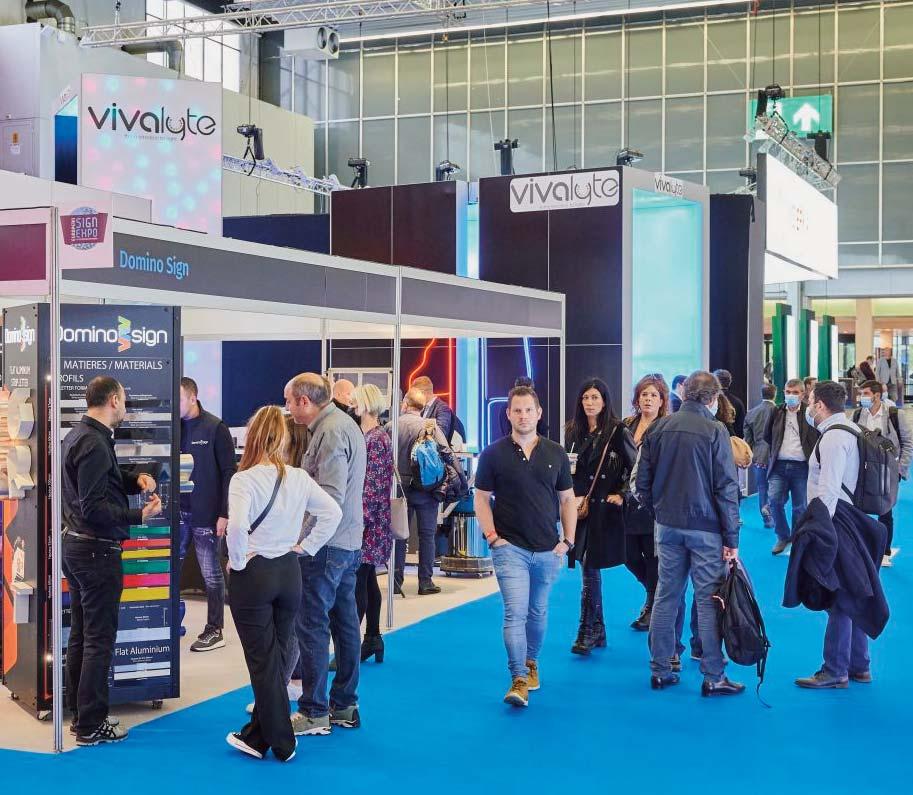
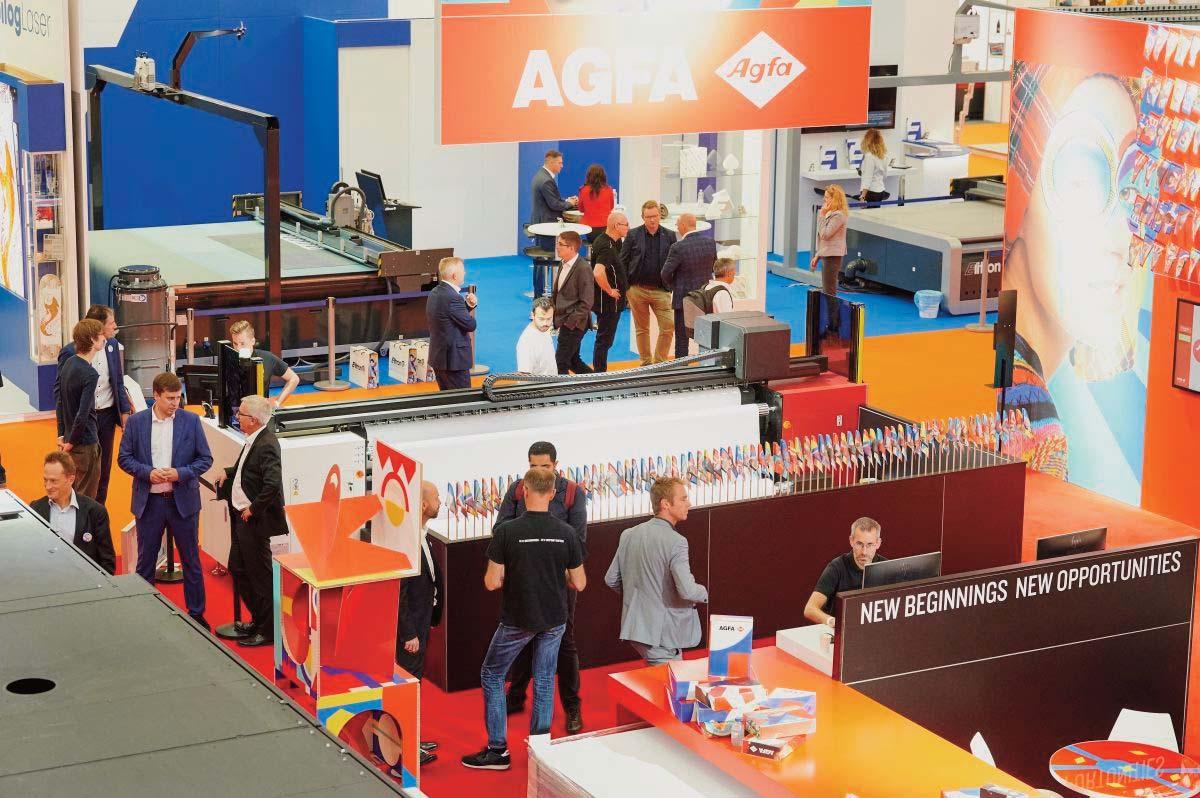
Italian Textile Machinery at Techtextil North America 2022
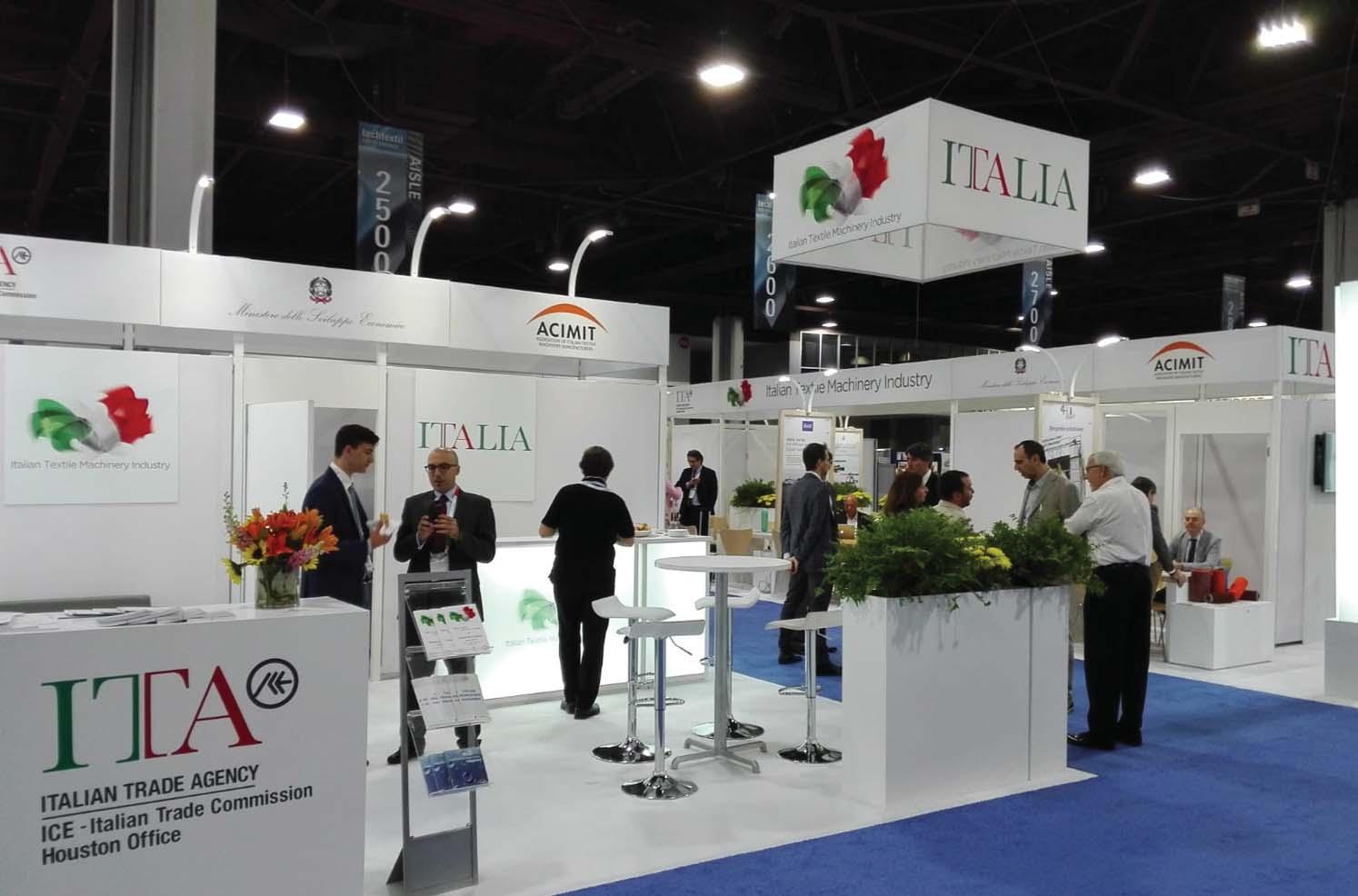
The next edition of Techtextil North America will take place in Atlanta from May 17th to 19th. At Atlanta ACIMIT, the Association of Italian Textile Machinery Manufacturers, and Italian Trade Agency organize an Italian Pavilion, where 17 Italian machinery manufacturers involved in the production of machines for technical textiles will show their innovative solutions.
ACIMIT members exhibiting in the Italian Pavilion are: 4M Plants, Aeris, Arioli, Computer House, Fadis, Flainox, Guarneri Technology, Ima, Kairos Engineering, Mcs, Ramina, Siltex, Stalam, Testa, Willy.
The US textile industry is one of the top in US manufacturing sector, with a sales volume of exceeding US$ 64 billion in 2020, with approximately 300,000 workers and about 15,000 companies. The industry’s strength lies in cotton, man-made fibers, and a wide variety of yarns and fabrics, including those for apparel and industrial uses.
In 2021, the USA represented the third market for Italian textile machinery exports, behind China and Turkey. In 2021 January-September period the value of Italian sales to US market was 93 million Euros, an increase of 74% compared to the same period of the previous year.
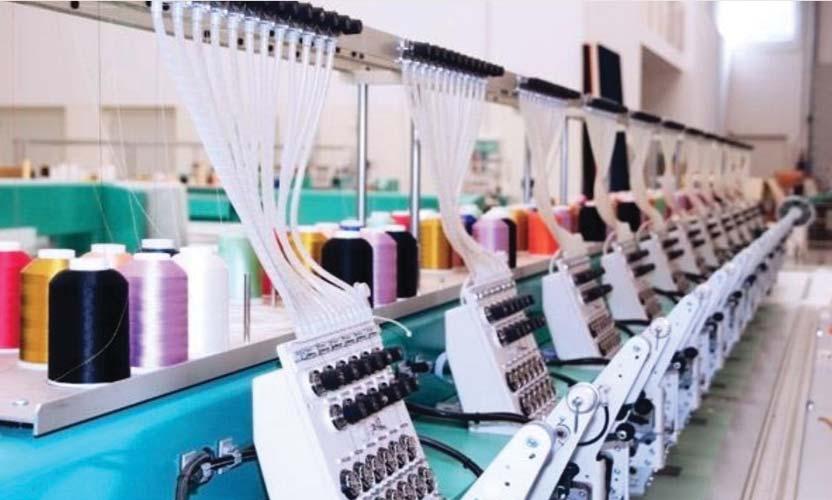

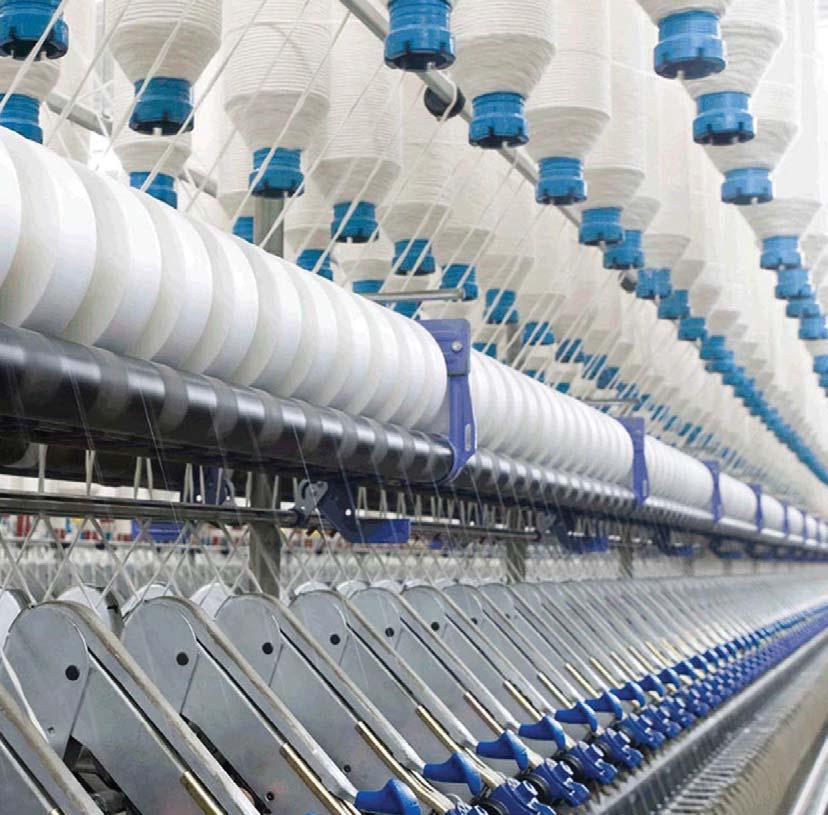


Peter Zimmer dies
Peter Zimmer, former managing partner of Zimmer in Kufstein/Austria and the pioneer of modern textile printing, passed away in Kufstein at the age of 98.
For more than 70 years until his death, Zimmer was occupied with new ideas for textile printing, inventing and developing processes and machines, leading the way for the entire textile printing industry.
He began his career in his parents' business. The company was reestablished in Kufstein in 1950 after the turmoil of World War II and displacement from Bohemia (now part of the Czech Republic).
A large number of important developments, underpinned by corresponding patents, helped the company to strive and prosper within a very short period. Rotary screen printing, the magnetic roll rod system, directly patterned galvanic screens, rotary screen carpet printing with widths of up to 5 m and repeats of over 3 m as well as the first digital carpet inkjet printer, the Chromotronic, are associated with the name of Peter Zimmer.
However, Peter Zimmer was not only a good developer, but also a valued consultant and salesman in all markets of the world with a focus on the Middle East, Pakistan, Bangladesh and India.
During the last years of his life, Peter Zimmer worked intensively within his Peter Zimmer KG, Kufstein, on a new type of process for digital printing on fiber strands and sliver, with which reproducible color shades can be achieved by means of additive color [1].
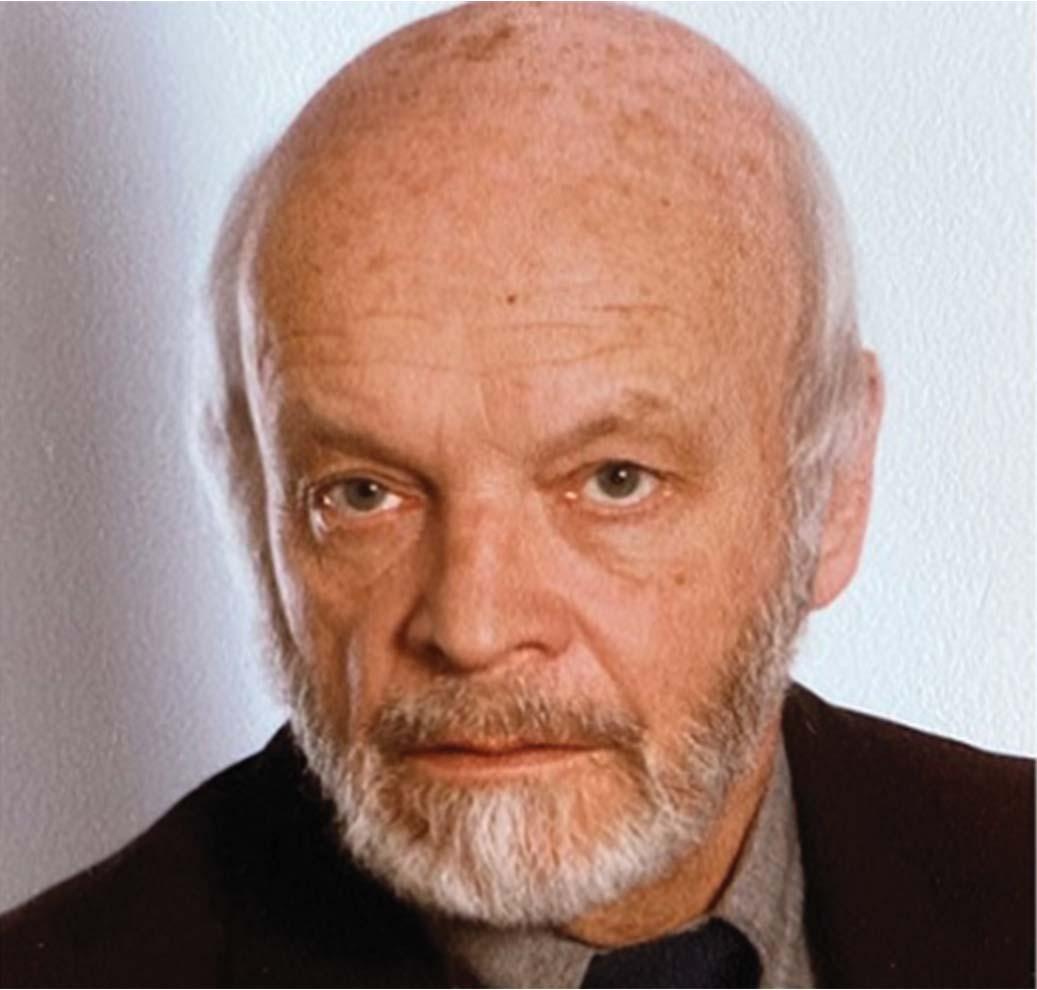

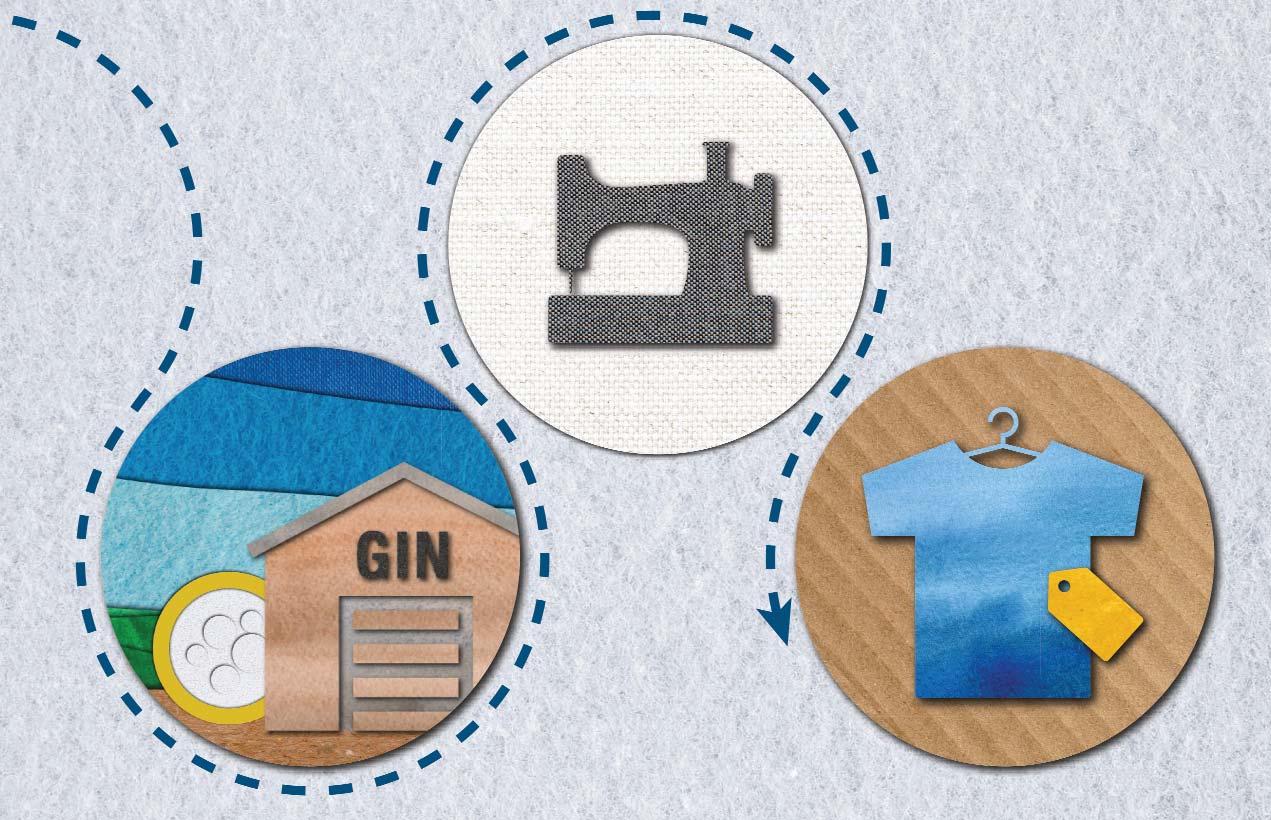
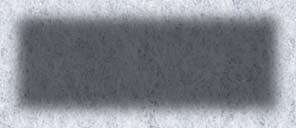
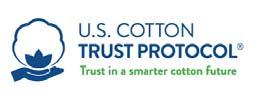
When it comes to sustainable cotton... Transparency Matters
Now more than ever, there is an imperative and understanding for the need to protect and preserve the planet.
In October 2021, COP26 brought together many fashion brands and highlighted the need for sustainability within the industry.
The event resulted in a new version of the United Nations Environment Program’s fashion charter, which now includes 130 signatures from companies like Gap Inc.
Evolving attitudes regarding sustainability and changing priorities among brands, retailers and consumers are creating demand for greater sustainability and transparency, starting at the fi eld and continuing throughout the entire supply chain. In fact, a letter published during COP26 highlights the need for collective action in sustainability. The letter focused on the need to achieve net zero emissions by 2050, readdressing supply chains, and a shift in attitude from profi t driven to wellbeing of the planet.
With the increased scrutiny on sustainability, brands and retailers want to ensure what they buy is what they get, with raw material sourcing more important today than ever before.
The U.S. cotton industry’s existing commitment to leadership in more sustainable cotton growing practices has been clear over the past 35 years. It has made signifi cant strides in reducing its environmental impact, decreasing water use, soil loss, greenhouse gas emissions and energy use while increasing soil carbon and land use. But the U.S. cotton industry knew there was still work to be done to ensure that it contributed to the protection and preservation of the planet.
Launched in 2020, the U.S. Cotton Trust Protocol is a farm level, sciencebased program that sets a new standard in more sustainably grown cotton. It brings verifi able goals and measurements to cotton production - driving improvements in land use, soil carbon, water management, soil loss, greenhouse gas emissions and energy effi ciency.
The Trust Protocol allows U.S. producers to showcase their sustainable practices and how they have been, and will continue to be, leaders in sustainability on a global scale.
”For sustainability to be meaningful we understand the textile supply chain must demonstrate continuous improvement...”
At the same time, the program was designed to meet the needs of brands and retailers in the fashion and textile industries, which are increasingly expected to show the sourcing data for their products.
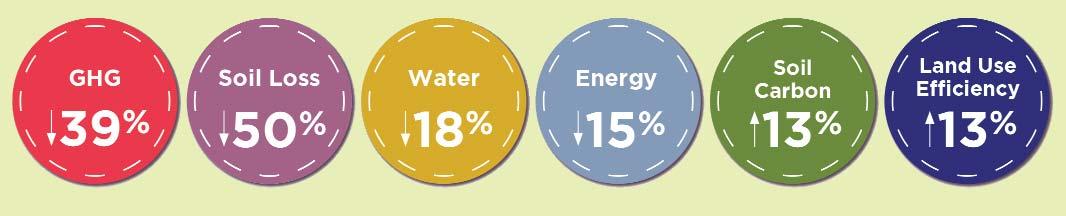
“The Trust Protocol measures, evidences and verifi es sustainability credentials,” said Dr. Gary Adams, president of the U.S. Cotton Trust Protocol. “With the Trust Protocol we are providing access to more sustainability grown cotton for brands and retailers, and science-based, data led assurances that their consumers can have confi dence in – something that has been lacking in the industry to date.”
Trust Protocol members have access to aggregate data based on selfassessment questionnaires of participating growers in key sustainability metrics.
This data-based approach, backed up by independent, third-party verifi cation from Control Union Certifi cations North America, gives brands and retailers the critical assurances that the cotton fi ber element of their supply chain is more sustainably grown.
However, the program does not stop there. Recognizing the growing importance of increased supply chain visibility to brand and retailer members, the Trust Protocol has selected to collaborate with TextileGenesis™ in order to be the world’s fi rst sustainable cotton fi ber to offer its members articlelevel transparency across the supply chain.
Harnessing blockchain technology, the Protocol Consumption Management Solution (PCMS) begins at the gin where it records and verifi es the movement of U.S. cotton throughout the supply chain and provides a transparency map, including the names and locations of Trust Protocol mill and manufacturer members that were involved every step along the way, into the finished products that are shipped to brands and retailers. Currently in pilot, the PCMS provides brands and retailers the assurance and visibility that U.S. cotton is included in their products.
Mills and manufacturers who join the Trust Protocol can also be identifi ed as part of a fully transparent supply chain and selected by brands and retailers as they look to source U.S. cotton fi ber.
“For sustainability to be meaningful, we understand that the textile supply chain must demonstrate continuous improvement and transparency throughout the entire process – building trust from fi eld to fabric,”said Adams.
In its fi rst year the Trust Protocol has welcomed more than 560 brand, retailer, mill and manufacturer members since its launch in 2020. This includes J.Crew, Madewell, Levi Strauss & Co. and, Gap Inc. as well as global apparel manufacturer Gildan. The Trust Protocol has also welcomed UK retailers Tesco, Byford and Next Plc.
To learn more about the U.S. Cotton Trust Protocol visit TrustUSCotton.org.
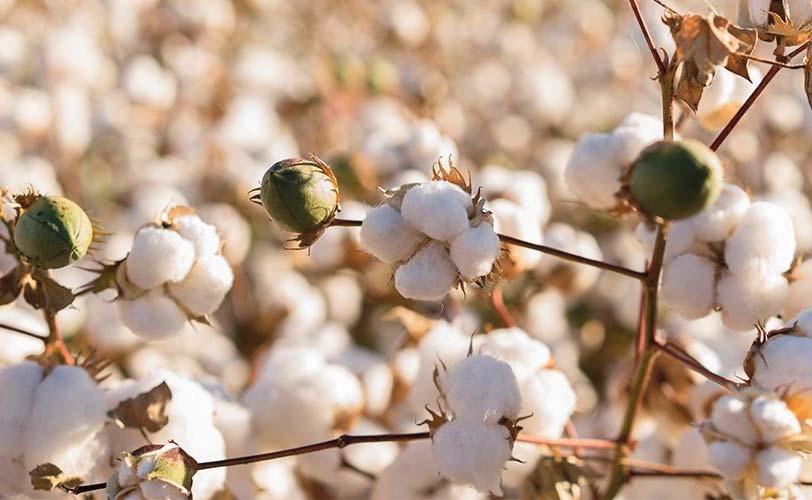
Naia™ from Eastman showcases sustainability and growth at Première Vision

Eastman, producer of sustainably sourced NaiaTM cellulosic fiber, announces its exhibition at Première Vision (PV), the global event for fashion professionals, February 8–10, 2022, and the online PV Digital Marketplace, February 7–11, 2022.
Having debuted at this event only three years ago, the versatile NaiaTM offerings have been expanded as the company has collaborated with dozens of brands and numerous value-chain partners worldwide.
NaiaTM representatives will be at booth 4D48 in the Yarns Hall (Four) at the Parc Expositions Paris Nord.
Ruth Farrell, marketing director of textile fibers for Eastman, will present at the event on Thursday, February 10, 2022, 11:30–12:00 CET, with a session titled Live, Learn, Lounge — Global insights into every closet’s must have item: Loungewear.
NaiaTM Renew offers clear advantages. It is available in a filament — featuring a silky hand, rich luster and fluid drape that can be used to create fashionable womenswear garments — or a staple fiber, which is inherently soft and quick drying. Its reduced pilling properties make it ideal for loungewear. It blends well with other eco-friendly materials such as lyocell, modal and recycled polyester to produce sustainable fabrics and garments that are ideal for every day and everywhere. From tops, dresses, Tshirts, comfy pants and sweaters, NaiaTM Renew offers a wide array of sustainable options. "The global pandemic has strengthened our resolve and allowed us to further innovate to meet our goal: making sustainable fashion accessible to all. We have experienced strong growth due in large part to the quality of our offerings, the inherent sustainability of NaiaTM and a strong network of global partners,” Farrell said. “Collaboration is key to creating measurable impacts in sustainable fashion. Numerous brands are working with us to meet their sustainability goals, and we’re helping our mill partners with their sustainability offerings to market.”
Two new Naia™ Renew staple fiber fabrics from Polopique: Polopique 2556 and Polopique 2557
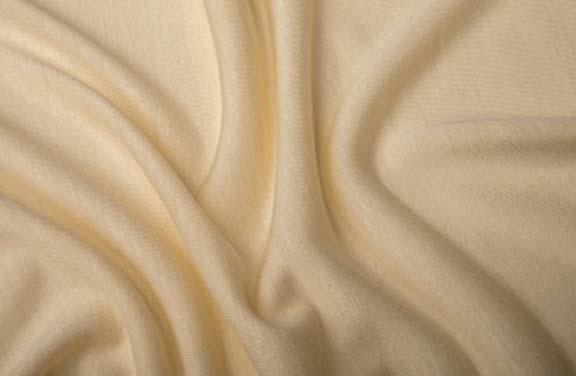
NaiaTM Renew is created with the highest safety, social and environmental standards, bringing the richness of nature to comfortable and effortlessly luxurious fabrics. It’s produced from 60% sustainably sourced wood pulp and 40% hard-to-recycle waste material* diverted from landfills or incinerators with a low carbon footprint in a closed-loop process where solvents are safely recycled back into the system for reuse.
NaiaTM Renew can be produced at scale with the circular economy in mind, providing the highest quality products without compromising creativity or the planet’s resources. With traceability from tree to fiber, NaiaTM Renew is the perfect choice for womenswear. NaiaTM certifications and traceability are available online. *NaiaTM Renew recycled content is achieved by allocation of recycled waste materials using an ISCCcertified mass balance process.
Some of Eastman’s value-chain partners exhibiting their NaiaTM fabrics at PV include Akin Tekstil, Brunello, Elyaf Tekstil, Eusebio SRL, Familitex, GI Tessil, Girani, Gülipek Textiles, Gülle Tekstil, Ipeker, Karsu, Kipas Textiles, Luxury Jersey, Manifattura Pezzetti, Marini Industrie (supplied by Ghezzi/Lombard), Mario Cucchetti Tessuti, Meltam Tekstil, Nilba Tekstil, Nuryildiz Tekstil, Parlamis Atadan Tekstil, Pastel By Yilmazipek, Riopele, Sampaio & Filhos, Barutçu Tekstil, Ekoten, Youngbo Textile Co., SNT Co., Ltd., and Saechang Commercial Co, Ltd. More fabric images and information can be found at the PV Digital Marketplace.
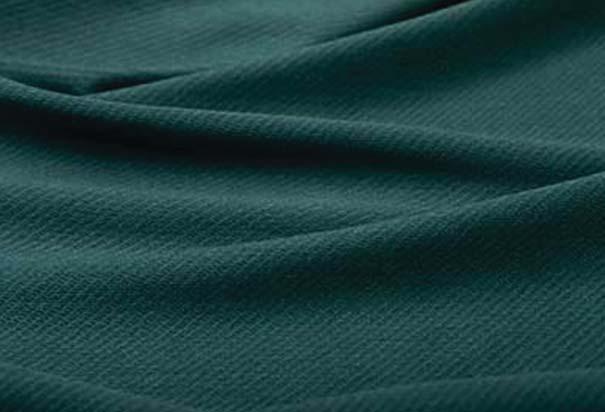
About Eastman
Founded in 1920, Eastman is a global specialty materials company that produces a broad range of products found in items people use every day. With the purpose of enhancing the quality of life in a material way, Eastman works with customers to deliver innovative products and solutions while maintaining a commitment to safety and sustainability. The company’s innovationdriven growth model takes advantage of world-class technology platforms, deep customer engagement, and differentiated application development to grow its leading positions in attractive end markets such as transportation,building and construction, and consumables. As a globally inclusive and diverse company, Eastman employs approximately 14,000 people around the world and serves customers in more than 100 countries. The company had 2021 revenues of approximately $10.5 billion and is headquartered in Kingsport, Tennessee, USA.
Two new Naia™ Renew staple fiber fabrics from Ekoten: Ekoten 2202 Teal Spun Diagonal Fleece Knit and Ekoten 2201 Sand Spun 2x1 Rib Knit
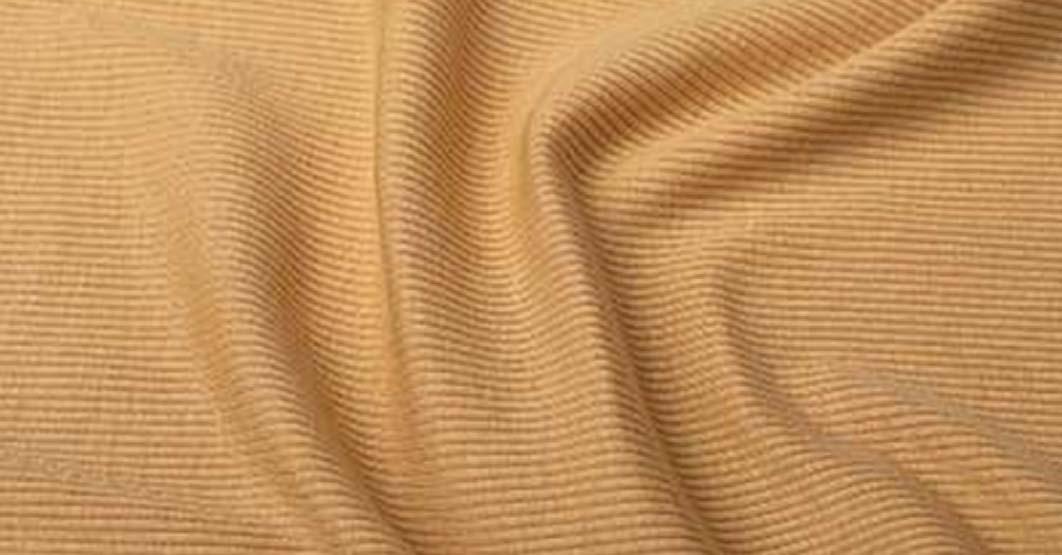
HYPETEX®, adidas Selected as JEC Innovation Awards 2022 Finalists for Kromaskin™ Field Hockey Stick
Hypetex®, London, February 4th 2022: Hypetex®, the market leaders in colouring carbon fibre materials, is delighted to announce that its Hypetex® Kromaskin™ field hockey stick for adidas has been selected as a finalist for the 2022 JEC Innovation Awards.
Hypetex® was commissioned by adidas to develop a market leading hockey stick differentiated from existing equipment not just by its unique pigmented carbon fibre finish, but also by its game changing hitting power and consistency. The patented range of KromaskinTM sticks, created with support from project partners Textreme® and Marque Makers, was found to outperform competitors in a benchmark study against eight other premium hockey sticks carried out by Loughborough’s Sports Technology Institute (STI).
Hypetex® lead the design, engineering, materials, and production process development for the adidas field hockey stick project. By incorporating the stick’s finish colour within the outermost carbon fibre layer, the stick mould could be adjusted outwards, placing the highly structural spread tow materials right at the outer extremities of the mould cavity, increasing mechanical performance and maximising the structural benefits of the composite materials used.
Whilst the KromaskinTM surface provides a stunning depth of colour with minimal finishing required after demoulding, the Hypetex® technology, including an epoxy based expanding microsphere system used in the core, delivers significant performance gains on the hockey pitch. In tests at the STI, adidas KromaskinTM sticks had up to 16% higher coefficient of restitution (COR), meaning they will return more energy and the ball will travel faster. In addition, through the production led design and materials used, the variation in COR was 70% less than the other sticks on test, a significant reduction in the production inconsistencies common with the manufacturing of performance sporting goods.
The JEC Innovation Awards are recognized as the composite industry’s most prestigious awards. Over the last 16 years, the JEC Innovation Program has involved nearly 1,900 companies worldwide. The award winners will be announced on the 26th April in Paris, and Hypetex® and adidas are finalists in the Sports & Leisure category.
“We are thrilled to be nominated as finalists for the 2022 JEC Innovation Awards and are delighted that the awards committee recognized the significant performance gains realized with the new adidas sticks as well as the stunning visual finish created by our Kromaskin™ technology,” comments Marc Cohen, CEO, Hypetex® .
Exhibiting as part of the Composites UK stand, Hypetex® will display its full portfolio of uniquely coloured materials at JEC World including 3K woven styles, ultra-lightweight spread tow fabrics, UD materials, and new coloured flax products. The Hypetex® Kromaskin™ hockey stick for adidas will also be on show in Paris as part of the JEC Innovation Planets platform.
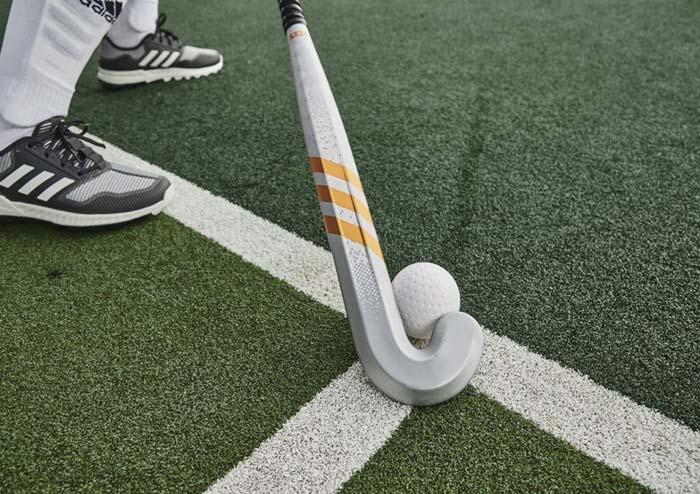
About Hypetex®
Hypetex® are leaders in colouring advanced materials, supplying a broad spectrum of visually stunning coloured technical textile reinforcements which, along with offering a colour as an option, provide significant part finishing time and cost benefits without the additional weight of a traditional paint system.
Hypetex® Special Projects (HSP) division in house engineering, product design, and processing engineering expertise supports clients throughout their composite project from initial concept to final production component. offering a complete end-to-end suite of services for companies that wish to design, create, and produce products using advanced composite technology.

Turkish upholstery leader opts for the Montex®Coat
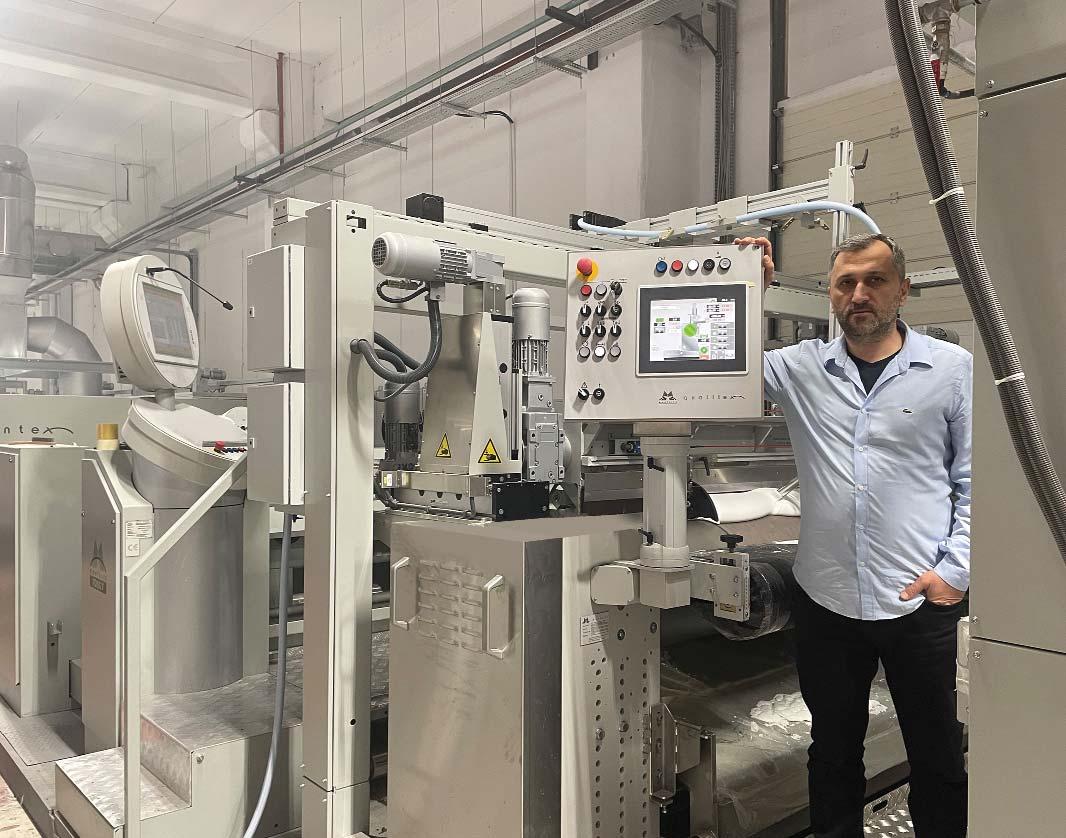
Turkish powerhouse in home textiles and furnishing fabrics Altun Tekstil has just commissioned the first Montex®Coat coating system in Turkey.
The advanced machine has been installed at the ever-expanding familyowned company’s industrial complex in Bursa and is being employed to provide an anti-slip and textured backing to upholstery fabrics with a stable and uniform foam, via knife-over-roller coating.
Founded in 1993, Altun exports its fabrics to more than 60 countries, with its major export markets being Russia and Ukraine, as well as many Middle Eastern and European countries.

Its integrated operations include the production of texturized yarns, weaving and raschel knitting, in addition to dyeing and finishing. With a major focus on tulle curtains and upholstery, the company’s fabric range also extends to a wide variety of apparel styles.
“Despite the current market conditions, our investments continue to increase,” said company owner Murat Altun. “We have established both a knit and woven fabric dyehouse and an integrated upholstery fabric weaving factory, where in 2022 we will also backward integrate into synthetic filament spinning from chips. In the longer term, we plan to bring all of our operations together in a single facility of 350,000 square metres, to employ approximately 10,000 people. We have new investment targets that aim to further reduce our dependence on overseas suppliers and enable us to do everything within our own operations.”
Altun has installed eight Monfongs stenters in various widths at its two plants since 2016 – coincidentally the year Monforts Turkish representative Neotek was founded.
“We have worked with Neotek from the start and both its service and the product quality with Monforts technology are extremely satisfying,” said Plant Manager Mehmet Mor.
All of the stenters are engineered for specific product lines and the Montex®Coat unit is integrated into the latest of these lines, which has a maximum working width of 2.2 metres and eight chambers.
“With the Montex®Coat unit Altun is able to achieve an even foam application at high speed which results in a very economic process,” said Monforts Sales Manger Thomas Päffgen.
The fully integrated line benefits from universal control technology and the unique Monforts visualisation system. The Montex®Coat’s bordering system has been optimised for enhanced userfriendliness, while the doctor blade adjustment range is the most precise available on the market.
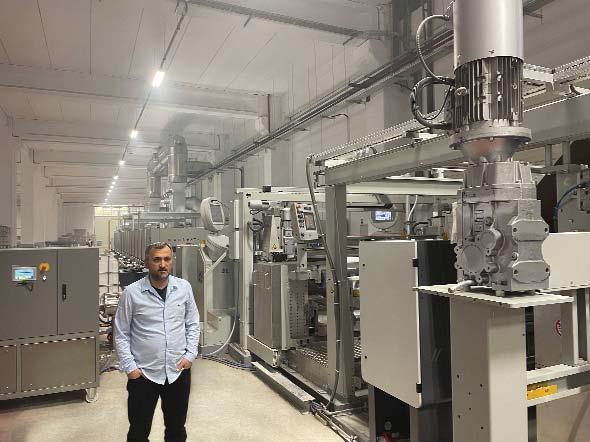
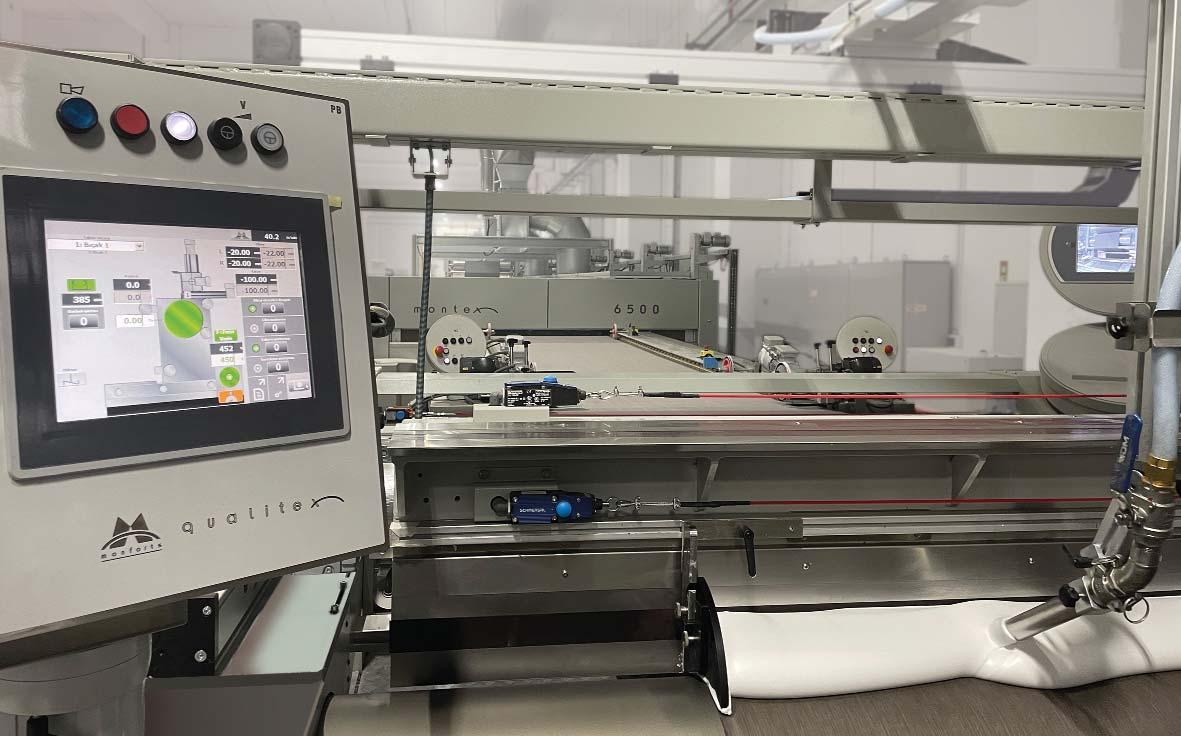

Cotton Council International Elects 2022 Officers
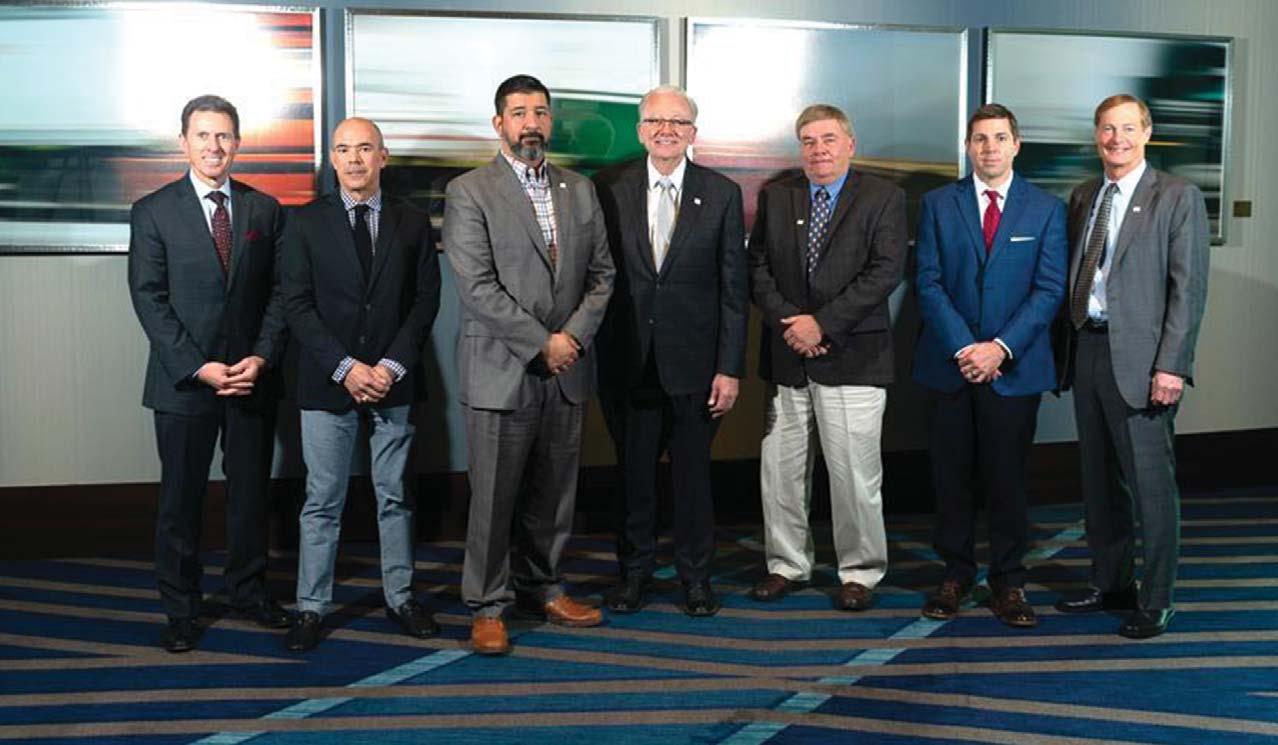
Carlos C. Garcia, a cooperative official from Lubbock, Texas, was elected as president of Cotton Council International (CCI) for 2022. CCI is the National Cotton Council’s (NCC) export promotion arm and carries out programs in more than 50 countries globally under the COTTON USA™ trademark. Garcia and other CCI officers were elected at CCI’s board meeting held as part of the NCC’s 2022 Annual Meeting that convened in Houston, Texas.
“Despite the global pandemic, CCI held 35 events – both virtually and in person – in 12 of the biggest cotton importing countries of the world in 2021,” Garcia said. “I was proud to represent the U.S. industry during a COTTON USA event last year and saw firsthand how CCI’s business-building programs resonate with our customers overseas. I will continue to communicate U.S. cotton’s competitive advantages with CCI in 2022 with a focus on the U.S. Cotton Trust Protocol® and COTTON USA SOLUTIONS™ .
Garcia is the export sales manager at Plains Cotton Cooperative Association (PCCA), a marketing cooperative owned by farmers in Texas, Oklahoma, Kansas and New Mexico dedicated to supplying sustainably-grown, high-quality cotton fiber around the world.
Originally from Van Horn, Texas, Garcia attended Texas Tech University. While pursuing his degree, he worked as a marketing intern in PCCA’s Traffic and Invoicing Department. In 2000 after earning a degree in multidisciplinary studies from Texas Tech, Garcia joined PCCA’s export department. He became the export sales manager in 2004 and has worked at PCCA for 22 years.
Garcia is past president of the Lubbock Cotton Exchange and current board member. He is also a member of the International Cotton Association and has served on the Advisory Committee on Universal Cotton Standards. A NCC Cotton Leadership Program graduate, he currently serves on the NCC’s Public Relations and International Market Development Committee.
Garcia is involved with several community organizations as well, currently serving on the Board of Managers of Lubbock County Hospital District, and as chairman in 2021. He is currently a UMC Foundation Board Member and past director as well as having served on the Slaton Independent School District Board of Trustees.
Other 2022 CCI officers elected include: chairman, Ted D. Sheely, a producer from Lemoore, California; first vice president, Steve Dyer, a merchant from Cordova, Tenn.; second vice president, J. Lee Cromley, a producer from Brooklet, Ga.; secretary, Gary Adams, also of Cordova; and assistant secretary, Bruce Atherley, from Washington, D.C. Newly elected as CCI treasurer was Carlo Bocardo, a cooperative official from Bakersfield, California.
Elected as 2022 CCI directors were Kevin Brinkley, a Lubbock, Texas cooperative official; James (Jim) Martin, a Gastonia, N.C. manufacturer; and Beau Stephenson, a Richardson, Texas merchant.
Re-elected as 2022 CCI directors were: PRODUCERS – Philip F. Edwards, III, a Smithfield, Va.; Barry W. Evans, Kress, Texas; John F. Lindamood, Tiptonville, Tenn.; Richard Gaona, Roby, Texas; Matthew R. (Matt) Hyneman, Jonesboro, Ark.; Neal Isbell, Muscle Shoals, Ala.; and Paul (Paco) Ollerton, Casa Grande, Ariz.; GINNERS – George G. LaCour, Jr., Morganza, La., and Curtis H. Stewart, Spade, Texas; MERCHANTS –John C. King, III, Memphis, Tenn.; Tim G. North, Dallas, Texas; Ernst D. (Ernie) Schroeder, Jr., Bakersfield, California; and William A. Barksdale, Cordova, Tenn.; COOPERATIVES – Frederick Barrier, Greenwood, Miss.; and Donald A. Robinson, Garner, N.C.; COTTONSEED –James (Jim) C. Massey, Harlingen, Texas; WAREHOUSEMAN – Vance C. Shoaf, Milan, Tenn.; and MANUFACTURERS –Robin Perkins, Sanford, North Carolina.
Fourcore Oil-Lubricated Technology for Sustainable Denim Production
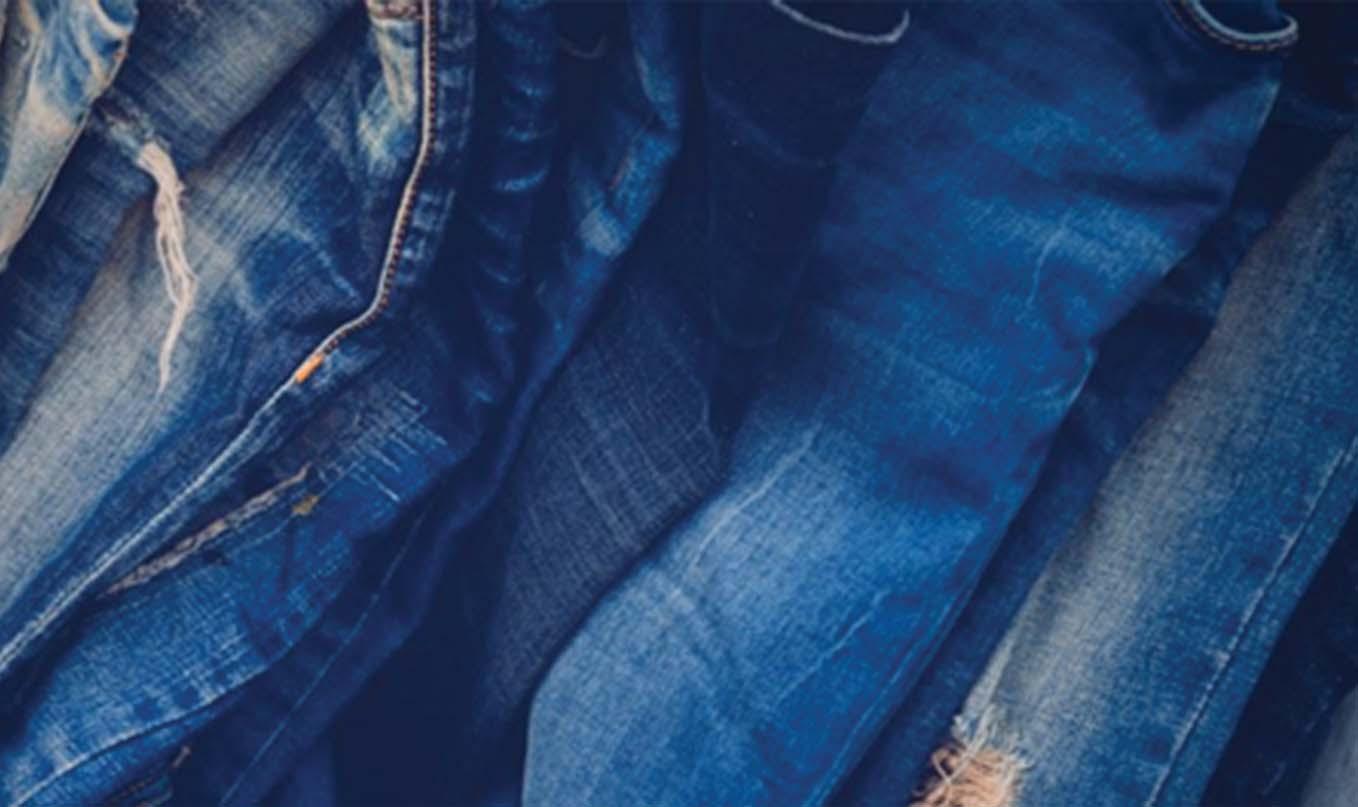
Sustainable design for Eco-Conscious textile businesses
While the history of denim is fascinating, its creation is no less captivating. Raw cotton, picked from the fields, goes through a plethora of processes and changes before being transformed into a pair of jeans or other apparel pieces. Earlier denim’s rugged, hardwearing nature drove its no-frills beginnings. From skinnies, baggies to ripped, distressed and more, denims have consistently evolved in character and style. Today’s innovative stretch fibers have propelled their flight into the fashion domain, ushering in the era of the “jegging”.
To meet the dynamic needs of constantly evolving fashion, textile manufacturers will need to improve the efficiency of their processes through energy-efficient technology. This is where CompAir reliable compressed air Fourcore oil-lubricated technology can help as it’s a necessity at nearly all levels of the process chain.
Fourcore: Reduced manufacturing materials and waste
In the case of the L200e model, compared to a conventional two stage 200 kW compressor: Reduces material used by 22 % Reduces waste by 19 %
CompAir’s new 160, 200 and 250 kW FourCore compressor has been designed with reducing waste and improving sustainability throughout the entire product lifecycle in mind. This has resulted in a system that not only runs more efficiently than alternative compressor technologies, but one that has been created with sustainability at its heart.
For example, a L160e model running 8,000 hours/year, compared to a conventional 160 kW compressor delivers reduced greenhouse emissions equivalent to that of 32 passenger cars, or space available, the opportunity to take advantage of the capabilities of twostage technology. When compared with previous single-stage compressors in this size range from CompAir, the new models are up to 8 per cent more efficient, offering a best-in-class oillubricated solution. 371,800 miles driven by a passenger car in a single year, and carbon sequestered by 181 acres of forest. While a L200e model running 8000 hours/year, compared to a conventional two-stage compressor delivers reduced greenhouse gas emissions equivalent to that of 6 passenger car, or 70,000 miles driven by a passenger car in 12 months.
The FourCore range also offers all the capabilities of a two-stage compressor, but with only the Footprint of a singlestage unit, providing businesses, who might not have previously had the onsites pace available, the opportunity to take advantage of the capabilities of twostage technology. When compared with previous single-stage compressors in this size range from CompAir, the new models are up to 8 per cent more efficient, offering a best-in-class oillubricated solution.

Shan Associates caters to the sales and marketing of textile machinery, wishes heartiest congratulations and well done to team south for arranging a successful seminar for SMIT- SANTEX RIMAR GROUP.
In the seminar, the marvelous participation of over 60 weaving units and more than 120 people from these units make it a successful event.
In the start, the CEO of Shan Associates, Rana Sohail Ahmed gave a brief account of the company’s work. Shan Associates started its journey in 1996 & has still been serving the Textile Sector with Machinery Solutions. Shan Associates is having their set-ups in three major cities of Pakistan.
Sales and marketing of textile machinery are on top in all three major textile markets. The sales workforce is very efficient & enthusiastic with an engineering background, which makes the company very progressive in the Textile market to represent many renowned companies.
Shan Associates is now offering different blends of yarns which we can directly supply from Indonesia and Thailand on demand of the customer.
They have also started collaborating with some Chinese machinery manufacturers in the last few years. Shan Associates is though a small company yet has young and enthusiastic personnel which makes it an energetic and fast excelling company in sales and marketing of their related fields: Textile Weaving, Textile garments, Alternate Energy Solution and Modern IT automatics.
He further informed that the company was modified not just to maintain, install and repair the existing access infrastructure, but also to improve it. They work to reduce inefficiency, waste, and environmental degradation. They have quite several experienced environmentalists/consultants dedicated to helping the business. They are investing in physical network assets and natural resources to reduce faults, environmental degradation.
Then Mr. Federico Businaro – Vice President Global Corporate Image presented his views related to sustainability in the textile industry. The textile industry
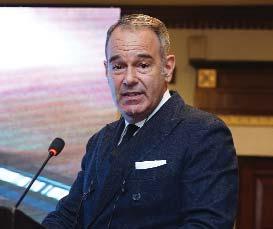
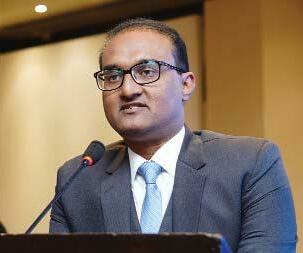
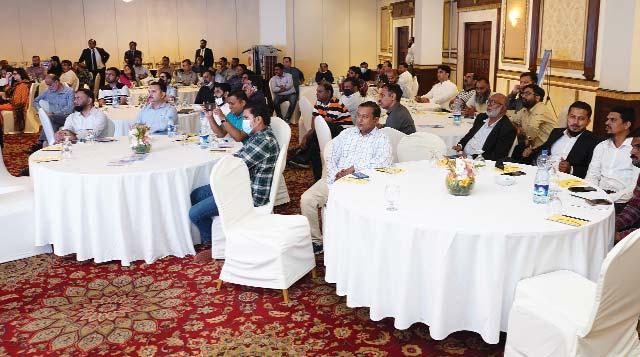

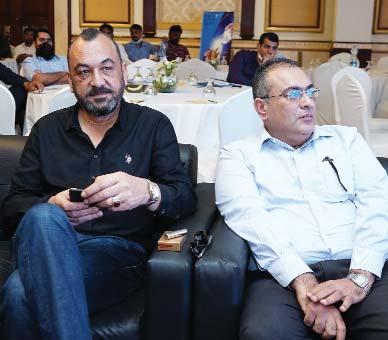

is the world’s oldest branch of consumer goods manufacturing. It is a diverse and heterogeneous sector that covers the entire production chain of transforming natural and chemical fibers (such as cotton, wool, and oil) into end-user goods, including garments, household goods, and industrial textiles.
Highlighting the importance of PV systems in textiles, he informed that the largest architecturally integrated photovoltaic system with 8420 modules for a total of 1.98 MWp. Architectural integration consists of the use of photovoltaic modules as the roofing of buildings thanks to a stainless steel structure with a European patent of Italian design. The plant has been in operation since 2011 and has approximately 2.3 GWh of energy with savings of 1200 tons of carbon dioxide per year. The machines made in Trissino are produced with solar energy.
Textiles are heavily intertwined with environmental, social, and governance issues. In the past, efforts of producers and retailers have primarily focused on improving the social aspects of textiles e.g. establishing fair working conditions, setting social standards, establishing minimum wages, ensuring occupational safety, imposing a ban on child and forced labor, etc. In his speech, he also
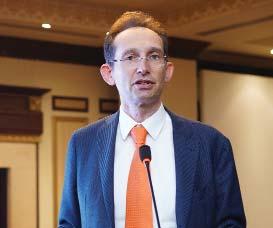
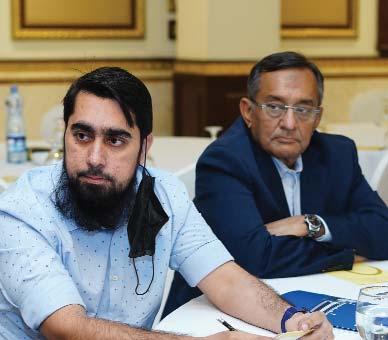
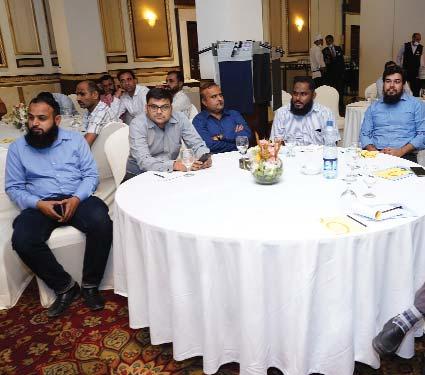
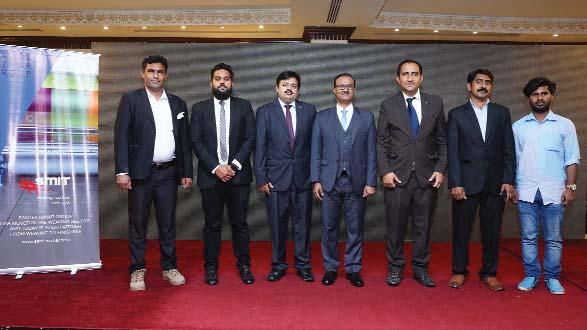
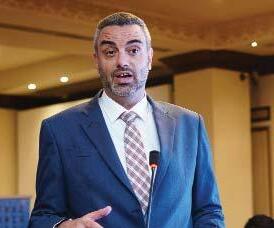
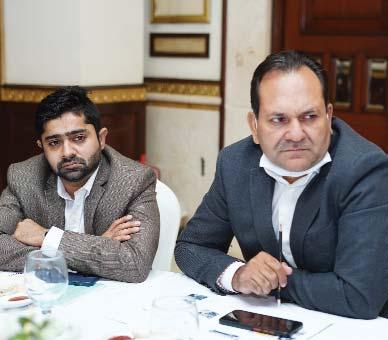
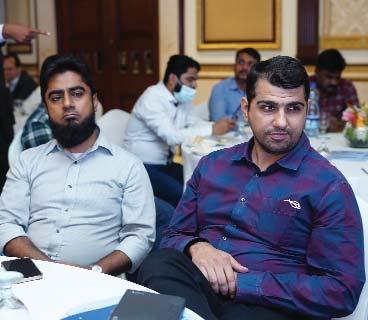

gave a brief account of some recent development in the machinery sector.
Then, Mr. Emanuele Zoppi, Sales Director SMIT briefed about the historical developments in the group. SANTEX RIMAR GROUP is present in various countries with four factories and more than 30,000 customers throughout the world to whom we offer specific solutions and services to become their reference point of excellence.
With over 50,000 installed looms and having the world’s first gripper loom the group products are 100% manufactured in Italy. Being close to local markets and employing local manpower allows us to be competitive and to offer our heritage of craftsmanship to global trade. Our know-how enables us to understand and fulfill the needs of our global customers to whom we offer not only high-quality machines but also a good and punctual after-sales service.
Mr. Giacomo Sala, head of the service and spare parts briefed about the business model and organization of the Group. He informed that in a new era, where sustainability and the production processes speed are the hardest challenges and, at the same time, the biggest opportunities to develop new business models, Santex Rimar Group is presenting new solutions for the textiles industry.
Santex Rimar Group aims to transfer the results of tireless research and improvements to the customers to give
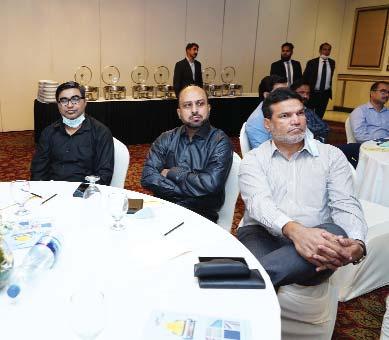
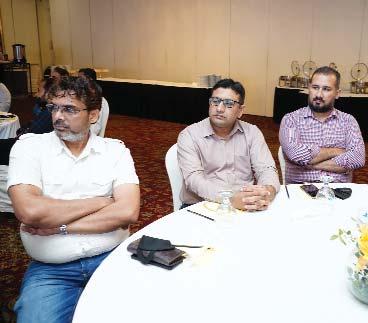
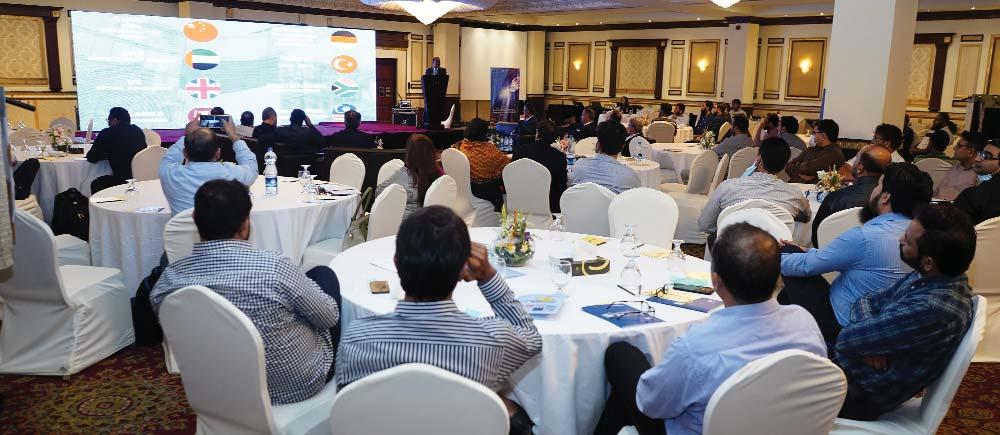



them unique competitive advantages, supporting them in the race to be sustainable and successful.
Then Mr. Giuseppe Tironi – Technical Marketing Manager discussed the technical issues in the industry. Highlighting the purposes of the group he informed that Santex Rimar Group is the market of textile finishing, technical textiles, weaving, and green technologies for water treatment and drying processes. The Group is a machine manufacturer and a technology partner for knitted, woven, and nonwoven fabrics and green solutions.
The Group has reached the perfect balance of deep knowledge, design, and high quality throughout the production process to build a strong, long-lasting, and mutually beneficial relationship with the customers. Santex Rimar Group stands for quality, reliability, and excellent automation.
Modern technology, knowledge, and many years of experience make Santex Rimar Group a provider of innovative solutions. They also care about the future. Every year they invest 4% of their annual global turnover in research and development to provide continuous technical innovation to have the best improvements available for their customers and for the people who work with us. They have funded startups and signed partnerships with Universities and big players in the chemical and electronics market.
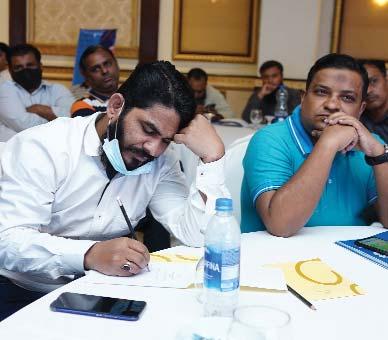
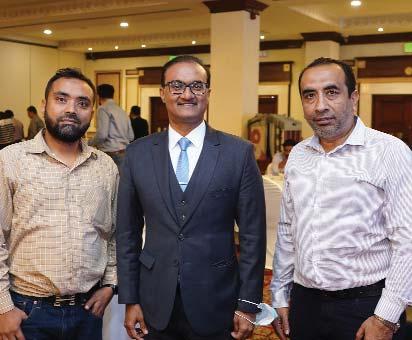
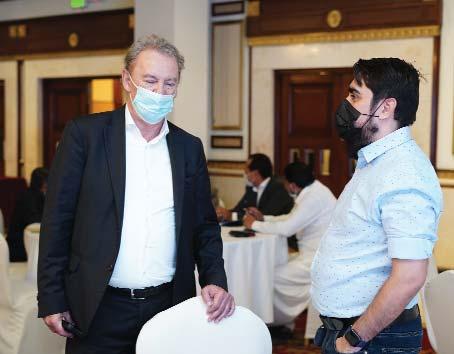
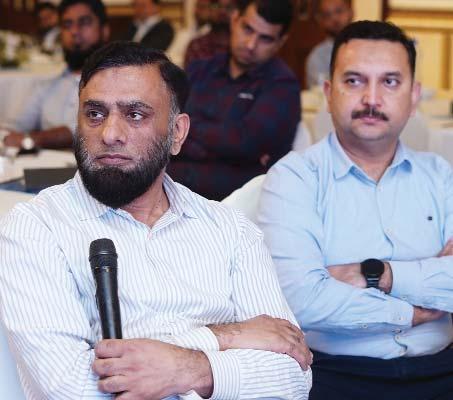
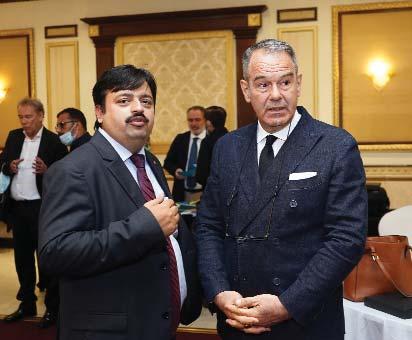
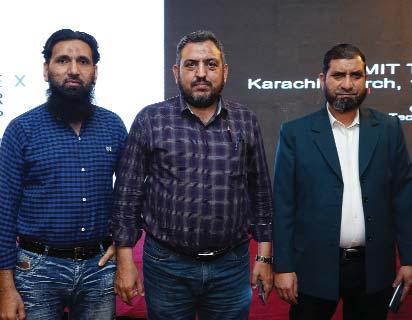
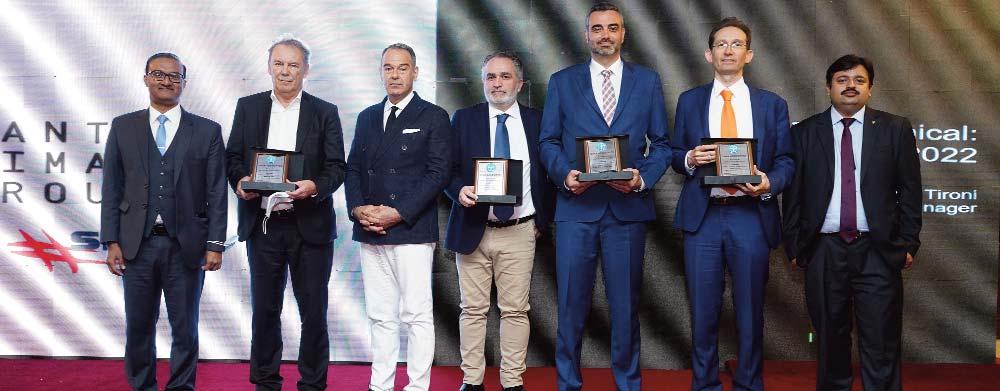
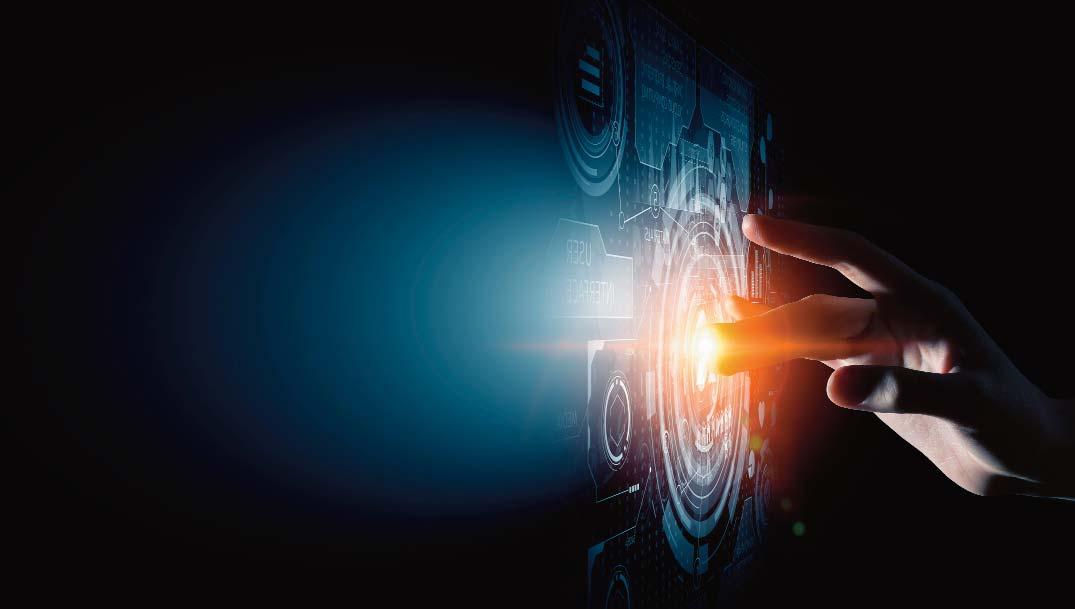
Going digital: Swiss textile machinery shows the way
Innovative technology for new business models
Members of the Swiss Textile Machinery Association introduced their innovations in the field of digitalization on the occasion of an international press conference on February 8, 2022. Digitalization is a big story in the world of business. It’s all about change, making use of technology to transform attitudes and create new opportunities to grow revenue. At its heart is innovation, with new systems and intelligent use of data. In textiles, the entire value chain is going digital, as evidenced by the commitment of Swiss Textile Machinery Association member firms. Their story was presented in six ‘chapters’ – spanning industry sectors through spinning, weaving, finishing and nonwovens. The member coompanies who gave their presentations were: Uster, Autefa, Espritech, Rieter, Jakob Müller and Saurer. The session was initiated by Cornelia Buchwalder, Secretary General, Swiss Textile Machinery who informed about the Swiss textile machinery sector and introduced the presenting member companies. Following are the exerpts of the presentations.
Uster Technologies
Presented by Michele Saig Product Manager
Better process, better workplace
Pioneering in the field of digitalization Uster embraces social responsibility along with the introduction of bold new technological innovations. That’s a commitment made by Uster, as it aims to shape future working practices in the textile industry in areas where its systems are applied. In fabric inspection, that means combining the strengths of human capabilities with the performance of Artificial Intelligence. Automatic defect classification with machine learning technology is the next leap in digitalization for fabric manufacturers, following on from automated detection of fabric faults, which is already well established in weaving and finishing mills. This will bring benefits in profitability for the manufacturer – as well as an improved working environment for their operatives, freed from repetitive tasks.
Autefa Solutions
Presented by André Imhof, CEO
See the future system today
Autefa Solutions uses the concept of digital twinning, visualizing any realworld concept of a nonwovens line to make it easier for potential customers to grasp the idea. It’s also a big help for training and servicing needs. Most of all they digitalize important parts e.g. of a baling press line with perfectly interconnecting software tools. This is an excellent method for reducing commissioning times.
Ordered bale presses reach technical readiness in the form of a digital twin, before they are commissioned in the real world. This typically halves the total time to get the line up and running. Speaking on behalf of Swiss Textile Machinery Association members, André Imhof, CEO of Autefa Solutions Switzerland AG, says:
“Making digitalization our friend opens doors for business model innovations, which is essential for our industry competitiveness. The approach is to digitalize everything that can be digitalized. We won’t stop.”
It’s also quite certain that there will be many more chapters of the digitalization story invented in Switzerland.
EspriTech
Presented byPhilipp Rueedi,CFO
Cost savings and more
The process of digitalization in the textile industry today is continuous –faster in some segments than others – but noticeable everywhere. Automation is promising in many areas of finishing and making-up, where initial investments are being made. An example is folding of finished goods, previously a slow manual operation. Now, high-performance automatic folding machines from Swiss company Espritech deliver the potential for cost savings, unlocking new options for positive change at this most laborintensive stage of production. For manufacturers in low-cost areas, the benefit results from its volume and is a simple financial one. In higher-cost segments, the application of this technology can be part of a completely new business model, taking production closer to the end customer.
RIETER
Presented by Selwyn Von Grunigen Head of Automation & Digital
Making the most of it
Rieter takes advantage of latest digital technology to offer customers a unique experience. Their digital spinning suite helps spinners overcome their daily challenges and manage costs and efficiency more effectively. This all-in-one mill management system connects all the machinery, giving quick access to the right information and a holistic view, from bale to yarn.
Users profit from full transparency, and are presented with recommendations based on long-standing experience and know-how. This is digitalization at its most practical, applied to allow spinners to make the most of their installed machinery.
Jakob Muller
Presented by Juan Carlos Product Manager Labels
Information, flexible and fast
Access to data is critical in the digitalized world of textiles. It must be flexible, fast and secure, and available to all levels of the company – worldwide. Jakob Muller serves the narrow fabrics industry ideally with a digitalization portal, perfectly developed to provide essential production information.
The portal is a browser-based production data acquisition system, with direct access to the machine controls. The system offers unique data monitoring and communication on a global framework. Digitized weave rooms present information 24/7 on desktops at the customer’s plant, as well as on tablets and smartphones remotely.
SAURER
Presented by Pia Terasa Marketing and Marketing Intelligence
Production, service, training – digital everything
As a solutions provider, Saurer puts digitalization at the core of business, integral to its technology offering to customers. Some latest examples include self-optimization of spinning machines, and a fully automated transport of cylindrical or conical cross-wound packages.
These are automatically stored in an internal buffer system, for later feeding to subsequent processes. Of course aftersales service is also digital: the e-shop and machine information hub, together with the web-based training centre, ensure that knowledge is transferred to customers – turning employees into experts.
Swiss Textile Machinery Association
The Swiss Textile Machinery Association is the representative body for Switzerland’s producers of textile equipment, systems and services. Founded in 1940 currently 45 companies are affiliated, including manufacturers of machines and components, and service providers, for the textile industry. The companies offer solutions covering the entire textile value chain, from spinning to weaving, knitting, finishing, embroidery and quality control.
The Swiss Textile Machinery Association is part of Swissmem – the leading association for SMEs and large companies in Switzerland's mechanical and electrical engineering (MEM) industries and related technology-oriented sectors.
Swissmem provides member companies in industry sectors with a forum for information exchange and marketing activities. Swiss Textile Machinery is the oldest of the 25 industry sectors within Swissmem.
The Swiss Textile Machinery Association is a member of the European textile industry committee CEMATEX (Le Comité Européen des Constructeurs de Machines Textiles), which owns ITMA, the world’s largest international textile machinery exhibition.
The mission of the association is to support and promote the Swiss textile machinery industry. This encompasses a range of activities, such as: Organisation of symposia in important textile markets.
Swiss Pavilions at exhibitions and events where a prominent Swiss presence is beneficial.
Innovation workshops, dealing with topics such as additive manufacturing or digitalisation.
Ernesto Maurer, President
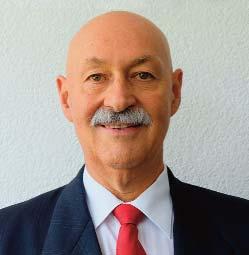
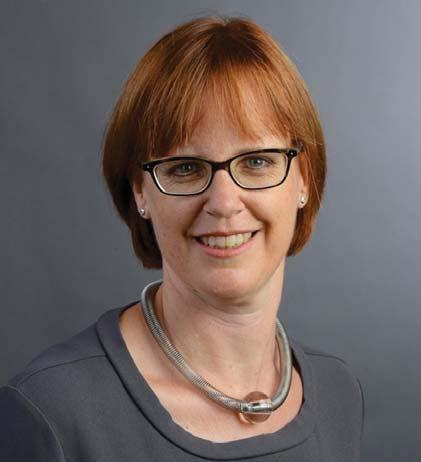
Q. What are the new developments and innovations introduced by the Swiss Textile Machinery in 2022?
The fields of efficiency, sustainability and digitalisation remain some of the fields in which further improvements and innovations will also take place in 2022. Personally, I am very much looking forward to ITMA 2023 in Milan. This is always a great showcase to see the innovations and developments in the textile and textile machinery world.
Q. Can you see a shift in the Swiss Machinery to support sustainability and green environment demands?
Sustainability is a big and very important topic. It has been for years, but now it is even more important due to the
Exports of Swiss Textile Machinery (Jan-Dec 2021 vs Jan-Dec 2020)
Country Ran k Exports Mio. CHF Exports ± CHF%
Exports Share CHF World 599.6 17.4% 100.0%
China 1 115.1 49.7% 19.2%
Germany 2 59.3 8.5% 9.9% Turkey 3 50.6 -4.5% 8.4% India 4 43.4 50.2% 7.2%
USA 5 42.3 6.2% 7.1%
Italy 6 29.9 65.9% 5.0% Pakistan 7 27.5 22.9% 4.6%
Japan 8 21.0 22.7% 3.5% Czech Rep 9 20.5 16.5% 3.4% Bangladesh 10 19.4 20.2% 3.2%
Source: Swissmem.
new EU strategy for sustainable textiles. As an association, we have also taken on this topic and are currently developing an individual programme for our member companies. Of course, some member companies are already very advanced in this topic, but others will certainly be able to benefit.
Q. How did the COVID affect the sales of Swiss Machinery and could you see situation getting better in 2022?
Looking back to 2021, most of our members reported a very strong year. The business climate has recovered faster and stronger than could be expected. Despite this positive and rapid recovery, there were some challenges to overcome. The still complicated and highly expensive transports, the scarcity and long delivery times of raw materials and the complexity of travel planning. For Switzerland, there was also the additional challenge of the again strengthening Swiss currency, mainly compared to the Euro. As it was a very strong year, both the capacity utilisation rate and the productivity rate developed positively. The view into 2022 will be somewhat more neutral. It remains to be seen how current geopolitical developments will affect consumption and investment. In addition, the aforementioned challenges will continue to exist.
Q. Industry 4.0 / digitalization how it is reflected on Swiss Machinery manufacturing?
Industry 4.0 or Industry 2025 as we call it in Switzerland offers various possibilities, be it in product or process optimization or in the development of completely new business models. Our member companies use these possibilities to generate maximum customer benefit. The pandemic in particular has shown us how important digitalisation can be. Customers and suppliers who can offer for example remote service were certainly in an advantageous situation.
Q. What is the biggest market/ country for sales of Swiss Machinery and what is Pakistan’s position?
The top five export markets in 2021 were China, Germany, Turkey, India and the USA. In 2021, the export volume from Switzerland increased by 17.4% to 599.6 million Swiss francs. However, this only shows a part of the Swiss textile machinery production. Almost all our members have production facilities in different countries such as China and India. These figures are not included in the Swiss export statistics.
Pakistan was the 7th most important market for Swiss textile machinery accounting for 4.6 of total exports. Swiss textile machinery leaders have been present in this important market for more than 50 years.
Table 1: Exports of Swiss Textile Machinery
Year Exports (CHF million) Exports ±(CHF %)
2015 1,064.3 -20.6% 2016 909.8 -14.5% 2017 880.7 -3.2% 2018 821.7 -6.7% 2019 694.0 -15.5% 2020 510.6 -26.4% 2021 599.6 17%
Source: Swissmem.
by Prof. Dr. Noor Ahmed Memon, Dadabhoy Institute of Higher Education / Associate Editor, Pakistan Textile Journal.
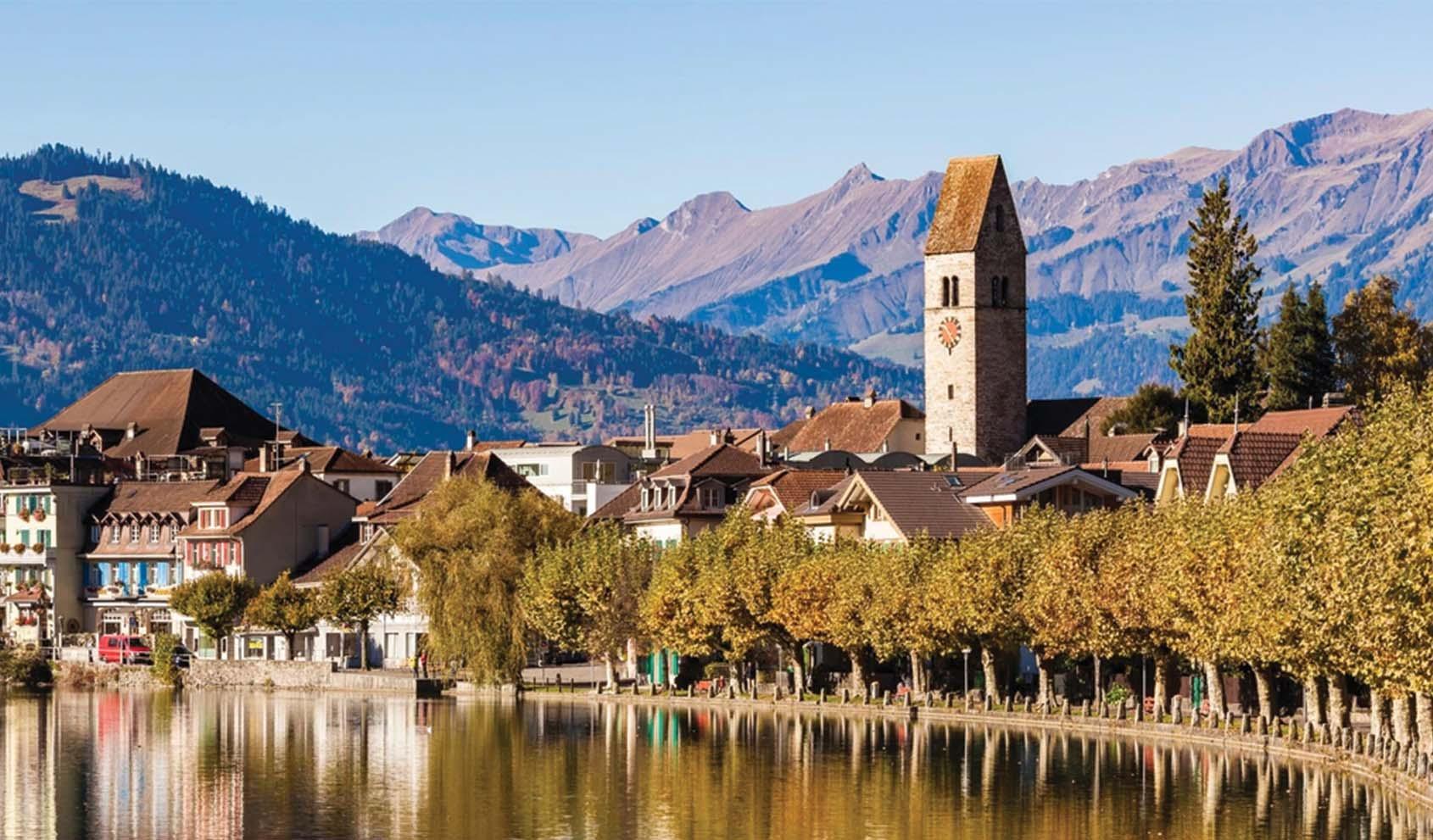
Table 1: Pak Swiss Trade Value: US$ Million Year Exports Imports Bal of Trade
Switzerland's highly developed economy is large because of its technologically progressive industrial sector, which is differentiated by highly specialized, internationally experienced, and flexible small and medium-sized companies.
Switzerland and Pakistan have good, long-standing relations. The two countries have signed a range of economic agreements that have helped to develop bilateral trade. There are numerous bilateral agreements between Switzerland and Pakistan covering a range of areas including investment protection, debt consolidation, aviation, double taxation and disaster relief. Switzerland also engages in regular political dialogue with Pakistan.
The Swiss Business Council had also been set up for providing guidance to Pakistani businessmen to enhance trade volume between the two counties.
Over the years this level of cooperation has increased significantly which is the reason why Switzerland has been among the top five largest investors.
The Swiss multinational companies that operate in Pakistan, do not just market their world class products and services, but also create employment opportunities in the country. There are 21 Swiss companies in Pakistan employing 15,000 people. Major Swiss companies that have invested in Pakistan include ABB, Archroma, Clariant, Sika, Gate Gourmet, Nestle and Novartis.
Pak-Swiss Trade
Pakistan's trade relations with Switzerland have been quite happy. The trade between Pakistan and Switzerland increased, but exports remained less than the imports. Over the past five years, trade between Pakistan and Switzerland has increased, but the rise in imports has been greater than the exports. The total trade volume between Pakistan and Switzerland in 2020-21 was over US$ 2.02 billion with the balance of trade favouring Switzerland.
In 2020-21, Swiss exports to Pakistan amounted to US$ 108 million and consisted mainly of machinery, chemical and pharmaceutical products and watches. Swiss imports from Pakistan mainly textiles and agricultural products amounted to US$ 752 million. Pak- Swiss Trade for the last five years are given in
Table-1.
Import of textile machinery from Switzerland to Pakistan increased from CHF 22.4 million in 2020 to CHF 42 million in 2021, thus showing an decrease of 22%. Imports of textile machinery (Major items) from Switzerland to Pakistan in terms of rupees are given in
Table 2.
Year Exports Mio. EUR Exports ±EUR%
2016 24.4 -34.5% 2017 35.5 +45.5% 2018 26.8 -24.5% 2019 38.5 +44% 2020 22.4 -42% 2021 27.5 -22.9
Source: Swissmem.
2016-17 57 850 -793 2017-18 128 1,084 -956 2018-19 95 926 -831 2019-20 98 649 -551 2020-21 108 752 -644
Source: State Bank of Pakistan.
References
Pakistan Bureau of Statistics. Swissmem. State Bank of Pakistan-Annual Reports.

“Archroma teams delivered the best ever all around performance inspite of significant challenges like global & local Covid lock-
down.” Mujtaba Rahim, President and CEO, Archroma Pakistan Limited.
Archroma is a Swiss multinational company with a heritage of 125 years taking its lineage from Sandoz way back in 1886 when it was formed in Basel as Kern & Sandoz to manufacture dyes. In 1995 Clariant came into existence as a result of the global spin of Sandoz specialty chemicals business came under its umbrella. In 1997 Clariant acquired the specialty chemical business of Hoechst. 2013 was the year of a global change as SK Capitals acquired the textile specialty chemical paper and emulsion business from Clariant and formed this new company Archroma. Shortly thereafter in 2015, Archroma acquired the global textile chemical business of BASF consolidating the portfolio to serve our valued partners with a full range of textiles specialties. Moving ahead in 2018 Archroma strengthened its product line
by completing the acquisition of a technical textiles business. In 2019 the optical brightening business was acquired from BASF India.
Today Archroma is a global diversified provider of specialty chemicals serving brand and performance textiles, packaging, paper coating, adhesives, and sealant markets. They operate with integrated customer-focused platforms. Specialized performance and color solutions in over 100 countries. Archroma works with 3000 employees in 35 countries and has 26 production sites. We touch and color people’s lives every day everywhere. This gives us a huge responsibility. It is our passion to deliver leading innovative solutions and enhance people’s lives and respect our planet. That is why at Arcrhoma we operate alongside the principle of the Archroma Way to a sustainable world safe, efficient, enhanced it is our nature. We are growing business by leveraging local entrepreneurship and our global organization in a collaborative way. We enable our customers to win their market. We push limits to outperform and we never give up. We deliver specialized performance and color solutions to meet our customers’ needs and achieve a fair value for our shareholders and stakeholders in return.
Archroma is the market leader operating with three main businesses committed to challenging the status quo in the deep belief that it can make its industry sustainable. An approach reflected in our innovations, excellent quality, standards, high service level, and cost-efficiency. I would now like to explain about our 3 main business units.
The biggest brands and textile specialty from fiber to finish Archroma’s brand and performance textiles specialties business plats a key role throughout the entire textile supply chain with special chemical for pre-treatment dying, printing and finishing of textiles our system solutions enhances the properties of Apparel and other textile's in application as diversify as high fashion home textile special technical textile, second packaging and paper specialties Archroma packaging and paper specialty provide expertise in the management of whiteness, colorations special coating and strength of all kinds of papers by combining our focus product range with the application service of our paper experts around the globe we enhance both the optical and functional properties of packaging paper and tissues, third coating adhesive and sealants from paints adhesive and construction to the textile and paper industries Archroma’s coating adhesives for a wide range of application literally thousands of satisfied customers have been a witnessed to the outstanding success of Archroma emulsions since it first painted was obtained in 1912.
The fast pace journey of Archroma in Pakistan has been remarkable, Archroma Pakistan is a subsidiary of Archroma LLC Switzerland, and is a public limited company on the stock exchange for the past 18 years we are amongst the top 25 companies on the stock exchange. Pakistan has the distinction of having two production sites one in Jamshoro and the other at Landhi Karachi operating on International standards for 5 decades we possess quality certification in our offices our green office is certified by WWF Pakistan. Jamshoro is one of the largest sites within the Archroma world. Archroma center of excellence located at Korangi Karachi is a state of Art R&D laboratory where research is conducted. Product stewardship and technical service are provided to the textile industry to meet their regulatory

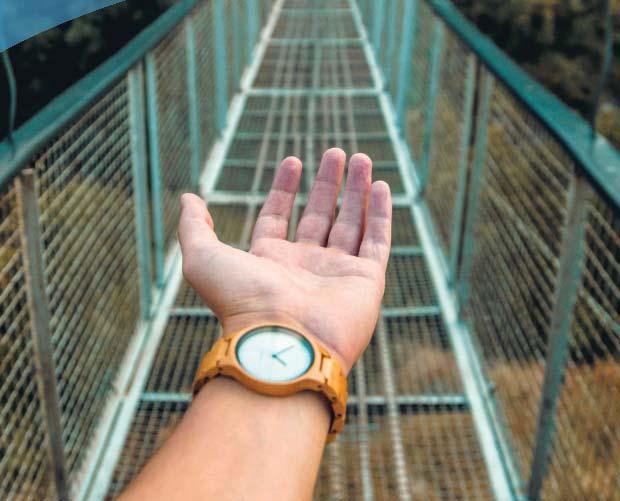
environment of exports to countries such as reach in Europe our R&D facilities have developed products that are globally patented and hence have received high recognition around the world.
These research products and patents millions of dollars for Pakistan. Alongside our RND Archroma Pakistan has a flagship education assistance program where they provide six weeks of internship to textile and chemistry students from academic institutions, we have trained more than 7 thousand students to date from various universities 25% of our interns are female students and entrepreneurs. Archroma Pakistan has built a strong academic linkage with academia and works on different projects for the development of the textile industry.
Memorandum of understanding has been signed with all leading academic institutions namely Textile Institute of Pakistan Karachi, Mehran university of engineering and technology Jamshoro, University of engineering and technology Lahore, National textile university Faisalabad, NED University of engineering and technology Karachi, and the latest one with Dice textile USA, distinguished innovations collaboration and entrepreneurship.
Another important milestone in our initiative on water conservation is our sustainable fluent treatment plant at Jamshoro production site was planned designed and by our engineers in Pakistan and is based on zero discharge, this set plant was inaugurated in December 2013 in the presence of high profile dignitaries and stakeholders it is the labor and passion of our dedicated team professionals, set plant is spread over an area 25 acres consisting of flocculation, equalization surface aeration, clarification, ultrafiltration and reverse osmosis to healed colorless reusable water.
Approximately 11 thousand clean drinking water is supplied to the neighboring communities free of cost as Archroma's commitment to corporate social responsibility. In this context, we are jointly working with WWF Pakistan on water-saving projects within the textile or leather industry. Due to our commitment to make to take on innovation challenges, Archroma developed an alternative system to produce aniline free types of denim by innovating aniline free indigo denisol pure 30 liquid removing hazardous impurity aniline from the denim supply chain, we aim to protect workers who produce denim, consumers who wear denim and the environment with cleaner waterways. Archroma Pakistan has a chief prestigious award in recognition of its services and management, good manufacturing practices, environmental protection, and safety, we aim to continuously raise our performance bar to bring prosperity to our
employees, associates, and Partners.
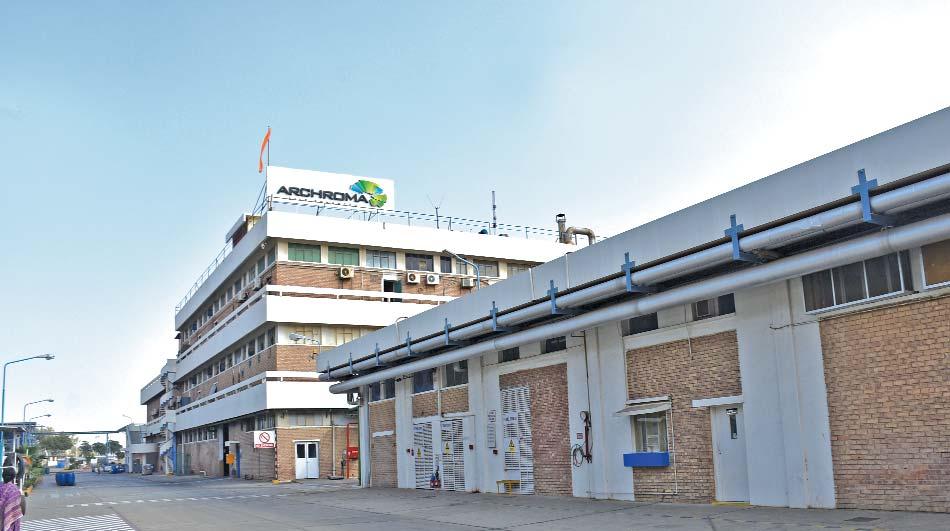
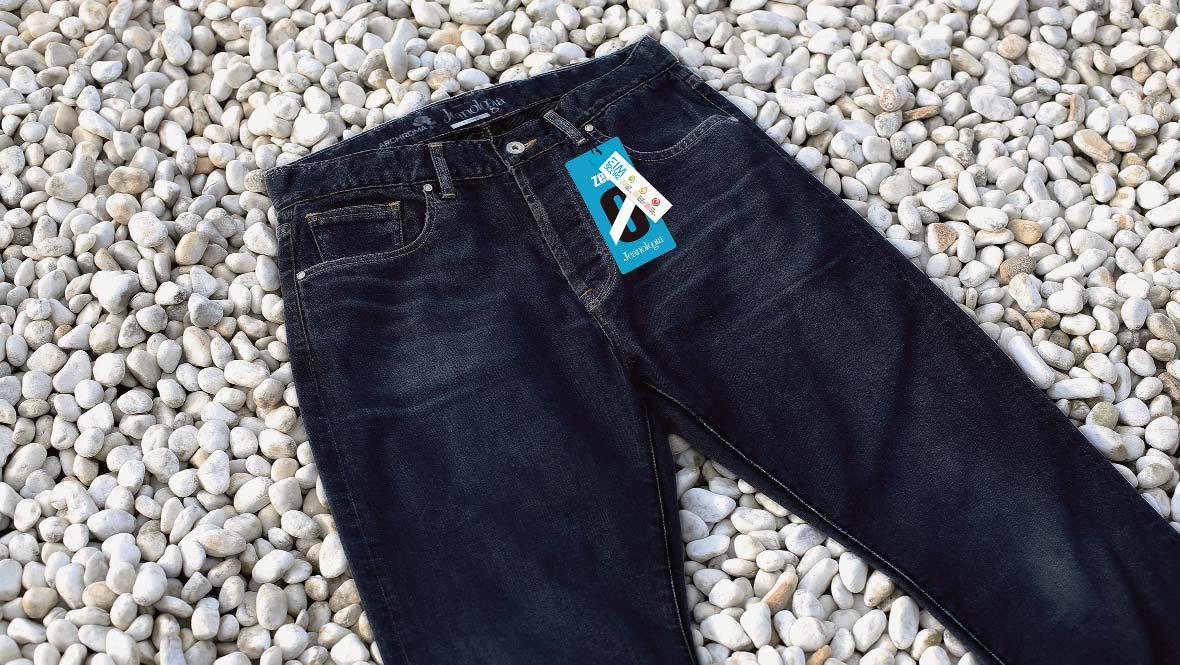
From the field to the plant: Shrubs of Indigofera US-grown by Stony Creek Colors (photo: Stony Creek Colors)

Archroma and Stony Creek Colors to enter strategic partnership to produce Indigold™ highperformance plant-based pre-reduced indigo at scale
Pratteln, Switzerland and Springfield, Tennessee, USA
Archroma, a global leader in specialty chemicals towards sustainable solutions, and Stony Creek Colors (“Stony Creek”), a trusted manufacturer of traceable natural indigo dyes, today announced that they have entered a strategic partnership to produce and bring to the market Stony Creek’s IndiGold™ high-performance plant-based pre-reduced indigo at scale.
Stony Creek extracts its dye from proprietary Indigofera plant varieties grown in partnership with family farms as a regenerative rotational crop.
Stony Creek Colors developed the new IndiGold™ concept as the world’s first pre-reduced natural indigo dye, which was then developed with Archroma to offer the first ever plant-based alternative to synthetic pre-reduced indigo. The dyestuff will be sold as a 20% concentration in a soluble liquid form that displays similar performance to comparable synthetic indigo products available on the market.
Stony Creek Colors evolved into an innovative leader in plant-based indigo due to its complete development of an
improved agricultural value chain, from seed breeding and production to biomass harvest and extraction. The company has been selling its US grown indigo to denim mills since 2015.
From the field to the plant: Shrubs of Indigofera US-grown by Stony Creek Colors (photo: Stony Creek Colors)
The pre-reduced plant-based indigo partnership took root in 2020 when Stony Creek was looking to work with likeminded partners to produce the new dyestuff at scale. Archroma emerged as the ideal partner as the company is well known for its expertise in indigo manufacturing and application, as well as for its commitment to transform the denim industry towards creating better blue jeans.
Archroma continuously introduces eco-advanced indigo innovation such as the first ever aniline-free* synthetic prereduced indigo or the Archroma x CleanKore technology for aniline-free* potassium permanganate-free* spray with no laser booster needed for white abrasion.
Archroma immediately offered to support the idea of Stony Creek Colors with extensive pilot scale manufacturing trials and engaged with its network of denim machinery manufacturers to test the first samples in industrial conditions. The trials showed excellent coloration and the typical indigo wash down, as with synthetic indigo. Archroma will produce the first batches of IndiGold™ in Salvatierra, Mexico, and has other locations where the product could be made. The company will support Stony Creek Colors through its manufacturing and logistics capabilities, and its expertise in denim dyeing with customers using pre-reduced indigo.
From the field to the plant: Archroma’s indigo plant in Salvatierra, Mexico (Photo: Archroma)
While this development was underway, the global innovation platform Fashion for Good selected Stony Creek Colors as an innovator in its global Innovation Program. The program connects brands with innovators to work together to test, validate and ultimately scale disruptive innovations in the fashion industry to drive positive impact. Through the program, Fashion for Good facilitated a collaboration between brand partner Levi Strauss & Co. and Stony Creek Colors which was announced in December 2021. The partners will pilot the use of IndiGold™ in denim mills at scale, with the goal of unlocking key learnings around shade application and other efficiencies of this new dyestuff.
“For years our consistent powder and paste products have been able to fill a void in the marketplace for denim mills needing verifiable plant-based indigo. We, along with many in the industry, see IndiGold™ as the holy grail for indigo dyeing and are ecstatic to now be bringing it to life with such a reputable partner as Archroma. The coupling of our two technologies allows us to fulfill the ultimate desire from our customers for an easy-to-use, pre-reduced liquid formulation that stems from a 100% plant-based supply”, said Sarah Bellos, CEO and Founder of Stony Creek Colors
“I am very proud that Archroma supports Stony Creek’s project. We shared the same vision that plant-based prereduced indigo can be scaled up and color the nature-friendly collections that denim brands & retailers have been dreaming of, and we are pleased to help bring it to the market,” comments Heike van de Kerkhof, CEO of Archroma.
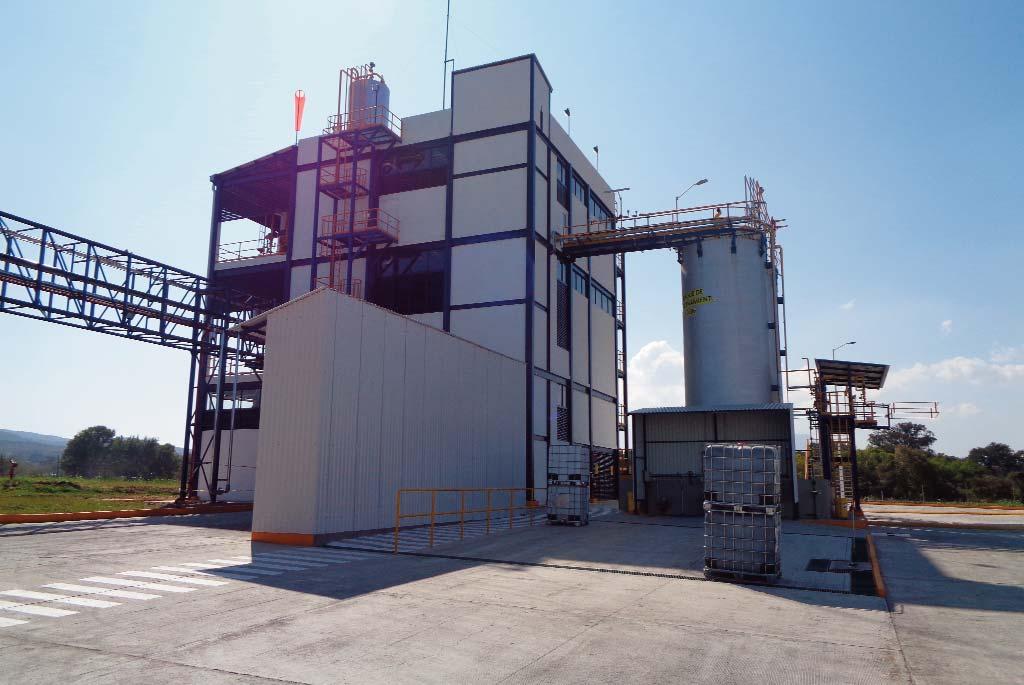

Celebrating highest ever sales and a decade of consecutively winning Management Association of Pakistan’s Corporate Excellence Award
Mr. Mujtaba Rahim & Mr. Irfan Chawala receiving the Corporate Excellency Award from the Honourable Chief Guest, Mr. Shabbar Zaidi
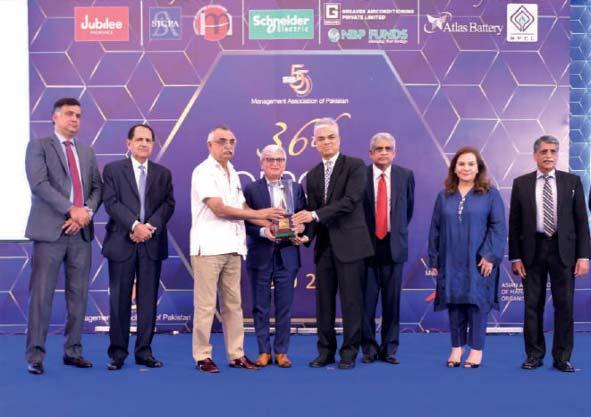
Top 25 Companies Award
Pakistan Stock Exchange ranked Archroma on 5th position for the year 2019. A remarkable feat achieved for the 18th time as Archroma wins positions amongst Top 25 companies at the Stock Exchange. Our achievement is a recognition of complying successfully with the highest standards of financial & operational excellence and crossing annually raised bars set by the Stock Exchange. The winning criteria is based on capital efficiency, good corporate governance, listing regulations, transparency and timely distribution of profits.
Decade of Corporate Excellence
Archroma completed a decade of consecutively winning Corporate Excellence Award – Chemical Sector by Management Association of Pakistan on 28th October 2021. The Award is a recognition of Good Management Practices which include a vast section of policies and procedures in finance, compliance, human resources and corporate social responsibility.
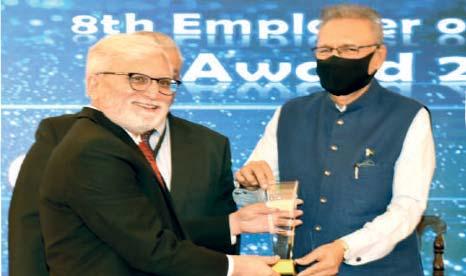
Living The Global Compact Best Practices Sustainability Award
Archroma is amongst the 20 founding signatories of Global Compact rolled out to the corporate world in December 2005 by Employers Federation of Pakistan. Its ten complying principles relate to Human rights, Labor, Environment and Anti-Corruption. Within Archroma, we observe all principles with full sanctity and discipline. We won 3rd position in a nationwide competition on best practices of UN SDGs & Global Compact principles on 30th March 2021 at Karachi. Mr. Irfan Chawala received the award from Mr. Zaki Ahmed Khan, Vice President, Employers Federation of Pakistan.
Employer of the Year Award
At the 8th contest, Archroma Pakistan once again emerged as winner of Diamond Award for the year 2020 in multinational category. The President of Pakistan, Dr. Arif Alvi conferred this prestigious award to Mr. Mujtaba Rahim on 12th March 2021 at Karachi in presence of a large corporate gathering. Archroma enjoys the unique distinction of winning Employer of the Year and Chief Executive of the Year Award three time in a row from 2015 to 2017.
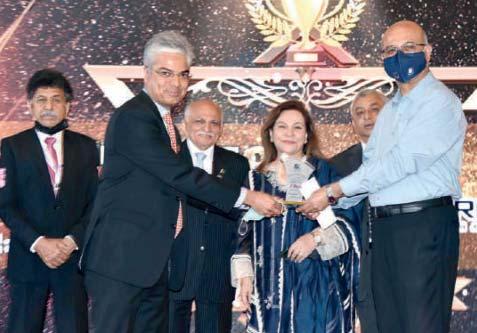
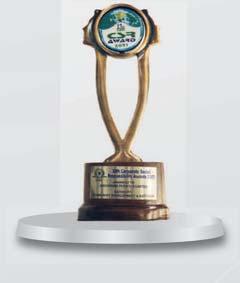
Corporate Social Responsibility Award
Archroma Pakistan won CSR Award in the area of Community Service in recognition of its many actions aimed at saving water, providing it to the neighbouring community and contribution to enhance education through internships at Archroma Center of Excellence. The national contest was organized by National Forum for Environment & Health. Mr. Ihtasham Elahi received the award from Governor of Punjab, Chaudhry Mohammad Sarwar on 25 February 2021 at Islamabad.
Tree Plantation Award
Archroma promotes tree plantation in schools, civil administration offices and neighbourhood. At our production sites in Jamshoro and Landhi, it is our motto to plant fruit trees with the resultant that mangoes, guavas, cheeku, dates, grapefruit, papayas and coconuts are available in abundance in every season. We utilize designated open spaces for growing vegetables. Archroma contributes to cleaner environment by converting organic solid waste into compost. So far 9,000 kgs of organic compost has been made to enrich the soil. Composting is an initiative of our team and is done inhouse using organic kitchen and garden waste, paper and saw dust. In recognition of our efforts to upscale the environment, National Forum for Environment & Health presented us Tree Plantation Award for the third year on 16 September 2021 at Karachi.
Environment Excellence Award
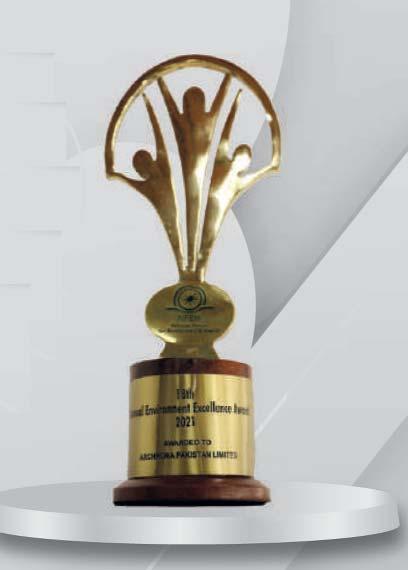
Once again Archroma came out as winner of this prestigious award. The nationwide contest was organized by National Forum for Environment & Health. Detailed inspection of Jamshoro and Landhi are held, the assessments revealed that both sites were fully compliant of all environmental standards, regulations and guidelines.
Green Offices
Archroma is amongst the forerunners to adopt “Green Office” initiatives of WWF effective 2016. It enables us to take concrete steps in environmental protection through internal management practices e.g. saving in water usage, utilities – electricity, gas and fuel and waste management.
Archroma Center of Excellence Labs are designed in such a manner that we take maximum benefit of daylight, here no bulbs are used. Water lines from taps are laid
towards green spaces where it is utilized for plantation.

Global Recognitions Archroma Sustainability Awards – 2021
In May 2021, Archroma announced a global contest on Sustainability inviting all countries wherein Archroma is operating to showcase their projects. Archroma employees all over the world voted to select projects of their choice in seven categories. Pakistan came out with a unique winning streak @ 100% –two of its project received highest votes from all over the world on 22nd September 2021:
Safety & Health category
It’s our Nature - ACCIDENT FREE ARCHROMA PAKISTAN
Sustainable Partnership category
Future R US – Archroma Harvesting New Minds Towards Sustainable Norms
Another accolade included Pakistan IT team
Excellence Improvement category
It Services Optimization Towards Cost Efficiency, User Satisfaction and Digitalization.
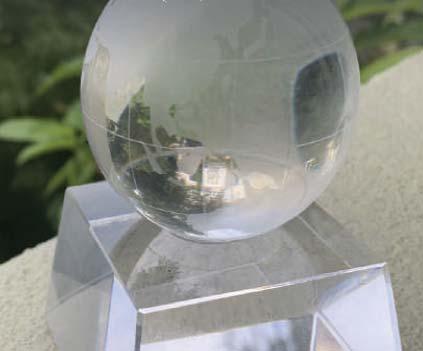


Mr. Mujtaba Rahim and Dr. Sarosh Hashmat Lodhi with MoU document
Customary to our past practices, Archroma started the year 2021 by signing a MoU with NED University of Engineering & Technology, Karachi on 1st January 2021. The signing was done at respective offices of the Vice Chancellor, Dr. Sarosh Hashmat Lodhi and Mr. Mujtaba Rahim. Archroma collaborates with NED University specially the Textile Faculty on Interships at Archroma Center of Excellence and research projects. Developmental projects are in pipeline leading to Industrial.
Aditya Arunkumar Biyani, Managing Director, is pleased with the energyefficient blowroom at Damodar.

How Customers Cut Energy Costs with VARIOline ECOrized
Rieter’s customers Damodar (India) and Karteks Tekstil (Turkey) integrated the intelligent solution VARIOline ECOrized into their blowroom lines and now benefit from lower energy consumption, smooth operations, and improved indoor air quality. The ECOrized option controls all fans dynamically and ensures that the fibers pass through each of the blowroom machines with excellent energy efficiency.
Damodar was the first customer in India to utilize Rieter’s high production blowroom VARIOline with the new precleaner UNlclean B 15. In another first for lndia, the intelligent solution VARIOline ECOrized which is managed via the control system UNlcontrol was integrated into the blowroom. VARIOline ECOrized automatically adjusts the air speed to the material quantity (Fig. 1), the process sequence, and when changing assortments. As a result, Damodar’s energy consumption has decreased by 4.5 kW/h in the pneumatic fiber transport and an additional 4.5 kW/h in the filter house.
Maximum production at a blowroom line in India
Damodar’s new blowroom VARIOline ECOrized is one of the most productive blowrooms in India. “If the Rieter blowroom is producing at 1 500 kg/h, it only requires one UNIfloc A 12 and one UNIclean B 15. In addition to this, the constantly measured and automatically adjusted airflow makes it the most energy-efficient blowroom”, states Aditya Arunkumar Biyani, Managing Director at Damodar Mills Ltd. (Fig. 2). Furthermore, no operator is needed to adjust the air balance manually. The system also facilitates predictive maintenance and helps to avoid interruptions in production.
Cleaner air improves working conditions
VARIOline ECOrized has considerably reduced the dust in the blowroom thanks to the closed exhaust air pipes to the filter station. This improves the working conditions in the mill significantly. Damodar also benefits from improved yarn quality: Compared to competitor’s spinning mills, the Rieter blowroom provides excellent cleaning performance with a much-less lint loss which is also evident in the yarn results. Based on test results, Damodar is confident that the blowroom will produce just as reliably at a much higher production rate.
Karteks Tekstil saves USD 19600 per year in energy costs thanks to VARIOline ECOrized.
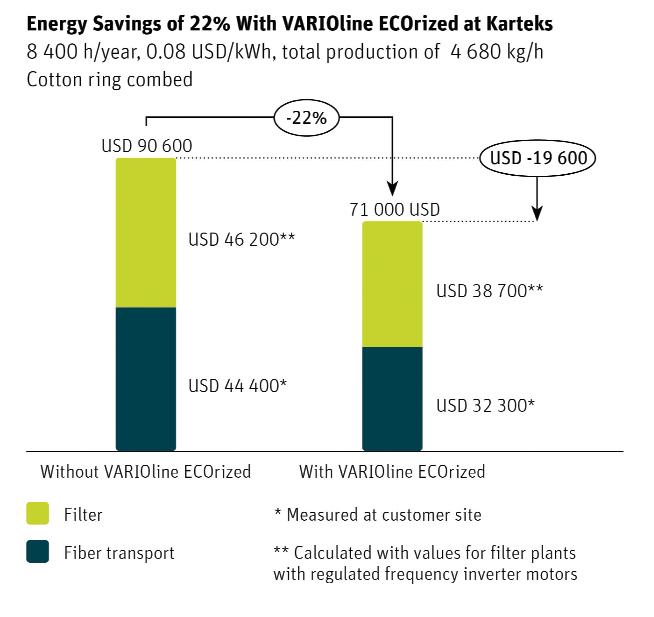
VARIOline ECOrized controls all fans needed for the pneumatic fiber transport in the blowroom dynamically.

Energy savings of USD 19 600 per year
VARIOline ECOrized also greatly reduced energy consumption at Karteks Tekstil in Turkey. The customer invested in three new blowroom lines VARIOline, including the intelligent solution VARIOline ECOrized. To determine the energy savings made thanks to the ECOrized system, Karteks Tekstil operated the three blowroom lines in the standard pneumatic fiber transport mode for the first three weeks. After collecting enough data, the lines were switched to the VARIOline ECOrized mode and have been operating in this mode ever since. The blowroom generated 22% energy savings, with 27% less energy for fans and 16% less energy required for the filter. This translates to savings of USD 19600 per year for all three blowroom lines (Fig. 3).
Optimum interaction of the machines
Karteks Tekstil operates a complete Rieter ring spinning system from bale to yarn. “The advantage of Rieter as a system supplier lies in the optimum interaction of the machines. An example for this is the solution VARIOline ECOrized, which – along with many other benefits – saves 22% energy in the blowroom. Rieter developed a solution with great added value by addressing customer’s needs,” says Mr. Hüseyin Kadi, Mill Manager at Karteks Tekstil. Like Damodar, Karteks Tekstil also benefits from better indoor air quality in the blowroom and a smoother operation thanks to predictive information and a permanent monitoring of the filter installation.
About Rieter
Rieter is the world’s leading supplier of systems for short-staple fiber spinning. Based in Winterthur (Switzerland), the company develops and manufactures machinery, systems and components used to convert natural and man-made fibers and their blends into yarns. Rieter is the only supplier worldwide to cover both spinning preparation processes and all four end-spinning processes currently established on the market. Furthermore, Rieter is a leader in the field of precision winding machines. With 17 manufacturing locations in ten countries, the company employs a global workforce of some 4 900, about 18% of whom are based in Switzerland. Rieter is listed on the SIX Swiss Exchange under ticker symbol RIEN.

Digitalisation is an integral part of the portfolio of the solution provider Saurer
By harnessing the power of the internet, Saurer empowers its customers through a range of digitalised innovations, including the Senses mill management system, Secos – Saurer Customer Portal, Saurer Academy and remote service.
As Saurer has transformed itself from a machine provider to a solution provider for customers along the entire textile value chain, interconnectivity and digitalisation have become vital. Since digital solutions are accessible remotely, Saurer customers are no longer limited by distance and also save time. Whether they need to order an original part, optimise the processes within their machines or have a machine serviced, customers can access the most relevant information pertaining to Saurer products as the information updates and without waiting for an external party to visit their mills.
An early start into digitalisation
Saurer started early into digitalisation of its spinning machinery. 10 years ago, Saurer launched the revolutionary Autocoro 8 that already offered the digitalised option DigiPiecing and DigiWinding. Today, Saurer is looking back at over 1 million supplied spinning positions of Autocoro 8/9/10. The customers benefit from the single-spindle technology, unprecedented productivity due to intelligent automation and digitalization. The latest version, Autocoro 10, is a secure platform for Industry 4.0 in the rotor spinning mill.
On the ring spinning side Saurer offers digitalised features like Optispeed. Together with the ISM (individual spindle monitoring) Optispeed is a function for self-optimisation of the spindle speed depending on the yarn break rate. The operator can set the limits for yarn breaks per 1000 spindle hours. Optispeed automatically raises or lowers the spindle speed, optimizing productivity.
Digitalisation and Automation
The Saurer Robot AGV is designed for the ergonomic handling and transportation of cylindrical or conical cross-wound packages. It picks up the packages from a pallet, buggy, trolley or from the conveyor belt of the machine and stores them in its internal buffer system. Due to the modern laser navigation system, the Saurer Robot AGV moves fully automatically and autonomously through your mill. It detects obstacles in its path independently and drives around them or stops if the minimum safety distance is not maintained.
Senses mill management system integrates all machines into one system
Saurer consolidates all digital information in Senses and has ensured that this mill management system can be integrated seamlessly into spinning plants. Senses enables customers to connect all their Saurer machines and allows third-party machines - all in one system. With Senses, customers can carry out various analyses to control the productivity and quality within their mills remotely using any mobile device. With the customisable Senses cockpit, customers can focus on the key data that is relevant to them. The system also provides the user with relevant key information, helping them to solve problems quickly and efficiently e.g., that a spinning position is not performing optimally due to the number of yarn breaks.
The efficiency of an entire machine is based on the cumulated efficiency of each spinning position. In order to increase machine efficiency, Senses’ offstandard function pinpoints single positions with low efficiency by monitoring all machines after every shift change. It then visualises all outliner positions, allowing the customer to implement countermeasures. With this
function, the customer is able to increase the overall efficiency by 2−3%.
The mill management system’s basic functionality can be extended with Senses Elements, which can be seamlessly integrated into all processes. These are additional features to increase functionality for key areas. Each Element focuses on a specific area: for example, the Senses Element Maintenance digitalises, structures and simplifies all maintenance processes to increase productivity. Senses Workforce digitalises personnel management and improves the efficiency of staff. With Senses Element Shop Floor, customers can optimise their increases productivity by optimising operator guidance, shortening the distances they need to walk in the plant. Senses Recipe enables customers to monitor and adjust the settings of their machines.
Secos assistance functions – saving time in day-to-day business
The Secos – Saurer Customer Portal is more than just an e-shop for Saurer original parts. With the updated version of the portal, it is easier for customers to find original parts – with photo uploads, customers can quickly identify the required original part they need. In the user’s Secos account, all machine-related manuals and technical documentation for their machines are saved for quick reference in case of questions on operation and maintenance. Like Senses, Secos can be accessed anytime, from any mobile device.
Saurer Academy – turning employees into experts
This platform offers a wide range of training and further education courses for machine operators. Customers can book classroom and live web-based training courses. In addition, the Saurer Academy offers e-learning courses with multimedia, audio-visual training material that explain complex issues and processes in a clear and easy-to-understand manner. Course contents include training on the function, operation and maintenance of Saurer machines and their assemblies. Webbased trainings (WBTs), recorded webinars and learning cards give employees the flexibility to decide for themselves when, where and at what pace they want to learn. Knowledge tests with certificates allow workers to keep track of their progress and review the work.
In 2021, during training sessions with a South African customer, the Saurer Academy team also arranged for specialists from various Saurer departments to join the class during the live virtual training sessions, to answer specific questions the customer’s employees had. After each training session, Q&A rounds were held to address specific issues that the attendees may encounter, along with solutions. This virtual offering has also proved particularly useful during the pandemic, when it was not possible for trainers to travel on-site.

The Saurer Robot AGV is designed for the ergonomic handling and transportation of cylindrical or conical cross-wound packages
Remote service – have our Twisting experts inside your machine in minutes
Saurer experts can access a fully digital read-out of the error log, which allows them to identify any issues immediately. They can also adjust machine control settings, update software and do diagnostics checks of any hardware defects as well as check CPU usage, energy consumption and machine temperature. This means getting the customer’s machine running at optimal capacity faster with less downtime. Using the Saurer remote service is also more affordable than calling out a technician. This service is particularly beneficial to customers that are located in more remote areas. Again, such services have been invaluable during the past lockdown-prone years.
Illustrating how this works in practice, Saurer technicians were able to remotely detect two defective pieces of hardware and restore a customer’s recipe list in just two hours. On another occasion, our technical staff quickly and successfully solved a major machine breakdown in 30 minutes, avoiding an unnecessary and costly on-site intervention.
Digitalisation has revolutionised traditional services such as site visits, inperson training and machine troubleshooting. Even Secos goes beyond being an e-shop but is instead a knowledge base tailored to each user. Increasing digitalisation, combined with functions that enhance machine intelligence – such as Optispeed, DigiWinding and DigiPieicing in the case of Saurer – will boost interconnectivity, allowing machines within Saurer systems to communicate, further providing customers with added benefits in the mill.
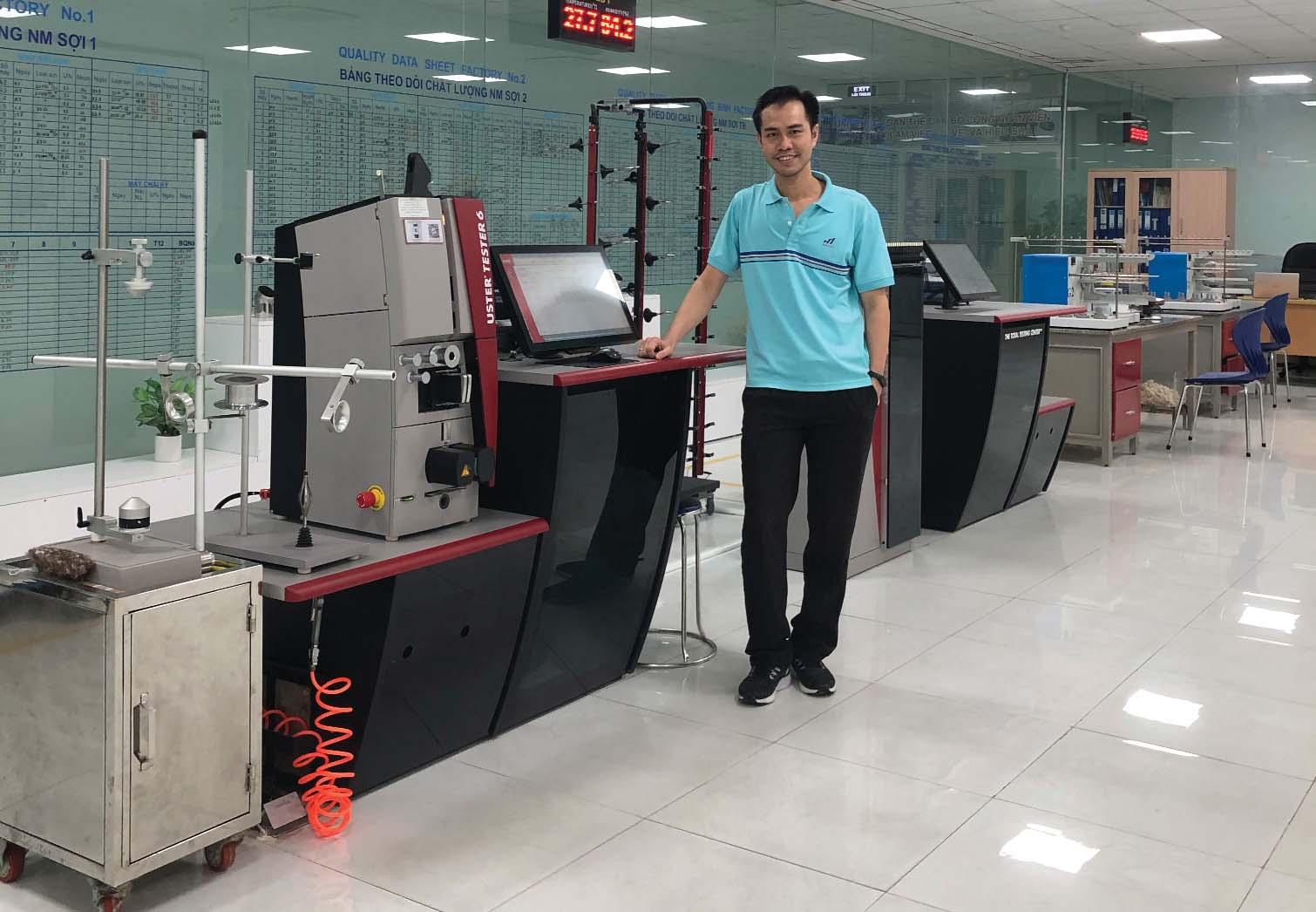
Uster’s Quality Management Platform makes a huge different to shopfloor personnel Looking for vital information in a busy textile mill can be quick and easy – or a tedious job, turning minutes into hours. Heavy e-mail traffic can just add to the burden. That’s why leading Vietnamese producer Hoa Tho Textile chose Uster Quality Expert, to give fast access to centralized key data and drive major efficiency benefits.
Founded in 1962, Hoa Tho is part of one of Vietnam’s largest and longestestablished textile and garment enterprises. Operating a number of mills, the company wanted to ensure that quality standards were equal across all of them – and equally high, to serve customers in demanding markets such as the USA, Europe, Japan and South Korea. So quality management must be comprehensive, including data from different locations as well as various instruments and systems, for quick reports and smart analysis.
One-stop quality data
Uster Quality Expert is the Quality Management Platform for advanced process optimization across yarn manufacturing processes. A single system provides full transparency and complete control, securing fiber, yarn and fabric quality. All information is in one place –definitely a valuable benefit of Quality Expert. Hoa Tho connected its Uster AFIS Pro 2, Uster Tester 6, Uster Tensojet 5 and Uster Quantum 3 yarn clearers to this one system.
With Quality Expert in place, the mill managers now have a common reference to compare quality levels in each mill. They can now access quality information very easily. Previously more time was needed to create quality reports, which were then distributed by email. “The information took too long to reach the right people and was not always up to date. Now, the latest quality results are available in real time and any required action can be taken immediately,” says Nguyen Huu Khanh, Manager of the Yarns Technology Department at Hoa Tho Textile.
The all-round view
Connecting to Uster Quality Expert is the route to effective all-round process optimization in textile mills. The system expands its insightful analytics with valuable intelligence, as each additional instrument is connected. It is the ultimate Quality Management Platform to drive consistent quality in every part of the spinning process. That’s what decided the Vietnamese spinning mill to invest. “It is
very important for us to control the quality in yarn clearing in combination with the quality results from blowroom, carding and roving,” says Nguyen. With Quality Expert, a combination of 100% in-line monitoring, precise laboratory testing and integrated intelligence delivers the power to predict potential faults and prevent claims.
Data-based preventive measures are a tremendous asset in yarn production, but Uster observes that customers also greatly appreciate the single Value Modules of Quality Expert. Each of these five modules is based on Application Intelligence, offering advantages in specific fields.
The Alarm Center creates awareness and triggers action – with problemsolving suggestions – in case of issues. Mill Analysis offers insightful analytics for data-based decisions, and Yarn Prognosis raises the spinner’s reputation to a new level with customers. The ‘star’ elements among the Value Modules are Total Contamination Control and Ring Spinning Optimization. TCC balances ejections in the blowroom with clearer cuts in winding in the most advanced way. RSO brings improved spinning performance with quality transparency from top to bottom of the cop.
Feelgood: efficiency and control
Nguyen has a secret favorite among Uster Quality Expert benefits: “The Uster Mobile Alert App is a great tool to access information while on the road, or away from the spinning mill. The personnel and I can be notified, and so solve most issues faster on the shopfloor. Our mill management has better control and this results in fewer problems needing to be escalated to me,” he says.
The Quality Management Platform was developed for decision-makers – but the biggest fans are actually the operators and managers working with the system on a daily basis. “Personally, I have a better view of the quality produced in our mills, while spending less time to get the information I need. I would not want to go back to the era before Quality Expert at any price,” says Nguyen.
Uster Quality Expert comes in two distinct versions – both with no compromises in ultimate analysis. It’s integrated within Uster Tester 6 and also available as a standalone solution.
About Uster Technologies
Uster is the world’s leading provider of quality management solutions from fiber to fabric.
Uster Technologies offers hightechnology instruments, systems and services for quality control, prediction, certification and optimization in the textile industry. This includes systems for quality management, laboratory testing and in-line process control for fibers, staple and filament yarns, fabric inspection as well as value-added services.
Uster provides the globallyacknowledged Uster Statistics benchmarks for trading, textile knowhow training, consulting and worldwide after-sales services – always aspiring to fulfill the textile market’s needs, to drive innovation forward with ‘quality in mind’.
Uster Technologies AG is headquartered in Uster, Switzerland and operates worldwide. It has sales and service subsidiaries in the major textile markets and Technology Centers in Uster (Switzerland), Knoxville (USA), Suzhou (China) and Caesarea (Israel).
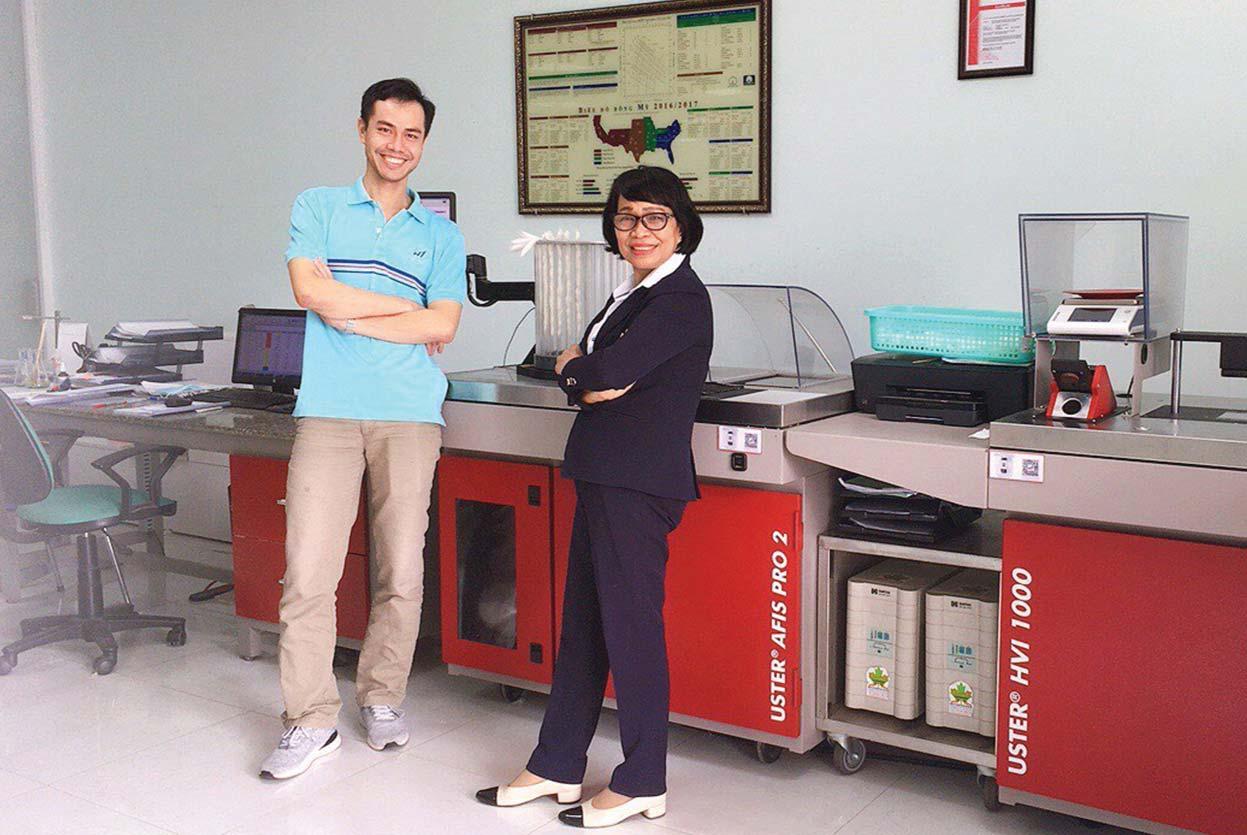
Strong growth and margin expansion in both divisions; expected to continue in 2022
CEO Roland Fischer stepping down for private reasons; Michael Suess will assume Executive Chair role.
“We grew the company and delivered strong margin expansion in 2021, and expect profitable growth to continue in 2022,” said Roland Fischer, CEO Oerlikon Group.
“Operationally, we executed well, efficiently managed cost and successfully mitigated supply chain shortages, driving EBITDA above preCOVID levels. Moreover, we successfully completed two accretive bolt-on acquisitions, further diversified our business and made excellent progress in our sustainability initiatives,” added Fischer. “The Board will propose a dividend of CHF 0.35 per share at the AGM.”
“In 2022, we will continue to execute on our strategy to expand in growth markets, take advantage of recovering markets and focus on cost control. We expect Group sales to be around CHF 2.9 billion and our operational EBITDA margin to be around 17.5%,” concluded Fischer.
Strong FY 2021 Group Top-Line Performance Driven by Both Divisions
Oerlikon delivered growth in orders and sales, supported by market recovery in Surface Solutions and strong demand in Polymer Processing Solutions.
Successfully Sustained Cost Actions and Operating Leverage in FY 2021
Group operational EBITDA increased by 39% to CHF 447 million, versus CHF 323 million in 2020. Correspondingly, the operational EBITDA margin improved by 260 basis points to 16.9%, reflecting sales recovery and the sustained positive impacts from cost actions.
Continued Strong Commitment to Sustainable R&D
In 2021, Oerlikon strengthened its innovation pipeline by filing 90 patents. The company continued to invest in innovation and spent 4.0% (CHF 105 million) of 2021 Group sales on R&D to develop new, improved and sustainable technologies to meet customers’ needs and demands.
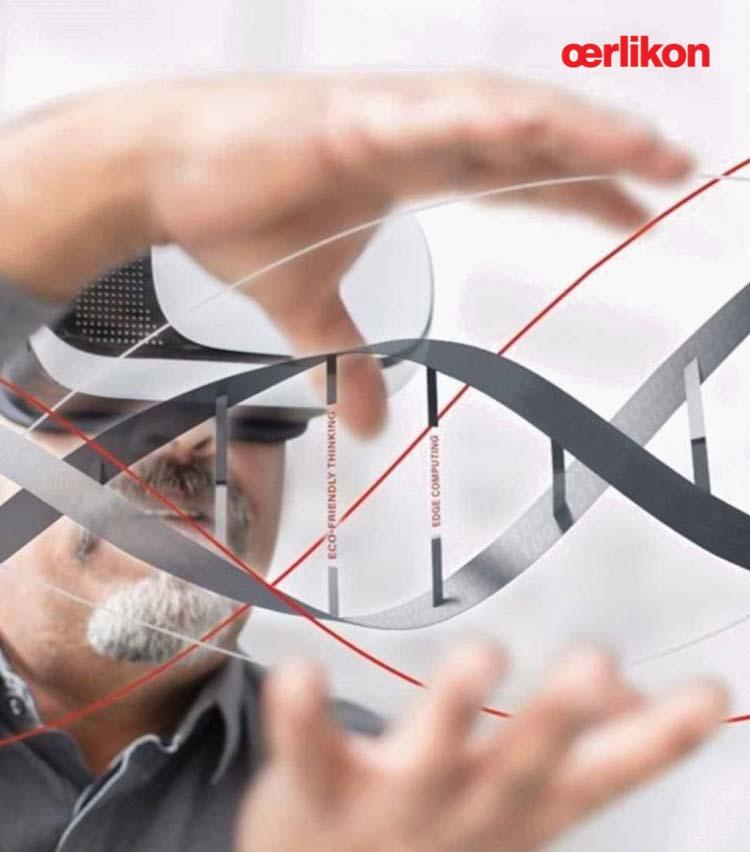
2022 Outlook: Continued Profitable Growth
Oerlikon will continue to expand its business in growth markets, leverage opportunities in recovering markets and exercise cost containment. The Group will continue to actively manage and mitigate any further impact from challenges stemming from short-term supply chain and COVID-19-related issues. For 2022, Group sales are expected to be around CHF 2.9 billion and the operational EBITDA margin to be around 17.5%.
New Group Leadership Structure as of July 1, 2022 with an Executive Chair Model to Support Strategic Focus of Oerlikon
After six years leading the company and ensuring its successful transformation, Roland Fischer, Oerlikon Group CEO, has announced his decision to step down for private reasons, effective June 30, 2022, in consultation and with the endorsement of the Board of Directors.
“I am proud of what we have achieved at Oerlikon since I joined as CEO, and how the company has been transformed into a globally active engineering and technology company with a clear strategic focus and organization,” said Fischer. “In the past two years, the Surface Solutions Division has successfully implemented cost
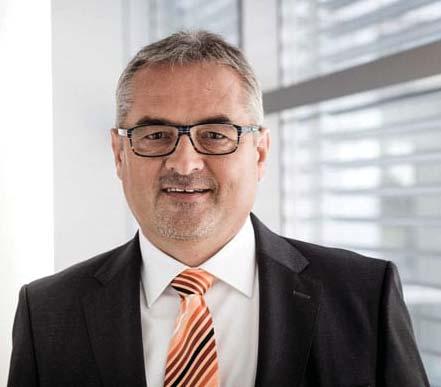
measures and embarked on a transformation to empower the regions and become closer to key markets. The Polymer Processing Solutions Division has successfully continued its strategic diversification into non-filaments markets. My priority now is to ensure a smooth transition so that the company can continue to be a global market leader in advanced materials, surface engineering and polymer processing.”
“I very much regret but fully understand and respect Roland’s decision. On behalf of the Board, I would like to express our deep gratitude for his extraordinary service. He has been a key driver in the successful transformation of Oerlikon,” said Michael Suess, Chairman of the Board. “Our two divisions are distinct from each other in that they serve different customers in different industries and also differ in their growth potential. With the Executive Chair model, the division CEOs will gain agility in decision making, which will enable them to expedite the execution of their business and ensure sustainable growth.”
Under the Executive Chair model, the Board of Directors delegates the operational management of the Group as follows: i. The two current division CEOs,
Markus Tacke and Georg Stausberg, will continue to have operational control and accountability in leading their divisions. In addition, the new management model will provide them the added agility and speed of execution to run and grow their business. ii. Michael Suess, will assume the position of Executive Chair, overseeing all Group-level management topics and leading the Executive Committee in addition to his role as Chairman of
Oerlikon’s Board of Directors. iii. The Executive Committee will be responsible for ensuring the harmonized Group-wide management of all organizational topics with cross-divisional relevance.
As of 1 July, 2022, the Executive Committee will consist of the two division CEOs, the Chief Financial Officer, Philipp Mueller; and the Chief Human Resources Officer, Anna Ryzhova, and will be led by

About Oerlikon
Oerlikon is a global innovation powerhouse for surface engineering, polymer processing and additive manufacturing. The Group’s solutions and comprehensive services, together with its advanced materials, improve and maximize the performance, function, design and sustainability of its customers’ products and manufacturing processes in key industries. Pioneering technology for decades, everything Oerlikon invents and does is guided by its passion to support customers’ goals and foster a sustainable world. Headquartered in Pfäffikon, Switzerland, the Group operates its business in two Divisions – Surface Solutions and Polymer Processing Solutions. It has a global footprint of more than 11 800 employees at 207 locations in 38 countries and generated sales of CHF 2.65 billion in 2021.
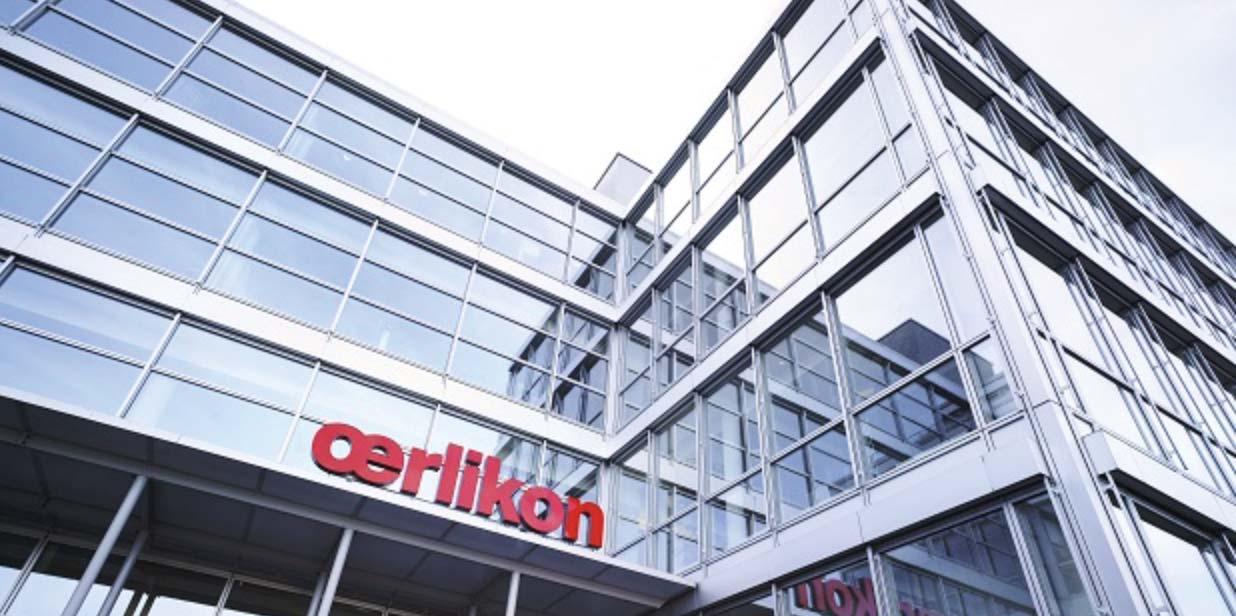
The Secrets Behind the Science of Winding
very yarn manufacturer’s dream is to achieve a perfectly wound package so that the yarn can be processed easily in downstream processes, like dyeing or weaving. What does it take to achieve a perfectly wound package and what makes this an amazing engineering feat that helps save energy and resources?
Winding is a small but crucial step in the textile value chain. This is when yarns are wound tightly onto a bobbin to prepare them for the next manufacturing stage. Every yarn manufacturer’s dream is to achieve a perfectly wound package so that the yarn can be processed easily in downstream processes, like dyeing or weaving.
preciforce sets new standards
The secret behind getting a perfectly wound package is achieving regular density across the entire package which is especially important for dyeing. But what looks easy on the surface is nothing less than a carefully designed engineering feat built on decades of expertise.
Until now, winding systems were limited to merely monitoring density without the ability to adjust pressure levels. SSM’s preciforce changes all this with the ability to regulate backpressure so that each and every bobbin reaches the same density. The perfectly even package densities make the dyeing process easier, thus optimizing results. Even better, dye houses save energy and water as they no longer need to repeat the dyeing process which is necessary when packages are wound unevenly.
A winning team: preciforce and DIGICONE 2
Perfect density is great, but costs also play a role. At SSM, the company’s mission is to help customers manufacture at the lowest possible cost and with the least amount of waste. Winding is a repetitive action so SSM engineers found that what was working for Google searches and algorithmic trading – which are based on recurring, sequential actions – was good for winding, too. They developed an algorithm that ensures the winding machines apply a step-by-step procedure to achieve a tightly wound package in the most economical way. DIGICONE 2 was developed with this advanced winding algorithm that ensures optimal accuracy in yarn laying. Together preciforce and DIGICONE 2 make an unbeatable team to manufacture a superior package in the most economical way.
In addition, preciforce helps to save roughly 20% energy compared to standard automatic backpressure systems.
To round it off, the reliability of SSM machines is unmatched, with the longest lifetime for machines and spare parts. SSM also provides a world-class service network with over 10 local service stations and 80 agencies worldwide. This translates into short journeys and fast response times for customers.
For further information please contact:
SSM Schärer Schweiter Mettler AG.
SSM’s preciforce™ offers the ability to regulate backpressure so that each and every bobbin achieves the same density.
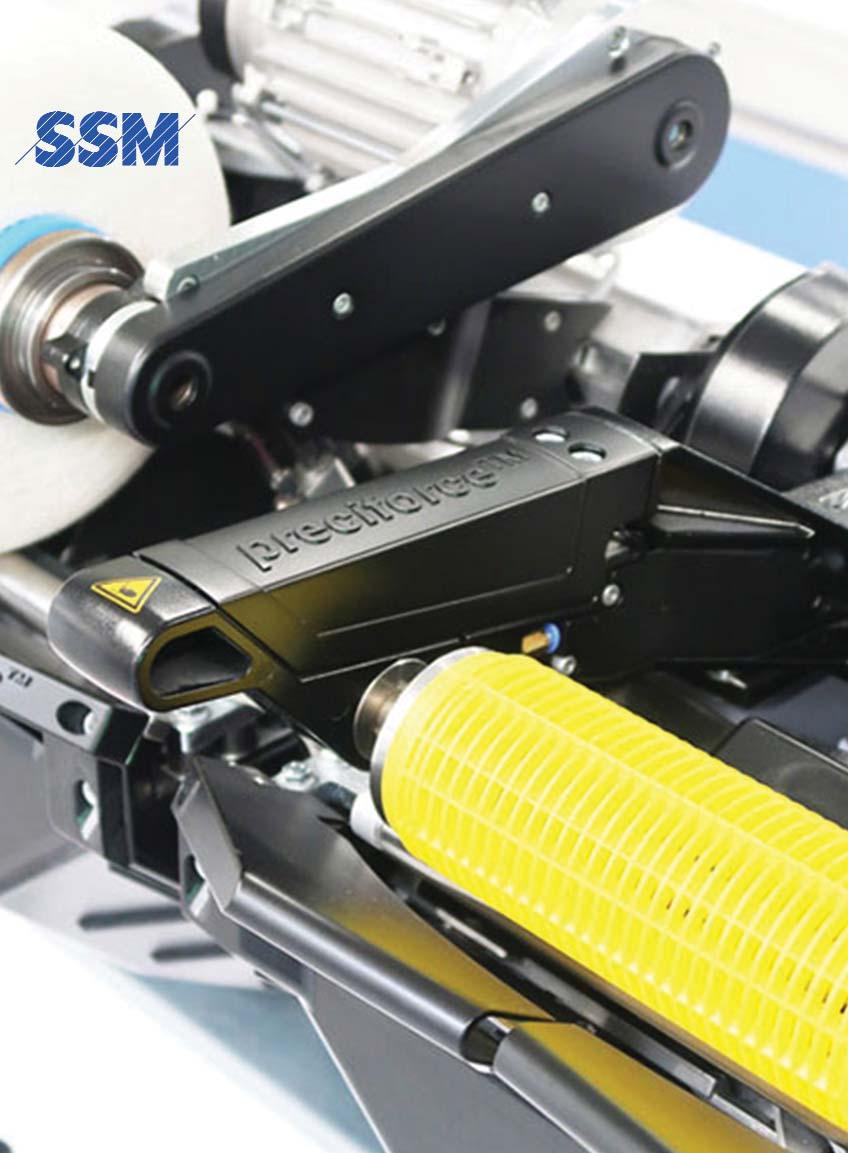
The fascinating world of narrow fabrics - product innovation and solutions for the digital transformation at Jakob Müller Group
Digitization runs through the entire valueadded process, from logistics to the end consumer. The Jakob Müller Group covers a large part of "Smart Production" and makes a major contribution to making the process chain even more efficient and sustainable.
Any solution in Jakob Müller Group’s digital portfolio is clearly focusing on customer benefit. In this context
mymueller® - the Jakob Müller Group’s
customer portal plays an important role. The mymueller® customer portal provides access to company-specific information, know-how, services and license products - online – around the clock - worldwide. mymueller® displays the customer's machine park on desktop computers, smartphones or tablets. In addition, operating instructions and spare parts catalogs can be called up and spare parts orders can be triggered.
All in all a “carefree package”, which is constantly extended with additional services and products for the worldwide customer base.
One of the latest products out of Jakob Müller Group’s license product portfolio is the browser based data acquisition and management software mymuenet®. Today's market environment requires flexible, fast and secure exchange and access to data at all company levels - worldwide. The production data management plays an important role here.
In this context Jakob Müller Group is providing a browser based solution. The mymuenet® production data acquisition and management system with direct access to the machine controls offers a unique data monitoring, communication and exchange in a global framework. Furthermore designs, which are being created by Jakob Müller Group’s design software MÜCAD can be transferred through mymuenet® to machines in any location worldwide.
Digitalization however does not only refer to software solutions, but also applies on end products in the field of Smart Textiles. For this constantly growing market Jakob Müller Group is providing specific machine technology for processing i.e. conductive yarns for various applications with digital features like humidity measurement, integrated solar cells and many others.

Benninger....................................................................17 Chhipasons................................................................72 CCI USA.....................................................................3 Fine Industries ..........................................................25 Graf............................................................................1 IGATEX Pakistan 2022...............................................31 Intex South Asia........................................................33 ITMA Asia + Citme 2022..........................................IBC
ITM 2022..................................................................27 iTextiles.....................................................................BC Jakob Mueller AG......................................................13 Jet Logistics................................................................72 Rastgar..............................................................39 & 72 Staubli........................................................................15 SPGPrints....................................................................9 SSM...........................................................................11 Zhejiang Rifa..............................................................IFC
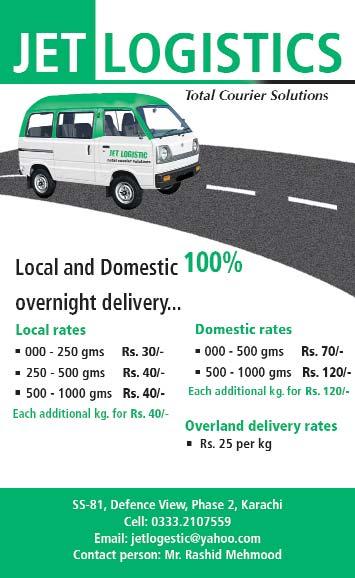
January 2022 Apparel and Knitwear / Denim Established 1951
February 2022 Spinning Review
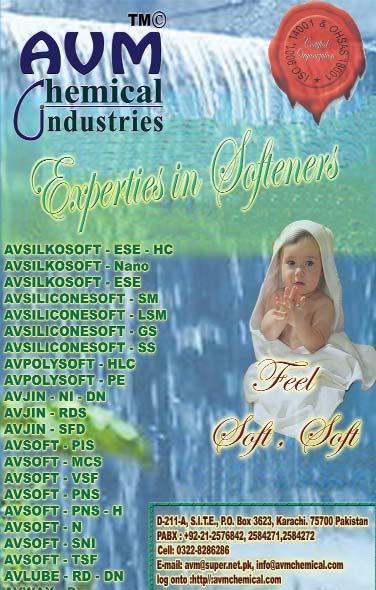
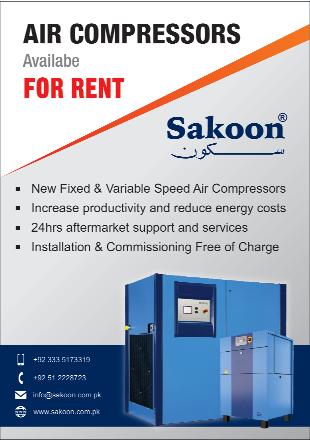
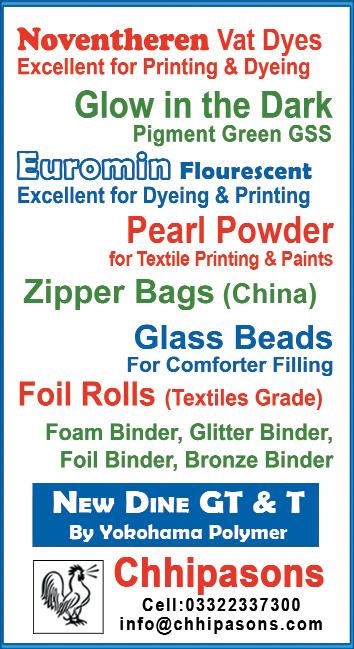

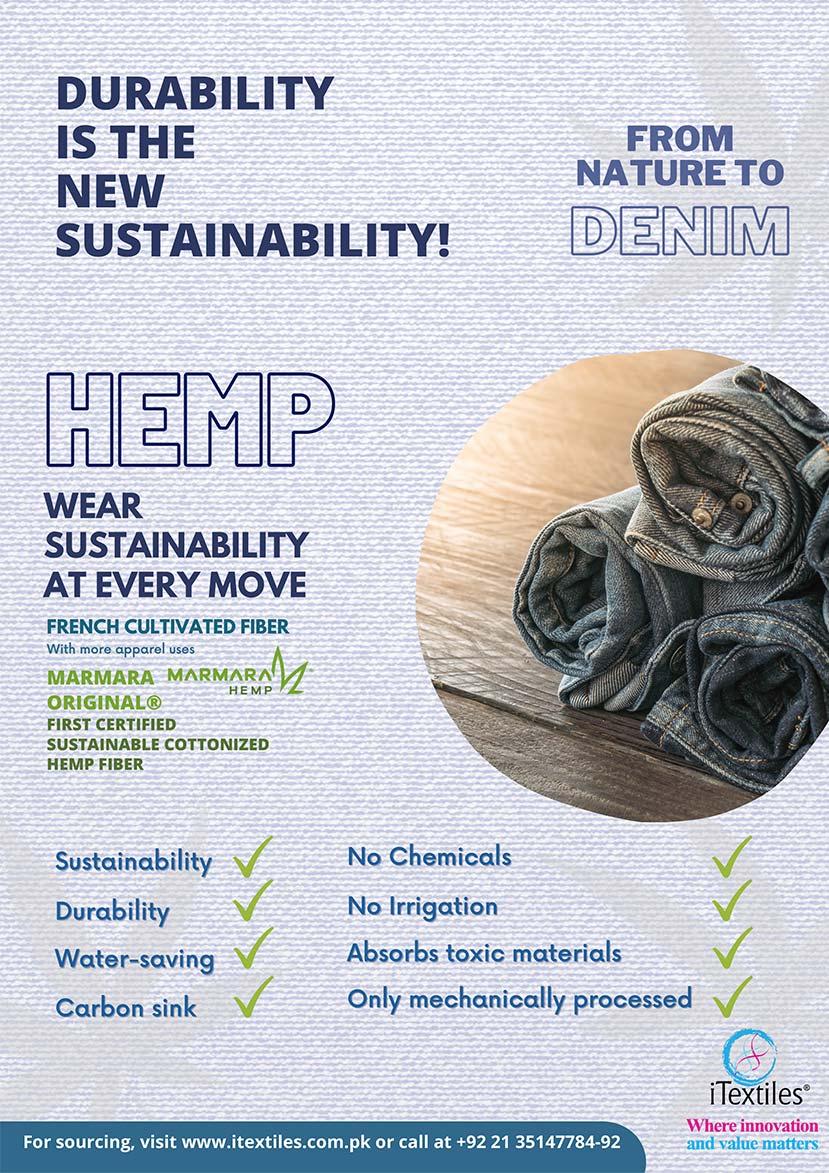