
4 minute read
TITAN Forte – Bräcker Spinning Ring for Maximum Coarse Yarn Production
Najam Yusuf, Technical Director, Nishat Mills
After denim’s story of success started in the French city of Nîmes some centuries ago, the manufacturing hub of the world’s favorite twill fabric has now moved to the fast-growing market of Pakistan. To help the local industry cope with surging demand, Bräcker, a leading supplier of rings and travellers for ring spinning machines, developed TITAN Forte to help expand service life. Field tests conducted at one of the country’s largest vertically integrated mills, Nishat Mills Limited, are showing promising results with TITAN Forte even extending service life by up to six times!
Advertisement
Denim is probably the most popular fabric today. The name denim stems from “Serge de Nîmes”, with “Serge” referring to a twill fabric which was formerly produced in the southern French city of Nîmes. After going mainstream in the US and around the world in the 20th century, Pakistan has now become one of the world’s most important markets for denim. A key reason is that the sturdy fabric benefits from the local cotton which is characterized by coarse and short fibers.
The downside of the country’s success, however, is that the huge demand for denim is pushing Pakistani spinning mills to the limit. The many textile applications on ring spinning machines put the ring/traveller system under intense pressure as it is a key component in ring spin-
ning. This is especially true for applications with coarse yarns from Ne 6 through to Ne 10 SIRO as they result in extreme loads for the ring/traveller system which potentially lead to premature failure of the spinning ring.
Technical innovations for a longer service life
Following extensive research and development to address this challenge, Bräcker launched a new ring called “TITAN Forte” based on the renowned TITAN coating. The key process parameters of the coating process have been optimized to provide a superior coating with significantly increased resistance against high load and high velocity wear phenomena.
Bräcker’s TITAN Forte for ring spinning helps to extend service life by up to six times
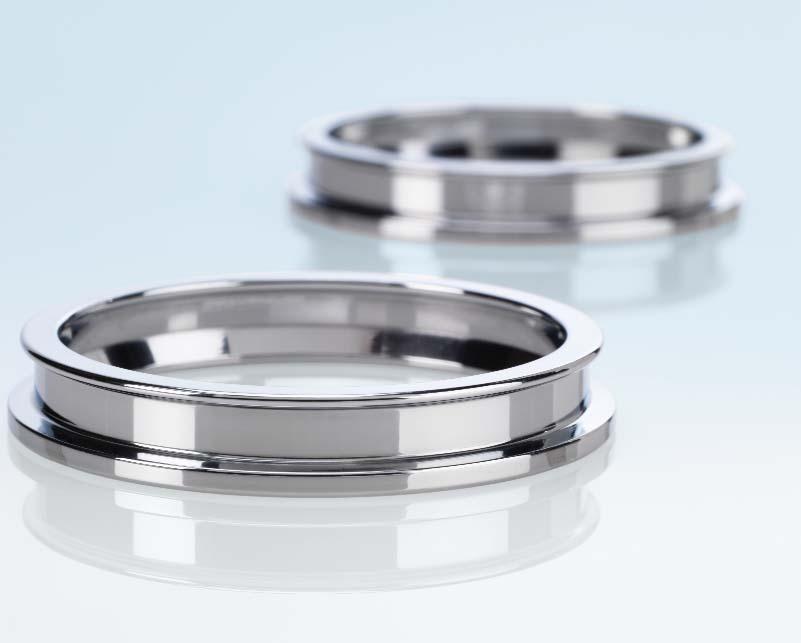
Boosting service lifetime by up to six times
Field tests at one of Pakistan’s largest vertically integrated textile mills Nishat Mills 54 in Sheikhupura Faisalabad are promising.
Tests across the board proved that the service life of the TITAN Forte is about six times longer compared to conventional spinning rings. The rings and traveller systems were used for 100% cotton plain, twin, weaving, knitting, compact as well as non-compact yarn ranges from yarn count Ne 8 to Ne 20. The new rings last about three years, even under extreme load and the continuous running of travellers over the entire service life of the spinning ring.
Mr. Najam Yusuf, Technical Director at Nishat Mills Limited, explains that TITAN Forte has significant advantages in the coarse yarn count range in combination with higher spindle lift. “We benefit from remarkable improvements for coarse twist yarn applications such as Ne 10 SIRO.”
Mr. Yusuf further highlights that with TITAN Forte spinning parameters remained constant over the entire service life of the spinning ring, without adjustments of the traveller weights. The reinforced and highly resistant surface of the TITAN Forte rings allowed a consistently high spindle speed by retaining and
absorbing more ring load. Reduced hairiness and the Imperfection Index of Yarn (IPI) result in a constant yarn quality level over the entire service life of the spinning ring.
TITAN Forte improved production efficiency thanks to increased spindle speeds and fewer traveller cycles, which together with the increased service life led to fewer downtimes. Mr. Yusuf in closing points to the commercial advantages: “With the longer service life of TITAN Forte at maximum operating parameters, which also applies to the travellers, we achieved optimized cost efficiency.”
About Rieter
Rieter is the world’s leading supplier of systems for short-staple fiber spinning. Based in Winterthur (Switzerland), the company develops and manufactures machinery, systems and components used to convert natural and manmade fibers and their blends into yarns. Rieter is the only supplier worldwide to cover spinning preparation processes and all four endspinning processes currently established on the market. Rieter is also a market leader in precision winding machines. With 15 manufacturing locations in 10 countries, the company employs a global workforce of some 4 420 employees, about 21% of whom are based in Switzerland. Rieter is listed on the SIX Swiss Exchange under the ticker symbol RIEN.
About Bräcker
Bräcker, the world’s leading supplier of rings and travellers for ring spinning systems, is a subsidiary of the Rieter Group. Bräcker, based in Pfäffikon ZH (Switzerland), creates customer value through system expertise, innovative solutions, after sales excellence and global presence. The company manufactures its main products – rings and travellers for ring spinning machines –in Pfäffikon and Wintzenheim (France). In addition, Bräcker offers grinding machines used for maintenance of cots.
About Nishat Mills Limited
Nishat Mills Limited is the flagship company of Nishat Group. It covers spinning, weaving, processing, home textiles, garments, bath division and Nishat linen. Spinning production capacity for both cotton and blended yarns is 200 tons per day. Nishat Mills Limited is the largest vertically integrated textile company in Pakistan, with the latest state of the art machinery setups. Nishat Mills provide equal employee opportunities for men and women and adopt and set terms in sustainability and environmentally friendly textile products.