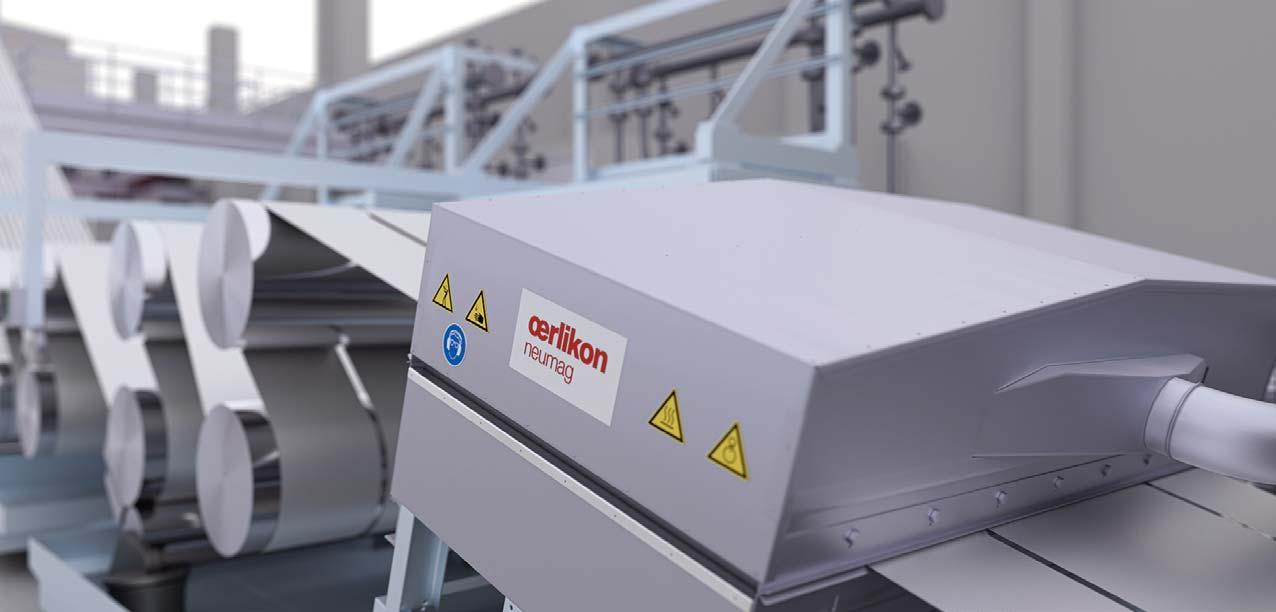
4 minute read
Oerlikon with world premieres at ITMA Milan 2023 “Technology is once again enabling us to create a better world”
Oerlikon Group is set to make significant world premieres at the ITMA Milan 2023 trade show. The company's focus is on addressing the current challenges faced by the textile industry, including the establishment of a circular economy, providing energy-efficient technologies, utilizing digital solutions for sustainable production, exploring new materials, and ensuring traceability and recycling of raw materials. Oerlikon invites trade fair visitors to engage with their experts at booth B211 in hall 1, where they will showcase their innovative technology solutions and provide answers to pressing questions related to the industry's present and future concerns.
Georg Stausberg, CEO of the Polymer Processing Solutions Division and Chief Sustainability Officer of the Oerlikon Group, highlights the company's commitment to innovative technologies that promote resource-saving practices in manmade fiber spinning mills worldwide. Oerlikon's aim is to expand its zero-waste production approach and achieve sustainability goals for both its customers and its own operations.
Advertisement
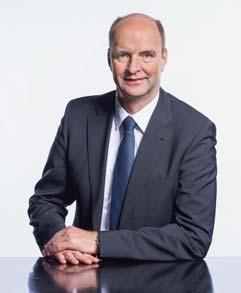
The challenge of creating a circular economy and promoting recycling in the textile industry is crucial due to the industry's significant environmental impact. The consumption of textiles is already the fourth-largest source of negative environmental and climate change impacts in the European Union (EU), according to the European Environment Agency. The global production of textiles nearly doubled between 2000 and 2015, and the annual consumption of apparel and shoes is projected to rise by 63% by 2030. Oerlikon recognizes the need for innovative recycling technologies and has partnered with Worn Again Technologies, a British company focusing on solvent-based recycling technology. Together, they are developing a large demonstration system in Switzerland to convert end-of-life textiles and PET plastics into circular raw materials and fibers.
Oerlikon also sets high sustainability goals for its own operations. The company is implementing pilot initiatives with the intention of achieving CO2 neutrality in all its locations by 2030. They have already achieved this milestone at their site in Liechtenstein, which serves as a blueprint for their sustainability commitment. Oerlikon aims to obtain 100% of its electrical energy from renewable sources and adhere to the "Zero Harm to People" standard.
One essential aspect of achieving a circular economy in textiles is fiber-to-fiber recycling. While only around 1% of used clothing was recycled into fibers a few years ago, McKinsey market researchers predict that 18 to 26% of textiles could be recycled by 2030 if technical recycling potential is fully utilized and more textiles are collected. However, there are challenges to overcome, such as automating manual processes, sorting clothing waste, removing buttons and zips, unambiguously identifying fiber compositions, and addressing the obstacle of separating mixed fibers. Nevertheless, there are promising solutions on the horizon, despite some processes not yet being ready for commercial use.
Oerlikon Barmag offers technological solutions for recycling PET (rPET) that can save millions of tons of CO2 per year. They have introduced a homogenizer recycling line specifically designed for customers in China and Asia, allowing for the agglomeration, extrusion, homogenization, and melting of bottle flakes and film waste to produce polymer melt or chips. This enables precise adjustment of the polymer quality of recycled bottles or film waste to meet the requirements of different downstream processes.
Another rPET solution from Oerlikon Barmag is the VacuFil system, developed in collaboration with BB Engineering. VacuFil is a PET recycling line that combines gentle large-scale filtration with targeted intrinsic viscosity (IV) regulation, ensuring consistently outstanding rPET melt quality. The system includes a patented upgrade component called the Visco+ filter, which enables precise IV setting and pure melt through vacuum assistance. The Visco+ process is reliable, verifiable, and 50% faster than conventional liquid-state polycondensation systems.
In terms of energy efficiency, Oerlikon Neumag will unveil its EvoSteam process at ITMA Milan. This process aims to revolutionize polyester staple fiber production by reducing operating expenses and carbon footprint while minimizing energy, water, and polymer consumption. With the growing demand for textile fibers, resource- and environment-friendly manufacturing methods are crucial for the future, especially considering the rising energy and polymer prices and the scarcity and cost of water resources.
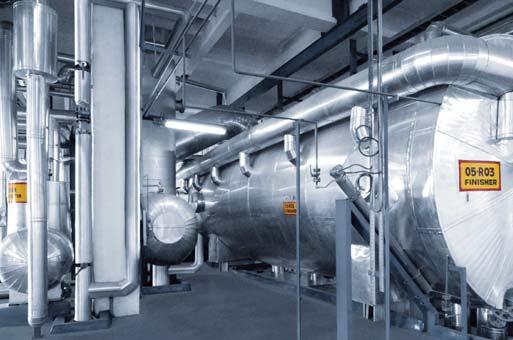
The introduction of new materials poses challenges as well, particularly in meeting the European Union's sustainability goals. While bio-based polymers and biodegradable polymers offer opportunities for a sustainable circular economy, their prices are not yet competitive compared to petrochemical-based polymers. However, Oerlikon believes that with their current and future technologies, they can transform any raw material into an ecologically attractive end product, with consumer acceptance being the ultimate determining factor.
Digitalization and traceability are essential for achieving a sustainable and closed-loop textile industry. The EU aims to become a pioneer in the global circular economy by 2030, with textile products becoming more durable, recyclable, and compliant with social and environmental standards. Oerlikon will present its own digital technology solutions and collaborations with various partners for use in their technologies to meet these requirements.
The concept of the digital twin plays a significant role in Oerlikon Barmag's vision for the future. They will showcase a complete WINGS POY winding head as a kinematic model, allowing for the mapping of all processes occurring during the operation of a winding head in virtual space. This digital twin enables faster and more cost-effective production solutions for customers.

Oerlikon is also launching the Digital Academy, an online training center accessible through the myOerlikon.com ecommerce platform. The academy offers role-based e-learning modules on operation, maintenance, and repairs for Oerlikon that can be accessed anytime and anywhere.

Additionally, Oerlikon will showcase other innovations at ITMA Milan 2023, including the ACW WINGS upgrade, wiping robots for spin packs, a new air-texturizing line for POY and FDY, gear metering pumps for continuous filament production, and the HycuTEC inline charging technology for high-end charged meltblown filtration media.
Oerlikon's participation at ITMA Milan 2023 demonstrates their commitment to advancing the textile industry through sustainable and innovative technologies, while addressing the challenges of circularity, energy efficiency, digitalization, new materials, and traceability. Their goal is to create a better world by leveraging technology and promoting a more sustainable approach to textile production and consumption.
