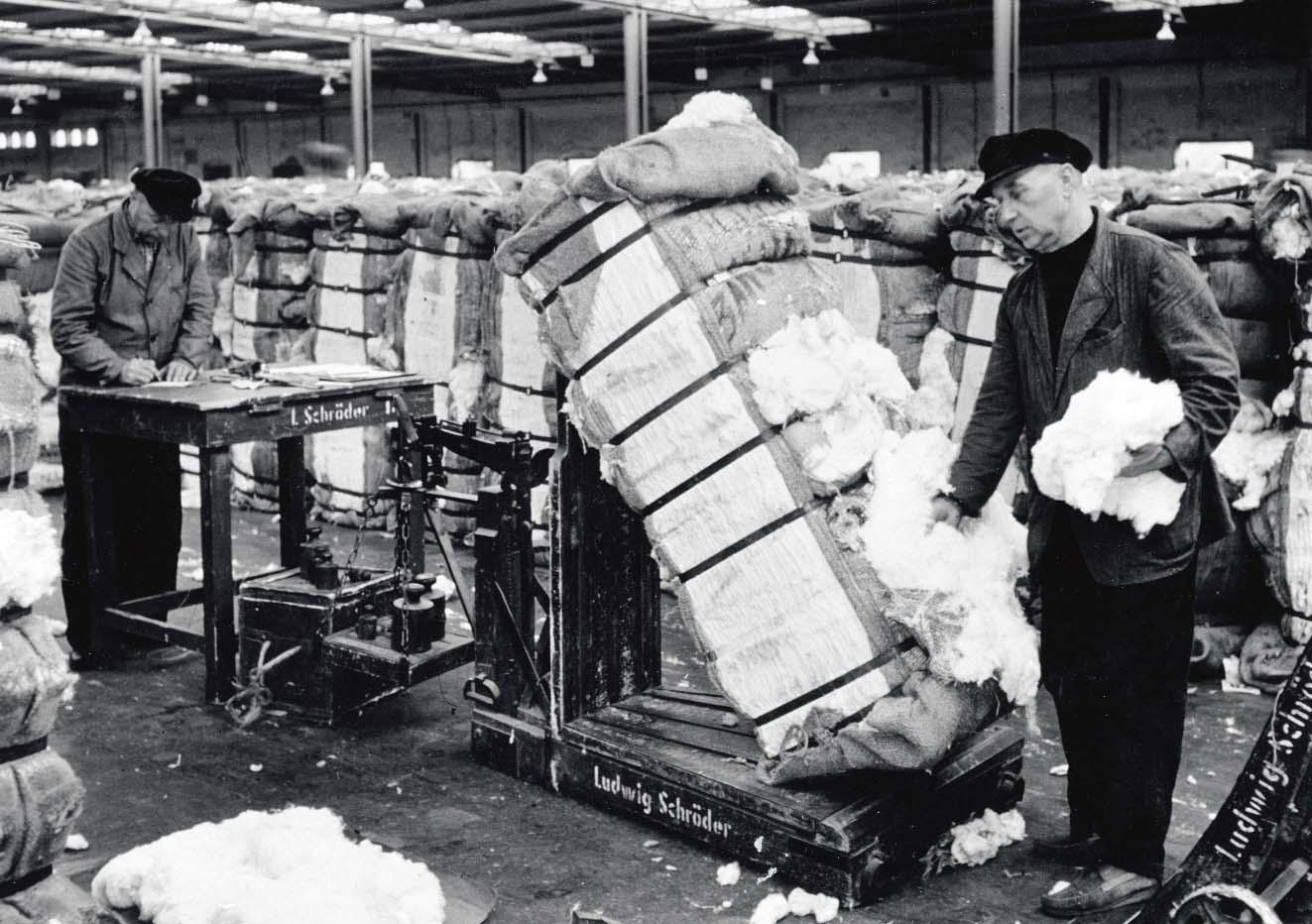
11 minute read
Uster: Cotton – the unique natural fiber Sellers Textile Engineers: Hybrid Shear for carpet manufacturing . . . . . . . . . . .40 Seeing beyond the patterns with Shelton Vision . . . . . . . . . . . . . . . . . . . . . . .42 46
Brockmöller collection (Kulturhaus Walle)
Cotton – the unique natural fiber
Advertisement
Today’s must-knows about cotton and Uster
World Cotton Day – on October 7 every year – is a celebration of the world’s most important natural fiber. It’s a good time to take a closer look at cotton from all the different angles – the growers and traders, spinners, fashion addicts and even museum visitors.
This article is dedicated to cotton, a unique fiber. It is a true multi-talent: from jeans to banknotes (US paper money is made with 75% cotton and 25% linen), it is almost unthinkable to imagine our everyday life without cotton. The fluffy fiber is found in many different products as an ideal and much-appreciated raw material.
Measured for value
Cotton can be precisely described with 14 quality characteristics – focusing on length, strength, fineness, color, maturity, trash and moisture content of the fiber. The value of cotton as a raw material depends on its quality. Key factors are long and uniform fiber length, optimal fineness for each application and high strength for precious fibers.
Some cotton growers and traders rely on their years of experience to set the right price for a batch of cotton, but over half of world cotton production is classed objectively by High Volume Instruments (HVI) from Uster Technologies. The HVI provides the most accurate and repeatable test results for the efficient classification of cotton quality – and more than 3,300 units are installed in 70 countries.
Measured for bale mix and efficiency
For spinning mills, cotton purchasing accounts for more than 50% of costs, so it’s critical to get it right. Sorting bales according to quality and end-use is best done on the basis of good data. Consistent data from HVI is the first step in successful production in spinning operations – in terms of both quality and cost.
Some of the costliest mistakes in yarn manufacturing arise from poor control of the raw material at bale mix before spinning preparation. But fiber testing is also essential during the spinning preparation stages, to minimize any negative financial impact of excess waste, unnecessary cuts, reworking, and customer claims. Another fiber measurement instrument is responsible for profitable production: Uster AFIS Pro2 provides the essential data necessary for modern process optimization techniques in the spinning mill, and best practice in process control.
100% cotton
A look into the cultural history of cotton is also illuminating. The cotton
story goes back over 5,000 years. Did you know that cotton was a driver for industrialization? Today, cotton fiber is found in clothing and cosmetics items. Applications span the invention of toilet paper to the recycling of denim pants into vehicle construction components. 100% cotton is printed on tags of countless items of clothing and on signposts leading to a special exhibition at the Übersee-Museum (overseas museum) in Bremen, Germany. The exhibition offers a fascinating look at cotton’s cultural history and shares surprising, new, but also controversial stories about the soft fiber (www.ueberseemuseum.de/en/100-cotton).
Uster is proud that the curators of the Übersee-Museum considered the HVI as part of cotton’s essential history. The Uster cotton classing instrument was selected as an exhibit and visitors have the opportunity to try their hand as a cotton tester to determine color, length and price.
This year’s jubilee of Bremen Cotton Exchange played an important role initiating the special exhibition. The Bremen Cotton Exchange has been shaping the global cotton trade through its competence, neutrality and authority for 150 years.
Everlasting
The first evidence of cotton use was found in India and Pakistan, and dates back to around 6,000 B.C. That means cotton’s been keeping people dressed for over 8,000 years.
Cotton’s place in the world was even demonstrated during the recent pandemic times, when home-working became a necessity for many. In that situation, the need for smart office wear was replaced by an increased emphasis on comfort in everyday clothing. This sparked a trend for ‘sofa to street’ apparel which is still here today. People clearly love the gentler touch of their cotton gear, and that has translated into a real fashion choice.
One apt description, first applied to Indian cotton was ‘Woven Wind’ –expressing the touch and feel of these fabrics. India was the foremost cotton processing country for hundreds of years, and it’s fitting that its traditions with the world’s favorite fiber still hold good today.
Cotton tuft About Uster Technologies
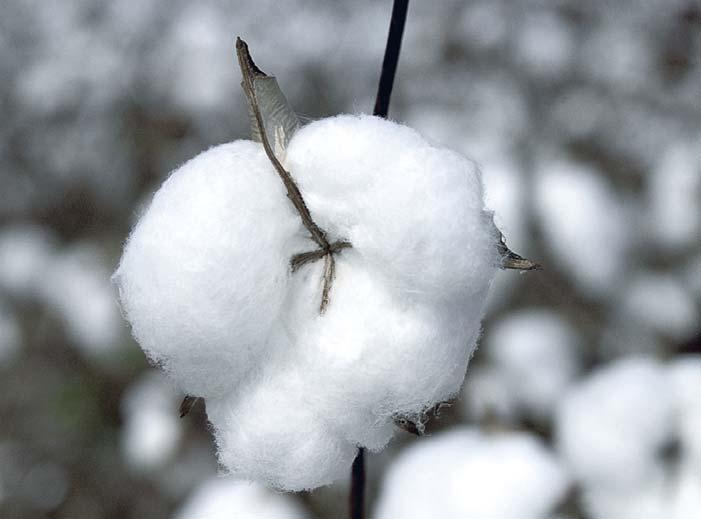
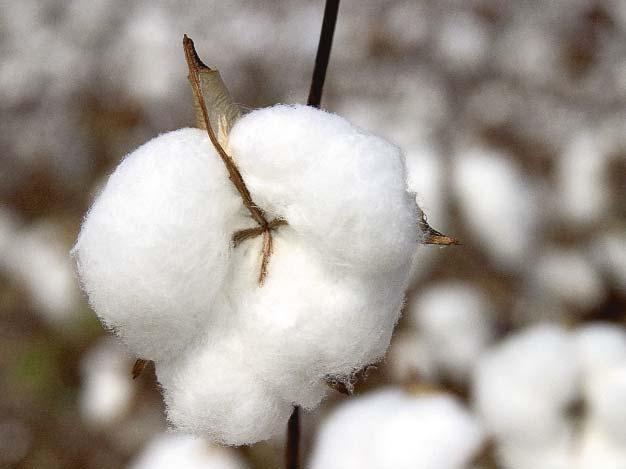
Uster Technologies is the world’s leading provider of quality management solutions from fiber to fabric.
High-technology instruments, systems and services cover quality control, prediction, certification and optimization. The portfolio comprises quality management, laboratory testing and inline process control instruments for fibers, staple fiber, and filament yarns, fabrics and nonwovens.
Uster Statistics, the unique global benchmarks for textile trading, complement a portfolio of value-added services that includes training, consultancy and worldwide after-sales.
The Uster philosophy aims to drive innovation forward by meeting market needs – always with ‘quality in mind’.
Uster Technologies is headquartered in Uster, Switzerland and operates worldwide. It has sales and service subsidiaries in major markets and Technology Centers in Uster (Switzerland), Knoxville (USA), Suzhou (China) and Caesarea (Israel).
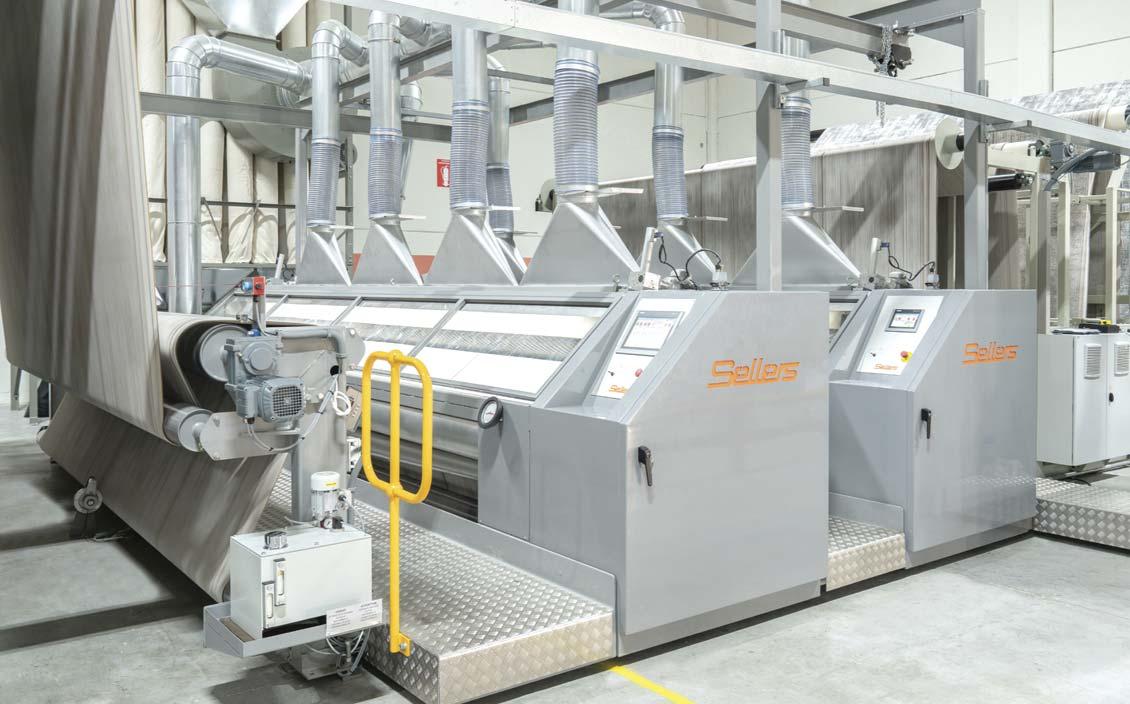
Sellers Textile Engineers: Hybrid Shear for carpet manufacturing
BTMA member Sellers Textile Engineers is marking its 110th anniversary this year with the introduction of an entirely new concept in carpet shearing, as the essential final step in ensuring tuft uniformity and ‘just new’ freshness in finished carpet rolls.
The company has for many years offered two options in the construction of its shearing cylinders – the first, namely the ‘strap-on’, incorporates spiral blades bolted to the cylinder body and the second, known as the ‘caulked-in’, includes spirals which are fixed very securely in a machined groove within the machine.
The new Sellers’ Hybrid Shearing Cylinder combines the benefits of both, resulting in an improved cut and finer finish, in addition to longer repeatable finishing and increased rigidity.
“The Hybrid Shearing Cylinder has all the advantages of the ‘strap-on’ spiral blade to provide a sharper and cleaner cut, along with enhanced rigidity which significantly lengthens the intervals between the necessary regrinding of the blade,” explains Sellers Director Neil Miller. “We currently have six Hybrid Shearing Cylinders operating in the field and the earliest, which has been installed in both No1 Head position, where the majority of the shearing operation and heaviest cut is performed, and also in No3 Head, where the sharper cutting angle has resulted in a much improved surface quality.”
Sellers shearing machines have led the field in carpet finishing for many decades, enabling the leading manufacturers to stay competitive by enabling the highest quality of finish to be achieved economically and efficiently.
The latest advanced features of these machines include a load cell tension control drive system, an automated touchscreen for easy operator control and fault diagnosis, an enhanced cleaning system including cylinder and blade separation and fully controllable pivoting beds. Further options include thickness monitoring, seam detection and metal detection systems.
“The Hybrid Shearing Cylinder will become standard on our latest machines and also be made available for retrofitting, to provide significant benefits to our existing users,” says Miller. “All of our equipment is designed, manufactured, assembled and tested at our plant in the UK, and as one of the few remaining European engineering companies to make all of our components in-house – with now over a century of accumulated know-how – flexibility in design allows our finishing solutions to be targeted to specific customers and their product requirements. Aligned to this is a lead in process control systems which ensure the accurate control, reliability and repeatability of the processing parameters on all of our machines.”
Sellers remains committed to providing complete finishing solutions for all carpet, tile and artificial grass products. Its range includes machines for tufted secondary backing, both conventional, powder and extrusion lamination, Wilton and Axminster products, artificial grass and foam lines, coating lines for bitumen,
PVC, PU and other polymers, as well as shearing for all carpet products.
Ongoing developments on the company’s coating and drying lines have resulted in improved guiding and product tension control as well as dryer efficiency, reducing heat loss and optimising energy use. These include a re-design of the fan pressure boxes and impingement nozzles to increase airflow efficiency, modulating gas burners and introducing easy clean, accessible filters.
In addition, the proven dual zone system has been enhanced, giving a temperature differential of up to 80°C between top and bottom zones. Dryers can be heated by either gas or steam and operation and access have been simplified with controls via touchscreen and PLC.
An extensive range of ancillary equipment is available to provide maximum flexibility to cover product requirements, for both new processing lines and as upgrades to existing equipment.
“Carpet manufacturing is now based on well-established, tried and trusted processes and it’s rare for new innovations to be introduced into this sector,” says Jason Kent, CEO of the British Textile Machinery Association. “The new Sellers Hybrid Shearing Cylinder can provide a competitive edge for manufacturers which is currently being proven in the field. It’s one of a number of new innovations the company is planning to showcase at next year’s ITMA exhibition in Milan.”

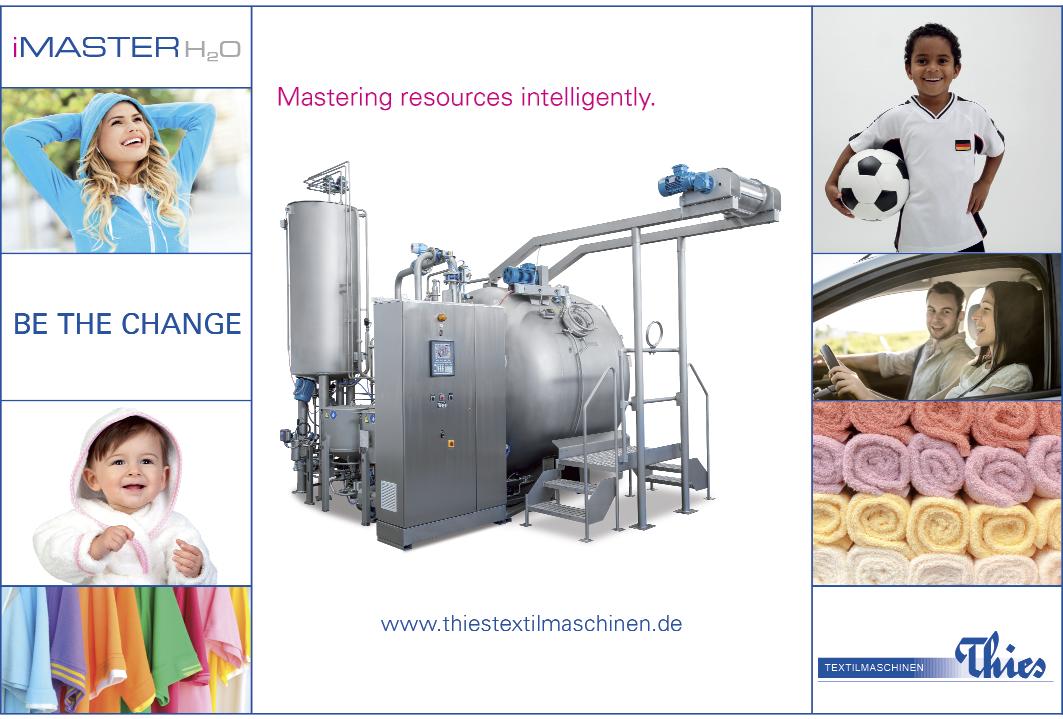
Seeing beyond the patterns with Shelton Vision
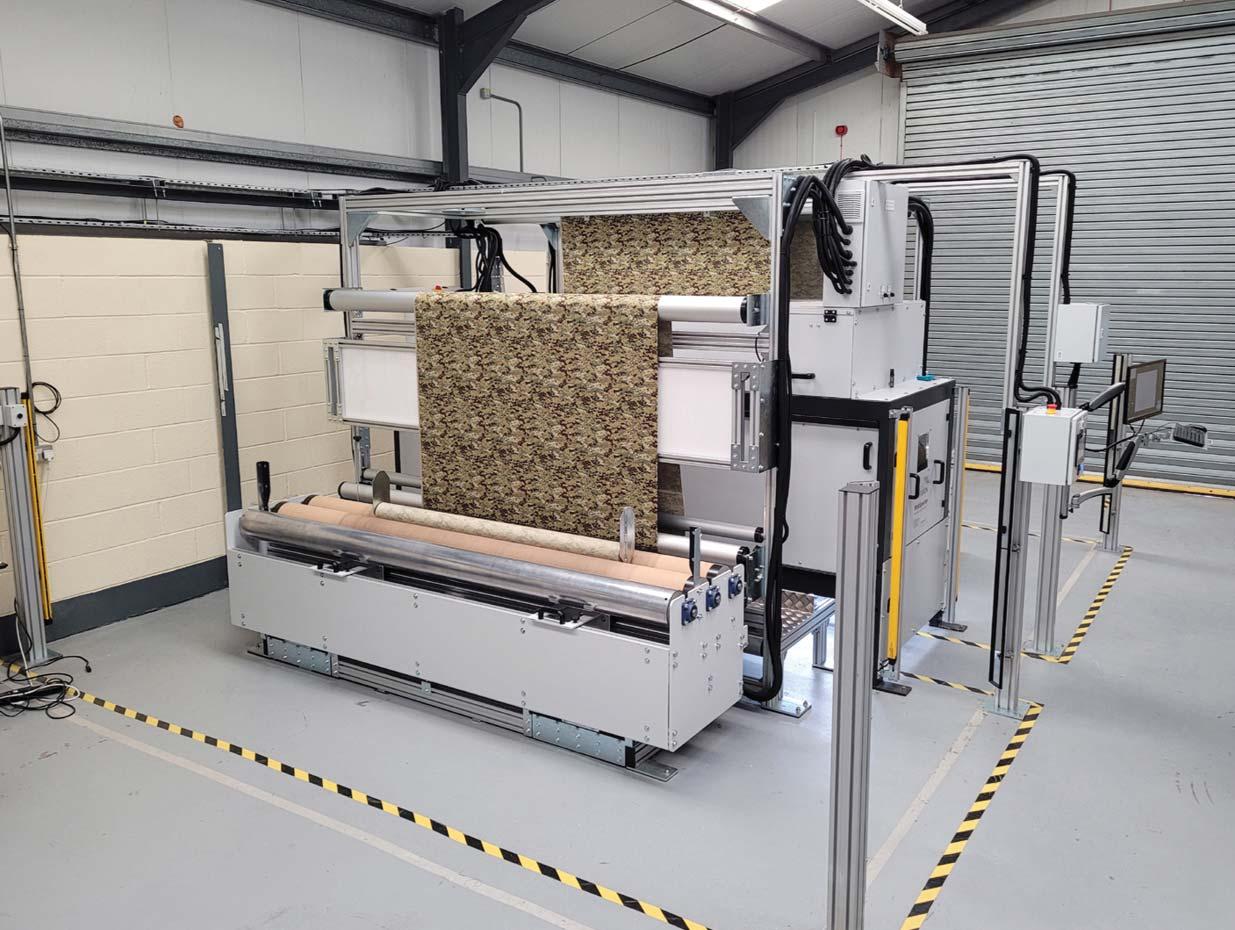
The patent-pending system has been validated through factory trials on a purpose built full scale inhouse demonstration system.
A ground breaking and unique new fabric inspection technique for accurately detecting the most subtle of defects on patterned fabrics during high speed production has been developed by Shelton Vision, of Leicester, UK.
The patent-pending system has been integrated into the company’s WebSpector platform – already the most powerful plain fabric inspection system on the market – and validated through factory trials on a purpose-built full scale in-house demonstration system with sophisticated fabric transport capabilities.
As a result, a first system has already been ordered by a manufacturer of both plain and patterned fabrics, including camouflage, in Colombia.
This follows the successful conclusion of a 21-month Innovate UK project in which techniques for the resolution of complex pattern deformations were developed by machine vision and computer scientists in the company, backed up by the machine vision and robotics department at Loughborough University.
Restrictions
Traditional methods for defect detection rely on human inspection which is ineffective, with detection rates under 65%, while the Shelton WebSpector machine vision system offers a sophisticated platform for automated defect detection of over 97%, but until now has been restricted to plain textiles.
“What our new system basically does is essentially make the ‘good’ pattern invisible to the detection software,” explains Shelton Vision Managing Director and CEO Mark Shelton. “Building on our market leading vision system for plain textiles, we have developed template matching techniques for the resolution of complex pattern deformations in order for the system to pick up defects in the pattern as well as underlying defects.”
While pattern matching and neural network approaches have previously been tried for patterned textiles they have failed to provide a practical solution due to the extreme complexity associated with pattern matching on deformable substrates like textiles, as well as the time required to train a neural network for each pattern type.
Challenges
“The challenge is that fabrics are not rigid and can be creased or stretched and are also subject to local distortion,” says Mark. “As a result, inspection without the technique we have developed, would lead to thousands of false positives. Our sophisticated pattern inspection software techniques ensure a clean image, allowing the detection of faults on fabrics running at speeds of up to a hundred metres a minute.”
The full system consists of:
A camera and lighting system for optimum image capture at high speed and associated image processing hardware.
Self-training software utilising statistical analysis to automate the system configuration for new textile products. An advanced suite of defect detection algorithms for the detection of all textile defect types. An AI-driven defect classification system which learns and automates defect naming in real time, as well as a real time defect grading capability based on client decision rules. A system for recording and retrieving complete roll map images for subsequent review and quality control.
The generation of textile roll maps with complete defect data allows for an optimised textile cut plan, improved downstream processing and quality assurance.
“Defect detection represents a major industry challenge,” says Jason Kent, CEO of the British Textile Machinery Association. “The failure to provide textiles within defect tolerance limits can lead to whole batch recalls, resulting in costly customer claims and downstream production delays.
Poor defect management is also a major source of industrial waste. The potential addressable market for patterned textile vision systems is estimated to be well in excess of £5 billion when considering on loom, on knitting machine, in process and final finished fabric inspection. No other vision system on the market offers these features for patterned textiles, so it’s a great example of UK innovation at its best.”
Founded in 1940, the British Textile Machinery Association actively promotes British textile machinery manufacturers and their products to the world. The nonprofit organisation acts as a bridge between its members and the increasingly diverse industries within the textile manufacturing sector.
Jason Kent, CEO of the British Textile Machinery Association.
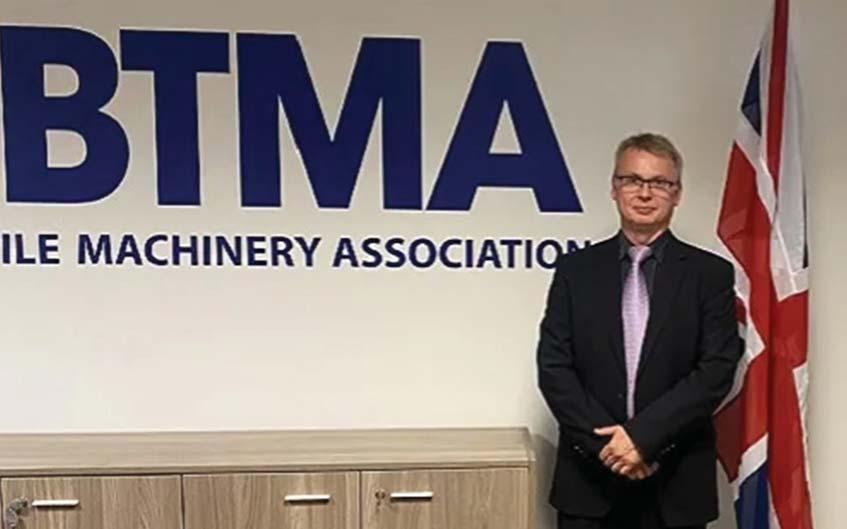
The Shelton WebSpector machine vision system offers a sophisticated platform for automated defect detection of over 97%.
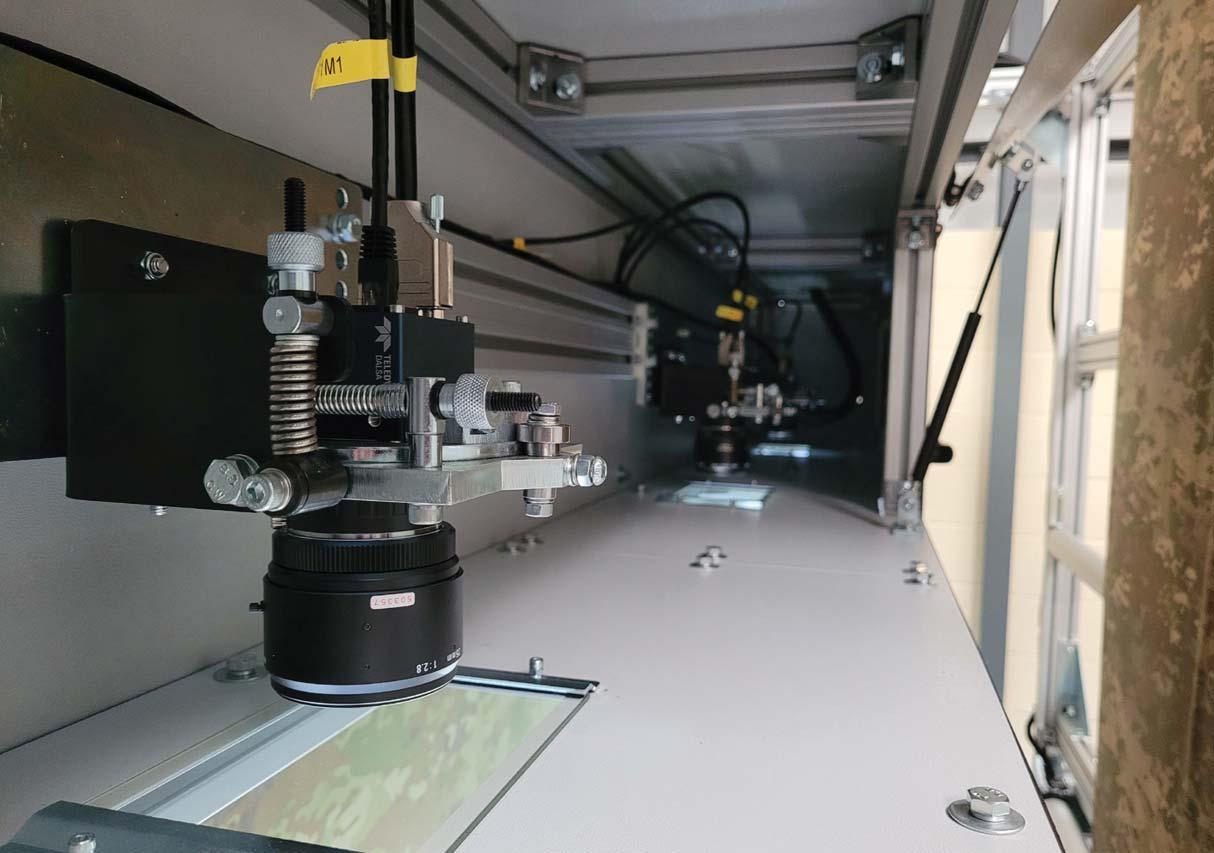