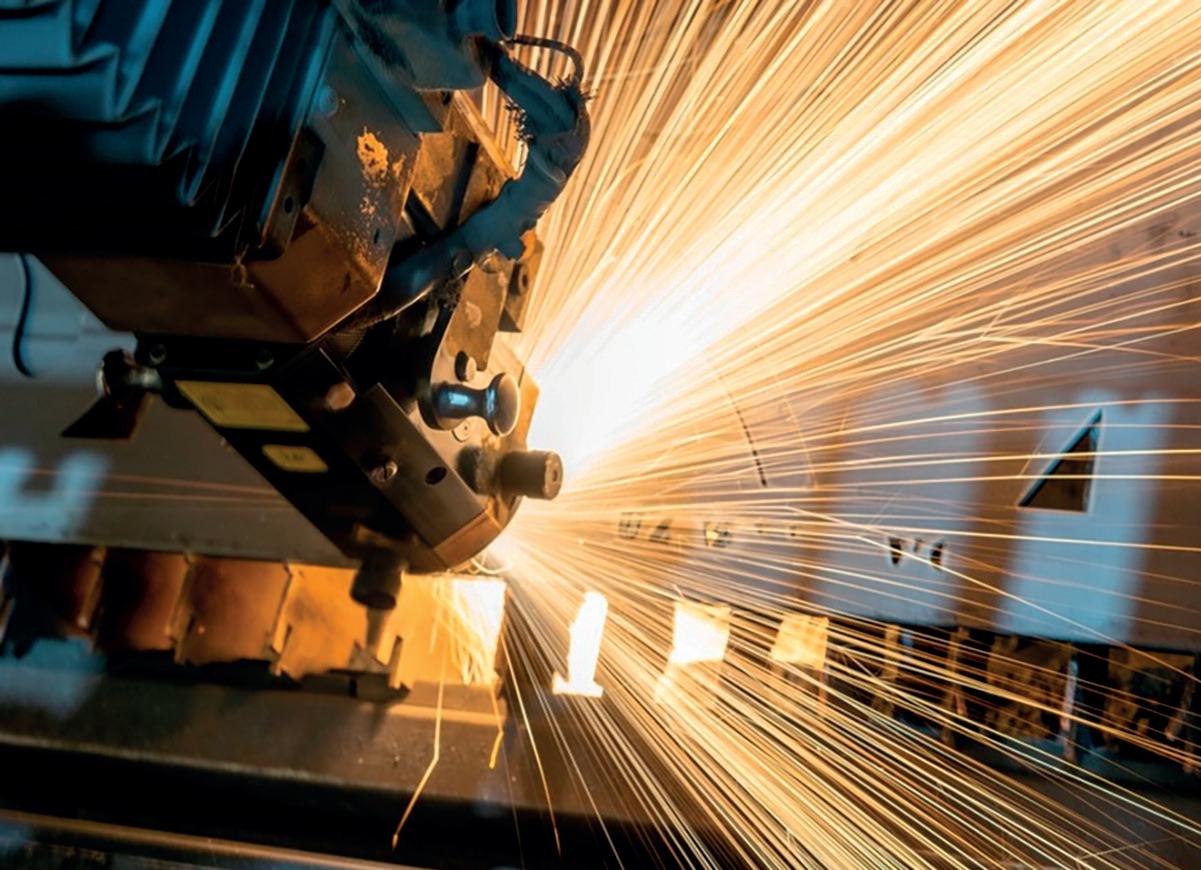
8 minute read
CONTROL AMBIENTAL
from Fluidos nº 452
by Publica SL
to con sustancias ácidas, poniendo en riesgo de contaminación al alimento procesado.
Los ingenieros deben tener en cuenta, también, el uso previsto del componente. Las máquinas que precisan una limpieza frecuente con soluciones agresivas deben ser capaces de soportar el entorno en el que están instaladas y resistir, al mismo tiempo, elevados niveles de estrés. Los materiales que precisan de bajo mantenimiento son también muy beneficiosos para las compañías que buscan mejorar la eficiencia de la producción, ya que tienen que dedicar menos tiempo a realizar la revisión y el mantenimiento de las piezas.
Liderazgo de mercado
En los últimos años hemos visto desarrollarse materiales resistentes que son capaces de soportar un elevado estrés, pero ninguno sobresale más que la reciente adopción de componentes cerámicos.
Los componentes cerámicos presumen de tener excelentes niveles de dureza, resistencia al desgaste, resistencia a la temperatura, resistencia al impacto, resistencia a la abrasión e incluso tener propiedades antiadherentes, permitiendo así que los procesos y las operaciones de las máquinas puedan ser más seguros y orientados hacia la calidad. Una industria que ya se ha beneficiado de las propiedades robustas del material es la de maquinaria herramienta, donde el material alternativo ofrece una aplicación muy precisa al tiempo que no muestra prácticamente signo alguno de desgaste, incluso después de un uso intensivo.
El material también es una buena elección para aplicaciones con cargas mecánicas exigentes gracias a su elevada resistencia y dureza a la flexión; toda la gama cerámica de norelem está diseñada especialmente teniendo en cuenta la vida útil de los componentes.
Allí donde la higiene es un criterio fundamental, el acero inoxidable de aleación de alta calidad sigue siendo el líder en la elaboración de alimentos y en las industrias farmacéutica y sanitaria.
No se trata solo de que el material pueda gestionar funciones de elevado estrés gracias a su durabilidad inherente, sino que también su acabado suave no absorbente ofrece una superficie higiénica que no aloja gérmenes o sustancias químicas. La superficie de los tornillos y tuercas de norelem tiene una rugosidad de Ra 0,8 µm que mitiga el problema de que los picos o acanaladuras del metal puedan servir como terreno fértil para los microorganismos. El material tiene también una resistencia sobresaliente a la corrosión y soporta cambios extremos de temperatura, convirtiéndolo en uno de los materiales más versátiles del mercado.
Allí donde el movimiento es fundamental, nada soporta mejor un alto nivel de estrés que los guiados lineales. Cuando se combinan con accionamientos de correa dentada y guías de perfil, el sistema de raíl es capaz de absorber las máximas fuerzas en todas las direcciones y ofrecer al mismo tiempo una excelente resistencia al desgaste. Las guías lineales están optimizadas para mover grandes masas sin necesidad de un mantenimiento continuo, siendo la solución ideal para transportar pesadas cargas en un entorno donde la eficiencia en la producción es fundamental.
La solución de norelem
El desgaste y la abrasión plantean un reto constante a la industria manufacturera, donde las piezas y los componentes de las máquinas deben resistir en una gran variedad de entornos, y por ello los ingenieros deben considerar muchas variables antes de iniciar la producción. Norelem es especialista en la fabricación de componentes de alta calidad que son fundamentales para prevenir las paradas y resistir un uso intensivo.
Norelem ofrece una gama completa de piezas con sus más de 60.000 componentes, incluidos cerámicos y de acero inoxidable.

Dürr entrega una de las mayores plantas de RTO del mundo a Yisheng Petrochemical
El grupo químico Yisheng Petrochemical Co., Ltd. confía desde 2010 en las tecnologías de purificación de aire de Dürr. La inversión más reciente en Ningbo/Zhenhai, al este de China, incluye un total de siete sistemas de control de contaminación del aire mediante regeneración térmica.
Estos sistemas garantizan una purificación segura de las corrientes de aire de escape contaminado con un ahorro de energía y reducción de CO2 a gran escala. El resultado es una de las mayores instalaciones de oxidación térmica regenerativa (RTO) del mundo, con una capacidad de tratamiento de 2,31 millones de m3 por hora. Para Dürr, el proyecto es uno de los más grandes de su categoría hasta la fecha.
En su planta en Ningbo en la provincia de Zhejiang, en el este de China, el grupo químico Yisheng Petrochemical Co., Ltd. produce principalmente ácido tereftálico purificado (PTA). El PTA se necesita como materia prima para el polímero más importante en la industria del plástico con el fin de producir botellas, textiles y recipientes de alimentos. Yisheng Petrochemical es uno de los principales productores de PTA del mundo y, por tanto, la capacidad de producción en Ningbo es una de las mayores que existe. Dos de las siete nuevas líneas de producción de este gigante químico producen tres millones de t de PTA al año cada una. Un reto específico en la producción del polvo incoloro son las corrientes de aire de salida parcialmente contaminadas. Por ello, se confió nuevamente en Dürr para instalar sus sistemas Oxi.X RE. Estos sistemas, basados en la oxidación térmica regenerativa (RTO), eliminan los componentes nocivos del aire de salida generado durante la producción de PTA. De esta manera, Yisheng Petrochemical se asegura de que no se escapen gases de salida contaminantes a la atmósfera.
Excelencia técnica para el control efectivo de la contaminación del aire
Dürr suministró a Yisheng Petrochemical siete sistemas Oxi.X RE idénticos, llave en mano, para el proceso de oxidación térmica regenerativa, cada uno equipado con un sistema Sorpt.X SW de lavado de gases tipo scrubber. Cada sistema se compone de un Oxi.X RE de nueve torres, seguido de una columna de lavado y una chimenea para el aire purificado. La capacidad de tratamiento de un sistema RTO de nueve torres es de aproximadamente 330.000 Nm3/h, representando una de las mayores instalaciones RTO del mundo, con una capacidad de tratamiento total de 2,31 millones Nm3/h para las siete unidades.
En las unidades RTO, el aire de salida de proceso contaminado pasa primero a través de un intercambiador de calor regenerativo de material cerámico. Esto calienta el aire entrante quedando muy cerca de la temperatura de reacción antes de llegar a la cámara de combustión. En la cámara de combustión del sistema RTO todos los contaminantes se convierten en componentes inocuos al exponerlos a la temperatura de combustión adecuada. Los gases, que ahora están purificados, pasan de nuevo a través del intercambiador de calor donde liberan
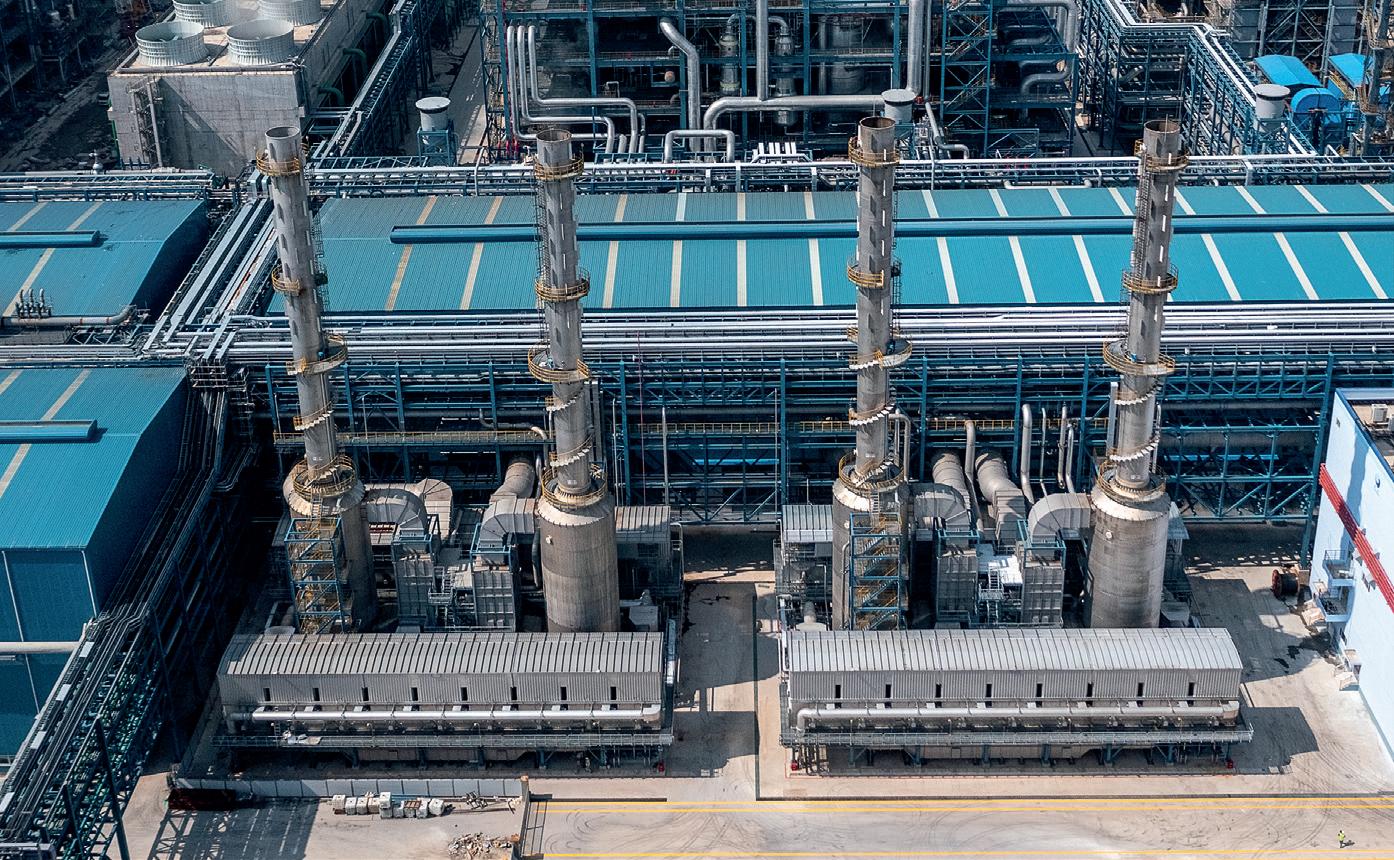
su energía al material cerámico. Así se completa el ciclo térmico regenerativo. Después de la oxidación total de los compuestos orgánicos volátiles (VOC) en las unidades RTO, el lavado por vía húmeda elimina el bromo y otros compuestos halogenados formados durante la combustión del gas de proceso. Finalmente, se emite el aire limpio a la atmósfera a una altura de 60 m a través de la chimenea, instalada sobre el scrubber.
Economía y eficiencia energética pese a sus grandes dimensiones
En unos meses, cuatro de las unidades RTO instaladas en Yisheng Petrochemical se pusieron en funcionamiento y operan desde julio de 2021, mientras que las tres unidades restantes se pusieron en marcha en enero de 2022. Se utilizó un total de 1.340 t de acero al carbón y acero inoxidable para las unidades RTO y sus conductos, así como más de 200 válvulas de asiento, más de 220.000 piezas de material cerámico y más de 150 km de cable. Para Dürr, este proyecto es uno de los más grandes de su categoría hasta la fecha.
Todos los sistemas de RTO construidos por Dürr tienen una eficiencia de destrucción y eliminación (DRE) de casi el 100%, requisito indispensable para cumplir con los límites de emisión cada vez más estrictos en China, y en todo el mundo. Los sistemas RTO de Dürr son económicos y ecológicos y tienen un bajo mantenimiento gracias a sus válvulas de asiento sin sellado, colocadas horizontalmente, y por su fácil acceso en caso de que se realice una inspección.
Optimizados energéticamente, los sistemas de oxidación de Dürr pueden operar sin combustible adicional y el combustible fósil solo se necesita en el modo de calentamiento. Autosuficientes con el aporte de energía contenido en el aire de salida del proceso, las unidades RTO contribuyen a reducir la huella de carbono del cliente al operar en modo autotérmico.

Sistemas de control de contaminación del aire de Dürr para la producción sostenible de PTA en China
El Grupo Dürr
El Grupo Dürr tiene representación directa en España desde 1974 y actualmente emplea a unas 210 personas. La sede central de Dürr Systems Spain, S.A., está en San Sebastián, además de contar con delegaciones en Barcelona, Valladolid y Madrid. La compañía ofrece gran parte de los servicios del Grupo. Aunque sus actividades se centran en las expansiones y modernizaciones de planta, Dürr Systems Spain también participa en proyectos nuevos llave en mano en España, Portugal y Marruecos. Entre sus clientes se incluyen fabricantes automovilísticos y aeronáuticos, la industria ferroviaria, así como aplicaciones domésticas y otras industrias. El Grupo Homag produce maquinaria y equipamiento para la industria maderera, dispone de un centro de producción (Homag Machinery Barcelona) y tiene sede de ventas y servicios cerca de Barcelona (Homag España Maquinaria, S.A.).
El Grupo Dürr es una de las empresas de ingeniería líderes en máquinas e instalaciones a escala mundial con destacada experiencia en automatización y digitalización/Industria 4.0. Sus productos, sistemas y servicios permiten procesos de fabricación muy eficientes y ahorrar recursos en diferentes industrias. El Grupo Dürr abastece a sectores como la industria automotriz, construcción de maquinaria, industria química, farmacéutica, tecnología médica y transformación de madera. En 2021 generó unos ingresos por ventas de 3.540 millones de EUR. El Grupo tiene 17.800 empleados y 120 delegaciones en 33 países, operando en el mercado bajo las marcas Dürr, Schenck y Homag con cinco divisiones:
• Paint and Final Assembly Systems:
Plantas de pintura, así como ensamble final, y tecnología de pruebas y llenado para la industria del automóvil, así como montaje y sistemas de pruebas para equipos médicos • Application Technology: Tecnología de robots para la aplicación automatizada de pintura, sellos y pegamentos • Clean Technology Systems: Sistemas de purificación para extracción del aire, sistemas de filtración de ruido y líneas de recubrimiento de baterías • Measuring and Process Systems:
Tecnología de balanceo y diagnóstico • Woodworking Machinery and Systems:
Maquinas y sistemas para la industria de transformación de madera.