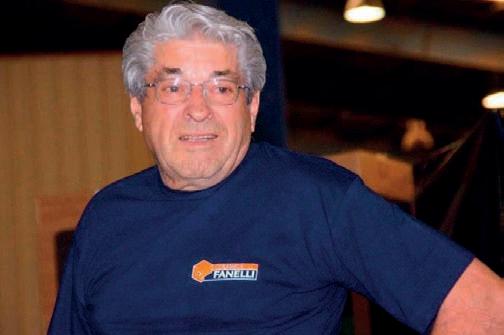
6 minute read
Companies
New plant Fanelli 3 focused on thermal efficiency
Cerámica Fanelli (Unicer Group), Argentina’s leading brick manufacturer founded back in 1949, started up its third production line in February this year. The new plant is designated Fanelli 3 and produces 2,000 tons of predominantly heat-efficient bricks per day. For more than 10 years the company has also been operating in the field of sustainable construction, a segment that is now enjoying a real boom in Argentina.
Nazareno Fanelli
According to figures compiled by the Cámara Industrial de Cerámica Roja (CICER), the country’s brick industry grew by 51.6% in 2021 and met high energy efficiency requirements even in the most extreme climatic zones. Automation and energy savings are the main characteristics of the new production line, the latest investment by the Unicer Group which has allocated more than $50 million to cutting-edge technology in recent years.
Cerámica Fanelli’s founder, Nazareno Fanelli, talked to us about the strategies behind the new project.
Question: What goals have you set yourselves with the new production line?
Nazareno Fanelli: Our biggest goal is to strengthen our market presence in the fast-growing sustainable building segment. The new plant involved an investment of $7.5 million and as well as significantly reducing energy consumption and improving product quality, it will allow us to increase production capacity initially by 20% (equivalent to 2,000 tons/day) to reach 2,400 tons/day in a subsequent stage. The line was installed in the new 9,000 m2 facility and is equipped with exclusive Italian-made technology: two extrusion lines, one supplied by Bedeschi and the other by Bongioanni; cutting, loading and unloading equipment, tunnel dryer and setting machine supplied by Marcheluzzo; circuit boards and software for automatic dryer control from Omega; as well as numerous dies made by Tecnofiliere using innovative tungsten carbide technology to guarantee constant stability throughout the entire extrusion process. Our partnership with Tecnofiliere’s owner Paolo Pedrielli dates back a number of years and continues to be very valuable thanks to the constant support, professionalism and high quality of the products supplied by the company.
What is driving the growth of green building in Argentina?
The Argentine government has launched several measures to promote energy efficiency in both new and existing homes. Some of these actions have been co-financed by the European Union, such as energy labelling of homes and the GEF (Global Environment Fund) project entitled “Energy Efficiency and Renewable Energies in Social Housing in Argentina”, which aims to cut greenhouse gas emissions by reducing energy consumption in social housing. The GEF aims to develop bioenvironmental design strategies, to promote energy efficiency measures and to introduce renewable energy in social housing construction. All of this activity is driving up demand for thermally efficient bricks, the factor that prompted us to make this latest investment.

Extruder dies Extruded clay columns
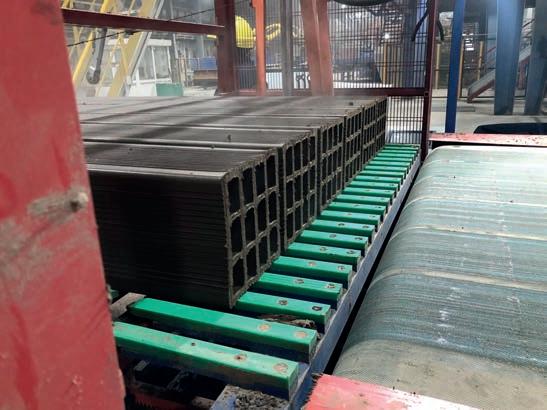
But after all, you have a good start given that brick is itself already a sustainable solution.
That’s right. The brick-making process uses organic materials such as clay, washed sand and rice husks. The quarries are located close to the factories, and the raw materials are subject to strict controls in accordance with applicable environmental regulations. Moreover, contrary to what one might think, brick production in Argentina accounts for just 1.4% of the energy consumed by the country’s entire manufacturing industry. The data are highlighted in the report entitled Informe de Diagnóstico del sector de Cerámica Roja. Octubre 2019 and produced as part of the energy efficiency cooperation project between the European Union and Argentina. Towards the mid-1990s, the Argentine heavy clay industry embarked on a process of modernization, incorporating cutting-edge technology that allowed for a significant reduction in energy consumption. In addition, the fact that the facilities are located nationwide makes it easy to supply products to a large part of the country with lower transport costs and a significant reduction in CO2 emissions.
Renewable energy and zero waste: what’s the current situation?
We are currently using 20% renewable energy for our energy requirements, a percentage that we plan to gradually increase in the coming years. Waste generated during the production process is completely recycled and reused within the facilities, all of which are environmentally certified.
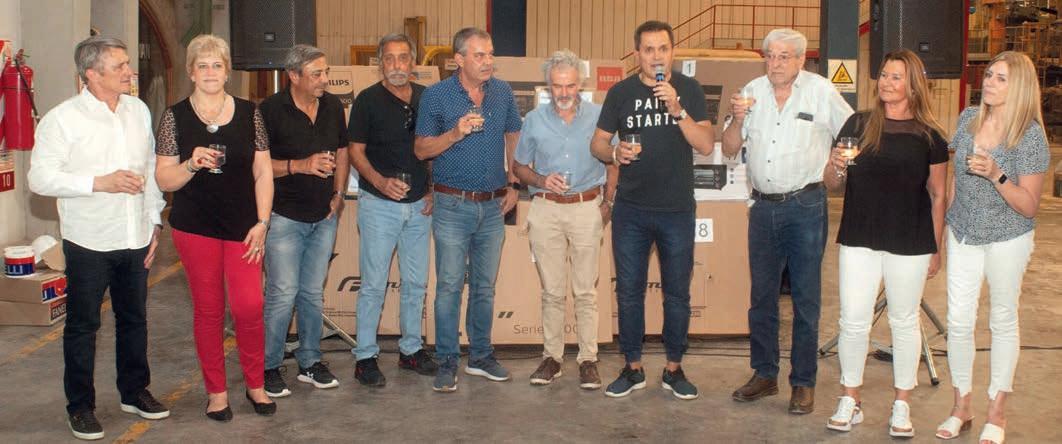

Extruder die store
What is your flagship product?
Our most popular product amongst modern building professionals is the DM20 (Doble Muro 20), which saves up to 40% on gas and electricity bills. Its special design with a larger number of air chambers helps maintain a more stable ambient temperature, as well as offering the heat resistance of a double wall with a single brick, thereby speeding up construction time and saving on labour and materials.
It is made of clays of natural origin and the end product is fireproof, non-toxic, durable and non-polluting. It also offers a high degree of versatility in building design and construction. More broadly, what sets us apart from our competitors is our wide range of sizes (14 to be precise) with different thicknesses. In addition to the line of hollow and thermal insulation bricks, we also offer load-bearing blocks, columns, lintels, and floor blocks.
How are you organized in terms of research and development?
We are proactively and continuously in search of new ideas, which we follow up and experiment with in order to deliver state-of-the-art products. Our R&D department is made up of highly qualified engineers, geologists and professionals who analyze raw materials and processes. We are involved constantly in R&D. Tests and preliminary development projects are carried out in compliance with national laws in order to continuously improve the thermal transmittance of walls.
What impact are the pandemic and energy price rises having on your business?
These are certainly two major factors, but while we have learned to live with the pandemic, the inflationary situation is an ongoing risk that is causing us great concern. Compared to 2021 when sales grew by 15% and our order book increased by 36%, the outlook is a little more uncertain in 2022, but we are confident that we can end the year with the same results.
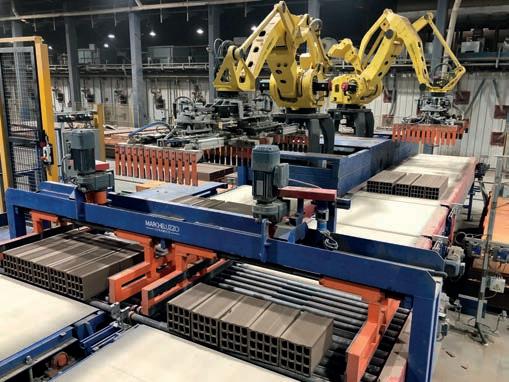
Handling with robots
Paradoxically, the pandemic has boosted construction activity all over the world. Has this also happened in Argentina?
Yes, it has. Since May 2020, following the prolonged lockdown, people have felt the need to improve their homes and make them more spacious and comfortable. This has led to a surge in demand for building materials, which we expect to continue in light of the country’s housing deficit, which is increasing by around 10% annually and now stands at 3 million homes. The government is proposing various schemes to help people purchase first homes, but the lack of low-interest mortgages is slowing down sales.
What will be your next step?
As I mentioned, we plan to increase the production capacity from 2,000 to 2,400 tons/day. A further step will involve making investments to improve the raw material pre-processing line and increase its storage capacity. At a group level we are modernizing the Later Cer, Palmar, Cunmalleu and Rosario plants to increase output by about 50,000 tons/month. We are determined to focus on the future of construction and to try to look ahead and anticipate needs. Unicer, which also includes Ceramica Quilmes, is a steadily evolving group that employs more than 800 people and produces a total of 250,000 tons per month (equivalent to 3 million m2 of masonry products), supplying 60% of the domestic market. We aim to maintain this growth. ◆
