
6 minute read
Ahorro y eficiencia energética en hornos y secaderos
En este artículo Oxycomb Sistemas, S.L., describe la implantación del Sistema Optima®, analizador de atmósferas de combustión en continuo. En los tiempos que corren es necesario controlar y optimizar mejor los procesos de cocción y secado reduciendo los consumos de gas natural y electricidad y garantizando a la vez la calidad del producto.
Oxycomb Sistemas, S.L.
El mercado actual, cada vez más competitivo y exigente en sus estándares de calidad, obliga a cualquier industria relacionada con procesos de combustión a destinar una parte importante de sus recursos a optimizar y mejorar sus procesos productivos.
Hasta la introducción del control multizona de %O2, presión, CO-ppm, CO2, partículas y humedad la regulación de los hornos y secaderos cerámicos se realizaba considerando la curva de temperatura, la presión estática en un punto y la presión de aire y gas en quemadores. En los últimos tiempos, el incremento continuado del coste del gas natural y la electricidad y las exigencias en cuanto a calidad del producto han sensibilizado a los fabricantes de baldosas cerámicas a tomar medidas que ayuden a hacer más eficientes los procesos de fabricación.
Para optimizar el proceso de cocción es esencial medir en continuo los niveles de oxidación y presión a lo largo del horno. Del mismo modo, para la mejora del proceso de secado resulta esencial medir en continuo los niveles de humedad relativa del aire, la temperatura y presión en cada módulo.
Oxycomb Sistemas, sumándose a la nueva metodología de organización y gestión de los medios de producción, la “Industria 4.0”, implanta el Sistema Optima® en la industria cerámica persiguiendo los siguientes objetivos:
• Mejora en la calidad del producto final
• Reducción del consumo de energía: térmica y eléctrica
• Reducción, control y seguimiento de las emisiones contaminantes, especialmente CO, CO2 y NOx.
Dependiendo de cada modelo, los analizadores Optima® miden in situ, en continuo y de manera simultánea las siguientes magnitudes: %O2, CO-ppm, CO2, presión, temperatura, humedad relativa, partículas, etc., de los gases de combustión en el interior de la cámara de combustión. El intervalo de temperaturas de trabajo es muy amplio (50 ÷ 1.550 °C).
La centralita DataTracker permite la entrada, visualización y calibración de las medidas tomadas por cada analizador. Asimismo, está dotada de entradas/salidas analógicas y digitales y/o conexión Ethernet TCP para la comunicación con otros equipos de control en la red del cliente para su integración en el autómata del horno/secadero, la configuración de alarmas o la regulación PID de cualquier variable del proceso.
El software de supervisión y registro SAD50 muestra, para cada variable, gráficas en tiempo real, registro de históricos, sinóptico gráfico del equipo de combustión, alarmas, informes, recuento de emisiones, consumos, etc.
❖ Optimización del proceso de cocción cerámico
En una planta de baldosas cerámicas, el horno es el elemento de mayor consumo de energía y la principal fuente de emisiones a la atmósfera. La gran variedad de formatos, el elevado valor añadido de los productos, la necesaria oxidación controlada de los carbonatos y el alto consumo de energía de estas instalaciones hacen esencial el análisis en continuo de las atmósferas de combustión en este tipo de hornos.
La variación del %O2 presente en los gases estará siempre sujeta a cada tipo de producto y formato, es decir, a cada curva de temperatura, disposición de presiones de gas / aire en anillos y quemadores, la regulación por receta de los ventiladores de aspiración de humos, aire caliente, enfriamiento final, etc.
Zona de precalentamiento
La medida del %O2 es fundamental para garantizar tanto el rendimiento global del proceso de cocción como para asegurar un nivel de oxígeno suficiente que asegure una completa oxidación de la materia orgánica que evite defectos de calidad. Niveles reducidos de %O2 en esta zona (de 700 a 950 °C) pueden provocar una desgasificación incompleta y favorecer la aparición de corazón negro.
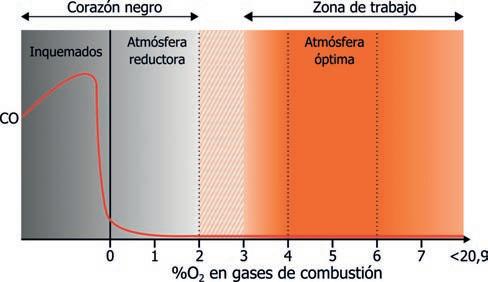
Zona de cocción
En esta zona es donde el ahorro de energía puede ser mayor. Una buena regulación de la presión de aire/gas de los quemadores y su balance con el exceso de aire contenido en los gases calientes que fluyen a contracorriente del producto, puede reducir el %O2 del 1 al 2%, lo que implica ahorros de combustible del 4 al 6%.
Zona de enfriamiento rápido
En la zona inicial del enfriamiento rápido, el %O2 medido debe ser elevado al encontrar únicamente aire limpio frío y no gases provenientes de la zona de fuego. Esta es la clave para minimizar las pérdidas de calor y evitar problemas en la zona final de cocción y principio de enfriamiento. Un control de las presiones en ambas zonas será fundamental para corregir cualquier desajuste (inversión de flujos) que provoque un trasiego de gases en la dirección incorrecta.
La cantidad de emisiones de CO2 producidas depende, entre otros factores, del exceso de aire introducido en el proceso de combustión. Se estima que por cada 1% de reducción de flujo de gases inquemados a través del horno, la reducción de emisiones de CO2 provenientes de la combustión será en torno al 3%.
Puntos de actuación
Del estudio de las curvas de presión, temperatura y %O2 obtenidas mediante el Sistema Optima®, se consigue mejorar la regulación del horno a fin de mejorar y optimizar el proceso. Los puntos de actuación sobre el horno de rodillos aparecen en la siguiente figura. Algunos de ellos se harán por receta suponiendo una regulación automática; otros, mediante ajuste manual de manera circunstancial.
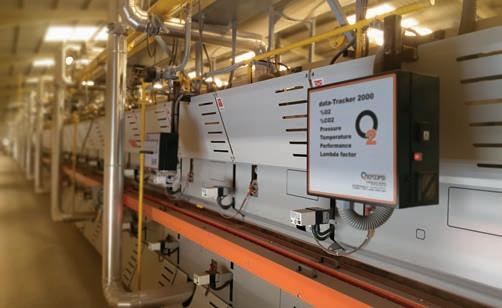
Resultados técnico-económicos
• Reducción del consumo específico por formato (4%-6%)
• Mayor control de la calidad (eliminación de corazón negro)
• Caracterización de los niveles de oxidación por formato, tipo de producto y esmalte (brillo/mate)
• Regulación optimizada de ventiladores
• Control de inversión de flujos en zona final de cocción – enfriamiento rápido
• Control de la curva de presión
• Disminución de emisiones de CO, CO2 y NOx
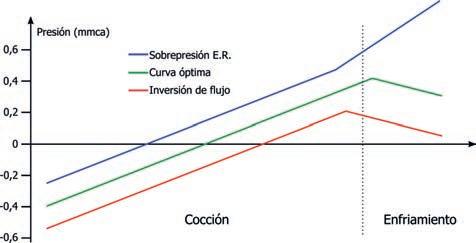
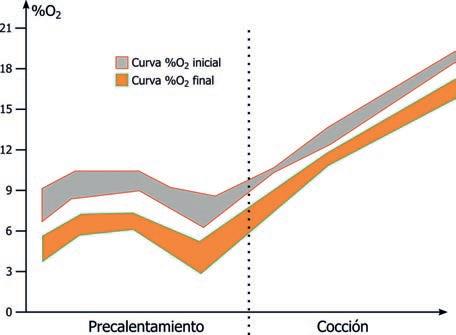
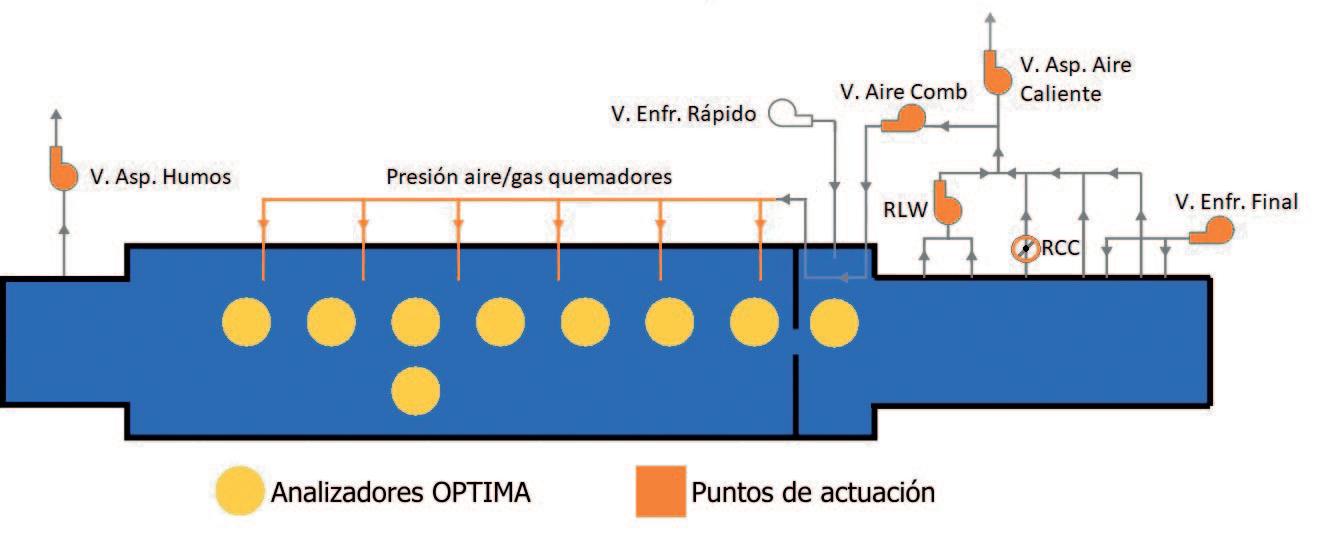
• Payback: menos de un año.
❖ Optimización del proceso de secado cerámico horizontal
En una planta de baldosas cerámicas, el secadero es el segundo mayor consumidor de energía. Los resultados que se pueden obtener regulando los distintos parámetros del secadero en función de la humedad relativa, la temperatura y la presión de los gases de combustión son inmediatos. Además, en los secaderos, cada zona requiere de una “atmósfera secante” diferente, lo cual obliga a un control exhaustivo de la extracción de humedad en todos los módulos para el mantenimiento de la misma.
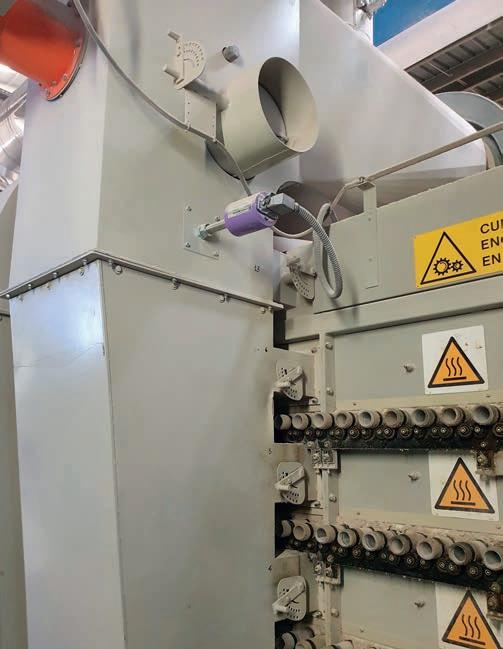
Zona de precalentamiento
En esta zona es donde el ahorro de energía puede ser mayor. La medida de humedad relativa (%HR) en los gases de expulsión es fundamental para garantizar tanto el rendimiento energético del proceso de secado como un adecuado nivel de calidad de las piezas al asegurar una eliminación de la humedad óptima y progresiva. Niveles de humedad excesivamente bajos en esta zona pueden provocar una retirada de calor innecesaria que favorezca un consumo excesivo de gas y luz y la aparición de grietas/explosiones en las piezas.
Zona de máxima temperatura
Una buena regulación del posicionamiento de las aperturas de válvulas en chimenea o de las frecuencias de estos motores de aspiración o de los de recirculación puede optimizar la curva de secado de una manera enorme, lo que implica ahorros de combustible y de electricidad muy considerables, por encima de los dos dígitos.
Uniformidad y control de huecos
El control de la temperatura a la salida del secadero permite conocer y uniformar las condiciones de trabajo en cada uno de los pisos del secadero. El control de la atmósfera secante dota de una mayor estabilidad al proceso de secado y a la adecuada eliminación de la humedad de las piezas.
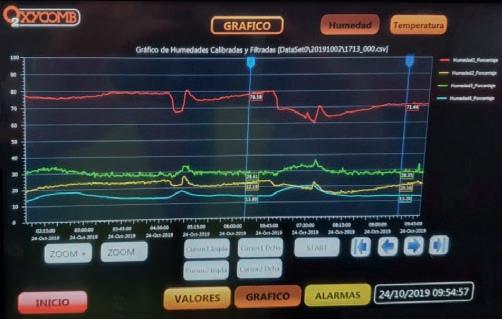
de consumo de gas y, por ende, de emisiones de CO 2 provenientes de la combustión será superior al 20%. La de luz será aún mayor.
Puntos de actuación
Del estudio de las curvas de %HR, presiones y temperaturas obtenidas mediante el Sistema Optima® se configuran las consignas más adecuadas a fin de mejorar y optimizar el proceso. El lazo de control controlará y regulará convenientemente el proceso.
Resultados técnico-económicos
• Reducción del consumo específico térmico (>15%)
• Reducción del consumo eléctrico (>30%)
• Mayor control de la calidad
• Caracterización de los niveles de humedad por formato, tipo de producto y esmalte (brillo/mate)
• Regulación optimizada de ventiladores de aspiración de aire húmedo y motores de recirculación mediante lazo de control
• Homogeneidad y uniformidad de atmósferas ante huecos
• Disminución de emisiones de CO2 y NOx
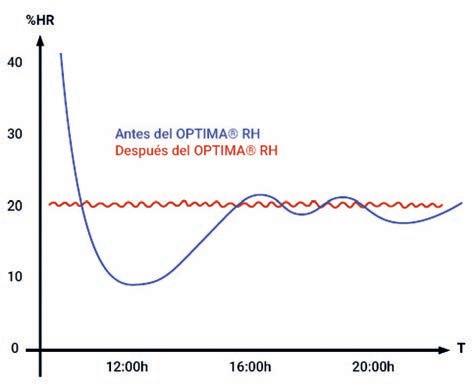
• Eliminación de condensados a la entrada del secadero (en caso de existir)
• Payback: menos de 1 año.
Al asegurar una humedad constante en cada zona, las piezas no sufren fuertes variaciones de secado ante la existencia de huecos en el secadero. Además, se garantizan importantes ahorros en el consumo de gas.
Esta es la clave para minimizar las pérdidas de calor. Un control con los analizadores Optima ® será fundamental para corregir cualquier desajuste. Se estima que, con un control efectivo de la humedad relativa y la temperatura en un secadero, ante la existencia de huecos, la reducción
❖ Ayudas / Subvenciones
Además, los fabricantes de baldosas cerámicas se pueden beneficiar de las numerosas ayudas y subvenciones públicas a la inversión englobadas en el Plan de Acción de Ahorro y Eficiencia Energética (fondos autonómicos, estatales y europeos). Oxycomb Sistemas, en su calidad de condición de asesor energético, facilita a sus clientes la gestión y tramitación de las ayudas o subvenciones que mejor se ajusten a sus intereses.