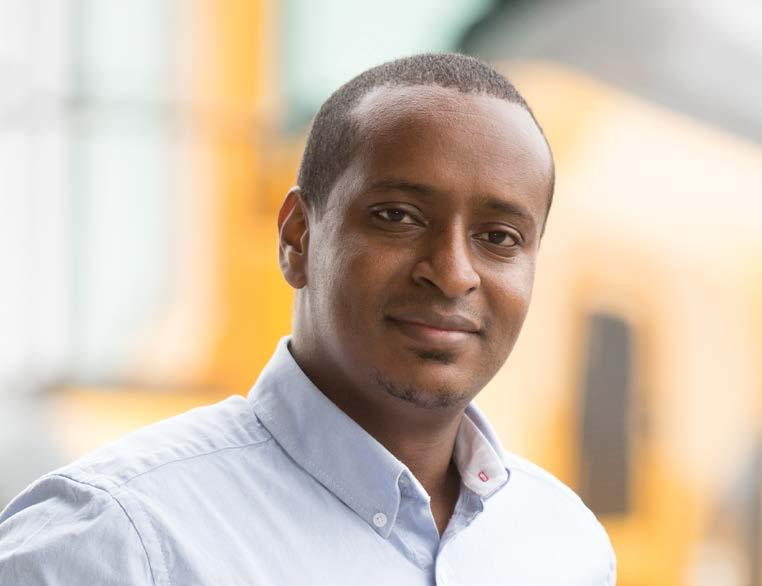
5 minute read
BOOSTING JOBSITE SAFETY
To help the industry achieve its zero harm targets, Volvo Construction Equipment has launched its Collision Mitigation System for wheel loaders. The automatic braking system supports operator response and helps reduce the risk or consequences of collision when working in reverse. By Munesu Shoko.
40-50%
Advertisement
Given that wheel loaders spend an average of 40-50% of their operating time being driven in reverse, Volvo Construction Equipment believes that the Collision Mitigation System is a valuable tool to boost jobsite safety
2-3 seconds
The braking action has a duration of 2-3 seconds, which effectively slows down the machine while prompting the operator to pay attention and take control
Given that wheel loaders spend an average of 40-50% of their operating time being driven in reverse, Volvo Construction Equipment (Volvo CE) believes that the Collision Mitigation System is a valuable tool to boost jobsite safety.
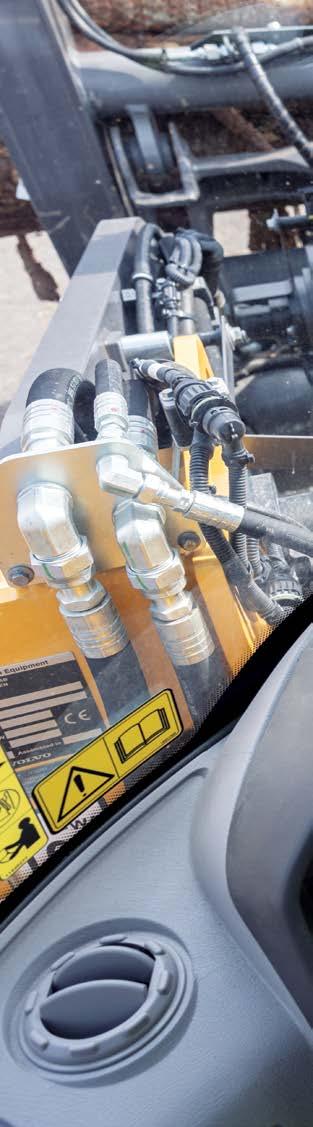
The system – said to be the first of its kind developed inhouse by an original equipment manufacturer – assists operators while working in reverse and automatically applies service brakes when the wheel loader approaches any obstacle, alerting the operator to take further action.
In a one-on-one with Quarrying Africa , Anteneh Gebremeskel, GPE product manager at Volvo CE, says while not designed to ever replace safe operator behaviour, the Collision Mitigation System is a smart tool to further enhance jobsite safety – a central focus and core value for Volvo since the company’s inception.
“Safety, quality and environmental care are our core values as a company and the cornerstones of our product development. We have a vision for zero accidents, so we build safety into every design element and work tirelessly to develop intelligent solutions that will not only mitigate the consequences of accidents but strive to avoid them altogether,” says Gebremeskel. “The new Collision Mitigation System for wheel loaders is an example of one such solution. It will help both experienced and novice operators
KEY POINTS
Volvo Construction Equipment has launched its Collision Mitigation System for wheel loaders
The automatic braking system supports operator response and helps reduce the risk or consequences of collision when working in reverse
The new Volvo Collision Mitigation System comes with smart software that detects slopes or objects present at the moment of driving past them forwards, so as not to mistakenly consider them as an object of collision risk while reversing in the same direction
The Collision Mitigation System is a factoryfit option currently available for the Volvo H-series wheel loader range, namely the L150H, L180H, L220H, L260H and L200H High Lift models, in the Middle East and Africa
“
The system is open for sales on models to improve safety on site.”
L150H to L260H in Africa, which represents a broad section of our wheel loader range. These models are part of the H-Series, which has all the enabling features for the system.
From a market perspective, Volvo CE has seen high demand for such safety features in Africa and elsewhere in the world. For quarrying and mining operations, says Gebremeskel, stringent safety regulations have become the order of the day to protect workers in such particularly hazardous working environments.
“South Africa is a good example of a market that is setting higher demands for safety technology such as Collision Mitigation Systems,” says Gebremeskel.
Range and availability
The Collision Mitigation System is a factory-fit option currently available for the Volvo H-series wheel loader range, namely the L150H, L180H, L220H, L260H and L200H High Lift models, in the Middle East and Africa. Currently, the system is only available to order on new machines from the factory. A retrofit kit is not available yet, but Gebremeskel tells Quarrying Africa that it will come in the future.
“The system is open for sales on models L150H to L260H in Africa, which represents a broad section of our wheel loader range. These models are part of the H-Series, which has all the enabling features for the system,” explains
Gebremeskel.
However, the system is not available on smaller models, as these form part of the F-Series, which lacks some of the enabling features required, including Volvo Co-Pilot. At the other end of the size scale, the Collision Mitigation System is yet to be developed for Volvo CE’s biggest wheel loader, the L350H.
“The Collision Mitigation System is an ongoing development. The reason we started with wheel loaders is the fact that the enabling components are readily available on these machines.
These include the radar detection system, the Volvo CoPilot and the Reverse By Braking (RBB) valve,” says Gebremeskel.
“The Collision Mitigation System is yet to be developed for haulers, but in the meantime, we are partnering with thirdparty suppliers to offer a proximity detection system for haulers. We would encourage any customers interested to discuss the opportunities available for such systems with their local Volvo dealer,” he adds.
How it works
The system works by identifying when there is a risk of collision and responding by automatically activating the brakes for 2-3 seconds to slow the machine down prior to impact or bring it to a stop to avoid it. This initiation of the braking alerts the operator to intervene. eliminating accidents – and therefore improving jobsite safety for everyone – but also reducing any unplanned interruptions that can be incurred during those avoidable knocks and bumps.
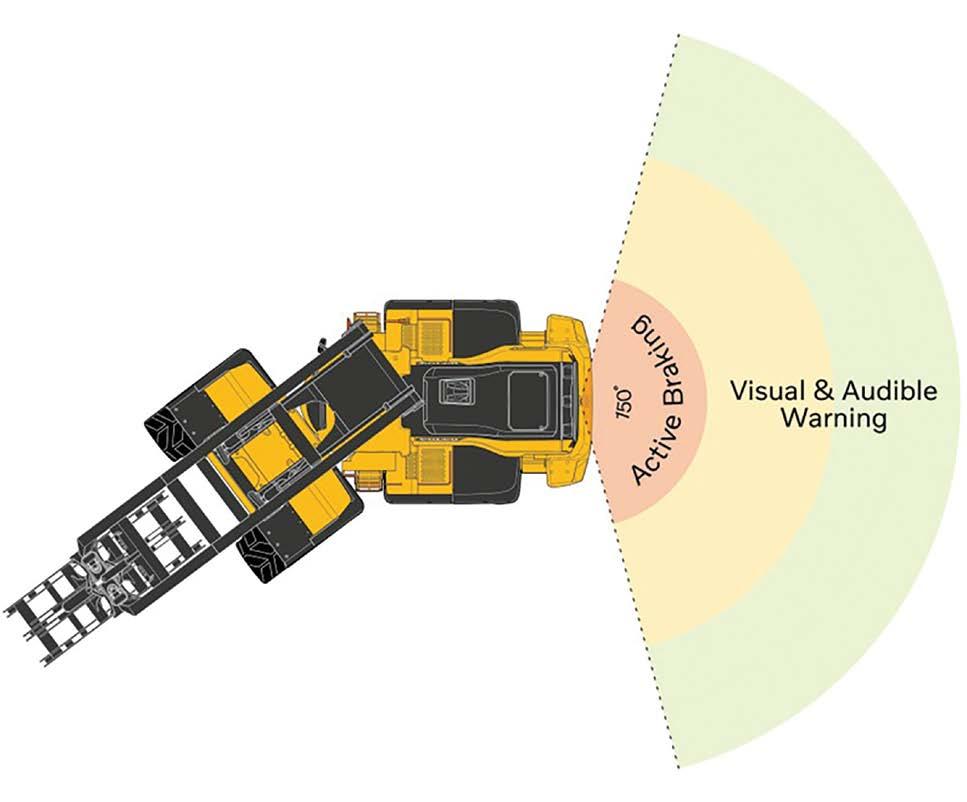
“Functioning only when the wheel loader is in reverse and driving at speeds of between 3-15 km/h, no matter what gear it is in, it serves as a facilitator to jobsite safety. However, even assistance systems like this cannot eliminate accidents, which is why Volvo CE always advocates for safe operator driving behaviour,” he says.
The new Volvo Collision Mitigation System comes with smart software that detects slopes or objects present at the moment of driving past them forwards, so as not to mistakenly consider them as an object of collision risk while reversing in the same direction. This enables the system to work with little disturbance while stockpiling or driving close to walls, for example.
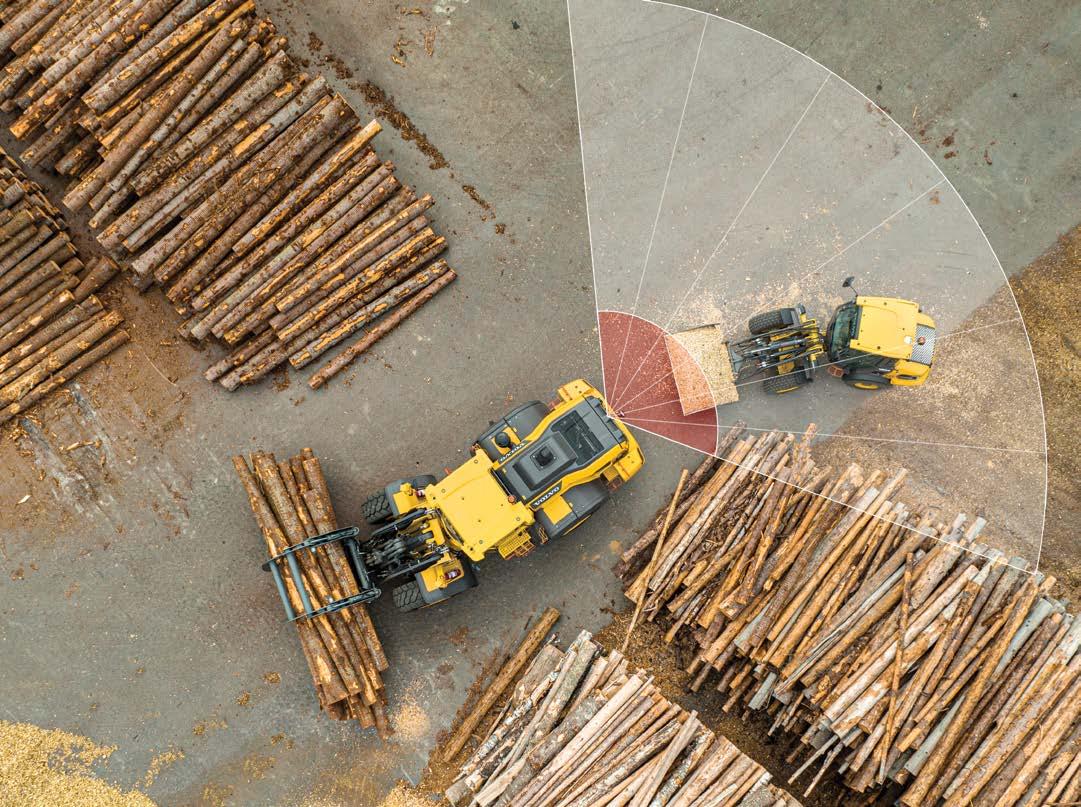
3-15
“This safety feature supports the operator before a potential collision incident by releasing an audible warning along with a visual warning on the Volvo Co-Pilot screen and, at the same time, applying the service brakes automatically in the event of object detection within the range,” explains Gebremeskel.
“The system is always active when the machine starts, but it is possible to temporarily deactivate. If manually deactivated, the system will automatically activate again after a 90-minute time lapse. It is designed to detect both stationary and moving objects,” explains Gebremeskel.
Key benefits
With this new system, he adds, customers are moving a step closer to not only
The braking action has a duration of 2-3 seconds, which effectively slows down the machine while prompting the operator to pay attention and take control. The operator still has full responsibility for the machine. The system works when gears are engaged or when the operator is coasting backwards in neutral.
“Requiring a Radar Detect System to be fitted, it works as an additional system to the existing wide range of features, options and site services provided by Volvo CE for its line of wheel loaders, all of which have been designed to elevate jobsite safety and minimise unplanned interruptions,” concludes Gebremeskel. a
Key
The DF514 has proven over the years to be one of the most robust and reliable compact scalping screens available on the market. Fully equipped with a 4,27 x 1,52 m double deck screenbox, the machine has one of the longest screen boxes in the compact screening segment.
27 000 kg
The machine weighs in at 27 000 kg in an apron feeder configuration, about 7 000 kg less than the larger DF518 model
Shaun O’Toole, Vermeer Equipment Suppliers sales manager
KEY POINTS
Having initially launched the larger DF518 scalping screen, Vermeer Equipment Suppliers is bringing the compact Anaconda DF514 model to the local market
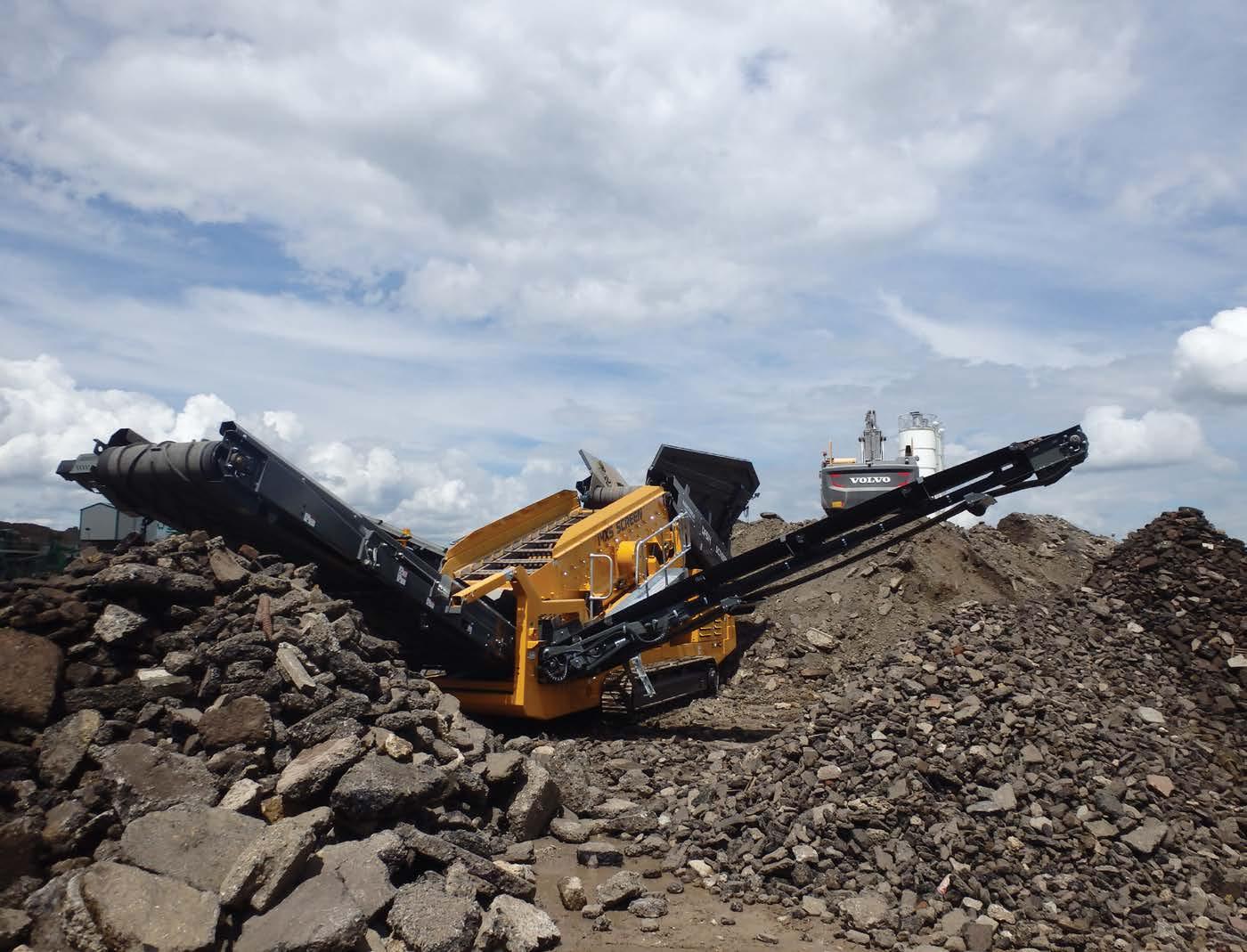
The first machine is expected to arrive during the second half of the year
With its compact nature, the DF514 fits the bill for entry level and mid-level contractor markets
The machine comes with either a belt or apron feeder, depending on customer preference