
41 minute read
Special Report: COVID-19 Update
COVID-19: Cleaning teams continue to work on the front line
Neil Nixon reports.
Following on from the features in the previous seven issues of C&M looking at the frontline role the cleaning sector continues to play in tackling the COVID-19 pandemic, I am continuing to migrate any news, new product information or video interviews/webinars online to allow for the more immediate dissemination of any updates. Please take a look at www.cleaningmag.com – content is changing on a daily basis.
I will continue to utilise the pages of C&M to focus on cleaning during the pandemic in detail and, as with this month’s column, to seek advice on best practice from recognised industry experts, and to learn from the experience of others.
PRACTICAL COVID-19 ADVICE FOR HIGH RISK AREAS WITHIN THE WORKPLACE
There is a lot of advice out there about safe working practices in the workplace relating to COVID-19, but this article focuses on those high risk, high traffic areas, including entrances, canteens, kitchens, and washroom facilities. What can you do to reduce the risk of contracting and spreading Coronavirus in these areas? Nina Wyers, marketing and brand director at The Floorbrite Group, has created a simple guide with ideas that are easily implemented to make a big difference.
Entrances High touch point door handles are obviously a huge issue in these areas as everyone in the building will have physical contact with them at more than one point throughout the day. What can you do? • Install hand sanitisers on both sides of the entrance ways so that only sanitised hands touch the door. Then re-sanitise on the other side. • If it is not practical to install external sanitisers due to being on a busy street and there is a risk of vandalism, then install on the inside of the building so all hands are sanitised following entry to the building. • Swap touch point fingerprint and button entry systems for individual key cards or fobs. • Clearly mark safe distancing from reception desks and consider installing screens to protect reception staff. • Install hand sanitisers outside lift doors or use antimicrobial lift button covers to eliminate viruses. • Ventilate the area well where possible. • Increase cleaning frequencies. • Use a combination of antibacterial and virucidal cleaners. The clue is in the name!
Antibacterial cleaners will only kill bacteria where as virucidal or anti-microbial cleaners will kill viruses and the later does both (NB: check which viruses the chemicals are effective against).
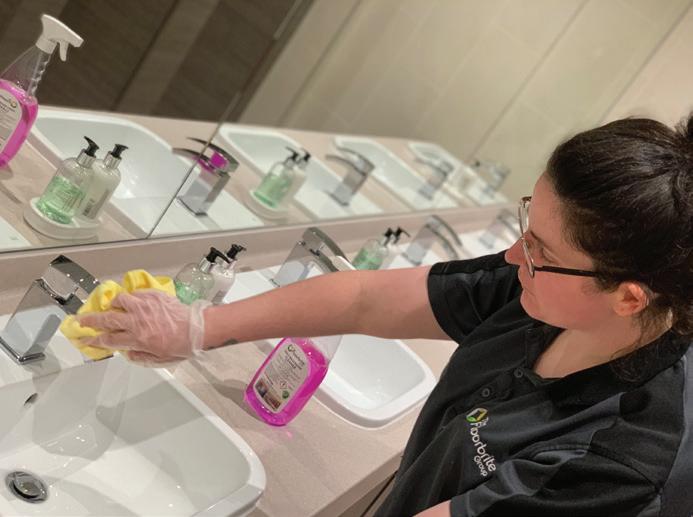
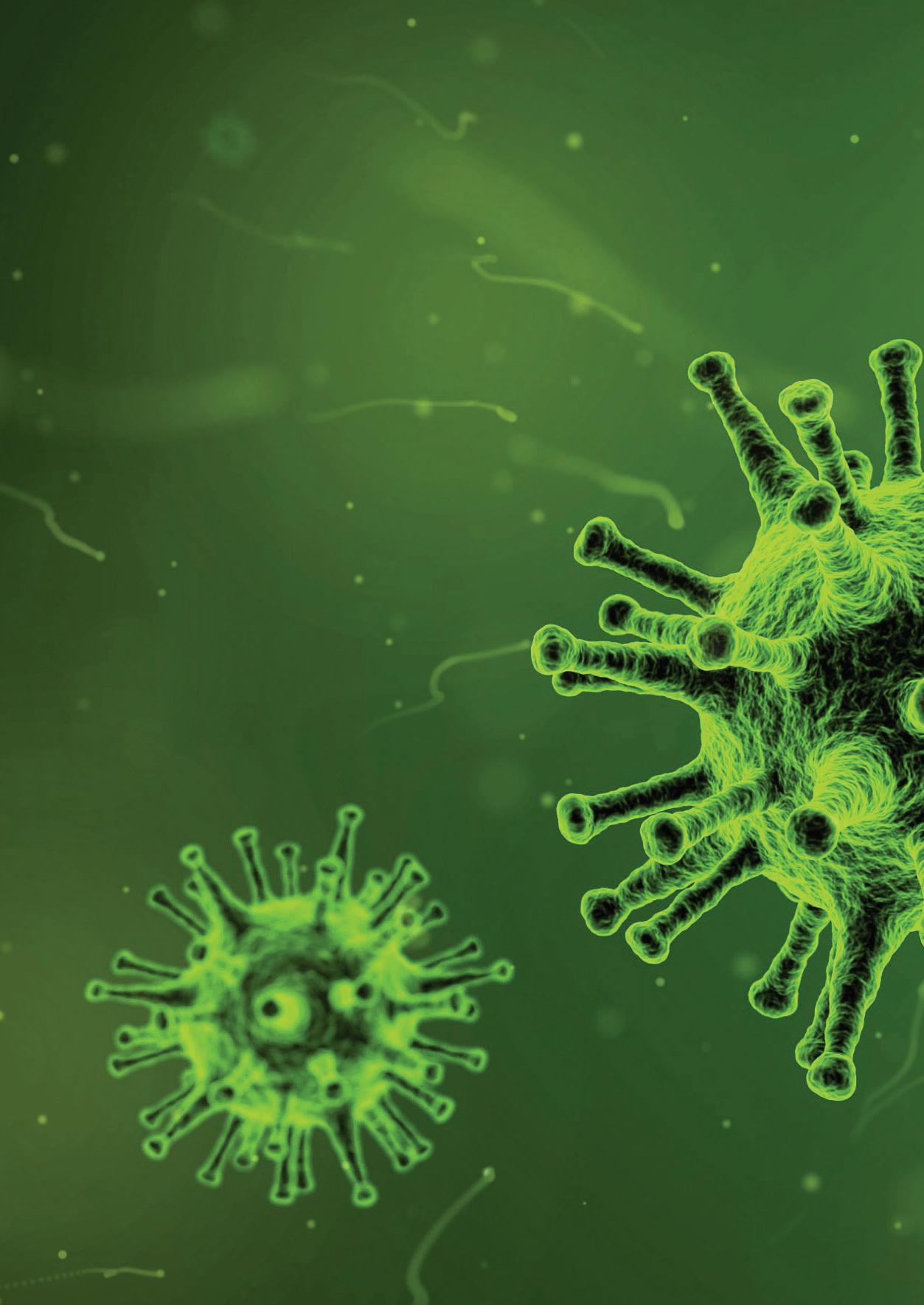
Canteens and kitchens Staff kitchens and canteens are high traffic areas. In addition to numerous people wanting to use the spaces at the same time during lunch and break times, tables, worktops, fridges, and microwave surfaces are high touch point risk areas. What can you do? • Stagger lunch and break times to limit the number of people in these areas at any one time. • Place hand sanitiser at the entrances. • Consider installing a sanitisation station within the space, containing hand sanitiser, virucidal or anti-microbial surface sprays and paper hand towels, and encourage staff
to wipe the surfaces they use before and after use. • Consider removing high touch point items like microwaves. • Mark vacant seating and table areas to clarify social distancing guidelines. • In larger canteens mark out a one-way traffic system. • Ventilate areas well where possible. • Install electronic air sanitisers (not to be confused with air fresheners) which actively kill germs in the air and neutralise smells. • Increase cleaning frequencies. • Use a combination of antibacterial and virucidal or anti-microbial cleaners.
Washroom facilities Washrooms are another high traffic area. When you’ve got to go, you’ve got to go. There are multiple areas to consider including door handles, toiles flushes and seats, taps, and hand driers. What can you do? • Limit the number of people in the toilets at any one time. • Place hand sanitiser at the entrance. • Mark vacant urinal and sink spaces to clarify social distancing guidelines. • Ventilate the areas well where possible. • Install electronic air sanitisers which actively
kill germs in the air and neutralise smells. • Install electronic washroom hygiene monitors which can track cleaning time and attendance. Manage, audit and review your cleaning regime and also alert the onsite cleaning team to immediate cleaning After months of lockdown measures to help stem the spread of Coronavirus, the nation will, in 2021, begin to emerge from its quarantine and adjust to the ‘new normal’. One step toward normality will be the government encouraging those working from home to consider returning to work. While this instruction may be a welcome relief to some workers, it starts a ticking clock for employers and facilities managers to make sure people can return to work safely.
requirements or the replenishment of stock items such as soap and paper products. • If you don’t have the budget for an electronic hygiene monitor you can always use a wall mounted toilet inspection sheet, which can be signed hourly or at a suitable
frequency for your business by the onsite cleaning team. • Increase cleaning frequencies. • Use a combination of antibacterial and virucidal or anti-microbial cleaners.
Preparing your facility for the return to work
Jamie Woodhall, technical and innovations manager at Rentokil Specialist Hygiene, reports.
WWW.FLOORBRITE.CO.UK
The eventual easing of restrictions will also represents a mindset shift - from reactive cleaning and disinfection against Coronavirus, to a more planned and proactive approach to keep people safe, and enabling the country to return to a sense of normal for the long term.
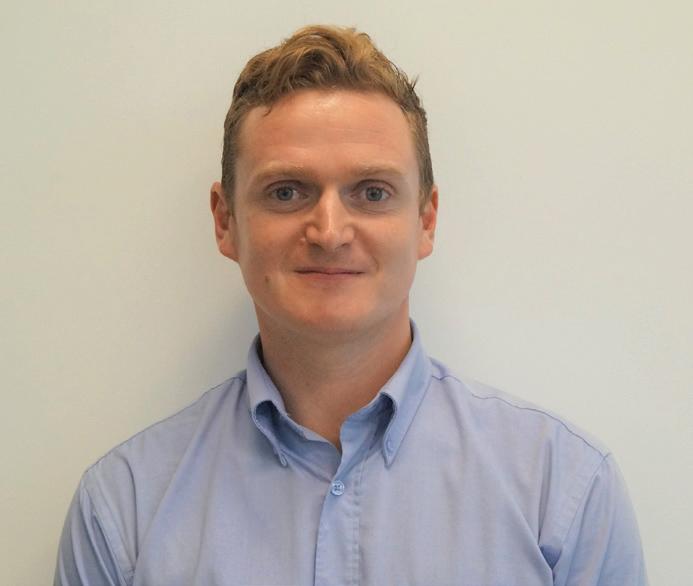
The HATS model Rentokil Specialist Hygiene’s HATS critical appraisal survey is helping organisations back Continued on Page 20.
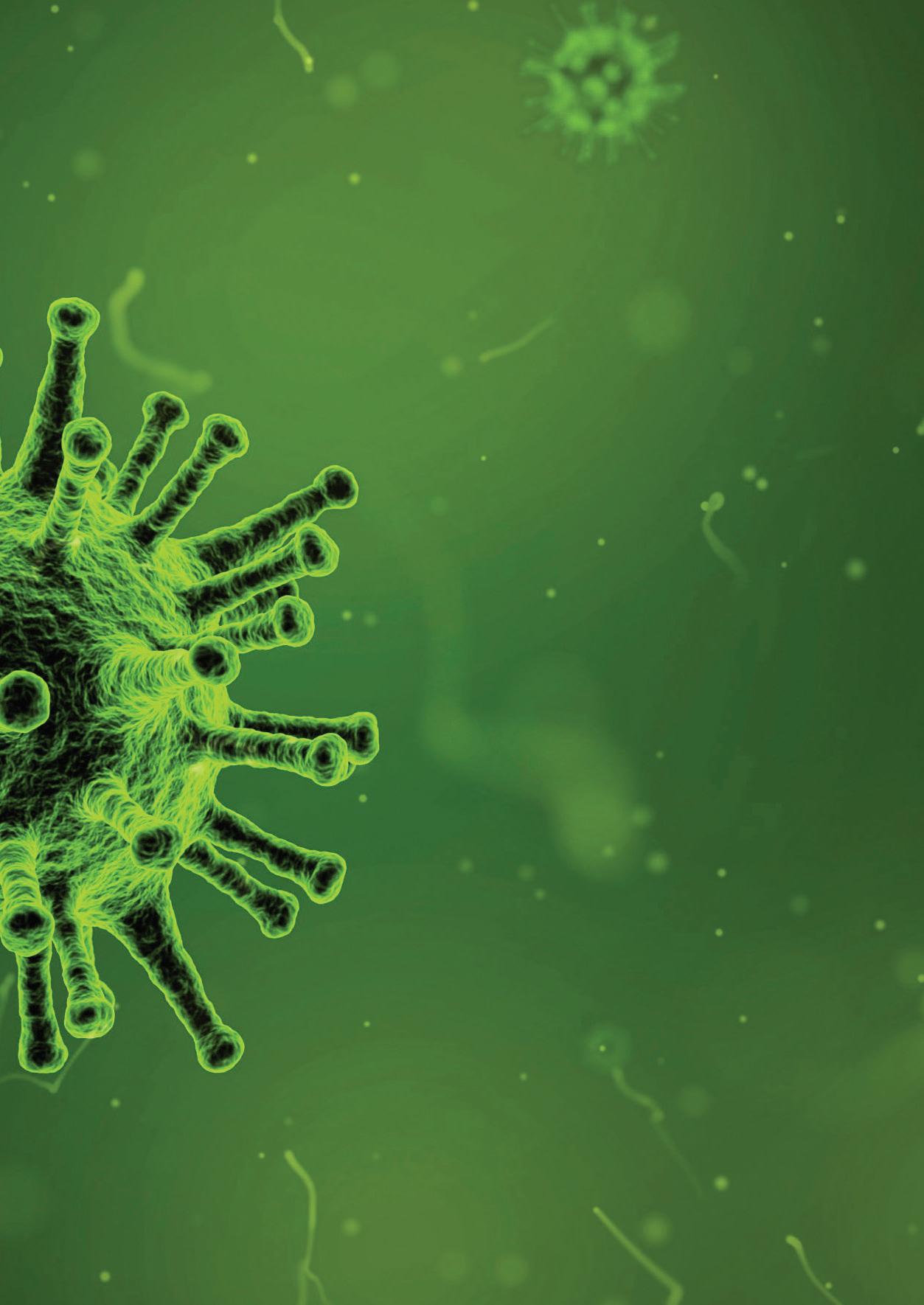
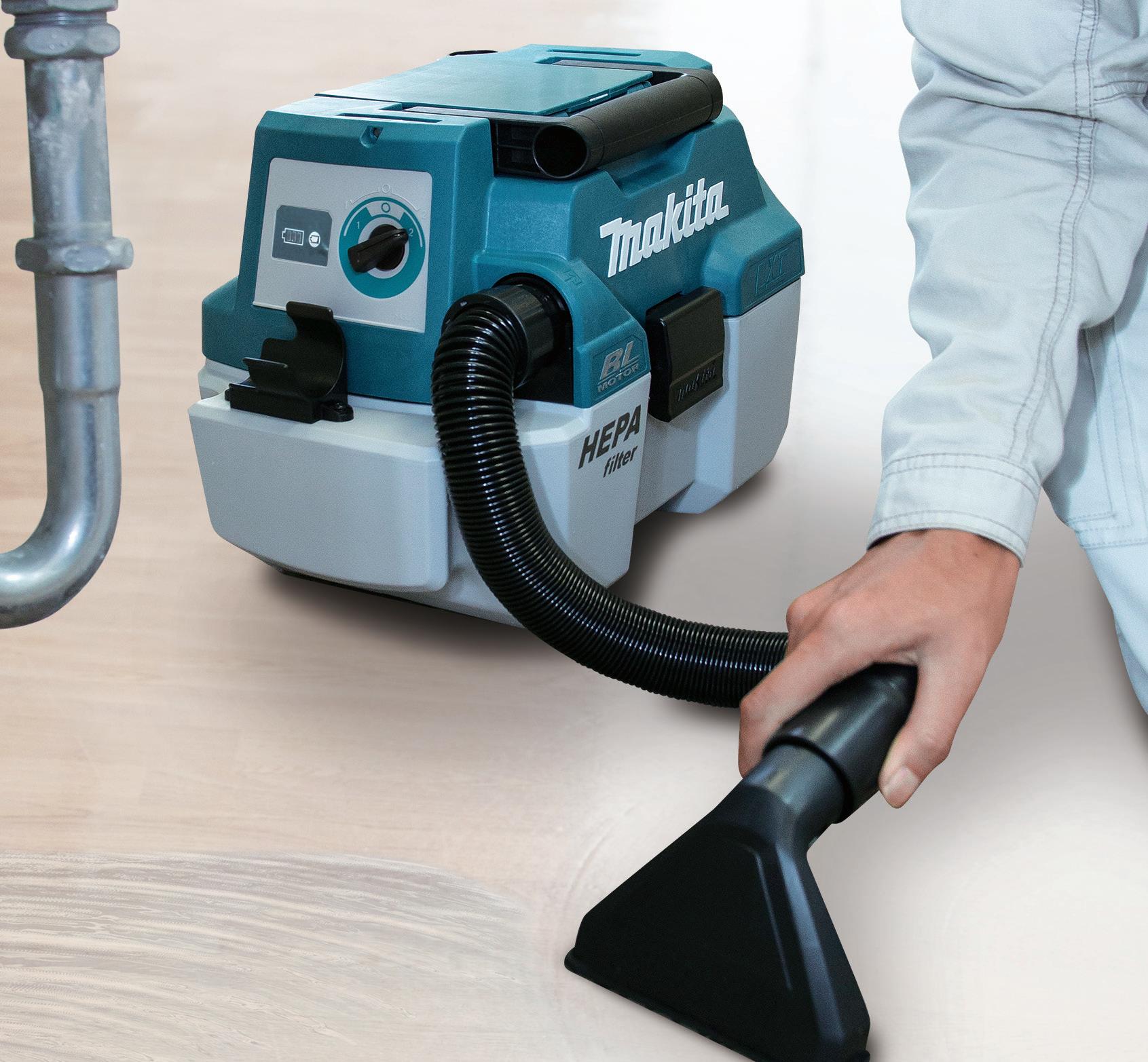
18V LXT Brushless Vacuum Cleaner DVC750LZ
Model DVC750L is a cordless portable vacuum cleaner for both Wet & Dry vacuum cleaning powered by LXT 18V Li-ion battery
18V 5.0Ah battery run time: Low Setting = 60 mins High setting = 30 mins
- Max Air Flow (Lo/Hi): 1.3 / 1.6 m2/min - Max Sealed Suction (Lo/Hi): 4.2 / 6.7 kPa - Dust Bag Capacity: 7.5 litres - Tank capacity Wet: 4.5 litres - Net weight: 4.6 kg - Brushless motor - Foldable handle - Blower function - Equipped with HEPA filter - Flexible hose with storage - Extremely low noise
Continued from Page 19. to business safely. When our experts survey premises to assess risks and implement solutions to ensure safety and compliance, we focus on four key areas: Hygiene factors, Atmosphere, Touch, and Social distancing (HATS). • Hygiene factors: Poor hygiene creates potential transmission routes for
Coronavirus and other microbial infectious diseases and pathogens, so the first thing to do is to assess the overall cleanliness of your premises and develop a cleaning regime that is fit for purpose. This should take into account the size, use and hours of operation. It should also factor in areas that require more frequent cleaning attention.
The most common hotspots include main entrances, waiting rooms or lobbies, washrooms, kitchens, canteens, and administrative areas.
• Atmosphere: Coronavirus can be transmitted by respiratory droplets which are expelled when someone with the virus coughs, sneezes or even speaks. This means that air quality is a vital consideration to help protect workers. It is important that air conditioning units and ventilation systems are regularly cleaned and serviced to ensure they are operating as they should. Air BioHygiene is advising the FM and cleaning sectors to remain environmentally conscious at a time when the use of disinfectants is likely to be at an all-time high across the country. The green-minded biotechnology company, which saw sales of its all-purpose and hand sanitisers rocket throughout the pandemic, is keen to stress that when considering ‘environmental disinfection’ we must look out for both short- and long-term effects.
Erum Ahmed, director of sales at BioHygiene, explained: “At present, there are still traditional products in the market that contain quats, alcohol, chorine, hydrogen peroxide, or a mixture of these. All of these can impact the
purifiers can help improve air quality - they should have a HEPA filter to tackle bacterial and fungal matter, and an activated carbon filter to help tackle volatile organic chemicals within indoor areas. • Touchpoints: When reviewing a facility’s hygiene hotspots, it’s important to consider high-frequency shared touchpoints. Once identified, these should be incorporated in the cleaning regime and hand sanitiser or surface disinfection stations should be installed nearby. • Social distancing: Wherever possible, facility managers must assess the immediate working area and layout plans to mitigate the risk of individuals coming into close contact with others. There are many tools to help ensure safe distancing such as signage, retractable barriers, floor mats with guidance and reminders, as well as protective screens being common solutions.

Proactive cleaning strategy A cleaning procedure or regime should mandate cleaning routines as well as specialist deep cleans at regular intervals. A deep clean should include a thorough disinfection of high frequency touchpoints, as well as moving all furniture or equipment away from the walls to make sure no areas are missed from the standard cleaning routine. There is a range of specialist tools and methods of application that can be used in deep cleaning, in order to eradicate pathogens such as Coronavirus, including: electrostatic disinfection - a powerful disinfection treatment that involves adding an electric charge to liquid droplets immediate or the external environment in which they are used. By immediate impact, we look at negative effects to the user - alcoholbased sanitisers that can dry out the skin, irritate the eyes and cause safety concerns due to its high flammability. In addition, the inclusion of alcohol in skincare products and the possibility of its transference and tainting in food preparation, can cause conflict with certain religious beliefs. By external, we refer to wider impacts on the environment in the traditional sense: quats and chlorine that can produce dangerous levels of aquatic toxicity, both short and long-term. This also includes manufacturing processes that release of disinfectant when they are sprayed; mist blowing space treatment - designed for very large, open spaces. The speed of the jet and the volume of air that is generated means that liquid disinfectant is powerfully blown out into large areas, effectively disinfecting these areas quickly and in a much shorter time than more conventional methods; ultraviolet (UV-C) light - UV light in the form of a handheld lamp causes the photochemical deconstruction of the DNA of microorganisms, deactivating its reproductive processes so that viruses can no longer spread; and ultra-low volume (ULV) disinfection fogging - a mist of disinfectant which settles on top of, underneath and on the sides of objects, enabling technicians to disinfect a large area in a short period of time.
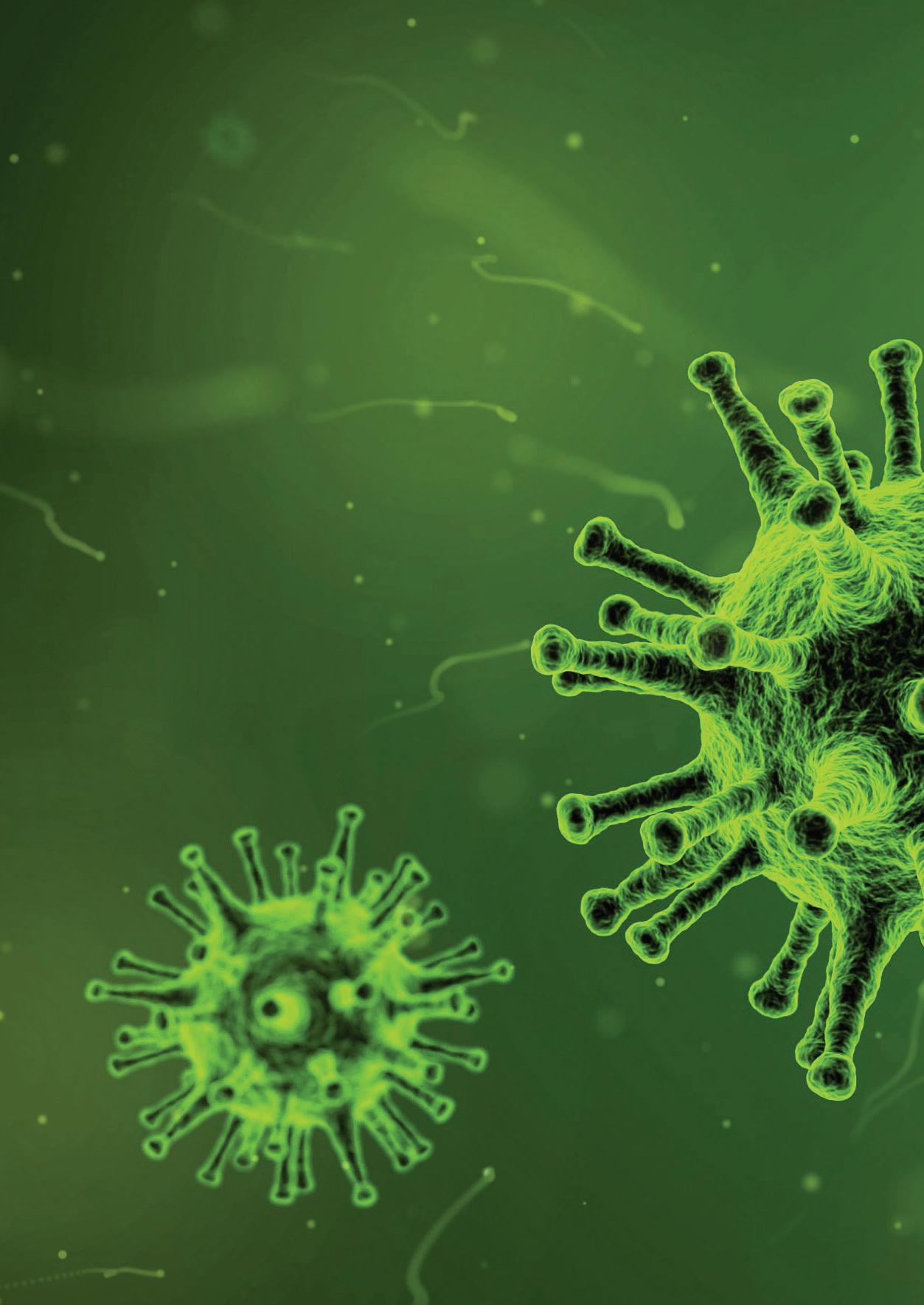
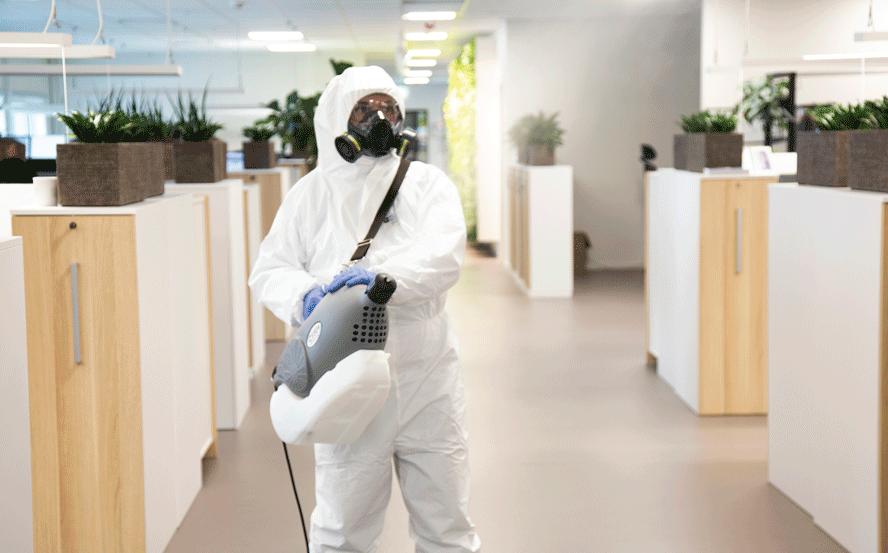
Final thoughts With offices looking to reopen across the country, hygiene and cleanliness is at the heart of government guidance. Making a facility safe for workers to return can be daunting for FMs as the guidance can be complex and is constantly changing. It is important you call in the experts, who will provide consultative knowledge and specialist hygiene services.
EMPLOYING A PHILOSOPHY OF ‘ENVIRONMENTAL DISINFECTION’
WWW.RENTOKIL-HYGIENE.CO.UK dangerous levels of CO2 into the atmosphere.”
According to BioHygiene, the cleaning and FM sectors should ask suppliers questions around raw materials, CO2e, packaging, and aquatic toxicity when purchasing sanitisers and disinfectants to ensure they tick the various boxes with regard to sustainability. Only through diligence on all these points can ‘environmental disinfection’ be delivered.
Unsurprisingly, BioHygiene’s range of alternative sanitising products tick all of these boxes. Its foaming hand sanitiser is 100% biodegradable, alcohol and quat free, and is made with natural and sustainable technology.
Questioning some of current products available, Erum Ahmed added: “The market has recently been flooded with hand sanitiser of varying quality. This can be attributed to the standard derogation made by the WHO at the start of the pandemic, approving any hand sanitiser Workplace hygiene specialist, Simply Washrooms, is working with its customers to ensure stringent infection control measures are in place to help tackle the challenges COVID-19 presents. Its specialist range of workplace hygiene services helps reduce the spread of viruses and creates a safer working environment: sanitiser systems to ensure everyone has access to important hand hygiene measures. and contact surface bacteria and viruses. including door handle covers and push plates that reduce bacterial growth and cross-contamination. that contained over 65% alcohol. This has ultimately allowed product to reach the market without going through the usual accreditation processes, raising questions of safety - for both the user and the environment. Ultimately, we do still recommend frequent cleaning as the first point of controlling the spread of germs with sanitising and disinfecting used as a belt and braces approach. We just want people in the industry to ensure that, however they choose to clean, they use our philosophy of ‘cleaner, leaner, greener!”
CREATING COVID-SAFE WORKING ENVIRONMENTS FOR CUSTOMERS
• Wall mounted and freestanding hand • Air purification systems to help reduce airborne • Antibacterial door protection guards WWW.BIOHYGIENE.CO.UK
Andrew Shelley, operations director at Simply Washrooms, said: “Now more than ever, choosing services and products that reduce bacterial growth and help stop the spread of viruses is central to creating a safe working environment and keeping people safe. We provide guidance and advice on infection control measures and our specialist range of workplace hygiene services and products help reduce bacterial growth and stop the spread of harmful viruses. Over the last few months, we’ve worked closely with our customers to ensure stringent infection control measures are in place and ensure their workplaces are COVIDsecure so they can remain operational.” WWW.SIMPLYWASHROOMS.COM
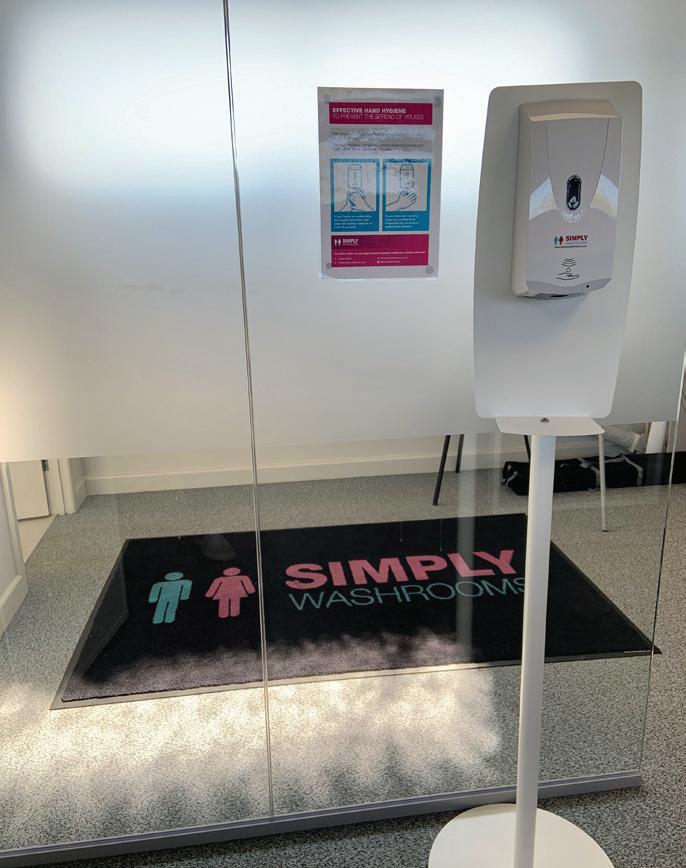
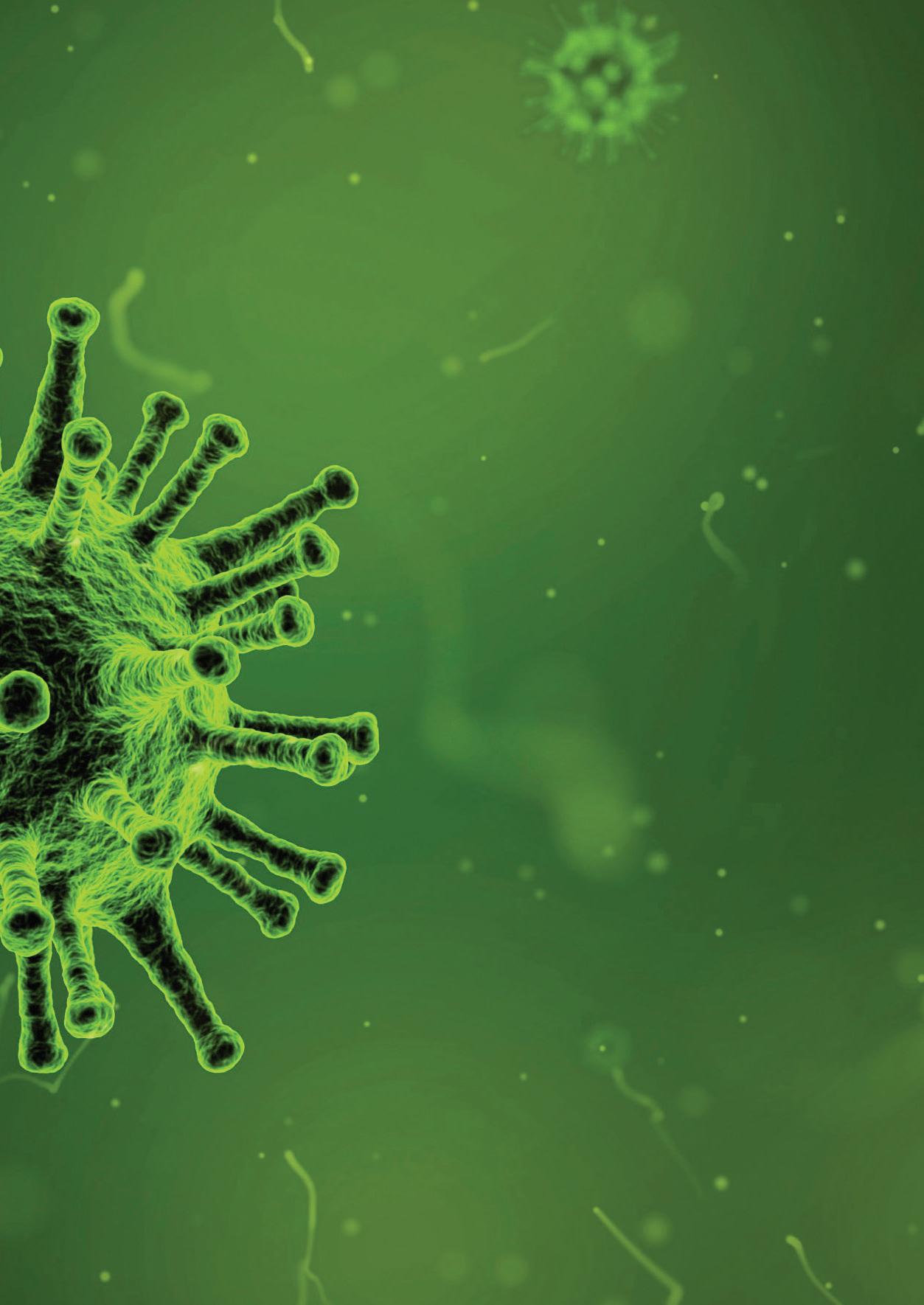
Dream team
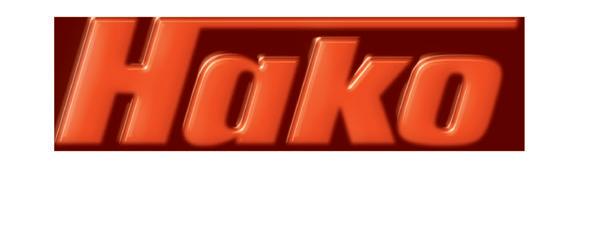
The unbeatable combination of Hako’s B120R scrubber drier and B980R sweeper are the perfect partnership for warehousing.
With a combined rental of just £140 per week* (including maintenance) on Hako contract hire, there’s never been a better time to talk to us. If you want dust and debris free floors, reduced cleaning labour costs, plus the benefit of outdoor sweeping capability, call us to arrange a demo. We think you’ll be impressed.
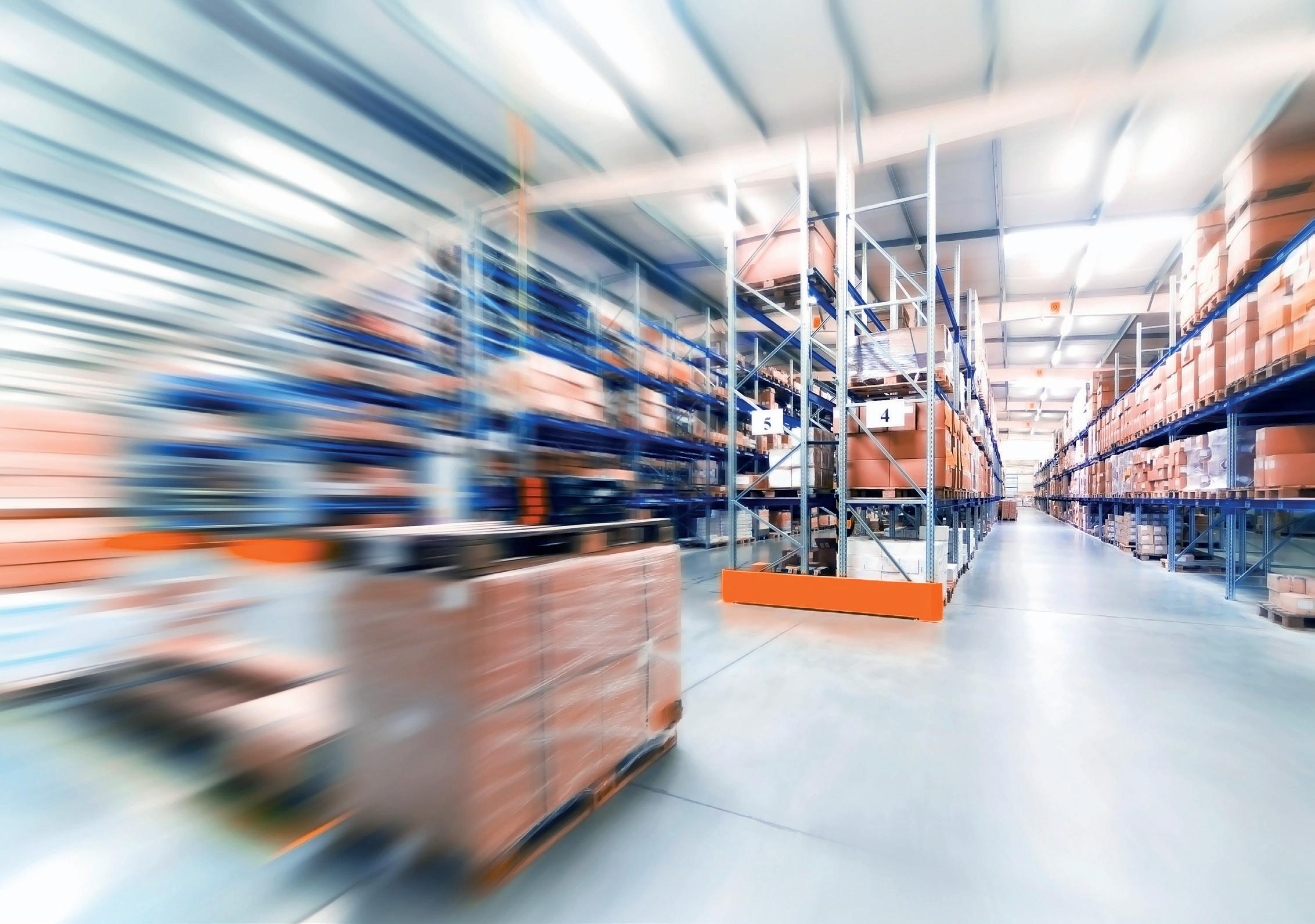
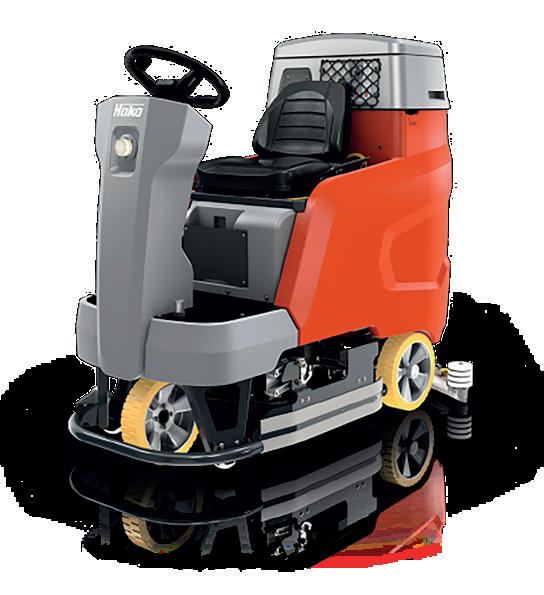
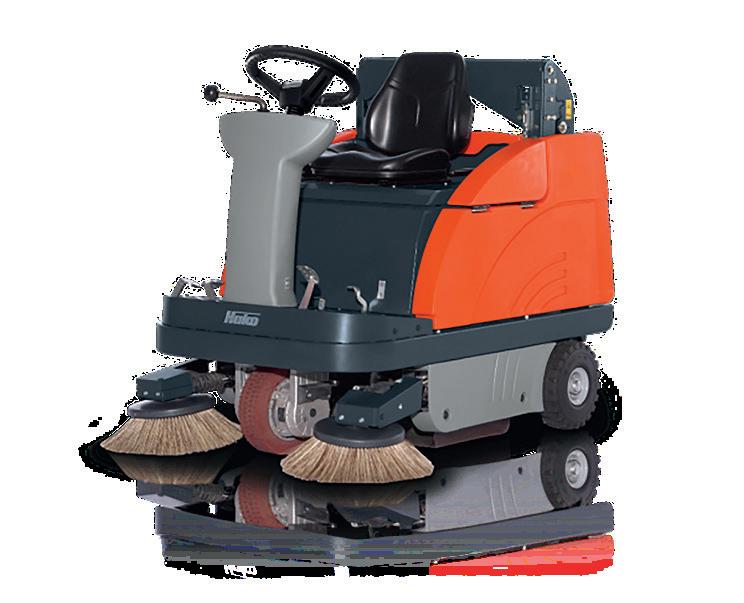
enquiries@hako.co.uk Tel: 01788 825 600 | www.hako.co.uk
Autonomous cleaning – embracing technology to deliver higher standards
Julie Kitchener, head of customer service and marketing at ICE, reports.
WITH the pandemic still very much in the forefront of our minds, there is now an even higher demand for automated and socially distanced cleaning. Earlier this year, ICE launched the highly anticipated Co-Botics line - the industry’s first comprehensive range of autonomous floor cleaning machines. We believe that automation will help shape the way cleaning operations and functions are carried out in the future, but in a collaborative and cohesive way.
The Co-Botics equipment has been designed to integrate into cleaning team operations, picking up the manual and repetitive tasks, which will then allow operators to focus on hygiene and sanitising activities to promote cleaner and safer environments. It’s not about replacing people it’s about embracing technology to deliver higher cleaning standards, infection control and ‘proof of clean’. Using autonomous cleaning is a very natural and progressive way of how we can help support and deliver these measures and improve wellbeing for hygienic environments - to coexist, to collaborate, and to work cohesively within the workplace to drive standards, efficiency and sterility.
These machines are as close to human activity as anything available. They are extremely intelligent and can be fully operated, controlled and managed by the cleaning teams on site. The features ensure the delivery of the following key requirements when using autonomous equipment in day to day cleaning activities: • Safety and efficiency - safe, consistent and easy to map and control. • Intelligent - it will clean any area without the need for technical intervention. • Environmentally friendly - water recycling capabilities and a run time of up to five hours. • Proof of clean - fully integrated telemetry and cloud-based reporting on a clean by clean basis.
We currently have machines installed and operating alongside cleaning teams in schools, airports, train stations, hospitals, hotels, manufacturing/warehouse facilities, and retail environments across the UK. And we are already seeing how the introduction of Co-Botics is helping facilities to provide hygienic and safe environments for employees and visitors. In fact, Luton Airport has become the first airport in the UK to receive certification from the Airports Council International (ACI) Airport Health Accreditation programme, which provides airports with an assessment of how well their health measures align with worldwide standards and industry best practices. The airport has introduced Co-Botic equipment into its daily cleaning operations, which has hugely contributed to the accreditation and means that passengers and staff can be confident of the utmost cleanliness and hygiene levels throughout the airport.
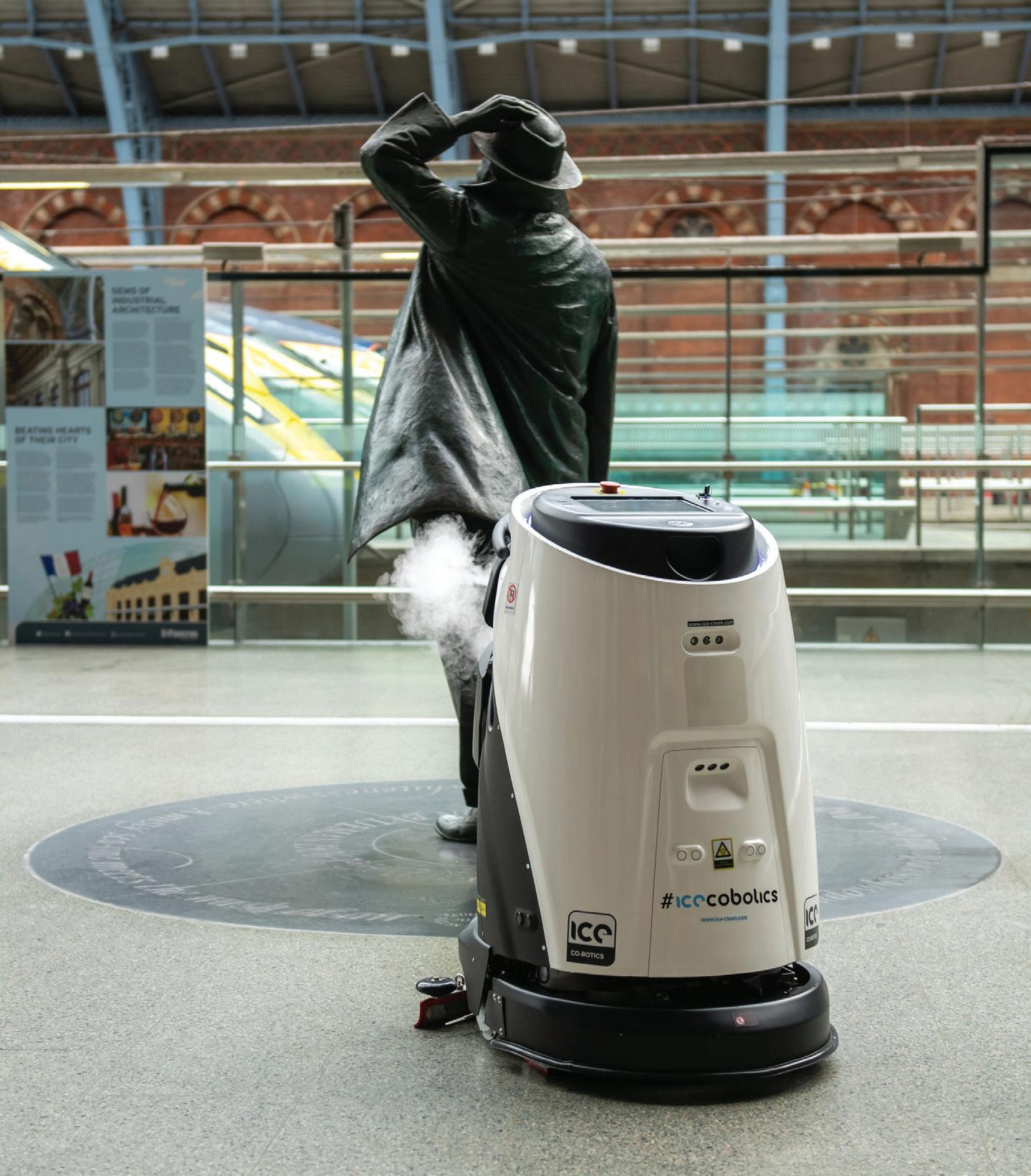
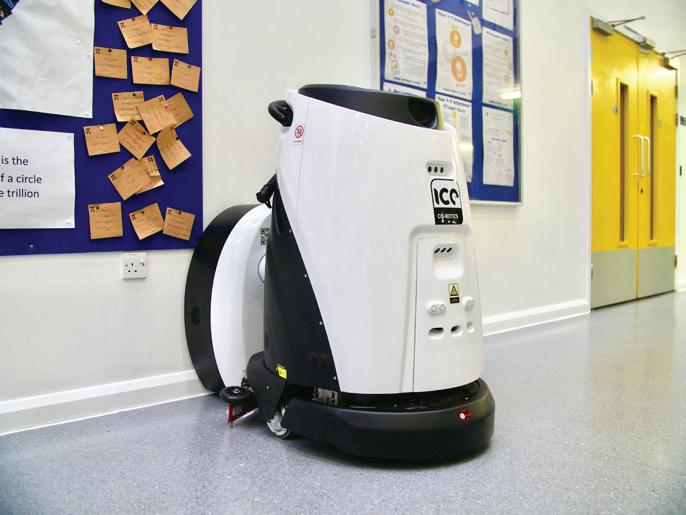
And it’s not only airports in the transport sector that have benefited from introducing autonomous cleaning equipment. Train stations across the UK have integrated robotic sanitising machines into their cleaning operations as part of a drive to re-instil confidence in travel as the pandemic continues.
In the area of education, schools have found that introducing autonomous equipment has resulted in increased efficiency as the Co-Bots are utilised to clean the corridor and hall floors whilst the valuable labour resource focuses on detailed cleaning tasks such as sanitising and deep cleaning. They also see real value in deploying autonomous equipment to support in the fight against viruses. The Co-Botic equipment helps with socially distanced cleaning and will be able to support cleaning with minimal human interaction during any future outbreaks or lockdown situations.
The demand for Co-Botics is really gathering pace, possibly fuelled by the heightened priorities for infection control at an appropriate distance. To clean as we have always cleaned will not be good enough as the world around us changes and we are always looking for ways to innovate and develop. Facilities service providers must achieve more, both in terms of productivity and quality, without compromising financial budgets. Therefore, we believe that investment in automated cleaning is not just pioneering, but essential for future cleaning. WWW.ICE-CLEAN.COM
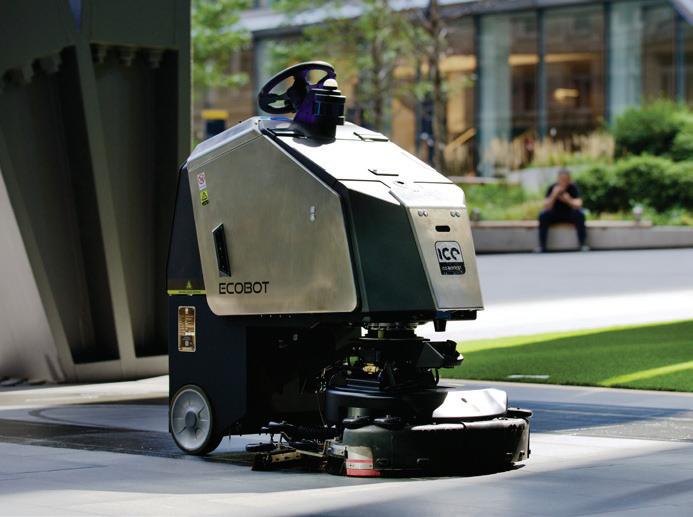
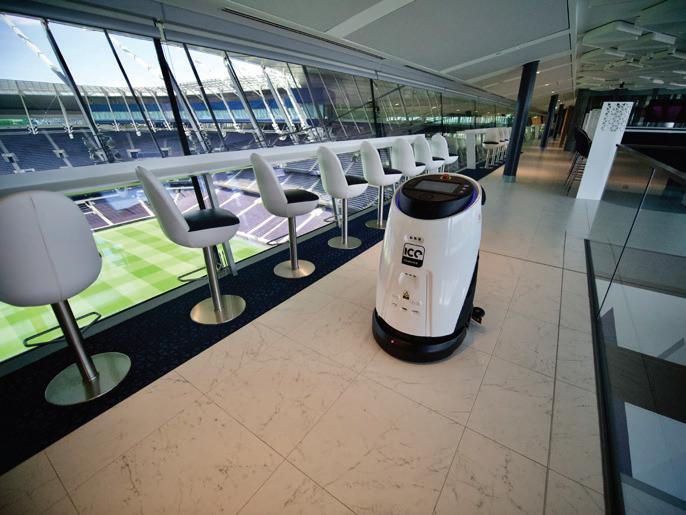
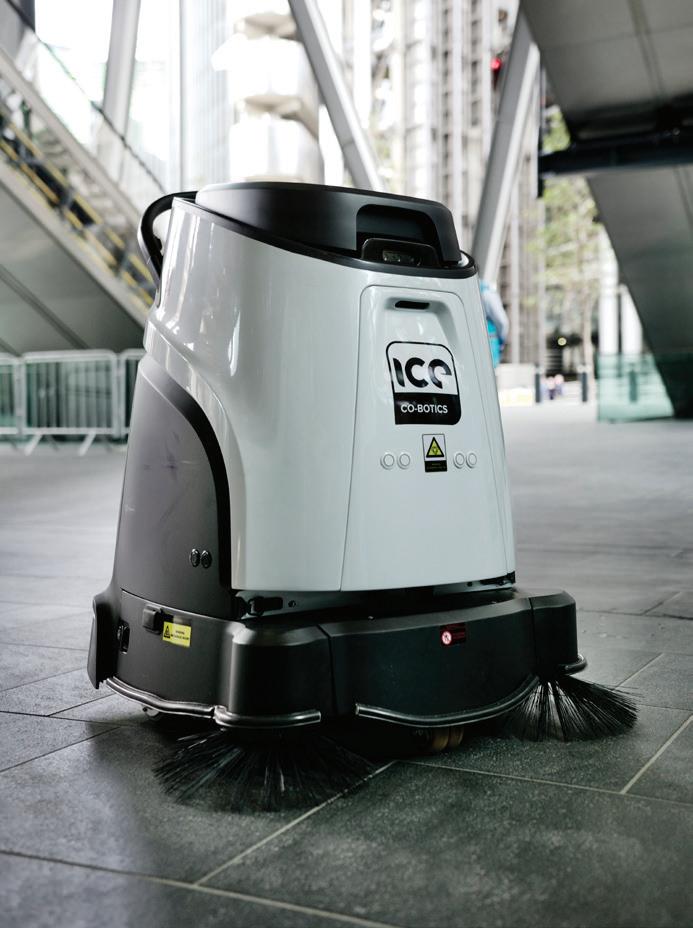
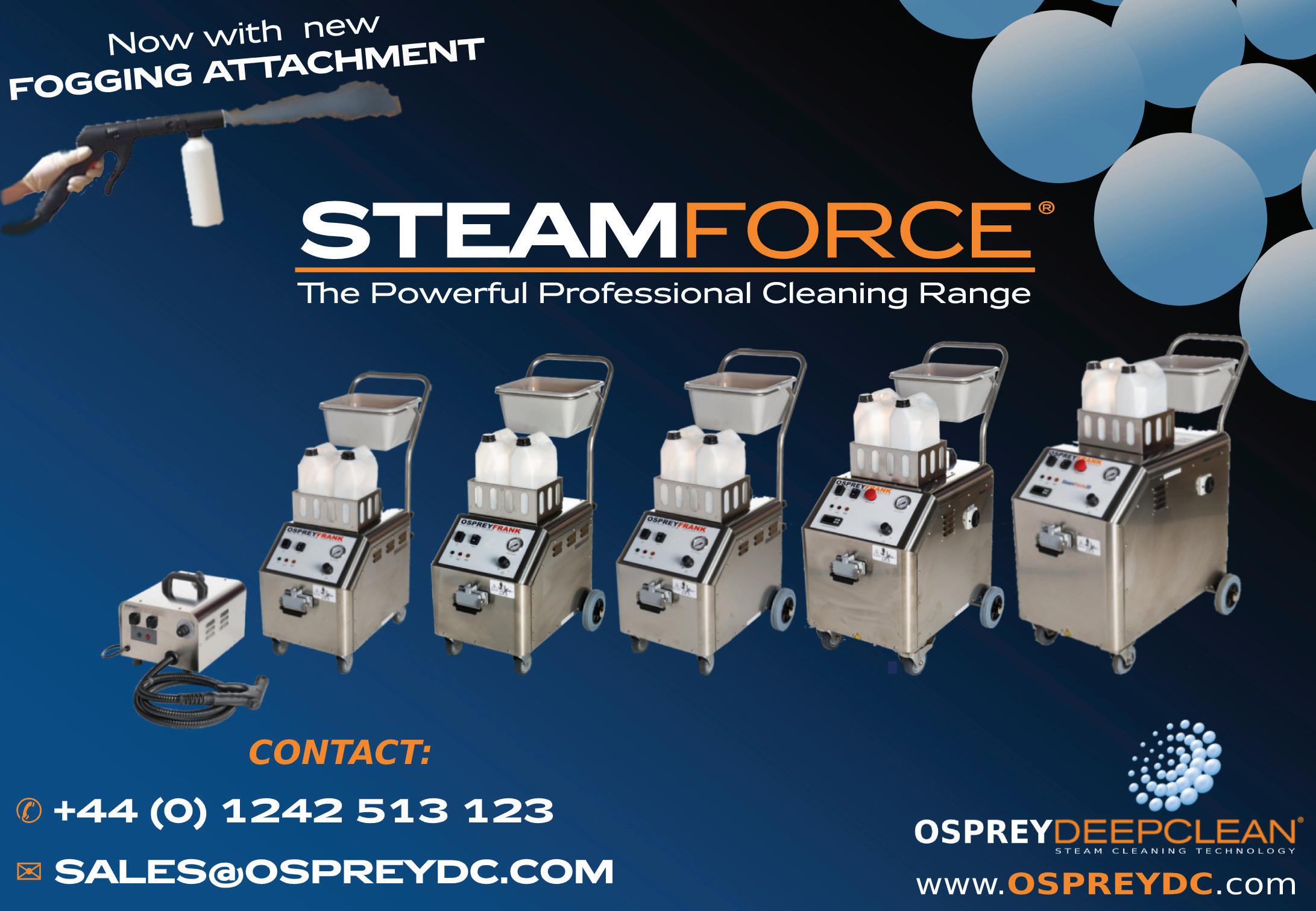
How do autonomous floor scrubber robots work?
Michel Spruijt, vice president and general manager of Brain Corp Europe, reports.
AUTONOMOUS floor care solutions work in parallel with employees and serve as an effective tool in helping teams get the job done. In the case of robots powered by BrainOS, Brain Corp’s commercial operating system, machines are manually trained to follow specific routes via a ‘teach and repeat’ process. Once a robot has an understanding of its environment, it can then operate seamlessly in autonomous mode, effectively navigate around obstacles, and adapt to dynamic, public environments.
This frees up time for employees, who can now concentrate on higher-value tasks such as restocking shelves, disinfecting surfaces and interacting with customers. Brain Corp partners with original equipment manufacturers who have been leaders in the floorcare industry for
Michel Spruijt
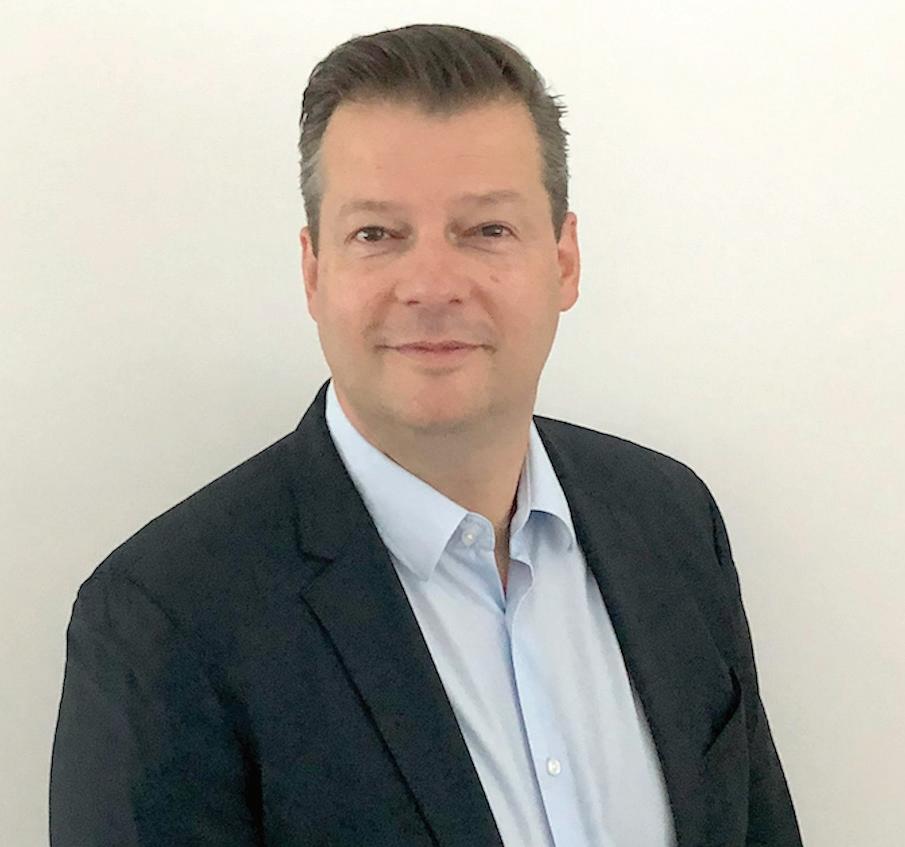
a long time. That way, the machines employees are working with are from the brands they already know and trust...now equipped with autonomous capabilities. Are specialists needed to teach and deploy robot cleaning machines? That depends on what autonomous cleaning solution you’re working with. One of Brain Corp’s biggest value propositions is that robots powered by BrainOS require no type of specialised set-up or technical expertise. With the help of an advanced and intuitive user interface, anyone can easily deploy the machine and have it running autonomously right away. These robots also require no specialised type of infrastructure changes. While some floorcare robots utilise specialised beacons or magnetic tape, BrainOS-powered machines can be set up in any indoor space with no additional environmental updates needed.
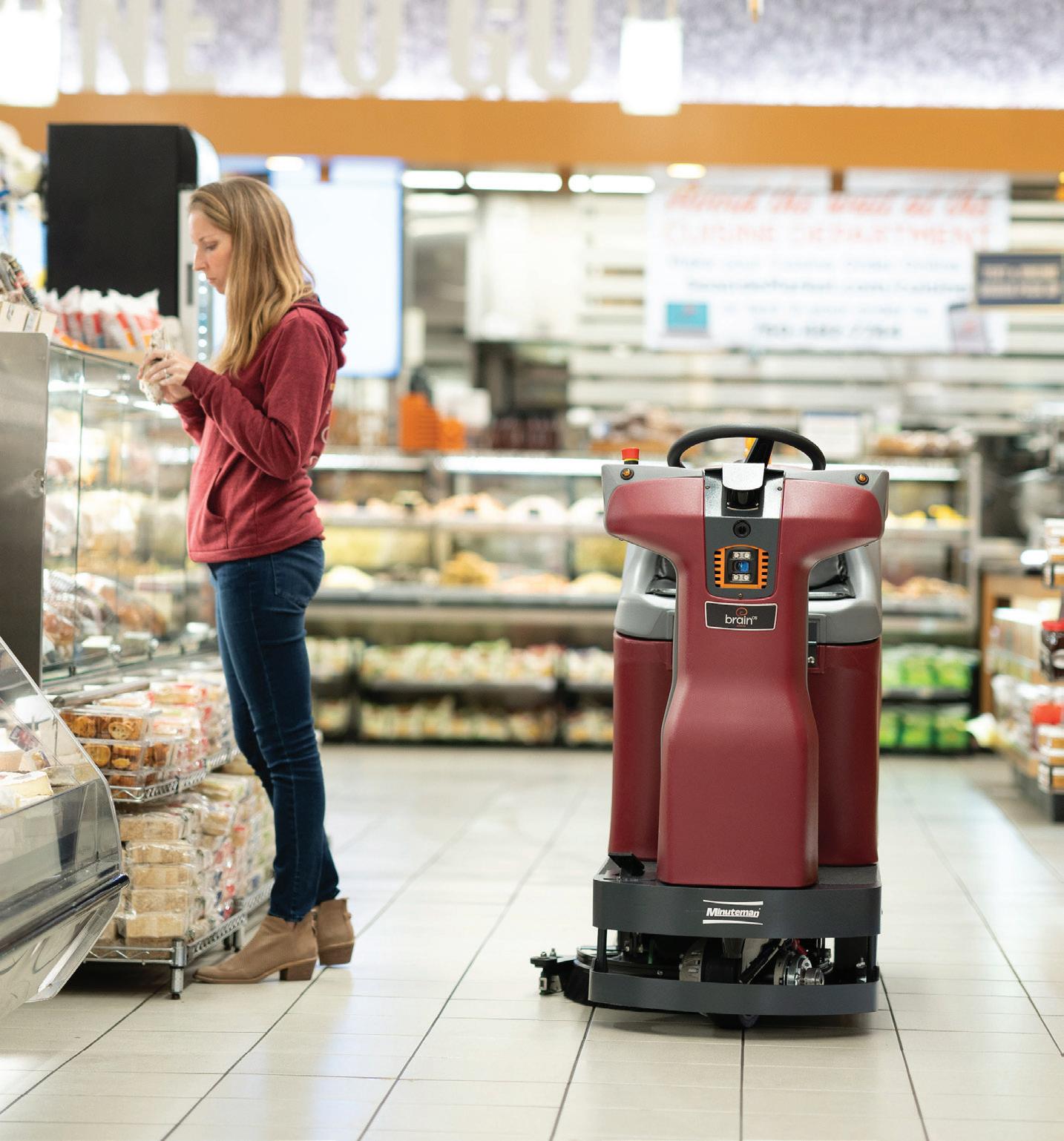
What are the benefits of autonomous cleaning? By automating the repetitive aspects of commercial floorcare, cleaning providers are able to offer greater consistency, coverage and quality in everyday operations. With cleaning more important than ever before, it’s imperative that businesses win back customer trust and keep employees safe with a state of ‘constant clean’. By leveraging the power of automation, managers are able to more effectively provide this and also audit their cleaning programmes through the use of advanced, digital reporting. Not only is the cleaning more consistent - it’s also verifiable.
The coronavirus pandemic has created an increased and consistent need for disinfection. How does robot technology improve cleaning consistency and ensure safety in various industries? A comprehensive cleaning programme always requires cleaning before disinfection (ie ‘c comes before d’). Robotic solutions provide the ‘gateway’ that every facility needs in order to be considered safe...and that’s the cleaning of an environment’s floors. Once dirt and germs are picked up from the floor, the use of disinfectant can be deployed if needed. As far as high-touch
surfaces are concerned, the use of robotic floorcare ensures that employees have more time to do the focused, detail cleaning that is now required to effectively combat the virus.
Has the data shown an increase in use of cleaning robots in response to the COVID-19 pandemic? Yes, absolutely. We saw robotic usage across the BrainOS-powered fleet increase by 24% in April 2020 compared to the same month the previous year and have seen a 15% increase in the year overall. 68% of that increase occurred during daytime hours. This shows that robots are not only being used more overall, but that they’re being deployed at times when environments may be experiencing high foot traffic (such as in the case of retail).
What impact will autonomous technology have on cleaning practices in the future? We can expect to see an increased use in autonomous technology and the digital reporting that goes along with it. Managers will become accustomed to using this data in order to streamline operations and maximise efficiencies. With employees now reallocated to other tasks, we’re likely to see the trend of additional detail cleaning and disinfection continue both in the short term and far beyond the pandemic.
Do you believe that there will be a greater need for automated cleaning technology in the future? Absolutely. What the pandemic has shown us, amongst other things, is that businesses must be as adaptable and flexible as possible. Coronavirus necessitated that businesses completely rethink their day-to-day operations in order to ensure safety and work within the parameters of the ‘new normal’. Technology like robotic floorcare can be scaled up and down almost immediately, making it a compelling solution in this new, highly dynamic environment. WWW.BRAINCORP.COM
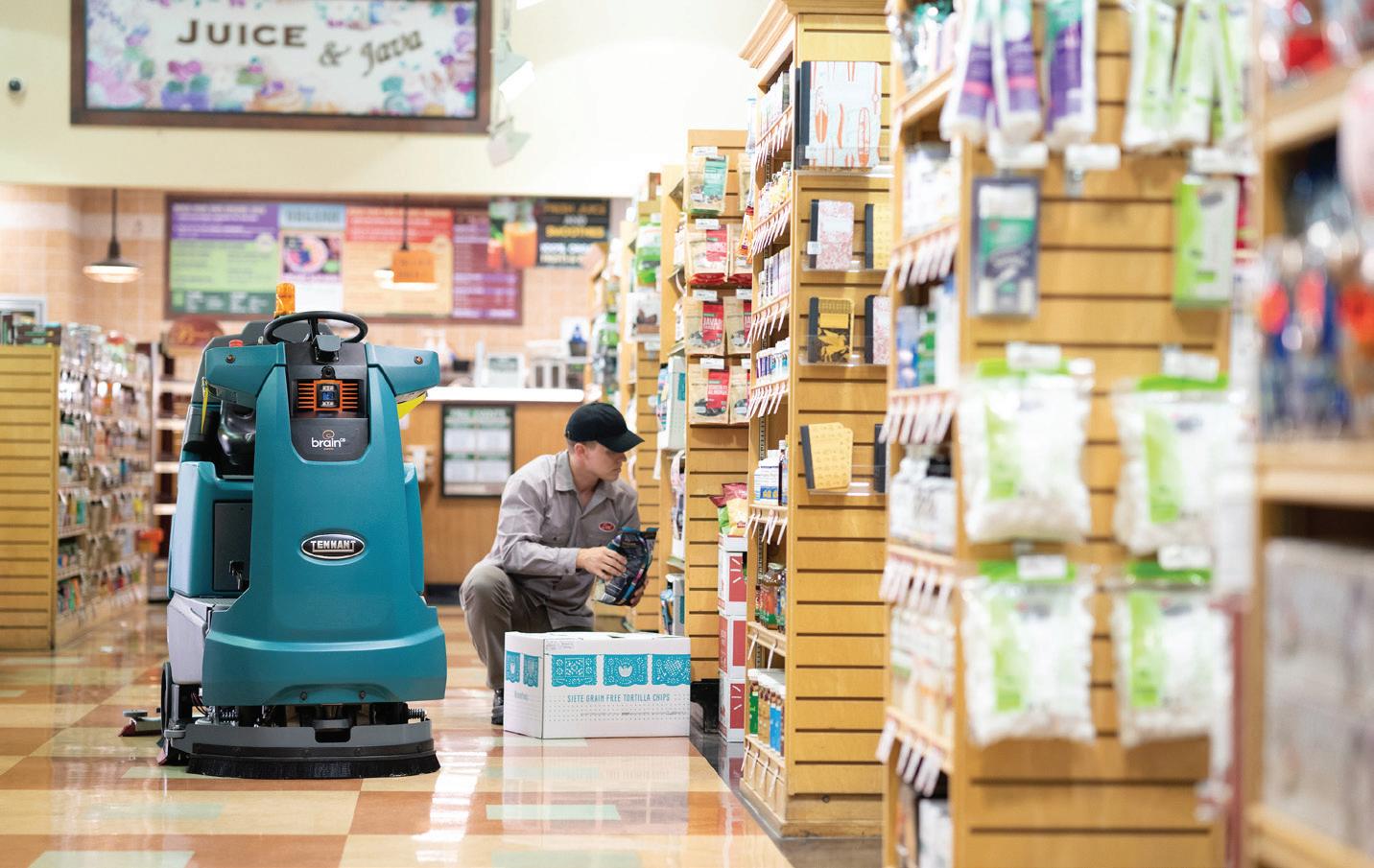
Digital Onboarding
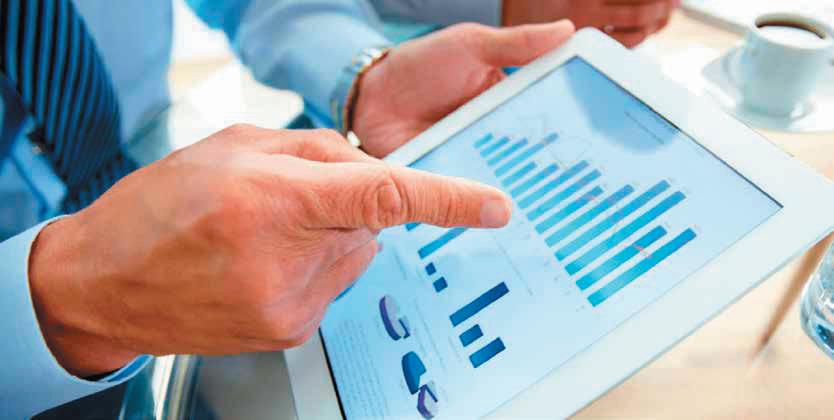
Worried about changing regulations? Right to Work, GDPR, Brexit, Recruitment, the list seems endless. uComply can help:
One standardised process for your eligibility to work, know your staff comply with Home Office RTW guidance
Embrace sustainability, get rid of mountains of paperwork using our App, it’s GDPR compliant too
Store all documents securely, centrally, fully encrypted in the cloud and improve your hiring efficiency.
Go Paperless, Protect, Save Time & ensure employees have the Right to Work
Book a Discovery call with us to find out more …. Call: 01707 802 899, email: enquiries@ucomply.co.uk or visit our website www.ucomply.co.uk
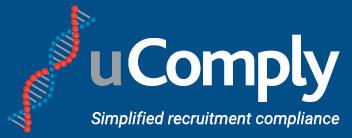
Scrubber dryer choices
SCRUBBER dryers are established as the workhorses of floorcare, whether managed in-house or by contract cleaning teams. The variety of machines on offer - and the accessories and options available - can make the choice daunting. With its range of Taski scrubber dryers, Diversey offers numerous choices, all supported with technical, application and maintenance expertise.
One of the most important considerations is to match the size of machine to the proposed application. Too large and it will probably be under-utilised and unproductive, ultimately costing more to own and operate. Too small, and it could be over-used, inefficient and prone to more unscheduled outages.
With the Taski range comprising 20 main models extending from compact uprights for confined areas to the large ride-on machines for expansive spaces, Diversey offers a broad choice. This makes it easier to match the performance of a machine to the application requirements with fewer restrictions. Moreover, offering a larger range helps ensure the needs of larger fleet operators can be met from a single source which can simplify pre- and post-sales support and enable greater deployment flexibility.
Total cost of ownership - sometimes called whole life cost - should be another factor HOOPER Services Ltd has recently announced its collaboration with Border Cleaning Machines in Shropshire as a UK distributor of the TSM Tools portfolio, which includes the Willmop 50B vertical scrubber dryer range.
Dave Clark, sales director at Hooper Services, said: “We are very happy that the team at Border Cleaning Machines has come on board with us to work with this fantastic piece of equipment. Not only are they able to sell the machines, Border Cleaning Machines is also available to support the range with any demonstrations, servicing or spares - which is exactly the sort of company that we have in the decision. A machine that has a lower purchase or rental cost may be less energy efficient, consume more water or products or be more prone to breakdowns than an alternative which initially appears more expensive. This combination of purchase price and running costs is the total cost of ownership. Manufacturers such as Diversey with a large installed base across multiple customers will be able to give a good prediction of whole life costs based on real customers’ actual experience.
Choose a machine that can be used with a wide range of cleaning products, pads or brushes. This will ensure it can clean a variety of flooring types and give the desired finish. Many operators are choosing to run their machines with advanced pads, such as the diamondimpregnated Twister by Diversey, that can be used on various types of hard flooring with water alone for reduced long-term costs and enhanced sustainability. Manufacturers offering a wide selection of pads and brushes will advise on the right ones for any machine or flooring type.
Choose batteries carefully and do not compromise on performance. Advances in battery and charger technologies also mean that machines of all sizes will work harder and longer between charges. That means more time working and less time standing still while being recharged, all of which adds to better productivity and cost-effectiveness.
Manufacturers with a consistent design approach are likely to incorporate common features across their range. This can include everything from user controls, routine service points, control systems, and technology. For users this means that one machine will look and work much the same as a larger or smaller alternative. This familiarity helps promote consistent use, reduces retraining requirements, and simplifies daily maintenance checks. For suppliers, it can simplify everything from manufacturing to service with resulting reliability gains and cost savings.
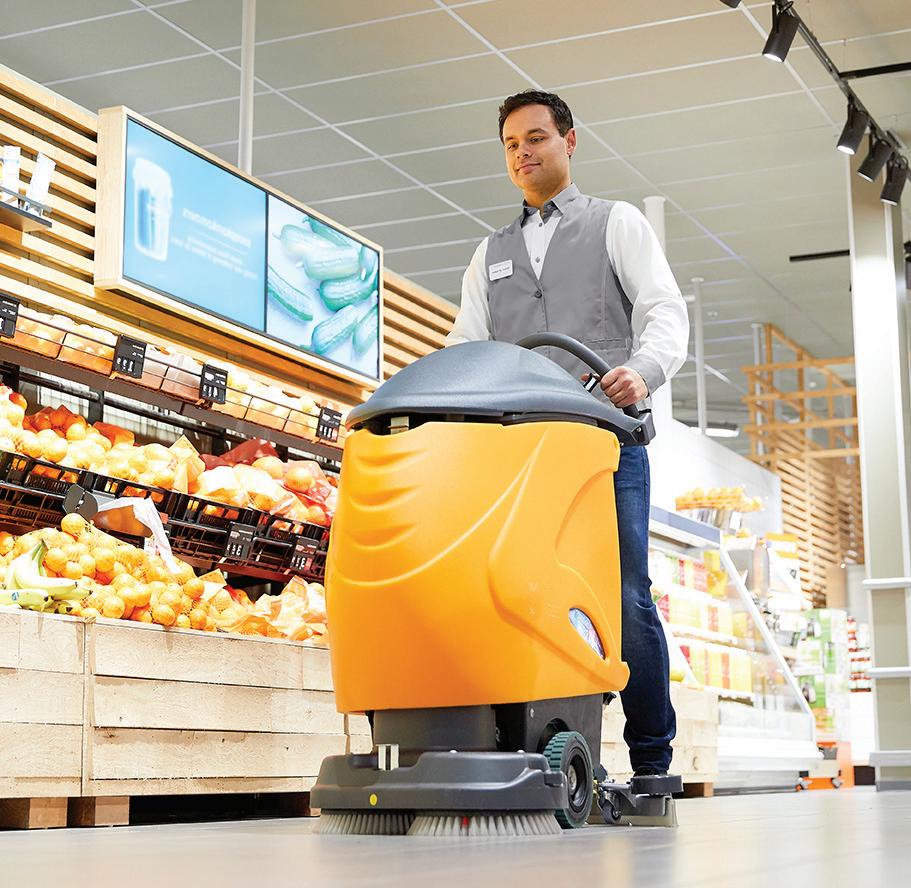
Partnership strengthens machine offering
WWW.DIVERSEY.CO.UK been looking for to become one of our UK distributors. Welcome aboard!”
Border Cleaning Machines Ltd has been established for over 25 years in Oswestry, Shropshire and operates throughout Shropshire and Cheshire and parts of Wales. It is a specialist in the supply of high-quality industrial scrubber dryers, sweepers, pressure washers, carpet cleaners, and industrial wet and dry vacuum cleaners. The company offers a full workshop repair facility and can also carry out on-site repairs and servicing from its fleet of mobile service vans. WWW.HOOPERSERVICES.CO.UK
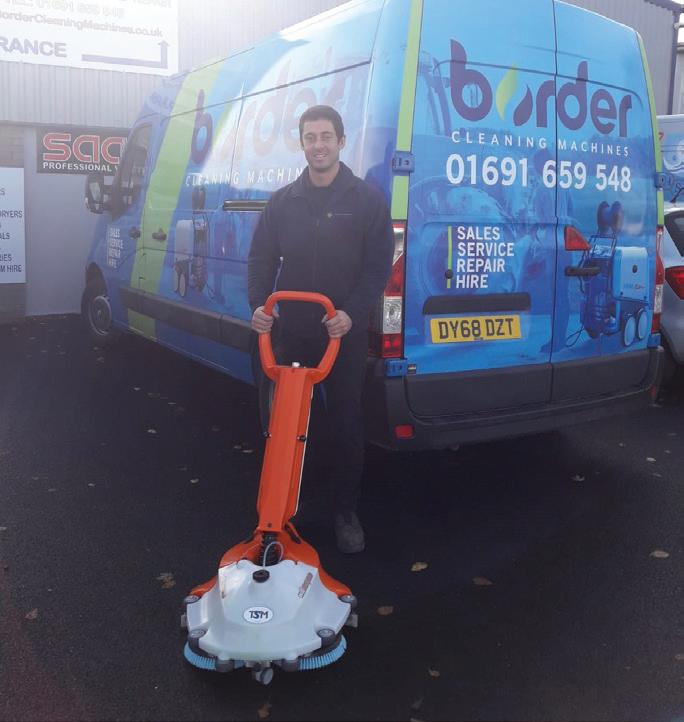
Textile wipes: reusable, recyclable and rentable
IT can be argued that cleanliness is a true sign of perfect standards in the workplace and in particular, on a factory floor or workshop. After all, if a factory isn’t clean, it’s possible that its processes and output are far from perfect too. In reality though, managers and employees have so much to think about, that keeping industrial machinery and the environment clean is often low on their list.
Factories and plants are naturally a greasy environment with oils and coolants often dripping onto surfaces and floors. Keeping areas clean and safe can be a challenge, but a clean working environment is crucial to efficiency and the health and wellbeing of employees.
Health and safety According to the HSE, Great Britain lost 28.2 million working days last year due to work-related illness and workplace injury. One of the primary HSE recommendations in addressing worker safety is the prompt cleanup of spills to reduce the risks of injuries from slips and trips and unnecessary exposure to hazardous substances.
Wiping cloths contaminated with hazardous substances are given the code 15-02-02 by the UK Environment Agency and must therefore be disposed of appropriately to comply with waste disposal regulations. Failure to do so can result in fines or even jail. Traditional cleaning methods Many industrial companies use rags or blue roll for all of their cleaning processes. Taking a onesize-fits-all approach, these rags and rolls are expected to clean up oil or chemical spills, safely remove metal filings, wipe down machinery, clean hands, and more. Lacking absorbency, an absence of specialty and an expectation too high for their capabilities, rags and rolls might leave the workplace cleaner, but certainly not clean. Adding to this that these items aren’t recyclable means the environment is impacted too.
Reusable, recyclable and rentable alternatives The situation is, however, changing for the better, with the advent of recyclable, rentable industrial cleaning wipes. These are far more absorbent that traditional materials, easier and safer to use. Such companies deliver high quality wipes and mats which, once used, are collected, laundered and returned to workplaces for reuse.
One of the leading European players in this sector is MEWA Textile Management which produces wipes at its factory in Immenhausen, Germany. Certified to EN ISO 14001 (Environmental Management), its range of highly-absorbent industrial cleaning wipes takes into account the varying surfaces that need to be cleaned by offering different weaves of cloth for different surfaces and applications. MEWA also offers an oil-trapping mat that actually absorbs up to three litres of engine oil, solvents or other liquids. Flexible in nature, the mat can be placed in any area where drips, leaks or spills might occur. It soaks up liquids and holds them in its special fibre core, keeping the surface dry.
Soiled wipes and mats are placed in a collection container and at an agreed schedule, MEWA collects the containers and delivers fresh wipes and mats without any interruption to the customer. The used wipes and mats are then thoroughly cleaned in an eco-friendly way, checked for damage and, once approved, put back into service - a circular economy - allowing them to be re-used up to 50 times. The washing process is in compliance with all legal environmental protection and disposal requirements. In fact, the oils and fats contained in the mats are separated, processed and used for heating and drying, further contributing to the reduction of energy consumption.
Reusable towels result in up to 95% less waste, use up to 48% less energy and represent around a third less global warming potential than virgin fibre paper. Even when compared to recycled paper, MEWA’s reusable approach scores highly.
This interesting new approach to cleaning is one that will undoubtedly save money, increase productivity, reduce injury risk, enhance overall quality, and allow staff to focus solely on their work without the worry of a dirty working environment. And of course, a clean and efficient factory will only serve the right impression to any customers or visitors to the factory floor. WWW.MEWA.CO.UK


Why getting the right wipe matters
WITH the extensive variety of wiping products available in the market today, it can be quite overwhelming to know which ones to choose. There are a whole host of cleaning wipe designs, from multipurpose, heavy duty to low linting, but do people actually know which wipe is the right wipe?
There are different wipes available for all industry sectors and each offer a range of unique benefits. The type of wipes a business uses can have a positive impact on the quality of its services and the safety of its working environment.
Not only does choosing the ideal wipe for your job ensure everything is cleaned properly with the right materials and chemicals, it also helps contribute to a healthy and productive workforce. Here are some reasons on why getting the right wipe matters and how it can assist your business.
Business efficiency Investing in the right wipe is a simple way to maximise cleaning speed and efficiency across your organisation. In addition, a higher quality wipe is important for completing operations more swiftly and boosting productivity. A properly selected wipe is more reliable, accessible and easy to use in all situations. The right wiping solution makes cleaning processes more effective and maintains cleanliness for longer, with less residue or fibres after use.
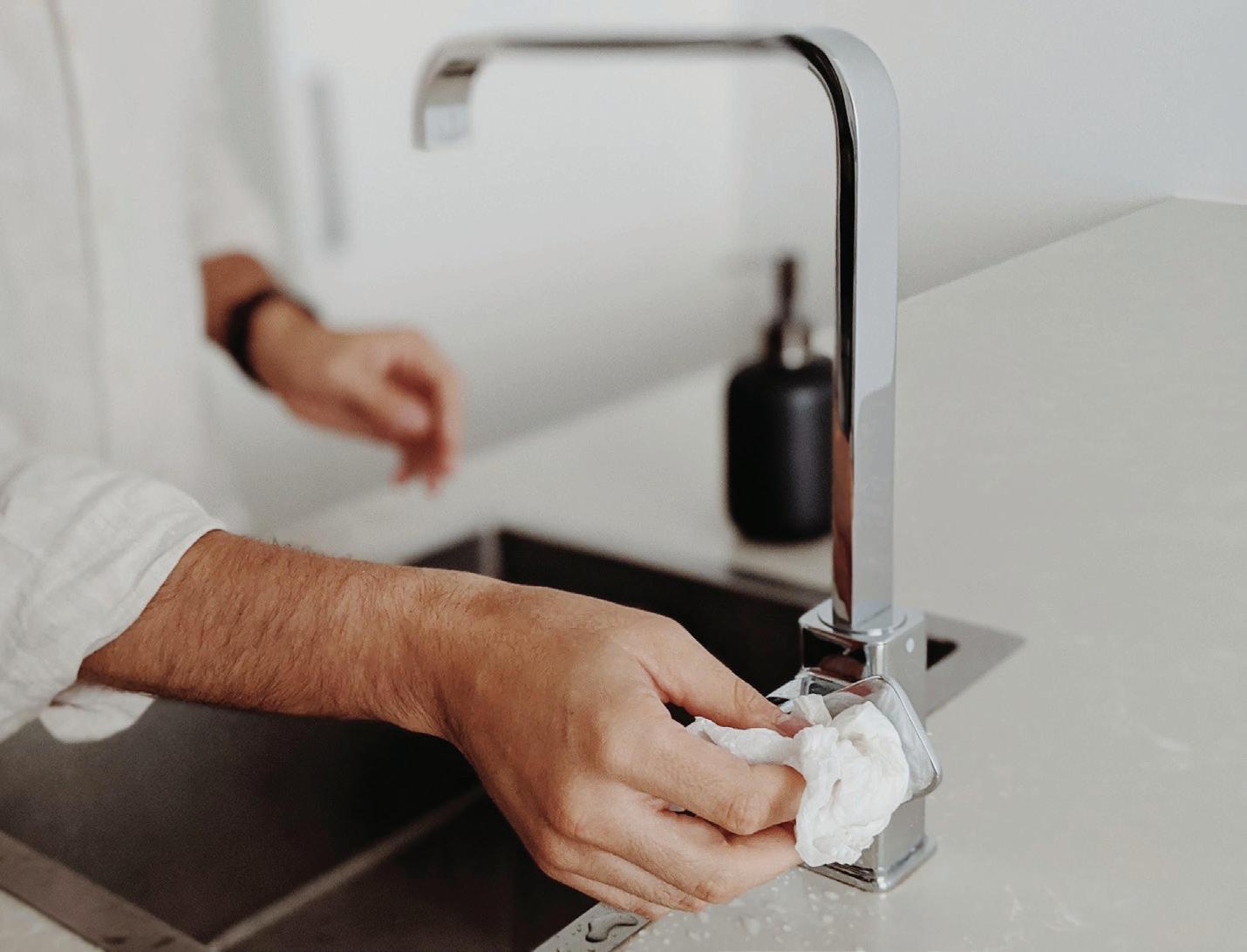
Reduce costs Cleaning budgets can also be limited, so it is key to make rational decisions when you purchase your wiping products. Although premium wipes may appear to be more expensive, they often provide multiple factors which help to cut cleaning costs.
As an example, industrial wipers and low lint cloths can offer a single-step cleaning process for superior wiping results first use. As well as a guarantee of little to no linting, tearing or shredding, you can get the job done more efficiently and with one wipe compared to using multiple wipes for the same process with a less efficient wipe.
Avoid cross-contamination When selecting a wipe, you’ll need to ensure it meets all necessary standards and be confident that surfaces are properly clean. By establishing a colour-coded cleaning system, this will assist with cross-contamination prevention and creates a more segregated cleaning solution to limit bacteria and viruses from spreading from one area to another. When using a wipe for an extended period of time there are also wipes that can help inhibit the growth of bacteria on the wipe itself.
Green cleaning While first and foremost it is important to have a wipe that is fit for purpose and does the job it is intended for, there are multiple ways to help the environment when selecting the right wipe. From using the wipe in the correct way which helps reduce overuse and therefore waste, to understanding the product makeup and from where the raw materials are coming which help reduce carbon emissions, there are multiple ways to help limit the impact on the environment.
Compostable wipes that will break down without leaving microplastics are also available. These wipes are eco-friendly alternatives which help to promote green cleaning.
COVID-19 The COVID-19 pandemic has highlighted more than ever the need for an effective cleaning process at all times. It is vitally important for businesses to take note and evaluate their workplace cleanliness and hygiene levels to eliminate bacteria and control disinfection.
By using the right wiping solution, it could make all the difference, from protecting staff and customers from contracting the virus to allowing everyday practices to continue normally. Whether it is a typical office, warehouse, factory, or clinical room, it is crucial that your wipes are appropriate for your setting and provide optimum level of safety.
Do you have confidence in your wipe? Getting the right wipe can have a valuable impact on every type of industry. However, our perception of cleaning products needs to shift as price is not everything. The attitude of simply buying any wipe must change if people want to maintain the highest standard of cleanliness and hygiene in their facility. WWW.HARRISONWIPES.CO.UK
Setting the standard for a cleaner future
For cleaning professionals, the onset of the coronavirus pandemic has only served to accelerate the requirement for optimum hygiene practices and infection prevention. James Taylor, marketing director specialties EMEIA at Berry Global, discusses the innovative cleaning solutions expected to play a critical role in meeting heightened expectations of cleanliness in the ‘new normal’.
NOW more than ever, effective cleaning practices and the close and careful sanitation of touch points, common surfaces, floors, and fittings is essential to keeping people safe. In a new age of cleanliness, where hygiene is coming under even greater scrutiny, failure to achieve high standards carries its own inherent risks.
While it is imperative that appropriate contingency plans and cleaning processes are in place to limit the risk in any setting, undoubtedly in certain environments the potential negative consequences of cross-contamination of harmful bacteria may be even greater. For instance, the broad spectrum of healthcare-associated infections (HCAIs), MRSA and at risk inhabitants, already place healthcare environments in a high risk category. Add to that the very real danger of the coronavirus disease, and the need for effective hygiene protocols becomes even greater.
Those in the industry who are able to adapt cleaning strategies to meet the increased demands placed on cleaning staff, and tailor them to the requirements of any given environment, are therefore likely to be able to achieve and maintain the highest hygiene standards in the post-pandemic landscape.
Central to any cleaning operation should be having the optimal solutions and tools in place in order to reduce the spread of pathogens and diminish infection rates, lessen the risk to the workforce and ensure compliance with cleaning standards.
Meeting the challenge With the prevention of cross contamination firmly in the spotlight amid the ongoing pandemic, one solution that has emerged as an increasingly valuable resource for cleaning team is disposable microfibre wipes and cloths - such as those produced by Chicopee, a brand of Berry Global and a leading producer of professional cleaning materials.
While traditional woven cloths have been a mainstay in the arsenal of cleaning professionals, with tests revealing around 30% [1] of the germs they pick up are deposited onto the next surface wiped, organisations are increasingly seeking more effective solutions. The superior cleaning performance and greater microbial removal proficiencies of reusable 100% microfibre cloths offer a logical alternative to woven cloth equivalents, but even such solutions have their pitfalls. For instance, 93% of laundered microfibre cloths still contain dangerous levels of bacteria even after washing, according to the American Journal of Infection Control.
Down to a science The limited time usage of microfiber-based solutions – such as Chicopee’s Microfibre Light - feature a unique structure that facilitates the removal of 99.99% of bacteria, securely trapping it in the material without the use of chemicals, and significantly reducing the risk of cross-contamination. By virtue of being completely disposable after use, it also safeguards against bacteria being released onto the next surface cleaned.
Increasing advancements in the material properties of such solutions - such as the utilisation of patented Chicopee’s Microfibre 4F fabric and APEX technology - facilitates the efficient removal and locking-in of dust and bacteria from any hard surface.
At the heart of disposable 100% microfibre solutions is a scientifically proven superior cleaning efficacy and lower pathogen transmission. Indeed, extensive testing at University College London Hospitals under simulated cleaning conditions - and against numerous bacteria - recently revealed that the number of median log10 MRSA and K. pneumoniae incorporating a soil suspension on the single-use solutions were consistently lower than reuseable (laundered) microfibre cloth comparatives.
Investigations were similarly positive in favour of disposable cloths and mops when determining the number of organisms present in pristine, laundered and disposable cleaning materials. While disposable cloth and mops displayed no relevant microbial contamination, spore forming bacteria were recovered from both pristine and laundered microfibre cloths and mop heads used for cleaning hospital rooms after washing.
Surface cleanliness Although the versatility and clinical performance of disposable cloths and mops make them an essential solution for any cleaning professional, inevitably decidedly niche cleaning procedures will require a more tailored solution. Surfaces that are customarily cleaned with spray and wipe systems, for instance, stand to benefit from advanced impregnated wipe systems.
The improved dwell times of innovative solutions - such as Chicopee’s Single Use Dispensing System (S.U.D.S.) - encourage better cleaning behaviour when compared to spray and wipe systems, where chemicals are often wiped off the surface with paper towels too soon.
A lower cost option than traditional presaturated wipes, cleaning professionals can simply add their own chemical of choice to the dispenser bucket and wiper roll to instantly create different high performing impregnated wipes for various areas. Such a degree of flexibility is an essential requirement for cleaning teams operating under budgetary restraints. What’s more, all this can be achieved while taking advantage of Chicopee’s patented Microfibre 4F fabric, a technical fabric specifically designed to deliver the power of microfibre cleaning while also releasing the maximum amount of cleaning chemical across the surface, and not locking it into the cloth. WWW.CHICOPEE.COM/EN-EU/MICROFIBRE
[1] Externally certified to officially documented test methods to produce a 4 log removal of S.aureus and E.Coli from a stainless steel surface, transferring 0% to a second surface.
THE Kardon pedal operated sanitiser dispenser combines advantages in hygiene with a professional design unique to the UK. These robust wood
Make your hand laminate dispensers come in a variety of colours to suit every interior. The sanitiser station foot operated solution reduces risk of contamination and requires no part of power supply. The dispenser comes with a 2.5 litre bottle so you can ‘fill and forget’. If the furniture you prefer to use your own pump dispenser, the internal mechanism can be quickly and easily adjusted. The bottle is secured behind a lock requiring minimum supervision from staff. Key features of the unit include: foot operated; powder coated steel internal mechanism; free standing, no-topple design with weighted base and optional floor bolts; fully mechanical - no batteries or power supply required; available in grey oak, medium walnut and light pine; available in two sizes – 129 or 123cm (h) x 30.5cm (w) x 30.5cm (d); the option to customise units with own branding; and an optional service contract available for sanitiser refills. WWW.KARDONLIMITED.CO.UK
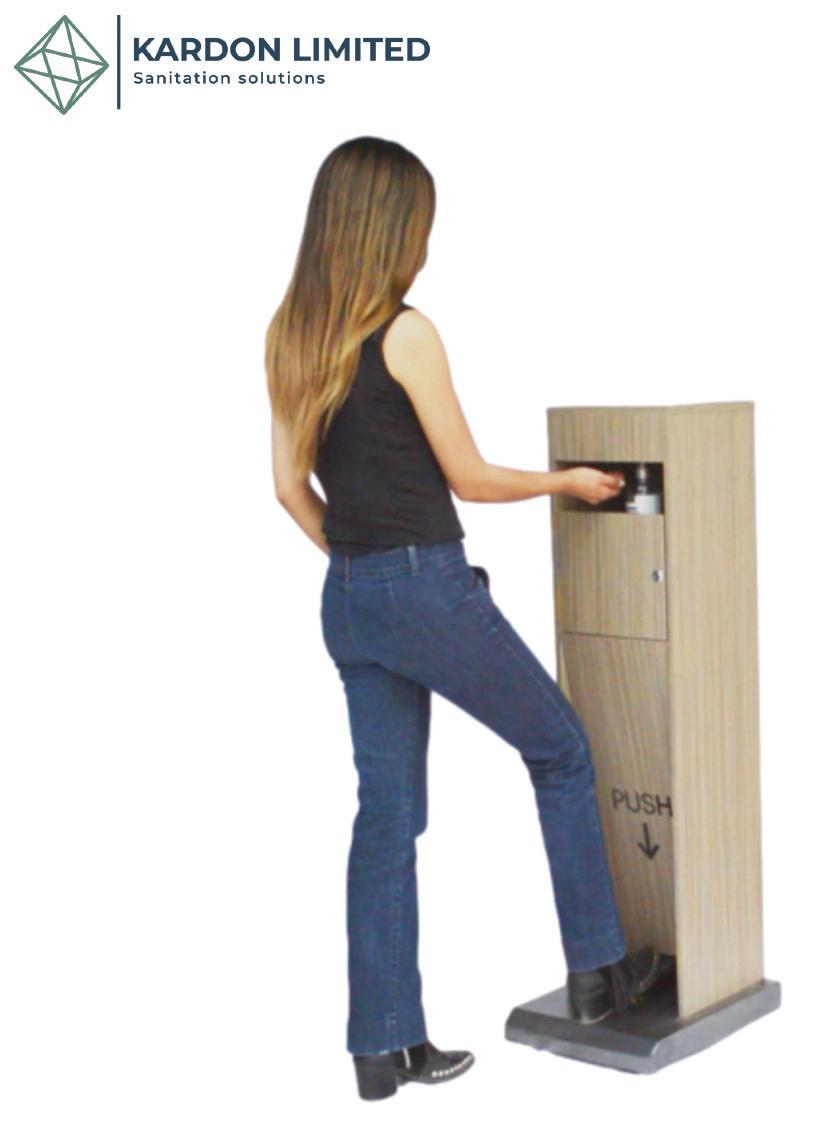
INFECTION control measures have forced the cancellation of many events this year, including traditional training courses. However, even with coronavirus prevention protocols that are currently in place, cleaning industry staff can still learn and develop their skills using the LMS offers Jangro Learning Management Solution (LMS). The Jangro LMS offers a flexible and contactless approach to training. Available to all ‘safe training Jangro customers and staff, this innovative, fully interactive and versatile e-learning platform is optimised for all devices. solution’ It covers a wide range of topics, with varying course lengths, so that users can train remotely at times that suit them. Joanne Gilliard, CEO at Jangro, said: “Training enables staff to perform their duties to a high standard, without risking their own health (or that of others). At a time when cleaning industry workers are putting their concerns aside to keep public spaces clean, hygienic and COVID-secure, ensuring they continue to have access to high quality and ongoing training is the least we can do for them.” WWW.JANGROLMS.NET
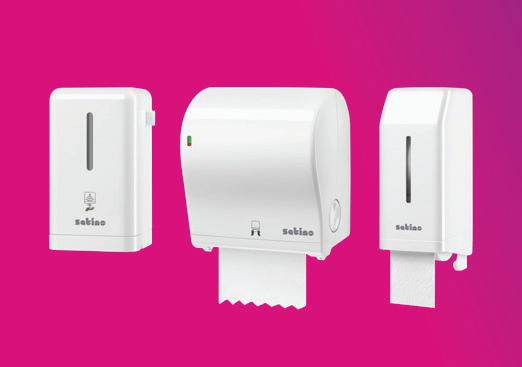
WEPA Professional, provider of sustainable, environmentally-friendly paper and washroom solutions in Europe, is introducing Satino by WEPA - a new brand
New range of cleaning and hygiene products for the UK market. The range will offer of washroom everything from paper towels, toilet rolls, kitchen rolls, and cleaning rolls, solutions to air fresheners, soaps, disposal systems, and washroom accessories, and will provide a variety of functional, sustainable options to meet the needs of introduced customers and washroom users alike. Targeting the independent wholesale sector and buying groups, the launch will be supported by a trade marketing programme incorporating strategic advertising and social media activity. Highlights from the new suite of products include: four soap/foam dispensers, with manual dispensing and sensory formats available; nine varieties of paper towel dispenser – one of which features a sensor function - to suit washrooms of differing sizes; six toilet roll dispensers, including jumbo and twin roll options; three waste bin options, available in 8, 23 and 43 litre capacity; and paper towels in w-fold, z-fold and v-fold formats. WWW.SATINO-BY-WEPA.CO.UK
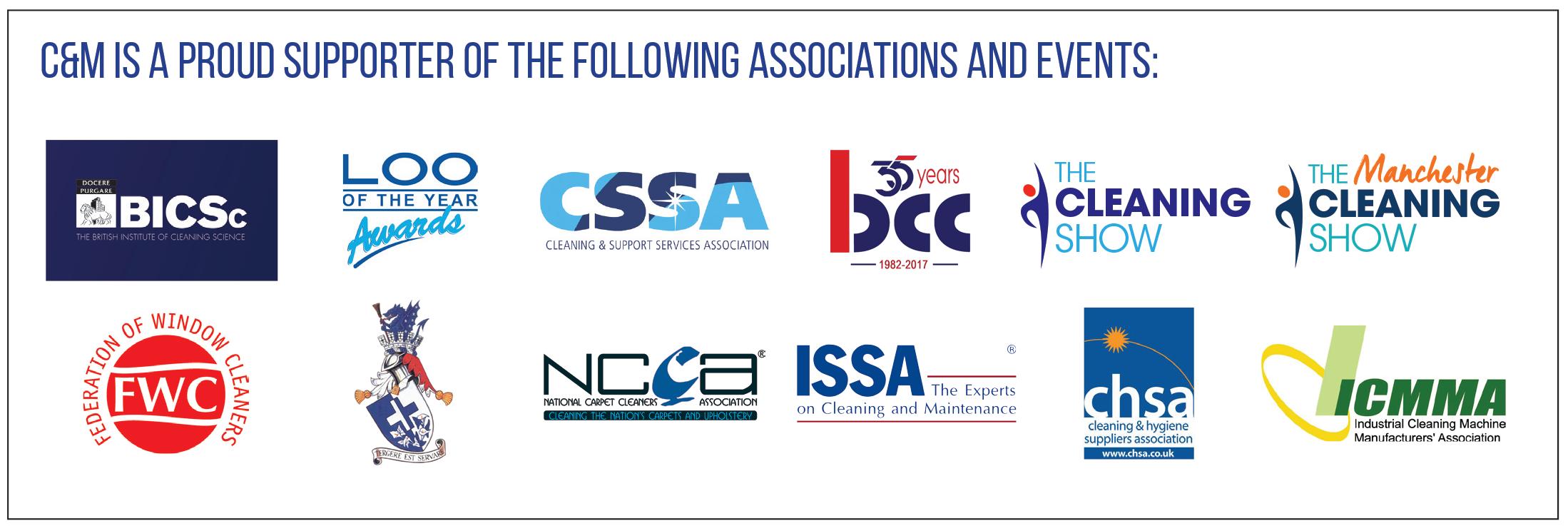
IN its first year of operation,
Spotta’s Bed Pods have reduced the amount of bed bug
Spotta puts incidents discovered by hotel bed bugs guests from 50% to just 3.3% to the test in its customers’ properties. The ‘always-on’ monitoring service uses AI-driven recognition technology to identify insects and provide real time alerts. The Bed Pod enables hotels, other accommodation providers and their pest control partners to identify occurrences of bed bugs and treat the problem early, limiting the damage pests cause.
Following its first year of real-world deployment in customer hotels - servicing over 91,000 room nights - 52.2% of detections made by Spotta were in rooms with no recent history of bed bugs, demonstrating the system’s effectiveness as an early warning against new infestations. Repeat detections in rooms helped hoteliers assess whether extermination treatments were successful or needed further, deeper treatment.
Across the 12 month period, Spotta was the first to identify bed bugs in 94.2% of cases, significantly reducing the number of guest encounters with bed bugs in multi-room properties. “For accommodation providers, most of the overall financial impact of bed bugs comes from contact between the guest and pests, which leads to complaints, bad reviews and loss of revenue,” said Robert Fryers, co-founder and CEO of Spotta. WWW.SPOTTA.CO
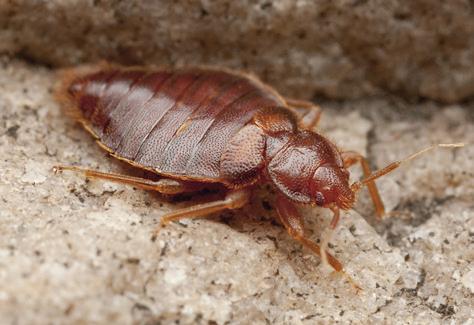
WITH the need for hand hygiene taking on a new urgency in times of COVID-19, Tork manager Essity has won the Visitor’s Choice Award at Interclean Amsterdam Online 2020 for its innovative and engaging hand hygiene training solution. VR training The Tork Virtual Reality app wins Clean Hands Training app is Interclean a training simulation aimed at improving hand hygiene in award healthcare. Essity collaborated with behavioural scientists, university hospitals and global hand hygiene experts to develop the tool. Jenny Logenius, global brand innovation manager at Essity, said: “We are proud to have been voted the Visitor’s Choice Award winner at this year’s Interclean Show. By offering fun and innovative training tools to healthcare providers we continue to support medical professionals as they improve hand hygiene compliance for improved patient outcomes.” WWW.TORK.CO.UK/TORKVR
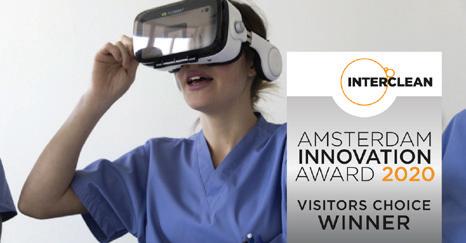
DIVERSEY has announced a 3% to 4% price increase across its Professional product ranges in Europe, effective 1 January 2021, Diversey due to continued cost movements and investment. Since the beginning of 2020, Diversey’s business has been announces confronted with significant challenges to supply chains,
European price exceptional demand increases and decreases across the different industries and sectors the company operates in increase and, most importantly, ensuring employees and customers stay safe. Sinéad Kwant , president Europe, said: “Whilst we continue to adapt our business to the challenge and absorb as much of the impact as we feasibly can, our investment and cost increases are significant and as a result we will be increasing the prices of all Diversey Professional products by an average of 3% to 4%.” WWW.DIVERSEY.COM
EDITOR
Neil Nixon neilnixon@quartzltd.com 07957 713316
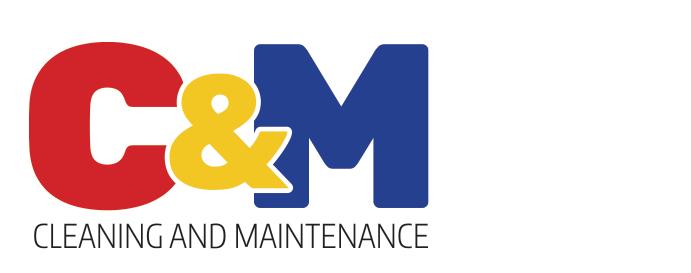
SALES DIRECTOR
BUSINESS DEVELOPMENT MANAGER
PRODUCTION MANAGER
Carol Baird carolbaird@quartzltd.com 01923 437619
MANAGING DIRECTOR
Tony Crinion
CEO
Steve Diprose
CO-CHAIRMAN Paul Michael
PAID SUBSCRIPTIONS & CIRCULATION ENQUIRIES
PUBLISHED BY
Quartz Business Media Quartz House 20 Clarendon Road Redhill, Surrey RH1 1QX 01737 855086 www.cleaningmag.com
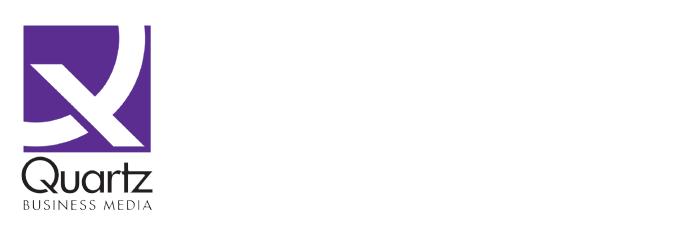
Annual Subscriptions 12 copies per year (10 print & 12 digital) UK: 1 yr £125; 2 yrs: £224 Rest of the world: 1 yr: £174; 2 yrs: £310
ISSN: 1473 723X © Quartz Business Media, 2020
All rights reserved. No part of this publication may be reproduced in any form or by any means, without prior permission of the copyright owner.