
4 minute read
Lubrication: Interglass
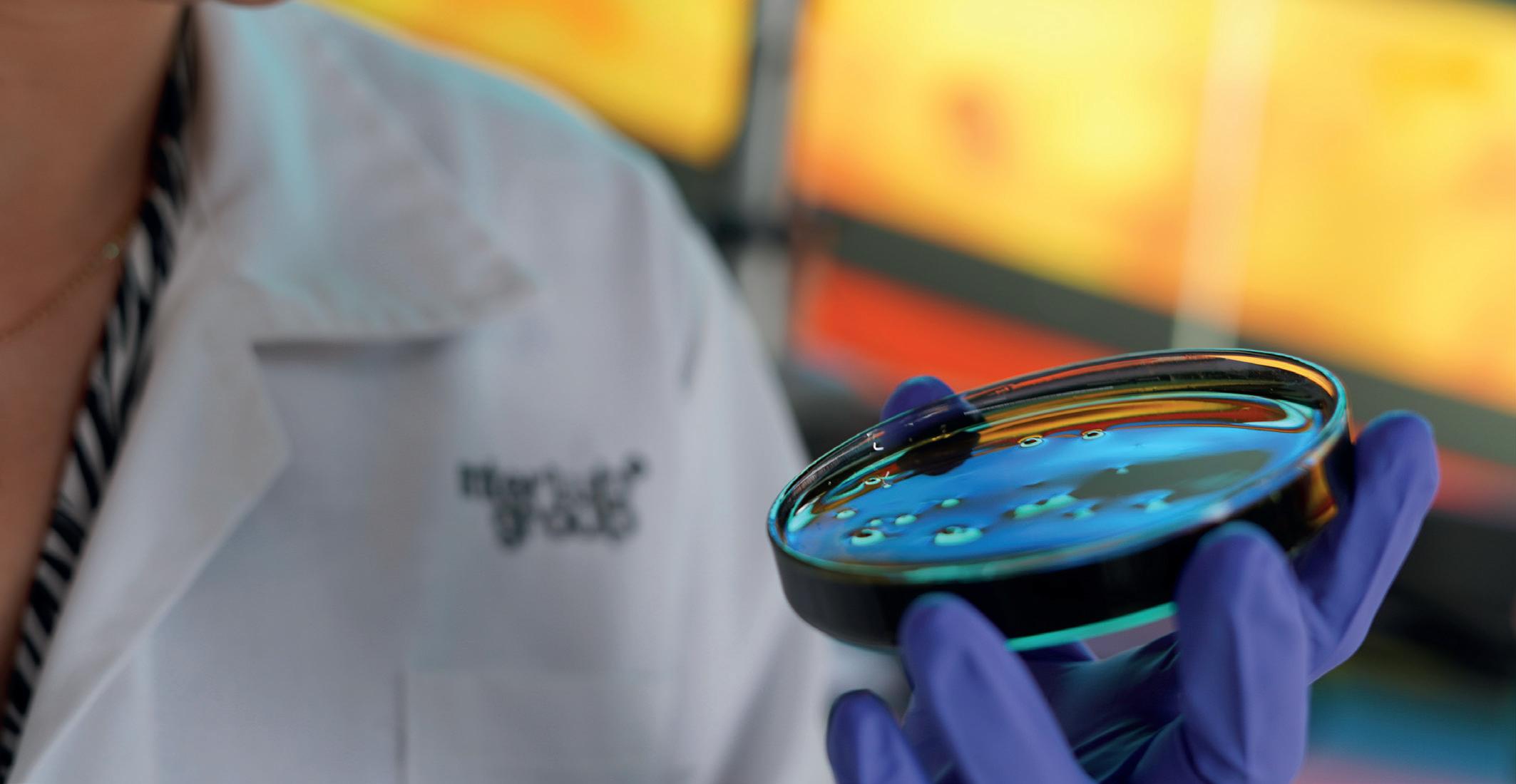
� Pic 1. Inside Interglass’s laboratory based in Zapopan, Jalisco, México.
� Pic 2 . A lubricant sample from Interglass’s factory.
Sustainably sourced lubricants for the glass industry
José Luis Vélez Escalante* outlines how Interglass will help the glass industry reduce its environmental impact through sustainably sourced and biodegradable lubricants.
As members of the glass industry, we all tend to think that our carbon print is next to zero. This idea is based on the fact that the final product coming from a glass plant (the glass container itself) is close to fully recyclable and therefore can be considered as selfsustaining.
But we usually leave aside the fact that during the process of production that takes place inside a glass plant, there are several aspects that inevitably create pollution and may harm the environment in the long term.
Aspects such as the high energy consumption needed to keep a furnace running 24/7, the constant emission of toxic gases going to the atmosphere or the amount of waste created by all the steel parts constantly being used and disposed, are some examples of this.
Therefore, even when we are certainly one of the most self-sustainable industries, there is still room for improvement. That is why at Interglass, we are constantly looking for ways to make our contribution towards this goal (Pic 1).
Biodegradable lubricants
lubricants, many people don’t understand what this means. Typically, people think these lubricants degrade as soon as they leave a mechanism. This, however, is not how biodegradable lubricants work.
According to the OECD 301B, the most recognised biodegradability test, to consider a lubricant as easily biodegradable, at least 60% of it must decompose within 21 days. However, these numbers may vary from test to test.
This does not mean that if you dispose of a biodegradable lubricant it will simply disappear after 21 days. These degradation values exist only in the controlled presence of bacteria, used specifically for tests like these.
Consider, too, that not all components in biodegradable lubricants are entirely biodegradable. When we say that a lubricant is biodegradable, we refer to the base oil that makes up the bulk of the formula.
Depending on the lubricant (Pic 2), we may find that more than 30% of its formulation contains non-degradable components. The breakdown of a typical lubricant includes base oils, thickeners, and additives to improve its performance.
Ester-based oils
One of Interglass’ greatest challenges is creating lubricants that not only get as close as possible to complete degradation, but that also have raw materials that come from more sustainable sources. Esters are fundamental in developing these biodegradable lubricants.
For more than six years, Interglass has invested in its own ester fabrication. We are one of the few companies in the American continent to have its own esterification plant, which we use to create base oils specifically for each individual lubrication challenge.
This capacity gives us the flexibility to serve different market needs.
Besides having biodegradable properties, esters are available from more sustainable sources since they don’t come from fossil fuels. By not being reliant on market-available materials, we can create truly customisable products that fully satisfy client needs. This capacity for customisation also allows us to create products that bring us closer to achieving our sustainability goals.
Sustainably sourced additives
� Pic 3 . The R&D team at Interglass.
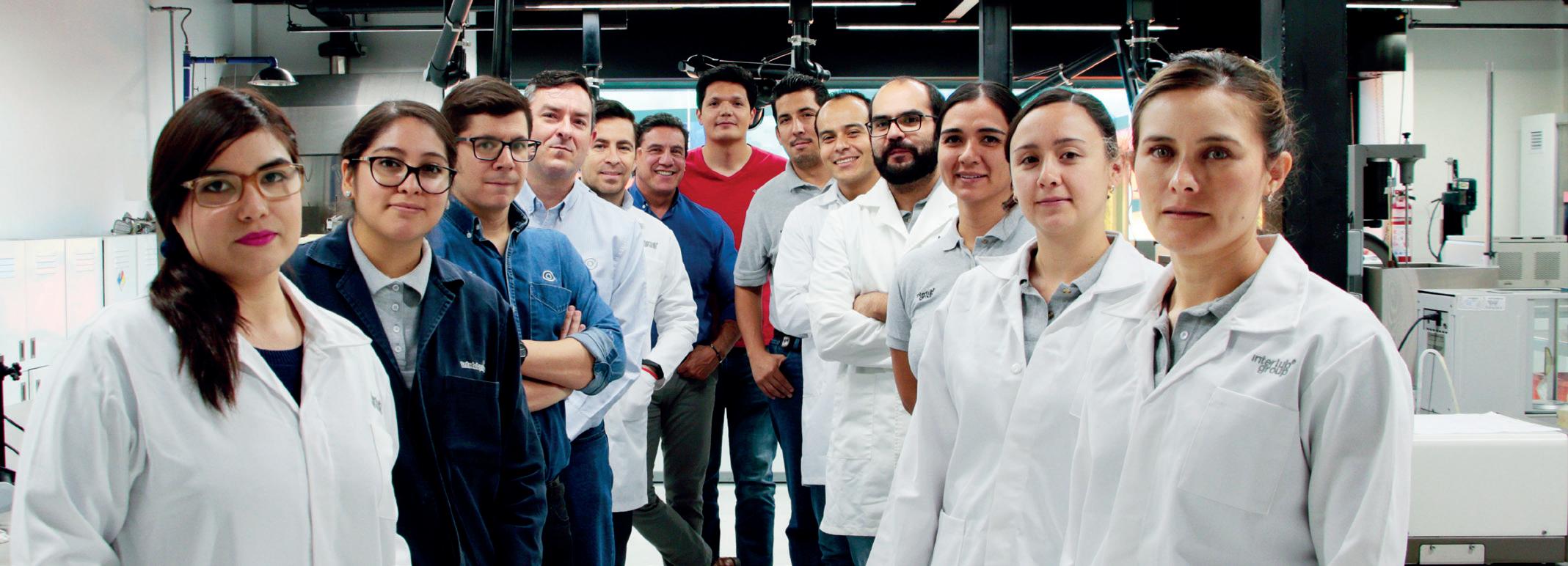
lubricant formulation. Additives are materials we add to lubricants to give them new properties or augment existing ones. There are a wide number of additives in the industry, with antioxidants being one of the most crucial.
As their name would suggest, antioxidants stop the oxidation of base oils, making an impact on a lubricant’s service life and resistance to high temperatures, which are extremely important to the glass industry.
As part of our efforts to develop products with a low environmental impact, we’re actively working on obtaining antioxidative components from agro-industrial waste, such as coffee. This means these materials come from more sustainable, low-impact sources than those readily available in the market.
This project’s innovation resides in developing an inverted micelle that encapsulates phenolic compounds extracted from coffee waste, capable of staying liposoluble - with minimal water content.
Through this project, we’ve ventured into biology and nanotechnology, which have brought our R&D team (Pic 3) to make strategic investments to remain knowledgeable in these areas.
Oleogel thickeners
As a fi nal element in the search for products with a lower environmental impact, we’re developing gel-based thickeners from sustainable sources such as shrimp shells, of which we currently have very promising prototypes.
This product comes from mixing the biopolymer chitosan with different types of vegetable-based oils or esters that align with our sustainability goals.
Future goals
Our efforts to develop better lubricants go beyond biodegradability: we want to develop lubricants that perform far better than those currently available in the market. By achieving this, we get closer to having carbon footprint-free lubricants, which would usher in a new generation of superior lubrication. �
*Managing Director, Interglass, Jalisco, México https://interglass.com.mx/
HIGH GLASS From Refractories to Hot Gas Filtration
for crystal clear results
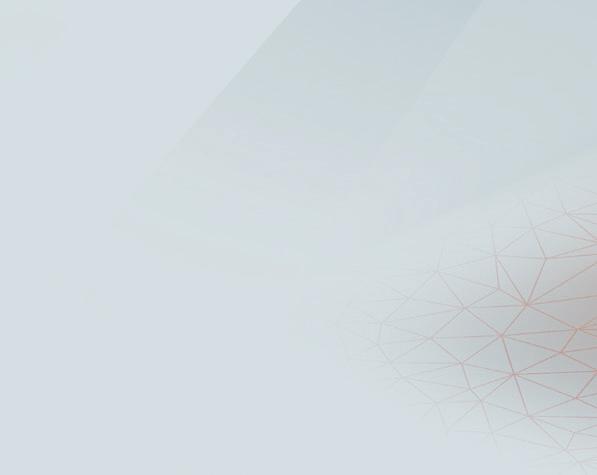
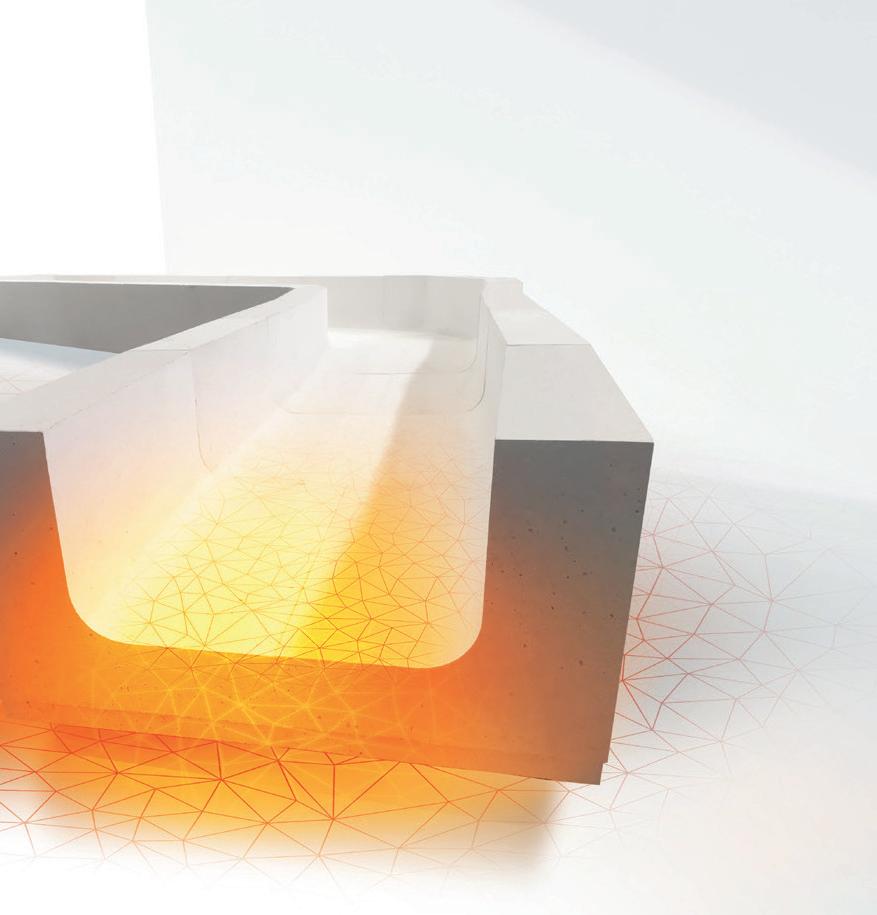
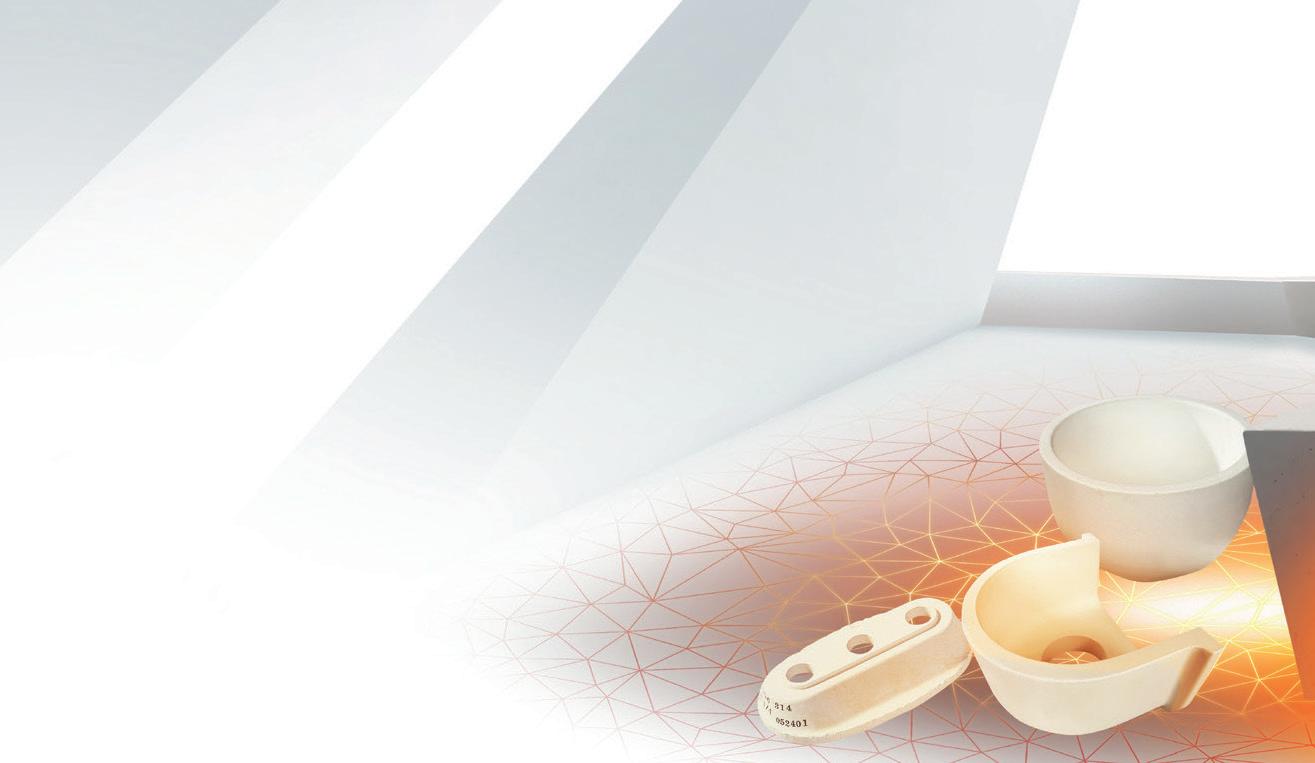
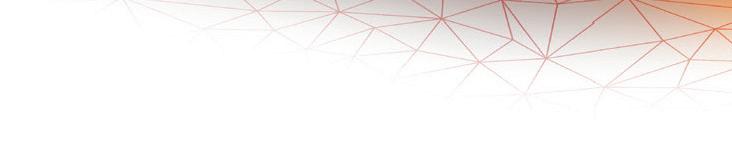
Regenerator Melting end Working end Forehearth Feeder Hot gas filtration
Experts in industrial glass applications RATH offers you the complete range of highest-quality refractory materials for the entire glass making process, including corrosion-resistant feeder expendables, forehearth systems and the original Emhart Glass System. Also benefit from our filtration of hot gases with our catalytic and non-catalytic filter elements. Contact our experts for your solution!