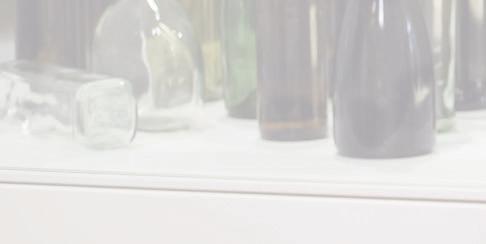
5 minute read
Renewables: Wiegand-Glas
Wiegand-Glas adds biomethane to the Eco2Bottle toolbox
German glassmaker Wiegand-Glas recently partnered with biomethane producer bmp greengas for its customer soulproducts. Lukas Neubauer* discusses why the use of biomethane can play a part in the manufacture of a ‘greener’ glass bottle.
� The partnership with bmp greengas is part of Wiegand-Glas’ ‘Eco2Bottle toolbox’ which aims to make the company a more sustainable manufacturer.
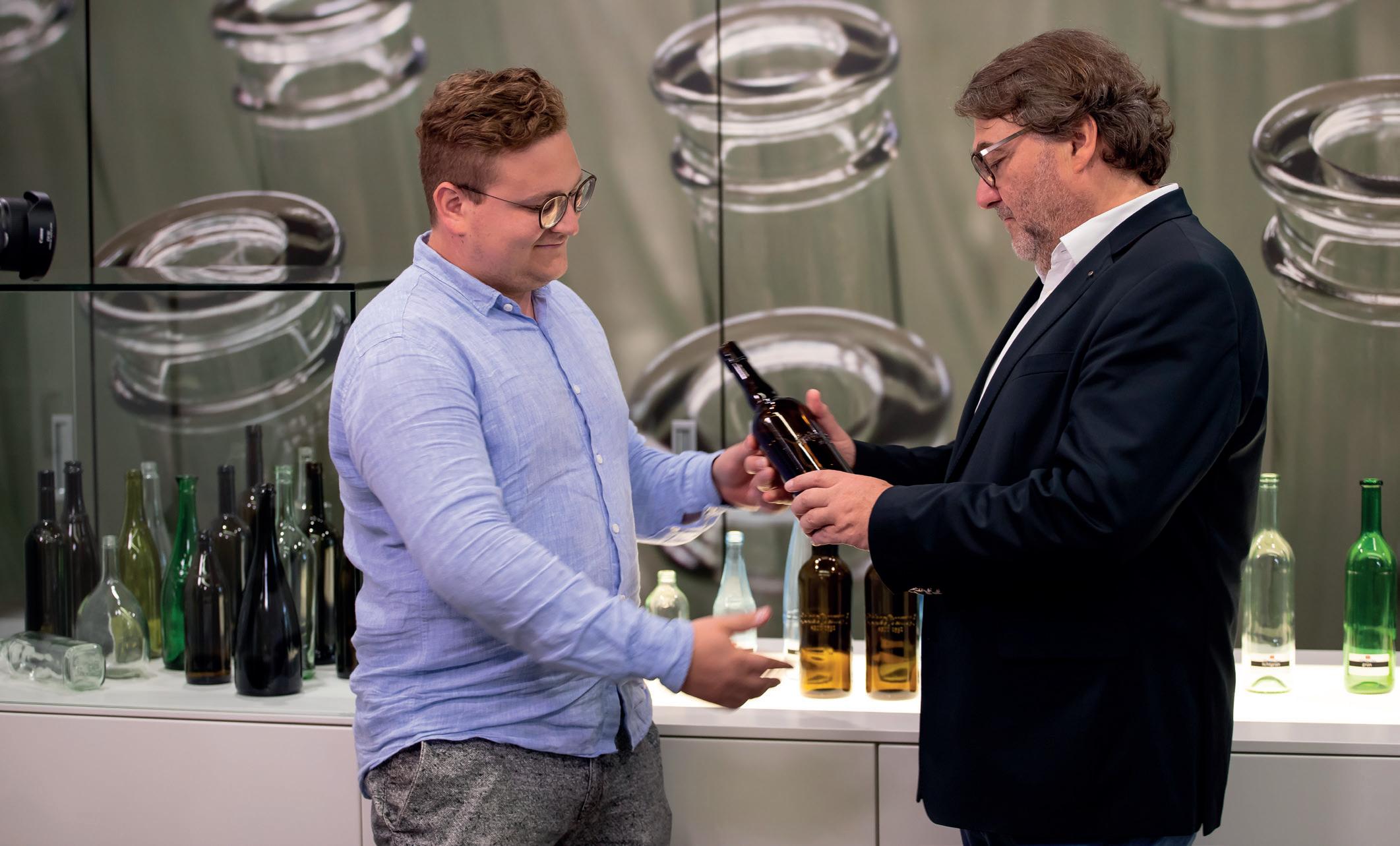
Reusable glass packaging can be used around 50 times before it is melted down again and put to a new use.
So glass fulfi ls the requirements of a circular economy in terms of reuse and recycling to the highest degree. Nevertheless, in many cases more can be done to improve the energy balance of glass containers. This is because glass production, from melting to forming and beyond, is an energy-intensive process that often makes use of natural gas. Wiegand-Glas has reacted and in doing so has also fulfi lled the wish of soulproducts GmbH: the production of a product line with biomethane.
Wiegand-Glas launched the Eco2Bottle concept in 2020, sending a clear signal for environmental protection and resource conservation to the market and its customers. The concept envisages avoiding, reducing or compensating CO2 emissions in all production steps - together with food and beverage producers all the way to the consumer. “It all comes down to individual solutions,” says Lukas Neubauer, Head of Controlling & Corporate Development at WiegandGlas. “We look at each customer, each market and each product very closely, provide recommendations for the entire supply chain and then develop the right packaging solution with the help of an optimally coordinated toolbox.” Consideration is given to power supply, recycling, the weight of the glass, further packaging, logistics and, of course, the energy needed for the production itself.
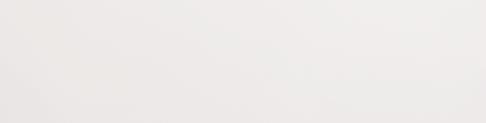
Eco2Bottle toolbox
Already from the fi rst Eco2Bottle, the 0.75 l. Bordeaux bottle, the possible measures for avoiding and reducing emissions are well known, which is why they are only briefl y explained below. The electricity used, which comes from the normal
� Biomethane is a natural energy source so no emissions are emitted during the production process.
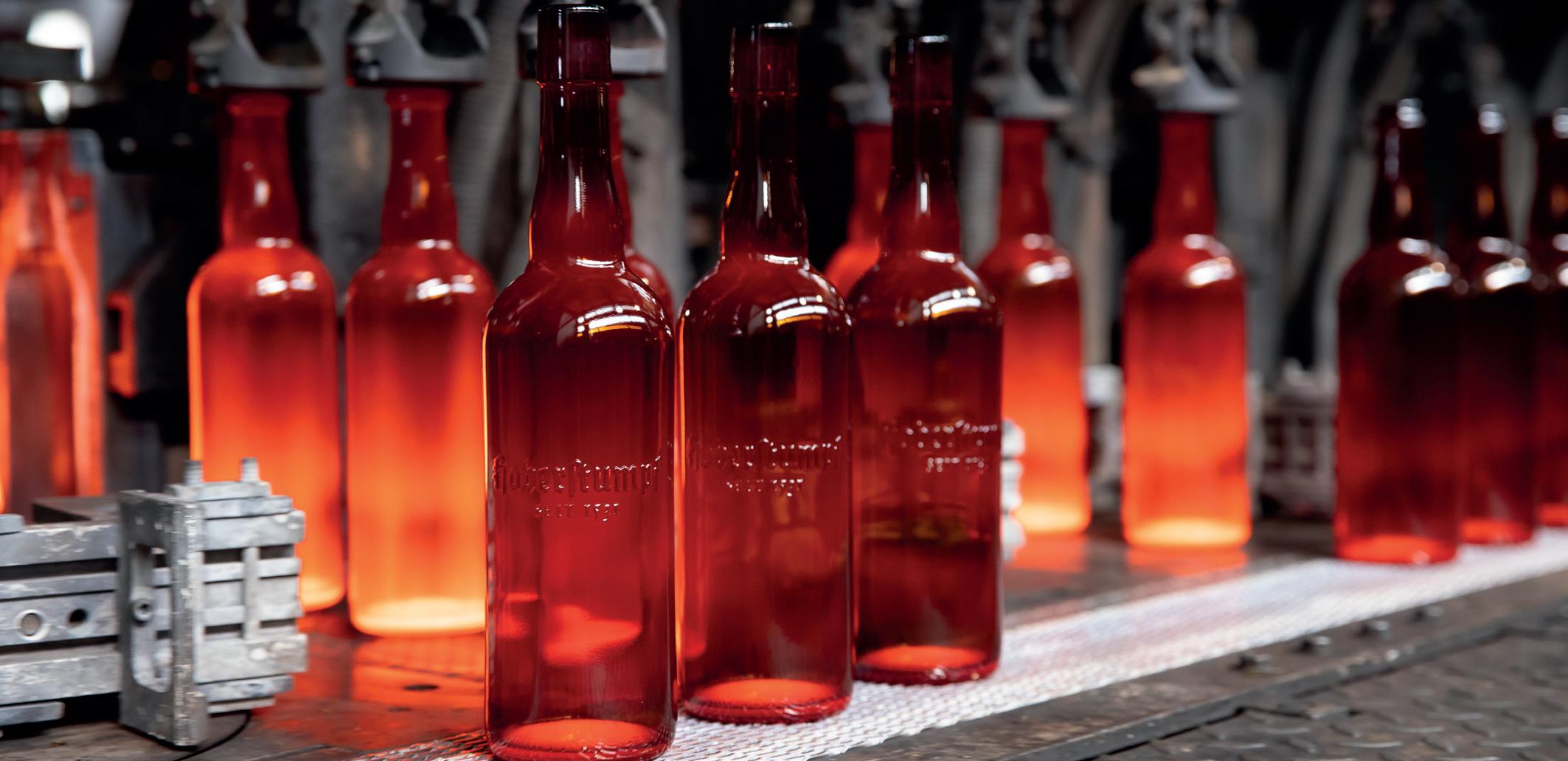
German electricity mix, can be replaced by green electricity.
Wiegand-Glas currently uses green electricity generated from hydropower. Furthermore, for each packaging it is checked whether the weight can be reduced or the amount of cullet. Less energy is needed to melt the old cullet than would be required for primary raw materials.
In addition, the packaging design is optimised, if possible. Attention is paid to using reusable intermediate layers instead of corrugated cardboard layers, and at the same time trying to get as many bottles as possible on to one pallet.
With the production of the soulbottle, the possibility of replacing the natural gas used in production with biomethane was added for the fi rst time. Soulproducts gave Wiegand-Glas the impetus to switch a complete production to biomethane and that’s how the contact with bmpgreengas came about.
“By using biomethane, we are resorting to a natural energy source generated from biogenic gases,” Lukas Neubauer reports.
“This avoids emissions that would otherwise occur when burning natural gas in the production process.” Especially in energy-intensive industries like the glass industry, there is a huge potential of CO2 savings with biomethane.
Roughly, it can be said that the use of biomethane can save about 30 to 40% of the total emissions per packed tonnage, based on the ‘cradle to customer plus waste’ approach.
The percentage given depends on several factors, including cullet use, glass colour and, most importantly, the furnace at which the item is produced.
Feeding biomethane
Due to its calorifi c value properties, biomethane can be transported via the existing gas network without technical conversions, long-term preparations or additional investments. By purchasing biomethane, Wiegand-Glas gives the order for a certain quantity to be fed into the balancing circuit of its energy supplier, which it can then use for production
Additional costs
Even though the price of gas has risen sharply in recent weeks and months, companies still have to dig deeper into their pockets for biomethane.
So it defi nitely involves a certain willingness to invest to reduce CO2 emissions. However, feeding biomethane into the grid also brings advantages for companies subject to emissions trading. This is because under the Federal Emissions Trading Act (BEHG) and the European Emissions Trading Scheme (EUETS), biomethane is currently exempt from the CO2 price up to and including 2022, and even for an unlimited period depending on the substrate and verifi cation.
Biomethane quality
It is important to know that there are very different biomethane qualities. The term ‘quality’ is a little misleading here, because all biomethane is fi rst of all good, green gas, whether produced from liquid manure, energy crops or biogenic residues and waste. However, it does make a difference where and how the biomethane is produced or obtained. Whether in Germany or in other European countries, from maize or municipal waste. WiegandGlas currently uses biomethane obtained from German municipal waste, as this is particularly regional and sustainable.
Perspective and news
Within the framework of an Eco2Bottle project, Wiegand-Glas customers now have yet another opportunity to genuinely reduce emissions by using biomethane in the production of their glass packaging.
Furthermore, it also applies that with each customer it is checked individually which measures make sense and how these can be implemented step by step. Thus, after the soulbottle, other Eco2Bottle projects followed in which biomethane was used, for example the fi rst beer bottle as an Eco2Bottle, a 0.75 l. individual bottle for the Haberstumpf brewery in Trebgast, Northern Bavaria �
*Head of Controlling & Corporate Development, Wiegand-Glas, Steinbach am Wald, Germany https://www.wiegand-glas.de/en
Mr Neubauer will speak at the Renewable Glass Manufacturing conference, held digitally on November 9 and 10.More information via www.glass-international.com
WHEN QUALITY MATTERS
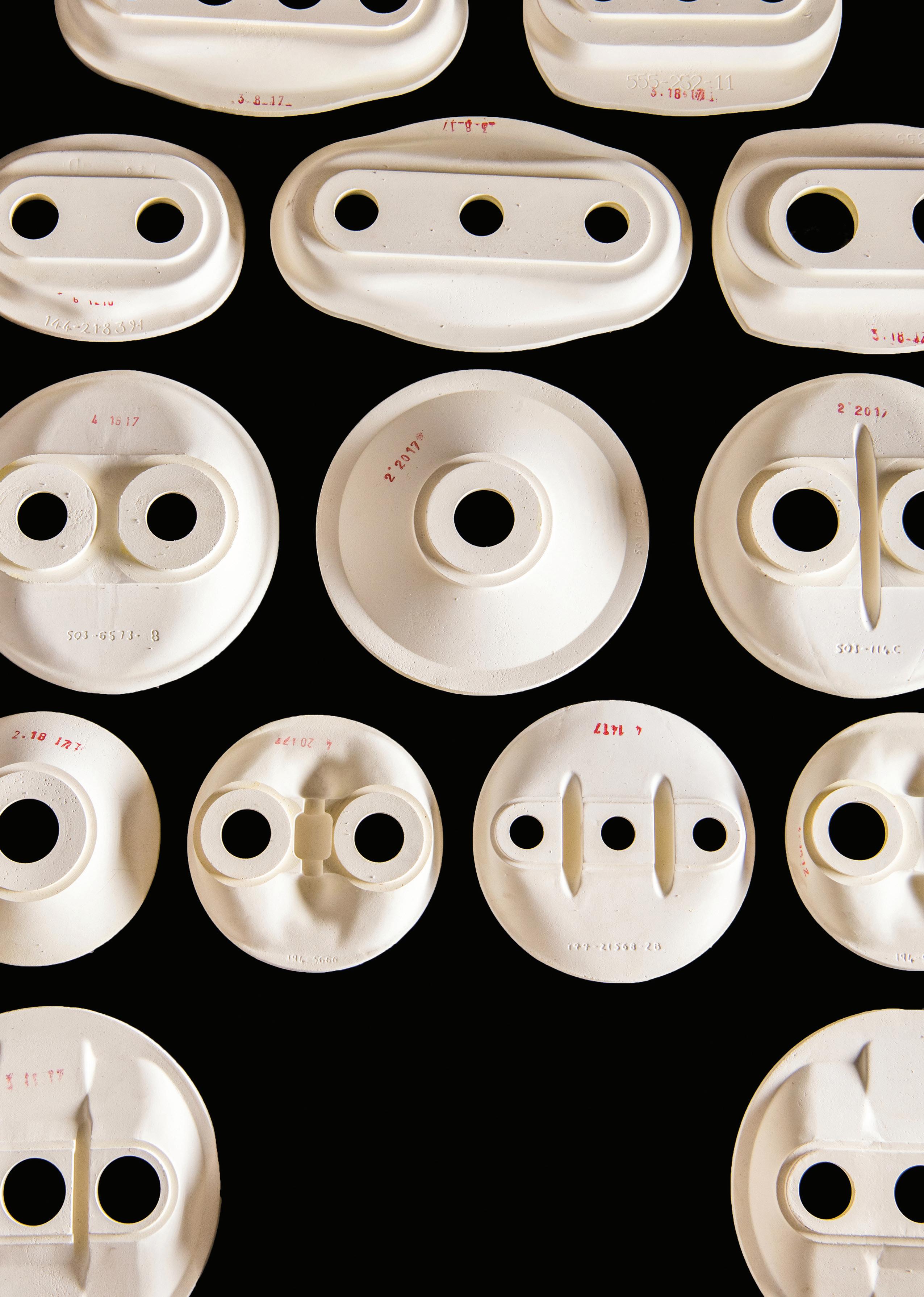