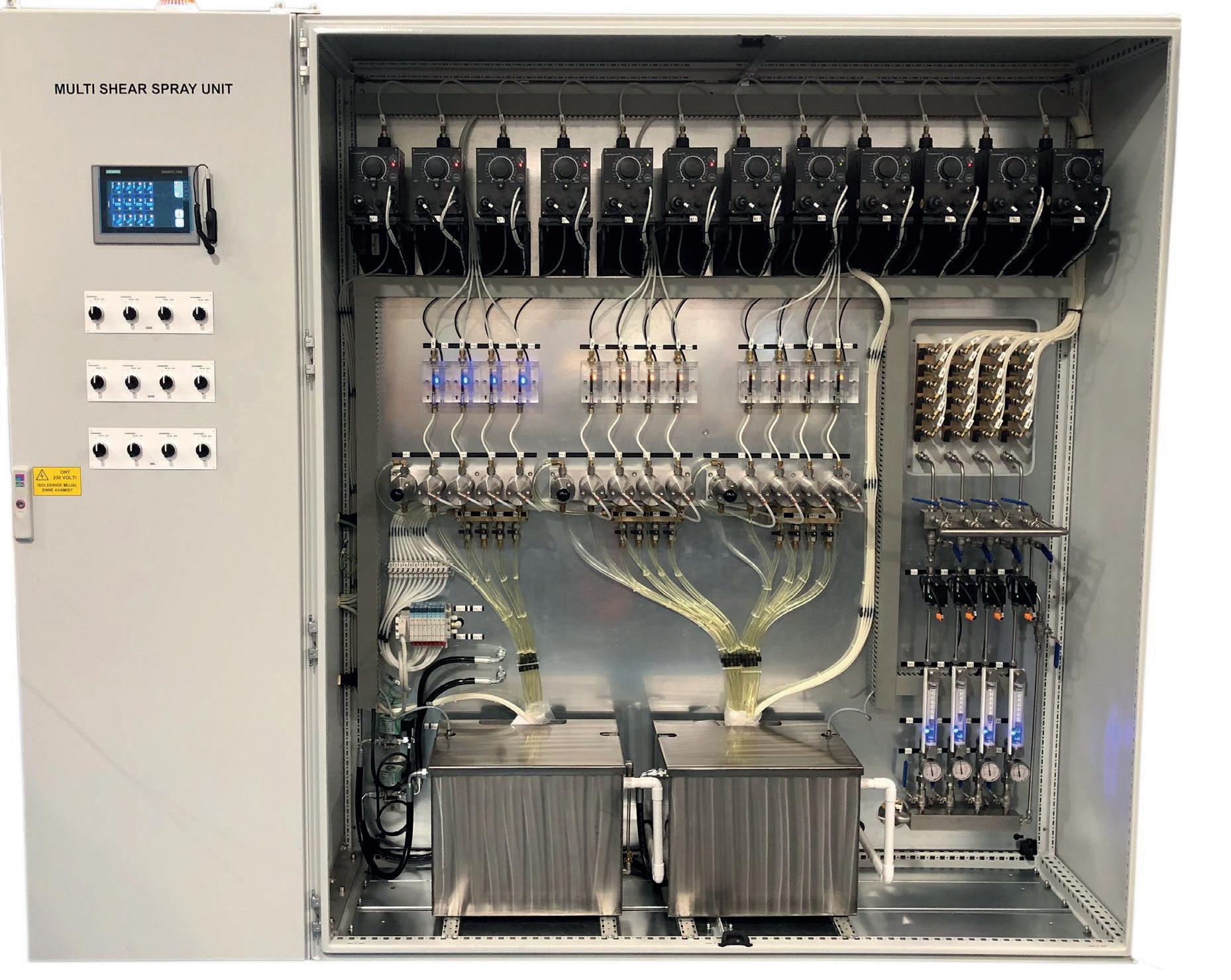
5 minute read
Lubrication: Graphoidal
A complete lubrication package for glass manufacturing
Andrew Clarkson* explains how Graphoidal can provide a total package for an integral part of the bottle forming process.
Graphoidal Developments, the Chesterfield, UK-based lubrication and engineering systems specialist now offers a complete solution for shear and gob delivery lubrication and cooling.
Its expertise is in precise pumping, control of mixing, dosing and spraying of the lubricants and coatings which form a vital part of the glass production process, both in hot end and cold end areas.
As a Rondot Group company, its success has been achieved by providing our customers with the support they require, with the ability in some instances to remotely support with our advances with Industry 4.0.
With thousands of products installed globally, Graphoidal Developments has a proven track record in the supply of quality equipment to the glass packaging industry.
Development of the Graphoidal Multi Shear Spray Unit brings further benefits with the addition of upper funnel lubrication, as shear and gob delivery is a critical component to the bottle forming process. (Fig.1)
The addition of lubricating the upper funnels improves the delivery process, whereas previously the funnels may have relied on excess lubrication from the shears with no control.
With Graphoidal’s direct lubrication process, it gives the customer full control of their lubrication, with the ability to manage consumption.
The reduction in oil and water usage on the delivery system can potentially reduce container defects, which could also reduce consumable costs.
Graphoidal’s centralised shear, funnel and scoop system provides the operator with a central control station.
The user-friendly easy-to-use software empowers the operator to independently monitor oil consumption on a line-byline basis, while also allowing the user to accurately alter the dosing ratio to tailor the lubrication for the gob delivery equipment.
The industry requires consistency for all aspects of the production process, this is achieved by the equipment monitoring and control programmed into the shear spray system.
To have accurate repeatability offers better and sustained gob delivery, reducing oil and water consumption.
Bacterial growth is a risk that can affect shear spray systems causing unexpected downtime and a loss in production. Using an Oil in Air system, the Oil is mixed with the water at the Spray Bar eliminating the potential for bacterial growth within the pipework, potentially reducing production downtime and unexpected maintenance.
The ability to dose of up to 1/2000 ratio Oil to Water consistently, precisely with automatic back and detailed human interface unit offers confidence and great return on investment.
Graphoidal Multi Shear Spray Systems have been designed to keep up with a fastmoving consumer goods environment, and to instil assurance and reliability that is a necessity for the container glass industry.
The system is equipped with automatic redundancy programmed to activate under alarm conditions. This ensures consistent and stable lubrication delivery while reducing the impact to production.
Easily defined alarms allow for quick and easy fault finding, combined with on-site training given by our specialist
� Fig 1. 4+4+4 Shear Funnel and Scoop MSSU.

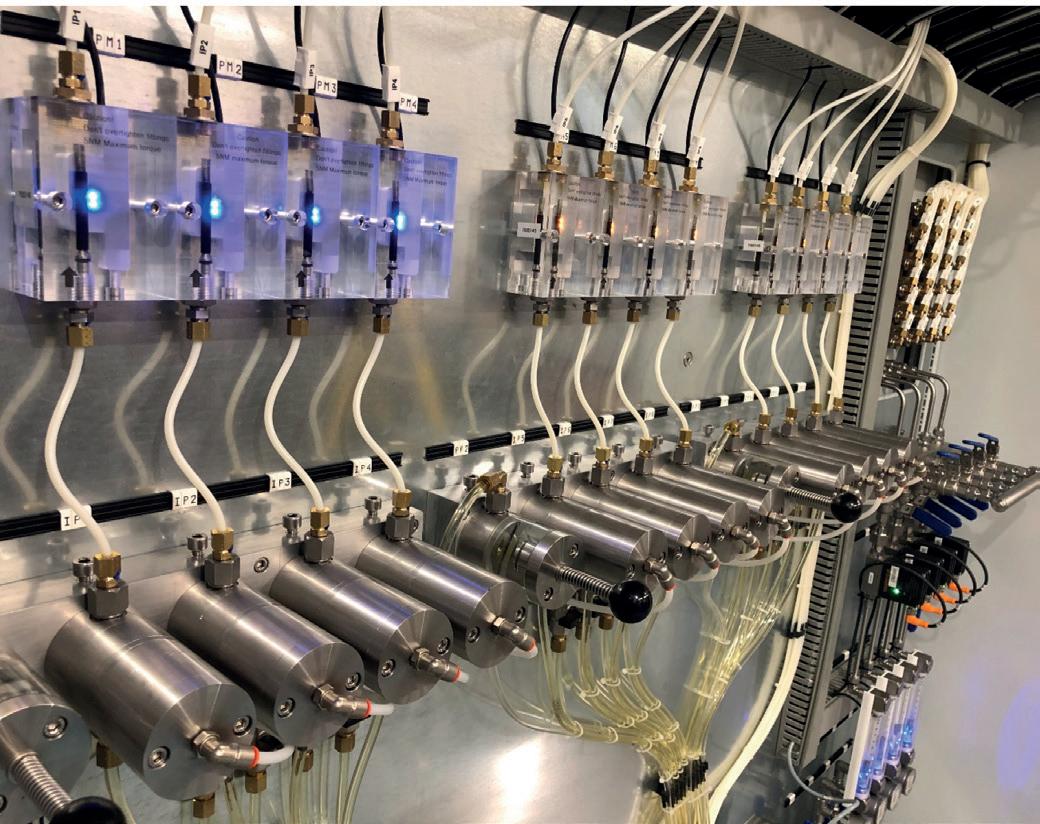
� Fig 2. Graphoidal precision dosing pumps with individual monitoring blocks. � Fig 3. Individual line backup pumps.
engineers, provides the user with the knowledge and capability of, on site fixes, reducing associated production down time (Fig 2).
Having efficient cooled and lubricated Shear Blades is imperative for the bottle forming process; too much water can have an adverse effect on the cooling process and is found to be inefficient and non-economical.
Graphoidal spray bars are designed to create a fine, atomised mist that cools the blades through evaporation.
Evaporation cooling the blades provides the most efficient cooling and lubrication with minimum consumption.
The ability to supply different oils to the Shears, Funnels and Scoops independently, offers a great range of diversity to tailor the lubrication process.
With ever increasing costs for materials, demand for more efficient and economical equipment is high.
Container glass groups require a premium quality system that delivers on application, efficiency, and a great return on investment.
Graphoidal is committed to developing innovative products that can be tailored to each project to provide highly efficient lubrication solutions to make its customers manufacturing process more efficient, productive, and profitable (Fig 3).
Floor space is at a premium within any manufacturing environment, so the ability to integrate systems together to reduce the number of cabinets is an advantage.
By integrating the lubrication of Funnels with the Shear and Scoop system, it has created a one-point reference for all the production lines.
Graphoidal’s automatic ratio control powered by Siemens technology provides an intelligent system, which encompasses the ability to manage dosing, relevant to water flow.
Sensors built into the cabinet allow the system to identify pulses from oil flowing through Graphoidal pump monitor blocks.
The easily identifiable LED indicates via a flash using neodymium magnets to show oil is dosing but can also indicate fault conditions by a constant flashing light aiding in fault finding.
The primary dosing pumps which are pneumatically driven, dose a set constant amount of oil, this aids in the ability to keep consistently dosing oil but is regulated on time.
Time is defined from the ultra-sonic flowmeter in place on the water inlet.
Each production line will have a water supply incorporating its own flowmeter. Monitoring water flow allows for dosing to automatically dose faster or slower relevant to the rate of flow.
This feature takes the responsibility away from the operator to change the dosing value if changes are made on the shear platform regulator unit. Graphoidal Multi Shear Spray Units can be tailored for a single production line up to currently six production lines. Graphoidal systems can be integrated with a Graphoidal Autofill system with ease. The automatic fill unit works off level sensors in the tanks within the cabinets to provide a clean refill system preventing contamination into the hydraulic system. Graphoidal understands its systems are critical in a 24hour production line process; therefore, automation integration is vital to reduce operator interaction.
Graphoidal - Your partner for providing innovative, economical, efficient, and forward-thinking solutions that give you the crucial competitive advantages you need. �
*Technical Sales Engineer Graphoidal Development Limited, Chesterfield, UK
KEEP SMILING THE WORLD NEEDS BEAUTIFUL THINGS
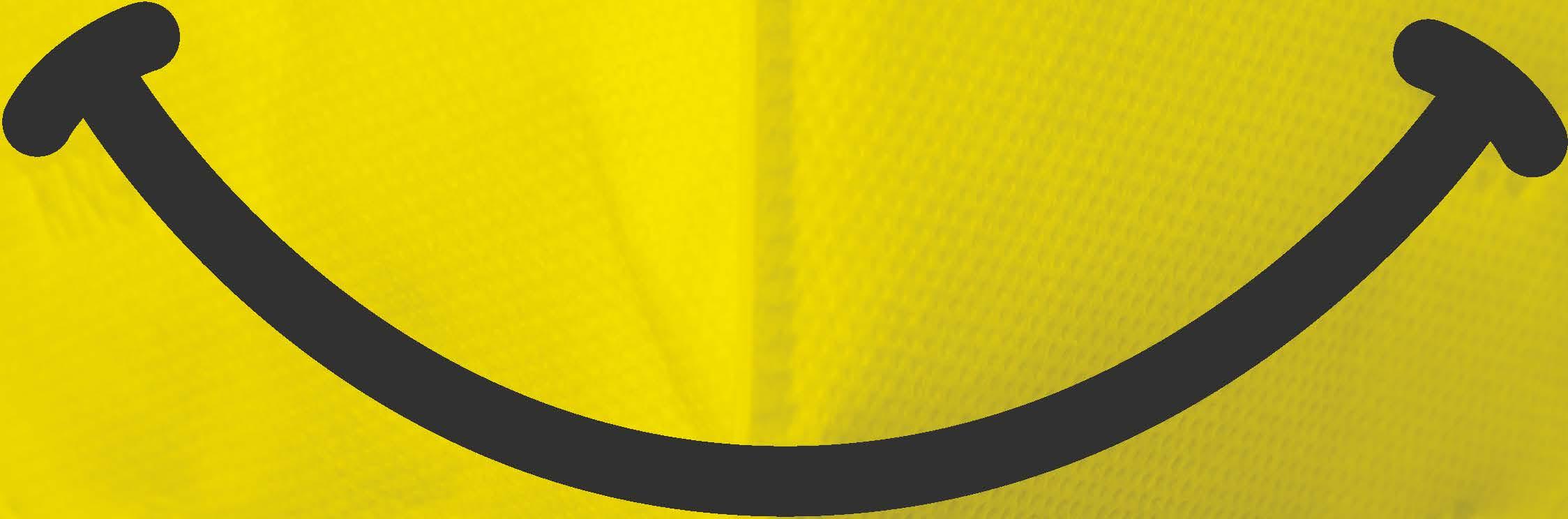
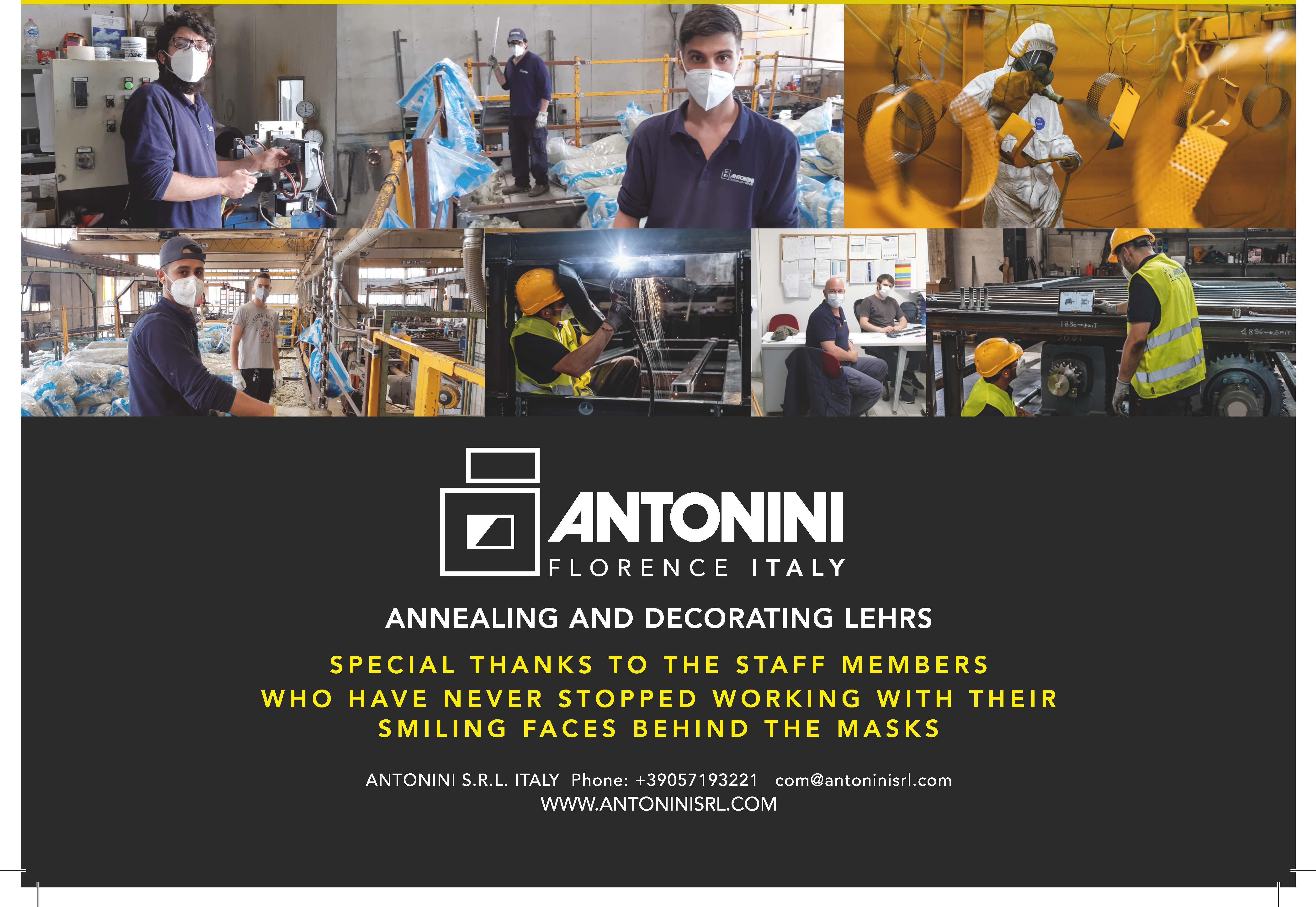
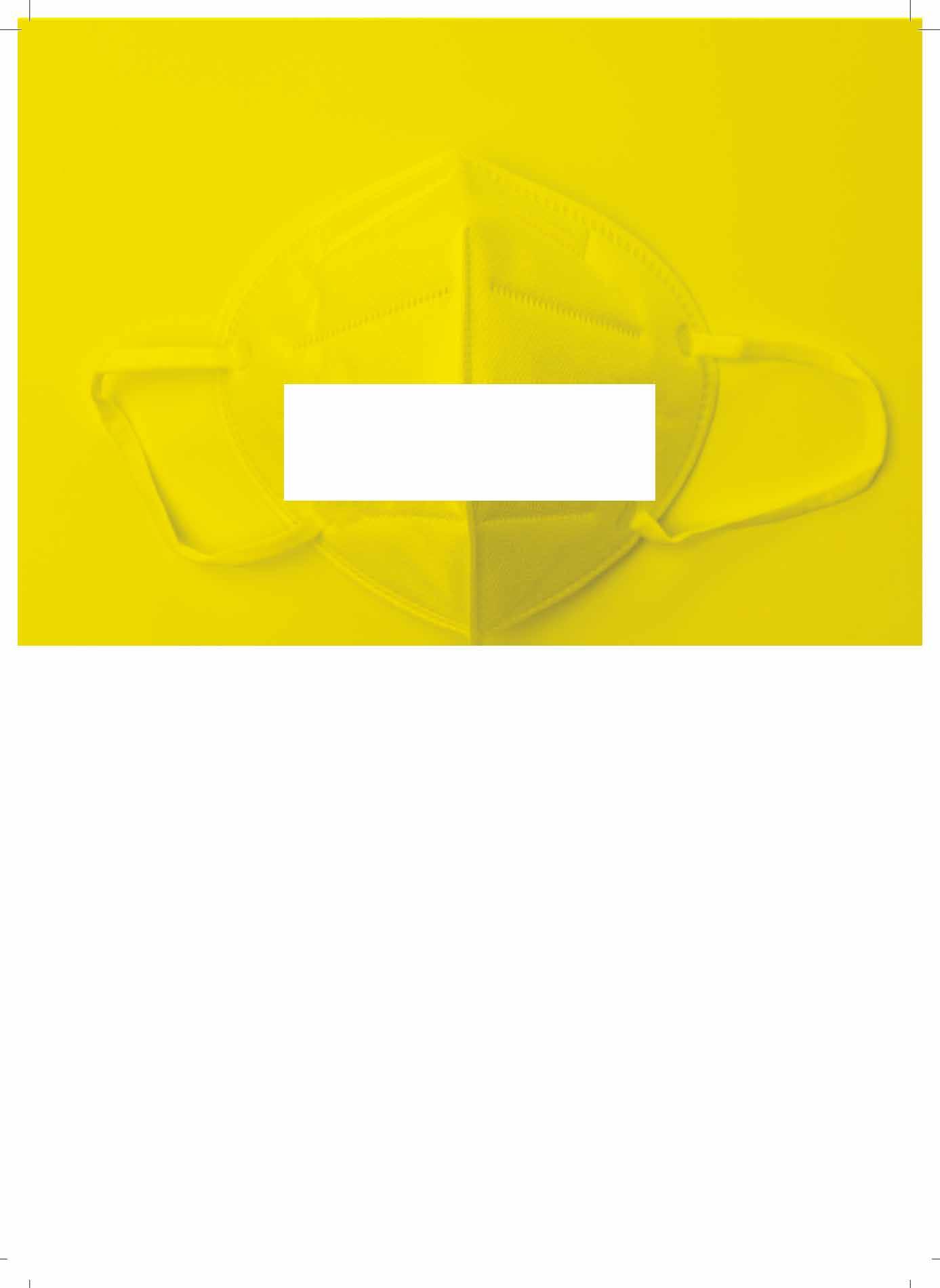