
4 minute read
New feedstocks, new adsorbents
New biofuel feedstocks, new adsorbents
Photo: Adobe Stock
Increasing biofuel regulations are forcing producers to turn to alternative feedstocks, which pose major puri cation challenges. Now, next-generation adsorbents aim to help producers overcome these challenges, maximising throughput and yields Carlos Rodriguez, Vinicius Ribeiro Celinski
Feedstock
Secondgenerati on feedstocks
Advanced feedstocks UCO/RUCO
Animal fat (category I & II) POME
Extracted oil from bleaching earth
Availability 2020-2030
Moderate to good Moderate
Moderate
Low
Algae Low
Main quality challenges
Alkaline metals, metals, oil stability, polymers N-content, metal content, acidity
Acidity, alkaline metals, metals, P-compounds Purest feedstock (already treated), some heavy metals from previous purifi cati on Metals, polymers
UCO = used cooking oil, RUCO = repurposed cooking oil, POME = palm oil mill effl uent
Figure 1: Availability and quality challenges of new biofuel feedstock variants
Source: Clariant With the EU’s revised Renewable Energy Directi ve (RED II) adopted for the 20212030 period, biofuel producers – hoping to meet stringent new requirements – are facing two main feedstock challenges: availability and quality (see Figure 1, below).
New feedstock variants, in limited supply and with a diverse range of impuriti es, greatly impact fi lterability during pre-treatment, and consequently, producti on yields and profi ts.
Overcoming these problems requires novel adsorbents and innovati ve technical strategies that can facilitate high throughput purifi cati on.
Pre-treatment of feedstocks
In a feedstock market that is stretched to its limits, quality and availability are in direct relati onship. Insuffi cient choice and supply of feedstock have forced producers to use lower qualiti es than their facility designs allow, adding considerable stress to their units.
The ability to “tame” diffi cult-to-treat feedstocks would give producers a strong competi ti ve advantage.
In the case of fatt y acid methyl esters (FAME) or hydrotreated vegetable oils (HVO), the feedstocks’ regulatory compliant specifi cati ons mean that the process remains stable. However, problems are found further upstream, in the pre-treatment unit. With such alternati ve feedstocks, there should be a fresh focus on two important steps: adsorpti on and fi ltrati on (see Figure 2, following page).
An adsorbent is required to reduce many undesirable substances that cannot be removed in the degumming steps.
Compared to vegetable oils, alternati ve feedstocks can contain higher levels of diff erent types of contaminants, such as phosphorous compounds, that can greatly aff ect effi ciency as well as the adsorpti on step (see Figure 3, following page).
Fresh focus on fi ltration
Aside from the batch reactor, the fi lter is one of the most important secti ons of a pre-treatment unit.
Conventi onally, horizontal leaf fi lters (Niagara type) were used with screens that had larger pores than modern designs in order to allow maximum fl owthrough during fi ltrati on.
Since a fi lter cake is formed with the adsorbent, its quality and development are criti cal. A stable and, especially, homogenous fi ltrati on ensures that contaminant removal is spread across the enti re fi lter cake and leads to more effi cient use of the adsorbent.
Assuming a parallel channel through u
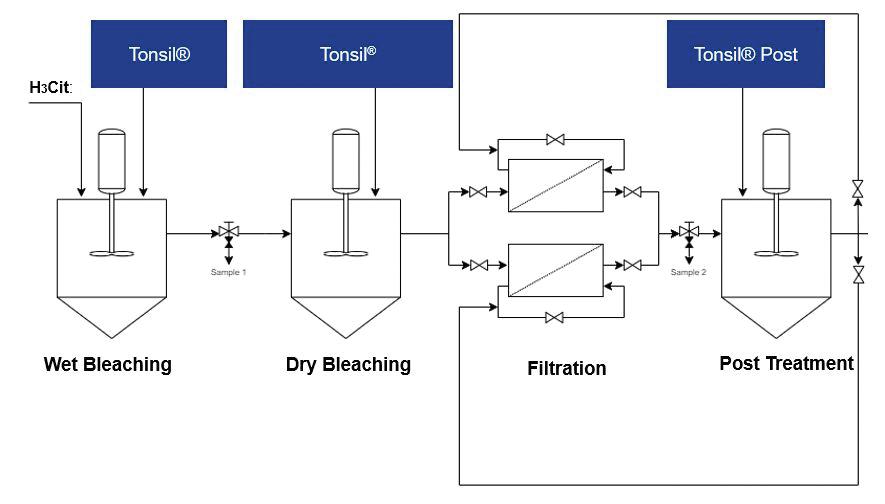
Figure 2: Pre-treatment of alternative feedstocks
u
Source: Clariant
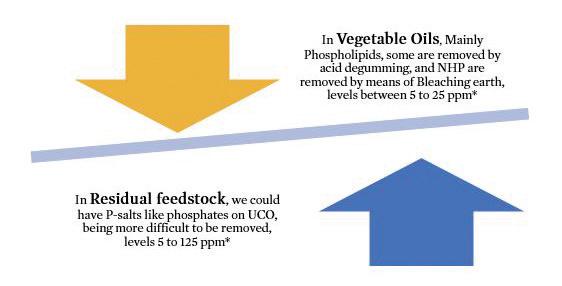
Figure 3: Contaminant content and removal of alternative feedstocks vs vegetable oils
Source: Clariant
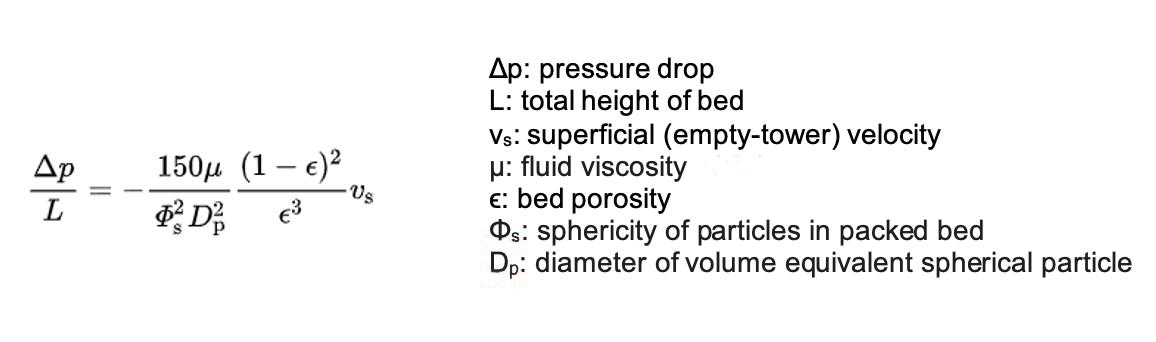
Figure 4: Evaluating filtration efficiency based on the Kozeny-Carman equation
Source: Clariant
Feedstock Clariant adsorbent
Palm oil mill effluent (POME)
Animal fat Tonsil 919X series
Tonsil 719X series
Tonsil 919X series
Filtration time of first pass (seconds)
93
65
440
Total metal * (mg/kg)
< 5 the filter cake, filtration efficiency is ideally defined by the Kozeny-Carman equation (see Figure 4, below left). The material inside the cake should improve porosity (µ).
Next-generation adsorbents
Due to the factors mentioned earlier, adsorbents must not only offer improved removal of a great variety of contaminants, but also enhanced filtration efficiency.
These qualities can be found in nextgeneration adsorbents, such as Clariant’s Tonsil 919X FF and its newly launched Tonsil 719X FF series, entering the market this year.
The highly activated, selective adsorbents considerably facilitate pretreatment of alternative feedstocks and help overcome filtration challenges caused by feedstock viscosity (µ) and contaminants featuring high molecular weights.
Another factor affecting the pretreatment unit’s throughput is adsorbent dosing. As alternative feedstocks have a complex contaminant profile at higher levels that are more difficult to remove than vegetable oils, adsorbent dosing usually needs to be significantly increased by 30-80% or higher.
A highly activated and selective adsorbent not only helps to reduce adsorbent dosage, but also to increase plant throughput and to minimise oil retention in the cake.
These aspects are critical to the total cost of ownership (TOC) in the adsorption process, and, thereby, the overall production costs.
Advantages for biofuel producers
Considering the total cost of ownership, next-generation adsorbents can make the difference between not being able to filter at all and having favourable throughput.
Latest lab test results have demonstrated approximately 35% shorter filtration times (first pass) with new generation adsorbents compared with with past generations (see Figure 5, left).
This is a major competitive advantage for biofuel producers, not only because it can significantly broaden the scope of feedstocks they can operate with, but also because it ensures high throughput production and minimises oil retention in the spent adsorbent. ●
Tonsil 719X series 287
*earth-, alkaline, Si, P, Fe, Al
Source: Clariant Carlos Rodriguez is the head of technical sales, and a product manager at Clariant AG, Switzerland. Vinicius Ribeiro Celinski is an application development manager at Clariant