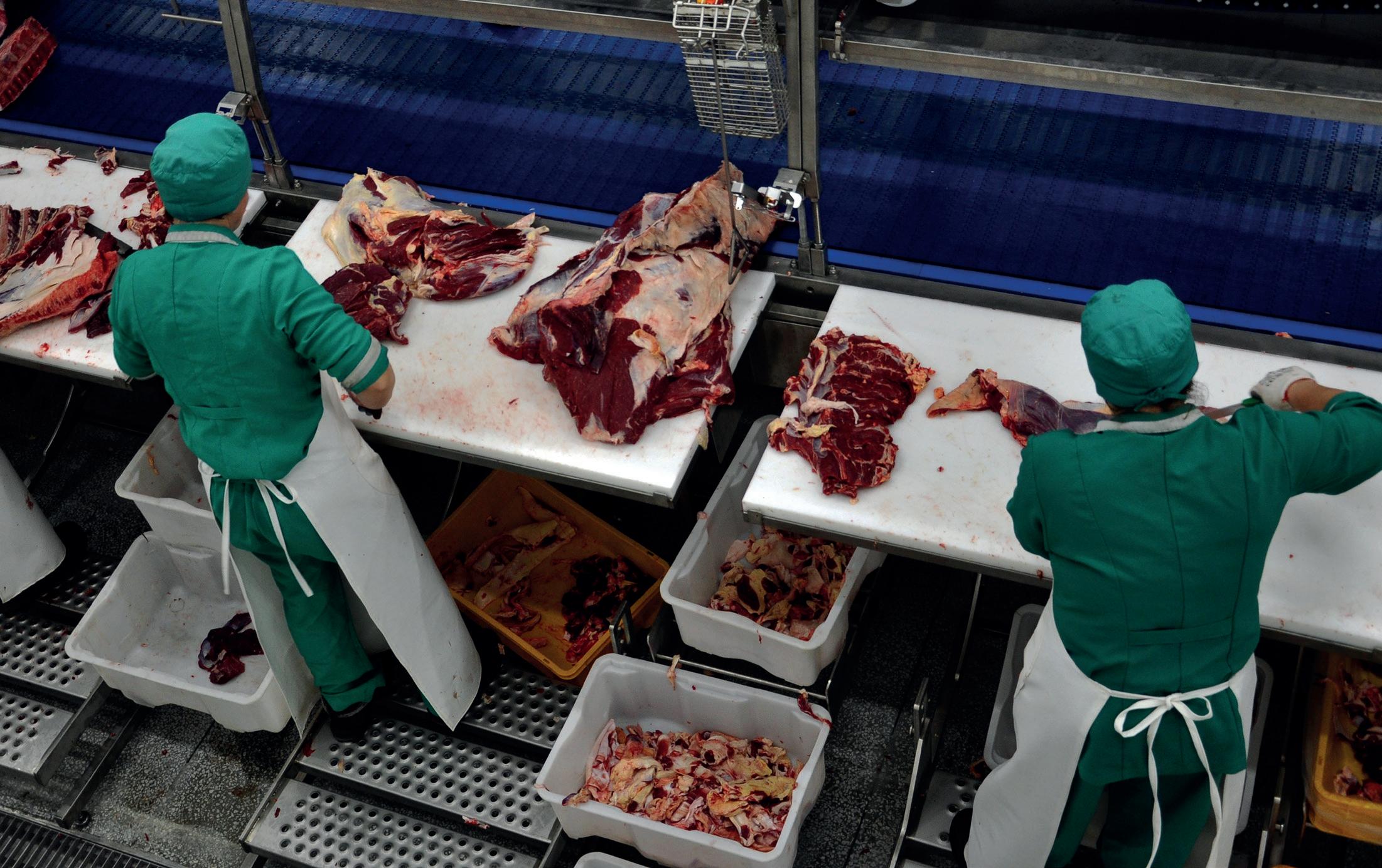
5 minute read
Pressing matters
Diverse raw materials from different meat industries are just one of the external factors renderers have to deal with during processing
Suppliers of rendering equipment are focusing on energy efficient plants which meet current safety standards, while yielding the highest amount of raw materials, with the screw press being a central element in the rendering process Lennard Münch
The rendering industry has recovered from the bovine spongiform encephalopathy (BSE) or so-called mad cow disease crisis of the 1980s and 1990s, in which the main affected nation – the UK – had to slaughter four million head of cattle to contain the outbreak.
During the crisis, 177 people died in the UK after contracting the human equivalent of the brain disease – Creutzfeldt–Jakob disease (vCJD) – and British beef was banned from export to numerous countries around the world, with some bans remaining in place until as late as 2019.
The BSE crisis led to new regulations including the removal of specified risk material from the food supply chain and the separation of fallen stock and animal by-products into different risk categories.
Since then, stricter regulations have challenged the rendering industry to adapt its processes.
From today’s perspective, it is even more important to operate an energy efficient plant which meets safety standards but also yields the highest amount of raw materials.
Suppliers of rendering equipment have focused on how to arrange the best setups of conventional machinery and their reliability. A second step in this ongoing development is the automation of plants and how to steer them towards greater energy efficiency.
There is no perfect process or automisation system because external factors such as constantly changing raw material, temperatures and handling issues are so diverse. Therefore, constant monitoring and correct planning of service intervals are very important.
Yields increase when servicing is scheduled regularly, according to press and spare parts manufacturers and service providers Rosedowns and Serptec, part of the Desmet Ballestra group.
Focus on screw press
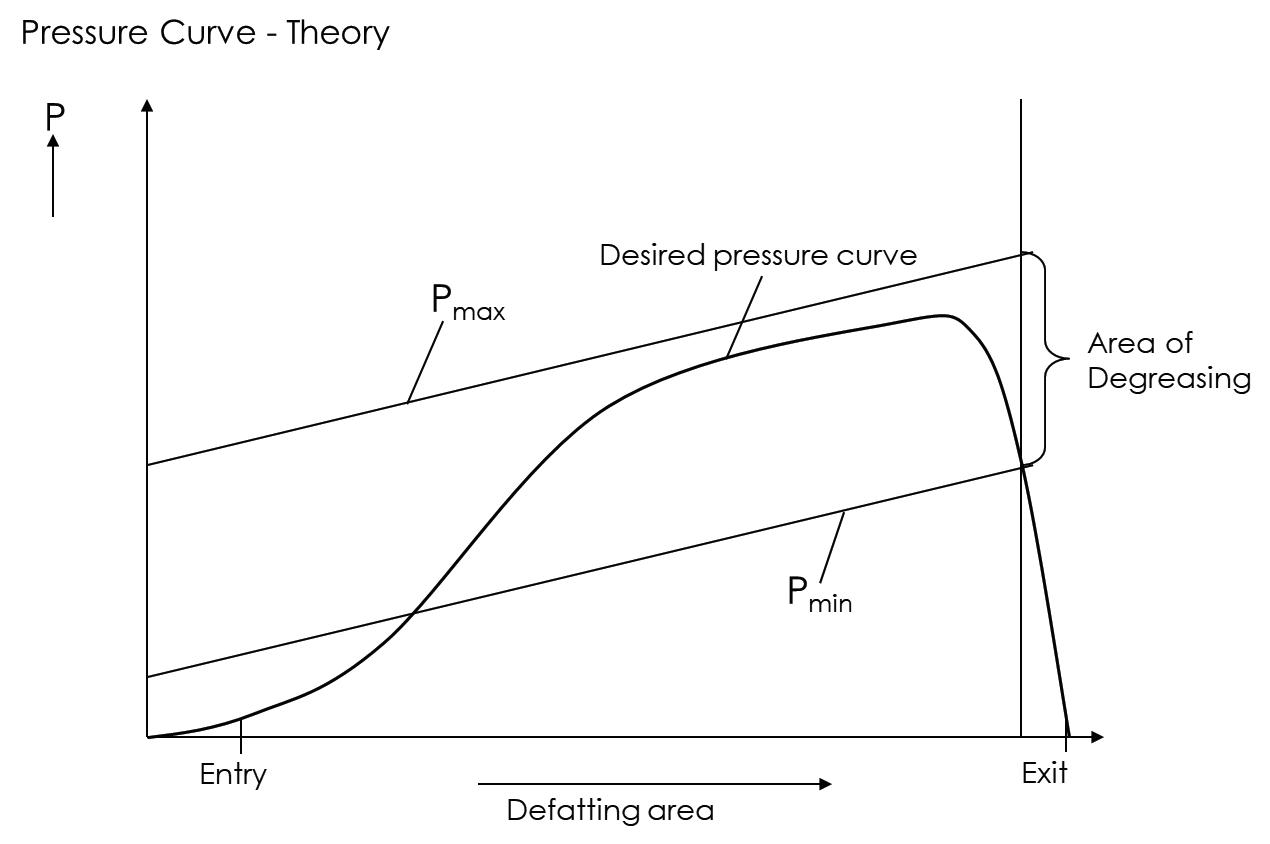
Figure 1: Pressure curve theory
Source: Serptec GmbH
u semi-finished product and separates it into solids and fats.
Crucial factors such as the mix of material (bone/soft parts), temperature and moisture have to be adjusted to receive a good separation with a high yield of oil.
Currently, there are two main pressing methods which are widely used in the rendering industry.
The first method uses a relatively short screw-cage configuration using a choke at the end of the press. Material is conveyed through the press with a small intensity of volume decrease in a relatively short strainer cage. A choke at the end regulates the back force so that material is compressed inside the strainer cage.
Due to the increase in counter pressure, separation of fat takes place and free oil flows out of the strainer cage. The solids exit on the sides of the choke, staying mainly inside until the outlet of the strainer cage.
This method is easy to control but does not give optimal results and consumes more energy. The process usually requires a fresher bone/soft material mix. Otherwise, pressing is mostly inefficient, with high residuals of oil content in the cake.
The second method uses a screw press with a relatively long screw-cage configuration without a choke. It has a higher intensity of volume decrease inside the strainer basket. The press geometry compresses the cake either with a constant increase of pressure or with special pressure elements which separate the material in different compression zones inside the strainer basket.
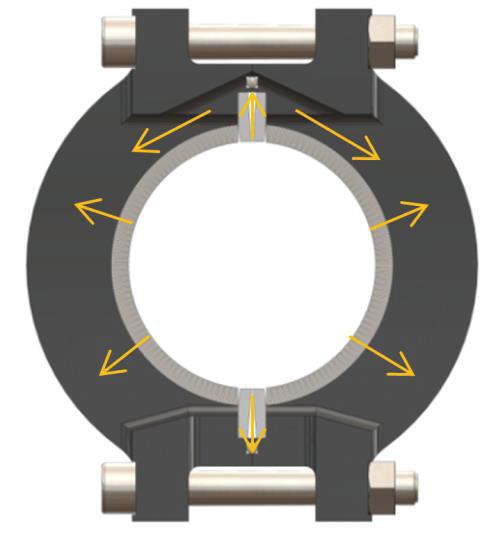
The Rosedowns SR4.000 rendering screw press has a new strainer cage which provides greater opportunities to recover oil from rendered material
The outcome is usually a better defatting value than with screw presses with a choke. The retention time inside the strainer cage is longer so the oil has more time to drain. But the operation, especially on start-up, must be monitored more carefully.
A ‘multivalent compression’ approach is, in theory, the most effective pressing method as it combines both radial and axial compression intensity levels (see Figure 1, above).
The volume decreasing curve is very steady if the compression levels are coordinated, allowing for oil yield out of the capillary structure of the material. This achieves a better oil flow.
In addition, this pressing method is more energy efficient due to the effectiveness of the compression method. Material with a low structure level can be forwarded into the press and the multivalent compression transforms it into a cake so that the separation process can start immediately and oil can flow off more quickly through the strainer cage.
Conventional screw geometries only use radial compression on each part, while axial compression varies only from part to part.
Conventional pressing also takes longer and another disadvantage is that when conventional parts wear out, the oil in cake level will rise. Combining radial and axial compression addresses these issues, maintaining efficient pressing for a longer time period.
Another problem with conventional pressing is free oil being separated from the solids while compressed inside the strainer cage.
In several trials, Rosedowns Serptec observed that not all of the separated oil will flow through the drainage of the strainer cage. Instead, it flows inside along the strainer cage and is absorbed from the cake as soon as the pressure level drops, usually when the cake leaves the strainer cage. Measured results have shown that up to 3% of residual oil content could be reclaimed.
The Rosedowns SR4.000 rendering screw press addresses some of the issues of conventional presses. The main development lies in the strainer cage.
The diameter and length of the cage have been optimised, taking into account the drawbacks of conventional pressing, and a 360° drainage zone provides the maximum opportunity to recover some of the 3% residual oil content in the cake.
The screw press’ clamping bars are CNC manufactured, providing an additional screening area. This provides new drainage possibilities by opening the upper and lower sides where free oil usually collects without a chance to drain.
The screw press is one example of suppliers developing new, more efficient machinery for the rendering industry. An automisation process which can adapt to constantly changing materials in rendering production is still to be developed, although Rosedowns Serptec has filed a patent for a new type of technology in this area.
Trials will start within the next few years, continuing the process to develop a complete process which will adapt to diverse materials and other external factors. ● Lennard Münch is the managing director of Serptec GmbH, which became part of the Desmet Ballestra group in 2020