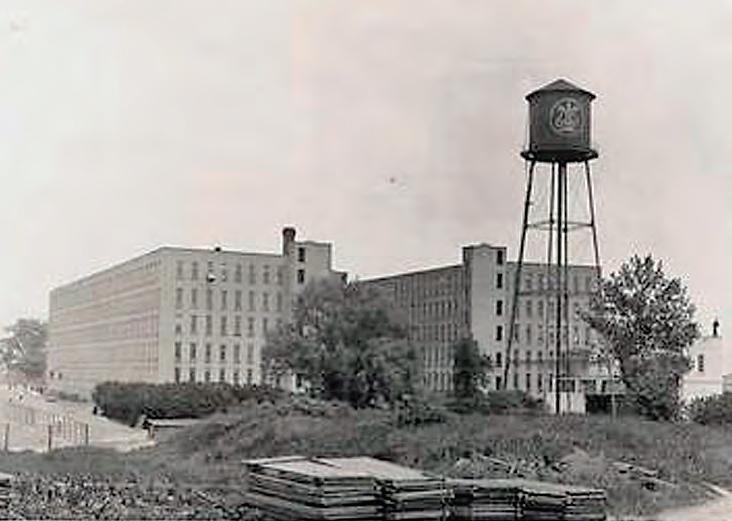
6 minute read
The making of a Steinway
The music and magic of a Steinway
Virtual tour shows how the best pianos in the world are crafted in Astoria
by Michael Gannon Senior News Editor
Since Covid stopped all visitors to Steinway & Sons, the company has been forced to postpone tours of the historic factory in Astoria.
But if you still want a bit of an inside look at the magic that crafts some of the world’s finest pianos, a 42-minute virtual tour on the company’s website lets you see the process virtually from start to finish without the bustle of the factory floor or the smell of fresh sawdust, lacquer and wood finishes — if, of course, you consider missing those to be good things.
Just go to the company’s website at steinway.com/misc/virtual-factory-tour and prepare to be amazed.
“There are more than 12,000 parts in a Steinway grand piano,” says Michael Cabe, director of customer experience at Steinway, who guides viewers through the processes from selecting just the right pieces of wood to packaging and protecting the pianos to head out the back door of the factory.
The tour starts in a massive room where the inner and outer rims are glued together from a total of 17 layers of wood — ebony for the outside and hard rock maple for the inner rim.
Then both are glued together using a machine and a process patented by Steinway in 1878. Now it is time to take the inner-outer rim, well over 10 feet long, and bend it in one piece to create the distinct shape of a Steinway grand piano.
In a factory that has embraced innovation and technology as readily as anyone, the most important tools in many parts of the process are the hands, eyes and unerring judgment of expert craftsmen.
Rim-bending is one of those procedures. The wood is placed around a form of the desired shape and secured in place with a series of hand-operated clamps and pulleys. Some pneumatic tools are used so that a certain and specific pressure is applied in specific places.
Finishing touches are applied not by machine but by craftsmen using hammers and awls.
“I think this is the foundation of what makes a Steinway piano a Steinway piano,” Cabe tells viewers. “This is where it takes its shape, where you see the beautiful wood come together and we see that elegant grand piano come to life.” The first Steinway to build a piano was Heinrich Steinweg, born in Germany in 1797. He went into business in 1829, but in 1850 lived his dream of coming to America for all it offered.
He and his sons worked for other manufacturers for three years before striking out on their own in Manhattan under the more Anglicized name of Steinway. They expanded to Astoria in 1871 and built a factory on the present site in 1873. The Steinway section of Astoria was practically a company town with housing, stores and schools for the workers and their families.
The rim sits in the press for 24 hours until the wood has taken the semi-horseshoe shape and is brought to the veneer and finishing room.
Here, sheets of wood veneer sit on racks all along the walls, enabling workers to search for perfect matches of shade and grain for a perfect appearance.
It will be brought to the climatecontrolled conditioning room to fix, among other things, the moisture that the wood had picked up in the veneer process. It will be dated and numbered in chalk, and could sit for two months or more.
Before it moves on to the casemaking department the wood is sanded to exact tolerances by computerized machine tools operating side-by-side with a woodworker making other adjustments employing the milenia-old technology of a mallet and chisel.
“This is where it starts to feel like a piano,” Cabe observes. “Traditional, woodworking furnituretype craftsmanship. It’s hard to find anywhere in the world this skill level.”
The only metals involved are the hand-adjusted clamps used to hold the pieces of wood together until they are joined as one.
“No screws, no steel fasteners,” Cabe says. “It’s all wood with wooden dowels so there are no issues with squeaks in the joints.”
The next part added is the soundboard, which will sit inside on the inner rim, with the metal plate and cords sitting above it. Sitka spruce has the flexibility and durability to reflect the sound as desired. Slats of the wood are laminated into one sheet that will be cut to fit.
“No knots, no imperfections,” Cabe says examining a slat of wood from a large cart. “There’s a little bend in the grains of this piece. This is not good enough to go into the soundboard of a Steinway piano, so it ends up here — the scrap bin.” The slat is dropped back in the cart.
Sitting just over the soundboard will be a metal plate that will support the strings made of steel wrapped with copper wire. The metal when necessary is ground to within a fraction of a fraction of an inch with hand power tools.
Strings are hand-strung through small metal pins hammered with precision to the proper place and depth into the wood.
The actions and hammers are the intricate, elaborate assemblage of moving parts that cause the felttipped hammer to strike the string when a key is played.
A clip near the end of the video shows a technician placing small metal weights on a key to make sure it requires just the right amount of pressure from a player’s or performer’s fingertip to strike the note, no more and no less.
An outer coating, “Satin matte and new gloss finish,” is applied by
Piano Makers experts wearing hazmat suits. And again precision is vital.
“You have a large surface area,” Cabe explains. “You’ll see any imperfection.”
Next a robot named Polly for a member of the Steinway family takes care of — you guessed it — polishing the nearly finished product.
With construction coming to an end, there is still the sound and tone to take care of. Each instrument, according to the video, will be tuned at least five times between receiving its strings and heading out to the back door loading dock.
In days of old, the hammers were checked by a technician who knew by ear if the note was somewhat off, and who stuck the felt enclosing the hammer with a small needle until it was just right.
In Astoria, they still are checked by hand and ear. Every key. Every piano.
“That piano has now found its voice,” Cabe says.
In preparation for shipping, pieces of cloth are placed between wood surfaces that come into contact with each other to avoid damage.
The pianos can even be packed in large, sealed plastic wrapping to avoid problems that could come with sending a piano from Astoria in winter to a tropical location.
All the work, Cabe says, is done with one goal in mind.
“Make sure today’s Steinway is the best Steinway ever made.”

While Steinway & Sons has robots and computers doing fine-touch work at its Astoria factory, hammers and chisels — and the hands, eyes and judgment of gifted craftsmen — still remain as essential to creating a Steinway grand piano as they were in this photo from 1908. LGCC WAGNER ARCHIVES PHOTO / FILE