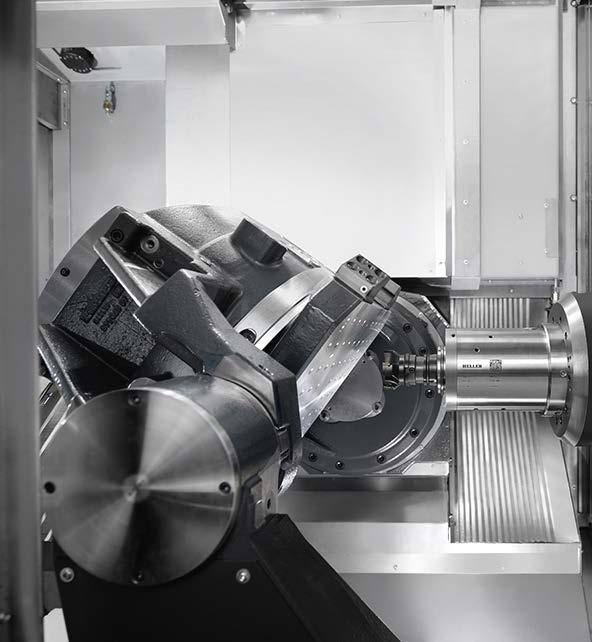
37 minute read
Obiettivo massima efficienza
Tavola rotobasculante supportata da controcuscinetto x lavorazione a 5 assi in simultanea (foto HELLER).
LE EVOLUZIONI TECNOLOGICHE ALLA BASE DI QUESTA LAVORAZIONE RISPONDONO ALLA RICHIESTA DEL MERCATO DI
LAVORAZIONI SEMPRE PIÙ COMPLESSE IN TERMINI DI DIMENSIONI
E MATERIALI CON L’OBIETTIVO DI MASSIMIZZARE L’EFFICIENZA E LA MULTIFUNZIONALITÀ DELLE MACCHINE. Di Patrizia Ricci
Come ben noto, la fresatura meccanica è una lavorazione per asportazione di truciolo con cui ottenere una vasta gamma di superfici mediante il moto rotatorio di un utensile a più taglienti con lavorazioni che vanno dalla sgrossatura alla finitura. La realizzazione di superfici complesse è direttamente collegata alla fresatrice, una macchina che negli anni si è evoluta riuscendo a rispondere con soluzioni innovative alle esigenze sempre più pressanti da parte del mercato in merito alla qualità e alla forma delle superfici con applicazioni in diversi settori, dalla costruzione stampi al settore aeronautico, dal medicale all’automotive fino alla meccanica generale. Questa tipologia di macchina utensile è in grado di lavorare pezzi di dimensioni diverse, dalle più piccole a quelle di grandi dimensioni e anche tipologie di materiali diversi, dai più tradizionali a quelli alternativi o di difficile lavorabilità. Negli ultimi anni, a fianco a lavorazioni di fresatura standard, il mercato ha richiesto sempre di più lavorazioni complesse, sia per i tipi di materiali lavorati sia per le caratteristiche degli utensili, che per le richieste di performance. Questo comporta impianti sempre più sofisticati, con la conseguenza che è sempre più difficile parlare di impianti generali che possono risolvere qualsiasi problematica. L’innovazione più grande sta proprio nell’incremento di specificità che gli impianti di fresatura devono avere con macchine sempre più performanti. Questo è possibile anche grazie alla partnership con i produttori di controlli numerici, CAM e utensili, passando poi per soluzioni studiate per aumentare la precisione nel tempo o per limitare il tempo di attrezzaggio, oppure accessori e configurazioni dedicate a settori quali l’aeronautico e dello stampo. Un’altra parola chiave in tema di innovazione è la multifunzionalità. Le tendenza è andare verso fresatrici (ma anche alesatrici e torni) dotate di dispositivi e accessori che permettono all’utente la multifunzionalità con l’obiettivo della lavorazione di pezzi complessi in un unico piazzamento, quando prima venivano lavorati su più macchine e con più piazzamenti. La multifunzionalità nelle fresatrici (e alesatrici) viene garantita da un’ampia gamma di accessori tra cui teste automatiche di fresatura, mandrini estraibili modulari, unità rototraslanti eccetera e da un’elevata automazione, il tutto supportato da dispositivi ausiliari all’operatore che così viene sgravato da interventi diretti sulla macchina. Anche efficienza, un termine forse scontato, è un’altra parola chiave. Per chi produce con una macchina utensile, scontrarsi con chi offre un prezzo minore, significa aumento di competitività, con conseguente aumento d’efficienza, e abbattimento dei costi orari. Lo sviluppo tecnologico deve prevedere tutte e due queste variabili per generare un solido successo dei propri clienti. Per rispondere a queste esigenze, vediamo con alcuni tra i principali produttori, importatori e rappresentanti di questa tipologia di macchina utensile, le sue evoluzioni tecnologiche.
SOLUZIONI DALLE AZIENDE
La fresa SSN11 è disponibile in diametri da 32 – 125mm, con dimensioni intermedie per applicazione su stampi.
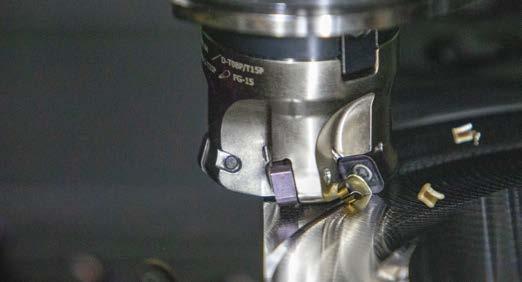
DORMER PRAMET FRESATURA PIÙ PROFONDA
Dormer Pramet ha esteso la sua gamma di frese per stampisti e meccanica generale con numerosi nuovi prodotti. Sono compresi i nuovi inserti bilaterali SNGX11 per lavorazioni ad alto avanzamento con profondità di taglio fino a 1.7mm. Un tagliente principale robusto assicura elevati livelli di durata e sicurezza di processo – specialmente nella lavorazione di angoli all’interno di una tasca. L’inserto quadro SNGX11 con i suoi otto taglienti rappresenta anche una soluzione estremamente vantaggiosa. Adatto per fresatura di copiatura, interpolazione elicoidale, lavorazione in rampa, tuffo progressivo e spianatura, SNGX11 è disponibile in due geometrie. M è per la lavorazione di acciaio, ma anche acciaio trattato e ghisa. MM dà un taglio più dolce ed è più indicata per acciaio inossidabile, acciaio pastoso e super leghe. La gamma è integrata dalla nuova fresa SSN11, disponibile in diametri da 32 – 125mm, con misure intermedie per applicazioni su stampi. Tutte le frese hanno la possibilità di far passare il refrigerante dall’interno per aumentare la sicurezza di lavorazione e possono essere montate con sbalzi fino a 10xD per permettere lavorazioni in profondità. Dormer Pramet ha anche aggiunto al programma di fresatura ADMX07 una nuova geometria F per applicazioni di finitura e semifinitura. Questo prodotto affianca le esistenti geometrie M, FA ed HF ed è indicato per lavorazioni leggere di acciaio inossidabile e acciaio con basso tenore di carbonio. Molto adatto anche per applicazioni su macchine sensibili alle vibrazioni, il rompitruciolo presenta una geometria altamente positiva con un ridotto piano periferico. Si riducono in tal modo le vibrazioni e si permette un’azione di taglio dolce senza bave anche sullo spallamento retto. È significativa anche la riduzione delle forze di taglio che, non solo riduce il consumo di energia, ma previene l’indurimento del materiale con conseguente aumento della durata dei taglienti. La gamma ADMX costituisce un utensile universale per spallamento a 90° adatto ad una grande varietà di applicazioni di fresatura. La gamma Multiside di Dormer Pramet è perfetta per le applicazioni di fresatura nella gamma dei materiali esotici, incluso titanio e leghe resistenti alle alte temperature. La gamma è costituita da tre specifiche frese: Multiside AD, Multiside SC e Multiside SD – il programma copre una grande varietà di operazioni: spallamento retto, fresatura di cave, copiatura, spianatura, tuffo progressivo e sgrossatura. Un fattore chiave della gamma Multiside, che è parte integrante della gamma di fresatura Pramet, è il suo sistema di bloccaggio brevettato SideLok. È questo un modo estremamente efficiente e sicuro di bloccare gli inserti che garantisce un elevato livello di stabilità, specialmente nella lavorazione di superfici complesse su macchine a cinque assi. Il risultato è un aumento del volume truciolo – anche in caso di materiali difficili da lavorare. Non essendoci la necessità del fissaggio centrale, l’inserto risulta molto più robusto, mentre il suo posizionamento nella sede garantisce una maggiore superficie in presa. Un altro benefit del sistema SideLok è che non c’è bisogno di rimuovere la vite dal corpo quando si sostituisce il tagliente, il processo risulta quindi velocizzato.
FAGOR AUTOMATION NON SOLO CNC: UNA GAMMA COMPLETA PER EQUIPAGGIARE LA MACCHINA UTENSILE
La gamma prodotti di Fagor Automation comprende CNC, azionamenti, motori, sistemi di misura lineari e rotativi sia assoluti sia incrementali, ideali per applicazioni di fresatura, tornitura e taglio laser. Nella fresatura, la serie “M” offre prestazioni di livello top, grazie ad una serie di caratteristiche che differenziano questo CNC rispetto ai competitors di mercato: prestazioni utilizzabili in modo semplice e intuitivo, sia per la programmazione pezzo, che per la gestione della macchina, grazie ad una dotazione software davvero completa. Grafica 3D con rendering solido, monitor multitouch 15” nella classica architettura compatta, oppure con architettura modulare, ovvero con PanelPC dotato di CPU dual/quad-core e schermo da 19 o 21”; la tastiera è disponibile sia a membrana (per applicazioni in ambienti gravosi), sia con tasti meccanici (per un gradevole comfort di digitazione). La serie “M” offre diversi linguaggi di programmazione pezzo: dal potente linguaggio ProGTL3 che consente di risolvere qualsiasi profilo senza utilizzo di sistemi CAD mediante le sole 5 funzioni base G810, G811,G813, G820 e G821, completata dalla visualizzazione grafica interattiva durante la programmazione, la simulazione in real-time con grafica 3D e le funzionalità per la fresatura di superfici, come la creazione di solidi definiti da un profilo piano e uno o più profili sezione (G8736), oppure la creazione di superfici rigate o solidi ottenuti da rototraslazione nello spazio mediante G8725, insieme a molte altre funzioni per solidi 3D. Per i particolari più semplici o ripetitivi, la programmazione può essere invece di tipo conversazionale; l’operatore può creare programmi a bordo macchina in modo rapido e intuitivo (il tempo medio di creazione di un ciclo è inferiore a un paio di minuti), senza conoscenze di programmazione e in pochi passaggi, grazie a maschere di input dati, suddivise in funzione del tipo di profilo/superficie/tecnologia desiderate (cave, punzoni, cicli fissi, lavorazioni su griglie, etc.). Sebbene disponibili in tutte le varianti di CNC (M/T/L), è nel modello M che trovano la loro applicazione più appropriata alcune prestazioni estreme quali ad esempio HSSA (High Speed Surface Accuracy), ovvero il modo in cui Fagor gestisce l’alta velocità: movimenti rapidi, ma sempre con il controllo dell’accuratezza di lavorazione. A complemento, l’esclusiva prestazione DYNOVR, ovvero un cursore con cui cambiare online la “fluidità” del movimento, in modo da ottenere un’elevata finitura superficiale pur mantenendo la velocità programmata; utile, per esempio, per ridurre le vibrazioni quando si fresano pezzi molto pesanti e materiali duri agendo sulla dinamica della macchina (accelerazione, jerk e altri parametri) in modo fluido, continuo e dinamico in-process, senza cambiare il programma, ma semplicemente “muovendo un cursore”. Pack Mold è la proposta di Fagor per garantire risultati di assoluto livello nella lavorazione degli stampi. Si tratta di un’opzione del CNC che aggiunge una intera suite di novità, come FMC, DMC e FCAS (anticollisione) alle già elevate prestazioni del modello M per la fresatura di meccanica generale. FMC (Fagor Machining Calculator) è la nuova calcolatrice tecnologica che comprende un database di materiali e lavorazioni integrato nel CNC, ma anche espandibile dal cliente. Dopo avere scelto un materiale e una lavorazione (sgrossatura, finitura, etc.), il CNC calcola i parametri di lavorazione per assicurare le migliori condizioni di taglio. Durante la fresatura, occorre poi assicurare che l’utensile rispetti queste condizioni; per questo è nato DMC (Dynamic Machining Control), che regola l’avanzamento per mantenere la potenza di taglio ottimale del mandrino. In particolare in sgrossatura fornisce un notevole risparmio di tempo, ottimizzando il movimento della macchina e l’impiego dell’utensile. Grazie al suo algoritmo di auto-apprendimento, sono sufficienti alcuni secondi di lavorazione, dopodiché il DMC funzionerà in modo autonomo. Infine, nel caso di macchine o lavorazioni importanti, FCAS (Fagor Collision Avoidance System) consente di descrivere i volumi della macchina che possono urtare tra loro, evitando le collisioni dovute a errori di programmazione o movimenti manuali incauti. È possibile sia simulare il programma offline (a bordo CNC) per scoprire in anticipo se ci saranno collisioni, ma anche attivare la sorveglianza real-time, attiva in qualsiasi condizione e stato del CNC, in automatico, come nei movimenti manuali in jog.
Macchina combinata
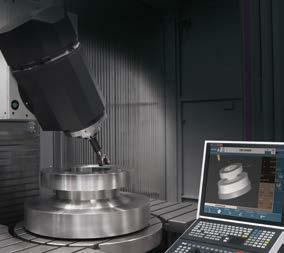
FANUC ROBODRILL, PRESTAZIONI ECCELLENTI IN QUALITÀ E PRECISIONE
Fanuc Robodrill
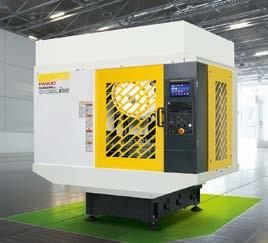
FANUC è l’unica azienda nel suo settore che produce internamente tutti i componenti principali e che sviluppa soluzioni in tre famiglie di prodotto chiave: sistemi CNC, robot e macchine utensili intelligenti. Questo significa che tutti i prodotti FANUC condividono una medesima piattaforma di controllo e servocomando, fornendo una connettività semplificata e rendendo davvero semplici gli scenari di automazione completa. Inoltre, la condivisione di parti comuni per realizzare i prodotti si traduce in una migliore efficienza nella gestione delle parti di ricambio. Sono i vantaggi dell’approccio ONE FANUC: un unico referente che possiede tutto il know-how tecnologico e l’affidabilità a 360 gradi per consentire alle aziende di concentrarsi unicamente sul proprio core-business. Protagonista delle lavorazioni di fresatura in alta velocità da oltre 40 anni, con oltre 240.000 modelli installati in tutto il mondo, FANUC ROBODRILL è un centro di lavoro CNC caratterizzato da eccellenti prestazioni in termini di qualità e precisione con un cambio utensili straordinariamente veloce, 0,7 secondi, capacità fino a 21 utensili e un sistema a torretta in grado di manipolare utensili del peso di 4 kg. Si tratta della macchina CNC a 5 assi più veloce e robusta sul mercato, versatile e ad alta velocità, tra le scelte di riferimento per gli stampisti che devono coniugare tempi ciclo veloci con precisione, affidabilità e un costo orario vantaggioso. Grazie a strategie di taglio efficientate dall’Intelligenza Artificiale, ROBODRILL ottiene gli stessi risultati di macchine più potenti e in meno tempo, indipendentemente dal fatto che l‘applicazione preveda lavorazione ad alta velocità, realizzazione di stampi o lavorazione a 5 assi. La gamma ROBODRILL α-DiB è costituita da sei modelli S, M e L nelle versioni Standard e Advance, offrendo così grande flessibilità in una vasta gamma di applicazioni di lavorazione, grazie al controllo numerico di punta 31i-B5 ed all’ utilizzo di mandrino BIG-PLUS BBT30. Per garantire l‘operatività, la serie ROBODRILL α-DiB è dotata di numerose opzioni: evacuatori trucioli, sistemi di refrigerante e pulizia delle pareti. Nelle versioni avanzate l‘interferenza dei trucioli è ridotta grazie a una copertura anteriore dell‘asse Y a forma di cupola, e a un mandrino completamente chiuso che separa l‘area di lavorazione dagli organi meccanici della macchina. ROBODRILL è equipaggiata con CNC FANUC 31i-B5, facile da usare e da programmare. Il display a colori da 10,4’’ è equipaggiato con interfaccia iHMI, che assicura semplicità di utilizzo e massima ergonomia. I centri di lavoro ROBODRILL sono equipaggiati con i controlli numerici FANUC di ultima generazione, sono completi di funzionalità di intelligenza artificiale e manutenzione predittiva, e sono IIoT-ready grazie al supporto dei protocolli OPC UA e MT-Connect. Inoltre, sono predisposti all’utilizzo della piattaforma intelligent edge FANUC FIELD e all’integrazione rapida di robot di asservimento. Il software ROBODRILL-LINKi permette di monitorare costantemente da remoto lo stato della macchina e la sua produttività, visualizzandone in tempo reale l’efficienza; si tratta quindi di uno strumento molto utile per contrastare il downtime, abilitare la manutenzione preventiva e accedere a servizi di riparazione e di consumo. Uno schermo di manutenzione dedicato e semplici istruzioni garantiscono il rapido ripristino se, ad esempio, i punti di zero vengono persi a causa di input errati dell’operatore. La funzionalità Preventive Maintenance Guidance riduce al minimo i tempi di inattività e consente di realizzare un ROI elevato. Disponibili infinte opportunità di automazione grazie al pacchetto QSSR (Quick & Simple Start-up of Robotization), che consente l’integrazione immediata di un robot. Questo tool di avvio rapido comprende tutti i componenti necessari a realizzare una soluzione completamente automatizzata, dove macchina e robot condividono lo stesso ambiente e linguaggio rendendo semplice l’integrazione. Le potenzialità dei centri di lavoro ROBODRILL vengono poi ulteriormente amplificate dalla disponibilità della funzione Fine Surface Technology, che consente di raggiungere risultati eccellenti in termini di finitura superficiale. Questa funzione permette di aggiungere un decimale al comando relativo alla posizione degli assi, aumentando la risoluzione di 10 volte (0,1µm) e riducendo così in maniera significativa gli errori dovuti all’arrotondamento.
GERARDI MORSE MODULARI DI PRECISIONE! Gerardi è la prima azienda e famiglie di morse che vantaggio della precisione in assoluto a proporre morse permette di riconfigurare ogni nell’operazione di serraggio modulari di precisione per morsa in maniera semplice e lavorazione del particolare centri di lavoro, con una e rapidissima a seconda da lavorare. Questo sistema delle più ampie gamme dell’applicazione. Le morse offre notevoli vantaggi in attualmente disponibili nel della serie StandardFLEX fresatura, poiché consente settore workholding della sono un evoluzione della di avere sempre la piastra presa pezzo. Si tratta di morsa Standard STD. La ganascia ideale per il tipo prodotti che non sono fini a loro caratteristica principale di lavorazione da eseguire. loro stessi, ma fanno parte è la sostituzione rapida delle La famiglia Tooling è l’altra di una gamma più vasta, e piastre ganasce che avviene grande divisione Gerardi, in sono dotati di accessori che manualmente e senza l’ausilio cui vanno considerate le teste implementano e diversificano di alcun utensile, questo è angolari della nuovissima le possibilità di utilizzo possibile grazie al sistema Linea Classic che nascono permettendo di abbinare perno-molla, che consente un da solide basi tecniche e tra loro diverse soluzioni diverso utilizzo della morsa in dall’esperienza maturata in a marchio Gerardi. La tempi ridottissimi. 40 anni trascorsi al fianco modularità che caratterizza Grazie al sistema a pettine dei clienti per la risoluzione i prodotti Gerardi consente di rigatura prismatica delle dei problemi più variegati al cliente finale non solo di piastre ganascia, risulta cercando la soluzione beneficiare delle continue migliorato anche l’effetto migliore e garantendo evoluzioni ed ampliamenti discendente che durante la sempre l’elevata qualità della gamma ma anche, fase di serraggio, trascina ed affidabilità dei prodotti quando occorre, di rinnovare il pezzo contro lo slittone Gerardi. Quasi 300 modelli o poter riconfigurare articoli garantendo anche una di teste angolari standard, già acquistati per una notevolissima precisione ideati, realizzati e distribuiti determinata esigenza in altre di riposizionamento. in oltre 60 paesi nel mondo attrezzature specifiche per L’allineamento agli assi della dalla Gerardi S.p.A., corredati nuove necessità produttive. macchina avviene grazie da una gamma di opzioni che Questo è l’aspetto vincente alle chiavette longitudinali ne completano le potenzialità della filosofia di produzione e trasversali (16H7) o fori applicative e prestazionali. modulare dell’azienda, di posizionamento (Ø16 Il design compatto, insieme che tuttavia non vuol dire mm F7), a richiesta, previsti alle specifiche descritte, standard ed uguale per tutti. sulla base di ciascuna consente alte perfomances, Grazie ad una scelta attenta morsa. Naturalmente elevate velocità, lunga di più prodotti modulari tutto ciò consente oltre durata degli utensili. Le si ottengono attrezzature alle precisioni dichiarate teste angolari Classic complesse e perfettamente tempi di installazione Line ormai consolidate sul customizzate, che possono ristrettissimi. L’effetto essere realizzate in base discendente guidato, che a specifiche esigenze del contraddistingue la linea cliente. Per quanto riguarda StandardFLEX rispetto la famiglia Workholding, allo standard di mercato, StandardFLEX è la morsa più garantisce un livello di evoluta in quanto dotata del ripetibilità di posizionamento geniale sistema a pettine per non raggiungibile con la rapida sostituzione delle sistemi tradizionali. Il piastre ganasce discendenti. risultato è un’ottima presa Si tratta di un sistema a pezzo con minor forza cambio rapido delle ganasce applicata, e di conseguenza applicabile su più tipologie minori deformazioni a tutto mercato e con una gamma ampissima, garantiscono ottime prestazioni in tutte le tipologie di fresatura, ma anche di foratura e maschiatura. Caratteristiche proprie di questa linea sono il cono integrale all’albero, l’alta qualità degli ingranaggi, sempre rettificati, e la compattezza delle dimensioni che le rende idonee a compiere lavorazioni in zone difficilmente raggiungibili. In linea con la filosofia modulare dell’azienda, Gerardi ha sviluppato anche una famiglia di teste angolari con cono di entrata macchina o addirittura gruppo flangia completamente intercambiabili in modo da permettere all’utilizzatore di servirsi della stessa attrezzatura su più centri di lavoro semplicemente cambiando il cono o la flangia, ed ottimizzando così l’investimento. Nel caso in cui ci siano più macchine in officina, con gli stessi mandrini è possibile usufruire dello stesso gruppo cono o gruppo flangia su tutte le macchine con un notevole risparmio che può arrivare anche al 20% della testina angolare.
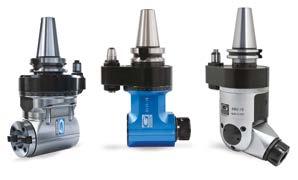
Mikron MILL S 400
GF MACHINING SOLUTIONS FRESATURA AD ALTA VELOCITÀ
La serie Mikron MILL S di GF Machining Solutions, dedicata alla fresatura ad alta velocità, è il risultato di un continuo sviluppo, orientato a combinare le migliori caratteristiche per creare una soluzione di riferimento nel settore. Velocità, dinamica e precisione sono solo tre delle qualità che contraddistinguono la gamma di prodotti. Per rispondere alle esigenze dei produttori che mirano a massimizzare i propri risultati nella produzione seriale ed estremamente precisa di componenti complessi di medio-piccole dimensioni, le macchine della serie MILL S offrono una dinamica di lavorazione impareggiabile e soluzioni di automazione integrate dedicate. Proprio in virtù dell’accuratezza e della ripetibilità di riferimento assoluto, questa serie si rivolge a settori come quello della meccanica di precisione, al settore Medicale e Dentale, caratterizzati da elevati standard qualitativi, criteri restrittivi e micro lavorazioni dove precisione di posizionamento e contatto utensile medio-lungo rappresentano la sfida. Una precisione senza compromessi è sicuramente una delle caratteristiche che contraddistingue i prodotti della gamma Mikron MILL S che garantiscono prestazioni eccellenti grazie ad una progettazione perfetta e al rispetto dei più elevati requisiti meccanici, associati all’implementazione di componenti all’avanguardia. In questa serie, così come in altri prodotti di GF Machining Solutions, si riesce a massimizzare la produttività e la qualità del pezzo da lavorare grazie ad una insieme di accorgimenti progettuali e scelte di materiali, quali il basamento in cemento polimerico con elevati valori di inerzia termica ed eccellenti proprietà di smorzamento, la distribuzione ottimizzata delle forze nella struttura, i motori lineari e le guide ad alta precisione. Il sofisticato sistema di gestione della temperatura include circuiti di raffreddamento separati e indipendenti per tutte le fonti di calore che comprendono i motori degli assi X, Y, Z, B e C, il corpo macchina, il mandrino con tecnologia OptiCool o CoolCore e l’armadio elettrico. Stabilità e affidabilità di processo che permettono di raggiungere precisioni impareggiabili anche su lunghi tempi di lavoro, sono frutto della stabilizzazione attiva della temperatura. I mandrini Step-Tec con cui sono equipaggiate le macchine della serie Mikron MILL S sono dotati della collaudata tecnologia OptiCool che, grazie alle più avanzate soluzioni costruttive, garantisce la stabilità del mandrino a livello termico e limita al minimo il naturale trasferimento di calore del motore verso la testa del mandrino grazie ad un anello supplementare di raffreddamento che funge da barriera termica. Questo fa sì che il mandrino sia termicamente bilanciato, cosa che assicura livelli elevati di precisione, ripetibilità e finitura superficiale. Per garantire precisioni ancora più elevate anche per sessioni di lavoro particolarmente lunghe, sono disponibili anche soluzioni CoolCore che aggiungono al circuito di raffreddamento dello statore un circuito dedicato di raffreddamento del rotore. Velocità di rotazione del mandrino fino a 60.000 rpm e dinamica elevate, cioè velocità di movimentazione degli assi di 100 m/min, rendono la serie MILL S particolarmente indicata per superfiniture. Gli azionamenti diretti sugli assi lineari e rotanti permettono di ridurre al minimo il calore introdotto nell’area di lavoro e di eliminare i tipici giochi causati dagli azionamenti meccanici. Grazie a questi accorgimenti è possibile ottenere finiture con livelli di rugosità estremamente ridotti, per incontrare le esigenze anche di quei settori che richiedono standard molto elevati, come quello medicale o dell’illuminotecnica. La possibilità di realizzare finiture di altissimo livello in un solo setup direttamente in macchina, non solo aumenta la qualità dei componenti lavorati, ma ne riduce anche il costo finale. Infatti un diretto aumento della produttività e della redditività viene ottenuto grazie alla notevole riduzione della manodopera. Poter disporre al proprio interno di tutte le tecnologie, delle attrezzature, dell’automazione e dei sistemi di gestione è da sempre uno dei punti di forza di GF Machining Solutions. Per rispondere alle esigenze di mercato sempre più sensibili al tema dell’industria 4.0, tutte le macchine nascono infatti per essere automatizzate o per essere integrate in linea, senza intralciare il lavoro dell’operatore. La serie MILL S presenta la possibilità di essere integrata nella parte posteriore sia con magazzini pallet fino a 20 posizioni sia tramite robot antropomorfi che permettono una configurazione estremamente flessibile, costruita seguendo le specifiche esigenze del singolo cliente. Produttività ed agilità vengono ulteriormente aumentate grazie al software di facile utilizzo JobToolManagement (JTM) di System 3R, disponibile anche per macchina con cambio pallet integrato. Con JTM, l’utente assegna un programma con controllo numerico (NC) alle singole posizioni dei pallet tramite una semplice operazione di drag-and-drop sul touchscreen.
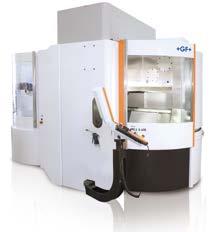
HELLER MAGGIORE PRODUTTIVITÀ E VERSATILITÀ CON LA NUOVA GENERAZIONE DI HF
Con il nuovissimo formato dell’evento virtuale V-CON 2020 a novembre, HELLER ha lanciato la sua nuova generazione di centro di lavoro a 5 assi HF. HELLER aveva già presentato per la prima volta i centri di lavoro a 5 assi della serie HF con il quinto asse sulla tavola nel 2016. Fornendo dinamiche potenti, tempi passivi significativamente ridotti e una cinematica AB unica, in combinazione con un controcuscinetto, la serie ha dimostrato un’eccezionale praticità negli anni. HELLER vede l’applicazione della prima generazione della serie - solitamente ordinata con cambio pallet, ma disponibile anche con carico diretto sulla tavola - principalmente per lotti di medie dimensioni nella produzione di serie e per lavorazioni produttive. Per la seconda generazione, HELLER ha ora ampliato la gamma di applicazioni delle macchine. L’obiettivo è fornire una maggiore universalità, inclusa la produzione di pezzi singoli, combinata con le solite caratteristiche HELLER di produttività, precisione e affidabilità. Tra le innovazioni più significative della seconda generazione ci sono, tra le altre, le nuove unità di lavorazione, che forniscono prestazioni ancora più elevate e specifiche per ogni fabbisogno, e l’uso opzionale di una seconda trasmissione nell’asse Z. Un componente chiave della seconda generazione della serie HF sono le nuove unità di lavorazione. L’obiettivo era combinare i vantaggi dei mandrini HSM già noti della serie H con i vantaggi di un elettromandrino. Le prove di lavorazione effettuate fino ad ora ei dati tecnici dimostrano che questo è stato raggiunto. La seconda generazione della serie HF è equipaggiata con le unità mandrino HELLER (HSU) di nuova concezione con design lineare. Questi mandrini “made by HELLER” sono prodotti sulla nuova linea di produzione ad alta precisione dell’azienda. I mandrini HSU sono impostati su dimensione zero, consentendo una sostituzione rapida ed economica del mandrino, in caso di richiesta di assistenza, fornendo al cliente un basso costo totale per un servizio normalmente molto dispendioso, non solo in termini di costi, ma anche di tempistiche di fermo macchina. Rispetto ai precedenti elettromandrini, i mandrini HSU sono anche più robusti e potenti in termini di comportamento di lavorazione. La nuova unità di lavorazione Power Cutting (PC), ad esempio, fornisce una velocità di 12.000 giri/min e una coppia di 228 Nm in combinazione con un attacco utensile HSK-A 63. La versione Speed Cutting (SC) consente velocità fino a 18.000 giri / min e 103 Nm di coppia combinate con una forte accelerazione. Le due unità di lavorazione DynamicCutting (DC) sono nuovissime. Il mandrino HSK-A 63 DC è stato specificamente progettato per una diversa gamma di pezzi, per una maggiore universalità e flessibilità e fornisce velocità fino a 16.000 giri/min combinate con una coppia elevata di 180 Nm, consentendo fino a 400 Nm in combinazione con un attacco utensili HSK-A 100. Un altro fattore importante nell’applicazione pratica o nella produzione in serie sono i tempi di accelerazione che comportano tempi non produttivi. A questo proposito, HELLER è riuscita a ottenerne un’importante riduzione con le nuove unità di lavorazione. Inoltre, le diverse versioni disponibili Power, Speed e ora PRO, per la seconda generazione, forniscono la scelta ottimale per ogni applicazione. La prima generazione della serie HF forniva già una stabilità e una precisione di fresatura estremamente elevate, grazie al controcuscinetto sulla tavola rotobasculante. Con la variante dell’attrezzatura PRO, la seconda generazione della serie HF offre anche un classico azionamento a portale della tavola nell’asse (Z), con due assi fisicamente separati nel controllo e due sistemi di misura diretti. Un grande vantaggio derivante dalla maggiore rigidità dell’asse della tavola è la capacità di assorbire le massime forze di processo in direzione Z. Questa è un’opzione utile, ad esempio in combinazione con le unità di lavorazione DC ad alta coppia, o se il centro di lavoro deve essere utilizzato per applicazioni universali, ad esempio per la produzione di pezzi singoli con la massima precisione a 5 assi e precisione del contorno o, se si prevede di equipaggiare la lavorazione centrandola con una funzione di rotazione, utilizzando una tavola rotante ad alta velocità. Oltre all’azionamento a portale, la nuova serie HF presenterà al lancio ulteriori nuove funzioni, tra cui il sistema di slittamento a sfacciare HELLER: un asse macchina aggiuntivo (U) integrato nel controllo macchina che consente una tornitura facile e altamente produttiva di contorni interni ed esterni, anche particolarmente complessi.
Monitor di controllo con visualizzazione dell’area lavoro in tempo reale grazie alla camera interna Una delle nuove unità di lavoro fatte in casa sulla nuova linea mandrini HELLER
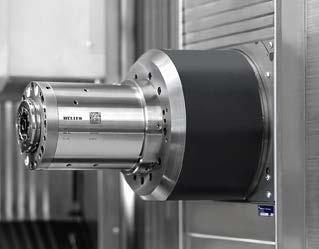
Grazie alla sua organizzazione aziendale snella e reattiva di bloccaggio zero point APS/WPS e Lang 96 mm e alle mutevoli esigenze del mercato, abbinata alle tecniche sono provviste di fori di montaggio di serie. Nelle morse produttive di ultima generazione, la società OML, con serie IMG la vite di manovra è completamente protetta sede a Travacò Siccomario, in provincia di Pavia, offre con sistema telescopico brevettato. Ciò evita la necessità un’ampia gamma di attrezzature di bloccaggio che si di rimuovere le ganasce in modo da trovare la posizione distinguono per la loro concezione innovativa e per la di bloccaggio ottimale. Normalmente le morse con vite loro estrema funzionalità. Nei suoi 45 anni di storia, protetta usano la slitta di manovra come strumento di l’azienda pavese ha maturato una grande esperienza nella protezione. Questo tipo di soluzione, però, obbliga a progettazione, sviluppo e realizzazione delle attrezzature continui spostamenti delle ganasce nell’apposita sede, che, oggi, configurano un catalogo di prodotti standard in quanto la corsa delle medesime si riduce a pochi estremamente ampio e diversificato. L’ufficio tecnico della mm. Al contrario le morse IMG, pur mantenendo la vite OML è anche in grado di studiare specifiche problematiche completamente protetta, consentono un movimento del cliente pervenendo allo sviluppo di soluzioni speciali. continuo di apertura e chiusura della morsa. Ideali in caso IMG è la sigla che identifica una speciale linea di di automazione e di utilizzo di sistemi di pallettizzazione, morse che OML propone in versione autocentrante, le morse serie IMG sono piuttosto semplici da installare: trasformabile in doppio bloccaggio e fissa. La serie IMG il montaggio avviene direttamente sulla tavola della (che comprende le configurazioni IMG 125-220, IMG macchina tramite l’utilizzo di staffe (disponibili in opzione). 125-320, IMG 160-270 e IMG 160-420) garantisce una È prevista un’apertura piuttosto ampia per l’uscita gamma di serraggio piuttosto ampia, oltre che massima ottimizzata dei trucioli; massima precisione e ripetibilità flessibilità e la possibilità di effettuare un bloccaggio sia vengono assicurate dalle guide trattate e rettificate. esterno che interno. Le morse IMG sono dotate di ganasce Con le morse IMG è possibile raggiungere una forza di riversibili Sintergrip che assicurano minima profondità di serraggio massima di 50 KN. Ad accrescerne la forza, bloccaggio e assenza di pre-lavorazione. Il bloccaggio di è l’abbinamento con il sistema brevettato SinterGrip tipo meccanico garantisce una protezione completa, grazie espressamente concepito per bloccare un pezzo nel anche all’impiego di un sistema telescopico brevettato. minore spazio possibile (ovvero 3,5 mm di presa). In Le morse IMG sono dotate di un’interfaccia per sistemi questo modo, oltre a poter lavorare completamente il pezzo in un’unica fase (soprattutto in caso di IMG autocentrante macchine a cinque assi) è possibile risparmiare sulle materie prime, aspetto molto importante quando queste possono avere una grande incidenza sul prezzo (alluminio, titanio, ecc). Inoltre, con il sistema Sintergrip è possibile sfruttare al meglio le prestazioni della macchina utensile e degli utensili assicurando un bloccaggio sicuro e senza deformazioni del pezzo. Il bloccaggio del pezzo con i sistemi tradizionali richiedeva infatti una maggiore superficie di presa, che oltre che comportare uno spreco di materie prime aumentava la possibilità di deformazione del pezzo. Con Sintergrip invece la superficie di presa è ridotta al minimo, non è richiesta alcuna perforazione preventiva del pezzo oltre a garantire grande stabilità di bloccaggio e maggiore velocità di lavorazione. Altro aspetto che identifica le morse autocentranti IMG è la modularità: possono infatti essere facilmente trasformate in morse a bloccaggio fisso o in morse a doppio bloccaggio. Le morse a doppio bloccaggio dispongono di un meccanismo completamente compensante; ciò vuol dire che è possibile bloccare due pezzi di differenti dimensioni.
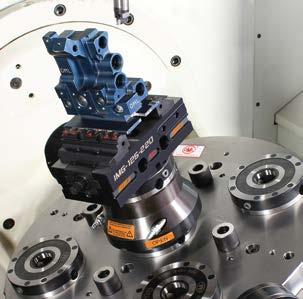
OPEN MIND MASSIMA SICUREZZA NELLA LAVORAZIONE A 5 ASSI
OPEN MIND, uno dei produttori più richiesti al mondo per le sue soluzioni CAM ad alte prestazioni per la programmazione, indipendentemente da macchina utensile e controllo numerico, sviluppa soluzioni CAM perfettamente coordinate e dotate di un elevato numero di innovazioni esclusive, le quali garantiscono prestazioni notevolmente migliori per quanto riguarda la programmazione e la fresatura. Una delle ultime novità nel mondo OPEN MIND è la nuova simulazione. Grazie a Optimizer, un modulo opzionale della nuova simulazione hyperMILL® VIRTUAL Machining, OPEN MIND consente di migliorare i programmi NC tenendo in considerazione la specifica cinematica della macchina. La lavorazione viene simulata sulla base di un “gemello” digitale, consentendo di controllare meglio la complessità derivante dalle numerose opzioni di serraggio e inclinazione nella lavorazione a 5 assi. hyperMILL® VIRTUAL Machining Optimizer individua automaticamente nelle lavorazioni multiasse la migliore inclinazione sotto il profilo tecnico, che viene sottoposta a controllo collisioni e dotata di movimenti di avanzamento efficienti. In questo modo, è possibile prevenire errori che, ad esempio, possono verificarsi in caso di ottimizzazione manuale delle posizioni degli assi. A causa dell’elevata complessità è difficile riconoscere gli effetti su tutte le fasi di lavorazione successive e prendere decisioni per un’ottimizzazione generale. Optimizer di hyperMILL® VIRTUAL Machining analizza le sequenze di lavorazione complete con potenti algoritmi di ottimizzazione, prendendo in considerazione anche le limitazioni degli assi. Ciò consente di evitare dispendiosi riposizionamenti. Questo modulo genera un’esecuzione della macchina efficiente e sicura. Uno dei vantaggi importanti di hyperMILL® VIRTUAL Machining Optimizer si ottiene quando si esegue la programmazione per centri di lavorazione molto differenti. L’adeguamento all’ultima macchina utilizzata, incluso il controllo collisioni, avviene automaticamente nel software di simulazione, i programmi CAM possono essere configurati in modo completamente indipendente dalla macchina. Ciò garantisce alle aziende una maggiore flessibilità nella gestione delle loro capacità di truciolatura. hyperMILL® VIRTUAL Machining Optimizer riconosce altresì possibili problemi: se, ad esempio, la macchina ha un movimento limitato dell’asse di rotazione, il software considera questo aspetto nelle inclinazioni e garantisce una lavorazione fluida. In caso di limitazione dell’asse, Optimizer interrompe il percorso utensile, esegue un morbido disimpegno e ruota l’asse per ovviare alla limitazione. Successivamente l’utensile affonda di nuovo dolcemente e riprende la lavorazione. Questo metodo consente, ad esempio, di eseguire anche una lavorazione a spirale in una macchina limitata. Anche le macchine con la testa a forcella possono essere impiegate per una lavorazione dinamica grazie a Optimizer. Il software di OPEN MIND ottimizza i movimenti di incremento e riconosce automaticamente se il posizionamento è più veloce ricorrendo a un asse di rotazione. In questa fase, gli assi di rotazione generano la traiettoria più breve e i movimenti degli assi lineari si riducono al minimo: il risultato è una maggiore velocità nei movimenti di avanzamento. Qualora un movimento a 3 assi non risulti possibile a causa delle collisioni rilevate, Optimizer di hyperMILL® VIRTUAL Machining provvede a modificare il movimento ricorrendo ad un quarto o quinto asse. Le diverse operazioni, che siano 2,5D, 3D oppure a 5 assi, vengono collegate in modo tale da ridurre i tempi morti. L’utensile si sposta, a prova di collisioni, lungo il pezzo in lavorazione senza il bisogno di raggiungere un piano di sicurezza elevato.
I movimenti di incremento ottimizzati riducono notevolmente i tempi di inattività (Fonte: OPEN MIND). hyperMILL® VIRTUAL Machining: Optimizer analizza sequenze di lavorazione complete prendendo in considerazione anche le limitazioni degli assi (Fonte: OPEN MIND).
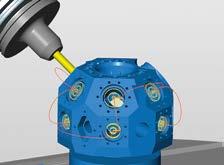

SORALUCE ALESATRICE A MONTANTE MOBILE SORALUCE MOD.FR18000-W OPERAZIONI DI FRESATURA E ALESATURA IN UN UNICO PIAZZAMENTO PER MASSIMIZZARE LA PRODUTTIVITÀ
SORALUCE ITALIA fornirà nei primi mesi del 2021 alla ditta gestito con un asse del CNC che garantisce la massima precisione MECCANICA LOVATO SRL di Chiampo nel vicentino il centro di rettilineità di uscita dello slittone più canotto e ciò avviene anche di fresatura-alesatura SORALUCE modello FR18000-W per la con tutte le teste accessorie caratterizzate da pesi diversi. Una tra le lavorazione di componenti per i settori della meccanica generale, ultime innovazioni brevettate da SORALUCE è il sistema DYNAMICS dell’energia e dei beni strumentali. Si tratta di una soluzione ACTIVE STABILIZER (DAS+ - Brevetto n. EP 3017911 ) che multitasking estremamente versatile ed consiste in attuatori posti sulla RAM della orientata alla massimizzazione della produttività, macchina che permettono di smorzare il con capacità di realizzare operazioni di fresatura “chatter”, ovvero vibrazioni autorigenerative, ed alesatura in un unico set-up, avendo la aumentando così la produttività della possibilità di lavorare pezzi di forme differenti macchina fino al 300%, diminuendo l’usura e dimensioni medio-grandi. La fresalesatrice dell’utensile, diminuendo le sollecitazioni a montante mobile SORALUCE modello meccaniche della macchina, aumentando FR18000-W presenta una corsa longitudinale la finitura superficiale delle lavorazioni e di 18.000 mm, corsa verticale di 4.500 mm, favorendo la lavorazione non presidiata. uscita dello slittone di 1.900 mm e corsa del La macchina è dotata di un completo canotto modulare diametro 150 mm di 1000 impianto liquido refrigerante e di controllore mm. La SORALUCE mod. FR18000-W è di frequenza per l’adeguamento della equipaggiata con unità di governo digitale pressione del liquido refrigerante tramite HEIDENHAIN mod. TNC 640, volantino CNC o tramite potenziometro collocato elettronico remotato wireless e pacchetto sul pannello di controllo. Un efficace Industria 4.0. Tutta la struttura della macchina impianto di filtraggio, costituito da un è completamente in ghisa perlitica GG30, separatore magnetico, con filtraggio a mentre la RAM è GGG70. La adozione carta più filtraggio a cartuccia per ciascuna della struttura totalmente in ghisa conferisce La alesatrice a montante mobile SORALUCE mod. delle due pompe, bassa e alta pressione, alla macchina una grande rigidità, ottimo FR-W è estremamente versatile e adatta a diversi tipi di lavorazioni nei differenti settori: meccanica garantisce un eccellente filtraggio del liquido assorbimento delle vibrazioni e la massima generale, energia, beni strumentali ecc. refrigerante da micro impurità (≤ 20 micron) stabilità geometrica ottenendo così una elevata preservando così i distributori rotanti e le precisione volumetrica. Le guide lineari a ricircolo di rulli combinati teste automatiche. La piattaforma operatore consente il movimento con pattini smorzatori garantiscono una elevata dinamica e rigidità, verticale e trasversale, inoltre è dotata di una ulteriore pedana mobile a nonché un’eccellente precisione in posizionamento e ripetibilità assi. scomparsa che permette all’operatore di accedere alla linea mandrino Inoltre, il sistema di scorrimento adottato da SORALUCE da quasi e all’utensile in sicurezza ed ergonomia. La macchina presenta 30 anni, con oltre 2500 macchine installate, garantisce bassi costi elevati indici di ergonomia, sicurezza e manutentabilità (premiati di manutenzione e di consumo energetico, diversamente da altri tipi con il “RED DOT AWARD 2016”): di fatto l’operatore ha un’ottima di guide tradizionali. La macchina è dotata di mandrino modulare visibilità dell’area di lavoro rimanendo al tempo stesso in totale stato estraibile (1.000 mm), brevettato da SORALUCE, tale soluzione di sicurezza. La macchina risulta estremamente versatile e permette permette di dotare la alesatrice di più mandrini estraibili (canotti) aventi di ridurre al minimo i tempi di fermo macchina grazie anche al sistema diametri e lunghezze diversi tra di loro. La macchina è configurata con di lavoro in pendolare ed alla presenza di n°1 unità rototraslante sistema di cambio teste automatico e un magazzino (pick-up dotato dotata di tavola girevole avente superficie di 2.500x3.000 mm con un di n. 4 posti di deposito) per lo stoccaggio delle differenti teste di asse in continuo (0.001°); corsa asse trasversale W = 2.000 mm e cui è dotata la FR18000-W, ciò per effettuare diverse tipologie di portata 40 ton. Un piano di lavoro avente superficie di 2.000x3.000 lavorazioni in un unico piazzamento tra le quali la testa automatica mm viene collocato a destra della unità rototraslante e un secondo ortogonale; la testa ad angolo con asse c indexato ogni 1° oltre alla piano di lavoro avente superficie 13.000x3.000mm verrà collocato a predisposizione per una testa d’Andrea. L’accoppiamento di tutte sinistra della unità rototraslante stessa, così facendo potranno essere le teste accessorie con la RAM/slittone avviene tramite dentatura lavorati pezzi di grandi dimensioni in pendolare massimizzando la Hirth garantendo così la massima precisione di posizionamento e produttività della macchina e minimizzando i tempi improduttivi. La di ripetibilità oltre che una assoluta rigidità di accoppiamento testa/ ditta MECCANICA LOVATO SRL è un’azienda storica fondata nel slittone. La FR18000-W presenta le più recenti tecnologie sviluppate 1994 a Chiampo (VI) dotata di alesatrici a montante mobile di medie da SORALUCE tra cui l’innovativo RAM BALANCE SYSTEM e grandi dimensioni tutte dotate di unità rototraslanti e sistemi di (DBS3 - brevetto WO 2010/072856), sistema elettromeccanico cambio testa automatici.
TEBIS TUTTA LA FRESATURA IN UN CAM
Accelerare la programmazione CNC automatizzando CNC di geometrie prismatiche regolari e a forma libera. i processi e sostituendo i passaggi più ripetitivi con Le strategie di fresatura 3D di Tebis per la sgrossatura, la l’accesso automatico alle informazioni già memorizzate finitura e l’asportazione del materiale residuo incorporano nelle librerie: tutto questo rappresenta il primo obiettivo tutte una serie di soluzioni anticollisione applicabili della tecnologia Tebis AutomillTM, cuore del software. sin dall’inizio del processo e ottimizzate per le diverse Nella programmazione CNC Tebis automatizzata, i situazioni di lavoro. Ad esempio, a seconda del tipo di programmi per le macchine utensili non vengono più creati applicazione può essere prevista la deviazione automatica nel modo tradizionale. Il software valuta il modello CAD dell’utensile oppure la limitazione delle aree a rischio. La digitale del componente e calcola il programma CNC combinazione di queste tecniche con le tecnologie di richiesto accedendo a una struttura precedentemente simulazione ad alta precisione e i percorsi utensile CNC memorizzata, formata da rappresentazioni digitali adattati alle pendenze permette di mandare in macchina dell’ambiente di produzione disponibile e a template che percorsi ottimali con tempi di lavorazione ridotti al minimo. raccolgono il know-how di produzione aziendale. In Tebis Superiore a qualsiasi altra tecnica di lavorazione nel tutte le competenze di produzione vengono salvate in realizzare superfici di alta qualità in modo veloce ed NCSets, features e nel Job Manager. Il programmatore efficiente, il pacchetto software Tebis per la fresatura a ha in questo modo a sua disposizione librerie di processo 5 assi continui permette di sfruttare al massimo grado il che contengono il parco macchine, i controlli, gli utensili potenziale dei costosi centri di lavoro ad alte prestazioni, e i sistemi di bloccaggio. I modelli virtuali comprendono consentendo di pianificare e calcolare molto facilmente tutte le informazioni dettagliate: le geometrie macchina con tutte le lavorazioni multiasse escludendo i rischi di gruppi ausiliari, cinematica, fine corsa e parametri dinamici; collisione. I programmi CNC specifici per macchine a 5 i valori di taglio comprovati e ottimizzati degli utensili; tutti assi con Tebis possono essere generati in vario modo: si gli accessori delle macchine utensili quali mandrini, lunette può optare per una programmazione CNC a 3 assi con e punte o tavole macchina, estensioni e divisori. I modelli orientamento spaziale costante dell’utensile e lavorazione digitali di machine, utensili e dispositive di serraggio su più lati; oppure elaborare un programma CNC a 3 assi non servono solo ad accelerare i processi, ma anche ad con conversione automatica in programmi a 5 assi continui aumentarne l’affidabilità. Ad esempio tutte le potenziali per evitare collisioni e ottenere condizioni di taglio ottimali. collisioni possono essere individuate e corrette già in Infine si possono sfruttare le funzioni CNC specifiche a 5 fase di pianificazione; in questo modo la programmazione assi continui, quali ad esempio. la sgrossatura di geometrie NC adotterà fin dall’inizio le impostazioni, gli utensili e e di tasche a forma, la fresatura lungo profili curvi, la i piazzamenti più appropriati. Molti utenti Tebis fanno finitura tangenziale e la finitura frontale. Ognuna di queste largamente uso del simulatore anche per pianificare le funzioni è pensata in modo specifico per una particolare lavorazioni, verificando in anticipo la fattibilità dei progetti. lavorazione e contiene solo i parametri effettivamente Che si tratti di fresatura 2,5 assi, 3 assi o 5 assi continui, necessari. Per ottenere una lavorazione il più possibile il software CAD/CAM di Tebis offre un metodo veloce, efficiente e la massima qualità delle superfici l’utente semplice e automatizzato per creare programmi CNC privi può scegliere il programma CNC che ritiene più adatto di collisioni. Tutte le soluzioni sono pensate in un’ottica ma al contempo può anche appoggiarsi all’automazione concreta e per questo sviluppate in stretta collaborazione CNC Tebis integrata e utilizzare template CNC ottimizzati con i clienti, così da rispondere prontamente alle reali contenti - ad esempio - gli utensili di fresatura disponibili e esigenze di produzione. Per lavorare anche su più lati i valori di taglio corretti. geometrie 2,5 D sia aperte che chiuse il software Tebis offre opzioni integrate di sgrossatura e finitura di pareti e fondi, che permettono di realizzare intere geometrie standard utilizzando una sola funzione e di semplificare così la programmazione CNC. In particolare la tecnologia feature - che include anche il riconoscimento automatico delle feature - consente di automatizzare la programmazione Grazie all’uso dei digital twins è possibile verificare e correggere i percorsi utensile nell’ambiente CAM.
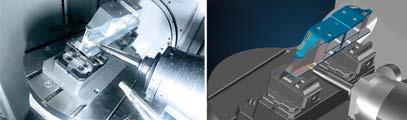