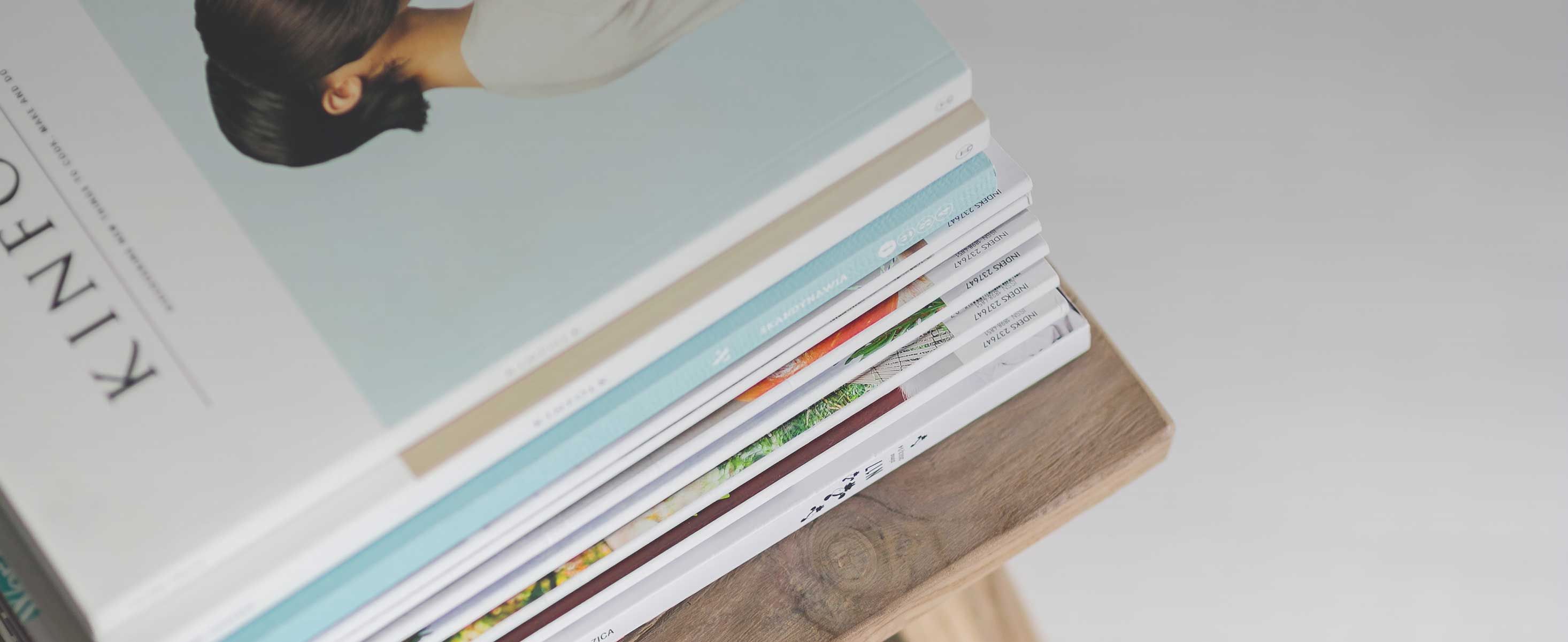
5 minute read
B1 Research Project
Electrifying the Cold Chain -
Phase 1: Concept Development
Final Report
RACE for Business
Research theme B1: Transforming energy productivity through value chains
ISBN: 000-0-00000-000-0
Industry Report
Electrifying the Cold Chain - Phase 1: Concept Development
March 2023
Citations
Bruno, F., Liu, M., Riahi, S., Pudney, P. and Evans, M. (2023). Electrifying the Cold Chain - Phase 1: Concept Development Prepared for RACE for 2030 CRC.
Project team
University of South Australia
• Frank Bruno
• Ming Liu
• Soheila Riahi
• Michael Evans
• Peter Pudney
• Lachlan Mudge
DEM (SA)
• Joanne Galley
• Peter Nattrass
Aldom
• Mark Haig
• Jurij Polischko
• Darren Harris
Simble
Project partners
• Bill McGhie
Acknowledgements
This project is supported by funding from RACE for 2030, Aldom, Department of Energy and Mining (SA) and Simble. We would like to thank the Industry Reference Group participants from the following organisations: Australian Alliance for Energy Productivity (A2EP), Delvic Foods, Massey University (NZ), Mondial Advisory, Queensland Farmers Federation, SuperCool Group
Although the IRG members and partners have provided valuable inputs and feedback throughout the project, the findings and recommendation included in this report do not necessarily reflect the views of each individual member.
Acknowledgement of Country
The authors of this report would like to respectfully acknowledge the Traditional Owners of the ancestral lands throughout Australia and their connection to land, sea and community. We recognise their continuing connection to the land, waters and culture and pay our respects to them, their cultures and to their Elders past, present, and emerging.
What is RACE for 2030?
RACE for 2030 CRC is a 10-year cooperative research program with AUD350 million of resources to fund research towards a reliable, affordable, and clean energy future. https://www.racefor2030.com.au
Disclaimer
The authors have used all due care and skill to ensure the material is accurate as at the date of this report. The authors do not accept any responsibility for any loss that may arise by anyone relying upon its contents.
Executive Summary
The cold chain is a low temperature-controlled supply chain to prolong shelf life and maintain the quality of perishable products. Worldwide, the cold chain is reported to account for 30% of total energy consumption. The low temperature is achieved by using refrigeration facilities, such as cold storage rooms, refrigerated display and storage cabinets and refrigerated transport. Of particular concern is food transport refrigeration, which is responsible for 15% of world fossil fuel energy. Diesel engine driven vapour compression is dominant in transport refrigeration systems. This type of engine is noisy and has low efficiency of 35%-40% and very high CO2-e emissions. In addition, the poor temperature performance of existing systems on diesel trucks is a key contributor to food spoilage.
This project has reviewed three commercial transport refrigeration systems, vapour compression, cryogenic and eutectic refrigeration. A concept design has been developed for an innovative eutectic refrigeration system suitable for use in both diesel and electric, light to medium refrigerated vehicles.
The on-board eutectic refrigeration system is the integration of an electric-powered refrigeration unit and a phase change thermal energy storage unit. The storage unit is electrically charged when the vehicle is not in service. This reduces the fuel consumption for diesel driven vehicles, or the load placed on the battery system for electric vehicles. Different from existing distributed eutectic systems, the proposed centralised design has the advantages of easy maintenance and better temperature control.
The novel system improves the energy productivity of cold chain logistics by reducing diesel fuel consumption and improving temperature control with more efficient refrigeration. For a medium size vehicle, a 70% reduction of CO2-e emissions could be achieved for the refrigeration system if charging is provided by grid electricity in South Australia The techno-economic analysis concluded that, compared to diesel-powered and battery-powered vapour compression refrigeration, eutectic refrigeration has the lowest energy consumption and operating cost.
Future work aims to construct a prototype eutectic refrigeration system and demonstrate its operation on a medium sized vehicle in South Australia
List of Figures
List of Tables
1. Introduction
With an increasing population, Australia’s food demand and food production have continuously grown in recent decades. Retail sales of food costs over $140 billion per year in Australia (Department of Agriculture, 2014). Refrigeration is required through the entire supply chain to maintain the quality and freshness of perishable foods, such as vegetables, fruits, meats, seafoods and dairy products. In 2018, more than 23 million tonnes of foodstuffs worth $42 billion (based on farm gate values) passed through the Australian food cold chain (Brodribb & McCann, 2020) Worldwide, the cold chain is reported to account for 30% of total energy consumption (Adekomaya et al., 2016). In addition, according to the Australian Food and Grocery Council, food is moved in and out of refrigeration control very frequently, on average 14 times before consumption (Australian Food and Grocery Council, 2017). In one Australian study, before reaching consumers, broccoli took 39 steps along the cold chain (Han, 2005).
Refrigerated transport plays a crucial role in cold chain logistics. It is estimated to account for 60% of the total cost in cold chain logistics (Food Logistics, 2008). The transport refrigeration system is dominated by diesel-driven mechanical vapour compression with refrigerant R404A, which is the main refrigerant used in low temperature applications. Due to the large variation in operating conditions, the mobile refrigeration system has a very low coefficient of performance (COP: 0.5 ~ 1.75), resulting in high diesel consumption and CO2-e emissions (Tassou et al., 2009). In Australia, refrigeration systems on trucks consume 70-90 million litres of diesel annually (Mark Ellis & Associates Pty Ltd, 2009), which generates 190-245 kilotonnes of CO2-e emissions (national greenhouse accounts factor of 2.717 kg CO2-e per litre of diesel (Department of Climate Change, 2022)) and costs about AUD$140-180 million (AUD$2 per litre of diesel). It has been reported that the worldwide refrigerated transport sector consumes around 15% of fossil fuel energy (Adekomaya et al., 2016).
R134A, R404A, R417B are commonly used refrigerants in refrigerated transport, which have a major impact on global warming. They have high global warming potential (GWP) of 1,430, 3,922 and 3,027, respectively, and are being phased out in developed countries (SOLGroup, 2022) Out of these refrigerants, R404A dominates refrigeration systems used in frozen food applications. Due to vibrations during transportation, on-board refrigeration systems have an additional risk of refrigerant leakage compared to stationary refrigeration systems When leaks occur, the energy efficiency of the system is also reduced and the refrigerant needs to be refilled regularly.
The refrigerated transport sector is facing increasing pressure to adopt new technologies to decarbonise. This can be achieved through improving the energy efficiency of the refrigeration system, electrifying the refrigeration system using electricity from renewable energy sources, adopting alternative refrigeration technologies, and using alternative fuels from renewable energy sources. The promising renewable energy sources include liquid biofuels (ethanol and biodiesel), biogas (converted to CNC and LNG) and green hydrogen to power either conventional or adapted internal combustion engines (A2EP (Australian Alliance for Energy Productivity), 2017c)
Chapter 2 of this report presents the various types of transport refrigeration systems and technologies that can help to improve their performance. Chapter 3 reviews phase change materials that have potential to maintain the refrigerated space at frozen temperature (-18°C) and summarises test results of candidates selected for further study Chapter 4 presents the methodology used for a technoeconomic analysis of the various types of systems along with results, while Chapter 5 provides a concept design for a vehicle using eutectic refrigeration and then models the performance. Finally, Chapter 6 discusses different schedules of charging patterns and Chapter 7 provides conclusions to the study.