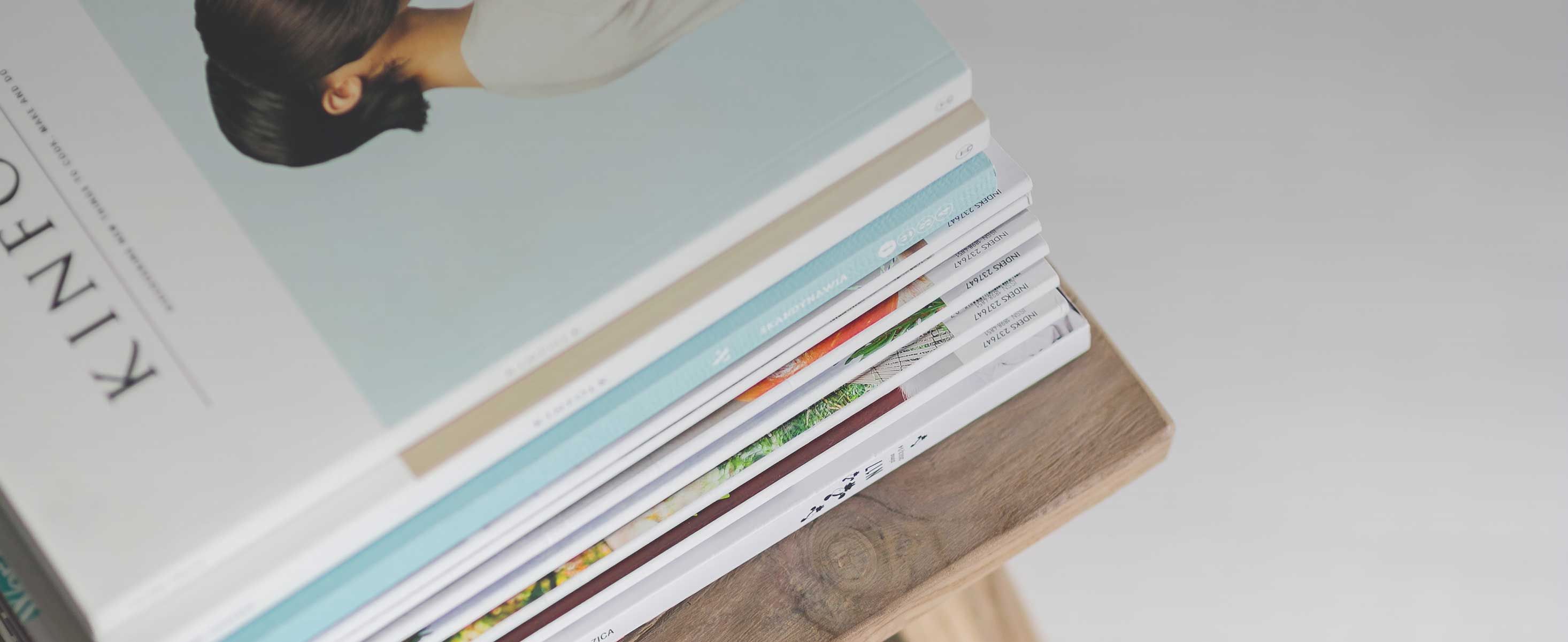
2 minute read
ENERGY AND DEMAND PRICING ________________________________________ 15
Suction pressure modification2
Blast fan optimisation (1 h @ 75%)2
Thermal battery (980 kWh)3
Electric battery (1 h)3
Hot water heat pump4
Retail tariff Retail with DR Wholesale1 Savings Payback Savings Payback Savings Payback
$/kW(h) years $/kW(h) years $/kW(h) years 0.88 Immediate N/A N/A 7.26 Immediate 6.05 Immediate N/A N/A 27.79 Immediate 2.19 123 5.13 53 16.52 16 14.95 53 24.66 32 135.78 6 44.41 17 N/A N/A 56.22 13
1 Annual savings presented in the table are based on Queensland, the most favourable NEM region during the 2020/21 year. 2 Annual savings are per kW of compressor capacity. 3 Annual savings are per kWh of storage capacity. 4 Annual savings are per kWth of heat pump capacity.
Unfortunately, despite the significant refrigeration loads onsite, given the time critical process cooling requirements of abattoirs, these sites are unable to adequately adjust their cooling demand profiles, resulting in limited load shed opportunities. The use of thermal batteries can offset some loads. Batteries may also be useful for reducing the size of refrigeration equipment and/or avoiding upgrades. Initial modelling has indicated that the relatively slow recharge rates reduce available savings, but this has not been reviewed in detail as part of this report. Electrical batteries provide good flexibility and a significant potential for varying net demand.
Should an electrical battery (or any of the items above) be implemented, it is essential that proper consideration be given to its operation in order to maximise savings and prolong life. In particular a plan should be prepared that covers:
• pricing contract with demand response aggregator to maximise load shed revenue • clear control strategy to optimise daily operation for energy and demand cost reductions, including interactions with other systems onsite • detailed modelling that predicts the overall operation and economics of the project—the model developed as part of this project is ideally suited for this.
Sites with cold storage are much better suited to load shed programmes, and the abattoirs reviewed that had large cold storage facilities were using them to good advantage.
In summary, the following characteristics of abattoir refrigeration loads make them difficult to flex.
• Time sensitive cooling profiles—chilling of meat is subject to critical and time sensitive cooling profiles that cannot be interrupted. • Very limited production flexibility—production throughput is not flexible without making significant changes to work shifts and days. • Relatively small demand charges—abattoirs are large energy users with relatively low energy tariffs and demand charges, which erode the customer-side value from load shifting. • Thermal storage limited to high-side loads—the availability of phase change materials is limited to the high-side (chiller) loads. • Loads that can be flexed are small—suction pressure variation and blast fan speed variations were found to be loads that can be flexed but offer very minor load reductions relative to site demand. • Battery storage may facilitate load flexing—however the business case for this investment was shown to be a case-by-case proposition that would require detailed investigation and careful consideration.