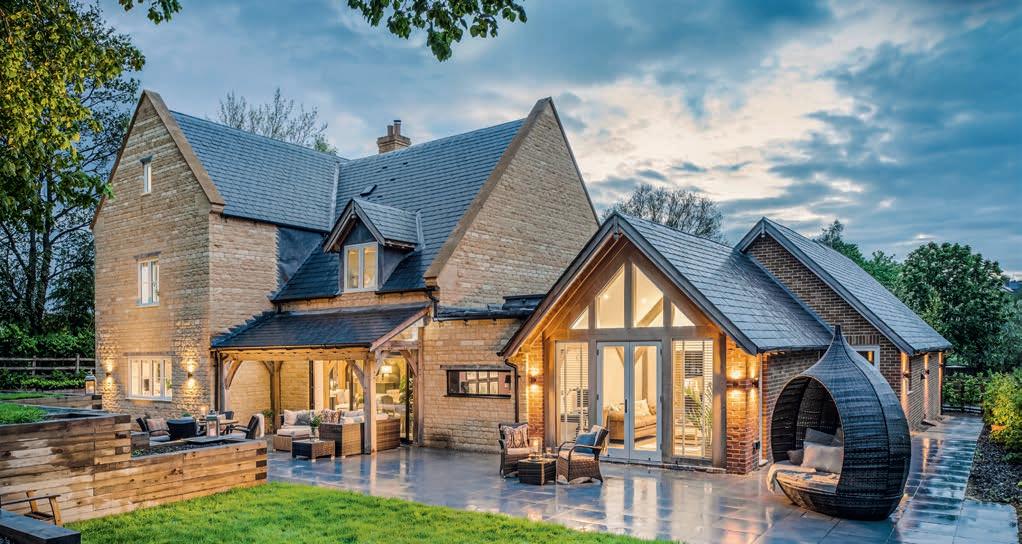
3 minute read
Hybrid build systems
Timber’s versatility as a construction material means it can be used alongside a range of other build systems
Timber has a host of advantages – it’s strong, sustainable and provides good thermal insulation. It’s also versatile, which means it’s easy to combine with other systems to get the best of both worlds from multiple solutions. “It’s becoming more common to build hybrid homes and there are many different systems that can be used this way,” says Simon Orrells, managing director at Frame Technologies. “Building hybrid means you can choose the best materials to suit the situation.” It’s not necessarily more expensive, either – in some scenarios, incorporating multiple structural solutions can provide a smart route to achieving your goals while keeping costs to a minimum.
According to David Williams, head of production at Oakwrights, a conventional panelised timber frame can work well with pretty much any other method.
“However, full consideration needs to be given to the physical attributes of each system so that they act as one, rather than working against each other,” he says. “The aesthetics of a building can be significantly enhanced by bringing together different materials and systems, too.” The most widespread partnerships include structural timber alongside materials such as steel, engineered wood products, concrete and even masonry. Here are the common combinations and where they make sense.
Oak frame encapsulation
Historically, the post and beam skeleton of an oak frame was infilled in wattle and daub. Today, oak homes are wrapped in a thermally e cient panelised system to provide an airtight shell. SIPs are one option, well-suited to homeowners who want to marry the aesthetics of oak frame with the thermal performance of SIPs. “Anything is possible. If accurate dimensions are provided from both system suppliers, the SIPs panels can be cut to fit any size to suit any setup,” says Darren Barnes, partner and head of design at SIPS@Clays.
Some suppliers, such as Oakwrights, manufacture their own high-performance encapsulation systems. These solutions provide outstanding thermal e ciency. If you have a tight budget, you might use less oak and more encapsulation. “With our aisle framed projects, we can achieve the desired effect of oak, while utilising the structural capabilities of our encapsulation systems,” says James Morgan, head of encapsulation design at Oakwrights.
Timber with elements of oak
Oak is widely acknowledged as a premium material – and if your funds won’t stretch to a full oak frame home, there’s another route. “Timber and oak frame is a popular
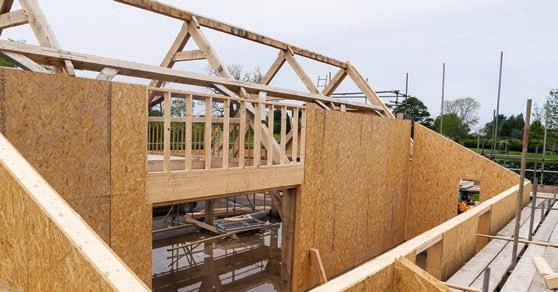
Key Considerations
You might need to work with multiple partners. “With hybrid systems, it’s best to use a single supplier for the entire build,” says Simon. “But if you’re having an ICF basement, for instance, these two elements would have to be designed together but sourced separately.” to waterproof. Other options include offsite manufactured pre-cast concrete panels, in-situ reinforced concrete and blockwork masonry. In all cases, you can combine their benefits for below-ground construction with the advantages of timber for the aboveground storeys. “This enables you to get the benefits of both they really complement each other in this situation,” says Simon. hybrid system,” says Simon. “The two complement each other, offering an ideal solution for self builders keen to build with oak but where the budget doesn’t allow.” You might use panelised timber frame for most of the build, but switch to oak where you want character – such as for feature beams, trusses, porches and sunrooms.
To ensure a successful result, it’s important to bring both companies in at the early design stages, ideally with a single engineer assuming overall responsibility. This way, you’ll be able to develop a plan that factors in the unique characteristics of each system and ensure they function harmoniously. derst d t e di ere ti l m eme t r m m i i di ere t se er l m teri ls t is is ully considered and detailed accordingly, there should be no issues,” says David from Oakwrights.
Building on a basement
A basement will maximise the size of your house on its plot. How this is built depends on site conditions, soil and budget – but fundamentally it needs to be a heavyweight system that can resist ground and water pressure, and can be waterproofed.
For instance, ICF, which is a method using stacks of polystyrene blocks filled with steel reinforcement and concrete, is super-strong and one of the most cost-effective systems
Above: On this project by SIPS@Clays, SIPs panels were used to build up the walling around the oak superstructure
Masonry might also be a contender for areas of your project where thermal e ciency is less important. For instance, a garage won’t need to meet the same standards as your timber frame house.
Timber & steel
As with other construction systems, large or complex timber-built houses often feature steels for design elements that require additional structural support. Metal columns or beams can be engineered into the wood frame to enhance robustness and durability. It might be needed to enable dramatic roof spans, arched structures or large spans of glazed doors. Glulam beams are another option that are very strong.
Steel beams can be hidden within the structure or left exposed to make a bold aesthetic statement (in either case, you’ll need to ensure fire-rated finishes are used . Similarly, bolts, fi ings and joints can be left on show – this looks great in oak frames.
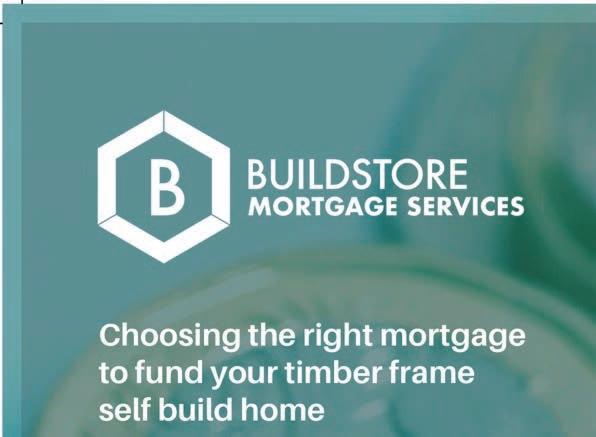
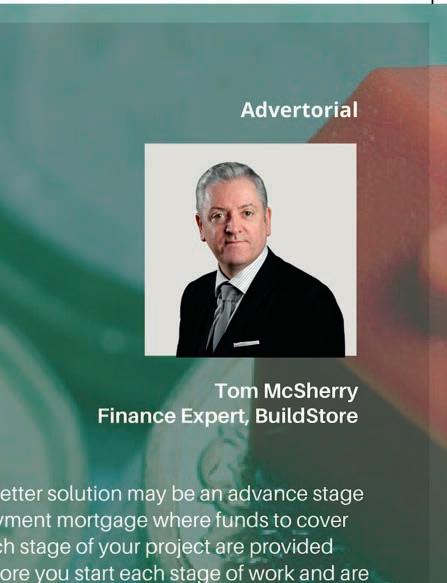
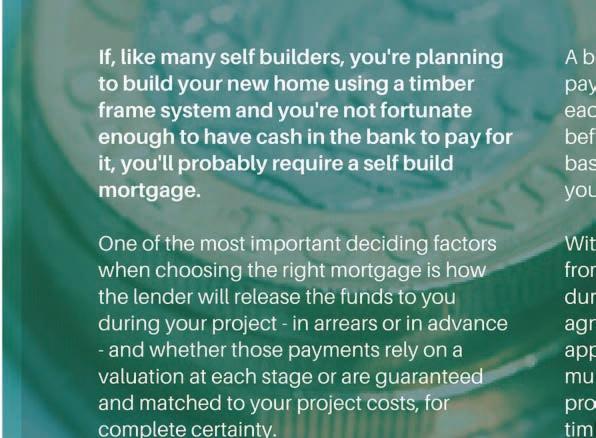
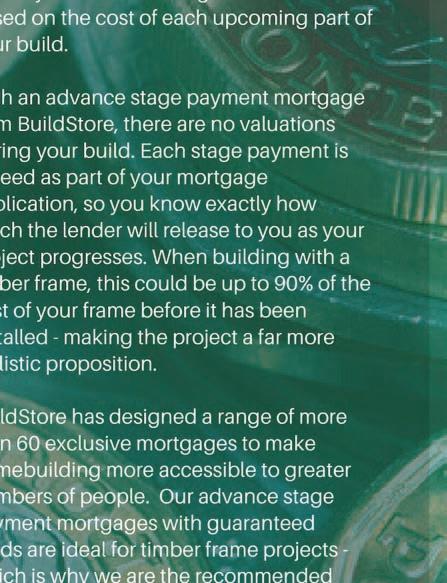
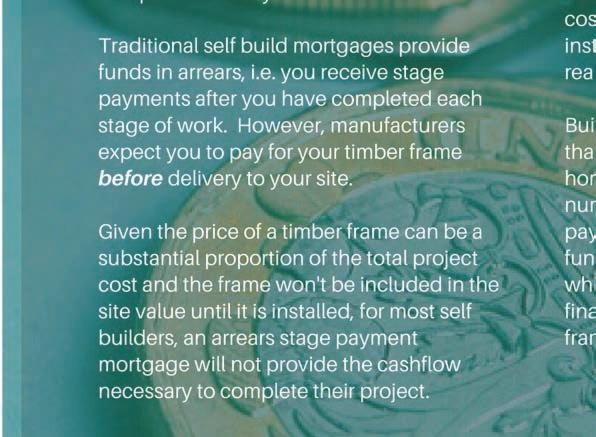

Using a structural timber supplier that is backed by STA Assure accreditation will give you reassurance
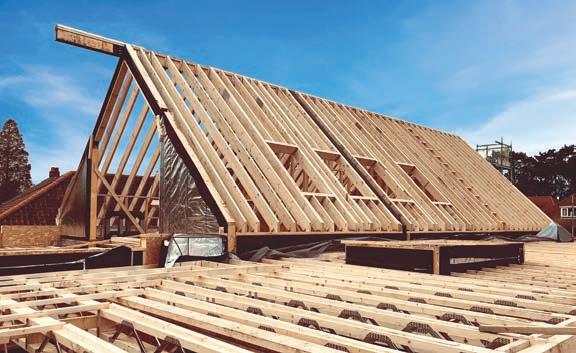