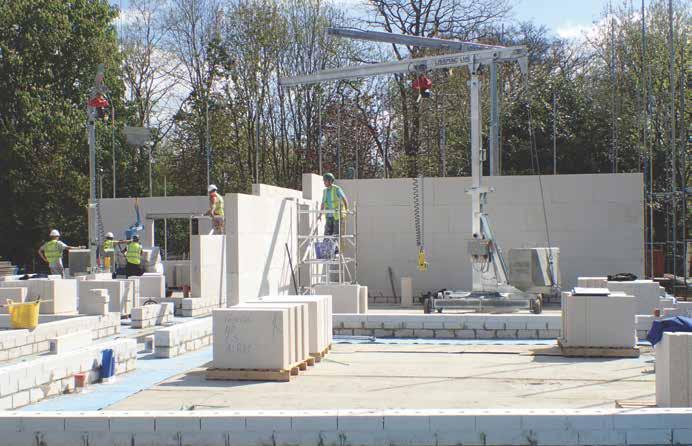
4 minute read
A Solid Platform for Construction
The award-winning MFS i-Form Solution™ is helping drive forward the concept of P-DfMA for offsite manufacture and building design.
The Masonry Frame Systems (MFS) team have formulated an offsite construction rationale, which has been trademarked as the MFS i-Form Solution™. This combines large scale calcium silicate elements and precast concrete components with an offsite methodology to drive forward a suite of 'platforms', or standardised and repeatable offsite components. This enables the delivery of a bespoke solution to the client's needs, in terms of building function and site demands.
The MFS i-Form Solution™ was trademarked in 2020 and is a highly engineered construction process, best described as a platform for design, manufacture and assembly (P-DfMA) approach. Platforms – this is a tried and tested suite of construction components – or standardised and repeatable platforms Design – digitally designed in BIM to enable highly efficient construction and high-performance buildings for end users – without any compromise to the architect’s vision
Manufacture – over 90% of all components are manufactured offsite, using methods that minimise the reliance on cement in the precast concrete components Assembly – delivered as a complete kit of parts for easy, swift and costeffective onsite assembly, with 80% less labour and up to 200% faster than traditional build.
1
Masonry Frame Systems are a specialist frame contractor with the i-Form Solution™ applied to everything that they design, manufacture and assemble and see the construction industry as a “low volume, high variety” industry with pretty much every project unique or bespoke to its environment or surroundings. One of the big advantages of the system is that it can be tailored to each project, specifically. The i-Form Solution™ is a masonry and precast concrete solution, combining the benefits of a suite of standardised calcium silicate or concrete components that can flex to bespoke designs, with all the cost, time and sustainability benefits of a volumetric or modular construction.
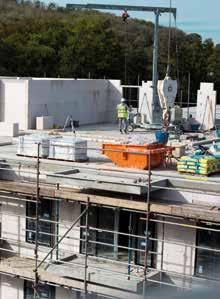
2
The MFS i-Form the combines Xella elements with precast concrete, such as floor planks, staircases and balconies, where we pre-stressed Hollowcore technology is used, which maximises strength, but minimises the need for cement. So, the system makes the most of concrete technology to achieve the highest technical achievements but with sustainability and the environment as primary drivers. Core to the i-Form Solution™ is offsite manufacture and sustainability. By constructing the whole structural envelope of a building, from ‘oversight to weathertight’, using offsite methodology savings of time and money can be delivered (typically 20% saving on the overall build programme) for clients and provide a high-performance solution.
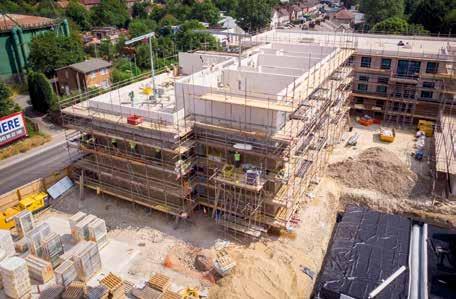
3
For more information visit:
www.masonryframesystems.co.uk
Images:
01-03. The MFS i-Form Solution™ is bringing a new dimension to offsite concrete technology
P-DFMA – THE SERIOUS APPROACH
Anne Daw, Associate and Head of MMC Delivery at HLM Architects on a few reasons why the Platform approach to Design for Manufacture and Assembly (P-DfMA) can deliver ambitious construction targets.
“Platforms can accelerate industry transformation by boosting quality, speed, outcomes and performance. The Product Platform Rulebook is a very positive step forward. It outlines a set of open-access rules and principles to create a common set of standards and processes for the industry to collectively develop product platforms and drive efficiencies, as well as societal and environmental benefits. It mandates that platforms must be deployable, configurable, and open – comprising repeatable, standardised assets with interoperable components.
“By harmonising repeatable features into a ‘kit of parts’ accessible to all, organisations can share knowledge, components and processes across a wide range of solutions and sectors, bringing economies of scale. This approach replicates what we’ve seen in other industries, such as aerospace and manufacturing, and can work to overcome challenges in the fragmented construction industry including lack of standardisation, productivity, quality and predictability. The platform approach will not only optimise the fabrication and installation elements of construction but will also free up architects to be creative and focus on designing high-quality projects tailored to specific needs while automatically meeting all technical, sector-specific requirements.
What the Product Platform Rulebook delivers is a set of common guidelines to bring clarity on how platforms can be successfully adopted at scale. Platforms can bring significant advantages, such as improved cost efficiencies through standardisation of solutions, faster delivery of projects, and safer conditions for workers on-site. They can also reduce the huge waste seen in the construction industry, which contributes 11% of all carbon emissions globally. We have no choice but to look at new options and accelerate innovation – it’s the only way for the built environment to reach net zero. Without embracing new models such as the platform approach, we will miss crucial environmental targets.
An industry-wide platform approach significantly streamlines and simplifies the process, with key connections and details decided upfront. The platform approach allows the advantages of MMC, which have been spoken about for years – such as using 67% less energy than traditional construction and being significantly faster – to fully materialise within the wider construction industry.