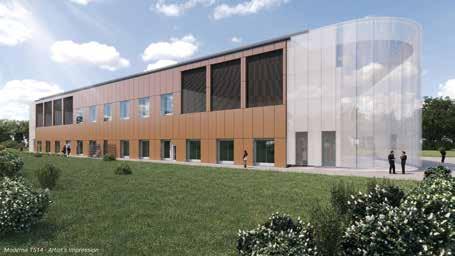
8 minute read
UK INDUSTRY NEWS

L&G Modular Homes Halts New Production
As has been widely reported in the trade press and across the mainstream media, Legal & General has stopped new production at its modular housing factory at Sherburn-in-Elmet, near Leeds with over 450 redundancies expected. The troubled provider blamed ‘long planning delays and weak demand’ for the problems.
Strategic options for the factory include a sale, merger, fundraising from third parties or eventual closure. The company will begin a consultation with employees about redundancies, retaining a number to build modular homes for existing projects in Bristol, Selby and Broadstairs in Kent. L&G’s modular housing business has made slower progress than expected, running up cumulative losses of £176million since it was established in 2016.
The L&G statement read: “Legal & General has announced today that it is proposing to reduce business activity and cease new modular production at its modular housing factory in Selby, Yorkshire, whilst reviewing and assessing potential strategic options for the business. As a start-up business with a significant fixed cost base, a strong and predictable site pipeline is required to make L&G Modular Homes a successful sustainable business.
Construction Commences at Moderna Innovation & Technology Centre
Moderna, Inc. (Nasdaq: MRNA), a biotechnology company pioneering messenger RNA (mRNA) therapeutics and vaccines, has commenced construction of its Moderna Innovation and Technology Centre (MITC) in Harwell, Oxfordshire. The MITC will encompass research, development and a manufacturing facility, which aims to provide the UK public with access to mRNA vaccines for a wide range of respiratory diseases, pending independent regulatory assessment and licensure.
The Moderna investment will create hundreds of jobs during construction and operation. The MITC will include a clinical biomarker laboratory that will be constructed by the offsite construction and engineering specialist Merit. The Drug Substance and Manufacturing facility will be fitted out by Birmingham-based engineering firm IPS and is expected to become operational in 2025.
Darius Hughes, UK General Manager at Moderna, said: “We are delighted to celebrate this important milestone today alongside our partners from the UK Government and Harwell. We look forward to continuing our collaboration throughout construction of the Moderna Innovation and Technology Centre,
“However, a number of factors, including long planning delays and the impact of recent macro events such as Covid, have meant the business has not been able to secure the necessary scale of pipeline to make the current model work. Without this pipeline, it has not proved possible to build a business that can sustain the significant running costs of the large factory in Selby. As a result, Legal & General is also commencing consultation with all employees around the proposal to make the majority of modular homes roles redundant. The business will be doing all that it can to support employees during this difficult time and will be actively exploring opportunities for redeployment.”
Bill Hughes, Chair of the L&G Modular Homes board added: “Legal & General is proud of what we have achieved in bringing forward a new approach to construction through our factory. However, without the necessary scale of pipeline it is not sustainable to continue producing more modules. We are therefore reluctantly proposing to reduce business activity and cease production of new modules at the factory. We recognise this will be a challenging and uncertain period for staff and we will be actively exploring redeployment opportunities.”
Source: www.legalandgeneral.com and beyond, to bring innovative vaccines to the UK public to help protect against emerging respiratory health threats.”
A groundbreaking ceremony was attended by Health Minister Maria Caulfield, CEO of the UK Health Security Agency Dame Jenny Harries, local community leaders and representatives from the UK’s health resilience and life sciences community.
Health Minister Maria Caulfield, said: “Thanks to this partnership between the government and Moderna, NHS patients across the country will have access to cutting edge mRNA vaccines to fight future Covid variants and other respiratory viruses, so it’s great to see construction starting on this new centre.”
Professor Dame Jenny Harries, chief executive of the UK Health Security Agency, said: “This facility will significantly strengthen the UK’s vaccine development and research capabilities, helping shore up our defences against future health threats, including pandemics. Once built, it will be capable of producing millions of vaccines against respiratory diseases and other illnesses, placing the UK at the global forefront of health science and innovation.
Source: www.merit.co.uk uk.westfraser.com
Our UK-made net carbon negative sheet materials are the number one choice in the construction, furniture and DIY sectors.
M-AR’s Growth Recognised in Yorkshire Fastest 50 Awards
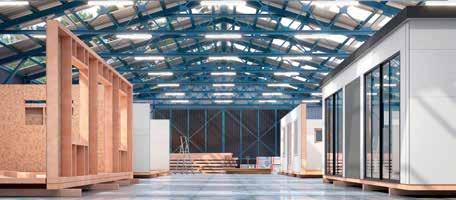
Specialist offsite contractor M-AR has been named as one of the 50 fastest growing companies in Yorkshire. The prestigious Ward Hadaway Yorkshire Fastest 50 Awards, in association with The Yorkshire Post, celebrate growth, innovation and the commercial achievements of Yorkshire businesses.
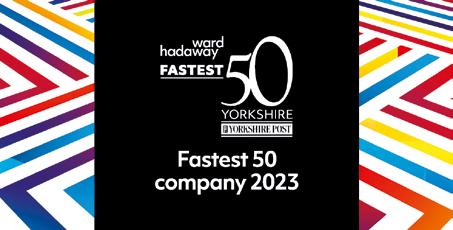
Based on financial data filed with Companies House, the list ranks the fifty best performing independent companies which have consistently increased turnover over the past three financial years, whilst remaining profitable. M-AR was ranked third as a result of its continued and strategic growth which has seen it not just increase turnover but also successfully scale up operations by investing back into its manufacturing facilities. As a result, the company is successfully undertaking projects of larger scope including a recently completed 33 apartment development built in London for the UK’s leading youth homelessness charity, Centrepoint.
Emma Digby, who is Executive Partner at Ward Hadaway's Leeds Office, said, "I’d like to take this opportunity to congratulate M-AR alongside all the companies in the Ward Hadaway Yorkshire Fastest 50 list for 2023 for their outstanding achievements. The companies in the Fastest 50 demonstrate that real, genuine growth is happening.
“Yorkshire businesses are thriving because they’ve not been afraid to go against the grain, take risks or follow their instincts at a time when uncertainty
New MMC Moves by Government
The Department for Levelling Up, Housing and Communities (DLUHC) has embarked on a ‘Modern Methods of Construction (MMC) Standardisation Research and Kit of Parts’ project to develop an open-source kit of parts that will encourage the uptake of MMC.
Following through on commitments set out within the Transforming Infrastructure Performance Roadmap to 2030 and Construction Playbook, the project represents a key step by government to translate policy into practice. Akerlof, a specialist MMC consultancy, has been appointed by DLUHC through competitive tender to lead a consortium of partners, including Buro Happold, HLM Architects and Limberger Associates, that will collectively undertake research and engagement to help shape a strategy that uses standard parts.
The focus of the project will be on MMC Categories 2 (2D primary structural systems) and 5 (nonstructural assemblies and sub-assemblies). Extensive is the norm. They’ve been brave, they’ve been bold and, as a result, rewarded through continued growth. This year’s Fastest 50 list, as always, boasts many management teams with an unwavering passion to succeed who have created high growth, profitable businesses. It’s this spirit, and the business success that it creates, that we are delighted to celebrate."
Ryan Geldard, Director at M-AR added: “It’s a real honour to be named as one of the fastest growing businesses in Yorkshire this year alongside 49 other incredible Yorkshire companies. We set ourselves a mission just a few short years ago to increase the size of our operations here at M-AR so that we could take on larger projects, but more importantly to carve out a place for ourselves so that we could continue to champion the benefits of offsite construction to the wider industry. I think this award recognises the fact that we’re well on our way to achieving our goal and with our passionate and dedicated team at the helm there is more to come from M-AR so watch this space!”
M-AR recently strengthened its core leadership team with a trio of new department heads appointed to co-ordinate both the offsite manufacture and on-site construction elements of projects for greater efficiency.
In the last six months, Ryan Guest, Steve Tate and Keith Hill have been appointed as Head of Commercial, Head of Manufacturing, and Head of Construction respectively. Together they also form part of M-AR’s newly created Senior Leadership Team where they’ll work alongside John Leitch (Preconstruction), Dan Lowther (Procurement), Robert Cousins (Design) and Charlotte Smith (Finance) to engage in open multi-departmental conversations intended to drive innovation and foster a mindset of collaboration and a ‘one team’ culture.
Source: www.m-ar.co.uk consultation with the wider industry and supply chain will ensure the solutions reflect the requirements of the sector and unlock growth within the MMC market. Commenting on the project, Housing Minister, Rachel Maclean MP, said: “Delivering more, better quality and greener homes is central to our levelling up mission. I encourage all industry partners to engage in this research which will harness the benefits of modern methods of construction, drive up productivity in the sector and help deliver the high-quality homes this country needs.”
Jamie Hillier, Partner at Akerlof added: “Akerlof is delighted to be working with the Department for Levelling Up, Housing and Communities, our consortium partners and the wider industry on this exciting project which will accelerate the move towards MMC within the housing sector. As a business we are committed to driving transformation that leads to a better built environment. We hope that this project will demonstrate the benefits of using common parts to create greater choice across housing and set the direction of travel for the sector.”
Source: www.akerlof.co.uk

Mulberry Homes Goes MMC
Mulberry Homes has made its first foray into the world of modern methods of construction (MMC) with a hybrid approach that combines an offsite roofing solution with traditional brick-and-mortar builds. A collaboration with Roofspace Solutions will see 37 i-Roof™️ units installed at a new residential development in Rugby – Mulberry Homes at Houlton – which will comprise two, three, four and five-bedroom homes.
Mulberry Homes’ ambition to modernise and increase the efficiencies of its build program led them to approach Roofspace Solutions, which has been pioneering MMC housebuilding systems as part of the Saint-Gobain Off-Site Solutions division. The i-Roof is a room-in-roof solution for 2.5-storey homes and was selected to be the first solution trialled across the Houlton site thanks to its ability to save time, minimise waste, reduce reliance on on-site labour and provide cost certainty.
Manufactured at Roofspace Solutions’ specialist manufacturing site in Alcester, the i-Roof system helps accelerate construction by reducing the roof element to a one-day install and providing the developer with enhanced preliminary savings. When built traditionally, the roof element can often take up to seven weeks –a timeline which can slip further with labour shortages or bad weather.

With most of the build taking place in a controlled factory setting, this reduces risk to workers on-site. For example, the danger of unsupported blockwork and gables collapsing in adverse weather conditions is replaced with a secure timber-engineered solution which works alongside traditional build methods. The factory environment also adds a layer of additional quality control, with inspections and audits ensuring that the MMC components are compliant with all regulations and standards.
Further time savings are achieved during installation as the system is delivered to the site ready for assembly. This also improves the development’s sustainability credentials, as it negates the need for multiple deliveries and minimises on-site waste.
Simon Yates, Business Development Manager at Roofspace Solutions, said: “i-Roof is an ideal MMC solution for property developers as it accelerates the room in the roof construction considerably, allowing the developers to deliver quality homes faster. Our goal is to make life better on-site by taking things off-site, and that includes managing the process from factory to installation. Doing it this way reduces carbon emissions and waste, while also increasing the speed of the project and the standards of on-site health and safety.”
David Morris, Associate Commercial Director at Mulberry Homes, said: “We’re working to strengthen our vision for the future of housebuilding. Working with the Roofspace Solutions team was a pleasure. They’ve shown us how MMC brings consistency to the build pattern and the manufacturing methods. It is also clear that they put health and safety first. The UK has a desperate shortage of housing, so anything that speeds up delivery is important. We saw how i-Roof could increase the quality of our homes and help us to build them faster, we knew we wanted to work together. I’m confident that MMC will become a common sight on Mulberry Homes’ developments in the future.”
Source: www.roofspacesolutions.co.uk