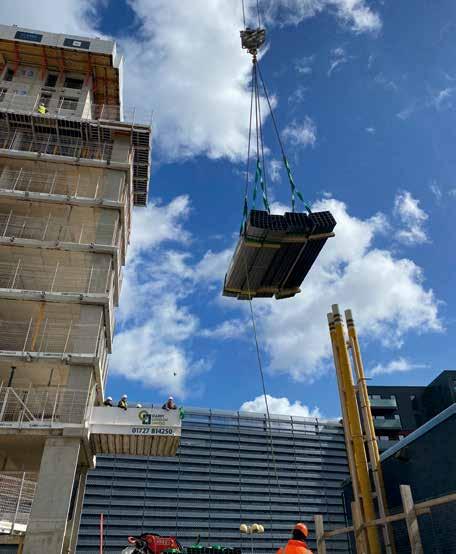
4 minute read
STEEL SUPERIOR PERFORMANCE BENEFITS
Mike Fairey, Managing Director of Fusion Steel Framing, outlines why FusionTRAX TM – a new non-load-bearing infill walling system – is set to boost the offsite marketplace.
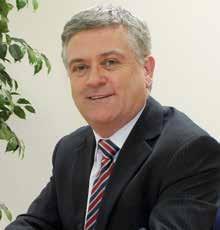
Fusion Steel Framing has a clear mission to improve the entire building process through more efficient supply chain solutions that integrate highquality offsite manufacturing with onsite processes. Products like FusionXTM, our load-bearing external walling system, continue to help reshape the construction process for a range of our developer and contractor clients.
The past month has seen the roll-out of another product which we believe will bring significant programme and performance benefits to the construction industry. FusionTRAXTM is a non-load-bearing infill walling system designed for concrete or steel mainframes, and capable of supporting a wide range of cladding systems.
One of the key advantages of FusionTRAXTM is that it can be custom-designed to fit any project specification. We have a team of experienced designers who work closely with the client to ensure that the FusionTRAXTM system meets their specific requirements. Once the design is finalised, we rollform the steel components in our own factory using advanced CAD/CAM technology to ensure a high level of precision and consistency.
We then deliver and install the FusionTRAXTM system on-site, taking full responsibility for the project. By serving as a ‘one-stop-shop’ for our clients in this regard, we can simplify the construction process and vastly reduce the risk of errors and delays. This can rapidly accelerate construction projects while de-risking the process of installing an infill system, which is so often a crucial element of any new development.
In terms of its application, the FusionTRAXTM system is designed for use in residential buildings such as apartments, hotels, and student accommodations. It can also be used for care buildings like hospitals, care homes, extra care facilities, and retirement living, as well as educational buildings like schools, colleges, and universities. Installation of FusionTRAXTM is straightforward and the product can be assembled on-site by our experienced team.
The FusionTRAXTM system consists of lipped ‘C’ shaped studs and plain ‘U’ shaped channels as base tracks, head tracks, and intermediate noggins, all designed to resist the projectspecific loads required. FusionTRAXTM is typically supported at the edge of the concrete floor slab or on top of the perimeter Hot Rolled Steel (HRS) beams. We use a deflection head detail at the top of each panel/ stud and secure it to the underside of the floor slab or HRS beam above, allowing for vertical movement (deflection) to the floor above, without impacting the finishes applied to the external façade.
Beyond simplifying the construction process, another major advantage of FusionTRAXTM is its ability to provide a high level of thermal and acoustic insulation. The system is designed to minimize thermal bridging, ensuring that projects are well-insulated and energy efficient. Using FusionTRAXTM can also help our clients achieve their sustainability targets as the steel framing is 100% recyclable and can be repurposed at the end of its lifespan, reducing the amount of waste that ends up in landfills.
Additionally, because FusionTRAXTM is fabricated offsite, it reduces the amount of on-site waste generated during the construction process. FusionTRAXTM is also a highly durable and long-lasting system. The steel is resistant to corrosion and manufactured to the highest standard of building regulations, ensuring that a completed project retains low maintenance costs and maintains its value over time. In providing a complete service, we can also provide FusionTRAXTM on a supply-only or supply-and-install basis, making it a flexible option for developers, contractors, sub-contractors, or any other parties seeking a reliable Steel Framing System (SFS).
A forthcoming project where we are excited to see the benefits of FusionTRAXTM in action is Kew Bridge Rise, the redevelopment of the former Citroen garage in Brentford by The Hill Group and L&Q. Fusion Steel Framing has been working closely with the production team on opportunities to improve performance with our offsite solutions.
At Kew Bridge Rise, we will use over 10,000 sqm of FusionTRAXTM across the whole project. The development will have a concrete frame structure and FusionTRAXTM will be used for the infill between floors, sitting on the floor slab up to the ceiling. In addition, we will create the window apertures, install EDPMs, breather membranes, external insulation, and wall tie channels thus providing a complete solution for the project. The scheme is an extensive regeneration project for West London, delivering 441 new homes, and so it promises to be a great example of the capabilities of delivering prefabricated SFS at scale.
Working with The Hill Group has brought us far closer to the development process and increased our understanding of customer needs, as well as the role that Fusion can play in improving construction programmes and delivery. The FusionTRAXTM product is a great example of how we can help our clients improve their processes. It is custom designed, fabricated offsite, and installed entirely by Fusion as a single provider, simplifying the construction supply chain and reducing the risk of errors and delays.
We aim to be the partner of choice for developers and contractors seeking to benefit from light steel framing solutions. Our expert team is always happy to engage with new clients, project teams and interested parties who want to learn more about our innovative product range. With the roll out of FusionTRAXTM, now is the ideal time to speak to us about the solutions we can offer.
Offsite manufacturing has come a long way in recent years, and I am proud that Fusion remains at the forefront of this exciting sector. Since 2000 we have delivered more light steel residential structures than any other European producer, and we have worked alongside a host of prestigious developers and contractors. Our approach is one of collaboration, working closely with our clients to find efficiencies that will simplify their construction projects. This outlook has led to Fusion advising a range of government and industry bodies, and our doors are always open to new conversations with clients, developers, contractors, and industry professionals.
For more information visit: www.fusionsteelframing.co.uk
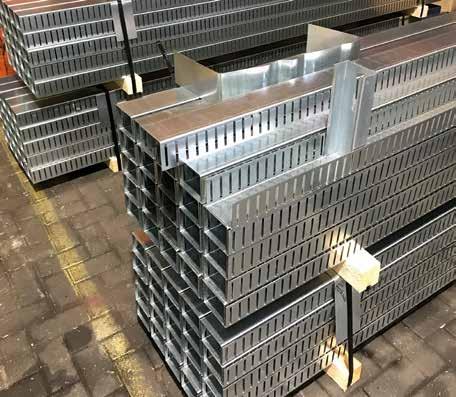
Images:
01. Mike Fairey, Managing Director, Fusion Steel Framing
02. Fusion TRAX system being loaded at Kew Bridge Rise
03. Fusion TRAX is fabricated offsite and reduces the amount of on-site waste dramatically