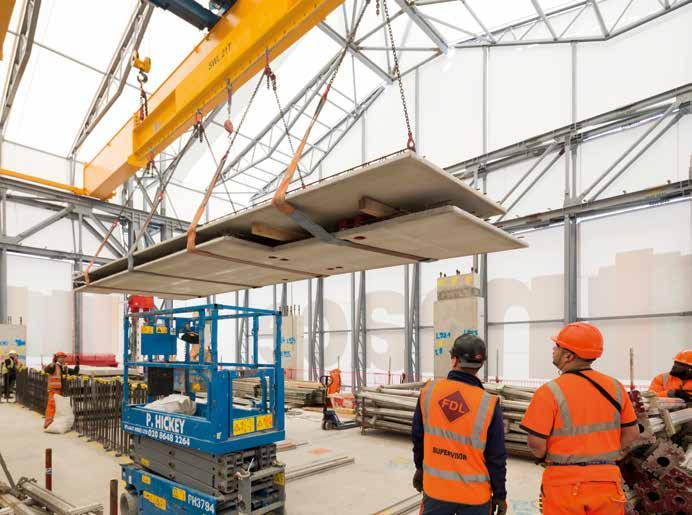
6 minute read
MEANINGFUL CONSTRUCTION CHANGE 1 2
There have been many critiques of the construction industry, which collectively paint a picture of an inefficient and wasteful industry that, at its worst, is harmful to its workforce, its neighbours and the environment. Readers of this magazine will no doubt have their own ideas about the numerous benefits offsite solutions can offer, but might offsite be able to improve the industry’s Environmental, Social and Governance responsibilities (ESG)?
ESG refers to the: “principles of environmental, social, and governance responsibility as they relate to the firm’s society relationships.” So Environmental governance might include policies aimed at protecting the environment from damage caused by firms’ activities. Social governance might refer to the means of improving relations with stakeholders. Corporate governance could be thought of as creating trust among stakeholders, such as employees, consumers, suppliers, and communities near where the construction activities are to take place. In short, companies’ ESG policies demonstrate the opportunities they’ve created to address the climate crisis and enhance the environment we all live in, whilst at the same time improving working and living conditions.
The drivers for establishing ESG policies are numerous, but perhaps one of the most significant is the availability of finance – a strong ESG profile can help attract investment since two-thirds of investors take ESG into account when making an investment decision.
The SCSS has produced two reports in the last year, both authored by my colleague Naomi Pratt, and both of which are relevant to ESG policies; the first is entitled ‘Delivering Social Value Through Offsite Construction’ and the second ‘Whole Life Carbon Guidance for Offsite Construction’.
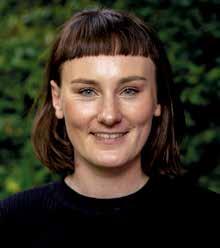
The first report explores the tension between trying to deliver social value locally, whilst simultaneously taking work away from the locale in which the construction site is located to remote factories. This tension arises from client requirements stipulating social value outcomes to be within a set proximity of the site and it cannot be ignored: for example, in the public sector PPN06/20 requires a mandatory 10% weighting on the social value accruing from the award of a contract. Therefore, the challenge for offsite construction, where the pre-manufactured value (PMV) of components and modules is much higher, is that the traditional benefits of local job creation and local spend may be harder to achieve.
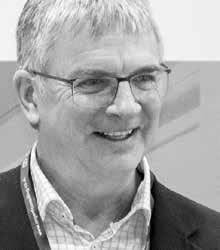
Of course, offsite creates significant local value in the areas where factories are located, but these are likely to be remote from the construction site. The report recognises, however, that significant benefits nevertheless still can be achieved locally to the site, for example through improved workplace wellbeing and air quality, and reduced carbon, nuisance and waste.
Also, offsite does not wholly negate the need for traditional trades. For example, during the ‘Enabling Housing Innovation for Inclusive Growth’ programme, SNUG Homes found suitable roles for trainees, residents, local subcontractors and the core team through trialling and refining allocation of construction tasks. Furthermore, depending on the design, jobs requiring less formal training can still be created local to the site, helping to empower community builds or bringing new entrants into the sector.
Meanwhile, the opportunities that arise in factories include benefits such as long-term engagements with education providers, creating opportunities for work experience and apprenticeships, not to mention improved work conditions, the potential for shift work (which can attract a more diverse workforce) and improved Health and Safety. All these elements can improve a firm’s talent pipeline and recruitment opportunities, and through enhancing a firm’s reputation and brand, it can support bid winning.
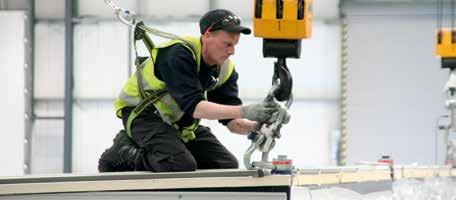
The second report, ‘Whole Life Carbon Guidance for Offsite Construction’ (see box out) acknowledges that the buildings and infrastructure that we build and operate are significant contributors to the climate emergency, with direct control over 25% and influence over 42% of the total carbon footprint of the UK. It identifies significant opportunities by which the offsite sector can help drive decarbonisation in construction projects, both new build and in the retrofitting of existing assets.
Significantly, though, the report highlights some specific features of offsite projects which may result in increases in embodied carbon.
For example, some elements may contain superfluous material mass for their specific use due to a standardised rather than tailored approach – also, in volumetric modular construction there are examples of additional structural elements being incorporated to enable the transporting and lifting of units, neither of which would be necessary in traditional construction solutions. The report recommends that project teams should consider these and work to offset these drawbacks by finding savings elsewhere.
On a more positive note, there are numerous ways in which the whole delivery team can drive out waste and reduce carbon. These include designing out waste, improving processes (made possible once work is moved to factories), decarbonising factories and using innovative low-carbon materials. During the construction stage, offsite can deliver shorter contract periods, which reduces energy consumption on-site, as well as reduced vehicle movements. Also, by considering the maintenance and any re-use opportunities at the outset, we maximise the asset lifespan and the higher quality manufacturing processes – compared to traditional construction – should result in better in-use energy performance.
Images:
01. David Emery, Consultant, Supply Chain Sustainability School
02. Naomi Pratt, lead author of the report ‘Whole Life Carbon Guidance for Offsite Construction’
03-05. The new report highlights opportunities and challenges for carbon management and reduction for the offsite sector
Nine Ways To Drive Down Carbon
A new report, published by the Supply Chain Sustainability School, reveals that nine significant opportunities exist for offsite manufacturers to help their clients in their drive for low carbon construction projects, both newbuild and in the retrofitting of existing buildings.
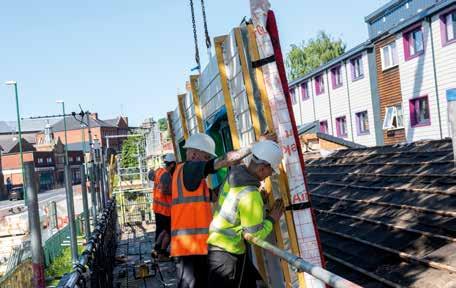
Drawing on the experience of more than 40 organisations working across homes, commercial, public and infrastructure, the new report, ‘Whole Life Carbon Guidance for Offsite Construction’ highlights opportunities and challenges for carbon management and reduction for the offsite sector.
The built environment industry needs to rapidly decarbonise existing and new buildings, as well as reduce embodied carbon produced in production of building materials and elements, construction, and maintenance of assets. The ability of offsite construction processes to reduce whole life carbon is often expressed, but evidence of this has been patchy.
This includes common benefits around the material and resource efficiency of premanufacture, reduced fuel and energy use in logistics and on-site, as well as greater confidence in operational energy performance with standardised designs. Some of the strongest evidence for carbon reductions exist in energy and fuel use for transport and construction processes, with studies finding savings of 30-40%, even when factory energy use is included. However, most of the embodied carbon within construction projects comes from materials and manufacturing: the product stage.
The report proposes that there is a big opportunity for Design for Manufacture and Assembly (DfMA) to drive emissions savings in this stage, sharing evidence for this across homes, schools, and commercial projects. It recommends early collaboration between manufacturers and design teams in order to fully realise low carbon design options. This collaboration will also aid robust whole life carbon estimates, which are likely to become mandatory in the coming years. The report also encourages manufacturers and contractors to embed processes for the collection and communication of activity data.
Andrew Shepherd, Managing Director at TopHat Communities, said: “We all know carbon is a problem, but without knowing how much of a problem, it is very difficult for us to start addressing some of the key problem areas. This report provides guidance on how to start assessing whole life carbon and understanding the impact each stage of the development cycle has on the environment about us.”
Naomi Pratt, lead author of the report and Consultant at Action Sustainability, said: “It’s been really encouraging to see projects cutting embodied carbon through offsite techniques. What these have in common is a design approach driven by material and carbon efficiency. What we need to see now is more organisations adopting this focus and sharing data.”
Ian Heptonstall, Director of Supply Chain Sustainability School, added: “The good news from this report is that yes, offsite and MMC can help us tackle the climate emergency. However, as the evidence suggests, we are currently missing many opportunities and it’s clear as an industry we need to think and act differently. My challenge to those not at the forefront of tackling carbon is: will you act now and make a difference, or be left behind whilst your customers transition to a low carbon economy?”
The examples of best practice highlighted in the report are crucial for whole life carbon reduction and the journey to net zero. The authors encourage organisations working within the sector to show leadership, take advantage of the opportunities, and share data and experiences.
For more information and to download the report visit: www.supplychainschool.co.uk