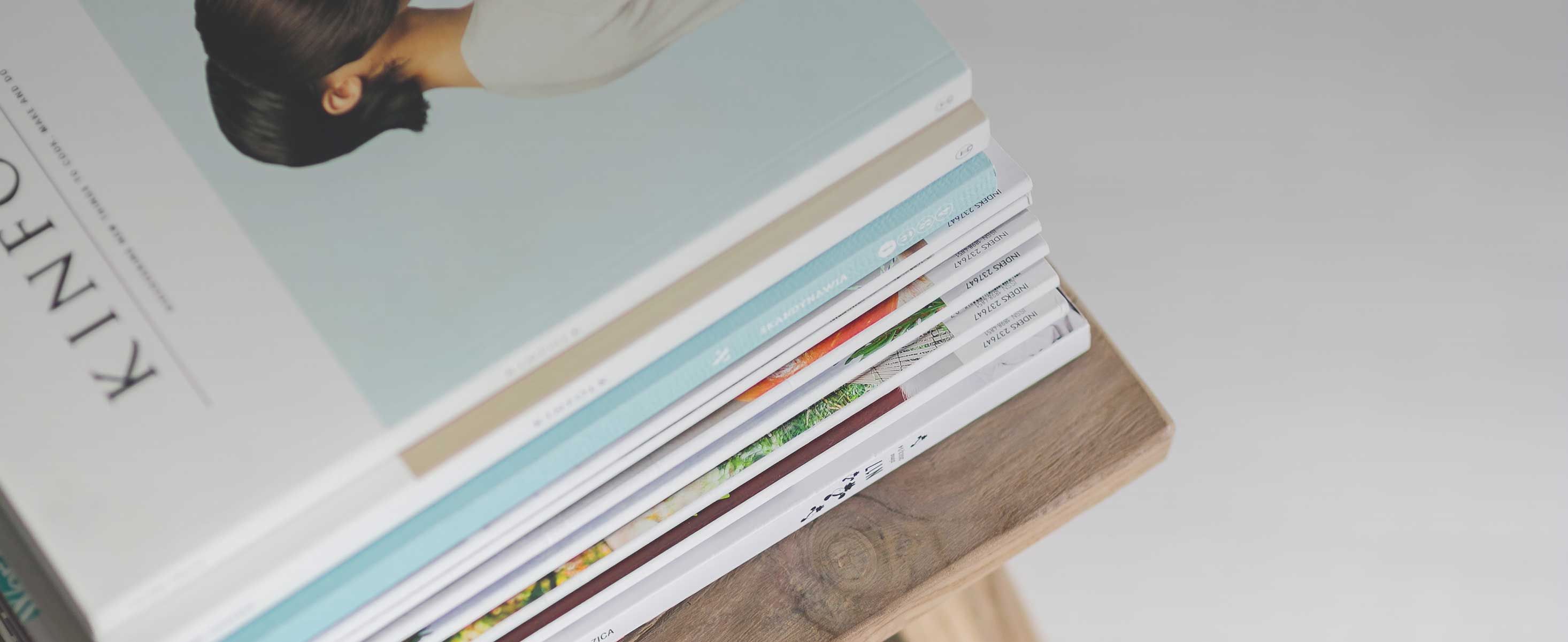
3 minute read
UK INDUSTRY NEWS Horizon Factory Ready for Operations
British Offsite, the build offsite company of Weston Group plc, has launched ‘Horizon’, a new £45million, 137,000sq ft facility in Braintree, designed in collaboration with Swedish robotic engineering firm Randek AB.
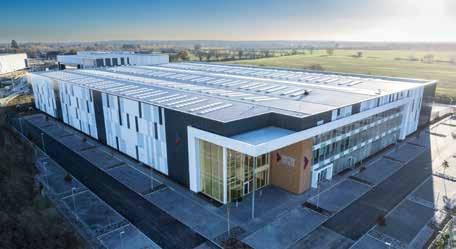
Once fully operational, the new factory in the Horizon Business Park will be able to assist with the delivery of up to 4,000 new homes per year, with building components provided to both Weston Homes, the Group’s volume housebuilding division, and also sold on the open market to builders and contractors, including local and regional housebuilders.
The Horizon factory will produce British Offsite’s panellised UniSystem range that includes light gauge panels, walls, roofs and floors, with the panels having windows, doors, insulation, vents, fire stopping and external cladding in place, manufactured exactly to a developer’s needs. The UniSystem is a specially developed hybrid MMC that is highly flexible and allows rapid integration into traditional building design.
The initial design concepts and commissioning of technology for the factory started three years ago, with the actual construction of the building taking 12 months. The completed factory has a glass and Trimco-panels façade with solar panels on the roof to help ensure sustainability and maximum power generation, with special energy monitoring systems to review factory production capacity.
Donaldson Timber Systems Launch New House Range
Leading UK offsite timber frame manufacturer, Donaldson Timber Systems (DTS), has launched the Donaldson Timber Systems House Range. The range of 18 core house types includes cottage flats with a mix of one and two bedrooms, semi-detached and detached two-bed bungalows and a selection of detached, semi-detached, and terraced homes of two, three and four bedrooms.
Utilising DTS’ Sigma II closed panel timber frame system, the house range provides long-term energy efficiency; meets and exceeds Homes England’s minimum requirement for a pre-manufactured Value (PMV) of 55% using only the timber frame build system and allows the frames to be windproof and watertight on site in one day. The homes are also land-efficient, with the width of each floorplan reduced to ensure roads, footpaths and services are minimised, and a consistent depth of floorplan allows different house types to be simply built as terraced blocks.
Underlining the ambitions of the factory, each of the robots is named after UK cities: Edinburgh (robot 1), Cardiff (2), Belfast (3), London (4), Manchester (5), Liverpool (6), York (7) and Cambridge (8). The production line delivery is not limited to housebuilding and has the capacity for doing modular school buildings, healthcare facilities and student accommodation. Alongside the triple-height main factory floorspace containing the production line, there are a 1,860sq m office, R&D suite, marketing and staff welfare facilities including a canteen and health-screening clinic.
Bob Weston, Chairman of British Offsite & Weston Group said: “Working with Randek AB, the launch of the ‘Horizon’ factory has created one of the most automated light gauge steel panel assembly lines in Europe and the largest single production line in the UK. Offsite construction is the future of the housebuilding industry and homes manufactured at ‘Horizon’ can be tailored to a development’s unique design vision.”
Shaun Weston, Managing Director of British Offsite added: “British Offsite is proud to be part of the new wave of high-tech British manufacturing, bringing very significant new capabilities to the UK construction industry. The new robotic production line at ‘Horizon’ allows for the consolidation of the work of up to five trades into one panel. Our MMC products are designed to be easily integrated into existing projects, helping to streamline traditional residential construction.”
Source: www.britishoffsite.com
John Smith, Technical Director at DTS, said: “We are working closely with the wider housing sector to drive continued quality and performance standards, and our new house range provides both to the market. We conducted extensive research in the sector across the UK to understand the needs of residents, developers, planners, and all relevant regulations, and these house types provide homes that are designed to offer maximum flexibility while meeting all space standards in the most efficient way possible.
“Sustainability and efficiency are also key to the sector, both for speed of build and longer-term performance for residents. Our timber frame system’s fabric-first approach comes with embodied carbon calculations and PMV assessment for each house type, to ensure sustainable, resilient, and affordable homes that efficiently meet the current build regulations and can be easily and simply updated to achieve the requirements of the Future Homes Standard.”
The house range is supported by a suite of architectural design information with Level 1 BIM models. DTS is also developing further supporting information, including SAP calcs, specifications, schedules and build costs for the full house range. Having this information in place will not only allow customers to reap the benefits of the efficiency of the house types, but vastly reduce the lead-times and up-front costs associated with developing a range of house types from scratch.
Source: www.donaldsontimbersystems.com