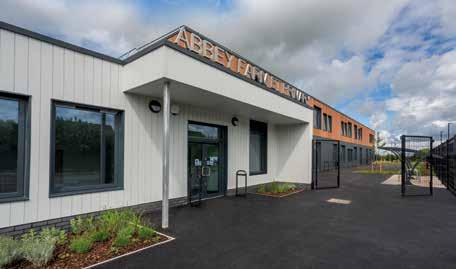
7 minute read
Reds10 Full Year Results Outperform Market
Vertically integrated offsite construction specialist Reds10 announces its annual results for the year ended 31 March 2023, delivering another strong financial performance, recording a third consecutive year of turnover and profit growth and significantly strengthening its balance sheet. The strong performance has been delivered by harnessing a platform approach and through considerable investment in customer relationships and customerfocused product development.
Highlights reported included: revenue up by 32% year on year to £83.8million (£63.4million in 21/22: £37million in 20/21, seeing a 126% total increase over three-year period, a robust pipeline in place that exceeds future projections – secured revenue (orders and intents) at year end of £272million – with 100% coming from long-term programmes of work, operating profit remained strong and well above industry benchmarks at 6.2%. Further expansion of its manufacturing facility in East Yorkshire, where it secured a fourth factory increased production capacity by 25%.
Matt Bennion, CEO of Reds10, said: “This year has been another period of high performance and achievement as Reds10 continues its consecutive year-on-year growth trajectory, bucking the market trend despite wider challenges. Our strong secured pipeline of work is testament to Reds10’s focus on innovating products that are tailored to meeting customers’ needs, our unique platform approach, vertically integrated delivery, an ongoing commitment to product innovation and in-house design capabilities.
“We have continued to enhance our reputation in the industry as a Tier 1 contractor that consistently delivers innovative building solutions. Our mission is to change the way spaces are designed, built, financed and operated, proving that MMC can deliver better, faster and more sustainably compared to traditional methods.”
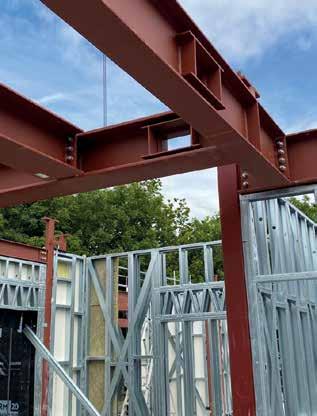
The company commenced £60million of construction work during the period on separate projects for the Ministry of Justice, the Department for Education and the Ministry of Defence. In addition, Reds10 secured positions on a further three value-creating frameworks, for the Crown Commercial Service Offsite Solutions, MMC New Homes and HNS SBS. During the year, Reds10 invested significantly in R&D to develop and deploy new technologies that help to improve end user experience and building quality.
Source: www.reds10.com
Setanta Hand Over Passive House
The keys of Setanta Construction’s SoLow Passive House have been handed over to a family from Mid Ulster who’ve been chosen as the lucky occupants to live for free in the property for twelve months.
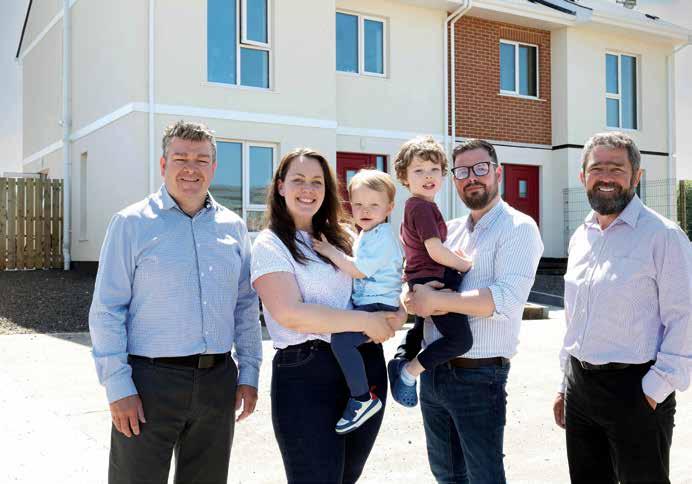
Courtney Gallagher, her husband Michael and their two children were chosen by Setanta Construction following a thorough interview and selection process. Canadian born Courtney and her husband Michael, originally from Castledawson, moved back to Mid Ulster from London last year to be closer to family and friends. In return, the family will participate in a live research monitoring study in collaboration with Ulster University. The research process aims to gather live feedback and data about what it’s like to live in Ireland’s first volumetric modular house constructed to complete Passive House standards.
The unique research will help provide key metrics and insights on the future performance of low energy dwellings, with factors such as internal heat gains, energy usage along with occupant behavior and the subsequent impacts on the overall performance of the SoLow house fully explored.
Crucially, it will also help determine the overall cost savings of living in a SoLow passive designed home, widely regarded by many within the affordable housing industry as a much-needed solution to help minimise the impact of the ongoing cost of living and energy fuel crisis.
Setanta Construction is calling for an integrated approach to help combat energy fuel poverty.
According to Mark Gribbin, Joint Director: “Over the past number of months, we’ve been consulting with housing associations, architects, developers and governmental bodies and they’ve definitely taken notice. Passive House design is still considered by many as an energy standard that only high-end projects could afford. We’re set to alter that thinking by applying complete Passive House standards to affordable housing.
“We’ve been long-term supporters of passive house standards and have been training our staff in Passive House techniques since 2011. This has allowed us to work alongside industry experts and consultants to carefully develop, design and construct a superior housing solution that will result in significant energy fuel savings whilst also delivering additional cost, time, health and environmental benefits for all.”
According to Niall Gribbin, Director at Setanta Construction: “We’re grateful to the Gallagher family for taking part in this unique research study – the first of its kind in Ireland. At the end of the twelve months, information gathered will help feed into future decision making about Passive House construction and the delivery of exceptional affordable housing.”
“The overall success of our SoLow Passive House will be measured in the long-term, through the production of completed houses, their operational efficiency and by the residents who live in them. We’re hopeful that the design decisions we've made combined with the high energy standards and all-round expertise that we’ve applied will result in good quality, life-long homes that will help decrease energy consumption and associated costs for residents making it a smart long-term investment for the housing sector.”
Setanta’s offsite method of construction means that it takes just two weeks to construct a SoLow Passive House in factory and assemble on-site in just a few hours. With plans for a new 30,000sq ft factory underway, Setanta Construction hope to increase productivity to one fully completed house every day.
Pictured L-R Niall Gribbin, the Gallagher family, Mark Gribbin
Source: www.setantaconstruction.com

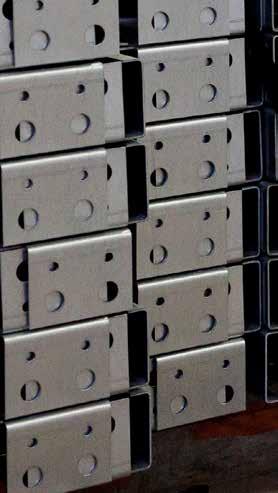
NHBC Accepts Welcomes LoCal Homes and Fusion Steel Framing
NHBC, the UK’s leading warranty and insurance provider for new homes has welcomed two new panelised building systems to NHBC Accepts: LoCal Homes’ ECO200 timber frame and Fusion Steel Framing’s FusionX™ light gauge steel frame.
NHBC Accepts – endorsed by the Government’s Modern Methods of Construction (MMC) Champion Mark Farmer and recognised by Homes England and UK Finance – enables accelerated assessment of innovative systems used in homes covered by NHBC’s Buildmark warranty, reducing the risk of project delays to the builder. Systems with the NHBC Accepts logo have been rigorously assessed and demonstrate, subject to appropriate design and installation, that they meet NHBC’s robust standards, giving confidence to developers, investors, lenders and homeowners.
NHBC Technical Innovation Manager, Chris Hall said: “We know from feedback that once a system is given the NHBC Accepts green light this creates confidence in quality, long-term durability and traceability. We actively assess construction quality both on-site and offsite to verify each system is suitable and acceptable to meet the standards set to obtain our ten-year NHBC Buildmark warranty.
“With demands on the industry to increase the volume of new homes and the simultaneous challenges around materials and skills, we are
Ilke Homes Faces Offsite Exit
The offsite industry has been shaken once again with the collapse of another major player in the housebuilding sector. After the demise of L&G Modular Homes in May, leading modular housebuilder ilke Homes entered administration in July with over 1,000 employees set to be made redundant.
The Flaxby-based company had been looking to further fundraise or seek new buyers with ilke Homes reportedly offering potential buyers the company for £1, to enable it to complete its 4,200-home pipeline and retain its workforce. This did not materialise.
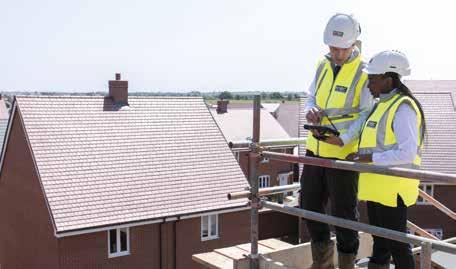
Clare Kennedy, Joint Administrator and a Partner and Managing Director at AlixPartners, said: “This is an incredibly difficult time for all associated with ilke Homes, and in particular its employees, who have worked tirelessly alongside management over recent months to find a resolution.
“With significant incremental investment the business returned to growth following the Covid pandemic, but then faced the challenges of unprecedented inflation and a lack of land supply linked to planning at a critical stage in the development of MMC. We are proud to be using our scale, expertise and knowledge of traditional house building to work with manufacturers to provide the confidence that innovative systems can meet and sometimes exceed the same high standards of quality and durability as traditionally built homes.”
Even once accepted, NHBC’s Innovation team continue to review quality through factory and site inspections and seek feedback from those working with the system on-site. This knowledge is shared with the owners to help continually improve their system.
Lee Cox, Technical Manager at LoCal Homes said: “We are proud to have our ECO200 system acknowledged and approved by NHBC under their NHBC Accepts Certification. We strive to develop our systems in innovative ways to meet the modern requirements and challenges of today’s construction industry. We aim to give our clients reassurance of quality products and that the system design and manufacture meet current regulations and standards.”
Mike Fairey, Managing Director at Fusion Steel Framing added: “We are delighted to receive endorsement from NHBC Accepts for our FusionX™ light gauge steel frame, as it provides the housebuilding industry with the confidence to utilise our high quality, rigorously tested offsite system within the construction of new homes. Also, importantly, homebuyers will have the assurance of purchasing a new home constructed to meet the exacting standards required to achieve a ten-year NHBC Buildmark warranty.”
Source: www.nhbc.co.uk/accepts processes. As a result, despite a strong product and pipeline, the business has not been able to secure the further investment needed to take it forward.
“Regrettably, this means the immediate closure of the manufacturing facility at Flaxby in North Yorkshire and all site activities will cease. As a result of this difficult decision the significant majority of the companies’ 1,150 staff will be made redundant with a small number being retained to assist the administrators in winding up the companies’ affairs.
“Unfortunately, the market and economic headwinds have proven too strong to overcome… our focus now is on helping all stakeholders, employees, suppliers and customers alike, to find the best possible outcome in this undoubtedly difficult time.”
It was only in December 2022 that ilke Homes announced it had raised a record-breaking £100million from new and existing shareholders following successive years of ‘triple-digit’ growth, with the round being led by funds managed by affiliates of Fortress Investment Group LLC a leading global investment manager with approximately $46billion of assets under management. As regular readers will know ilke Homes and its projects have been covered at length since its inception in many issues of Offsite Magazine. The future of the 250,000sq ft factory, its state-of-the art equipment and assets remains to be seen.