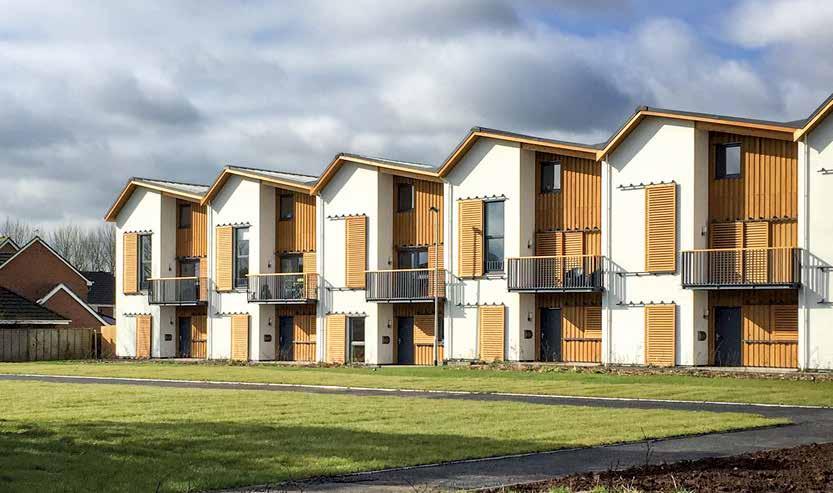
4 minute read
POLICY FOR IMPROVEMENTS
Despite more than a decade of progress, particularly in the creation of a number of ‘product’ housebuilding manufacturers, we are seeing just how challenging it is to disrupt the traditional construction methods and business models for housing delivery in the UK.
We cannot hide from addressing this paradigm – we are facing a future where a declining workforce and the disappearance of contracting capacity in the current economic crisis will create a major structural issue for the future delivery of the homes we now most certainly need. In the big push for rebalancing the UK economy, there continues to be a fundamental failure to invest in the skills we need, and the productivity we must have, to navigate and compete in a growingly complex world.
We can already see, even before the current downturn, that the capacity in the contracting sector struggled to build back from the loss of a huge number of SMEs in the 2008 crash. The sector was additionally tasked with addressing the difficulties and renovation activities that followed from the Grenfell tragedy. More recently a condensation and mould ‘crisis’ and push for sustainable renovation has meant that public sector has oriented away from demand for contractors in the newbuild sector, towards those who can undertake large scale refurbishment projects. This is adding an existential challenge to supply chain capacity and materials availability at the same time as the rest of the world is undertaking similar work.
Over the last 40 years the business of building homes has become increasingly sophisticated and complex. Construction requires absolute adherence to the science of building and in the areas of fire safety, energy performance and lowering carbon, we are adding real challenge and cost to traditional construction. The contractors we are working with are making huge strides in addressing these issues, which should be celebrated as we need to encourage both traditional methods and modern methods of construction (MMC).
Yet with MMC, its greatest asset is to learn and to reapply lessons and come out stronger from its learnings. Matthew Syed in his excellent book ‘Black Box Thinking’ argues clearly, that it was through learning from difficult lessons that the aircraft industry dramatically increased safety.
When Mark Farmer and I wrote our report ‘Build Homes Build Jobs
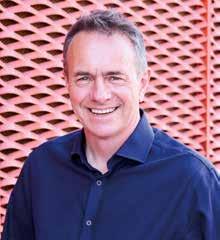
Build Innovation’ in 2020, we could clearly see a link between a green industrial strategy, rebuilding after COVID-19, and aligning with the economic rebalancing of the country via ‘Levelling Up’. To make this happen we needed to progressively attack the paradigm within which modular delivery works.
The current failure of some fantastic organisations who have benefited from huge private investment, and some from the public purse, has demonstrated that a piecemeal and ‘cherry picking’ approach just will not work. At HTA we have benefited from working with the best manufacturers in the world and have seen first-hand how important it is to control every aspect of construction from inception to delivery and even aftercare. The critical element is in creating a visible forward pipeline of demand which is available to the manufacturer and a consistent operating environment where delivery can happen.
In the report, we observed that there was a strong link between rental housing, particularly social rented housing, with speed of delivery, quality, and sustainability outcomes. These in turn led to higher job creation and quicker placemaking outcomes. We highlighted the Clive Betts
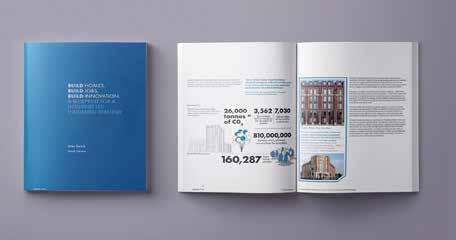
MP 2020 Select Committee report
‘Building More Social Housing’, which called for a grant funded programme for 90,000 social rented homes a year as a route to pipeline for modular delivery. Moreover, we could see that this represented a real opportunity to align procurement, planning and the thorny issues of warranties and insurance.
To achieve this, we need an enlightened government to grasp the opportunity of capitalising on the fledgling progress we have made that has already led us to be, arguably, global leaders in the delivery of modular homes. Instead, there is now an inherent risk with the many failures we are now witnessing by pioneers and investors in trying to grow the modular sector, that it will become the stuff of ‘I told you so’ and ‘let's stick to the knitting of traditional delivery’.
This is entirely against the interests of the UK. Rather than shying away, now is the time for government to lean into the lessons that we have learned about modular delivery and align policy to support modular much more than it is currently doing. In this endeavour, I strongly believe that it is through data, positive and negative, that we can convince the key players, and particularly HM Treasury, that
5 4 housing should now be seen as critical infrastructure for the UK, with modular specifically a key underpinning of the industrial strategy and recovery that we will need to build back from the current crisis.
Regarding this, I was encouraged that Homes England research into the benefits of investment in town centre regeneration has led to the Treasury positively adjusting its value calculation in the green book that dictates the rules of investment into that sector.

Therefore, this is a call out to those in the manufacturing sector to come together to share critical data on areas such as productivity, carbon, fire safety and cost using lobbying platforms such as Make Modular UK to make the case for the sector. Unless we plan for the capacity in the market recovery that will certainly follow the current slowdown, we will not get to a position where we will be increasing the level of homes we need.
For more information visit: www.hta.co.uk
Images:
01. Mike De’Ath, Partner, HTA Design
02. The report ‘Build Homes Build Jobs Build Innovation’ outlined a clear strategy for modular housing and UK urban regeneration
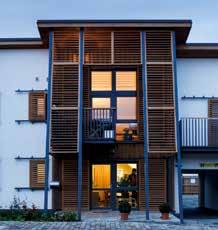
03-04. Hanham Hall
05. Savoy Circus