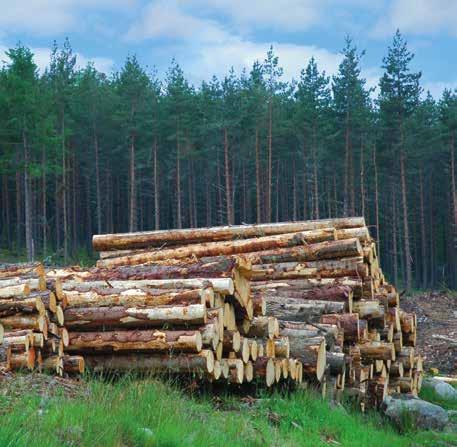
5 minute read
MAXIMISING OUR NATURAL
MAXIMISING
OUR NATURAL RESOURCES
Timber is the ultimate renewable material, but where does it fit into the circular economy? Charlie Law, Managing Director, Sustainable Construction Solutions, examines how the timber industry could embrace a system that makes the most of its available resources.
01
Traditionally, industry has followed the ‘take, make, dispose’ linear consumption model, where resources are taken from the earth to make whatever is needed and the products are disposed of at the end of their life. The circular economy is based on the three key principles of: designing out waste, keeping products and materials in use and regenerating natural systems.
Although the timber industry has been promoting a circular business model for years, and the latest report from TRADA (based on data from the Environment Agency and the Wood Recycling Association) found that less than 1% of ‘waste’ timber ends up in landfill, it is estimated that only 23% was recycled into other construction products, such as insulation or panel boards, with a further 12% used for animal bedding and surfaces. The remaining 65% was either known to be used as a biofuel for energy production or believed to be indirectly used for energy production as part of the mix of refuse derived fuel (RDF) from waste facilities.
It is therefore clear that we need to do more with what we have, e.g. by maintaining timber products in place for longer, by refurbishing, remanufacturing and/or reusing timber components. We also need to ensure we become more self-sufficient in timber production, with the UK being second only to China as the largest net importer of timber and timber products.
The UK must consider the long-term security of its vital timber supplies. Although there is currently a stable supply chain from many countries around the world, particularly those in Europe, for the 60% plus of the UK’s construction timber requirements, this may not be the case in the long term. The need to reduce carbon emissions from the built environment means that every country will have to look at constructing lower embodied carbon buildings, and timber is a key material in helping to achieve this.
There must therefore be a sustainable homegrown timber supply for the future, as well as ensuring more is done with existing resources. For example, only 10% of the hardwood felled in the UK today is used for timber production much of the remaining 90% is used for biomass, without any previous use. Although the utilisation rates for softwood timber are significantly higher, this demonstrates that this valuable resource is not being used as efficiently as it could be.
02
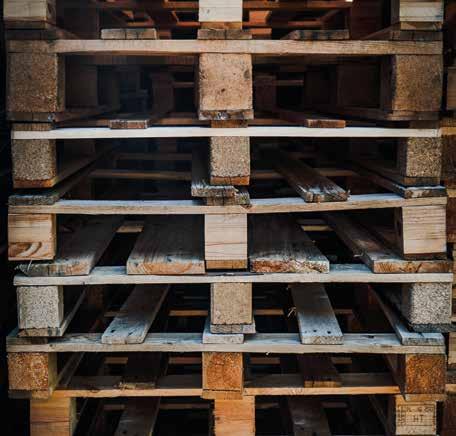
Doing more with what we have primarily means finding new engineering solutions. Work already done in this area includes the Edinburgh Napier University research project on producing cross laminated timber (CLT) panels from UK timber used for pallet manufacture. If we ensure that more of the 43 million pallets manufactured in the UK are recovered and reused, this will release a significant amount of timber for UK CLT manufacture.
Traditionally, to make timber last longer, durable species have been sourced from the UK or overseas, or nondurable species of softwood timber chemically treated with hazardous heavy metals such as copper and chromium. However, due to the availability and cost of durable hardwood timbers, and restrictions on the use of the chemical treatments and issues with reuse and disposal at end of life, other innovative solutions are now available.
One such solution is the thermal modification of timber. Through this process non-durable hardwood species, such as ash and sycamore, can be converted into a durable product reaching class 1 or 2 durability. An alternative to thermal modification is the acetylation process pioneered by Accsys Technologies in their Accoya® products, where certain softwood timbers are in effect pickled in an industrial vinegar. This has a similar effect to the thermal modification process, making the wood unpalatable to insects, fungi and bacteria. This has resulted in Accoya® products in external above-ground applications, such as windows and doors, being guaranteed for 50 years, with an expected lifespan much longer than this. This means these products are likely to last at least the 60-year period required for the external skin of a building. They can also be used for certain structural components.
Ideally, at end of life, all components of a building need to be dismantled with the intention that they are refurbished as required and reused or sent for remanufacture into new components. This may mean the use of, for example, quick release connections, such as Sherpa connections for structural timbers, which can be lifted off, or the use of innovative joints installed in products during manufacture, such as the Kährs Woodloc© 5S system, which allows the flooring to be dismantled. Recycling timber, which in most cases actually means down-cycling, should only be considered where maintenance, reuse or remanufacture are not viable options over the life of the building or product. To facilitate the take up of the above options, changes in business models will be required. Where components are to be recovered for reuse, refurbishment or remanufacture at the end of their service life, it would be beneficial if the ownership remained with the component supplier. This allows them to control any required maintenance on the component to ensure it remains in use for the required service life, and also the recovery of the component at the end of its service life.
There are various business models that could be used for timber products, and the one used would depend on the intended service life of the component, and the level of maintenance required throughout this life. Possible business models that could be considered are short-term hire, longer-term leasing, service contracts or incentivised return in addition to, or preferably instead of, standard sales contracts.
For example, in the long-term lease of a component that needs little or no servicing, such as a partition wall system, the wall system would need to be flexible enough to be used in various locations, both on the original site of installation or other similar buildings where the nominal floor to ceiling height was within a defined tolerance. The manufacturer could then control the installation and removal, and any subsequent refurbishment or remanufacture before being leased to another client.
There is already much innovation in the timber product industry with many products already in place that could easily adapt to a circular economy model. Therefore there is clearly scope for timber product manufacturers to move to a circular economy business model, but this will require a change in the way products are marketed to the construction industry, as well as education and an acceptance of these business models by clients.
www.susconsol.co.uk
IMAGES:
01. Only 10% of the hardwood felled in the UK today is used for timber production with much of the remaining 90% used for biomass 02. A significant amount of timber for UK CLT manufacture would be available if we recovered and reused more of the 43 million pallets manufactured in the UK