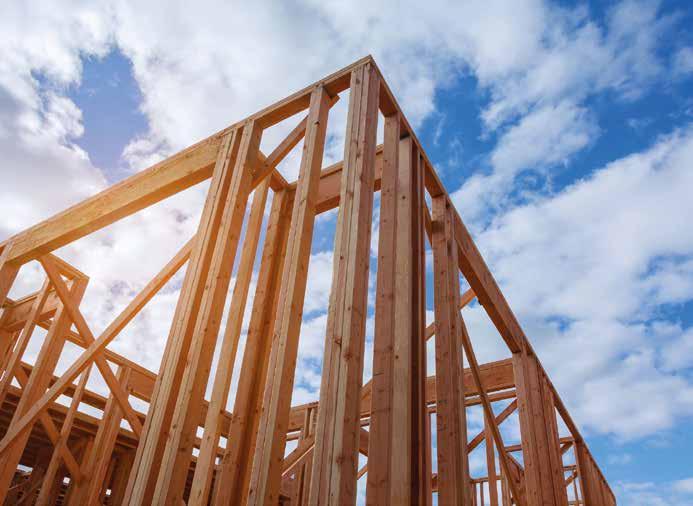
3 minute read
SUPPLY CHAIN WOES LEADING TO PROFIT LOSSES
Three in five (59%) UK construction companies that have been hit by supply chain issues over the past year have seen once profitable projects turning unprofitable, research from business insurer QBE has found.
In a survey of senior leaders in the construction industry, 83% said they had experienced an issue with their supply chain over the past 12 months, while 85% said that they expected supply chain issues to pose a challenge in the next 12 months. 85% said that the cost of importing construction materials increased at a rate higher than inflation over the past year.
According to a new report from QBE Business Insurance in partnership with Oxford Economics and Control Risks, ‘Supply Chains and the UK Construction Sector’, the outlook for the UK construction industry in 2023 is likely to be equally as disruptive as 2022. Geopolitics and domestic developments will continue to affect access to materials and their price. Since the first pandemic lockdown, a shortage of materials has been the largest factor constraining construction activity in UK. Nine out of 10 (89%) of respondents impacted by supply chain issues said that they were currently experiencing a shortage of materials.
Andy Kane, Portfolio Manager, Construction, QBE International said: “Construction firms in the UK have seen continuing shortage of materials and supply chain disruption since the start of the pandemic. Therefore, it is no surprise that the majority of those we surveyed have seen disruption which has ultimately impacted profitability. With these challenges set to continue throughout most of 2023, now is the time to take action to limit disruption and protect profitability. There are steps that construction industry leaders can take in order to lower their supply chain risk. This includes shifting away from the ‘just in time’ supply chain model we have witnessed in recent years to a ‘just in case’ supply chain.” www.qbeeurope.com
In addition, businesses can take steps such as using technology to automatically order supplies when stock levels go below a certain point, look to diversify suppliers and, where higher input prices are the likely fallout from supply chain disruption, consider adding a cost escalation clause to future contracts. Many of the construction firms surveyed said they are taking steps such as diversifying supply chains (42%), holding greater stocks of strategically important materials (31%), establishing robust monitoring systems of stocks and suppliers (23%) and nearshoring (17%), however the survey found nearly one fifth 18% have not taken any action.
Dts Appointed To Building Better Dps
The objective of the alliance is to ensure its members have access to a variety of modern methods of construction (MMC) solutions to provide suitable, trustworthy and high-quality solutions for every type of site they develop. The DPS was launched in May 2022 following its original volumetric framework in 2021 and aims to produce approximately 5,000 MMC properties by 2026.
opportunity for us to increase our presence in the affordable housing market.
Donaldson Timber Systems (DTS), has been appointed to the Building Better dynamic purchasing system (DPS) for MMC category 2 construction systems. Building Better is an alliance of 30 housing associations and councils supported by the National Housing Federation.
In England, there is a total housing backlog of four million homes across the country. With new house build completions hitting just 175,390 in 2021, there was a shortfall of 164,610 completed homes that year - and the trend is expected to be similar for 2022. To address the overall shortfall, 340,000 homes need to be built every year until 2031. DTS’ appointment to the Building Better DPS will support this objective by increasing the number of timber frame homes constructed.
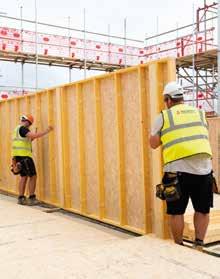
Mike Perry, Business Development Director of Donaldson Timber Systems, said: “We are thrilled to have been appointed to Building Better’s DPS and to have the opportunity to work with its members. With over 215,000 homes managed by the member organisations, it provides a great
“MMC systems are an increasingly important consideration for developers of all kinds, and our offsite timber frame systems can play a leading role in housing associations and local authorities meeting the energy requirements of new homes. By demonstrating our quality and experience to Building Better, we are now a trustworthy resource for these members and look forward to working in partnership with its members.”
Trina Chakravarti, Project Director at Building Better added: “We are pleased to welcome Donaldson Timber Systems into our group of category 2 offsite manufacturing partners. Building Better is aggregating demand in the affordable sector so our members can procure high quality, sustainable offsite homes at the right price. We’re confident that Donaldson Timber Systems will be able to work with us and our members in delivering the sector’s housing ambitions over the next three years.” www.donaldsontimberengineering.co.uk