
6 minute read
Stylish Student Life
Upperton Road Student Accommodation is a purpose-built modular newbuild scheme, delivering luxury high-end student accommodation in Leicester.
The scheme consists of 46 selfcontained studio apartments for student living, includes a gym, cinema room, and private study areas as well as indoor and outdoor communal areas. The project was for the refurbishment of an existing block and the design and construction of two additional three-four storey blocks housing the studios, self-contained flats, and ancillary accommodation. The development is 1900sqm and Block A and in parts to Block C Roof there is a green roof. The scheme is located within cartilage of a Grade 2 listed building and the design was developed with this in mind. Utilising MAS skills and expertise in old and new approach, a well-balanced contextual design approach was applied. Upperton Road will provide a new level of much needed contemporary student accommodation within Leicester city centre providing all the necessary facilities on site, creating a luxurious environment for students to thrive in.
Upperton Road is the fourth highend student accommodation project delivered by the trio formed by the same client, contractor and architect. This continuing partnership has helped create some of Leicester’s most sought-after student accommodation.
Utilising MAS skills and expertise in old and new approach, a wellbalanced contextual design approach was applied. This luxury student development is located within a short walking distance to the main campus centre of De Montfort University, it has good connections to Bede Park
1
and Nelson Mandela Park to the south by foot along Regent Road. These connections allow easy access for the students to the various University departments and to local services and facilities within the area, bringing additional life and vitality to the location.
The 46 self-contained, ultra-modern and smart studios have various internal and external communal spaces. Each of the studios has been designed with comfort and quality in mind, taking into account good on-site amenities and featuring an open courtyard towards the rear elevation. The layout for each room is designed to be spacious to allow for a flexible flow of movement. Each studio is designed to allow for a double size sofa in the room, if needed, with generous views towards all elevations.

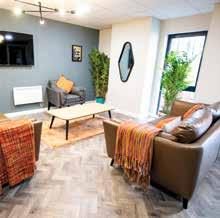
The bed space and study area are located nearest the window to allow natural light to be utilised during the day and there is plenty of storage combined with personal en-suite shower room facilities and a kitchenette. The site also boosts amenities such as a gym, cinema room, study pods, internal and external spaces as well as a laundry room and a large outdoor cycle store. The teams involved drew on their extensive record of working in busy locations and managing the challenges of constrained sites through the construction of this complex in the city centre. Solutions introduced to cut construction time, minimise disruption and ensure excellent quality included the use of modular bathroom pods which were manufactured in factory conditions and delivered fully fitted to site. The use of precast concrete for stairs and intermediate floors also contributed to less environmental damage and meant the project was delivered on time despite lockdown restrictions and difficult circumstances in 2020 due to COVID-19.
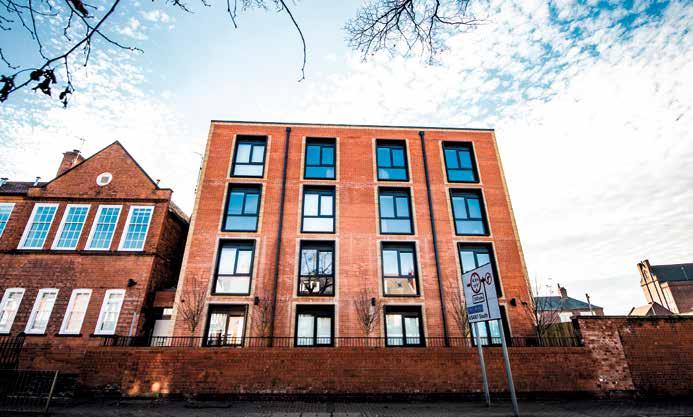
Less energy and resources were used and less waste was produced onsite due to the fact that the modular bathroom pods were manufactured to precision in a factory and delivered
3
to the site on time. As the bathroom pods were manufactured offsite there was greater manufacturing precision, materials were more accurately calculated, reducing energy consumption and running costs. By manufacturing offsite there were less workers needed on site thereby reducing running costs too.
The use of a crane provided a faster installation process saving on both construction time and cost. Using offsite technology also meant that delivery was guaranteed on time and to the highest quality as mitigating circumstances such as bad weather did not delay the project. The design didn’t need to allow for margin of error and therefore costs for remedying
2
4
construction defects have been greatly reduced. The project was delivered on time ready for University students to accommodate at the beginning of the academic year 2020/2021. Director Neil Thakkar, from client, Zone Developments said: “This project is set to deliver exciting, contemporary student accommodation in an excellent location.”
For more information visit: www.masarchitecture.co.uk
Images:
01-04. The 46 self-contained, ultra-modern and smart studios have various internal and external communal spaces.
WHAT A DIFFERENCE A YEAR MAKES AS M-AR TREBLES TURNOVER
It’s been an exceptional year for the construction industry as a whole but for off-site contractor, M-AR, it’s been exceptional for all the right reasons – with record-breaking sales and turnover reported. And now the company has its sights set on breaking even more records this year and beyond.
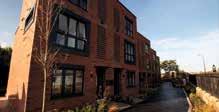
The Hull-based off-site contractor, which is still privately owned today, was founded in 2007 and has gone from strength to strength ever since. It primarily operates across the residential sector, both private and social housing, as well as education and the commercial sectors.
M-AR: the 2020 results are in
Following a period of unprecedented growth, M-AR has reported an increase in turnover of more than 300 per cent up on the previous year. This makes the year ending March 2021 truly exceptional – especially in the face of industry-wide challenges posed by the Covid-19 pandemic and subsequent national lockdowns.
M-AR has reported annual turnover in excess of £20 million for 2020/2021 and, with a clear strategy is on track to increase turnover by a further 50% in 2021/2022. Moreover, the company’s profitability also increased significantly, making it M-AR’s most successful year to date and the sign of things to come as it makes a name for itself as a trusted offsite contractor.
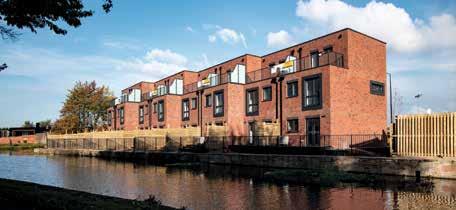
1
What’s the secret to M-AR’s success?
M-AR works in partnership with customers and supply chain partners to find the right solution for each project brief, using its expertise to tackle any challenge to create and deliver schemes without compromise. The company primarily focuses on volumetric schemes but has the ability to provide alternative construction solutions, making its offering truly unique. M-AR also owes its success to its continued commitment to selfinvestment in all areas of the business with the latest period of growth fuelled by large-scale company-wide investment. M-AR was early to the housing market and is now part of the Buildoffsite Property Assurance Scheme (BOPAS) and has invested significantly in its technology to allow it to increase its offering within the housing market.
In the last year the company has appointed 35 new members of staff, moved to a brand-new dedicated 100,000 sq. ft. manufacturing facility and invested over £2m in new machinery and equipment.
2
This ongoing investment will continue to reduce the cost base for its customers and lay the foundations for M-AR’s ambitious five-year growth plans, allowing it to increase the volume of projects it can deliver sustainably and without impacting on quality or customer service.
What’s next for M-AR?
Ryan Geldard, Operations Director at M-AR commented: “We’re delighted that our novel approach is working well for our customers, and that is reflected in our financial results and forward order book. We’re entirely focussed on creating better project outcomes and lowering costs for our customers through our holistic assessments of their needs and by aligning our people and technology, merging the gaps between traditional contracting and manufacturing.
“Our management team is committed to making M-AR a happy and healthy place to work and also supporting our peers in industry to drive better collaboration. We’re first in line on many great initiatives that are breaking the mould of how high quality housing is delivered.”
For more information visit:
www.m-ar.co.uk
Images:
01-02. Modular construction is going to play a vital role in the UK’s ‘Build Back Better’ drive thanks to its speed and efficiency.