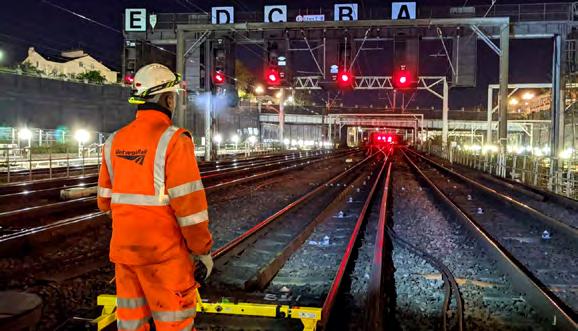
6 minute read
Acceleration of digital signalling
The acceleration of digital signalling
Government invests £1.2 million for development work to be rolled out on three key rail routes
Feasibility work for digital signalling will be accelerated through £1.2 million of new government funding.
Vital sections of the West Coast Main Line, Midland Main Line and East Anglia route are set to benefit. This includes Peterborough to Kings Lynn on the Anglia route, and in the Warrington and Wigan area on the West Coast Mainline North. This work will identify the most effective way to apply this type of technology to the railway and will showcase a new way of working that capitalises on early engagement with the supply chain. It will also create further opportunities to encourage innovation and driver efficiencies across regions. Learning from the recent experience of the East Coast Digital Programme, where a partnership with route-based operators has been a success, this early scoping work will lay the foundation for future digital signalling renewals – part of a wider national plan to introduce digital signalling across the rail network in Great Britain. Rail Minister Chris Heaton-Harris said: “We’ve come a long way since the era of metal levers, used by Victorian signallers to provide safe passage for trains rolling into and out of stations. Now it’s our turn to be modern transport pioneers as we build the railway of tomorrow.
“The latest investment brings forward early investigation work with Network Rail engineers and suppliers on how best to roll out digital signalling across the rail network, reducing delays and improving safety in the long term. “Our ambitious programme to modernise Britain’s rail network will support the supply chain by creating high-skilled jobs and boosting the economy, as we level up the country and build back better after COVID-19.”
An end to conventional signalling at the side of tracks Conventional signalling means the network can struggle to recover quickly following disruption, with a small delay on one part of the railway still causing knock-on delays hundreds of miles away on other parts of the network many hours later.
This new technology gives signallers much better real-time information about train movements, enabling them to communicate with train drivers continuously to reduce the impact of delays. This ‘in-cab’ system will mean an end to the conventional signalling at the side of tracks first used in the Victorian era.
As part of this work, the Department is engaging with suppliers of digital signalling and industry experts across the country in order to learn from similar schemes and drive efficiency. The Government’s nationwide programme to roll out this technology on the railway is part of its commitment with industry within the rail sector deal.
Andy Jones, Director of Operational Programme Delivery at Network Rail, said: “We’re delighted with this development funding, which reconfirms the DfT’s commitment to pursuing the long-term deployment plan for digital signalling on Britain’s railway.
“The first three schemes – on the East Anglia route, the West Coast Main Line and the Midlands Main Line – will help drive forward the modern railway we all need.”
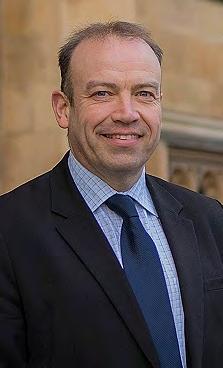
Investing in the future The news follows the announcement of £350 million of new investment towards the East Coast Digital Programme, which will introduce digital signalling on the East Coast Main Line, between London King’s Cross and Stoke Tunnel in Lincolnshire, ensuring that more passengers reach their destinations on time.
David Clarke, Technical Director at the Railway Industry Association, said: “With around 60 per cent of signalling equipment units on the UK rail network needing to be replaced over the next 15 years, rail suppliers will need to gear up to ensure they are ‘match fit’ for a significant amount of work in ensuring its rollout is delivered efficiently, to time and to budget, and in order to ensure value for money for taxpayers and passengers.
“New digital technology will improve the reliability and resilience of the network, providing better services for passengers and freight, and will create highly skilled jobs across the UK at a time when they are vitally needed.”
Advice for Railway Companies – monthly feature by Jobson James Rail – The Rail Broker Hiring plant tools and equipment? Read the T&Cs
Railway companies often have to hire equipment – mobile plant, hand tools, surveying equipment, etc. – but the companies that hire out this equipment will trade on terms and conditions that are important to understand.
Plant and tools destined for contract sites are commonly hired out under Construction Plant Hire Association terms – CPA, or the rail version, RPA. These terms make the hirer responsible for not just theft and damage to hired items, but also for the lost hire income while the plant company is waiting to be paid for their loss – these are the “continuing hire charges”.
Often a plant hire company will allow the hirer to pay a higher rate of hire so they are not responsible for losses and that the plant hire company retains risk of theft or damage.
If a railway company is spending more than £300 per month on hire, then it is usually cheaper for them to buy their own insurance for the hired equipment.
The quality of policy cover varies. Many insurances exclude overnight theft losses unless the hired plant is in a locked building or compound.
Policies are also often restricted to cover hired under CPA, when there are other conditions used in the industry like HAE (Hire Association of Europe). Be aware that plant hire terms often state that the hirer accepts the plant is in good condition unless a query is raised immediately upon receipt. A client of ours hired a theodolite and tripod. It sat in their office for two weeks before use due to contract delays. When it was finally used, the tripod collapsed and the theodolite was smashed.
It was discovered that the tripod was very worn and was defective.
Under the plant hire terms, the hirer was liable for the £30,000 replacement of the theodolite, and their insurance had to pay as they had not checked the item for condition when it was received.
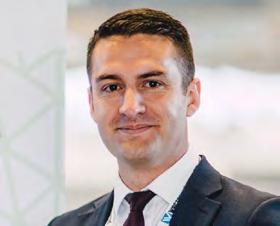
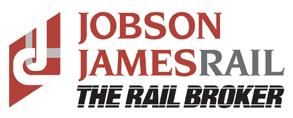
Tim Smith, NEBOSH Cert Cii Client Director at Jobson James Rail - 07493 868305
www.jjrail.co.uk
We Are A Rail Specialist Insurance Broker (RISQS Link up approved)
WE INSURE
• RRV and Plant Companies • P-Way/S&C, S&T, OLE/Third Rail and Civils contractors • Rolling Sock Turnkey Modifications companies • Manufacturers, Wholesalers and Installers of rail products • ROSCOs and TOCs supply chain • Rail Consultants, Surveyors and Design Companies
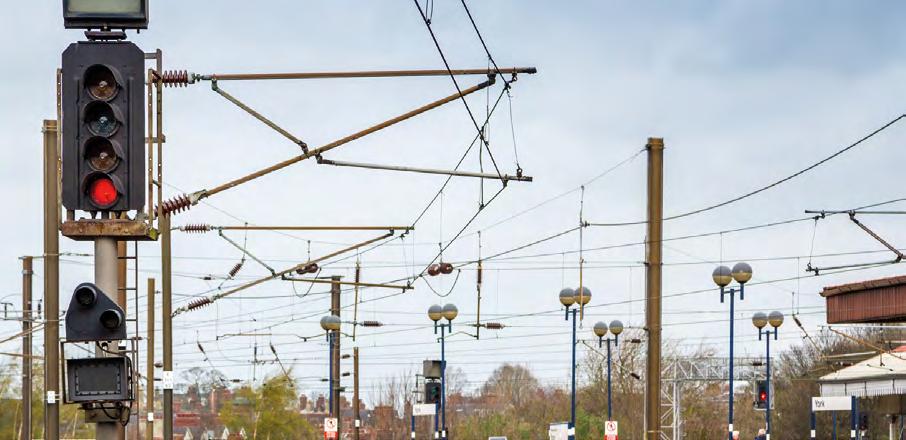
WHY US?
• Specialist Rail Knowledge • NEBOSH/Safety approach producing lower premiums • Contractual Liability checking • Better Technical advice • Specialist rail safety consultancy site audits funded by insurers
Contact Keven Parker on
07816 283949 / 0121 4528717 / 0207 9839039
Email: Keven.parker@jjrail.co.uk
Offices in London and Birmingham. Nationwide coverage.
Jobson James Rail is a trading name of Aston Lark Limited. Authorised and regulated by the Financial Conduct Authority.
Rail Plant and Civils Principal Contractor – £65m turnover
This client is one of the UK’s leading plant/RRV providers and a multidisciplinary Principal Contractor for Network Rail.
Unreasonably high premiums were identified, as were policy excesses in respect of plant, motor and third-party liability claims.
We also pointed out numerous, rail-relevant gaps in cover which had left the client both uninsured for day-to-day exposures and in breach of contract had an accident or claim occurred.
We then successfully negotiated substantial premium savings and an enhanced retrospective premium rebate for the expiring policy year.
This resulted in a premium saving of over £211,000 compared to the previous broker’s rates.
Policy excesses were reduced, gaps in cover closed and Business
Interruption extended to insure incidents both on site and in transit.
GAPS IN COVER CLOSED 33-PAGE RISK REPORT TO INSURERS £65m TURNOVER HAPPY TO RECOMMEND
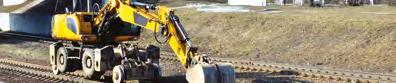