KEEPING BRITAIN’S RAILWAY RUNNING
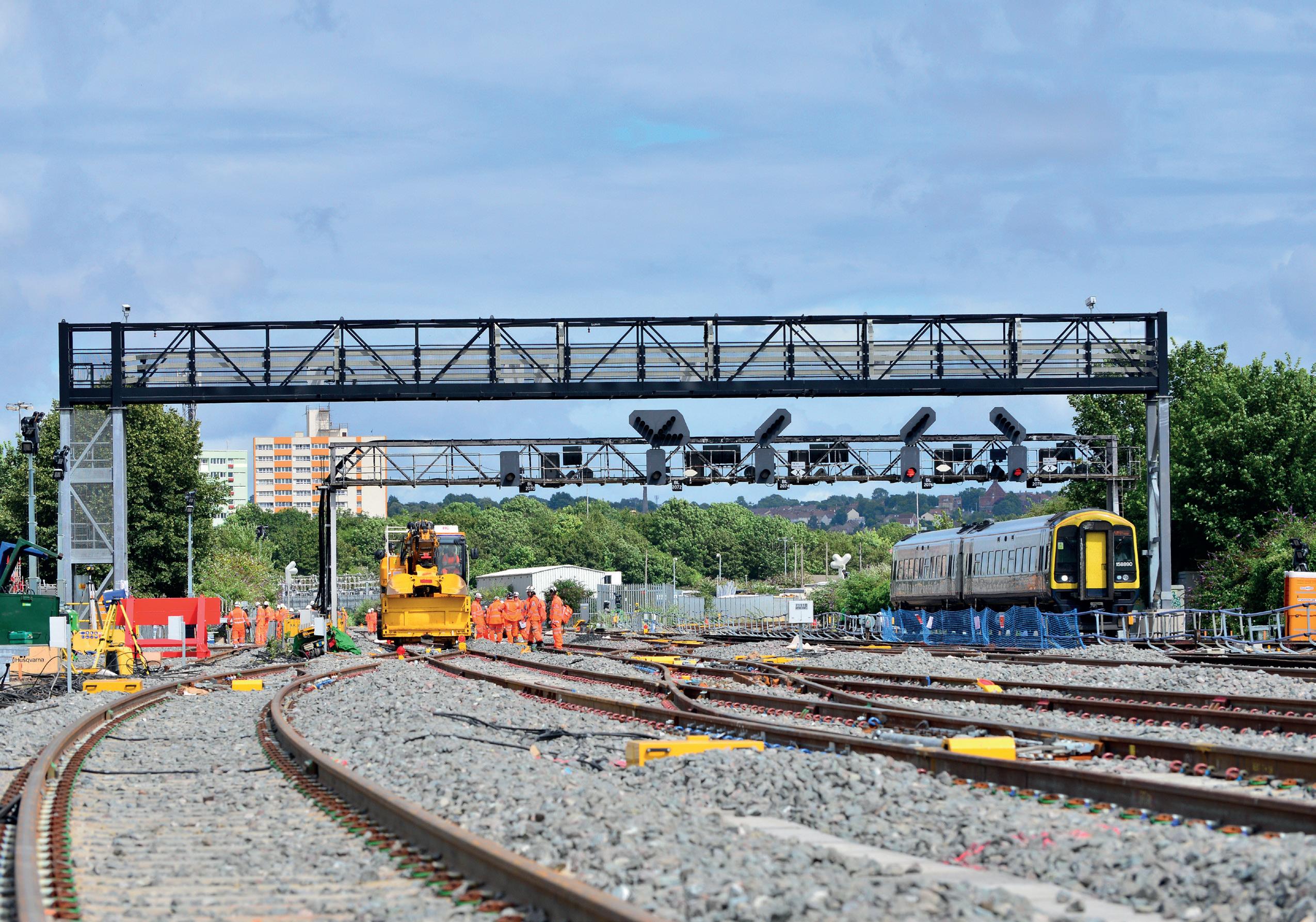
When it comes to manufacturing concrete for the rail industry, Anderton go a lot further.
Our cost effective, bespoke concrete offering means a client’s very own concept can be both designed and built in-house at the Anderton factory.
With a proven track record for bespoke solutions, our experienced team has successfully completed projects this year for Feltham Resignalling, Werrington Separation, Durham Coast and Birmingham New Street to name but a few. What’s more, our own on-site mould manufacturing facilities ensures quicker lead-times, better availability and saves you time on site.
So, if you’re thinking bespoke, speak to Anderton.
Welcome to the latest edition of Inside Track, which has been put together against a backdrop of continued industrial action and political discussion regarding the railways
David Brough, director at Rail Competence and Compliance Ltd, explains the importance of competence and how it benefits the rail industry
NTC trains prove their worth to the country’s rail infrastructure
New Track Construction machines are a modern solution to keeping on top of the industry’s ‘permanent ways’
Out of sight, out of mind is an apt description for the miles and miles of control, communication and power cables that the railway depends on every day
First IPEMU unveiled for Merseytravel network at InnoTrans
Stadler’s impressive units on display at Berlin trade show as Liverpool City Region’s Metro Mayor looks forward to seeing the trains in action by the end of the year
Infrastructure owners have to know that their railways are in good condition and capable of operating safely. But, with mile upon mile of track to check, how do they do that?
Supply chain partners and suppliers invited to find out more about opportunities worth around £250 million
Eli Rees-King writes about her trip to InnoTrans and the exciting launch of OnePlace
When warm days mix with a fairly constant supply of rain (in most years), the lawn grows like crazy and needs constant cutting while the shrubs, trees and bushes try to take over the garden
TfL has been forced to rely on more than £5 billion in government support since the start of the pandemic. Now it has been given a long-term deal, but as Inside Track editor Richard Clinnick explains, questions remain
A successful bank holiday weekend for Network Rail Network Rail used a bank holiday weekend to undertake maintenance and upgrades on the railway. Richard Clinnick reviews the major projects carried out
A busy time in Berlin InnoTrans, the global exhibition for the rail industry and its suppliers, returned after a four-year break
Communities ready to use railway again after 60-year gap Network Rail is aiming to reintroduce passenger services from Southampton Central to Marchwood station and create a new station at Hythe
Inside Track takes a closer look at the ORR’s periodic review that will inform Network Rail’s SBP for the next control period
Design consultancy Mosaic Rail is bringing something different to the industry
The company behind Britain’s new highspeed rail network is trialling technology to dramatically cut fuel consumption, carbon emissions and improve air quality
Ambitious Central Hall set to cement NRM’s position as world’s leading collection of locomotives and rail artefacts
Welcome to the latest edition of Inside Track, which has been put together against a backdrop of continued industrial action and political discussion regarding the railways
The theme of this magazine is permanent way, which is the very foundation the railway is built on, yet it feels like the industry is gearing up for major change. There remains the prospect of the biggest reform since privatisation, however, national media reports continue to query whether or not Great British Railways (GBR) will happen. Nevertheless, plans need to be made accordingly and you can read how funding for the next control period, due to begin on 1 April 2024, is decided upon. Permanent way will, of course, feature heavily in CP7 as maintenance and renewals will likely once again be a major expenditure.
The control period model used to fund the national network is something that the Railway Industry Association (RIA) is very keen to see introduced for Transport for London (TfL) instead of the current short to medium-term agreements between central government and the organisation responsible for operating public transport such as the London Underground (LU) in the capital.
Ever since the outbreak of COVID-19, TfL’s finances have been decimated due to the fact it receives more than 70 per cent of its income via the farebox, something that was hugely affected by the government decreeing that people should work from home wherever possible during the pandemic. Combined with mixed messages about what people could and could not do, and companies allowing staff to continue working from home, LU has not recovered to pre-COVID figures or even near preCOVID figures like the national system, and so has relied on the government for financial assistance, already to the tune of more than £5 billion since March 2020. This money has come at a cost for TfL, which has been forced to scrap a planned fares freeze, reduce management headcount and investigate the introduction of driver-only trains despite political misgivings. Interestingly, by the end of October, two of the three main protagonists in this situation have left or are leaving their roles. Grant Shapps is no longer Secretary of State for Transport following Liz Truss’ victory in the race to be Prime Minister, while Andy Byford will leave his role as London transport commissioner on 25 October, leaving only London Mayor Sadiq Khan still in post. With an agreement now in place until 2024, there is hope that TfL can start to plan ahead. This is vital, as more than 50 per cent of investment on the TfL network is spent outside London. Combined with plans for CP7, this could offer a significant boost for a supply chain that has been forced to wait more than 1,000 days for the ‘annual’ Rail Network Enhancement Pipeline (RNEP) to be published by the government, detailing planned expenditure on the railway.
Many of those companies interested in work from either Network Rail or TfL will have joined more than 2,800 companies from across the world that attended the InnoTrans Trade Fair in Berlin last month. Britain’s rail industry was represented by more than 100 companies and in this issue Nigel Wordsworth, who attended on behalf of RailBusinessDaily, reviews the event.
A highlight of InnoTrans was the unveiling of an Independently Powered Electric Multiple Unit (IPEMU), which also happens to be Britain’s most accessible passenger train. Built by Stadler, this will operate on Merseyside and offer a glimpse into what is possible for the industry.
We hope you enjoy this edition of Inside Track.
By the end of October, two of the three main protagonists in this situation have left or are leaving their roles
“ “Image: shutterstock
What is competence? Many people have different views on this, however, there is only one view that really counts in terms of rail business, that of the Office of Rail and Road (ORR).
In an extract from the ORR guidance on developing and maintaining staff competence, the regulator defines competence as: “competent people performing activities consistently and within their competencies.”
This is not the Oxford English Dictionary explanation but it is the view of the governing body over Britain’s railway. This is a fundamental practice that must be embedded in companies to ensure risk is minimised to its lowest possible level at all times.
So how do you ensure this is the case?
The ORR has produced a document that has been in place for over 10 years and which was last revised in 2016 as ‘Developing and Maintaining Staff Competence’ (RSP1).
This document gives good guidance on how this process should be done and recognises that every business is different and has different needs, so it doesn’t just fit to passenger operators and freight operators but recognises that the supply chain has a duty under the Rail and Other Guided Systems regulations (ROGS) to be compliant.
So, to each and every business, a question – is your Competence Management System (CMS) good enough, or is it there just to pass an audit?
Many senior people in the rail sector are not familiar with this document and do not understand the nature of a robust CMS, how to check compliance with it or know how to review and develop a CMS that adds real value to the skill sets in the workforce, therefore reducing the risk profile of their business. A CMS is not a database that records all your records and training, this is just one part of the bigger system.
“However, anyone with an interest in competence management will also find useful advice in this guidance. Directors and senior managers responsible for the overall policy of the company need to be aware of the general objectives and benefits that may result from the use of this guidance.
“Managers responsible for the maintenance and improvement of an existing competence management system, those responsible for implementing a system and those operating and assuring the quality of systems will need to understand more of the detail of this guidance.”
Too many people rely on flooding their paperwork with signatures, dates and references to national standards as a benchmark, however, there seems to be little substance behind this
“ “
The RSP1 document summary states: “This guidance is primarily aimed at those who are responsible for managing and assuring the competence of individuals and teams in the railway and other guided transport systems industry, and whose work may have an impact on operational safety and on occupational health and safety.
It doesn’t represent just train operators, it addresses the whole industry, supply chain, overhead line companies, permanent way, signalling, telecoms, T&RS maintainers, T&RS operators, OTMs etc. If your business poses a risk to the infrastructure, then you need to have a robust CMS in place.
A lot of these parts of the industry rely on their initial training and professional body registrations to imply competence, however this is a one-off check to see if the bar has been met to allow the individuals to carry the accreditation of that body; ongoing competence is down to the individual company to make sure it meets the requirements.
The guidance says that a national occupational standard can be utilised, or you can derive your own.
If a national occupational standard is used, do you use it all for your sections, or do you pick and choose the elements you want? If you do the latter, how have you selected these over the other areas? Has the impact of this been part of the risk assessment principle? Principle 1 – identify tasks and assess the risks.
So what is a CMS? It is initially a suite of documents that in any system, such as ISO, tells you how you comply and in this case, with the RSP1 document from the ORR. There are 15 principles as guidance to assist you on the development of your bespoke CMS. The ORR suggests that as a first step, you utilise Principle 15 – ‘Review and feedback’ on your current system. This gives a heads up on what state your CMS is in and where to tackle your problems.
The rest of the principles illustrated give individual guidance on what needs to be addressed. When this system is undertaken correctly and you adopt the Risk Management Maturity Model (RM3) from the ORR model, OP2 score may be increased and not just be an ad-hoc system.
Too many people rely on flooding their paperwork with signatures, dates and references to national standards as a benchmark, however, there seems to be little substance behind this. Having true meaning and added value to your CMS is vital, to reduce your risk profile, to increase staff development and maintain skill levels.
The sharp end of the CMS is the assessor, and this role needs support in the form of an Internal Quality Assurer (IQA). The IQA provides a reporting line in terms of assessment functions and not necessarily direct line report. The assessor is making decisions based on evidence gathered on the day of assessment and judging if the evidence collected is suitable and sufficient to claim competence; however, how do you know that all of your assessors are making the same level of judgement call as to what is sufficient? What is the correct answer to specific questions? The IQA is in place to standardise the role of the assessor and ensure a fair and even balance of checks and evidence gathering and recording is undertaken.
Regular monitoring of staff by interim checks is also required to prevent skill fade between the assessment end points and this may take the form of managerial checks, unannounced monitoring, in process evaluations by production staff. There are quite a few variants on how this may take place.
The IQA will RAG rate each assessor and provide a supporting framework to ensure consistency of decisions made.
This is at least an annual observation or each assessor ensuring they are maintaining the standards set by the awarding body for their assessment qualifications. Reducing skill fade in the assessors is a key aspect of the IQA role, and this cascades through the CMS system so that the skill fade of the workforce is reduced by several different methods.
Accurate reporting of the IQA function to the senior teams in a business will provide valuable information on the state of the workforce and highlight any areas that are a potential threat in terms of skill fade risk.
Early intervention here will allow the business to stabilise and ensure corrective measures are implemented through the IQA and assessment teams.
It is essential that this is not just a problem area given to the training department to deal with; it is of real value to involve other departments, such as HR, safety, audit, document control. These departments have valuable input and potential workstreams to input to this process as they are detailed in the 15 principles of the ORR document.
A full, open, honest review of what you have is your first step, independent if necessary, to see the one version of the truth, providing a baseline to work from. If you truly want to add value to your business and want to eradicate as much risk as possible, this is an essential starting point.
Systematically work through the areas highlighted and address the shortfalls, and praise the areas that have little or no need to improve.
Empowering the right people to manage this process and giving them time is essential to develop and maintain an effective competence management system.
As senior people in your business it is your role to support them. Invest in the people passionate about developing your staff and you will see the rewards in staff development, motivation, devotion and loyalty.
The end result is that the business will have an evidence trail detailing what has been done, by whom and how often. This gives confidence that the individual has the correct skills to undertake the tasks requested and with upmost confidence. The records will demonstrate this and that fair assessment has been carried out ensuring the candidate is not put under duress to perform, as they have the right to appeal assessment decisions.
Any issues highlighted are then used to ensure the candidate is given the right skills and opportunity to develop to ensure they are able to meet the required standards of the assessment and of the business, driving it forward, building credibility and quality work done.
New Track Construction machines are a modern solution to keeping on top of the industry’s ‘permanent ways’
Permanent way is the very foundation that the railway is built upon. This generally consists of pairs of rails usually laid on sleepers or ties that are embedded in ballast, with the purpose of carrying trains.
The description permanent way came from the early days of railway construction when contractors would often lay a temporary track to transport spoil and materials about the site and, when the time came, this would be removed and the ‘permanent way’ would be installed.
Over the years the process has changed considerably due to the changes in working methods, design, and technology, but despite all these operational developments, a pair of steel rails laid on sleepers or ties embedded in ballast remains the situation to this day.
In the 21st century methods have changed again, particularly as railways have got busier. Lengthy possessions have increasingly been
restricted to mostly overnight or bank holiday periods.
sleeper alignments, positioning of the rail into its housing, and then clipping the sleepers into place to complete the process.
The key specifications of the NTC are that it is 45 metres long (148 feet) including its various vehicles. The weight of the NTC is 250 tonnes while the Truss wagon is capable of carrying 10,886kg (24,000lbs) loads. Although it is powered, when being moved between worksites it can be towed at speeds up to 80km/h (50mph).
A key innovation has been the introduction of the New Track Construction (NTC) train. This was first brought to this country by Balfour Beatty in 2004. Initially the NTC was required for a specific task of relaying plain line track. The machine has the ability to deliver plain line track renewals to exact client specification and this can include relaying various spacing as well as numerous
An NTC is able to deliver track laying approximately three times faster than the stick building method. A major innovation is the ability of the NTC to control the flow of material without the use of overhead cranes.
The NTC machine consists of three wagons –these are the truss wagon, the power wagon and the reception wagon. The former delivers the sleepers to the front of the machine for them to be positioned onto the ballast formation, where they are then balanced and aligned.
The train is able to lay around almost one mile of track per day when used in continuous operation
“ “
The rail is then positioned into the sleeper houses using a series of clamps. The truss wagon at the front of the NTC train will move the rail into the correct position before then placing the rail into the housing of the sleeper.
Inside the reception wagon is the NTC train’s engine, which is used to operate all the components of the machine; this vehicle is also home to the delivery conveyor for the gantry.
The gantry unit obtains the sleepers from the trailing sleeper wagons and delivers them to the conveyor in order to feed the truss wagon. The clipping unit that is located under the reception wagon clips the sleepers, thereby completing the final stage of the process.
The NTC is able to move independently through the worksite using the powered wagon and moves between sites using the traditional hook and haul method.
The train is able to lay around almost one mile (1.5km) of track per day when used in continuous operation and can therefore improve productivity, safety, efficiency and quality. The NTC can be used with concrete, pre-plated wood or steel ties.
As for its performance, the NTC has the ability to lay rails up to 136lbs and can operate at speeds of up to 10 ties per minute, however it is still able to deliver more precise tie spacing and tie squares. Harsco Rail says that its contract NTC units have installed more than four million ties, which is the equivalent of 1,515 miles (2,400km).
A recent example of the success of the NTC has been its use on the reopening of the Dartmoor line between Okehampton and Coleford junction in Devon. The railway was reopened using the Project SPEED (Swift, Pragmatic and Efficient Enhancement Delivery) method that was jointly developed by the Department for Transport (DfT) and Network Rail during 2020.
Higher, further, faster Infrastructure projects at different stages of development were reviewed to identify how government funding could go further and work could be carried out faster.
The Project SPEED approach identified 10 key themes to introduce lower costs and speed up the delivery of infrastructure schemes, such as rapidly increasing the use of innovative construction methods and removing complexity from planning processes. As a result of this, the Okehampton project was identified as one such scheme and was opened under budget and several months ahead of schedule, with the use of the NTC key to this.
When government funding for the Dartmoor line was confirmed in March 2021, engineers started immediately and worked to upgrade the 14-mile section of track. As well as working day
and night on drainage, fencing and preparing the ground for the new railway, the NTC was key to advancing the project.
More than 11 miles of new track was successfully laid as well as 24,000 concrete sleepers installed using an NTC machine, which was able to drop sleepers simultaneously evenly into position, lay the track on top and then clamp the track into place.
The concrete sleepers were stored at the work site adjacent to Okehampton station and were transported along the Dartmoor line using a locomotive. On average, each time the NTC was used, it contained 2,430 sleepers.
The 29,000 tonnes of ballast was also nearly all installed at the same time.
Speaking following the completion of the NTC’s work, Becky Tipper, Network Rail scheme project manager, said: “We are delighted with the progress the team has made and this is credit to the hard work and dedication of our engineers involved in this project.
“To have already laid the 11 miles of track, 24,000 sleepers and nearly completing the installation of the 29,000 tonnes of ballast is no mean feat.”
The rail minister at the time was Chris HeatonHarris, who said after the NTC completed its work: “Network Rail engineers have done an incredible job installing 11 miles of new track and 24,000 sleepers, bringing us closer to seeing regular passenger services restored later this year.”
Richard Burningham MBE, the manager of the Devon and Cornwall Rail Partnership, added: “Hats off and many thanks to all involved in this tremendous feat. To have laid 11 miles of track already is fabulous and it’s been great to see video of the very innovative piece of kit which has helped on the Dartmoor line. Thanks too to the government for funding all this work.”
An NTC machine is now also being used on the second phase of the East West Rail (EWR) project ahead of its planned opening in 2024.
The clear success of NTC machines cannot be underestimated, and as initiatives such as Restoring Your Railway seek to enable the reopening of mothballed or closed lines, such as the Dartmoor line or EWR, the NTCs will remain a key component of the country’s rail infrastructure offering.
To have laid 11 miles of track already is fabulous
“ “
Out of sight, out of mind is an apt description for the miles and miles of control, communication and power cables that the railway depends on every day
Look out of the window on any long, and perhaps tedious, train journey and what do you see?
On the right, there is probably the other track that carries trains in the opposite direction. From time to time, a train will scoot past, so quickly as to make you jump. Beyond the track, and the fence that guards the railway, lies the British countryside, interspersed with villages and towns along the way.
On the left is the strip of land alongside the railway known as ‘the cess’. There is actually a cess alongside the other track out of the righthand window, but that is perhaps too far away to see properly. In either case, it is an area that is kept at a lower level than the track, to help provide drainage. It is also where track workers can walk, and in some places you will see the gravel paths that form a safe walking route.
You will also see various items of railway paraphernalia. Lengths of rail – not all of it scrap, sometimes it is new rail waiting to be installed –
discarded sleepers, white sacks of ballast and other aggregates, posts, old lineside cabins, the universal grey location cases and a seemingly endless off-white ribbon that runs alongside the railway for miles on end.
This is the ‘trough’, where the cables that support the railway are tucked away safely to prevent damage
“
This is the ‘trough’, where the cables that support the railway are tucked away safely to prevent damage. Signalling and telecommunication cables, low and high-voltage power cables, all hidden from site. Occasionally, when the ‘troughing’ is in poor condition, you can even see the cables through breaks in the trough.
Looking at it from inside the train, it seems to be a simple product.
A three-sided trough is mostly buried in the ground alongside the track, or embedded in the ballast shoulder, covered by a flat, rectangular lid. Sometimes a lid is cracked or broken, or even missing, but it all passes by too quickly to see easily.
However, like all products that seem simple, there is more to cable troughing than meets the eye.
In its simplest form, a trough is made up of a three-sided concrete element with a square or rectangular cross section. They are closed off using a flat rectangular lid.
There is some sophistication, most of it not easily seen. The sections have a tang at one end and a rebate at the other, so they can be locked together, and the lids are recessed so they don’t easily slide off. The troughs come in one-metre lengths, though other lengths are available. The also come in various sizes – in the UK the most popular sizes are C-1/8 (internal dimensions 150mm wide x 200mm deep) or C-1/9 (190mm wide x 130mm deep).
Concrete cable troughs have been a feature of the railway since the 1940s. More recently, changes have been made to their design for a variety of reasons. One is ease of handling. Concrete is heavy, and alterations have been made to the formulation to keep the weight down. Most sections are now under 50kg in weight, meaning they are a two-person lift.
Lids have additional recesses, so fingers are not trapped so easily.
A second reason for the design to be modified is security. In recent times, theft of signalling cable – often made out of valuable copper – has increasingly become a problem. In the dead of night, thieves enter the railway, lift trough lids and cut the cables. They then do the same a distance further down the track. Tying one end of the cable to their van, they drive off, dragging the valuable cable out of the troughing behind them.
This type of theft causes many problems, including the cost of replacing the cable and the disruption to services while signalling is out of commission.
So, cable trough lids are now often fastened down, so they can’t easily be lifted, and the cables themselves are clipped or strapped into the troughs, so they can’t be pulled out. Although this slows down legitimate cable removal, during maintenance or replacement, this work can be planned and is better than having to deal with an out-of-commission railway.
Cables are also often doused in Smartwater, which rubs off when they are handled and can be highlighted using UV light and traced by varying the chemical composition of the additives, allowing both thieves and stolen cable to be identified on site and later in the scrapyard.
To overcome the challenge of the weight of concrete troughing, both for manual handling on site and for transport, several manufacturers have introduced their own designs of ‘plastic’ troughing, many from glass-reinforced polymer (GRP).
Conforming to the same internal dimensions as the approved standard concrete troughs, they are considerably lighter and easier to handle and, while there is often a price premium, this can be offset by reduced transportation and handling costs. Again, T-pieces and curves are available.
While cable troughs are not normally intended to be walked on, as the smooth surface can lead to slips and trips and there is always the danger of breaking the lids, many GRP designs incorporate a tread pattern into a curved top surface, so water drains off and a slip is less likely.
One manufacturer has even recently developed a double-width trough with an aggregate moulded into the lid that is actually designed to give a safe walking route, as well as protecting the cables underneath.
While conventional troughs are laid on the ground, or even partially buried in it, there are locations where this is impractical. On undulating ground, or on the side of a slope, it is often easier to mount the troughing on posts.
These elevated systems are more versatile but can be limited as to their size and the weight of cable they can carry.
In addition to straight sections, curves and junctions, these systems need transition pieces from ‘conventional’ systems, both in terms of cross-section but also so they can be ramped up to an elevated position and returned to ground level.
Care must be taken, when using these systems, to calculate the stiffness of the trough and the weight it carries so that the correct span between posts can be specified. And, of course, using it as a walking route is out of the question.
Even with these advantages, there are locations where neither a conventional nor an elevated trough will work.
Through tunnels and alongside track as it runs past station platforms are two cases in point,
and here the cables are often simply hung off the tunnel wall or the platform support face using cable hangers.
Manufactured from galvanised steel, these are available with multiple ‘hooks’ on one vertical plate, allowing any number of cables to be run alongside of the track yet safely out of the way. Cleats are available to lock cables into position, reducing the chance of a cable being dislodged or stolen.
These troughing systems are all very well while cables are being run alongside the track, but what about when they have to cross it?
Concrete is heavy, and alterations have been made to the formulation to keep the weight down
“ “Image: Network Rail Damage caused to cable troughing after the Hillmorton landslip
One solution is to simply cover the cable in a protective orange sheath and run it across on top of the ballast but under the rails. These can be seen all over the railway, but they aren’t good for permanent installations as they have to be lifted every time the track is tamped or the ballast cleaned.
The best but highest cost solution is an undertrack crossing (UTX) – in effect, a small-bore tunnel under the track. These are made by digging a channel under the track and then relaying sleepers and ballast, by using small versions of tunnel-boring machines with a flexible tube being fed through the resulting bore and the cables safely installed inside, or by directional drilling and then ‘blowing’ the cable through the resulting hole attached to a small parachute.
Hollow bearers (sleepers) are the halfwayhouse solution. They allow the track still to be maintained and tamped as they act as standard sleepers, but their hollow nature means that cables can safely be run through them out of harm’s way.
Often steel fabrications or GRP mouldings, they can even be installed on an existing railway line by digging out and removing a standard sleeper and replacing it with the hollow bearer.
Conventional concrete sleepers with a groove cast into them are an alternative solution.
So, next time you look idly at that thin ribbon of cable trough running alongside the track, just ponder this question. If Network Rail has 20,000 miles of track in the UK, how many miles of cable trough is that? And at one metre per section, how many individual elements?
To make the mental arithmetic even more complex, how many cables are inside each trough? And how many miles of cables does that add up to? It should help to pass the time on your journey…
Image: xxxx Green trough walkway Image: Network RailIf Network Rail has 20,000 miles of track in the UK, how many miles of cable trough is that?“
“Image: Trough-Tec Systems Cable troughing installation
Stadler’s impressive units on display at Berlin trade show as Liverpool City Region’s Metro Mayor looks forward to seeing the trains in action by the end of the year
Stadler unveiled the first Independent Powered Electric Multiple Unit (IPEMU) for the Merseytravel network at the InnoTrans trade show in Berlin on 22 September.
The Class 777/1 is one of 53 four-car trains ordered by Merseytravel for the Merseyrail operator. While 46 will be electric multiple units (EMU), seven are IPEMUs equipped with a battery-based energy storage system. The new battery traction equipment is mounted in the underframe and the cooling system is located on the roof. The interior and the number of passengers it can carry are the same as the EMU, with the IPEMU retaining all the basic functionalities of the Class 777.
Stadler says that IPEMU trains can operate beyond the electrified third-rail network on non-electrified systems, preventing costly infrastructure changes, and allows for operators to extend their network beyond the existing electrified network.
This provides greater flexibility and means more services for passengers, says the Swiss manufacturer.
While an IPEMU is running on the electrified network, the batteries can be charged from the third rail as well as through regenerative braking.
undergo more than 10,000 charge/discharge cycles which, says Stadler, is about four times the lifetime of a battery used in electric vehicles (EVs). The battery/vehicle weight-ratio of a Tesla is about 25 per cent, while the ratio of the IPEMU is only about six per cent.
The IPEMU is capable of reaching a speed of 50mph (80km/h) when fully charged, and able to cover a distance of 34 miles (55kms) on one battery load, and it retains all the basic functions of the original Class 777 EMU design.
The belief is that IPEMUs have the potential to replace diesel trains, which helps operators and local and national governments meet de-carbonisation targets. Stadler says that passengers will not notice the transition from EMU to IPEMU mode. Furthermore, IPEMUs avoid passengers having to change trains, enhancing the journey experience and reducing travel time.
When in traffic, IPEMUs can be recharged in less than 15 minutes and the IPEMU battery can
Ralf Warwel, sales director for the UK and Ireland at Stadler, said: “This ground-breaking vehicle will be the first of its type to operate in the UK. It exemplifies Stadler’s focus on green technology, highlighting our determination to work with operators and governments all over the world to cut carbon emissions and tackle the climate crisis. It will boost the Merseyrail network, providing greater flexibility for our client and helping provide a more compelling transport offering for the residents of the Liverpool City Region.”
This groundbreaking vehicle will be the first of its type to operate in the UK
“ “Image: Statler
Liverpool City Region Combined Authority’s programme director David Powell said: “The IPEMU concept has been an integral part of our strategy for the new fleet of trains for the Liverpool City Region. We are delighted to be one step closer to realising our vision of an expanded Merseyrail network without the need for electrification infrastructure. This will bring significantly improved, high quality service and direct connectivity to a greater proportion of the 1.6 million people in our city region.
“The IPEMUs will also contribute to our carbon reduction strategy by using only 20 per cent of the energy of the diesel powered trains that they can replace.”
Currently no Class 777s have yet entered traffic despite being ordered in December 2016, with several of the trains now in the UK undergoing testing and commissioning. But good news is now on the horizon in that respect.
The aim is for Stadler Class 777s to enter traffic on Merseyrail before the end of the year, according to Steve Rotheram, Metro Mayor for the Liverpool City Region.
Speaking at the launch of the first IPEMU at on 22 September, he said: “Hopefully this will give you an understanding of where these trains aim to be running before the end of this year.
He added: “As you know, public transport is so much more than just infrastructure. It’s about connecting people with opportunity and that’s what we intend to do. We intend to connect people with jobs, education, training opportunities, cultural attractions, and each other. These new trains will be a giant leap forward in making that vision a reality. We’ve invested £500 million in the city region, not just on the trains, but with making improvements to our platforms. We want to improve the passenger experience. We’re doing that with improvements to accessibility in our stations. And we’re also building new stations.”
“When I was elected as the Mayor I promised that we would build a better, faster, and cheaper and greener public transport system. These are definitely cleaner and greener. Let’s face it, they look fantastic. And when you get a chance, go and have a look inside them. That’s the experience that the people who travel on these every single day will be getting.”
They will provide 50 per cent more capacity than the Class 507 and 508 EMUs they will replace.
The Mayor also referred specifically to the benefits the IPEMUs, the first of their kind to be used in daily traffic in Britain. He said: “These trains will go to places that currently we can’t get to because we have a third rail infrastructure.
“So this is going to open up huge possibilities for us. We’re rightly proud of what we’re going to do with these. They have been designed in consultation with the public and are the most sophisticated trains, but also the most accessible fleet in the UK.
offers bespoke services throughout the UK, such as security
Public transport is so much more than just infrastructure. It’s about connecting people with opportunity
“ “
“You’ll see the sliding step technology as you come into a platform. These will come in absolutely level so people with accessibility problems or people with disabilities can use them.”
The Mayor also told invited guests how the trains have been bought by the region rather than a leasing company. He explained: “These trains are the first in the UK that have been bought by us the public, for the public. And we will be putting public back into public transport in the Liverpool City Region, integrating this with our buses and our ferries.”
The Mayor later exclusively told Inside Track at the InnoTrans show in Berlin on 22 September that he wants a transport system similar to London, however he also believes that Merseyside’s system will be better.
He said: “From day one, it’s been my ambition to develop a publicly owned, integrated transport system that we can be proud of.
“I actually want something like London, we call it a London-style with better ticketing, better accessibility, clean and greener and cheaper.
“These new trains that we’re launching today [22 September] are battery-operated, and these will take a sub-part of the network that previously we couldn’t get to. That means that we can open up really good quality alternative rail travel to many people who currently use the car, and to areas that have been left behind.”
He says ordering the IPEMUs made sense after the Office of Rail and Road (ORR) didn’t really want to extend the third-rail electrification used in the region.
“These battery-operated trains will take us to some of the outskirts of the City Region where people have wanted something. Merseytravel will be going to places that actually haven’t been Merseyside. They believe in being part of it geographically but haven’t felt part of the Merseyrail network because those trains never went there.”
He told Inside Track that Merseytravel could now plan for the future and investigate the infrastructure required to expand services. He says that Class 777s will run initially to Kirkby, but that the IPEMUs will run to Headbolt Lane, which is expected to open next year. There are ambitions to run beyond that to Skelmersdale as well. He said: “That means then we open up a whole conurbation who have not had the opportunity for rail travel. Skelmersdale is one of these new towns.
Owner Merseytravel
Operator Merseyrail
Axle
Supply
Axle
Seating
Maximum
Battery
Installed
Recharging
Floor
Entrance
Coupler
Vehicle
Bogie
Sixty years ago they were promised the station and they still haven’t got a station. So I mean, that’s for the government to do because it’s outside of our jurisdiction, but we would then be able to run our services to that area.”
Under the bonnet Technology-wise, the trains are manufactured using a lightweight carriage body made of extruded aluminium profiles. The electrical front door is combined with a sliding step for front-end evacuation and detrainment between two units, which is a patented solution. The Class 777s are fitted with newly developed Jacobs motor and trailer bogies with internal bogie frames and pneumatic suspension. The trains are also fitted with plug doors and automatic sliding steps and have been prepared for later retrofitting of European Railway Traffic Management System (ERTMS) equipment. The trains also meet the highest fire protection requirements EN 45545 Level HL3.
Internally, the trains are fitted with what Stadler describes as “a bright, passenger-friendly interior with an iconic design.” Class 777s also have wide entrance doorways for rapid passenger flow, level access at all entrances, a spacious multifunction area and wheelchair spaces. Advanced passenger information system, CCTV and Train Connectivity and Information System (TCIS) are also fitted to the trains. For staff, there is a spacious cab with enhanced driver sight lines, ergonomically designed driver’s desk and automated cab side doors for comfortable access.
The Class 777s are set to revolutionise railways in Merseyside. Not only will the battery technology enable new routes to be opened up for the region, but the accessibility features for the trains are a real game-changer for the industry. It’s going to be fascinating to see how their introduction goes and how Merseysiders react to them.
Surveying the railway is nothing new. The Victorians surveyed the route when they first constructed the network, and then surveyed it again afterwards to record what they built.
Since then, every time the railway is extended or modified, the same process takes place. A survey is carried out to establish the starting position, and then the finished work is surveyed when it is handed back to the infrastructure owner. But once the work is finished and trains start running, why does the railway have to be continually surveyed?
The answer is because the railway is not static. It is a ‘living’ thing, with its components constantly on the move. That may be a surprise. After all, the railway is a major piece of engineering. So how can it move enough to need continuous surveying?
The most obvious part of the railway network is the track. Two ribbons of steel, 1,435mm apart (on the British main line network) and anchored firmly to a concrete, wooden or sometimes steel sleeper every 650mm or so.
But that track sits on a bed of ballast – granite chippings that interlock and hold it in position.
That ballast compresses over time, requiring the track to be tamped – to be lifted so the ballast underneath can be stirred up and refreshed, after which the track is laid back down again in its original position. In the process, the track may move sideways a little, just a few millimetres.
will the train be to trackside structures? Will it still clear the platform edges of every station along the route? And what if one of those platform copers has had a knock and now sticks out just a little further than all the others?
The only way to answer those questions safely and with certainty is to do a survey.
Network Rail alone has 20,000 miles of track –that is 40,000 miles of rail. To spot defects in that rail will therefore take a lot of walking, or to have an automated survey system.
That amount is seemingly insignificant. But repeat it a few times, and deal with frost heave and any other movement of the underlying ground, and those few millimetres become a few centimetres.
Now the question becomes how much closer
When metal components are loaded repeatedly, they can suffer from a phenomenon known as fatigue. A load very much less than that which would normally cause the component to break can cause cracks to form after a high number of cycles. These cracks then propagate – growing by a minute amount each time they are loaded – until the crack reduces the crosssectional area of the component to such an extent that the load is now high enough to break what remains. This is a fatigue failure.
The railway is not static. It is a ‘living’ thing, with its components constantly on the move
“ “
Infrastructure owners have to know that their railways are in good condition and capable of operating safely. But, with mile upon mile of track to check, how do they do that?
Whenever a wheel passes over a length of track, it compresses it. The repetitive nature of this compression results in rolling contact fatigue, generating cracks in the surface of the rail. Left untreated, these will propagate and the rail will break.
Grinding or milling the surface of the rail – and there are high-speed machines that can do both –removes the surface layer and the cracks. There is now nothing to propagate so the rail is safe for another period until the repetitive loading starts to generate cracks once again.
These cracks are almost impossible to see by visual inspection. However, eddy-current testing can detect them as it recognises the disturbance in the magnetic field caused by the cracks. Trains can be fitted with eddy-current devices that will test for these cracks – another form of survey.
Other track defects can be cracks and broken rails caused by expansion in hot weather, steel becoming brittle in cold weather, manufacturing defects, damage from flats on rail wheels and broken joints.
Rail clips that fasten it down to the sleepers can break or fall out, allowing the rail to move. Ballast can become contaminated and not let water drain away, causing ‘wet beds’ and an uneven ride.
There is even the dreaded ‘cyclic top’, almost invisible to the naked eye, in which the rails undulate and cause an unpleasant rocking motion in trains that pass over them – and which can cause derailments if they are bad enough. All can be detected by regular track surveys.
Apart from the track itself, the railway is affected by the environment it runs through. The most obvious variable is vegetation. Trees and bushes grow, and before long they are
overhanging the railway, damaging trains and obscuring signals.
Trees also fall on the line, causing more damage, especially if trains run into them. Much better if trees at risk of falling are identified in advance and cut down before they cause a problem. It isn’t just trees that fall. It is less common, but not unknown, for signal posts and other lineside items to fall down as well, perhaps because they rust through at the base.
Then there is debris, often blown onto the line but sometimes left accidentally or maliciously. Trampolines are a favourite, blown from lineside gardens during storms, along with supermarket trolleys, bicycles, concrete blocks and even maintenance work trolleys forgotten after overnight work.
Many of these are noticed by the driver of the first train of the day, but there is also a forwardfacing video camera – another form of survey.
The UK places a legal requirement on the infrastructure owner to fence the railway. Not every country needs this, but the UK does. Many fences can’t be seen from the train, so checking them needs another form of survey. Fences not only prevent access by people – a cow is a large animal and can derail a train if it gets on the line.
Network Rail owns 30,000 bridges, tunnels and viaducts, and there are others on the UK railway owned by Transport for London (TfL), other railways and the highways authorities.
Normally they don’t cause much problem although they have to be checked periodically for structural integrity. But low bridges seem to be a magnet for high-sided lorries and double-decked buses. Every major bridge strike closes the railway while a survey is carried out, and the wrecked vehicle is dragged out from underneath.
Tunnels can spring a leak, culverts can become blocked by detritus and overflow, roofs can blow off buildings… there is always something that needs checking.
Overhead electrification cables can sag in hot weather. They can also be torn down by a train with a damaged pantograph, but that usually
makes such a mess that a survey is hardly needed to identify the problem! However, a survey of the damage will enable repairs to be planned.
Just as there are many reasons for surveys to be carried out, there are also many ways to do them.
To check the overall condition of the railway is obviously a task for automated systems. In the 21st century, the railway simply doesn’t have the manpower – or the budget – to do it any other way.
To cover the ground – and 20,000 miles of track is a lot of ground – Network Rail has a fleet of track inspection trains that covers the entire network on a regular basis. Chief among these is the New Measurement Train (NMT), a High Speed Train (HST) converted from a passenger train that can survey the railway’s infrastructure at 125mph.
Having been in service for more than 15 years, the NMT is hardly new, although it has been continuously updated to include the latest inspection technology.
Network Rail has a fleet of track inspection trains that covers the entire network on a regular basis
“ “Aerial surveys can carry out visual inspections
With over 20 years of Rail and Construction industry experience, our familyrun company provides expert advice and cost-effective solutions to all sectors looking for experts that they can rely on. Delivering safe and sustainable solutions at the forefront of innovation and technology, ensuring the highest quality results first time, every time. We can assist clients from advisory and design to compliance and delivery, providing tailor-made solutions to meet clients’ needs.
Installation of all Piled foundation - bored, driven & screw piles
Erection and installation of OHL Gantry structures (masts, booms)
RED, LOC and DNO foundations and platform installations (GI, Design & Install)
Platform renewals and
Cess walkways and throughing routes
Fencing and Access stairways
Site compound establishment and access road
Holes
Excavation and installation of concrete bases
Cess
The reason for the high-speed capability is so that the NMT, and the other trains in the fleet, can operate between passenger services without slowing them down, meaning they can run during the working day and not be confined to purely night-time operation.
The work is continuous, the NMT surveys 4,800 miles of track every two weeks, carrying out shifts of up to 1,000 miles at a time and covering 115,000 miles in a year. It has 14 sensors on board, from linear variable differential transformers and lasers to gyroscopes and accelerometers. It has lights and cameras on the roof to monitor the condition and position of overhead wires and has cameras underneath to look at the track.
The technique used on rail inspection is known as Plain Line Pattern Recognition (PLPR). Cameras mounted underneath the trains capture an image every 0.8mm, taking 70,000 images a second at the top speed of 125mph.
PLPR identifies potential defects and sends them to Network Rail’s expert inspection team in Derby.
Local track section managers then receive information about confirmed defects, enabling engineers to target track maintenance more effectively. In addition to the NMT, four other trains in Network Rail’s fleet are fitted with PLPR. Further vehicles test other elements – the MENTOR (Mobile Electrical Network Testing, Observation and Recording) coach is fitted with a pantograph, so the overhead line can be measured while under load.
Increasingly, lines are being surveyed using in-service trains. Monitoring equipment is attached to the buffers at the front or rear of a train, or mounted in the cab windscreen, and data is recorded as the train runs through a section in the normal way.
As more and more equipment is mounted on service trains – rail cameras, accelerometers, pantograph monitors and so on – engineers will have increasing amounts of data to work with. Just the NMT alone generates 10TB of image data every 440 miles. (1 terabyte (TB) = 1,000 gigabytes (GB); a USB memory stick is typically 8 or 16GB of storage, so 1TB is equivalent to 60-120 memory sticks!)
In localised areas, there is no real alternative to having surveyors out on site. Surveying for a trackrenewal scheme that may be only 400 metres long is not a job for the track-inspection fleet.
The general area is surveyed using traditional equipment. The old-fashioned theodolite has been replaced by a total station, and the striped pole with a variety of prisms, but the general philosophy remains the same – plotting the horizontal and vertical position of a series of points.
This information is also used to calculate clearances between the train and structures, especially important on those routes where tilting trains are in operation, or where heavy freight trains run.
The track itself is checked using a trolley fitted with inertia sensors, gyroscopes, accelerometers and a very accurate GPS or GNSS positioning system.
These capture the absolute position of the rails, cant (the tilt between the rails) and gauge. These are captured as the operator pushes the trolley continuously along the rails, or when stopping at specified intervals.
Ground surveys, including ground-penetrating radar, may be needed to define the condition of the track bed and the terrain underneath.
The gloriously named Rail Trackform Stiffness Tester is designed to do just what it says – a weight is dropped onto the trackbed and the deflection response of the ballast, sub-ballast, formation and subgrade is measured using geophones, enabling the layer stiffness to be determined.
Fencing surveys are most easily carried out from the air. A drone can follow the line of the fence and is reasonably cheap to operate. However, it has to remain within line of sight of the operator, so the survey will have to be carried out a few miles at a time.
Fencing surveys are most easily carried out from the air. A drone can follow the line of the fence and is reasonably cheap to operate
“ “
A helicopter, despite its high operating cost of almost £2,000 an hour, can carry out far more work in that time and may actually be more cost effective. Aerial surveys can also assess the growth of vegetation and carry out visual inspections on hard-to-reach places such as the underside of viaduct arches, which otherwise can only be checked by abseilers or workers using specialised access equipment.
A number of viaducts and bridges have their piers in rivers or estuaries. Not only does their condition need monitoring, but the ground surrounding them as well. Scour, when fastflowing water washes material away from the river or seabed and undermines the structure, is a particular problem.
Often, the only way to check for this is by sending divers down to use their fingers, as
experience in providing innovative, safety-driven capture solutions allow railway operators
reduce impacts on operations
enabling digital management
existing aging assets.
the water may well be so cloudy that visual inspection is impossible. Whether using drones or helicopters, high-speed trains or total stations, track trolleys or geophones, all of these survey methods have one thing in common – their use of technology. As that technology becomes lighter, quicker, more innovative and (hopefully) cheaper, surveying the railway will continue to improve safety and passenger comfort.
When it comes to the different modes of transport, rail is a comparatively low-carbon way of travelling and moving goods. But with the UK Government’s aim of achieving net zero emissions by 2050, the decarbonisation challenge faced by the rail industry is still significant.
Today much of our energy must be focused on electrification of the lines, with 278 miles (448km) of railway needing to be electrified each year to meet Network Rail’s target of net zero. However, with only 111 miles (179km) electrified between 2020 and 2021 according to the Office of Rail and Road, and electric trains estimated to emit between 20-35 per cent less carbon into the atmosphere than traditional diesel-powered engines, it is important to consider other areas that need improvement too.
One such way is to harness the power of data and technology. From digital twins that provide up-to-date asset data to support operational planning and the management of assets, to IoT devices being placed trackside to monitor rail positioning and much more. In fact, technological advancements, such as design tamping, can make improvements across the network beyond driving down emissions. It can also improve efficiency and passenger ride quality.
Tamping enables rail operators to correct track alignment. It’s a vital aspect of railway maintenance and plays an important role in preventing derailments. By maintaining an optimised track rail operators can cut carbon emissions, provide a safer working environment, and reduce maintenance costs. Improving on our traditional tamping methods presents the rail industry with an opportunity to get closer to realising our emission reduction targets.
Traditional ‘compensation tamping’ is a three-stage process: a tamper collects information about the current relative geometry of the track, the machine calculates how far the track needs to be moved to bring it within specification, and the tamper then mechanically repositions the rail and packs ballast under the sleepers to keep it in position.
Although this conventional approach creates a safe track geometry, it does not optimise the alignment. Over time, with repeated cycles of tamping, this can lead to longer wavelength problems such as multi-compound curves and poor cant build-up at the approach to curves. Compensation tamps are also generally constrained to maintenance tolerances of 25mm X and Y and 40mm in Z from the original designed position so alignment can’t be optimised. Over time, and after several compensation tamps, the position of the track will no longer be in the original designed position, and this will necessitate the need for more gauge clearance checks to be carried out.
Design tamping is a process where a survey team is sent to site to collect information on the current track position to then be able to design the track to an optimal position. The tamper will then be sent out to reposition the track to the designed position. This is also used in applications such as managed track position (MTP), absolute track position (ATP) and to maintain through alignment design (TAD).
The application of smart technology has taken tamping to a new level. Fugro RailData® solutions include Smart Tamp – a modified approach to design tamping. The system approach relies on creating a track baseline position or ‘geodetic backbone’ created using Fugro’s RILA® survey system.
Changes in track position are then calculated automatically using information collected periodically with RILA® with the backbone model being updated. This means that new track alignment designs can be created at any point in time without the need to commission a track survey or put surveyors on the track. Mounted on the front of regular in-service passenger trains, RILA® surveys the network at normal track speed (up to 125mph), collecting geodetic referenced data on the track and rail corridor with millimetre precision and at a higher density than conventional track surveys.
The RILA® data is post-processed, and a 3D laser point cloud is produced, along with absolute track position data.
This data is combined to model the optimum track alignment, while maintaining adequate gauge clearance to structures and a compliant height and stagger for overhead line equipment.
By modelling the track in 3D space in relation to surrounding assets, it is possible to design the new track alignment with confidence beyond the maintenance limits to achieve the optimum alignment for the smoothest ride. Once finalised, the designed alignment is converted into the corresponding track adjustments (lifts and slews) and can be input to the tamping equipment.
The surface derived from the lidar point cloud profile can be used to accurately determine the current ballast volume and the tonnage of ballast needed to bring the ballast profile into line for the new track alignment, providing exact locations of where to drop the ballast. This eliminates the problem of some parts of the track being deficient while others are overballasted. It also introduces new efficiencies, because if there’s not enough ballast available to support the designed track lift, this can be remedied well ahead of the tamping operation. Design tamping using Fugro Smart Tamp is a comprehensive solution that offers more sustainable whole-life geometry, and increased track quality, which ultimately will reduce maintenance costs and improve safety.
Carbon savings
Fugro Smart Tamp gives optimal ride, low dynamic forces, and less rolling resistance between track and rolling stock. This offers a saving in the amount of traction power that is required to power a train. Better aligned track with lower rolling resistance delivered through design tamping will offer approximately five per cent saving to traction power, cutting both the amount of electricity and diesel used.
In 2019/2020 Network Rail used 4256 million kWh of traction electricity on the electrified parts of the network and 648 million litres of diesel on the non-electrified parts. With the potential saving of CO2e set at five per cent we can estimate a saving of 144,600 tonnes of CO2e released into the atmosphere. This is based on saving 213 million kWh of electricity and 32.4 million litres of diesel.
Further, by collecting survey data from RILA®, there is the potential to save an additional 217 tonnes of CO2e by not having operatives travel to site to carry out surveys. This has been calculated using an average journey distance of only 12 miles (20km) so the actual saving may be higher as operatives often travel further to reach their work sites.
Extension of life to assets
The Network Rail sustainability strategy 2020-2050 explains: “We use lots of materials to build and maintain the rail network, spending around £7 billion a year on our supply chain. Our activities produce a lot of waste; 2.1 million tonnes in 2018/2019. We must use less and manage unavoidable waste better. We have a huge opportunity to contribute to a more circular economy, where we extract fewer virgin resources from the planet, keep materials and resources in circulation and waste to an absolute minimum. This action will also help us significantly reduce our carbon emissions.”
Using Smart Tamp, we’re able to perform asset management on the entire rail network. By monitoring the status of all assets within the rail corridor and performing timely maintenance, a new level of cost-efficiency can be achieved. Reduced wear and tear of track and rolling stock allows for reduced renewal and a 20 per cent reduction in track maintenance. This will in turn increase the life of track assets and lower the whole life carbon pricing for the entire network.
With design tamping based on traditional surveys, the survey team needs to work on or near the track, which incurs a safety risk. Approximately 8800 survey shifts would be needed to execute surveys across the whole of the network. Having on average five operatives per survey team (including protection), and working a normal engineering shift, this adds up to the total 352000 exposure hours per year.
The RILA® crew is on the track only at the beginning and end of a shift, while mounting the survey unit to a train. This means that two people are on the track for four minutes, two minutes to mount RILA® and two minutes to dismount, reducing ‘boots on ballast’ by 97 per cent.
Currently, for compensation tamping, time is lost on the shift as the tamper itself needs to survey the track during the night. In a tamping night, the tamping machine is on location for approximately four hours. The first hour is needed to do this survey run, set back and calculate/approve the compensation lifts and slews which are to be applied. This reduces the amount of time available for actual tamping by 25 per cent. By having the full amount of time to complete a tamping shift (minus travel to site) the tamper will be able to complete 25 per cent more meterage per night, cover more sites or reduce the risk of overruns occurring.
With the Network Rail budget on renewals and maintenance available, it is possible to estimate the long-term savings for Network Rail. £778 million is spent on maintenance and the percentage of cost reduction, based on coordinate-based maintenance, is set at 30 per cent. The long-term savings on track maintenance would then be around £233 million per year over the whole network.
By introducing Smart Tamp to the network, there is the potential to change the way data is collected and how tamping is implemented. As a result, analysis of the data captured can help overhaul and modernise track maintenance practices, as well as improve safety across the network.
In addition, it offers a way to decrease carbon emissions and cut down on track worker exposure hours with a solution that will also offer considerable financial benefits and improve ride quality for passengers and freight. Ultimately, this technology will see the industry benefit across the board and enable a smoother ride for passengers in the future.
The next stage in the process of constructing the exciting Global Centre of Rail Excellence (GCRE)
will take place on 2 November with a ‘meet the buyer’ event in Cardiff.
GCRE is inviting prospective supply chain partners and suppliers to the event to find out more about the contracts, which are expected to be worth in the region of £250 million.
Spanning the former Nant Helen opencast site and Onllwyn Washery in Neath Port Talbot and Powys, South Wales, GCRE will feature the UK’s first net-zero railway and become the ‘one-stop shop’ for railway innovation, from research and development, through testing, verification and certification, to applied innovation on main-line passenger and freight railways.
The facility will include two 25kV electrified test loops, one being a 4.5-mile (6.9km) highspeed rolling stock track with a maximum speed of around 110mph (180km/h) and the other a 2.8mile (4km), 40mph (60km/h) test track.
A formal procurement process for the GCRE project is expected to commence early next year. This may potentially include works associated with passive rail systems including permanent way, overhead line electrification, civils works and active rail systems such as signalling, SCADA, power and telecoms, fencing, depot and buildings-related requirements along with the bulk purchase of materials.
Kelly Warburton, GCRE chief commercial officer, said: “This is an invitation to those interested in being part of the wider team that will deliver this transformational project. We’re beginning early consultation with prospective suppliers about the opportunities, to discuss current thinking and set out our plans to deliver a modern and dynamic test facility for international rail innovation with leading-edge research and development facilities.
“GCRE has the potential to transform the railway industry in the UK and across Europe and we want the supply chain to be part of this with a real focus on collaboration and a genuine sense of partnership.
“There will be plenty of opportunities to engage and be part of our journey. Beginning the discussions now will help suppliers to introduce themselves to our team and understand the opportunities available.”
A further development for GCRE is the purchase of three five-car Siemens Class 360/2 trains from Rail Operations Group. Less than 20 years old, the trains will be moved from storage at MoD Bicester to Wales next year when the site’s commercial rolling stock storage facility becomes available to the wider market.
The trains will be used as part of the GCRE research and innovation offer and will be available to the industry as test train ‘mules’ to test European Train Control System (ETCS), novel train control, traction and suspension and many other railway innovations for the industry.
The shorter loop at the site will be dedicated primarily to infrastructure testing, where heavy passenger and/or freight trains, including the Class 360s,will operate for 16 hours a day, five days a week to provide the 20 MGT/60,000 axle passes ‘load’ on the infrastructure loop. GCRE will provide state-of-the-art rolling stock testing, infrastructure testing and storage and maintenance for both the British and international rail industries.
Established in 2021, GCRE is a wholly owned subsidiary of the Welsh government with an initial commitment of £50 million.
The UK government is expected to confirm a further £8 million for research and development along with capital funding of £20 million. An investment prospectus designed to attract private funding for the project is also in development ready to launch this year.
As well as the test tracks, other facilities at the site will include a dual-platform test environment, rolling stock storage and maintenance facilities, operations and control offices, staff accommodation, shunting staff facilities and connections to the nearby main line. There will also be state-of-the art secure testing environments; equipment, systems and communications development facilities. Education, training, visitor and conference facilities and an industrial development zone are all envisaged in the wider site. Registration details for the 2 November event can be found at https://directory.railbusinessdaily. com/directory/gcre/
RBD Community’s Eli Rees-King writes about a trip to InnoTrans and the exciting launch of OnePlace
Heading to InnoTrans last month was a first for the RBD Community and with a tight schedule, it meant that with precious little time to get everything done, the time spent in Berlin was a whirlwind of meetings and what felt like thousands of steps to walk the halls of the Messe!
For those who haven’t experienced InnoTrans, it really is an immersive experience of all things rail and I can highly recommend both visiting and exhibiting. Where else in the world can you go where you can see the latest innovations and technology across the entire spectrum of rail infrastructure, freight, and transit?
The event organisers reported 140,000 visitors from more than 131 countries went to see
displays from 2,834 exhibitors and 56 countries.
Meeting up with members is always a highlight (and I am only sorry we didn’t get to meet up with everyone!). Looking ahead to the next few weeks we have some more exciting announcements to make which will further strengthen the RBD Community and its commitment to members.
We are delighted to have launched OnePlace and it’s been great to hear the feedback which has been extremely valuable. OnePlace will be a central feature of membership with tools and resources constantly being updated. Please keep an eye on the notice board for the latest
updates on events, special offers, important announcements and opportunities.
The next development phase for OnePlace will focus on MarketPlace – the one-stop shop for business support/specialist service discounts and offers exclusive to members. If you are a member of the community or an organisation with a discount or special offer you would like to offer members of the community, we would love to hear from you!
To contact the RBD Community team email: community@railbusinessdaily.com
For more information on how to join the RBD Community and the benefits of being part of this vibrant and agile membership, go to www. community.railbusinessdaily.com
As every gardener knows, over the British summer, when warm days mix with a fairly constant supply of rain (in most years), the lawn grows like crazy and needs constant cutting while the shrubs, trees and bushes try to take over the garden
This doesn’t just happen in suburbia. Network Rail also has a garden, although it is rather larger than most. The railway estate covers 50,000 hectares (123,000 acres or 193 square miles) in which grow six million trees. A further seven million trees grow outside Network Rail’s boundaries but are within 60 metres of the railway.
In between all those trees grow a variety of grasses, wild plants, brambles, scrub and saplings. As in a private garden, if nothing is done, nature will quickly take over.
On top of all this, some areas of the railway estate are infested by invasive plants, such as Japanese knotweed, and these have to be rooted out. Special measures are needed for their disposal.
Of course, this is nothing new. The railway has always run through open countryside and, even in urban areas, contained areas of wild vegetation within its boundaries. In older days, when labour was comparatively cheap, work gangs were assigned a section of route and they kept the grass short, cut back bushes and felled trees that were too close to the line and could
pose a threat if they were to fall onto tracks or overhead power lines.
Today, even though Network Rail employs 40,000 people directly and many more as contractors and subcontractors, labour is in short supply.
In addition, the UK has become more conservational in its approach. Nesting birds are protected, as are many forms of wildlife, from bats to badgers. The latter, even though being culled in some areas, are protected under the Protection of Badgers Act 1992 in England and Wales and by even more protective legislation in Scotland.
Yet nature still has to be kept at bay. Otherwise, trains can be damaged by foliage overhanging the railway, lines can be blocked when trees fall on them or shed branches onto them. In 2015, 1,000 trains collided with fallen trees or large branches, so it is a major problem.
or large
Leaves on the line can cause traction and braking problems and long dry grass poses the risk of fires. Indeed, during the days of steam, grass was kept short for that very reason. Modern diesel and electric trains don’t cause the same problems, but steam trains still run on the railway, hauling heritage tours. On 2 September 2011, fires caused in the Doncaster area by former Southern Railway ‘King Arthur’ No. 30777 Sir Lamiel resulted in disruption to the timetable and Network Rail introduced a blanket ban on steam locomotives using the East Coast main line.
Returning to the garden analogy, it is important to plan where plants grow, bearing in mind the size they will become when fully developed, and to separate good plants from weeds, though of course they are all plants, just weeds are not wanted or are growing in the wrong place.
The same rules apply to the railway. While brambles and Japanese knotweed are definitely ‘weeds’, others have to be protected and nurtured. For example, in the Avon Gorge on the Portishead line, there are six rare species of whitebeam trees on the cliffs above the River Avon that can’t be found anywhere else. They have all evolved within a self-contained ecosystem and have to be carefully managed, under the supervision of Natural England, to ensure the rock faces can
be kept safe while protecting the trees. Older, or ‘veteran’, trees are a fixture of the railway landscape.
Many of them existed even before the railway. Some are protected by legislation. Veteran trees are important as deadwood habitats for rare fungi, invertebrates, lichen, birds and bats – they have a structural complexity providing many habitat niches that do not exist on younger trees.
The biggest trees on the network are an avenue of coast redwoods (sequoias) either side of the railway near Bradford on Avon station. The largest is 32 metres tall and 2.5 metres in
diameter. They are likely to date back to when this stretch of railway was built in the 1830s, which would mean they would have been some of the first coast redwoods to be grown in the country.
In 2017, Network Rail commissioned an aerial survey covering all 20,000 miles of track as part of the Offering Rail Better Information Service (ORBIS) programme. This provided engineers with a ‘heat map’ indicating higher priority problem trees or overhanging tree canopies which needed attention before they could fall onto the railway and cause delays to train journeys.
Surprisingly, it wasn’t dead or dying trees that caused the problem. Paul Meads, head of lineside safety at Network Rail at the time, said: “Our analysis revealed the majority of trees that fall on the railway during storm conditions are healthy – yet previous inspections may have assessed these as lower risk. We’ve surveyed up to 60 metres either side of the railway covering 20,000 miles and catalogued over 100 different attributes per tree including height, thickness, health, slope angle, proximity to bridges and power lines etc, which are measured to predict the risk an individual tree represents to the railway.”
Using this information, asset engineers were able to identify areas to be managed, resulting in both greater safety and reduced costs as local tree surveys were no longer needed.
On 28 November 2018, the Department for Transport published the findings of the Varley Review of Network Rail’s approach to vegetation management in England and Wales. John Varley OBE, a board member of both Natural England and the Environment Agency, was asked to review Network Rail’s approach to vegetation management across England and Wales.
This followed concerns about the impact that tree felling, considered necessary for the safe operation and performance of the railway, was having on nesting bird populations.
In his foreword to his report, John noted that
there was an opportunity for Network Rail’s lines to be linear routes for wildlife as well as trains and, when ‘connected’ to adjoining landscapes, to be a powerful source of improvement for the country’s natural capital.
Consultancy Ltd (GCL)
Rail Industry
Access and Inclusive Design Appraisals
Access and Inclusive Design
Access and Inclusion Project Management
Access and Inclusion Strategy
Access Audits/Reviews
Promoting a
of
He continued: “Firstly, and foremost, we must value lineside vegetation as an asset, not a liability. We need the right vegetation in the right place, reflecting a ‘balanced scorecard’ which optimises the need for a safe and reliable railway with positive environmental outcomes.
“The goal should be to give lineside vegetation the same weight as other performance assets such as track and signalling. Sending this message to senior managers would have an immediate and positive effect.
“Teams responsible for managing and undertaking the management of lineside vegetation should be trained with the necessary new skills. To support them, the status of those qualified in arboriculture and ecology should be enhanced and they should be widely deployed.
“It can be done: the best practice we witnessed should be adopted across all routes and advice sought from expert bodies. Network Rail should be more consistent in its management across the devolved routes. Crucially, it needs to improve its engagement with stakeholders and the public, listen more, explain why things are done, and seek new partnerships and collaborations.”
The report made six recommendations:
1. The government must set out a clear policy position for Network Rail in terms of delivering for the environment.
2. Appropriate governance must be put in place at organisation, route and project level.
3. Network Rail should publish an ambitious vision for the lineside estate.
4. Network Rail must value and manage its lineside estate as an asset.
5. Network Rail must improve its communication with communities and key stakeholders.
6. Network Rail should lead a cultural change for valuing nature and the environment across the organisation.
Network Rail responded positively to these recommendations. Chief executive Andrew Haines said: “Working with biodiversity and sustainability experts, we are developing an ambitious vision for managing our lineside habitats. Getting the right mix of habitat types alongside the tracks is crucial for safety but can be achieved in such a way that enables a thriving diversity of plants and wildlife, including many protected species.
“I want to record my sincere thanks to John Varley and his team for the important work they have done, recognise the importance of this issue to many local groups and experts, and confirm our commitment to valuing and enhancing nature alongside Britain’s railways.”
For all of the above reasons, Network Rail manages the trees and plants alongside the railway for the safety of passengers and railway workers and to protect lineside habitats.
It’s a coordinated effort – maintenance teams regularly cut back plants that are growing too close to the trains, whereas teams including specialist tree workers will carry out larger scale felling work. Vegetation is routinely cleared from the area immediately next to the track. Where trains run at higher speeds, in cuttings or embankments, or where there are level crossings or overhead line equipment, vegetation may need to be removed further back.
Trees that are, or could be, dangerous, or that could negatively affect the reliability of services that millions of passengers rely on every day, are removed. In addition, there are times when areas of vegetation have to be cleared to help trackside teams examine or repair earthworks and structures or as part of larger programmes of work, such as to prepare for overhead line electrification.
To reduce the problems caused by leaves falling on the railway in the autumn, certain broadleaf tree species such as poplar and sycamore have to be managed or removed.
A mature tree can have between 10,000 and 50,000 leaves, and windy conditions, especially in autumn, can cause heavy leaf-fall in a short space of time while rain means they are more likely to stick to the rails. When trains pass over leaves, the heat and weight of the trains bake them into a thin, slippery layer on the rail, equivalent to black ice on the roads.
Slippery rails make it hard for trains to accelerate and brake effectively. When this happens, drivers have to pull out of stations more slowly and brake much earlier for stations and signals to make sure they stop in time. This can lead to longer journey times and delays.
A build-up of leaves on the tracks can also cause delays by forming a barrier between the train wheels and the electrical parts of the track that help pinpoint where trains are.
When this happens, the trains behind will be delayed at red signals until the first train’s
location is established so control rooms can be confident there is always a safe distance between trains.
Network Rail operates a fleet of leaf-busting trains that move around the railway cleaning the top of the rail by spraying it with a high-pressured water jet to blast away leaf mulch. These trains also apply a gel, containing a mix of sand and steel grains, to help the train wheels run along the tracks as they normally would.
However, much of the work of controlling and cutting back vegetation alongside the line has to be done by hand. Gangs of men and women, often from specialist contractors, attack the undergrowth using hand and power tools, feeding cut material into chippers. Some of the resulting chips are left on site to rot down and nourish the environment while some is taken away for disposal.
Approved herbicides are used to prevent the spread of injurious and invasive non-native plants and to prevent weeds spreading into safety zones where vegetation growth can cause problems.
It’s a never-ending task that can only properly be conducted at certain times of the year, when birds aren’t nesting and when weather conditions don’t make it hazardous for teams to be working on steep slopes and up trees. But it is an essential task that keeps the trains running safely.
Much of the work of controlling and cutting back vegetation alongside the line has to be done by hand
“ “
As a diverse delivery partner specialising in bespoke solutions for infrastructure projects, D2 brings a blend of technological innovation and seasoned industry expertise to complex rail projects. Here we focus on two pioneering pieces of technology to visualise possession data and calculate track access compensation
he company was formed in 2011 by founder David Diesbergen, who continuously found himself facing the same challenges on projects – a lack of early ‘real planning’ engagement, where realistic and achievable programmes are developed by individuals who can relate to both the building and sequencing of works.
Over the past decade, D2 has now expanded its service offering to include planning, constructability, project controls, utilities management, digital technology, information management, capacity planning, collaboration and project management.
Throughout this growth, D2 has always remained committed to its core mission of ‘creating the highest possible value for its clients by viewing actions from their perspective’.
Key to this has been D2 consistently investing in developing elegant digital solutions and innovative products that help solve common industry issues and frustrations – the ultimate goal being to help improve the success of complex infrastructure projects and make delivery more efficient for everyone.
This approach has led to a portfolio of highprofile schemes which D2 has supported delivery of, including The Northern Hub’s Ordsall Chord, and the Transpennine Route Upgrade.
The development of two pioneering pieces of technology – Swiftview and a compensation management tool Schedule 4 Calculator – have helped D2 shine a light on how innovation and development of digital solutions can transform efficiencies on rail infrastructure projects.
Producing weekly possession diagrams is resource-heavy, repetitive work which carries a high risk of human error.
To make access planning easier, quicker, and more efficient, D2 has developed Swiftview, an online resource that enables real-time upload and visualisation of possession data.
Developed by D2’s industry experts and software engineers, Swiftview completely transforms the way project managers interpret and apply possession data.
This bespoke system has been meticulously designed by D2’s specialist system engineers to operate specifically for the rail and freight industry, providing a safer and more efficient way of working.
Swiftview takes possession data in various formats and seamlessly overlays it. This means users can see any possessions, conflicts or areas of concern in seconds, leaving them free to focus on other important aspects of their work.
The system makes long-term possession planning more auditable, scalable and efficient, reducing the errors caused by manual data entry using Excel spreadsheets. This means processes that could take weeks to be completed manually can be completed in minutes.
Swiftview is cloud-based for maximum efficiency, enabling large volumes of users at any given time. Through many years of testing and development, the software is now in use on live rail projects. Matt Sykes, D2’s Head of Digital
Technology, described the software’s formation: “The idea for Swiftview was born from a request that we kept receiving for visualised possession data. Clients were taking basic text-based possessions from location to location, and they wanted a visual solution. They were asking for this on a weekly basis, and it was a manual job of overlaying that footprint on a map.
“So, our digital team developed a solution that can read in possession data that is text-based and then visualise it as a geographical map.”
During the development of Swiftview, the D2 software team faced the challenge of a lack of one complete set of geographic data relating to the rail network. While the network data existed individually, it just wasn’t joined up. D2’s digital technology team collected and checked this disparate data, starting with the geographical line data that make up the network.
Each line was checked and tagged with information such as line of route code, direction, and location. Next, the team aligned each location on the network with PPS location data, at the same time building in the route information for each line.
Image: Mulholland MediaUsing pathfinding algorithms, the team built a system that can analyse the ‘from’ and ‘to’ location for any given possession and determine the geographical lines that make the route up.
There are many different formats that possession data can take and D2 wanted to make the process as easy as possible. The team uploaded possession data using an import system that supports both CSV, PPS and box plan import. This allows the user to import data seamlessly with any validation errors automatically fed back to the user.
The system naturally developed from its original concept, adding automatic import, possessions editing and creation tools directly in the system. This meant it functioned as a possession management tool with geographical visualisation as a feature, rather than the main element.
Through rigorous testing and development with an industry expert product champion, Swiftview is now a fully working possession management tool with a range of features. The product is currently being rolled out on TRU West Alliance.
Matt explained: “Once we have visualised the possession we can integrate different resources, for example, if the possession is running over the weekend, we can ask: ‘what manpower do you need?’ ‘What wagons do you need?’ What materials?’ Then we can start tagging this information onto the possession.”
With support from Innovate UK, D2 was recently awarded a contract to investigate how it could provide digital innovation to the Canadian rail system. For this project, D2 aimed to investigate how Swiftview could be developed in Canada to provide a safer, more efficient way to gain visibility of works with improved access planning and analysis. The focus was to investigate what geographical rail data is available and how it can be used in conjunction with maintenance planning data.
The D2 digital team is now working in Canada supporting the GO Expansion project and the development of its own possession management and access tools, using their experience and lessons learned to shape the direction of the system. The team plans to integrate the visualisation tools developed through Swiftview to bring the same benefits to the project that they have in the UK.
The current rail possessions regime in the UK is known as Schedule 4. This schedule is the portion of track access contracts that sets out the level of compensation Network Rail is required to pay train operators for delays, service changes or cancellations as the result of planned disruption on the network.
There are five different types of disruptions for which operators can be compensated*:
Possessions which are shorter than 60 (continuous) hours, known as type 1 possessions;
Possessions which are longer than 60 hours but shorter than 120 (continuous) hours, known as type 2 possessions;
Possessions which are longer than 120 (continuous) hours, known as type 3 possessions;
Periods of sustained planned disruption (SPD), which are identified when the disruption caused by a possession exceeds specific revenue and cost thresholds;
Late notice (within 12 weeks of delivery of the possession) cancellation of a type 1 possession.
Compensation to operators is a complex calculation and includes factors such as the size and location of the station, the number of passengers using the service, whether a bus replacement is required, and many more. D2 has developed a Schedule 4 tool that allows users to calculate the compensation owed to operators whenever a Network Rail possession affects their services.
The development of the Schedule 4 forecasting tool followed D2’s work on the Transpennine Route Upgrade (TRU) Alliance, where initial estimates for possession compensation made up a significant portion of the budget. The project team wanted to test the robustness of these figures, so they automated and simplified the method used by Network Rail.
John Johnson, Rail Operation Director explains some of the benefits: Using Schedule 4 Calculator on TRU has helped us calculate the forecasted costs to within 10% tolerance of the actual outturn figures.
“Some of these calculations were up to 50 per cent lower than original predictions. This is useful because it means that budget can be spent elsewhere on the project. Once we can harness the ability to understand these forecasts it provides projects with a really good optioneering tool.
“It also means we can optioneer different access strategies to identify the most efficient ‘industry’ solutions.”
D2 is currently supporting the TRU West Alliance with access planning and possession cost forecasting. As the software continues to develop, the aim is to bring it to other infrastructure projects spanning the wider UK network.
Making data manageable and meaningful D2’s digital technology team offers unparalleled experience in data analysis, web design and desktop software development, combined with the company’s wider knowledge of the day-to-day operations of the rail sector. It is this skill set that makes the company ideally placed to deliver these innovations to infrastructure projects and to help project teams better understand how they can use their data. To be able to calculate Schedule 4 costs, an understanding of all of the different attributes of the calculation is required. You also need to understand the process of train planning, which is where D2’s data analysts are used. D2 is working at the moment to bring that knowledge and its experience of working with operators to automate the tool so that it can be used by anyone.
Ultimately, D2 believes it can provide a tool that can help users make more efficient calculations. At the moment, there’s a lot of reliance on people’s knowledge in the rail industry, but the D2 digital technology team is keen to automate things so that users can benefit from the firm’s tools by making processes and calculations easier and more accurate.
If you would like further details of any of these products, please contact info@d2rail.co.uk
*Source: Office of Road and Rail
TfL has been forced to rely on more than £5 billion in government support since the start of the pandemic. Now it has been given a long-term deal, but as Inside Track editor Richard Clinnick explains, questions remain
Following weeks and months of negotiations, the Department for Transport (DfT) and Transport for London (TfL) confirmed a longer-term funding settlement on 30 August.
In a letter to the Mayor of London Sadiq Khan, former Secretary of State for Transport Grant Shapps confirmed a funding settlement that will ensure the delivery of key capital renewals and investment in London worth £3.6 billion until 31 March 2024. He wrote: “This settlement will enable delivery of, among other things, completion of a number of major projects, new road schemes and increased bus priority.
“The objective of this long-term Funding Settlement is to provide certainty for TfL as it transitions from short-term extraordinary funding provided by government to financial sustainability, while maintaining the existing quality of the transport network and reflecting post-pandemic demand.
“The terms of this Funding Settlement shall remain in effect until 31 March 2024 or until TfL and DfT agree TfL has reached financial
sustainability, whichever is the sooner (hereinafter referred to as the Funding Period). If TfL wishes to exit from this agreement, they must do so in agreement with DfT, having provided DfT with at least 28 days’ written notice. This Funding Settlement will end on the last day of the Reporting Period following agreement from both parties that the funding settlement is concluded.”
Shapps wrote: “[The government] will provide financial support to fund the difference between TfL’s costs and revenue up to the level of an agreed annual envelope on operational and capital expenditure. In exchange for this financial support, TfL will be expected to exercise restraint in their operating budget and manage their capital programme rigorously to ensure value for money for both farepayers and the national taxpayer. TfL will make every effort to maximise revenue. If any decisions that reduce revenue are made without [the government’s] agreement, TfL will bear the cost.”
Until 31 March 2024, the government will retain passenger revenue risk due to the ongoing uncertainty of demand, while capital and operating cost risk will sit with TfL.
TfL board papers for the same day called the situation: “A pivotal moment in TfL’s recovery from the pandemic.” It continued: “The devastating impact the pandemic had on TfL’s finances meant that extraordinary government revenue funding has been required to continue to operate our services.”
As part of the settlement, the Mayor will be required to continue work on the introduction of driverless trains on London Underground
“ “
The final extraordinary settlement had expired on 3 August, and negotiations continued between the two organisations. By that point, central government had provided more than £5 billion in support, albeit with some demands on TfL including ways to make the organisation more financially efficient and to investigate the introduction of driverless trains.
The board papers explained that late on 22 July TfL received a draft proposal for a funding settlement from the DfT. To provide time to properly consider and respond to this detailed proposal, TfL wanted an extension of the funding settlement to 11 August, but this was rejected by DfT which, instead, offered a five-and-ahalf-day extension until 12:00 on 3 August. For the subsequent 27 days TfL was operating using its cash reserves, without any revenue protection or support from central government. During the negotiating period, TfL said that drafts were received on 4, 9 and 16 August.
Between 3 August and 30 August, the Mayor of London Sadiq Khan had suggested that money would run out, while senior officials at TfL have often spoken of the need for ‘managed decline’ due to the lack of financial support from government.
However, outgoing TfL commissioner Andy Byford explained: “After weeks of negotiation, we have reached agreement with government on a funding settlement until 31 March 2024. This agreement, which was hard won, means that we can now get on with the job of supporting London’s recovery from the pandemic – to the benefit of the whole country. There is no UK recovery without a London recovery, and no London recovery without a properly funded transport network.
“The agreement with government means that across the funding period, TfL expects to receive further base funding of around £1.2 billion from government until March 2024 and gives TfL ongoing revenue support should passenger numbers not recover at the rate budgeted, which is crucial at this time of ongoing economic uncertainty. It helps us avoid large-scale cuts to services and means that we will commit £3.6 billion to capital investment over the period, with around £200 million of new capital funding from government beyond previously budgeted sources like business rates, which were devolved to the Mayor in 2017.”
Andy Byford, who TfL announced on 22 September would be leaving his role on 25 October, says that the support offered by government left an unfunded gap in TfL’s budget, and it has been working hard to identify how it will be filled.
He says that this work has made good progress and TfL is confident that it will achieve an outcome that allows it to balance its budget and maintain its minimum cash balance.
“This longer-term settlement includes over £1.1 billion of additional grant funding until March 2024 for London transport, which will unlock almost £3.6 billion-worth of critical infrastructure investment, with a number of projects set to revolutionise travel across the capital.
“As a result of our longer-term settlement, major upgrades will be delivered for Londoners, including new Piccadilly line trains and the modernisation of the District, Metropolitan, Hammersmith and City and Circle lines –maintaining the London Underground’s worldclass status.
“We will need to progress with our plans to further modernise our organisation and make ourselves even more efficient, and we will still face a series of tough choices in the future, but London will move away from the managed decline of the transport network. We are grateful for the support of both the Mayor and the government as we now set out to continue serving the capital and investing in safe and reliable services for the millions of people who need them,” he added.
Former Secretary of State for Transport Grant Shapps, who left his role on 7 September, spoke to the House of Commons on 5 September, and said: “Following my statement to the House on 13 July, I am writing to update the House that today we have agreed a new longer-term funding settlement between TfL and government. The final extraordinary funding settlement expired on 3 August and I have agreed with the Mayor of London a new settlement until 31 March 2024 or until TfL reaches financial sustainability, whichever is the sooner.
“As part of the settlement, the Mayor will be required to continue work on the introduction of driverless trains on London Underground, in use on the Dockland Light Railway for more than 35 years. At a time when strikes are crippling both the Underground and national rail systems, never has this work been more important.
“Alongside all of this is government’s continued commitment to mitigate TfL’s loss of passenger revenue from the ongoing uncertainty of demand following changes to travel patterns since the COVID-19 pandemic. None of this would have been possible without government funding.”
The former SoS added: “The settlement letter requires TfL to modernise and control its operating costs, to make it a modern, effective, efficient and financially stable operator. It is a settlement that is fair and proportionate to London while also taking into account funding provided elsewhere in the country and the cost to the national taxpayer, at a time of great pressure on national finances.”
The transformation of TfL in recent years has made it much more efficient and resilient to financial shocks
“ “
He said the agreement comes on top of more than £5 billion of funding support already provided to TfL since the start of the pandemic, and government’s commitment to more than £1 billion per year until 2025 for London transport through business rates retention.
At the start of the pandemic, in March 2020, TfL issued a statement regarding a reduction in passengers and the impact this could have. It read: “An underlying softness in demand and passenger revenue, largely caused by economic uncertainty, had been experienced by TfL since October 2019, with both Tube and bus revenues trending at around two per cent below the previous year. During February, TfL’s revenue was further affected by three significant storms and a period of prolonged bad weather. This fluctuation was within TfL’s usual financial forecasting tolerances.
“In the week commencing 2 March, further reductions in ridership became apparent, coinciding with growing public awareness of the COVID-19 virus, starting with modest reductions in ridership of around two per cent compared to the same days the previous year.
“Since then, a growing number of firms and individuals have changed their travel behaviour, with greater numbers of people working from home. This has led to an acceleration in the reduction in passenger numbers in the last week to around 19 per cent on the Tube and 10 per cent on buses compared to the same week the previous year.”
The statement said the situation was evolving and that the financial impact would be difficult to predict, with the duration and severity of the spread of the virus set to define what would happen. At the time, TfL forecast a reduction in passenger income of up to £500 million based on government scenarios.
TfL said at the time: “The transformation of TfL in recent years has made it much more efficient and resilient to financial shocks. Tight cost control and efficiency measures have meant that TfL has reduced its deficit from £1.5 billion to £200 million. This has enabled it to mitigate in part the withdrawal by government of £700 million per annum in operating grant, delays to Crossrail and a softening economy. But these financial shocks have also demanded tough decisions about priorities to keep London’s core transport network operating effectively, including delaying plans to upgrade the signalling on the ageing Piccadilly line. The very significant additional impact of COVID-19 will now also need to be managed.
“TfL’s financial policies require it to keep a minimum cash balance of £1.2 billion to provide liquidity to absorb sudden financial shocks. Above this, TfL aims to hold a further £600 million for other strategic risks, for example sudden reductions in passenger numbers due to pandemic. These reserves are actively monitored and managed in order to protect day-to-day operations.”
The forecast was that TfL’s current end of year cash balance for 2020 was expected to be more than £2 billion, which meant TfL felt it would be able to manage the initial impact of the pandemic. It said it would consider further budgetary flexibility to ensure it maintained its financial resilience but said that the Mayor and TfL would be looking to the government to provide appropriate financial support to ensure that the core transport network continues to operate safely and reliably to the benefit of the UK’s entire economy.
The financial model TfL was working with was introduced by Sadiq Khan’s predecessor Boris Johnson. Prior to the pandemic, TfL had achieved significant progress in reducing its operating deficit while still delivering a wide range of improvements to the Tube, bus and rail networks during the previous financial year. Indeed, at the start of March 2020, just before the pandemic hit, TfL was still forecasting it would reduce its likefor-like operating deficit by 86 per cent by the end of 2019/2020 compared to the end of 2015/2016 and had already increased its cash balance by 31 per cent to £2.2 billion.
The removal of the Government Operating Grant meant TfL was the only public transport network in western Europe with no government subsidy, with around 70 per cent of its income required to operate the network received from fares, laying bare the impact of the pandemic on TfL. At the peak of the first lockdown, passenger income was reduced by more than 90 per cent compared to 2019, which meant assistance from government was needed.
However, there were demands laid down by government for the ongoing support, which included a wide-ranging review of TfL’s future financial position and future financial structure being undertaken.
Since the first lockdown, various funding agreements were reached, initially lasting for six months at a time. In November 2020 it was confirmed that as part of an agreement for circa £1.8 billion over six months, TfL would continue working on long-term funding plans to ensure its financial sustainability.
At the start of June 2021, another funding package was agreed, and this included TfL committing to deliver savings and/or new income of at least £300 million in 2021/2022. However, when considering the amount of funding available to TfL in the funding package, there remained a shortfall in funding compared with the organisation’s budget for 2020/2021. This meant that TfL had to, in practice, deliver savings and/ or new income of around £900 million over the course of the year.
At the time, TfL said: “This is expected to be met through a combination of measures, including utilising cash reserves, additional non-passenger income and reduced or deferred costs. These additional savings are incremental to TfL’s existing efficiency plans.” It was also this agreement that first mentioned ‘a DfT-led joint programme on the implementation of driverless trains on the London Underground’.
In its board papers, TfL said that during the pandemic its approach of a tight cost control and rebuilding revenue meant it had been on a declining trajectory of extraordinary government support. The 2022/2023 TfL budget outlines the final step back to financial sustainability and sets out a £1.2 billion full year funding requirement in 2022/2023, with no further extraordinary revenue support being required in 2023/2024.
TfL says that due to a lack of certainty on longer-term capital funding from central government, the 2022/2023 TfL budget is based on a ‘managed decline’ scenario. This involves significant service reductions, deteriorating asset condition and no new enhancement schemes.
TfL states that on a like-for-like basis, the planned capital expenditure in 2022/2023 and 2023/2024 is circa £800 million lower than was planned pre-pandemic, which is a reduction of almost 20 per cent.
A large proportion of the TfL capital programme was contractually committed prior to the pandemic, for example on major contracts for rolling stock procurement.
This reduction in the managed decline budget has not been equally applied across the capital programme.
The managed decline scenario also had a disproportionate impact on smaller schemes that have a shorter lead time in contractual terms.
In terms of rail, the most significant impacts were on step-free access with no further projects included in the budget after the current tranche was completed, many of which were third-party funded anyway.
The board papers state that to create a like-forlike comparison of the 2019 business plan and current managed decline budget, a number of adjustments are required, but TfL says that a superficial comparison of the headline figures would not provide a meaningful evaluation. Even after these quantified adjustments, TfL claims it is likely to understate the negative impact of the managed decline budget.
During the pandemic in 2020/2021 and 2021/2022 the planned expenditure on capital renewals was significantly reduced by £280 million, resulting in a backlog of asset renewals and ongoing deterioration in the state of repair. To achieve a similar level of outcomes as the 2019 business plan, an increased level of asset renewals is required to address the backlog.
In a letter from the former SoS to the mayor, the issue of driverless trains was mentioned. Grant Shapps wrote: “TfL’s record of modernisation and innovation should not leave it behind other European networks, which are achieving significant operational efficiencies through driverless trains. Accordingly, DfT and TfL will press forward with the joint programme on the implementation of driverless trains on the London Underground, recognising TfL’s safety, regulatory and statutory responsibilities.
“Taking the findings of the network review to the next stage, TfL will continue to work with DfT to develop the evidence required to make a strong case for investment in driverless trains on the London Underground. This will include but not be limited to the work set out below. TfL will work with DfT to assess the case for introducing Grade of Automation 4 (GoA4) on the London Underground network, taking into account opportunities and risks.
“TfL will undertake further studies and wider research to support progressing driverless trains on the lines where the case(s) are strongest.
“In addition, TfL should continue working with DfT to make progress developing and testing innovative technology, where it can save money in the delivery of driverless trains. Based on the findings of the above, TfL will work with DfT to develop a business case for driverless trains as necessary.
“TfL will ensure senior representation on the joint programme and will actively support this work through the provision of staff resources, expertise and access to both the London Underground network and any information sources.
TfL’s participation should seek to explore all options in a collaborative and open manner and work with the programme on an implementation plan. [The government] will provide resource funding to TfL to enable it to support the programme’s work.”
The long-term ambition is for TfL to be able
to return to the financial situation it was almost in before the pandemic struck. Politics have clearly intervened in subsequent decisions and negotiations; however London relies on its transport network and that has been recognised. It is now for TfL to make these finances work set against the parameters laid out by DfT.
Former Secretary of State for Transport Grant Shapps wrote in his letter to Mayor of London Sadiq Khan on 30 August that the operating envelope assumes the following as agreed in previous extraordinary funding settlements:
On 15 December 2021, you confirmed how you plan to generate between £0.5-£1.0 billion p/a of additional revenue from 2023. The operating envelope assumes TfL will progress its recommended options with a view to ensuring implementation by 2023, while noting that any council tax precept revenue will be ordinarily raised and used in the same financial year;
Delivery against TfL’s accelerated modernisation programme as set out in its report of 15 October 2021;
That TfL’s pay award for 2022/23 continues to follow public sector pay policy, and the assumptions set out in TfL’s latest budget. TfL will provide an update on pay at the Oversight Group meeting (as set out in paragraph 58). The operating envelope may need to be updated each year, after public sector pay guidance is issued.
The latest pay awards for London Underground were out of step with wider public sector pay policy. The operating envelope assumes TfL will find savings equivalent to this incremental amount from within the London Underground cost base and rebalance this settlement in future pay deals;
On fare revenue, the operating envelope assumes a rise in fares for 2022/2023 and 2023/2024, however it is for the Mayor to decide whether to increase fares and should he decide not to, no additional funding will be provided by government.
If you and TfL wish Londoners to continue to benefit from travel concessions and/or other benefits above those typically available elsewhere in England (such as free travel for all Londoners aged under 18 and 60-65, excluding statutory entitlements including under the Education Act 1996) then you and TfL recognise that the costs of these additional benefits will not be met by government funding; and you and TfL commit to meeting the costs of these additional benefits during the Funding Period, without recourse to additional borrowing, savings, service changes, the new revenue streams resulting from paragraph 11a or deferrals;
TfL maintains average quarterly useable cash reserves of £1.2 billion throughout the Funding Period;
TfL maintains previously planned service levels in line with its core package as set out in its September 2021 service level review and continues to provide funding to boroughs in line with spend in 2021/22.
Source: Letter from Grant Shapps to Sadiq Khan.
s key participants in the TIES Living Lab strategic partnership, Mavin Powercube and Transport for London (TfL) have successfully collaborated to develop a custom, containerised, off-site built Signal Equipment Room (SER) that will enable fast delivery of a harmonised environment, significantly reducing overall carbon impact versus previous SER designs.
The new standard offers massive cost savings, minimises on-site disruption and health and safety risks, as well as improving predictability of successful, project performance. The Powercube SER prototype has now been successfully deployed at TfL’s TUCA (Tunnelling and Underground Construction Academy), with the final phase – installing the green roof substrate and solar –currently under way. The Powercube is a British designed and built, modular, containerised solution; re-deployable and fully customisable.
It utilises innovative technologies that enhance the security, efficiency, and sustainability features of SERs and is easily modified to suit other critical infrastructure purposes, including Train Movement Rooms (TMR), Emergency Service Network Rooms (ESN), Containerised Modular Data Centres (CMDC), and Electrical Transformer Rooms (ETR).
Typically, a Powercube solution is 98 per cent
built off-site, delivered plug-and-play ready, significantly reducing environmental impact, site disruption and delivery timescales.
The SER project is one of four physical demonstrator initiatives being undertaken by the TIES (Transport and Infrastructure Efficiency Strategy) Living Lab partnership – a transformative collaboration that seeks to improve the framework from the ground up, providing the catalyst for longterm cultural change within the sector. We hope to be welcoming Trudy Harrison, Minister of State at the Department for Transport, to the TIES Living Labs project showcase, soon to be organised at TUCA. Trudy and her team will experience firsthand the positive impact these innovative solutions will have in the rail and wider transport sector, here in the UK and potentially other countries worldwide.
T: +44 (0) 845 612 1155
E: contact@mavin.global
The Powercube is a British designed and built, modular, containerised solution; re-deployable and fully customisable
“ “
Network Rail once again used a bank holiday weekend to undertake maintenance and upgrades on the railway. Richard Clinnick reviews the major projects carried out
The railway traditionally undertakes engineering work when it’s quiet, such as at weekends, overnight and during bank holidays. Travel patterns are changing, with weekends in particular far busier post-pandemic than before COVID-19 struck.
Nevertheless, Network Rail continues to carry out such work, and over the August bank holiday, the infrastructure owner and rail supply chain delivered more than £90 million of engineering work.
All told, there were more than 3,500 worksites delivered within 1,053 possessions. These delivered major enhancements as well as core renewals and maintenance work across the network. Network Rail said that there were 12 projected delivering infrastructure upgrades through a total of 16 worksites identified as RED through the Delivering Work Within Possessions (DWWP) standard, therefore deemed to carry out a greater risk of possession overrun and/or a more significant impact in the event of an overrun. Significant projects were delivered across all regions, with a mixture of asset renewal schemes and enhancement schemes to enable future network upgrades.
Highlights from the weekend included the resignalling and recontrol of the former Macclesfield signal box area of control in Manchester Rail Operating Centre (ROC), renewal of the East Stour River Bridge near Ashford, Kent, as well as the refurbishment and re-waterproofing of three bridges in the vicinity of Waterloo East station, renewal of a bridge at Shamford Close to help facilitate the reopening of the Northumberland line, concluding the Hertford Branch line blockade that enabled Greater Anglia to introduce pairs of five-car Class 720 electric multiple units on the route, and switch and crossing (S&C) renewals at Whifflet South Junction (Scotland), Drayton Green (Western) and New Cross (Southern).
Of the planned 1,053 possessions, 11 serviceimpacting overruns occurred, with the total number of overrun delay minutes reaching 1,101 minutes. Compared with the previous August 2021 period, this is a successful possession hand back rate of 99.0 per cent.
There were also zero significant safety incidents reports over the weekend, with only a single highrisk close call being registered.
The NEAT Infrastructure Change (Hertford Branch Blockade) was part of a programme of works to deliver infrastructure upgrades to allow the introduction of new rolling stock, specifically
Alstom Class 720 Aventras that operate in five-car and 10-car configurations, replacing trains that previously operated in four and eight-car formations. Work was undertaken at St Margarets, Ware and Hertford East. The benefits include improved network capacity, and the new rolling stock will provide a better experience for passengers – it has been designed to be compliant with TSIs introduced in 2017 covering accessibility and is more energy efficient than the legacy stock it replaces. The work completed included lengthening platforms 1 and 2 at Hertford East by 84 metres, platform 1 at Ware by 81 metres, moving signal L1241 at St Margarets, moving and renewing a point at Ware and two at Hertford East, and works to the signalling and electrification system have been undertaken to suit the new layout.
All told, there were more than 3,500 worksites delivered within 1,053 possessions
“ “A major resignalling project was carried out at Macclesfield over the bank holiday weekend. This is the final train to be controlled by the old signalling system
At Chippenham Junction, also on the Eastern region, the renewal work here forms part of the staged works for the Cambridge resignalling project and Network Rail say this stage will be delivered in its entirety in three possessions, delivering 1500 yards of CAT 02 re-rail, CAT 11 plain line renewal and 3x CAT 71 S&C renewal. There will be mechanical alterations in Chippenham signal box with the POE temporarily mechanically electric until the main Cambridge commissioning in Christmas 2023. A DNO at Newmarket is to be upgraded to facilitate the new points heating installation as the current points are heated with gas. There will also be a speed increase to 50mph across the junction which requires network change.
The benefits of this include track renewal to improve reliability in the area and reduce the risk of points failures and associated train delays and/ or cancellations. Passengers will enjoy smoother journeys and a reduced number of disruptive possessions for maintenance and faulting activities as well as staged works to facilitate the Cambridge resignalling project.
Further north on the Eastern region, at Sharnford Close on the Northumberland line, work continued on the reopening of the railway. Sharnford Close is a single skew span pedestrian underbridge located near Backworth, Northumberland. The structure comprises two forms of construction and carries the single, ballasted, bi-directional railway over a public right of way.
Work included removing the permanent way, demolishing and removing the existing underpass structure and excavating the existing embankment. Then a new underpass was installed, as was drainage and waterproofing. Permanent way works carried out included stressing, welding and tamping. Furthermore, the S&T cables were reconnected and tested.
Another project on the Eastern region was the Mk 1 Mid-Life Refurbishment Project.
The existing Mark 1 overhead line equipment (OLE) system was commissioned across Anglia between 1959 and 1962 and is being replaced to improve performance. The majority of the OLE is auto tensioned, however some is fixed termination. This project aims to replace the existing Mark 1 system that is deemed life-expired and is being carried out on the line between London Fenchurch Street and Upminster, and between Barking and Pitsea. This will replace 144 wire runs and 99 structures. Network Rail said that 1,024 metres of contact and catenary wire was replaced on one section, and 1,596 metres of catenary wire on another.
Commissioning of the Macclesfield resignalling scheme, which brought the new signalling CBI WTS interlocking and Dorman equipment into operational use, and control transferred to a standalone Macclesfield workstation
at Manchester ROC, was completed over the weekend. This was supported by the commissioning of the new FTNx telecoms network and the new signalling power arrangement. This is designed to improve asset condition, performance and reliability, reduce the number of lineside assets, remove the permanent speed restriction through platform 2 at Macclesfield station caused by signal sighting and also collaborating with stakeholders regarding a mural at the station.
Work included bringing 63 new signals and associated lineside equipment into use, along with 54 signalling location cases, one signalling REB and four FTNx nodes. Also introduced was a new standalone workstation at Manchester ROC, new signalling power arrangement (1 PSP, 2 ASPs, 1 HC switch), 151km of new cabling, recovery of all redundant signals and commenced recoveries of redundant lineside equipment houses and cables, and the recovery of REED FDM equipment for national strategic spares.
Ian Robinson, project manager for Network Rail, said: “This once-in-a-generation overhaul of Macclesfield’s signalling system has brought this key section of the West Coast main line up to the most modern standards. The investment will futureproof journeys and create a more reliable railway for passengers and freight services.
“I would like to thank local people and passengers for their patience while we carried out this essential work.”
Gus Dunster, executive director of operations and safety at Avanti West Coast, said: “We’re excited the upgrades to the signalling system are now complete and would like to thank customers for their patience and understanding while Network Rail carried out these works. Modernising the signals on a key section of our Manchester route is an important milestone for the railway and will help to make journeys on the West Coast main line more reliable for decades to come.”
John Robson, CrossCountry West Midlands and North West regional director, said: “Futureproofing this busy part of the West Coast main line has been essential to ensure a safer and more reliable railway. We’d like to thank our customers for being patient while this important modernisation took place.”
Chris Jackson, regional director for Northern, said: “We welcome the completion of these works and the improvement to reliability they will bring for customers travelling on our Manchester Piccadilly to Stoke-on-Trent services.
“It is always important to invest in rail infrastructure to ensure we can keep the region moving, getting people from where they are, to where they want to be.”
Also on that region, work was undertaken on a project to replace 687 yards of ballast at Wolverton on the Down Fast line.
The track quality throughout this site is poor and has suffered from high rates of deterioration, with GPR records indicating erosion and formation issues. Network Rail confirmed that 508 yards was reballasted and renewed in a change to the plans due to preparation shift possessions being cancelled as a result of strike action.
The scope of work for Whifflet South Junction, Lanarkshire, is a renewal of two points, the refurbishment of two more points along with three separate installations totalling more than 1,100 yards of plain line track to remove the poor condition of the asset. There was also full replacement of components such as fastenings and ballast. These works were carried out over two weekends.
The project at New Cross Country End was to renew three S&C units, 163 metres of associated plan line track, install new conductor rail and point heating strips. The benefits of this work were the renewal of life-expired assets, improved geometry and modern equivalent from materials for improved resilience and the removal of clogged ballast and wet beds. This work was completed in one 72-hour possession over the bank holiday weekend.
At Waterloo Bridges, the project was to disconnect and reconnect S&T, remove and reinstate wheel timbers and track removal, repair cleats, clean the structures via jetting and blasting and waterproof the bridges. The benefits include renewing the life-expired assets, using paint with a planned 25-year lifespan, and removing the need for a temporary speed restriction which
had limited trains to 25mph running. This was all completed during the bank holiday weekend.
The East Stour River bridge is a mid-span bridge over the River Stour. The works involved the replacement of the centre span deck and associated civils works. Network Rail said that the existing bridge abutments, piers and wingwalls remained in place and now support a renewed bridge deck. Existing S&T equipment has been relocated into new cable containments fabricated underneath the walkway platforms on both sides, and a new permanent way design was also constructed.
The aim of the project was to mitigate agerelated issues, replace the structure with a new one that has a 120-year design life, and by introducing the new structure Network Rail was able to remove a restrictive weight limit that had been in place.
The Drayton Green Junction project was a track, switch and crossing renewal at the north point of the triangular junction near Drayton Green station.
This involved the renewal of points including points operating equipment with a modern equivalent and 130 metres of plain line track on the Up Greenford line. Additional civils works included heating and minor copper works at the station to accommodate track alterations. A new cross drain was installed to improve drainage, the existing electrical supply was upgraded, while 300mm of ballast and 100mm of sand were installed.
Renewing vital track and components has enabled the introduction of smoother, more reliable journeys for passengers and reduced the need for future maintenance at this key junction.
Track at Parks Bridge Junction, Lewisham, awaiting top stoneRowe Hankins designs & manufactures a wide range of non-contact, multi-channel Speed and direction Sensors, designed for safety critical systems to operate in harsh environments. Speed Sensors can have single, dual or multiple output channels. In turn, we can isolate a specific channel or channels to receive power from a different power supply. They can be designed and manufactured bespoke to customer requirements using Hall Effect & GMR technology.
Our new innovative 4 Channel Speed Sensor can be used to replace existing single and dual channel Speed Sensors as the physical footprint is of the same form of sensors used in typical applications. This means fewer Speed Sensors per train, having a novel design that improves the EMC immunity and improving product life expectancy and reliability.
InnoTrans, the global exhibition for the rail industry and its suppliers, returned after a four-year break. Held in Berlin between 20 and 23 September, around 140,000 visitors from over 131 countries went to see displays from 2,834 exhibitors and 56 countries
xhibitors and visitors were glad to be back after a forced break due to the COVID-19 pandemic. The first three days were particularly busy as crowds walked the halls and visited the 128 vehicles and exhibits on the track and outdoor areas.
Over 100 British companies, and many more with UK interests, participated in the event. A number were on one of two British pavilions, organised by the Railway Industry Association and the Department for International Trade.
There was the usual mix of product launches, train unveilings, contract signings, evening receptions and earnest discussion, fuelled by coffee, canapés and, later in the day, German beer.
There was also a lot of walking. With 42 halls to cover, plus 3.5 kilometres of on-track exhibits outside, everyone was complaining of sore feet by the second day.
Two train launches – in fact covering three trains – were hosted by Stadler. Two were for Transport for Wales – the Class 231 tri-mode FLIRT and the class 398 Citylink tram-train, both built by Stadler.
The second launch, of the third train, was of the Class 777 for Merseytravel.
Although several examples are already on Merseyside, this gave InnoTrans visitors the chance to see the new trains for themselves.
A particular talking point was their battery capability, which will allow them to run over lines not currently part of the third rail network.
type transformers – high efficiency, environmental safety and reduced zoillnermaintenance.
The Rail Safety and Standards Board (RSSB) signed a memorandum of understanding (MoU) with the Korea Railroad Research Institute (KRRI), enabling more collaboration in research and development to improve railway safety.
Hitachi Energy, which took over ABB Power Grids in 2020, launched a new oil-free traction transformer that can operate at up to 25kV.
A new development of the RESIBLOC® Rail transformer that was launched in 2018 with a maximum operating voltage of 15kV, it has an integrated cooling system that significantly reduces installation complexity for train manufacturers while retaining the benefits of dry-
Meanwhile, the new Welsh railway test track – the Global Centre of Rail Excellence (GCRE) –signed an MoU with Orange Train Wash, a start-up company that has developed a new way of washing trains and is backed by Dura Composites and RBD Advisory. Around 30 UK companies exhibited in the two British pavilions, and another 80 had their own stands. The Railway Industry Association hosted a reception at the British Embassy on the Wednesday night for around 300 exhibitors and their guests, with sponsorship from Rail Products UK, Xrail, Rail Business Daily, British Steel, Furrer+Frey and Pandrol.
The night before, the University of Birmingham had taken over the same venue for a sit-down meal for 90 guests, including many overseas trade advisers and their clients.
The British exhibitors more than held their own against the major players, some of whom had very large stands indeed.
With 42 halls to cover, plus 3.5 kilometres of on-track exhibits outside, everyone was complaining of sore feet by the second day
“ “
Siemens Mobility took over a major part of hall 27, which accessed the outdoor display where several Siemens trains were on show.
Destination Digital was the theme of the stand, ‘because meeting the growing demand for rail doesn’t necessarily mean you need to make large investments in new infrastructure. Improving your existing one may be even more effective.’ Key to this was the launch of the new Siemens Xcelerator
open digital business platform, helping train and rail network operators deliver added value across their core processes.
Wabtec also had a major presence. The American multinational is heavily involved in the UK and Europe.
The corporation has a vision to achieve a zero-emission rail ecosystem worldwide, and its team showcased the sustainable equipment,
“It’s fantastic to be back in Berlin to attend InnoTrans after a fouryear break caused by the pandemic. This week has shown once again that the UK rail supply sector is an exporting powerhouse, selling the very best innovations, products and services to the rest of the world while also helping to innovate and improve our railways at home.”
systems, digital solutions, and value-added services that will accelerate the future of transportation.
Systra, too, is heavily involved in the UK, having acquired TSP Projects (formerly Tata Steel Projects) from British Steel in 2019. A new low-carbon ballastless track and an innovative automatic track warning system developed with Zöllner were on display.
Head of rolling stock strategy and programmes, Transport for Wales
“We’re here to celebrate today the FLIRT units and the Citylink tram units, all manufactured by Stadler. The tri-modes will start to be delivered to Wales in November/December this year and the Citylinks will start arriving in our Taffs Well Depot in January of next year.
“The FLIRTs are replacing legacy stock of several different types, but the Citylink is a whole new concept, capable of running as a tram as well as a train.
“Obviously, we will have a phased introduction – initially main line running and then we will move on to the to the off-street running.
“We were in the design phase of the of the project when COVID struck and everybody was instructed to work from home. But we were fortunate because we were able to work in a very collaborative way through that design phase and to achieve the result we see today.
“We’re really looking forward to introducing them to the travelling public from early January.”
Global product manager for dry transformers at Hitachi Energy
“This is the world premier of our liquid-free main traction transformer for the 25kV network. It has a very high energy efficiency in comparison to a traditional oil transformer – up to 50 per cent higher. And we have reduced the need for complex maintenance, making it almost maintenance free.
“The existing 15kV version is already in service with hundred of transformers. Now we have increased the power and voltage rating to 25kV and improved the cooling at the same time.”
Frank Cornelius Rob Hale“GCRE is a new Welsh railway test facility that we’re building up on an old coal mine near Port Talbot.
“We’re here at InnoTrans to share what we’re doing, the opportunity of what we’re doing and explaining the chance for suppliers to test their products properly, to standardise it, authorise it, get it into use, test their trains, test European trains, bring European products to the UK, that enable British companies to sell to Europe.
“We’ve got a lot of interest from European countries to do this test track. The European RJU is interested in doing some testing here because this will be a unique facility in Europe.
“The special feature is the infrastructure loop, which will run a train 16 hours per day. It’s an aggressive opportunity to test infrastructure products to their full life, enable us to understand reliability, maintenance requirements and tease out those problems before they’re put on the main railway. This will be a unique facility in the whole of Europe. It’s the infrastructure we’re testing –normally, on a rolling stock loop you keep the infrastructure test constant and you vary the train; on the infrastructure loop you keep the train constant and you vary the infrastructure.
“It’s a very simple concept, and actually a real opportunity for the UK to be doing something no one else does. It will be fully operational in 2025, however we hope that the signings and other facilities will start coming online from the middle of 2023.”
Robust, rapid, pivoting, retractable, elegant & highly conductive — Furrer+Frey’s Rigid Overhead conductor Rail system ROCS is renowned throughout the world for its superior standards of quality & reliability.
In tunnels, in stations, in the open, on bridges, in workshops and depots, ROCS can easily adapt to any structure. Furrer+Frey has supplied its groundbreaking ROCS system for more than 3400km of track across the globe and it is currently tested up to 302kph line speeds.
“Our aim is really to talk about sustainable technology. This is so important for us because we all have to work against climate change, all of us. So, we are showing our Mireo train platform –our commuter platform – which we have for overhead catenary, we have it for battery trains and we have it for hydrogen, the newest generation.
“And if I talk about hydrogen, normally they have less power than the battery because of the hydrogen cells. But here, we boost this over a battery so that you can also make the same acceleration with these trains from Siemens, the Mireo H2, as you can do with a battery train or in a normal catenary train. So, we were quite happy to be here.”
“Regarding infrastructure, we have some amazing innovations on show. Our booth has four sectors, showing how we can reduce the life cycle cost, improve availability, what we can do on digitalisation and how software can steer the whole process much better.
“I think the next step is to really bring it into the cloud – make it all independent of hardware so you can really combine it wherever you need it in the world.”
Melanie Gangl Managing director, Frauscher UK“InnoTrans is a very important exhibition. It is four years since we were here the last time, and, from a global perspective, it is important that all our locations are coming together here and bringing our new innovations with us.
“Our new sensor is a very important product which we are looking forward to seeing in the UK in level crossing applications. We will be working together with our end users like Network Rail, getting feedback from the market, and introducing it to the market during control period 7.”
“We have developed massively in the UK since 2019 with the acquisition of TSP Projects. It doubled the size of our staff in the UK. Now we have more than 900 people and the UK is the seventh largest market for us – 30 per cent of our business is inside France and 70 per cent international.
“Our business is growing well in the UK. One of the major projects is HS2 where we are part of the Balfour Beatty Vinci alliance for Old Oak Common station, and we are continuing to make some more bids and tenders for HS2.
“But behind that we are on course to develop a deep footprint in the UK. Systra UK is covering UK and Ireland, and we have a British CEO – it is our policy to always have local management of the company.
“We act as a true British engineering company in the UK, with the connection with the Systra network which is supporting them to develop business and to have access to more resources.
“We invest in the UK because we believe in this country where there is a long tradition of developing railways.”
“This is our seventh visit to InnoTrans. We like to come here, it’s obviously the place to be and it’s important for us to network.
“We’re doing lots of work in Africa, south America, Asia, so being here at InnoTrans is important to keep all those relationships alive. We’re signing an agreement with Saudi Arabian railways SAR, around education and research. We’ve been doing work with them and it’s now becoming a more formal agreement, so that’s a nice step.
“The University of Birmingham has a campus in Dubai so some of that activity will happen here in Birmingham and some will happen in Dubai.
“We’ve also signed an agreement with GCRE – the new test track in Wales. We’ve now signed the formal agreement to look to build a centre of excellence in testing and validation, which will both do some testing, but actually really look at the science to testing and how we can do earlier compliance in big projects.”
“InnoTrans is really important for us because rail is now making up almost half our business globally.
“It’s a fantastic opportunity to meet colleagues from all around the world in a time zone different to their own, so you’ve got time to have a good quality conversation.
“It’s enabled us to showcase our digital innovation and also, it’s allowed attendees from the company to see the rest of what’s happening in railway technology around the world.”
“From day one, it’s been my ambition to develop a publicly owned, integrated transport system that we can be proud of. These new trains that we’re launching are battery operated and will reach parts of the network that previously we couldn’t get to. That means we can open up really good quality alternative rail travel to many people who currently use the car, and to areas that have been left behind.
“Because of this, Merseytravel will be going to places that actually haven’t been Merseyside. They have been part of it geographically, but haven’t felt part of the Merseyrail network, because our trains never went there.
“The first of these battery-operated trains is going run from Kirby, which is the end of the line at the moment, to a new station at Headbolt Lane, with plans to connect Headbolt Lane to Skelmersdale. This means we can open up a whole conurbation who have not had the opportunity for rail travel.”
Simon Charlesworth Vice-president of transit sales and marketing, Wabtec
“InnoTrans is the premier rail equipment show in the world. We are showing new technologies in electric locomotives, in brakes to increase safety and reduce stopping distances, in air conditioning using clean refrigerants, in passenger-information systems to improve safety and passenger flow, both in stations and within the train.
“So, a full spectrum of equipment, both on the freight and the transit sides. It’s been a really busy show and it has been a pleasure to be here.”
Frauscher was also promoting its latest digital offerings. Under the motto ‘On track beyond tomorrow – your partner for life’, the company presented its latest solutions which go far beyond wheel detection and axle counting, covering the entire product lifecycle.
Two ‘British’ firms of consultants were in Hall A of the City Cube. Mott MacDonald is very
much a UK organisation. Atkins is another wellestablished supplier of professional services, even though it is now owned by Canadians SNCLavalin.
Outside, while the new trains from Siemens, Alstom, Stadler, CAF, Skoda and others were crowd pleasers, track-maintenance companies such as Linsinger, Schweerbau, Rail Technology
and others displayed the latest technology for keeping the railway performing at its optimum level.
After four days, over 63,000 steps, and with a pocket full of business cards, it was time to return to the UK. Until another two years, on 24-27 September 2024, when we can look forward to doing it all over again.
Trespass continues to be a major issue for the rail industry, with 16,431 incidents reported on Britain’s rail network between April 2020 and March 2021.
Gramm Barrier Systems, one of the UK's leading installers of acoustic barriers and security fencing systems, is increasingly seeing a demand from clients for a single solution which not only reduces rail noise, but also deters trespassers.
The company's SoundBlok® panel and post range tackles both these challenges and are used across the UK rail infrastructure.
Not only highly-effective noise dampening barriers, SoundBlok® systems are available in a variety of heights up to 10m as standard, creating a physical obstacle to discourage encroachment.
• POLYSoundBlok® panels are manufactured from PET plastic - primarily recycled water bottles – helping to divert plastic from the ocean and encased in upcycled plastic to produce a lightweight noise absorbing barrier. Highly-durable and rot-proof, the maintenance free design has an operational life of 40-plus years.
• CONCRETESoundBlok® system incorporating Durisol wood-crete ( organic softwood shavings processed to an acoustically-engineered size) and bonded with Portland cement. Porous, non-combustible, thermally insulating and freeze-thaw resistant, the product has a 60-year plus lifespan.
• METASoundBlok® panels, made from galvanised steel plating with a sound-absorbing mineral wool core, have lifespan of 40-plus years. The lightweight (22.0kg/m2) design makes the METASoundBlok® the barrier of choice for bridges, overpasses or other elevated structures unable to support heavier products.
Steve Barnes, Business Development Manager at Gramm Barrier Systems, says: "We are increasingly being asked for more robust solutions which can act as both noise barriers and also offer a degree of rail line security.
"With a choice of three different solutions, our SoundBlok® range is dual-purpose, mitigating noise and providing a deterrent to potential trespassers.
"SoundBlok® systems are cost-effective, quick and easy to install and offer an improved whole-life cost, increased asset value and lower carbon footprint compared to installing a noise reduction system and fencing solution."
Gramm Barrier Systems design, supply and install acoustic barriers and security fencing systems and is the
Telent is responsible for keeping much of the UK’s critical digital infrastructure safe, secure, and running as effectively as possible. As well as being trusted by blue light organisations such as fire and ambulance authorities, builders of next-gen fibre networks and the country’s local and national roads and highways agencies, Telent plays a critical role in the running of the UK’s rail ecosystem.
Telent works with bodies like Network Rail and Transport for London (TfL) and with train operating companies to design, install and maintain crucial assets like CCTV and public address (PA) systems, control room systems, station assets and station management systems.
Mick Mohan, group engineering director at Telent, answers questions on the rail projects, employment opportunities and working culture at a company that’s been providing efficient communication systems in safety critical rail environments for the past 30 years.
vertical within Telent, so out of our 500 or so engineers, 175 work on rail for customers like Network Rail, TfL, and Transport for Greater Manchester, to name a few.
They work on projects like delivering free public Wi-Fi at Network Rail’s 20 managed stations, which include the busiest stations in London, and needed to be delivered to the customer quickly. This has so far received excellent feedback. Our work stretches as far as rural northern Scotland, where we recently played a role in the introduction of a more efficient train-stopping system –meaning passengers no longer have to stick their hands out to get the drivers to stop.
We also work on safety critical assets like traction control management systems panels for Network Rail, which shows the diversity and the breadth we have got within the technical base, right from the radio and wireless engineers through to network engineers and software writers.
2. What kind of roles do Telent workers take on for these projects? Is there a wide variety of positions filled up and down the project delivery chain? The number of engineers at Telent has grown considerably over the last few years, and they’re working across a range of different disciplines, right from design and testing to electrical engineering and installation.
The good thing about Telent is that we have the two ‘pathways’ those engineers could take when joining the business. They can specialise in a focused area or be a bit more of a generalist and run their own team by going down the project management route.
1. Can you tell us about some of the projects Telent has been involved in or led over the past year which have shone a light on engineers at Telent? We have about 30 to 35 major projects on the rail side of the business. It’s our biggest technical
The type of work we’ve undertaken and skills we’ve honed over the past few years have changed and expanded, not least because of the greater focus on security for many of our customers. For example, many are switching from analogue CCTV to digital, which provides many more opportunities, like providing detailed analytics, faster speeds and a direct response for our customers.
Due to the stringent requirements of our customers, and given the critical infrastructure they own and manage, our engineers often need to be highly specialised and skilled. For example, many stations have heritage regulations meaning that the engineers need to be very well aligned with the rules and processes for working at these stations.
Radio wires is another massive skill base within Telent as you can imagine, as is working with CCTV and PA systems, which are key in the rail industry for keeping passengers informed and safe. Likewise, the help buttons you see around the stations are something we’re very familiar with when designing, installing and maintaining the network.
Cyber security – and ultimately keeping people safe and secure – is a megatrend at the moment that isn’t just happening in the rail industry but is happening in all businesses. That’s driven two things for us: we have grown our skill base of engineers offering those services and technologies but are also making sure when we put new networks in place for our customers that they have the very latest cyber-secure safe credentials.
4. How do you make sure that you are able to attract a diverse pool of candidates, not just for apprenticeship and graduate positions, but also for your regular vacancies?
3. Telent is known for its graduate and apprenticeships programmes and the progression offered through the company via these routes –what opportunities are on offer and how large is your intake each year?
Last year we saw a record intake of 98 graduates, and we’re set for even more to join this coming September, thanks to our growing capacity to take on more roles across a variety of projects. Around 60 per cent of them will be working within the engineering space, and around 20-25 per cent will be within the project management space.
We have a multitude of opportunities at Telent, and we like to recruit in areas where we know there is growth, such as security and network engineering. We try to match people’s skills with their aspirations using the opportunities we have on offer. Once you join the business, you have the chance to try different areas of the business, learn different skills and discover what Telent is all about. Once that’s complete, it’s our job to make sure we get those people in positions where they can grow their careers and be successful.
Now is a great time for opportunities for young people working in Telent’s sectors, as the technology is moving at such a fast pace. For example, post-COVID, lots of people wanted open communication systems, and there are a lot of opportunities, so we need to make sure we are well placed and positioned to deliver that. For that, we need the correct people, and many of those people come through our training schemes.
And if a graduate or apprentice has got the right potential, and they’ve demonstrated their capabilities and skills and we think that they can progress quickly, they’ve got a massive opportunity to grow their career within Telent. We’ve got lots of good examples as to where we are doing that.
One current employee only six months into their graduate scheme was made project manager, involved in a key project in Manchester looking after their live ‘meds’ system, and that’s quite a big responsibility. But they’ve succeeded because they’ve shown the potential, the appetite and the skill levels to want to do that, to want to learn more, and we are going to support and mentor them and help them achieve their goals.
We recognise that a diverse workforce is a strong workforce. Different values, cultures and views coming together enrich the working environment and that is really important. But the reality is that hands-on, practical work still needs to be done to bring more people from different backgrounds into the sector and the engineering field is one that, traditionally, has not been terribly diverse.
Personally, I have real pride in the fact that we have more women in engineering jobs within Telent and that our ratio of women-men is above the UK average. We’ve still got work to do though. Some of the ways we’re attracting more women to our roles is by amplifying the voices of the women who are already part of the Telent team and making sure we use gender-neutral language in our job vacancies.
the way we behave, that’s part of the DNA we have got as a business. I see the decisions people make day-to-day, and it’s doing the right thing for the customer, and then we will think about how we can address things once the customer is happy.
We also centre our culture around four key values:
Being inclusive;
Taking responsibility (like doing the right thing for Telent and the customer);
Collaboration (which is critical given the number of group projects within the business); and
Customer focus (without customers, we don’t have a business. We are very, very close to our customers, and they rely on us greatly. It’s so important that we continue to grow and prosper those relationships with them).
6. Initiatives in local communities, from workshops to sponsorships, are important to Telent in the areas where it has projects. Can you tell us more about these and give us some examples? We take our corporate social responsibility seriously, from ensuring that our work has a positive impact on local areas, to committing to carbon reduction initiatives for the better of the planet.
We’ve also set up workshops for women’s voices to share their experiences within the business and our family-friendly policies around homeworking for mothers has helped women in the business balance their home-work lives.
We don’t want to just pat ourselves on the back and say ‘well done’ – we want to be hands-on and involved in initiatives that are changing the rail, and wider critical infrastructure industries, for the better.
That’s why we got involved in the Greater London Authority’s Design Labs scheme, a 12-month programme to support large businesses committed to tackling the underrepresentation of young black men aged 16 to 24 through workshops and one-to-one coaching and engagement with young people.
5. How would you sum up Telent’s working culture and environment?
It sounds like a cliché, but we’re very much a family-feel, non-bureaucratic company. It’s a quick moving environment, and we are very close to our customers. The customer is number one and, although I know a lot of businesses say that, if you look back at a lot of the things we do and
For example, we’ve encouraged local people to get involved with our Telent STEM ambassador programme, and apprenticeship and graduate schemes to provide job opportunities to the areas we’ve work and have worked in. On top of that, we’ve run workshops with local SMEs to share knowledge on many facets of running a business.
Raising awareness of engineering or health and safety issues in local schools, sponsoring after-school sports clubs and local sports teams, and getting involved with the Wellchild Project to help young children with complex care and health issues in the area have also been important to us.
Our charity partnerships are very close to the hearts of people at Telent too. We’ve recently committed our 2022-2024 fundraising campaign and awareness efforts to the mental health charity Mind. The last couple of years have been tough on the mental wellbeing of many, many people. Our last charity partner was the Alzheimer’s Society, that Telent raised £185,000 between 2019 and 2021.
Our culture and environment is very much one that, if anyone in the business wants to get involved in community and charity projects, they can give us a knock on the door, and we’ll do our best to facilitate what they need to get involved and make it happen.
We have a multitude of opportunities at Telent, and we like to recruit in areas where we know there is growth
“ “
Established in 2017 by career railway professionals
Craig Speed and Daniel Cartwright, EnPro is going from strength to strength with the opening of a new office in Scotland and a planned recruitment drive
The business offers bespoke project managed solutions for the rail industry across five key sectors: railway projects, train presentation, support services, facilities management and security provision.
It is not by chance that EnPro is active in these areas as its offering evolved from the needs and requirements of various customers when delivering to third-party sites. Additional infrastructure is often required to undertake the work needed, and examples of local infrastructure work carried out includes electrical installations, drainage, fuel points, waste streaming and installation of welfare facilities. Furthermore, EnPro’s facilities management teams can conduct standalone projects as well as facilitate ongoing maintenance of depot infrastructure.
EnPro’s culture is built on the consistent delivery of a quality service, with its teams striving to meet customer requirements. These are delivered via innovative and sustainable solutions, with EnPro offering a ‘can-do’ attitude to most situations, enabling it to build relationships through trust and collaborative working. There is a constant process to identify, define and optimise benefits for all parties.
Projects undertaken by EnPro have included fleet modifications, fitting CCTV to locomotives and carrying out deep cleaning for entire train fleets. EnPro was contracted by GB Railfreight to keep cabs clean and safe on more than 100 locomotives during the height of the COVID-19 pandemic. This was undertaken across the country, from Inverness
to Eastleigh across a 16-month contract with 20 sites including office premises and depot facilities sanitised on a rolling 28-day cycle. Road vehicles were also treated and EnPro was able to facilitate callouts around the country within 12 hours in response to customer requirements.
At a time when costs are important to the rail industry, EnPro recognises that outsourcing services can be extremely beneficial to a business and has delivered a ‘one-stop-shop’ solution for operators.
A recent example involves train presentation, bodywork corrosion and paint repairs and system installation on ScotRail trains. This relationship also saw EnPro responsible for managing and integrating complex projects with various stakeholders including ScotRail, Network Rail and Siemens. During the high-profile COP26 conference held in Glasgow at
the start of November 2021, SNC-Lavalin contracted EnPro to supply Controlled Emission Toilet (CET) extraction and water tanking services at Mossend freight depot on behalf of rolling stock leasing company Porterbrook which was demonstrating its HydroFLEX train at the event. Because the freight yard did not have the required machinery for the train, EnPro sourced and provided the necessary equipment to ensure the necessary waste transfer was completed.
Another major project in Scotland was the delivery of the GSM-R radio upgrade programme across all fleets. This involved the control of float, logistics and installation from Inverness to the Central Belt.
Indeed, the majority of the EnPro workforce typically operates at third-party sites across Britain and setting up new operations has been key to the business from its very inception, with the primary consideration being health and safety when mobilising and delivering projects. This is underpinned by the company’s management support who can deliver to tight timescales and have experience of installing temporary facilities at various sites within a matter of days.
EnPro is at the forefront of five key rail sectors and has a proven track record of delivery. To find out how they can help your business, visit https://enprogroup.co.uk
We
of
use,
Network Rail is aiming to reintroduce passenger services from Southampton Central to Marchwood station and create a new station at Hythe
ailway reopenings are a useful tool for governments seeking to decarbonise public transport and offer improved connectivity for communities cut off from the railways, especially following the Beeching cuts of the 1960s.
One line that often appears in reopening plans is the Fawley branch line in Hampshire –an eightmile route. It’s located on the opposite side of Southampton Water from Southampton itself and connects to the South West main line at Totton, west of the city.
The railway was authorised in 1903 but only opened in July 1925, with passenger trains serving Marchwood, Hythe and Fawley. There was also a station at Hardley Halt that opened in 1958 for workmen but closed seven years later in 1965.
Passenger traffic on the line was light at first, until the Fawley oil refinery opened in the mid1920s with patronage growing as a result of people travelling to work.
Despite being deep in the third-rail electrification territory, by the mid-1960s the line itself was never electrified and so diesel electric multiple units (DEMUs) were used until the line was closed to passengers on 14 February 1966.
After the passenger trains ceased operating the line remained open for freight trains, not only for the refinery but also for Marchwood Military Port, however these flows both ended in 2016.
As far back as 2009 the Association of Train Operating Companies (ATOC) announced plans to investigate the possibility of reopening the railway to passengers. Trains would operate as far as Hythe under these proposals, but there were also aspirations to run to Fawley if an agreement could be reached with Esso, which owned the land where the former station stood. ATOC suggested that the link could be built over a five to 10-year period and cost around £3 million, with trains running to Southampton and operated by South West Trains, which was the franchise holder at the time. Diesel traction was the preferred choice, but a possibility of electrifying the line was mentioned. Service frequency was expected to be half-hourly during the peak decreasing to hourly off-peak.
Plans were shelved by Hampshire County Council for five years, and there were concerns about the impact of the opening of the line on local bus and ferry services that could have lost local government funding as a result of the reopened railway. The council claimed that there was a poor business case but it did leave the door ajar for the project to be revisited in the future. With an increase in housing development in the area, the council announced plans to investigate the proposals again in November 2017. In August 2018 it was confirmed that reopening plans were to be included in the development plans known as Fawley Waters. A half-hourly service between Southampton Central and Fawley was the aspiration, with trains operating at 60mph on the branch.
In February 2019 the Campaign for Better Transport (CBT) confirmed that the line was a priority for reopening, highlighting that it would reduce air pollution while also relieving pressure on busy roads adjacent to the New Forest National Park.
Fifteen months later, in May 2020, the Department for Transport (DfT) announced that the Waterside line, as it was now known, had been shortlisted for further funding to investigate the restoration of passenger services. This was to be provided as part of the Restoring Your Railway (RYR) initiative, which has already resulted in daily passenger trains returning to the Okehampton line after almost 50 years. RYR is a £500 million programme designed to reopen lines and stations closed by the Beeching report in the 1960s.
Under the RYR plans, Marchwood station would be reinstated and a new facility would be constructed at Hythe Town, which was actually a little further west of the previous station, while a southern terminus would be constructed on the site of the former Hardley Halt station, called Hythe and Fawley Parkway.
Hampshire County Council applied successfully for funding to develop the plans, with the DfT agreeing to contribute £50,000 towards economic studies and a business case.
Current franchise-holder South Western Railway (SWR) operated a train along the branch on 28 July 2020, stopping at Marchwood. This was designed to showcase the line’s potential and so became the first passenger train to serve the station in some 54 years. SWR operated a second train on 7 May 2021, again calling at Marchwood.
Meanwhile, in February 2021 HCC released an updated strategic outline business case containing three proposed service patterns. The first was one train per hour (tph) between Salisbury or Romsey and Hythe and Fawley Parkway. The second was one tph between Salisbury or Romsey and Hythe and Fawley Parkway and one tph between London Victoria and Hythe and Fawley Parkway. The third option was three tph between Southampton and Hythe and Fawley Parkway. This latest business case also included reopening Marchwood station and electrification of the line, however that depended on the service level.
The outcome of the feasibility study and Strategic Outline Business Case (SOBC) resulted in the DfT awarding an additional £6 million of funding, which was confirmed in the Comprehensive Spending Review (CSR) of October 2021. Network Rail says that this extra funding was used to develop a final business case and to continue to develop proposals. The infrastructure manager is engaging specialist suppliers to develop design options with engineers conducting investigations on the line.
Between 8 August 2022 and 9 September 2022, Network Rail ran a public consultation on its proposals to gather feedback to help further develop the design and proposed service. This was held at eight public events in Hythe, Marchwood, Totton and Fawley and the feedback is now being analysed before being used to make a recommendation to government. Network Rail’s ideas are for passenger services to run from Southampton Central to an upgraded Marchwood station and the aforementioned new station at Hythe.
New infrastructure is required in Hythe including a new station with associated facilities, a new station forecourt, cycle facilities and connections for onward travel. Network Rail says there are two options for the station location with one alongside the railway behind the New Road car park, and one alongside the railway between Jones Lane and School Road. At Marchwood the plans include reopening the station with associated facilities, new station forecourt, cycle facilities and onward travel connections.
Under the plans there is the possibility of a new station depending on service patterns. The new services would also use the existing Totton station. Trains would service platform 5 at Southampton Central and this will be refurbished should the plans be approved.
Network Rail says that the benefits of reintroducing passenger services on the Waterside line would strengthen and improve transport links to the communities in the vicinity, support their growth, provide a more sustainable mode of transport and support both government and industry objectives. An example of the growth is that 1,500 new homes have been approved in recent months, with 2,500 jobs provided as a result.
In recent years the communities of Marchwood and Hythe have growth through residential and commercial developments.
This has led to increasing congestion on local roads, as CBT has also highlighted, particularly the A326 that links Fawley, Hythe and Marchwood with the main A35 road into Southampton.
Network Rail suggests that a regular passenger service could alleviate this problem by supporting the local communities and their travel patterns while also supporting their growth.
Any reopening of the railway in this corner of Hampshire now relies on the DfT. The success of the Okehampton line further west suggests that returning passenger trains to the route, which is unlikely before 2025, could have a major impact on the area. After almost 60 years, the communities are ready to use the railway again.
Inside Track takes a closer look at the ORR’s periodic review that will inform Network Rail’s SBP for the next control period
Network Rail is currently developing its business plans for Control Period 7 (CP7), which is due to begin on 1 April 2024 and last until 31 March 2029.
The 2023 periodic review (PR23) is an Office of Road and Rail (ORR) led statutory process that will establish the infrastructure manager’s funding and outputs for five years, starting from the first day of CP7. Subject to legislation being in place, this is also due to be the first day of Great British Railways (GBR), although that is subject to possible delay due to the length of time needed to get legislation required for the planned rail industry reform through parliament. Should GBR come into existence then it will adopt the CP7 commitments set out by Network Rail and be held
to account for delivering them. While Network Rail develops its business plans for CP7, the role of the ORR as the independent regulator is to assess these plans to see if they are achievable, both from a practical and financial view.
The ORR focuses on two key stages, with the first being its advice to the Secretary of State for Transport and Scottish ministers to help inform their decisions about how much funding they intend to make available to Network Rail during the next control period and what in return is expected to be delivered. The other is the ORR’s assessment of the Strategic Business Plans that will form the basis of the overall determination for the infrastructure manager, as well as the underlying settlements for the business units that
will set out their funding allocation and specific outputs that Network Rail must deliver.
The ORR says that its assessment will also help ensure that Network Rail’s CP7 business plans meet the infrastructure manager’s legal obligations, that they are consistent with funders’ priorities as set out in the Statements of Funds Available (SoFA) and the High-Level Output Statements (HLOS), are designed to deliver safety, performance, asset sustainability and efficiency to the benefit of taxpayers and users of the rail network, and take appropriate account of the views of passengers, freight users and other stakeholders.
Image: Network Rail Engineers undertake maintenance on the Moorgate linean acknowledgment that
being undertaken
challenging
for the rail industry. Passenger revenues have fallen due to the changes in travel patterns following the COVID-19 pandemic, and although passenger levels are approaching 100 per cent of pre-pandemic numbers, the markets have changed with leisure users dominating compared with the previous commuters, meaning the types of tickets have changed, with a large reduction in season tickets. The ORR states it is unclear when passenger revenues might recover.
There are also challenging macroeconomic conditions which means the government decisions on Network Rail’s CP7 funding are likely to be difficult. However, it remains important that the industry is able to demonstrate its efficiency in challenging times and therefore focus on managing costs; this means the assessment will consider how the CP7 business plans account for these challenges and balance the relevant risks and opportunities.
A periodic review is a statutory process that the ORR leads.
A key objective of this process is to establish the level of funding for the main line GB rail network and the outputs and outcomes it should deliver to rail users and taxpayers over a five-year period. The periodic review process also decides the framework for the contractual charges and the performance and possessions regime and sets out how Network Rail will be held to account in CP7.
that deliver new infrastructure capabilities – or how they should be funded, with the Department for Transport (DfT) and Transport Scotland (TS) continuing to manage these separately.
Setting funding and outputs on a five-year basis is designed to facilitate efficient and longer-term decision-making by providing stability and certainty about what the railway (including the supply chain) needs to deliver. It also helps ensure an enduring focus on the periodic review’s core objectives. The process is such that the Railway Industry Association (RIA) is keen for a similar method to be introduced for Transport for London (TfL) so that investment on the capital’s transport network can be planned.
The PR23 programme was formally launched in June 2021 and focuses on the funding and outputs for Network Rail’s infrastructure activities relating to operations, support, maintenance and renewals activities over the five-year period. In line with the previous approach taken five years ago for PR18, the ORR did not expect PR23 to include rail enhancements – large-scale projects
Governments decide the level of funding they will make available and what they want it to deliver, which is likely to replicate different strategic priorities. The ORR says that for England and Wales these relate to five strategic objectives as outlined in the whole-industry strategic plan (WISP): meeting customers’ needs, delivering financial sustainability, contributing to long-term economic growth, levelling up and connectivity, and delivering environmental sustainability.
Meanwhile in Scotland the ORR says that ministers’ priorities include decarbonisation of rail by 2035, improved resilience and asset management, growing the freight market and meeting the net cost challenge.
The funders will then set out their decisions through the HLOS and SoFA documents. Formal advice for both documents is provided by the regulator and this is based on its assessment of the infrastructure manager’s initial CP7 plans as well as its own holding-to-account work and other analysis. The ORR says this is part of a wider and ongoing engagement with funders about CP7 funding and outputs.
Once HLOS and SoFA documents have been issued and the ORR has possession of Network Rail’s Strategic Business Plans, it issues a formal determination that sets out its decisions on funding and outputs for the infrastructure manager for the duration of CP7 and this will include whether the funding available will deliver the outputs. The ORR explains that this process is conducted separately for England and Wales, and Scotland.
The ORR will also issue separate settlements for each region and the System Operator (SO) in Network Rail, and these set out the regulator’s expectations about the funding that will be allocated to them and the outputs that will be delivered by them. As part of its continuous business planning approach, Network Rail will submit its business plans for the next control period at key stages throughout the P23 process.
These will include the initial business plans, submitted by the end of March, the Strategic Business Plans and the Delivery Plan for CP7.
The ORR expects to use this plan to hold Network Rail to account for the delivery of its commitments. Across all plans, Network Rail will cover three key areas of business planning: outputs, expenditure and income forecasts.
For the outputs the CP7 business plan will identify the expected outputs that it aims to achieve based on expenditure and income forecasts. This will cover core areas of responsibility including, but not limited to, health and safety, train performance, asset management and efficiency.
The ORR expects Network Rail to set out what it will deliver against the funders’ priorities and for its customers and stakeholders, including in the key areas of safety, train performance, asset sustainability and efficiency.
This should also reflect how Network Rail is complying with its legal obligations (relating to, for example, health and safety or environmental).
Network Rail will do this for each region and function; however, the ORR would not expect the initial CP7 plans to include detailed quantified forecasts for all measures at this stage. For the Strategic Business Plans, the ORR would expect Network Rail to articulate in more detail the full range of outputs and outcomes it would expect to deliver, with quantified forecasts where appropriate. This reflects the fact that, once funders have issued their HLOSs and SoFAs, Network Rail has more certainty about the outputs it needs to deliver and the level of funding available to it.
The SBPs would need to include, where appropriate, forecasts for each region/function and by year. Network Rail will provide a consolidated SBP for England and Wales and for Scotland, as well as a GB-wide plan.
The expenditure forecasts are expected to cover operations, support (human resources or IT), maintenance and renewals, while the income relates to Network Rail’s key income streams, including government funding made available through the SoFA and the revenue generated from rail users such as passenger and freight operators via track access contracts. Other revenue streams include property rental, sales and advertising.
The ORR’s general approach to assessing the plans involves reviewing, challenging and assessing Network Rail’s CP7 business plans. The objective here is to determine whether, through the plans, Network Rail is likely to meet its legal requirements and that the Strategic Business Plans and the CP7 Delivery Plan are consistent with funders’ HLOSs and SoFAs and the PR23 core objectives.
Customers and other stakeholders’ views are also considered by the ORR, which uses a riskbased, progressive-assurance and collaborative approach to assess Network Rail’s plans.
The multi-disciplinary team will consider a wide range of sources of information. Consideration is given as to whether the forecast outputs in the business plans (individually and when considered as a whole) and the associated expenditure are consistent with funders’ priorities and PR23 objectives; there are income assessment reviews of Network Rail’s forecasts and once a funder has issued its SoFA and HLOS, the regulator will also carry out an affordability assessment that brings together its own assessments relating to expenditure, outputs and income to determine whether there are sufficient funds in each SoFA to meet the associated HLOS. Again, this is conducted separately for England and Wales, and for Scotland.
The principles of the assessment approach are progressive assurance, risk-based approach and collaborative assessment. The ORR also relies on evidence produced from its own internal analysis and this includes its own knowledge and experience along with results of its own sessions with Network Rail, its own internal analysis on specific areas, its cost benchmarking statistical analysis and input from external independent parties. Network Rail is expected to engage with funders and stakeholders while developing its business plans, but it should also explain how this engagement has informed or changed its plans and make clear that there are issues where it has not been possible to address concerns. It’s worth noting that the ORR also regularly engages with funders as well as industry groups (the Rail Delivery Group and the Railway Industry Association for example), and it will also continue to meet with individual stakeholders to discuss specific issues.
Ahead of issuing its Final Determination, the ORR will consult formally on the proposed allocation of funding and outputs to each region and function and by activity area. Stakeholders will have an opportunity to engage on this, including by providing a formal response.
The ORR’s assessment will put particular focus on ensuring Network Rail is being as efficient as is realistically possible and can deliver the HLOS for the funding set out in the SoFAs. Network Rail’s CP7 business plans should draw out any areas where there could be long-term implications on health and safety, asset condition and performance of the network, and the regulator will assess how Network Rail is planning to manage any emerging risks.
The income forecasts are important because that should mean, all things being equal, that the amount of money required for funding is reduced. To ensure this is the case, the ORR will review any gaps between the funding and planned income and also whether there are further opportunities that could be explored as well also assessing whether market assumptions are accurate. To achieve this the regulator must, where possible, compare Network Rail’s forecasts to comparable businesses. There is particular focus by the regulator on the infrastructure manager’s assumptions for money raised via sales and rentals and the Group Property Unit’s business plan is reviewed as well as the regions’ plans for property within their control.
The ORR says that Network Rail must do everything reasonably practicable to deliver the outcomes within the funding available, however if it is considered that
there are insufficient funds to meet the associated outputs, then the regulator is required to notify the relevant government, either that in Westminster for England and Wales or Holyrood for Scotland, and this may then revise its HLOS and/or SoFA.
The ORR’s assessment of the regional business plans will focus on health and safety, asset management, deliverability, cost efficiency and allocation, train performance, financial risk management, innovation and technology adaptation, environment, and accessibility. Consideration will also be given as to how these aspects of the plans relate to each other and what they may mean for Network Rail’s overall delivery. Assessment of the system operator’s business plan will consider each of its key accountabilities including its role in capacity allocation, timetabling, strategic planning, and delivery to freight and national operators, while the assessment of the business plans will evolve as plans become more detailed.
There is also consideration as to the extent to which Network Rail and its supply chain can deliver its plans. The regulator expects to consider changing rail demand and the scope to optimise track access in delivering works, as well as the impact of other and competing infrastructure such as HS2 on the capability of the supply chain to deliver work. The ORR must also consider how Network Rail should be required to report on its delivery to provide transparency and confidence to funders and stakeholders.
When providing its advice to Ministers, the regulator will consider whether planned volumes of renewals work set out in the initial CP7 plans
are realistic based on its own knowledge about the capacity and capability of Network Rail and its supply chain. It will also specifically consider whether the initial plans consider the likely CP6 exit point, reflect appropriate input from key stakeholder groups including the supply chain, and reflect the findings of Network Rail’s own internal assurance.
On 28 July this year, the ORR published documents relating to the future regulation of the rail network. Announcing the publication, it said that it expects funding decisions to made in October for England and Wales followed by a decision for Scotland in November and that following this the ORR expects Network Rail to submit its Strategic Business Plan in February 2023. After that the ORR will produce a draft determination and, later in the year, a final determination.
Speaking in July, Will Godfrey, ORR director of economics, finance and markets, said: “Periodic reviews like PR23 are one of the main ways in which we look to secure value for money for users and funders of the railway. Periodic reviews help ensure there is sufficient long-term focus on issues such as safety, performance, asset sustainability, and efficiency.
“ORR looks forward to hearing from stakeholders on the proposals set out in our PR23 consultations and working with industry to set the right long-term framework for the rail infrastructure for 2024-2029.”
Image: Network Rail Air Operations An aerial view of pre-assembled SAS 13 bridge showing closed Stechford to Aston freight lineTim Samuel and Matt Wilton launched Mosaic Rail in 2017 after identifying a gap in the signalling market; namely for a smaller, more agile design consultancy that would provide expert support without full-scale mobilisation.
This flexible, responsive approach has helped Mosaic win work with Network Rail and a range of tier one suppliers, with overseas growth planned.
Mosaic remains committed to its original aim of providing cost-effective signalling design solutions. Mosaic works as a delivery partner or as part of a client’s existing team, providing support with everything from initial feasibility assessments to full-scale signalling design. Experienced design engineers Tim and Matt met working together in Manchester and discovered shared misgivings about Network Rail’s framework procurement model and its impact on the signalling industry.
“What we were seeing, from our personal point of view, was that with a large-scale supplier working across a region, we weren’t managing to do justice in both timeframe and costs to the smaller renewals and enhancements that were also coming under the framework umbrella,” Tim explained.
“We were seeing that the availability of a small, agile design house that could come in, deliver a piece of work, and disappear again, didn’t seem to be in the market. We deliberated as to whether we could fill that gap in the market effectively. At the end of 2017, we decided the time was right to set up Mosaic.”
Matt and Tim agreed that Mosaic would not compete with existing suppliers, instead picking up small signalling projects major companies could not deliver quickly and cost effectively.
“CP6 and into CP7 is concentrated a lot less on the major resignalling projects, and more on patch and mend, renewals, and more efficient technologies,” Tim said. “To mobilise a tier one to do that kind of work, especially one geared up for major projects with a product to sell to the industry, isn’t cost effective. What we have seen within the industry is Network Rail delivery units have struggled to deliver fairly rudimental but important works, such as signal head renewals, remote condition monitoring, track circuit conversions, effectively and efficiently.”
As part of this strategy, the duo set about adapting the offshoring model employed by other suppliers over a number of years.
“The model was that work considered to be relatively complex, with multiple interfaces, was kept in the UK, while relatively straightforward work was sent offshore,” Tim explained. “We saw that this didn’t breed a sense of belonging in terms of the project; it was a very siloed mentality.”
“We were so impressed with the attitude and skillset of the offshore staff,” Tim said. “The rates are comparable now to the UK, so it wasn’t about cost savings, but we managed to secure a resource that is becoming rarer in the UK, primarily down to historical lack of investment in the training of UK engineers.”
Matt and Tim established an Indian sister company, Mosaic Rail PVT. Today, they ensure that its team is involved in projects from concept to completion.
“We’re finding that it’s really working, and our offshore team have risen to the challenge over the past few years,” Tim added. “It’s creating more well-rounded engineers. It means you have an appreciation of how your design impacts the person who installs it, tests it, and maintains it.”
This model was something that both Tim and Matt felt had previously been missing from the marketplace.
“While we are not involved with the installation and testing, what we do like to do is ensure that our
designers have that appreciation of how the design impacts the installer, maintainer and the tester, so that when the design is presented to site, we can have confidence it can be implemented, tested and maintained with the minimum of effort,” Tim added.
This approach, coupled with Mosaic’s flexibility and willingness to take on smaller signalling projects, makes it unique in the industry.
“From the start our offering was different, because we came along with highly trained staff and complemented existing design teams,” Tim said. “We wanted to build up that rapport, build up trust, and provide a flexible and friendly alternative.
“If a client sends us tenders, we’re happy to price and deliver them, but we also said to more established partners, ‘if you’ve got overspill as part of existing framework commitments, let us support you’.
“We wanted to offer something that was a bit more agile,” Tim said.
Indeed, after working within the framework model, Matt and Tim were keen to take a different approach.
“We don’t want people to be turned off by the idea that signalling projects are too difficult and too expensive,” Tim explained.
“We’re not visionaries, but we could see the way our industry was moving, and the way that kind of contract strategy was driving certain behaviours in the supply chain.
“Traditionally, if I had a problem as an engineer, I could contact peers in different companies, say ‘have you seen this before?’, and they’d give me their time,” he said. “But the way the contract strategy is, it has tribalised the industry, engineering teams are hidden behind a paywall, whereas in reality we’re all engineers trying to deliver the best quality.”
Tim and Matt’s responsive, more collaborative approach has helped them to win work with a range of leading clients – including Network Rail. In late 2018, it contracted Mosaic to assist with Project Alpha, a performance improvement programme for the North West and Central Region.
“We were approached by Network Rail in late 2018 to investigate the timetable delays being incurred due to the signalling controls approaching Crewe,” explained Tim.Mosaic could respond quickly and efficiently to the request and commence a feasibility study.
“Within two weeks we had provided an initial feasibility report explaining the reasoning behind the signalling controls and where, with consultation and due process, these could look to be relaxed,” Tim added.
Matt and Tim are keen to forge relationships with major civil contractors, picking up small-scale work while clients focus on the bigger picture.
“If you’re encountering elements of signalling, such as signs that need moving and sighting assessments, you can just pick up the phone to us and we’ll look into it,” Tim said. “We’ll assess the work and come in with our competent team, provide advice as necessary, undertake the delivery, and allow you to proceed with your specialism.”
Supporting the framework supplier, Mosaic undertook stakeholder consultation, liaising with the passenger and freight operators, and Network Rail. The replacement TPWS solution proposed meant that existing CDR controls could be removed. Mosaic has built relationships with several tier one suppliers, including infrastructure specialist Linbrooke and VolkerRail. Its ability to deliver solutions quickly and cost effectively continues to win repeat work.
“The proof of the pudding is that they keep coming back to us, which is fantastic,” Tim said.
Mosaic is also exploring the growing Australian market. “We’ve been providing services to the equivalent of a tier one in Australia for around about two years now, and we’ve been in some very fruitful discussions with a number of other companies out there,” Matt explained.
If it continues to win work in Australia, Mosaic will open a second sister company in the country. “It’s about targeted markets, and Australia is one of them,” he added. “North America is another.”
However, bringing the UK rail industry together remains a priority for Matt and Tim.
“The idea behind the name was that the individual pieces come together to create the bigger picture,” Tim said. “It’s something that is a passion of ours – getting people together to showcase the industry.”
We’ll assess the work and come in with our competent team, provide advice as necessary
“ “
The company behind Britain’s new high-speed rail network is trialling technology developed for motorsport to dramatically cut fuel consumption, carbon emissions and improve air quality at one of its London construction sites
uston station is the site of various innovative new technological advancements on the HS2 project which, when complete, will link the capital with the West Midlands and northern England.
Trains are due to begin operating into Euston between 2029 and 2033 as part of Phase One of the scheme, which will initially see trains running between London and Curzon Street in Birmingham.
Construction at the site is under way, while planning for the new station continues.
Technology used in the highly innovative world of F1 motorsport used to reduce emissions is being trialled by the company behind Britain’s new highspeed rail line.
The aim of the trial, launched by HS2 Ltd in August this year, is to dramatically cut fuel consumption, carbon emissions and improve the air quality at one of its London construction sites. The site, which is where HS2’s London tunnels surface, is operated by the project’s tier one civils contractor Skanska Costain STRABAG joint venture (SCS JV).
This trial is part of the HS2 Ltd Innovation programme and involves a tower crane on the railway’s Euston approaches site.
Usually, this would be powered by a 500kVA diesel generator and would lift loads of up to 24 tonnes, but instead it will be driven by one less than half that size.
The significantly smaller 200kVA generator’s power difference is bridged by pairing it with an energy storing flywheel system developed and supplied by Silverstone-based engineering specialist PUNCH Flybrid.
Incorporated within the PUNCH Flybrid-supplied unit is a flywheel measuring just 35cm in diameter, however it is housed in a vacuum chamber to all but
Delivering Britain’s zero carbon, highspeed rail network for the 21st century is a national endeavour
eliminate energy-sapping resistance that would result from any contact with the air.
The technology matches the power of larger, thirstier generators by using the 200kVA generator’s surplus power during the crane’s low load periods
to charge the spinning flywheel to very high speeds, equivalent to a ground speed of 550mph. The kinetic energy stored by the flywheel can then be quickly released to support the generator when the crane demands maximum power to lift heavy loads. This expertise was originally deployed in Formula 1 motorsport before then being subsequently put through its paces in endurance racing, including the famous Le Mans 24 Hour race held in France, before both sports opted to focus exclusively on electric battery-based hybrid technology, which is now widely used in passenger cars.
Able to perform up to 10 million charging cycles compared to 3,000 of a typical electric vehicle battery, the PUNCH Flybrid’s flywheel know-how is, through HS2’s Innovation programme, proving to be the perfect fit with the extreme and repetitive demands of the construction industry.
“Delivering Britain’s zero carbon, highspeed rail network for the 21st century is a national endeavour that is drawing on skills and technology both in and beyond the rail and construction sectors,” said HS2 innovation manager Rob Cairns.
“Our trial work with PUNCH Flybrid is another great example of how investing in long-term national infrastructure programmes creates opportunities to draw on technology that could potentially unlock significant benefits for our industry.”
Such is the hybrid system’s efficiency that in May this year, the Euston trial more than halved the diesel consumed by the single tower crane to 6.3lt per hour thereby saving 4.8 tonnes of carbon – the equivalent to the average monthly CO2 emissions of 40 family cars.
“In motor racing, a team’s quest for higher performance spurs the search for greater efficiency – essentially doing more with less,” said Tobias Knichel, PUNCH Flybrid managing director. “Racing cars typically accelerate and brake around 500 times during a 90-minute F1 grand prix. Each time the car brakes into a corner at high power our flywheel system spins up, storing energy that is then released quickly to boost acceleration performance as the car leaves a bend.”
Designed by the Silverstone-based company, the technology is also able to work with hydrogen, mains electricity and battery-powered generators, and the innovation trial is a significant step towards HS2’s ambition of diesel-free construction sites.
“We developed our flywheel technology to improve performance and efficiency at the very pinnacle of the automotive industry, but its fundamentals mean there are opportunities to deploy its benefits in other sectors,” Tobias added.
UK, said: “Innovate UK is delighted to work with HS2 in the delivery of innovation for this prestigious programme, and through this collaborative working a new relationship between HS2 with PUNCH Flybrid has created the opportunity to explore the potential offered by a tried and tested automotive technology to save fuel, cut costs, reduce CO2 emissions and create possibilities for future economic growth in the high value manufacturing and engineering sectors.”
“That’s why we’re very pleased to have an opportunity to utilise the technology for the construction industry under HS2’s Innovation programme.”
Linked with HS2 after applying to Innovate UK’s Innovate at HS2 2020 competition, the partnership with PUNCH Flybrid demonstrates how linking Britain’s largest infrastructure project with industries beyond the construction and rail sectors has the potential to create long-term benefits and opportunities throughout the wider economy.
Kelvin Davies, innovation lead for rail at Innovate
SCS JV managing director James Richardson said: “SCS JV is committed to reducing our environmental footprint by identifying innovations like this flywheel technology, which has immediately halved our diesel consumption of one of our cranes operating at our Euston approaches site.”
The trial is due to conclude before the end of 2022, but it is not the only innovation taking place at Euston. In what HS2 Ltd says is a first for the UK, an SME graduate of HS2’s Innovation Accelerator programme is harnessing the power of Artificial Intelligence (AI) and laser-based Light Detection and Ranging (LiDAR) sensors developed by the automotive industry to help design a stress-free passenger experience of the future.
Seaton Rail’s Railway and Track Safety Training Courses provide companies with the skills, knowledge and certification to ensure that works on the railway are carried out efficiently and safely as well as in full compliance with Network Rail Standards.
Seaton Rail’s Railway and Track Safety Training Courses provide companies with the skills, knowledge and certification to ensure that works on the railway are carried out efficiently and safely as well as in full compliance with Network Rail Standards.
Seaton Rail are one of the leading railway training and assessment providers. Our courses are delivered by professional, full-time trainers who know how to get their message across. We can also tailor course content and format to meet your specific requirements. Our courses are delivered at our modern training centres in Bridlington, Goole, York, Rotherham and Glasgow where we have excellent facilities, lunch is provided, unlimited free hot and cold drinks and free wi-fi.
Seaton Rail are one of the leading railway training and assessment providers. Our courses are delivered by professional, full-time trainers who know how to get their message across. We can also tailor course content and format to meet your specific requirements. Our courses are delivered at our modern training centres in Goole and Bridlington where we have excellent facilities, lunch is provided, unlimited free hot and cold drinks and free wi-fi.
We also arrange training to meet the requirements of our Clients shift patterns including early, late and night turns of duty. Training is also available at the weekends, or at a premises of your choice.
We also arrange training to meet the requirements of our clients shift patterns including early, late and night turns of duty. Training is also available at the weekends, or at a premises of your choice.
Courses we deliver
Personal
Alone
Using digital data from a live main line station it will establish, for the first time, information to aid future design and operations
“ “
The collaborative project, led by hi-tech SME OpenSpace Group Ltd, is part of HS2 Ltd’s Innovation programme and brings together Network Rail, train operator Avanti West Coast (AWC), and the University of Birmingham, as well as HS2 Ltd.
Called Future Stations Living Lab, it is the first time a train operator, in this instance AWC, has joined infrastructure providers and academia to put the passenger at the heart of design through digital twin technology. In a radical break from the past, the six-month proof-of-concept project will use LiDAR technology to digitise passenger flow data and inform the design of future HS2 stations, delivering an improved, low-stress customer experience.
HS2 Ltd explained that traditionally stations have been designed, built and run in a way that focused on smooth running of trains for the benefit of passengers. Now the Future Stations Living Lab will put passengers at the heart of design by creating a real-time replica of the existing Euston station.
Central to the project is the combination of computer vision systems with cutting-edge LiDAR sensors that will capture highly accurate people movement data at Euston’s forecourt, concourse and ticket gates. Developed by the automotive industry to guide driverless cars, just one LiDAR sensor has the potential to collect movements across the station’s large forecourt and concourse areas.
The anonymous data will then be overlaid on a virtual replica of Euston station and used to generate gaming-derived simulations of how people use various key station locations and ‘what-if’ scenarios. The unprecedented granularity of the data will provide new insights into how people interact with the station, enabling new opportunities for designing passenger-centric stations of the future
The data will also help both Network Rail and
AWC to develop both the customer experience and safety procedures of the existing main line station, which is served by not only AWC but also London Northwestern Railway, London Overground, Caledonian Sleeper and various charter operators.
HS2 innovation manager Heather Donald said: “Future Stations Living Lab is doubly innovative because it draws on both AI and virtual reality (VR) technologies as well as know-how from the automotive and video gaming industries and is rail’s first inter-sector collaboration.
“Using digital data from a live main line station it will establish, for the first time, information to aid future design and operations.”
OpenSpace Group Ltd founder and CEO Nicolas Le Glatin said: “This innovative collaboration will help forge a new chapter in station design and operations, fusing an array of emerging digital twin technologies for the benefit of customer experience.”
The Future Stations Living Lab proof-of-concept project is due to conclude during the autumn.
As for Euston station itself, a new concept design for the exterior and interior were unveiled in March this year, with the updated design enabling a less complex, more efficient 10-platform station that can now be constructed in a single stage.
The designs have also been showcased to people in the local area via CGIs and sketches of the design and a 1:1000 ratio 3D model of the station, which put the station in the context of its local area.
The new designs were drawn up by a design consortium consisting of multiple organisations including Arup, WSP and Grimshaw Architects working into HS2’s Station Construction Partner, Mace Dragados JV (MDJV).
The new station will feature a bold geometric roof design that allows natural light to flood into the station concourse, emphasising its northsouth alignment. Elements of the roof can be prefabricated off site and installed using modular construction techniques that reduce costs, carbon emissions and local disruption.
Laurence Whitbourn, Euston area client director for HS2 Ltd, said: “HS2 arriving at Euston is a transformative opportunity for the area, and we want to work with local stakeholders and partners to create a new piece of the city of London, creating homes, public spaces and thousands of new jobs.”
The design also includes key elements to improve connectivity around the stations at Euston, including a north-south route through the HS2 station concourse that will be linked with new public east-west routes constructed at an elevated level through the HS2 station.
Proposals for future regeneration of the Network Rail station will seek to complete these east-west links to provide pedestrian connections from Cobourg Street to Eversholt Street. Better connections on the London Underground (LU) at Euston and Euston Square will also be delivered and, for the first time, LU passengers will have seamless connections between the Northern, Victoria, Circle, Hammersmith and City and Metropolitan lines at Euston.
The station will now be built in a single stage, reducing the construction period and the impact for the local community and passengers using the existing conventional railway station at Euston. The station will maintain the capacity to run up to 17 trains per hour. MDJV will carry out the main station construction work.
The HS2 Euston station is also designed to target a ‘BREEAM outstanding’ rating, which is an industry recognised standard for buildings that reduce energy usage and materials waste and minimise impact on the natural environment. As well as an enhanced Euston Square Gardens, HS2 Ltd also plans to deliver a major new public green space in the north as well as a community gardens in the west, which will be designed to respond to local community needs.
The station design encourages walking and cycling as part of a sustainable transport strategy, providing new cycle routes and 2,000 cycle parking spaces to encourage a safe and active travel environment. Once Euston is complete it will not just be a major transport hub according to HS2 Ltd, but it will be a destination and one where the local community are an integral part of the development. Through the development, Euston will be a place where existing and new communities will thrive together.
The integration of the stations at Euston will enable the comprehensive transformation of the area by unlocking development above and around the stations and tracks.
Already Lendlease, the government’s appointed Master Development Partner at Euston, has started an 18-month public consultation to seek the views of the local community about what would be of
value to them in the development. Following this community engagement, HS2 will be moving forward with the Schedule 17 Planning Application for HS2’s Euston station.
The National Railway Museum (NRM) in York is to be transformed over the next few years in a project that will make it the ‘world’s railway museum’.
Plans for a new Central Hall at the NRM have been approved by the City of York Council’s planning committee.
This new structure is expected to transform the museum and herald the start of delivering the long-awaited York Central development.
According to the NRM, this new development will help it realise its potential as the cultural heart of York Central and unite the museum for the first time.
Under the approved plans, Central Hall will be a new welcome space and gallery located between the NRM’s Great Hall and Station Hall. By connecting existing museum buildings, it is seen as a cornerstone of the museum’s Vision 2025 plan, which aims to transform its offer and become not only Britain’s railway museum but the world’s railway museum.
The NRM has the largest collection of railway objects in the world and, prior to the pandemic, attracted more than 750,000 visitors a year. The collection also includes more than 260 locomotives and rolling stock, 600 coins and medals as well as railway uniform, equipment, documents, artwork and photographs.
The NRM said that it is a condition of the Stopping Up Order for Leeman Road that it will not be stopped up until the alternative highway routes are in place for pedestrians, cyclists and vehicles; construction is already under way on these routes.
As part of the vision there is also Wonderlab: The Brammall Gallery, which is an interactive gallery aimed at inspiring children to think like engineers through experience, interactivity and play.
In a statement, the NRM explained that Central Hall will feature a Railway Futures Gallery showcasing the latest innovations in rail technology, a café overlooking the new museum square, a shop, a flexible event space and new visitor facilities.
Sustainability is also at the heart of the Central Hall design, with environmentally friendly design principles and materials that are in keeping with the city’s rich railway history and the surrounding area.
Judith McNicol, director of the NRM, said: “We are very pleased the planning committee has approved the Central Hall plans, which will have transformative benefits for York and the wider region. This approval will allow the museum to realise its potential as the world’s railway museum by improving our offer, welcoming more visitors and helping us to inspire the next generation of engineers and problem solvers.
“The museum aims to be the cultural heart of York Central and this decision brings us a step closer to realising that ambition. We remain on track for opening Central Hall in autumn 2025, in time for the museum’s 50th anniversary.”
As the project moves towards construction, the NRM will engage with residents and visitors to ensure that the planned changes act as a true community resource for the evolving neighbourhood.
Central Hall forms an early stage of the delivery of York Central, a 45-hectare regeneration site
that will be delivered by a partnership including Network Rail, Homes England, City of York Council and the NRM. Work is expected to commence early next year and should be complete in time for the 50th anniversary celebrations in 2025.
The new building has been designed by Feilden Fowles with Montagu Evans acting as heritage consultant. Graham has also been appointed to deliver pre-construction services for Central Hall.
Neil McFarlane, Graham strategic projects director, said: “We are delighted to have been appointed as the preferred bidder for the NRM’s Central Hall project. We understand the significance of this project for the Science Museum Group and recognise their aspirations for Central Hall to become the gateway to the transformed museum. Our highly experienced team has a strong track record of working to deliver shared project goals. We will be responsible for ensuring key project milestones are achieved under the PreContract Services Agreement.”